2025 Author: Howard Calhoun | [email protected]. Last modified: 2025-01-24 13:10
Many moving mechanisms are designed in such a way that the transfer of energy directly from the driving device to the executive body is impossible. In some situations, the motor and the driven device are structurally spaced far apart and offset from each other. In other cases, the energy must first be converted: reduce or increase the engine speed, change the direction of rotation, or turn the rotational movement into translational.
Then some intermediate mechanisms are required to transfer or transform this energy. One of the main elements used for this purpose is gear wheels. They are used wherever significant power transmission is required while maintaining a compact device and a long service life - whether it is a car gearbox, a fishing rod reel or a hydroelectric turbine.
What are the transfers
There are many varieties of gears. They are classified according to the following criteria:
- direction of motion transmission - cylindrical, worm,conical;
- side of the wheel on which the teeth are cut - internal or external gearing;
- teeth direction - straight, oblique, chevron;
- shape of teeth - cycloid and involute gear, Novikov engagement.
Cycloid gearing
This technology was patented in 1931 by German engineer Lorenz Braren. Unfortunately, it has significant drawbacks.
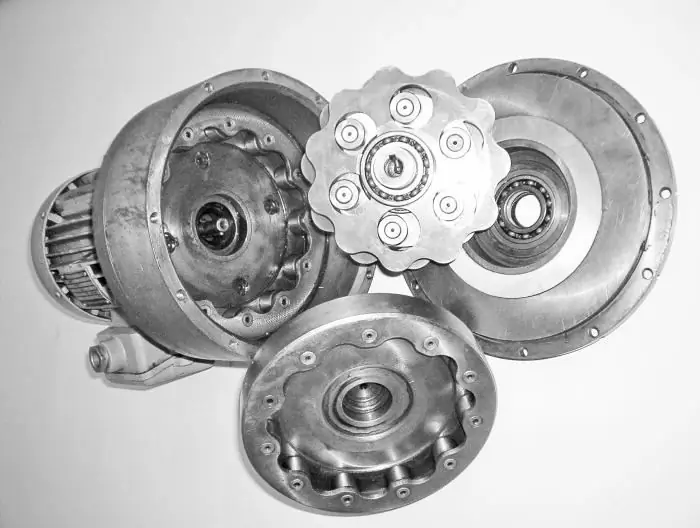
- Difficult to manufacture - each wheel is cut with a separate gear cutting tool.
- Extremely high sensitivity to changes in center distance. In other words, this type of engagement requires the highest precision in production and installation, and in the event of the slightest mechanical damage, it fails.
- Difficulties in repair due to the lack of standardization of such engagements.
The advantage of this gear is that the stress at the point of contact of the teeth is greatly reduced due to their rounded shape, resulting in greater durability of the parts.
As a result, the cycloidal connection has found its application in a rather narrow area of industry - in the manufacture of watches and other precision instruments, some types of compressors and pumps.
Involute type
This type of tooth design was proposed by the famous mechanic and mathematician Leonhard Euler in 1760 and is the most widely used in industry.
In a gear pair, a part with a smaller diameter is usually called a gear, and a part with a large one is called a wheel. ATinvolute connection, the teeth have a profile with convex edges. It is the same for both gear and wheel. From this follows the main economic benefit of involute gearing: low complexity of manufacturing parts while maintaining sufficient accuracy and, accordingly, high productivity. These wheels do not require complex equipment to manufacture, and their quality is easy to control.
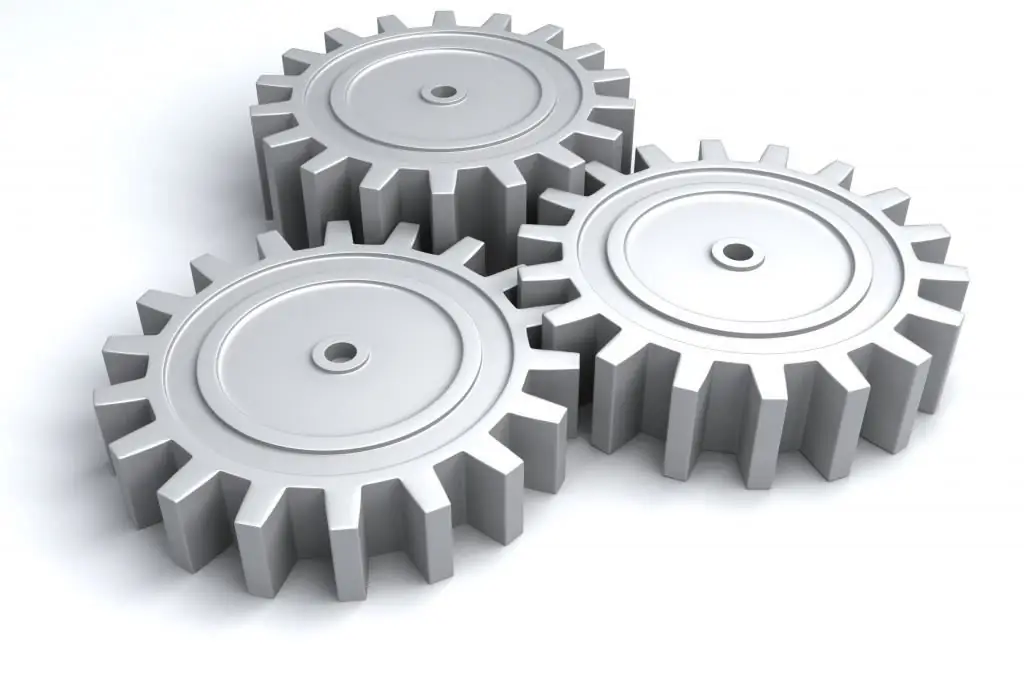
This connection has another indisputable advantage associated with the presence of a human factor in production: involute teeth are insensitive to changes in the center distance, if their engagement is not interrupted. Simply put, such wheels "allow" some inaccuracies in both manufacturing and installation without much loss in performance.
Also, involute gearing provides the gears with a long service life due to the fact that the surfaces of the teeth, which have a convex shape, roll over each other. Due to this, the friction of the surfaces is significantly reduced, that is, the wear of parts is minimized.
Creation of the Novikov transmission
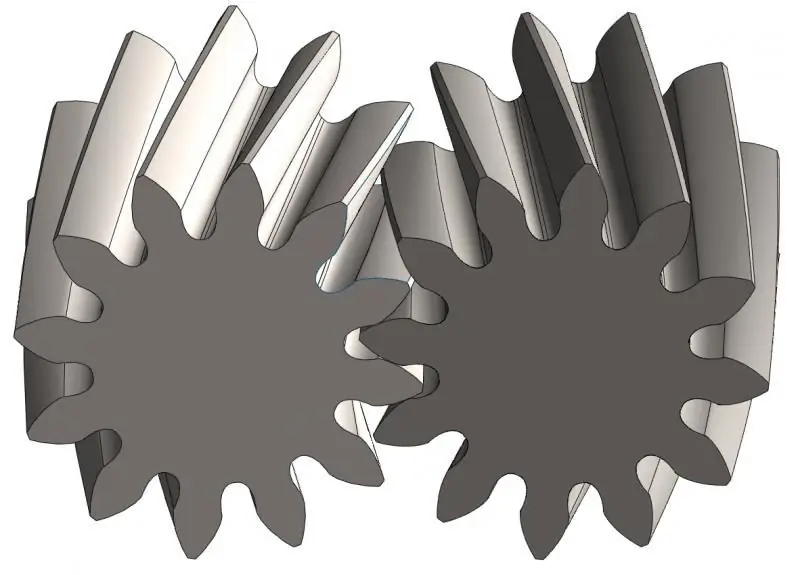
Sometimes you need to transmit a very high torque and at the same time not go beyond a certain size and weight of the mechanism. Under these conditions, the involute connection may not be reliable enough - due to high contact stresses at the point of contact of the teeth, they can quickly fail.
Here comes to the aid of the so-called circular screwengagement. It was developed in 1954 by the Soviet engineer and inventor M. L. Novikov. He came to this decision by researching the problems that arose in the design of heavy but relatively slow machines such as tractors and tanks.
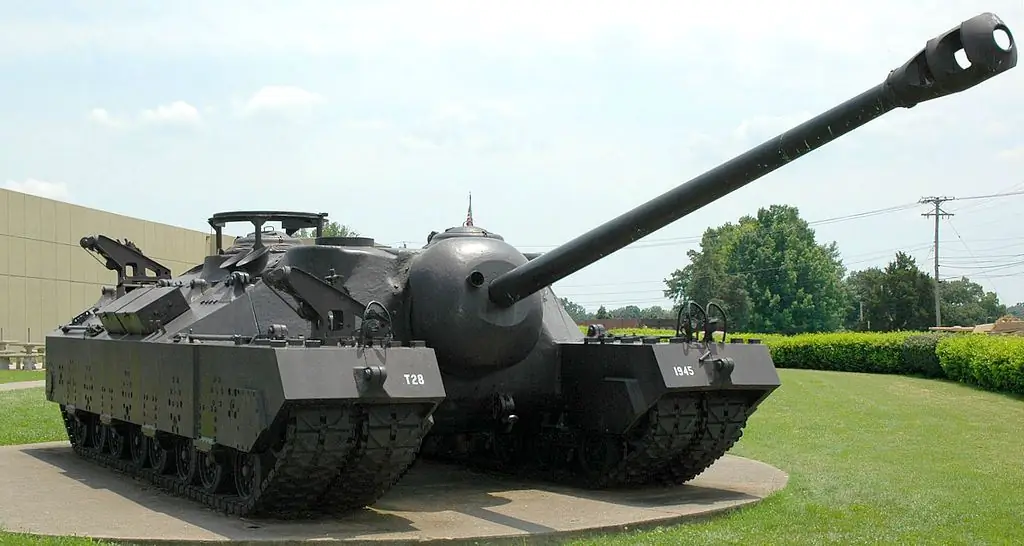
This technique has a large mass, which requires the transfer of the appropriate torque from the engine through the transmission to the wheels or track rollers. Involute teeth are not always up to the task.
What are the benefits of opening…
A connection has been created in which the teeth of the gear and wheel are convex and concave respectively. Due to this, a significant increase in the contact surface of the teeth was achieved, since the gear teeth and the depressions between them at the wheel have very close radii.
Thus, the voltage at the point of contact was reduced. This made it possible, depending on the specific circumstances, either to significantly reduce the size of the mechanism while maintaining the value of the transmitted power, or, while maintaining the existing dimensions and weight, to significantly increase the load on the connection without fear of an early breakdown.
…and its flaws
In contrast to the involute connection, where two convex surfaces touch, in Novikov gears, the convex and concave parts form an almost integral whole when connected. Because of this, the friction between the teeth increases significantly, affecting their durability. Although in the case of low-speed machines, for which initially anda circular screw connection was developed, this factor is not so important.
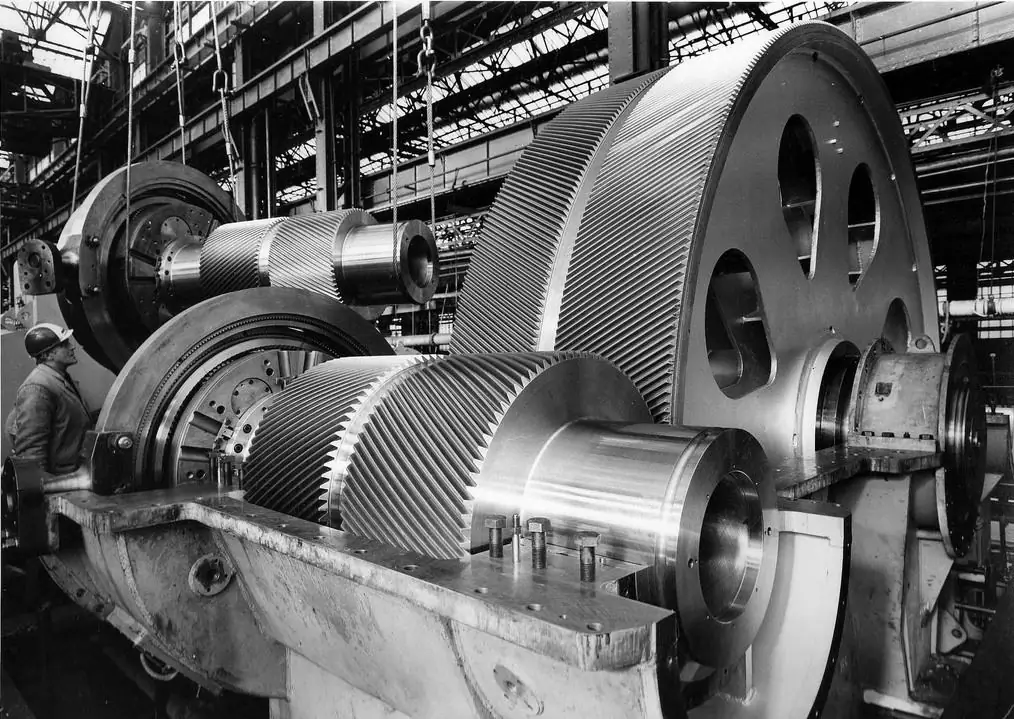
In addition, this design, similar to the cycloid gear, places high demands on the quality of workmanship and assembly care, since violation of the center distance can lead to catastrophic consequences.
Before Novikov, numerous attempts had already been made to improve the design of the engagement, but only he managed to develop a viable technology. After some improvements, it was introduced into many industries.
Improving the invention
There are two types of Novikov links in total:
- with one touch line (can be prepolar and polar);
- with two touch lines (dozapole).
In the first type, the teeth of the gear and wheel have the same curvature along the entire contour. With a polar connection, the profile of the drive wheel is made convex, and the driven wheel is concave. With prepolar - vice versa. This compound was directly developed by Mikhail Novikov, who received the Lenin Prize for this.
However, it soon became clear that the manufacture of gears of this type is technologically quite difficult. Since the wheels are not the same, but have different tooth cuts, two different pieces of equipment are required to make a pair of wheels, which is not very economical.
Research in this direction has begun. Their result was the development of dozapoleny gearing, in which the teeth of the wheel and gear are the same,but they have a convex contour closer to the top and a concave closer to the base, with a smooth transition between them. This not only achieved the unification of the production of parts, but it was also found out that such gears have a much greater load-bearing capacity than connections with one line of engagement.
Distribution of new development
Being originally developed for heavy, including military equipment, Mikhail Novikov's gearing scheme began to spread rapidly across many industries. The Lugansk Machine-Building Plant in Ukraine was the first in the territory of the former Soviet Union to manufacture products using the new technology.
others.
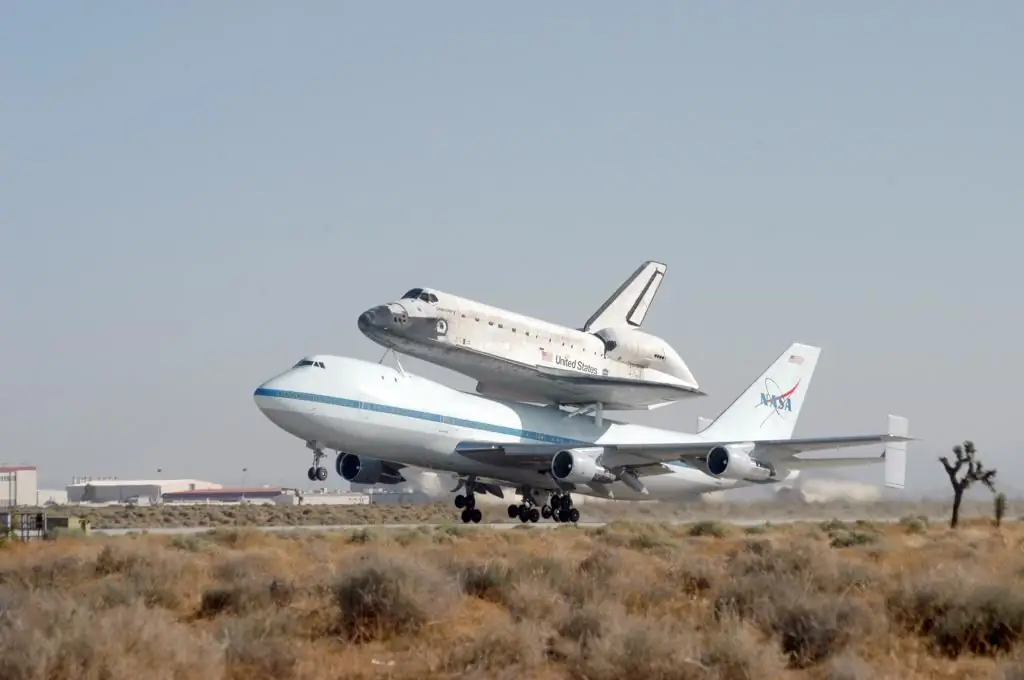
Foreign countries are also actively interested in this development. Japan is developing for its implementation in the automotive industry, and England and the United States are also not left out. The invention of a Soviet scientist may well go to conquer the Universe: international organizations are funding research on the application of the Novikov gear in space shuttles, probes and other equipment.
Spheres of use of rotary screw technology
For the most part, this development has been implemented in the following areas:
- traction gears of various heavy vehicles - trolleybuses, buses, trams, helicopters);
- pumping units and other oil industry equipment;
- coal mining machinery;
- hoist and travel crane gearboxes.
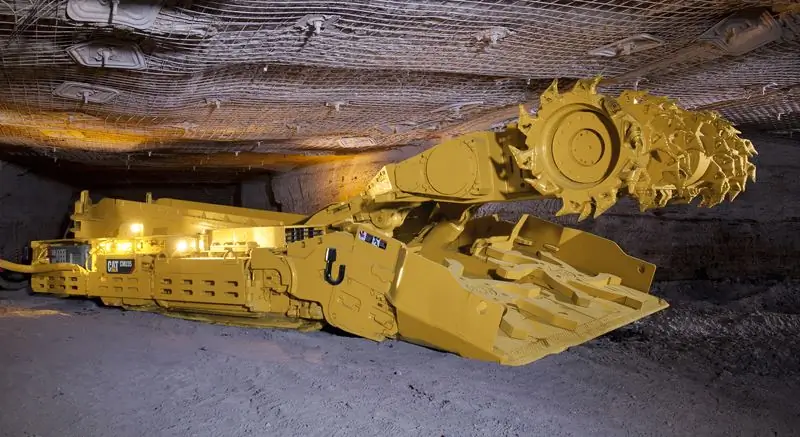
There are also special bearings made using Novikov gears that have three times the load capacity of conventional bearings.
Production of Novikov gears and regulatory documents
Special equipment was developed for cutting teeth in the manufacture of Novikov's engagement - a milling cutter. This tool has a rather high cost, since high requirements are applied to the accuracy of the manufacture of gears. A slight deviation - and that ideal harmony of the contact contours, which ensures a high gear life and transmitted power, will no longer be observed.
Since the quality of both the teeth themselves and the cutters for cutting them are subject to particularly high requirements, separate state standards have been developed to control their manufacture. For the Novikov engagement itself - GOST 17744-72, for gear-cutting tools - GOST 16771-81.
The new principle of manufacturing teeth, developed by M. L. Novikov, was recognized not only in the territory of the former USSR, but also in many other countries.
Recommended:
SRO approval in design. Self-regulatory organization in the field of architectural and construction design. Non-Profit Organizations
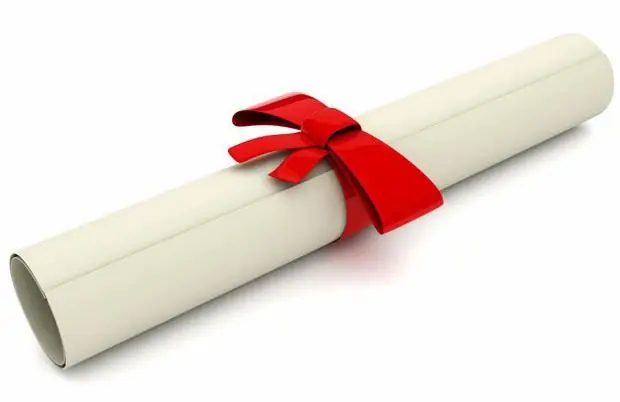
Specialists in various fields, start-up and existing entrepreneurs, as well as civil servants will definitely face such a definition as SRO. What is it and how is it related to construction and design? You can find out more in this article
The gear wheel is an indispensable part of the machine

One of the most common and rational ways to transmit and convert movement is still a gear or worm gear, the main element of which is a gear
Aircraft landing gear: from the Wright brothers' Flyer to Ruslan
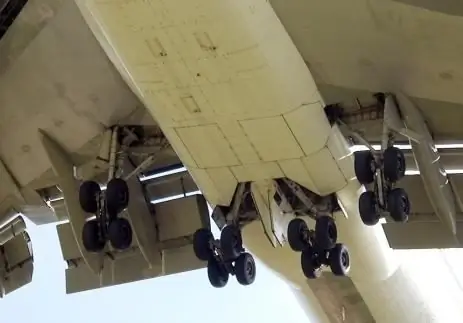
In terms of its diversity, few structural elements can compare with the landing gear of an aircraft. The scheme, which has received the greatest distribution in modern aircraft industry, is tricycle. It involves two main racks and one auxiliary (most often - bow, taking on up to 9% of the weight of the aircraft)
Gear shaping machines: description, characteristics, types and mode of operation
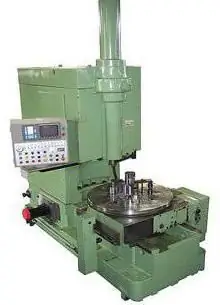
Gear shaping machines: specifications, settings, operation, features, purpose. Gear shaping machines: description, principle of operation, photo
Gear coupling: scope and features
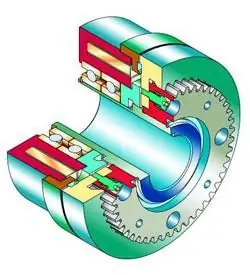
Most mechanisms, turbines, conveyors would not be able to work if they did not use such a small but very necessary part as a gear coupling. Let us consider in more detail the scope and features of gear couplings