2025 Author: Howard Calhoun | [email protected]. Last modified: 2025-01-24 13:10
Granular blast-furnace slag is a waste of metallurgical production. To be more precise, this is the raw material that remains after the smelting of pig iron in blast furnaces.
What is slag and where does it come from?
In order to produce raw materials such as pig iron, certain raw materials must be loaded into the blast furnace. Such materials were iron ore, flux stone, coke. At the exit from the furnace, only two substances are obtained - this is pig iron and slag. The composition of blast-furnace slag includes substances such as quartz, aluminum oxides (processing from iron ore), calcium and magnesium oxides (waste from flux stones). The molten slag obtained at the outlet of the blast-furnace unit can have a temperature of 1500 degrees Celsius, and in some cases even more. Naturally, cooling of the material is required. Currently, the plants use only 4 main types of blast-furnace slag processing.
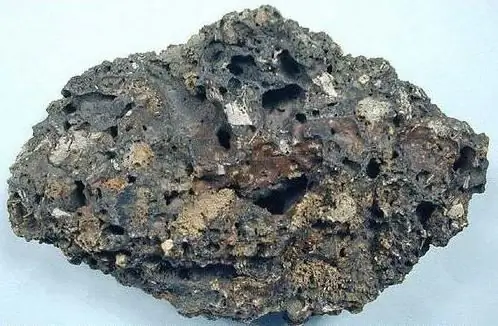
- The first method involves cooling the raw material with ordinary cold water. This operation is also called slag swelling.
- The second method uses coolingsubstances with the help of air.
- The third way is crushing.
- Fourth - grinding.
Main material components and processing results
It is important to note here that the choice of the method of processing blast-furnace slag will determine what kind of substance will be obtained in the end, and what properties it will have. Each method imparts unique qualities to the raw material. Another important observation is that the main oxides that are part of the slag - oxides of magnesium, calcium and aluminum, do not occur in nature in a free form. In other words, they do not exist, and they can only be obtained by processing slag and iron ore in a blast furnace. In addition to the main oxides, the composition of the substance includes manganese, iron and sulfur compounds, quartz.
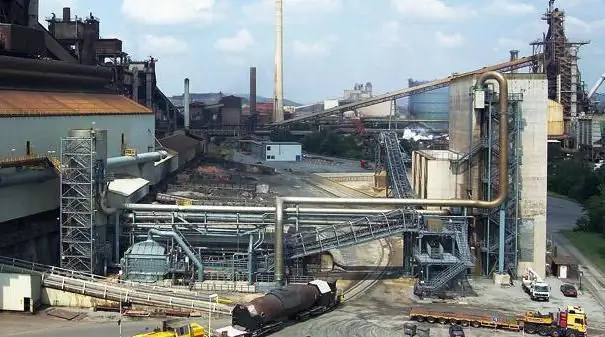
For example, if you resort to cooling the spent material with air, then the composition of the blast furnace slag will be approximately the following: silicates and aluminosilicate materials such as wolastonite, melilite and merwinite.
How is the granulation process?
The process of granulation of a substance is carried out by the method of rapid cooling of the molten raw materials. It is important to add here that in some cases a mechanical crushing process may be added, either still liquid slag, or already half-solidified. The main purpose of this operation is to process large pieces of material into smaller grains that will be more convenient to process in the future, as well as to improve such quality as hydraulic activity. ita very important operation, since this property is the most important, since slag can be used as a constituent component for slag cements, and can also act as an additive to Portland cement.
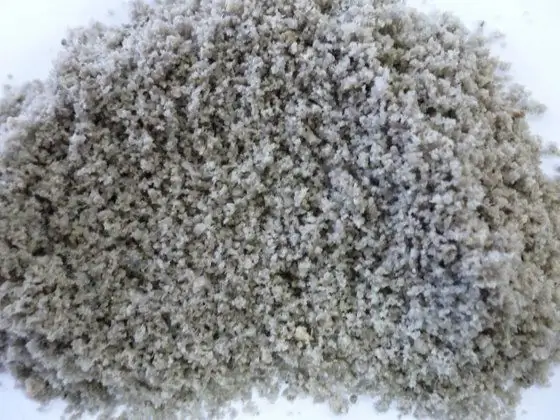
You need to understand that there is no special production of blast-furnace slag as such. It is obtained only by processing ore and other substances in a blast furnace.
Methods of granulation
You need to know that for the granulation of production waste, that is, slag, there are several methods, as well as devices that carry out this operation. Depending on what moisture content of the slag is obtained in the end, the installations are divided into types. There are units for wet and semi-dry granulation.

If the method of wet granulation is carried out, then the slag loaded into the slag buckets in hot form is fed to reinforced concrete pools filled with water. After that, from the buckets it merges into these pools through special gutters. A slight advantage of the method is that the pools are divided into several sections. This allows the cooling process to be carried out almost continuously. When the red-hot substance merges into one section, the already cooled blast-furnace slag can be unloaded from the other at the same time. For the shipment of raw materials, the factories have clamshell cranes that deliver it directly to open-type railway cars. After that, the slag is delivered either to the warehouse or directly to the consumer.
Contentmoisture
It is worth noting here that the moisture content of the material depends on the total weight of the blast furnace slag that goes through the granulation process. In other words, the more porous the structure of the grains, the more moisture remains in them. The formation of pores in the solidified granular slag occurs due to the action of gases. These volatile substances are contained in the molten raw material and begin to evaporate when the temperature of the slag decreases, that is, when it is cooled. However, it is important to note here that the cooling and solidification of the material occurs so quickly that the gas does not have time to evaporate from the slag. It remains inside in the form of small bubbles, which create the porous structure of the grains. Porosity, and because of this, the moisture content of the slag also directly depend on the conditions that are used directly in the process of cooling the slag. That is, not only the final result, but also the structure itself depends on the choice of method.
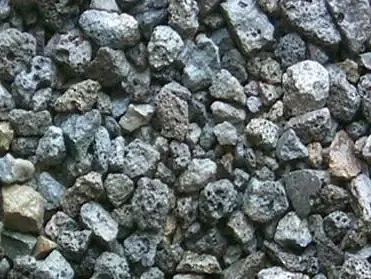
Semi-dry method
Semi-dry slag is obtained by using the method of mechanical crushing, as well as throwing into the air pre-cooled, but at the same time not yet solidified slag. Thus, the structure of the material turns out to be much denser, which significantly increases the physical weight by about one and a half times, compared with the weight that the slag would have if it passed through wet granulation, having the same initial amount of substance. If we talk about such a characteristic as humidity, then for wet raw materials this value is in the range from 15 to 35%, quiterarely 10%. While dry granulation is accompanied by slag moisture ranging from 5 to 10%. If we compare the volumetric weight, then with a wet method of processing it will be in the range from 400 to 1000 kg / m, and with a dry one - in the range from 600 to 1300 kg / m. Here it is worth adding that with an increase in the temperature of blast-furnace melting, the final weight of blast-furnace slag will decrease.
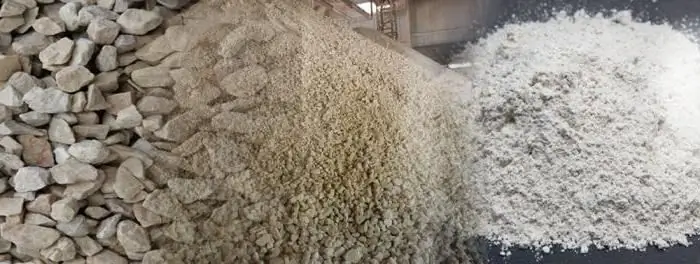
It is important to add that most factories use wet granulation, despite the fact that the method has several disadvantages:
- High fuel consumption for drying the material before it breaks.
- The productivity of slag drying equipment is low.
- Freezing of wet slag in wagons, warehouses and other storage areas in winter.
Blast furnace slag GOST 3476-74
This standard describes all technical requirements, test methods and acceptance rules, as well as methods for storing and transporting blast furnace slag. One of the points of the state document concerns the moisture content of raw materials. It is said that the percentage of humidity must correspond to that which was agreed upon by the customer and supplier. In other words, it can be said that the customer chooses the material granulation method.
Recommended:
Modern production. The structure of modern production. Problems of modern production

Developed industry and a high level of the country's economy are key factors influencing the we alth and well-being of its population. Such a state has great economic opportunities and potential. A significant component of the economy of many countries is the production
Bronze is an alloy composition. The chemical composition of bronze
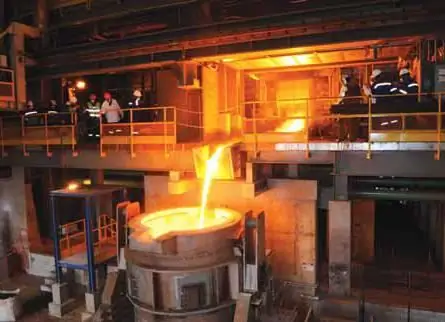
Many people know about bronze only that sculptures and monuments are cast from it. In fact, this metal is undeservedly deprived of popular attention. After all, it was not in vain that in the history of mankind there was even a Bronze Age - a whole era during which the alloy occupied a dominant position. The qualities possessed by an alloy of copper and tin are simply indispensable in many industries. It is used in the manufacture of tools, in mechanical engineering, casting church bells, and so on
Gas production. Gas production methods. Gas production in Russia
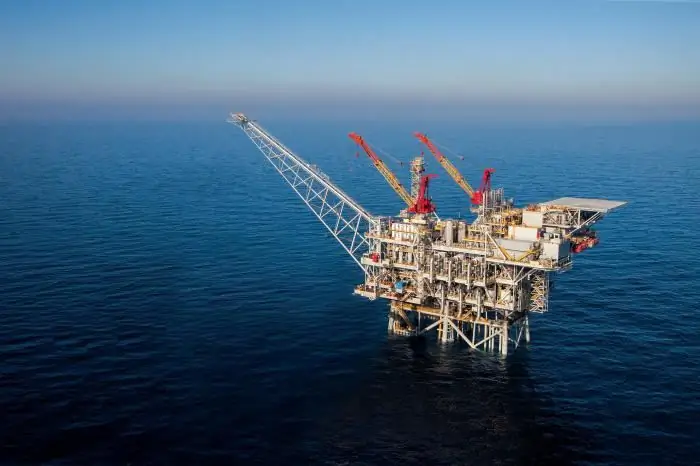
Natural gas is formed by mixing various gases in the earth's crust. In most cases, the depth of occurrence ranges from several hundred meters to a couple of kilometers. It is worth noting that gas can form at high temperatures and pressures. In this case, there is no access of oxygen to the place. To date, gas production has been implemented in several ways, each of which we will consider in this article. But let's talk about everything in order
Beet pulp granulated: production, application, composition
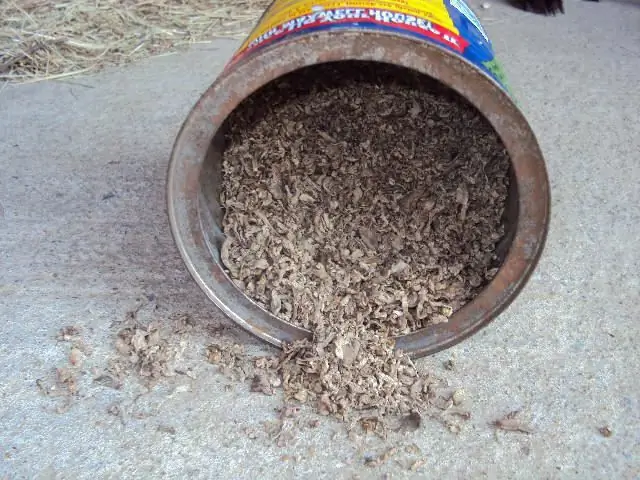
Beet pulp is a valuable feed product containing a large amount of carbohydrates. It is sold mainly in granules
Density of crushed stone - gravel, granite, limestone and slag. Bulk density of crushed stone: coefficient, GOST and definition
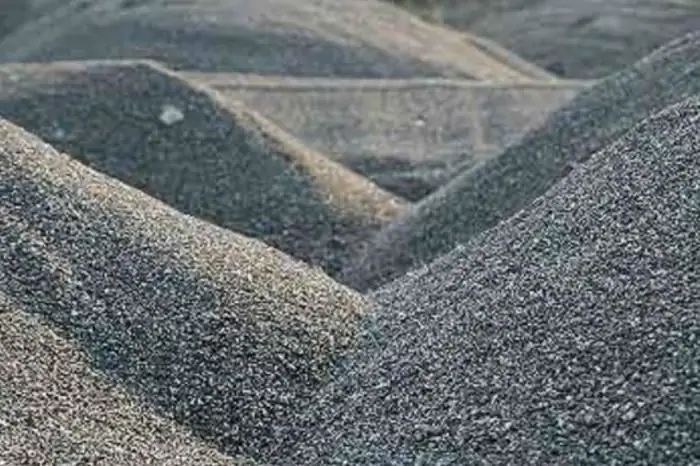
Crushed stone is a free-flowing, inorganic and granular material obtained by artificial crushing. It is divided into primary and secondary. This is an important fact. Primary - the result of processing natural stone: pebbles, boulders, pumice and other materials. Secondary is obtained by crushing construction waste, such as concrete, asph alt, brick. In this text, we will consider in more detail such a property as the density of crushed stone