2025 Author: Howard Calhoun | [email protected]. Last modified: 2025-01-24 13:10
Sometimes enterprises accumulate inventory balances for the most popular positions. However, it is impossible to increase stocks indefinitely. It is necessary to determine the optimal order sizes. For this purpose, the Wilson formula is used.
Views
Stocks in warehouses are divided into production and commodity. The first category includes purchased stocks intended for the manufacture of products. Their purpose is to ensure an uninterrupted production process. Inventory is stock left in warehouses and in transit to wholesalers and retailers.
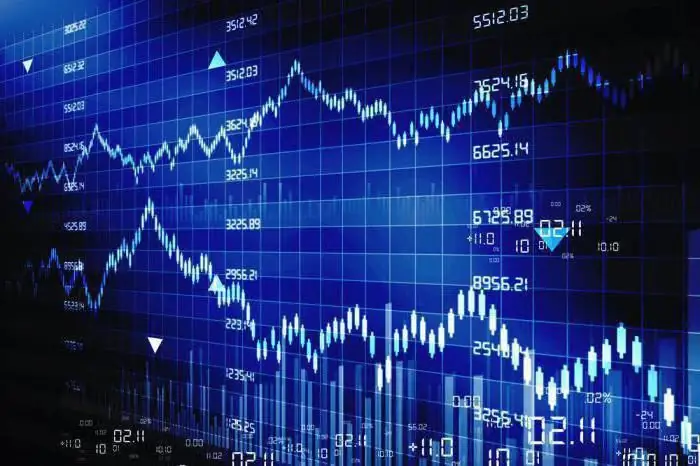
Current stocks are designed to ensure the smooth flow of trade or production between deliveries of goods. Safety stocks are accumulated for the same purpose, but in case of unforeseen circumstances: change in the supply line, increase in demand, delays in transit. In a normal market situation, the amount of safety stock does not change.
Whystockpile?
Stocks in the economy ensure the stable operation of the system. But this method is quite expensive. According to foreign sources, it costs 25 cents a year to store a unit of production worth 1 dollar. Domestic economists give similar figures - 20-30% of the value of the goods. If a company has inventories worth 100 million rubles, then it spends another 25 million to maintain them.
Risks
Storage has a number of disadvantages. This is:
- freezing financial resources;
- suspension of the quality improvement process, as the organization first liquidates stocks and then buys new products;
- isolation of logistics in the distribution scheme;
- expenses for the maintenance of special premises and the wages of storekeepers;
- risk of loss due to property damage or theft.
Based on how much storage costs an organization incurs, the entire inventory management process is determined. The Wilson Formula helps you calculate how much inventory you need to cut. Although there are risks involved in storing products, entrepreneurs are forced to take them, as the lack of stocks entails a loss of profit.
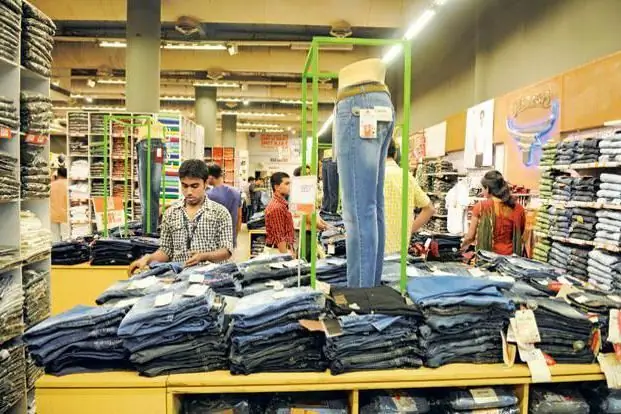
The result of the calculations obtained using the Wilson model, the formula of which was presented earlier, should be compared with other expenses. The cost of purchasing each type of product should be less than the cost of storing it. Only then does it make sense to stockpile.
Problemscontrols
- The size of an order is influenced by a large number of factors: its size, uneven consumption, remoteness of the supplier, logistics.
- Stocks can be formed for both current deliveries and seasonal sales.
- A large number of inventory control systems: from periodic to continuous.
- With the expansion of the range, the risk of calculating the optimal delivery batch increases. Wilson's formula does not exclude this risk.
- Increased lead times in regions with cheap labor.
Term
Optimal order quantity (Wilson's formula) is a model that can be used to determine an economically viable order quantity at minimum cost. It applies under the following conditions:
- Clearly known product demand and delivery time.
- Receive the goods instantly.
- No stockouts and bulk discounts.
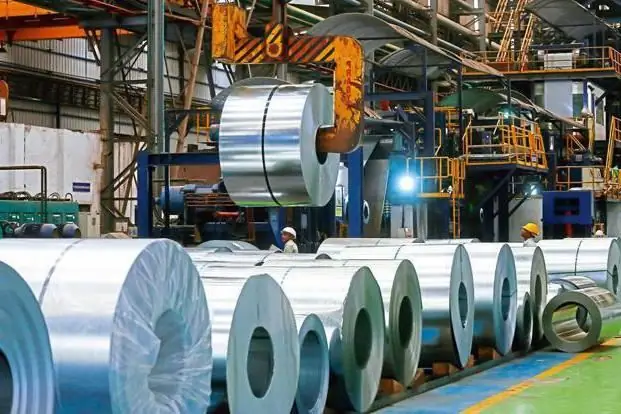
Wilson formula
Optimal order quantity TS=PR + CR / Q + PFQ / 2, where
- Q - order size;
- C - placement costs;
- R - annual demand;
- P - the cost of purchasing 1 piece of products;
- F - storage cost factor (usually 10-15%).
- PF - the cost of storing goods for the year.
For whom?
Wilson's formula was developed for large industrial enterprises. It cannot be used in this form in modern trading companies. First of all, it should be expanded to take into accountdebt costs and a wide range of products. Only after that you can apply the Wilson formula on a group of weighty (ABC-analysis) and stable goods (XYZ-analysis).
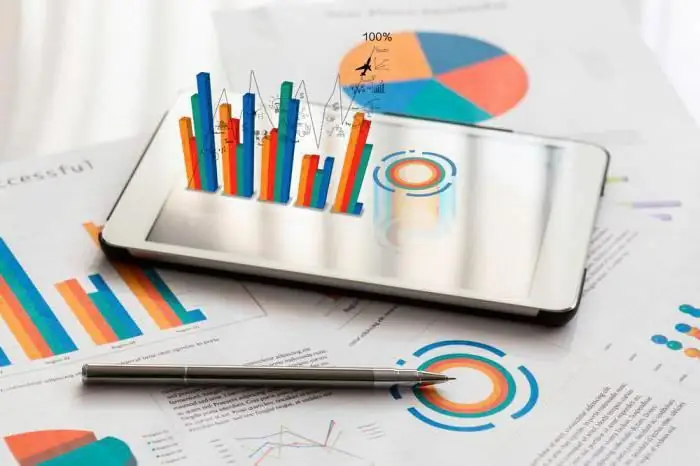
Other indicators
To manage inventory, you can use not only the Wilson formula. In economic theory, there are a number of other coefficients that refine the results of calculations.
Inventory turnover shows how many times a product goes through all sales cycles in a specified period of time. Using this indicator, you can calculate the possibility of obtaining a gross profit from one ruble invested in the purchase of goods:
Oz=Cost of purchased goods per month (quarter, year) / Average stock of goods for the same period.
When calculating the indicator, products purchased for a specific order are not taken into account.
Stock availability - how many days will the organization's current stocks last if supplies suddenly stop:
Safety=Inventory Value x Days / Average Inventory
Share of inventories in current and non-current assets:
UD=Inventory value / OA (IA)
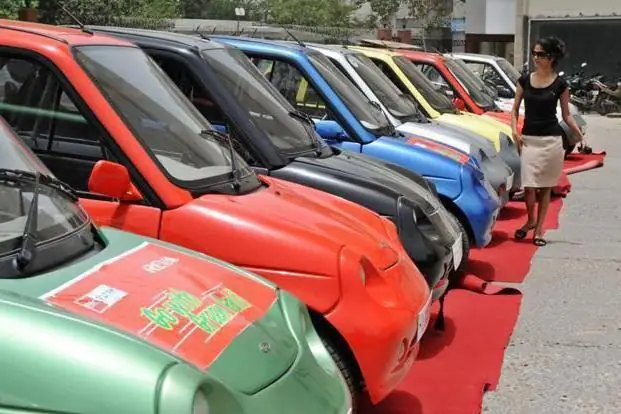
ABC analysis
This method of calculation determines the firm's most important resources. It can be applied to all types of organizations. It is formed according to the Pareo principle: 80% of the turnover gives 20% of the goods. Reliable control of this part of the resources (reserves) will make it possible to control the system as a whole.
As part of the ABC-analysis, commodity items are divided into threeCategories:
- A - the most profitable: 20% of the assortment brings 80% of orders.
- B - intermediate: 30% of the assortment brings 15% of sales.
- C - the least valuable: 50% of the assortment brings 5% of orders.
ABC-analysis is ranking by parameters. Moreover, you can sort not only products, but also customers, the duration of the sales period, and other important statistics. The goal is to group objects according to the degree of their influence on the final result. During the analysis, a graph is also formed, which is called the Pareto curve (Lorenz or ABC curve). The same method can be used to rank customers by the number of orders in logistics. Wilson's formula is not suitable for this purpose.
Objects can be grouped according to cost indicators. In this case, the share of objects and the overall result are added up (for example, if the products bring 50% of orders, then this value is doubled). The value of the sums is in the range from 0% to 200%. Groups are formed according to the following criteria: A - 100%, B - 45%, C - the rest.
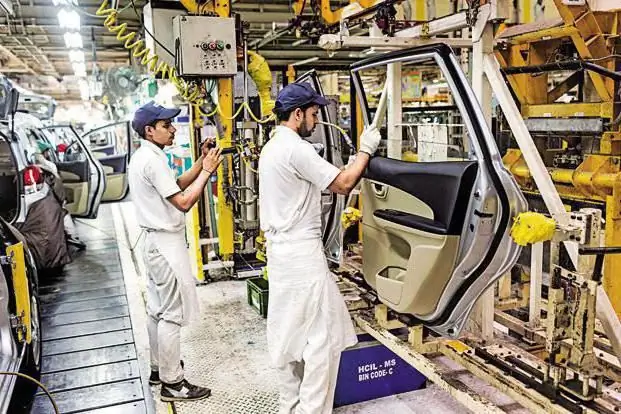
XYZ analysis
Another way to determine the optimal order is to calculate the coefficient of variation (XYZ analysis). It reflects the spread of the value relative to the average (order volume, sales level, number of customers, etc.). With it, you can exclude the influence of seasonal factors on the final indicator. The calculation process uses the standard deviation percentage formula.
Information is ranked as followsway:
- X - the smallest changes in the average value (0-10%);
- U - changes in values by 10-25% of the average;
- Z - change in values by more than 25%.
The first two groups of indicators have the greatest influence on the final result.
Thus, before applying the Wilson formula, you should determine the most significant product groups for the organization, and then calculate the stock limit.
Recommended:
Calculation of northern allowances in the regions of the Far North: calculation procedure, determination of size, coefficients
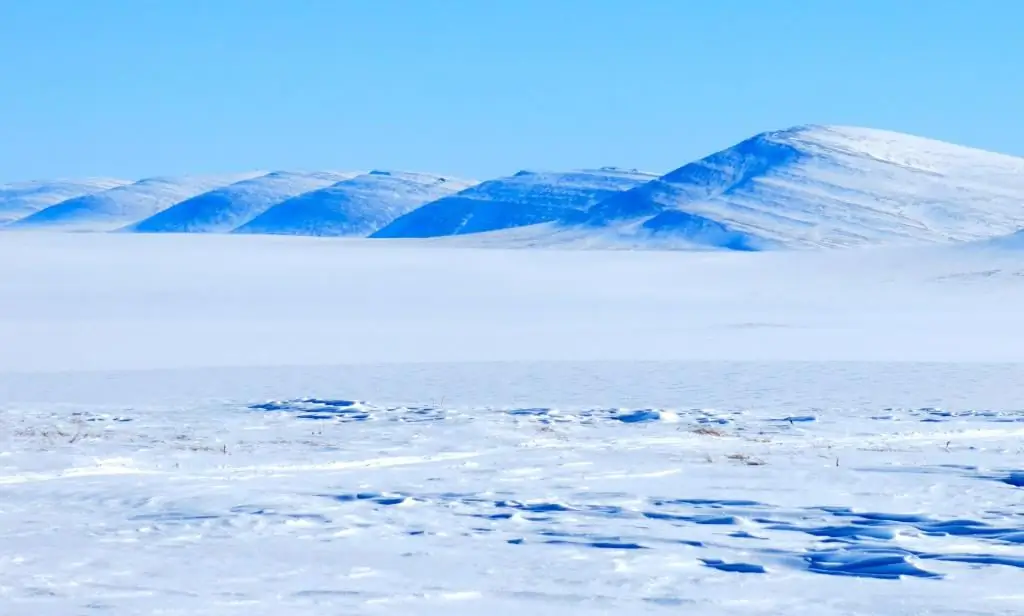
Which regions are considered the Far North according to the legislation updated in 2018? What acts regulate northern allowances? Basic rules for calculating these surcharges. Four groups of localities - four sizes of allowances. Features, conditions, procedure for their accrual to young professionals, indigenous people, citizens over 30 years old, military personnel. Is there a connection with the district coefficient?
Vacation calculation: formula, example. Calculation of parental leave
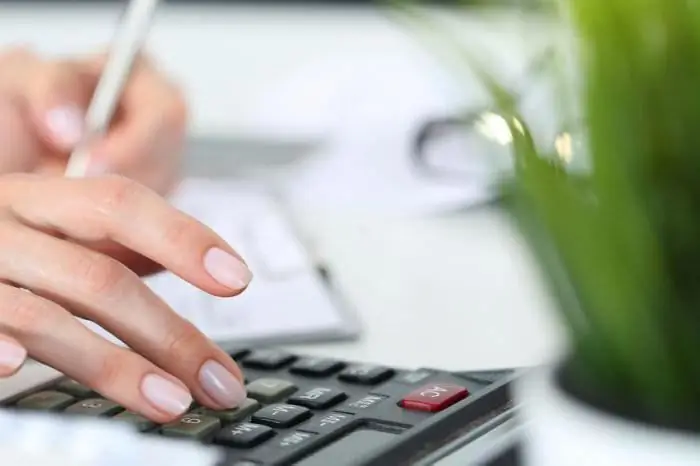
In the framework of this article, we will consider the basic rules for calculating vacation pay for an employee, including in various interpretations: on maternity leave, for child care, upon dismissal, as well as for harmful working conditions
Wage fund: calculation formula. Wage fund: formula for calculating the balance sheet, example
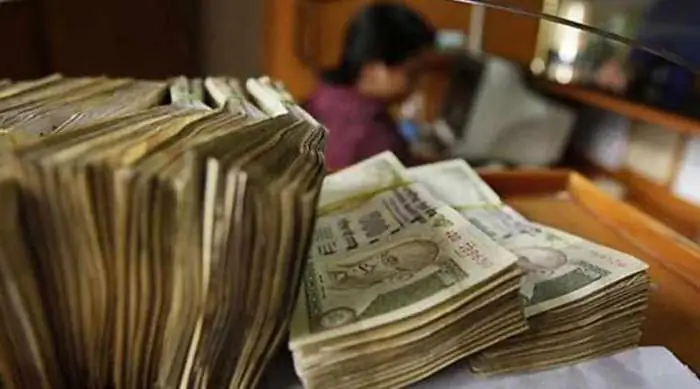
As part of this article, we will consider the basics of calculating the wage fund, which includes a variety of payments in favor of company employees
The effective interest rate is Definition, calculation features, example and recommendations
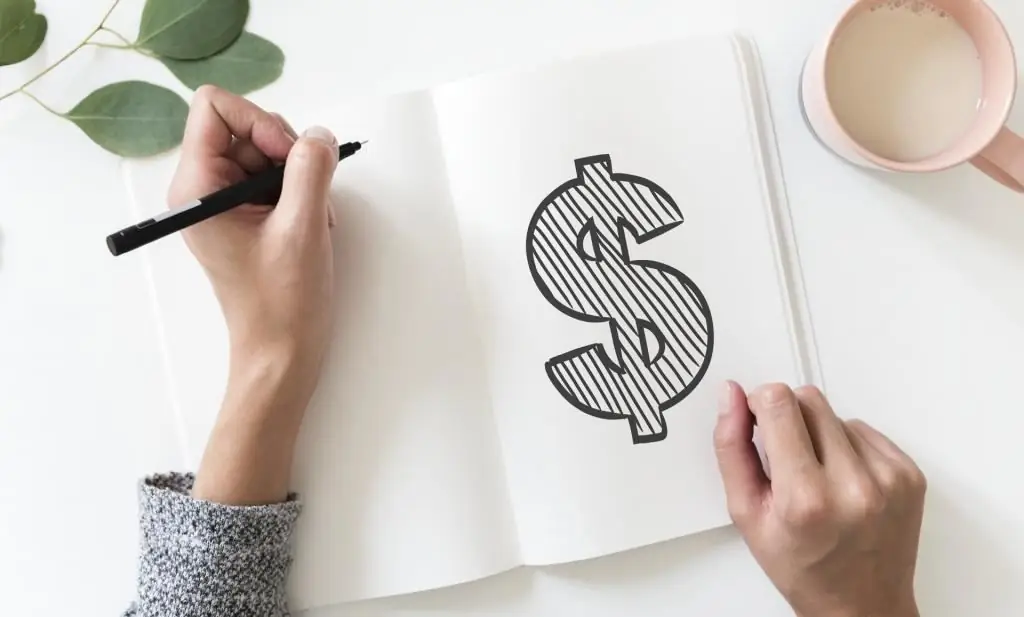
As part of the analysis of a loan (or investment), it is sometimes difficult to determine its true value or profitability. There are different terms that are used to describe rates or profitability. For example, we can talk about annual percentage yield, effective and nominal rate, etc
Decreasing depreciation balance method: example, calculation formula, pros and cons
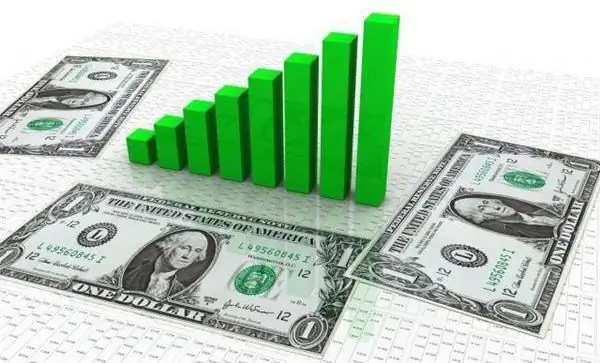
Depreciation charges are one of the most important accounting processes in an enterprise. Depreciation, one way or another, is charged by all enterprises, regardless of the taxation system that they use