2025 Author: Howard Calhoun | [email protected]. Last modified: 2025-01-24 13:10
Transportation of goods is the basis of production processes in warehouses of various types. Lifting and moving operations are less and less carried out manually and require the use of specialized equipment. At the current stage of development of the technical support of the warehouse, automatic components and assemblies are considered the most effective solution for this type of transportation problems. Another thing is that the implementation of this automation may have different structural forms and functional content.
What equipment is used for automation?
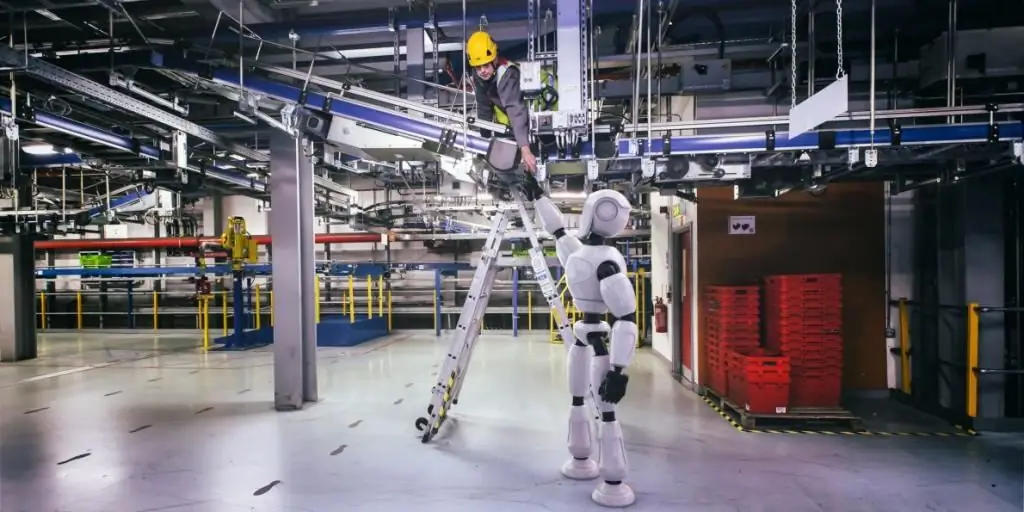
The whole working infrastructure can be defined by three functional groups:
- Stationary immovable devices and structures. These are traditional containers and other components of warehouse support that perform the immediate task of containing the target product. In particular, the mosta common unit of this type is a shelf or rack.
- Automation as such is provided by drive mechanisms. These are motors connected to control controllers on the one hand, and mechanically connected to manipulators and other executive bodies on the other. As a rule, the operation of automatic warehouses and their equipment is supported by electric motors, but in the presence of an effective forced-exhaust system, the use of gasoline engines is also allowed. Although trends still show an increase in demand for compact storage batteries and industrial batteries, which, together with automation, comprehensively provide warehouse engineering functions.
- Executive devices. A wide range of technical means and mechanisms that directly perform the operations of loading and unloading, lifting and transporting goods. These can be stacker cranes, chain conveyors, overhead manipulators, conveyor belts, etc.
Design of automatic warehouses
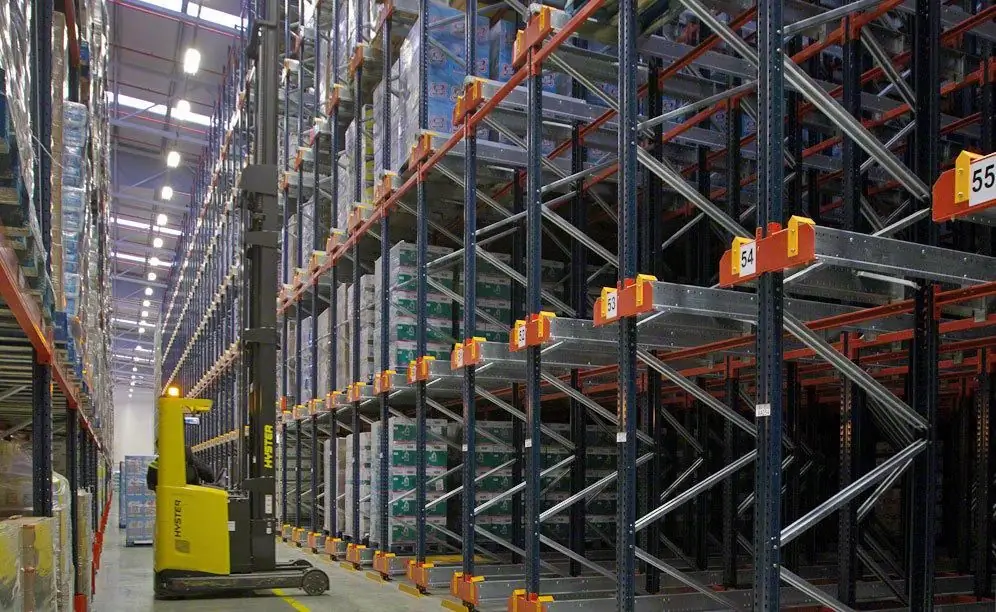
Design is carried out in several stages, taking into account a large array of input data. First of all, a scheme of cargo flow logistics is determined, which will have to work within a specific warehouse area. By modeling, designers build a dynamic scheme for the movement of goods with working points for loading, unloading and lifting. For the transport network, the contours of the movement of flows with the technical infrastructure are calculated - the parameters of the rails are determined,conveyors, suspension systems, etc. At the design stage, each executive body of an automated warehouse system receives its own specification indicating the required performance characteristics. It is mandatory to take into account the carrying capacity, gripping method, material of manufacture, wear resistance and other qualities of the equipment. On the basis of the functional scheme, the final design part is being developed with the distribution of places for optimal storage of goods in terms of ensuring their safety and ease of physical manipulations.
Elevator systems
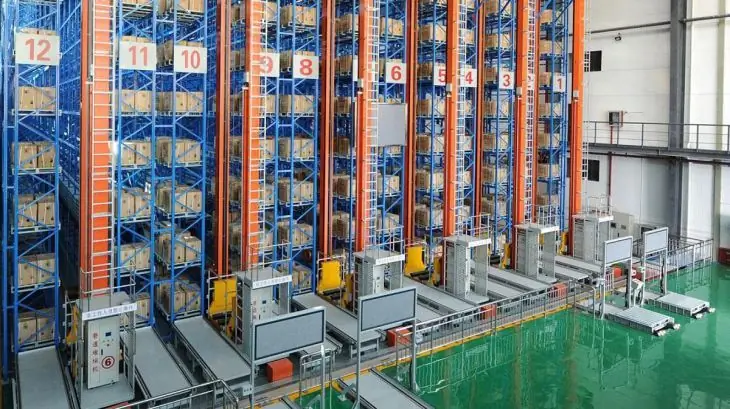
In the conditions of keeping bulky goods in high-rise industrial areas, it is advisable to use an elevator configuration for arranging an automated complex. These are vertical storage mechanisms on pallets that move along certain contours between technological storage points. Moreover, modern elevator designs are flexible in installation. They are built on prefabricated modules that allow a wide range of height extensions. Interaction with goods in an automatic warehouse of this type is carried out by a manipulator-extractor with a given program of movement between the shelves. The device moves on rollers with certain speed settings. To ensure the accuracy of manipulations, the mechanism is also equipped with special sensors for monitoring the position of the load, which interact in real time with response sensors in free places.cargo content.
Carousels
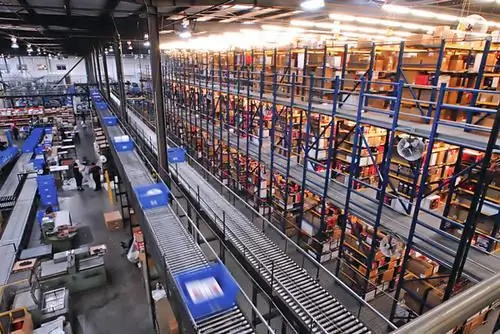
Such systems are also called elevator systems. They are used in commercial warehouses to hold a variety of products. However, designers recommend in advance to determine the dimensions of the shelves in terms of length, depth and height as accurately as possible. This will optimize space when managing multifunctional shelving. The basis of the automated storage systems of the elevator type are shelves connected by chains. They also move along closed rails due to the force of the electric motor. But unlike elevator systems, carousel systems can be not only vertical, but also horizontal. In the second case, a lower load is assumed due to the lack of lifting force.
Equipment of automatic warehouse for small products
The configuration of the warehouse infrastructure designed to store small products is more focused not on power characteristics with optimized movement patterns, but on the rationality of cellular content. Also important is the principle of goods-to-person storage, according to which the service process must provide a short access time to a specific unit of goods. In its optimized form, this concept is implemented without handling the containers, which initially involves a special configuration of high-density racking and many transition areas. In terms of management, automatic small goods warehouses providepoint connection of an electronically controlled drive system to each section. Together with the physical control mechanism, in this case, a high degree of security with unauthorized access control is provided.
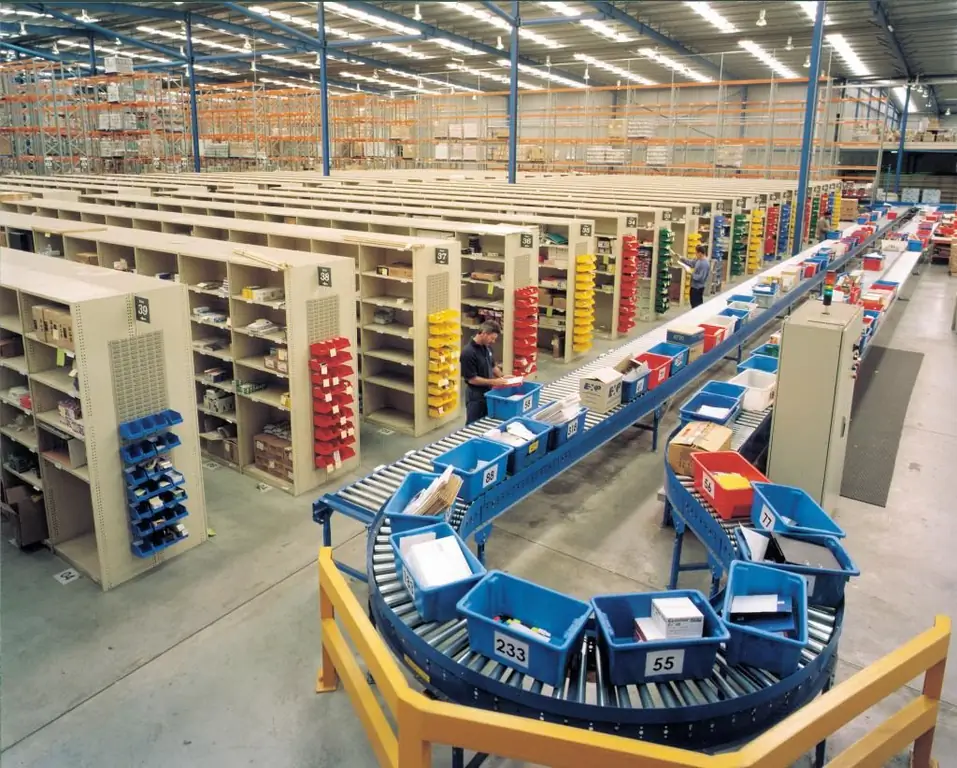
Positioning systems
Along with mechanical controllers and manipulators, devices for address positioning of "smart" racks and shelves are increasingly being introduced. The structure of such systems includes code plates, through which synchronization with the execution equipment is ensured. For example, in the coding of automatic warehouses with stacker cranes, a binary number system or Gray code is usually used, which increases the reliability of the address. General operational control is carried out through an on-board computer or a centralized dispatcher console.
Advantages of automated warehouse
The warehouse automation concept brings many benefits to the direct owner of the facility and maintenance personnel. Among its main positive properties, the following can be distinguished:
- Rational use of space. Space savings compared to traditional storage models can be up to 75%.
- Minimize picking and distribution errors.
- Possibility of integrating intelligent access control with multi-level identification according to the corresponding rights.
- Ergonomic handling. At the present level of development, warehouse automationstrives for the complete exclusion of physical contact between a person and the working environment. In the near future, such systems will be able to be controlled via wireless remote channels with digital monitoring.
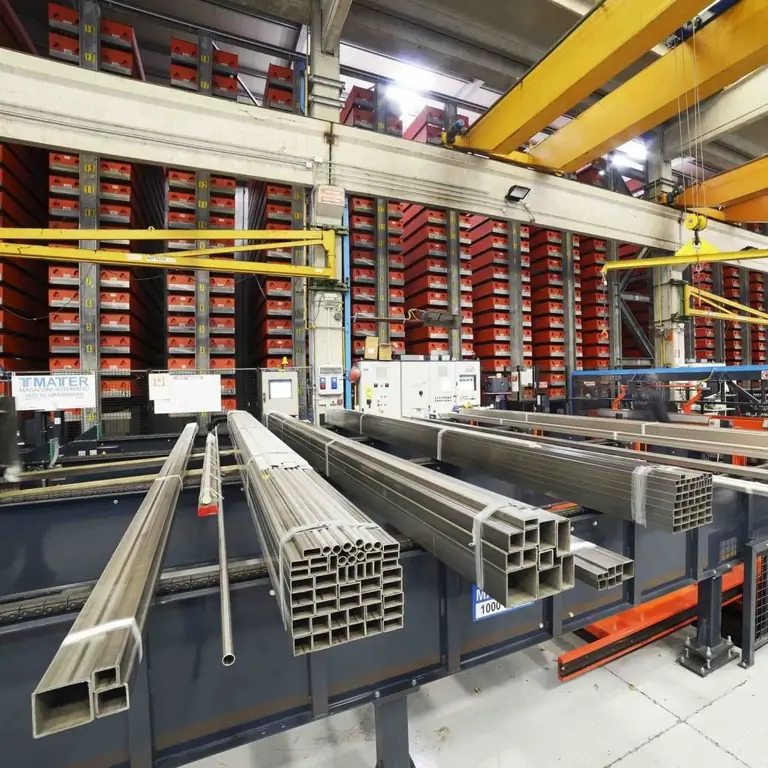
Disadvantages of an automated warehouse
Along with the advantages, there are also weaknesses in automation systems in terms of warehousing of goods. They are associated with the following nuances of application:
- High investment. Like all new technologies, the automatic warehouse system requires a lot of money at the first stage of implementation. Another thing is that in the future these investments may pay off.
- Problems of interaction with clients. Sufficient for payback efficiency of warehouse infrastructure management is possible only in cases where all logistics stages are more or less subject to the principles of automatic control. Otherwise, technological difficulties may arise with the acceptance of goods, recognition of markings and the performance of other operational processes.
- High requirements for engineering and communication infrastructure. Technologically, it is possible to provide a warehouse with automation only if there are certain engineering and structural capabilities at a particular site.
Conclusion
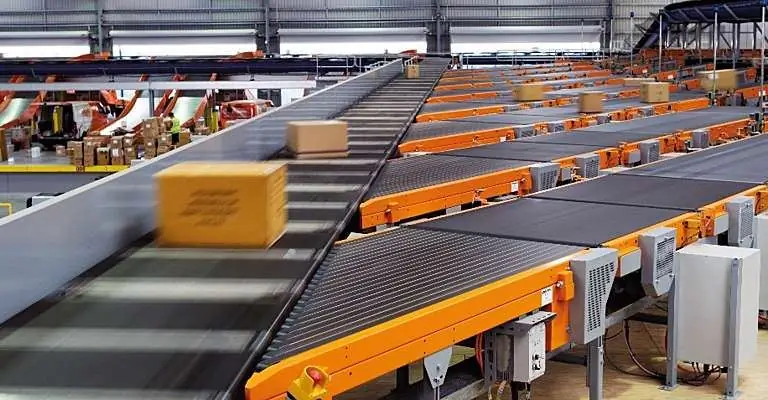
In Russian conditions, the scope of application of automated systems is constantly expanding. And although the warehouse infrastructure is traditionally considered quite conservative in terms of technological support,increasing requirements for the characteristics of logistics processes are forcing the owners to modernize such facilities as well. However, so far this applies only to large industrial enterprises and, in principle, technologically advanced areas. For example, automatic warehouses for tools and equipment for construction purposes successfully work with elevator and carousel service technologies. Small goods are even more interested in a managed automatic storage system. In particular, electronics, spare parts and other oversized but high-value goods are increasingly moving into rooms with tamper-controlled sections.
Recommended:
Production and production systems: concept, patterns and their types
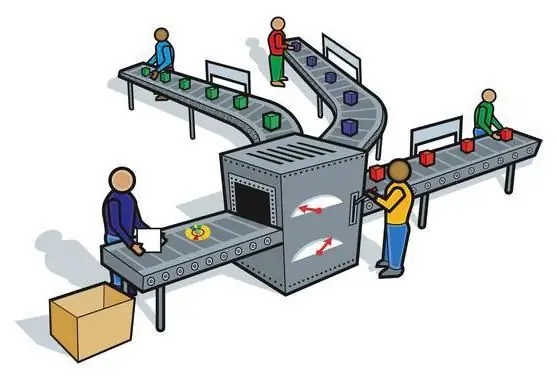
Production systems are structures that involve people and equipment working together. They perform their functions in a certain space, conditions, working environment in accordance with the tasks
Automated enterprise management systems: technologies, program and functions
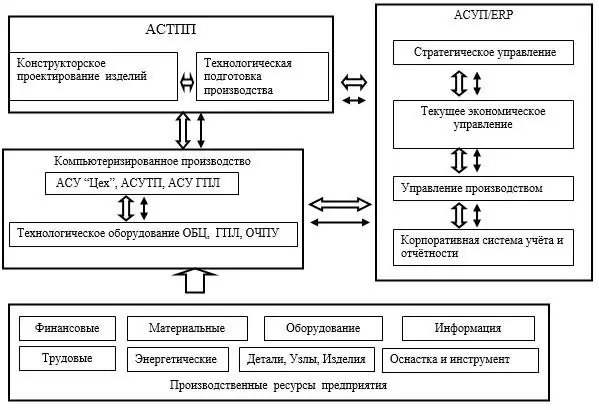
Automated enterprise control systems - this is exactly what the current industry is in dire need of. Process automation can significantly increase the productivity and efficiency of organizations. In addition, this has become relevant also because at present there is a global computerization of almost all branches of human life
Automatic lathe and its characteristics. Automatic lathe multi-spindle longitudinal turning with CNC. Manufacturing and processing of parts on automatic lathes
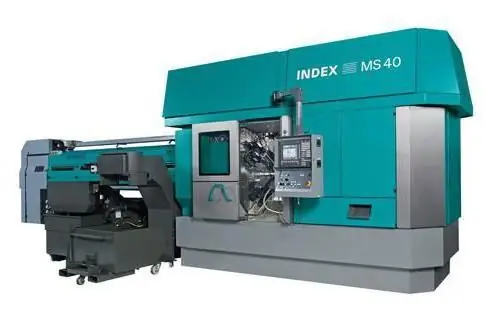
Automatic lathe is a modern equipment used mainly in mass production of parts. There are many varieties of such machines. One of the most popular types are longitudinal turning lathes
TSW - what is it? Customs warehouses and temporary storage warehouses
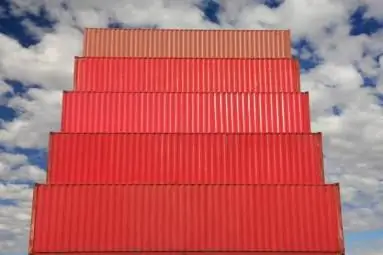
Often, the processing of the necessary customs documents may take some time. Therefore, cargoes are sometimes transferred to temporary storage warehouses. These are temporary storage warehouses, where the storage of goods has a limited period and is strictly regulated by the relevant legislation
Visa and Mastercard systems in Russia. Description of Visa and Mastercard payment systems
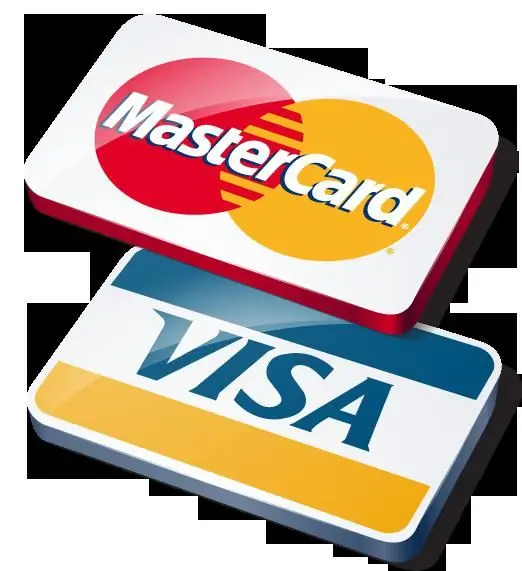
Payment system - a commonality of methods and tools used for money transfers, settlements and regulation of debt obligations between participants in economic turnover. In many countries, they differ significantly from each other due to the diverse provisions in the levels of economic development and the characteristics of banking legislation