2025 Author: Howard Calhoun | [email protected]. Last modified: 2025-01-24 13:10
The process of oil production involves the use of special deep-seated equipment, which is based on the so-called pumping units. This is a type of surface drive mechanism that is controlled by operators during the operation of wells. As a rule, an oil pump is based on the operation of plunger pumps that provide the function of the production infrastructure.
Destination of oil pumps
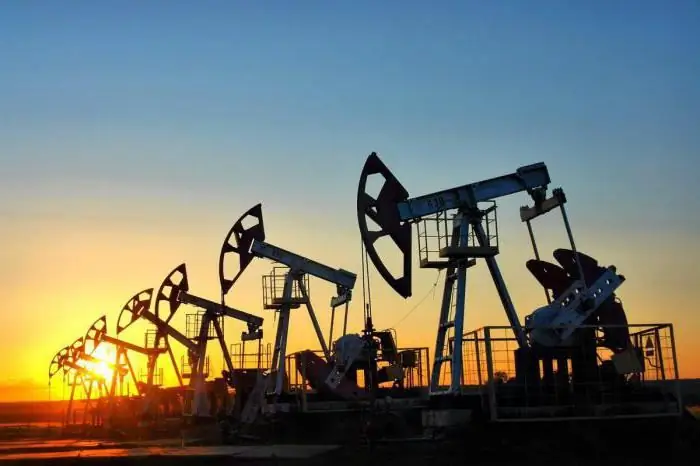
The most common rod pump drive is designed for pile mining. With the help of this unit, users develop wells in permafrost conditions. Oil and gas equipment in the form of rocking chairs with one-arm balancers is also popular. Such machines are used as an individual drive in oil production.
In essence, any oil-producing infrastructure is focused on the implementation of raising the resource. The general principle of operation of the equipment can be compared with the function of the syringe, which in this case is provided by rod pumps. Also, as an obligatory element, the oil rocker is equipped with columns of compression pipes. Through these channels, the rise and transfer of oil is realized.
Process of oil productionrocking chair
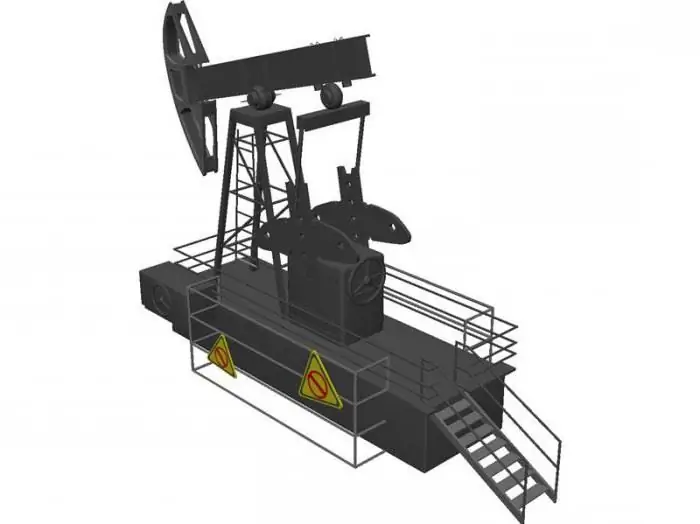
Technological organization of the mining process is divided into several stages. Work begins with drilling a well, the depth of which can reach several kilometers. As a rule, 1500-meter holes are developed, and wells of 4000 m are the record holders. Further, casing strings are installed, which become the basis of the oil production infrastructure. The activator in this system will be the pump. To understand the principle of its operation, one should understand how the oil pump works in the general structure of the pipeline. It performs the function of a drive mechanism, due to which reciprocating actions are performed. Pumps operate in a cyclic manner, allowing oil to concentrate around the well for efficient pumping. In addition, this maintenance principle minimizes wear and tear on machine parts.
Oil pumping unit
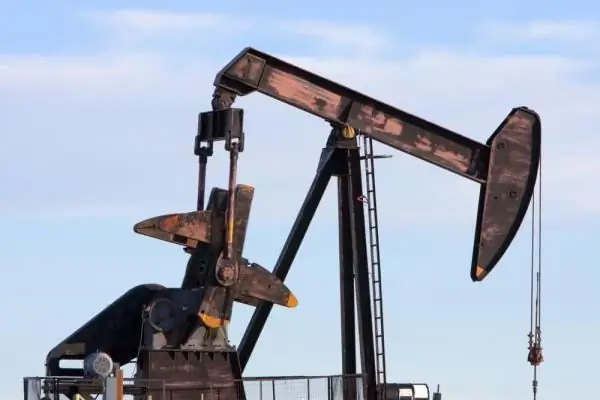
The machine is mounted on a special concrete base in the form of a foundation. There is also a rack, platform and control station for the operator. After completion of work on the organization of the platform, a balancer is placed, balanced by a special head, to which a rope suspension is also connected. To ensure the force impact, the oil rocker is equipped with a gearbox and an electric motor. The latter can be located under the platform, but due to the high risk of operating this configuration, this placement is extremely rare.
Regardinggearbox, then it is connected to the balancer by means of a crank mechanism. This bundle is designed to convert the rotational action of the shaft into a reciprocating function. The task of the control station is also noteworthy. As a rule, its basis is formed by a box complex with electrical stuffing. A manual mechanical brake is also installed next to the control relay.
Varieties
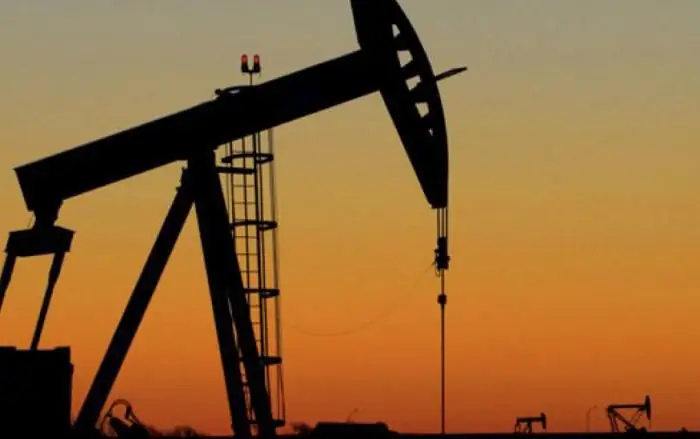
Despite the similar principle of working with the oil resource, different modifications are presented in the family of pumping units. As already noted, the most popular is the classic balanced machine, which provides for rear fixation of the connecting rod, as well as a gearbox connected to the frame with a balancer. But there is an alternative to this equipment. This is a hydraulic rod pump, which is mounted on the upper flange of the borehole fittings. Its features and advantages include the elimination of the need to install a foundation pillow. This difference is of great importance when it comes to the development of wells in permafrost zones. There are other features of hydraulic installations. In particular, they involve the implementation of stepless length adjustment, which makes it possible to select the operating modes of the equipment with greater accuracy.
Characteristics of pumping units
Technologists analyze a wide range of technical and operational parameters that give grounds for choosing one or another machine. In particular, the load on the rod, stroke length, dimensionsgearbox, torque, swing frequency range, etc.
One of the main characteristics of pumping units is the power of the electric motor. So, typical oil pumps cope with their functions, provided that a force of 20-25 kW is applied. A deeper analysis of the parameters also takes into account the type of belt, pulley diameters and features of the brake system. At the same time, in addition to operational operating capabilities, one should also keep in mind the overall parameters that make it possible to fundamentally install a particular machine in certain conditions. Again, a typical installation can be 7 m long and 2-2.5 m wide. Weight usually exceeds 10 tons.
How is an oil pump serviced?
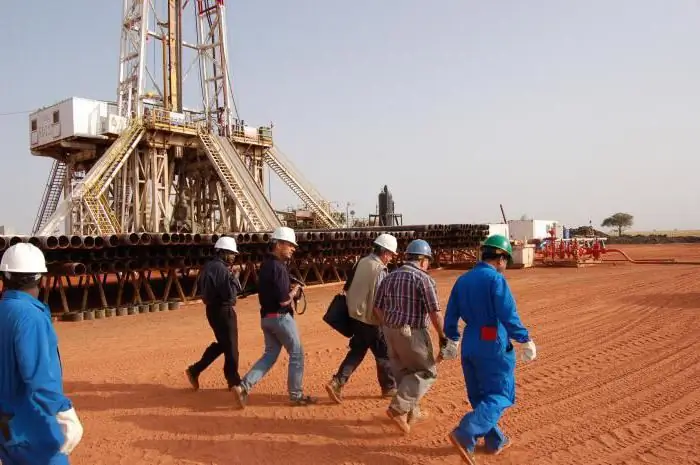
To work with pumping units, designers provide special mechanisms. For example, to service a traverse with a balancer, a special platform with drive systems is mounted. Operators can control the parameters of a detachable balancing head support integrated into the machine body. The kinematics of the drive system ensures optimal movement of the head and can be adjusted for a fast downward movement if necessary. At the same time, it is important to separate directly the functions of operators and personnel who technically service oil pumps during operation. If the former are engaged in the regulation of the rise of oil, then the latter monitor the performance of the mechanisms in terms of maintaining their function within the tolerance of peak loads.
Conclusion
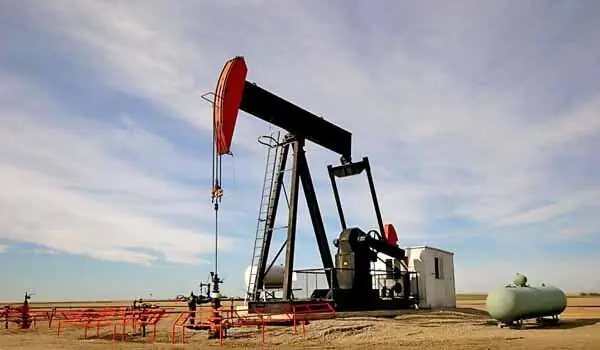
Manufacturers of pumping units regularly offer new technological solutions to ensure the oil production process, but there is no need to talk about serious revisions of existing concepts yet. The fact is that oil and gas equipment is expensive and many customers are reluctant to change the existing fleet of equipment. Nevertheless, a partial update of significantly outdated components still occurs. There is also a trend of transition from balancing machines to more advanced hydraulic ones. This is due precisely to the desire to optimize the operation of the existing infrastructure. As a result, oil companies reduce the cost of organizing and operating equipment, but at the same time do not lower the quality of the target product.
Recommended:
Review of the gas mask GP-21: device, variations, equipment
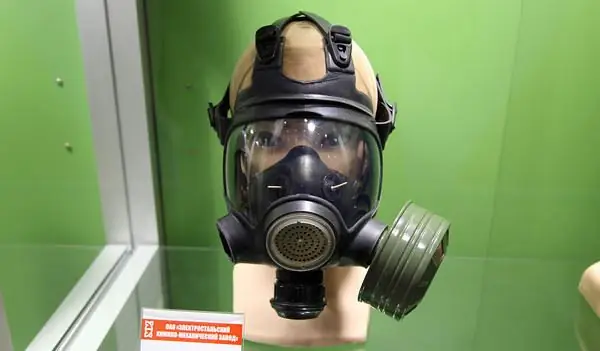
Purchasing personal protective equipment is an extremely important undertaking. The choice of a low-quality gas mask can lead to disastrous consequences for its owner. Therefore, this article contains all the most important information about the GP-21 gas mask. Familiarization with it is guaranteed to save you from making mistakes when choosing
Laying a gas pipeline: methods, equipment, requirements. Gas pipeline security zone
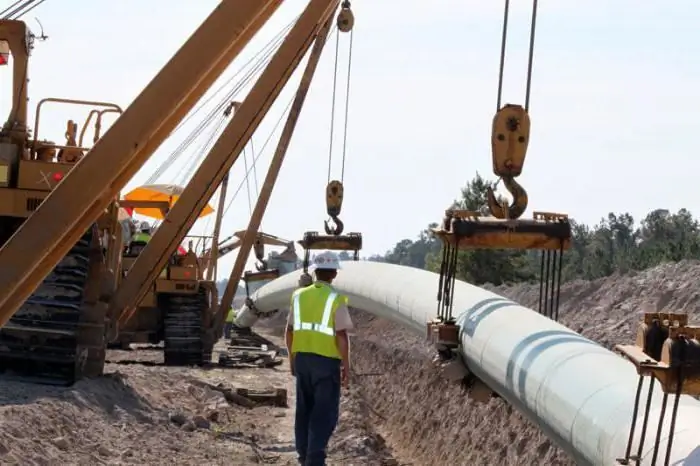
Laying of the gas pipeline can be done by underground and ground methods. When choosing equipment for such systems, safety standards should be followed. Actually, the laying of highways is carried out with strict observance of all the required technologies
Equipment for agriculture: classification and types, purpose and application
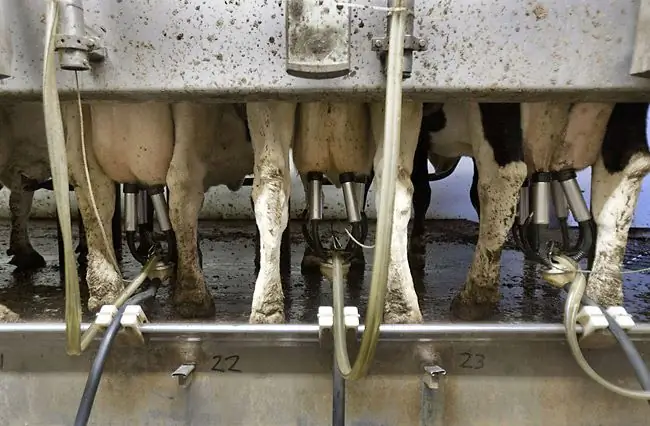
Modern industry produces a variety of equipment for agriculture. It can be, for example, soil-cultivating equipment, as well as fodder, harvesting or sowing. Of course, tractors are also widely used on farms
Gas drying: definition, characteristics, methods and types of work, application of installation and special equipment
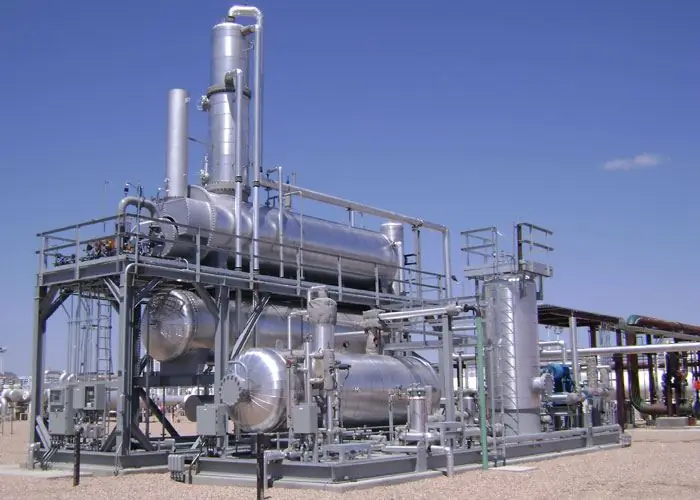
Gas drying is one of the cleaning methods that helps to get rid of moisture inside the pipeline. Its appearance is quite dangerous, as it causes corrosion of the metal. In addition, since mining is also carried out in conditions of low temperatures, ice formation is possible
Why does the ruble depend on oil and not on gas or gold? Why does the ruble exchange rate depend on the price of oil, but the dollar exchange rate does not?
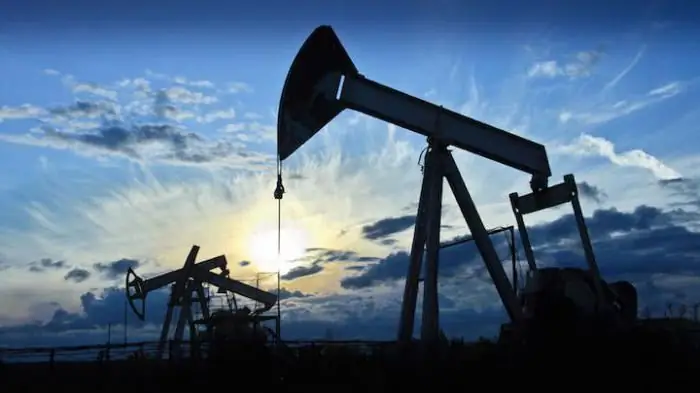
Many in our country are wondering why the ruble depends on oil. Why is it that if the price of black gold decreases, the price of imported goods rises, is it more difficult to get out to rest abroad? At the same time, the national currency becomes less valuable, and with it, all savings