2025 Author: Howard Calhoun | [email protected]. Last modified: 2025-01-24 13:10
The Kanban management system is a logistical methodology for organizing industrial enterprises. Ease of implementation, the ability to significantly save material resources and an increase in the overall level of control contributed to its popularity and popularity.
History of creation and development
The origin of the Kanban system is considered to be Japan, where it was first used at the Toyota Motors automobile plant in the early 60s. Development and implementation were directly related to the need to minimize financial losses through "instantaneous" inventory control and timely completion of required tasks. To date, the main area of application is industrial production, especially with continuous production cycles (automobile industry, railway transport, etc.). Given the simplicity of the algorithm embedded in the method under consideration, in recent years this is one of the most effective approaches to project management.
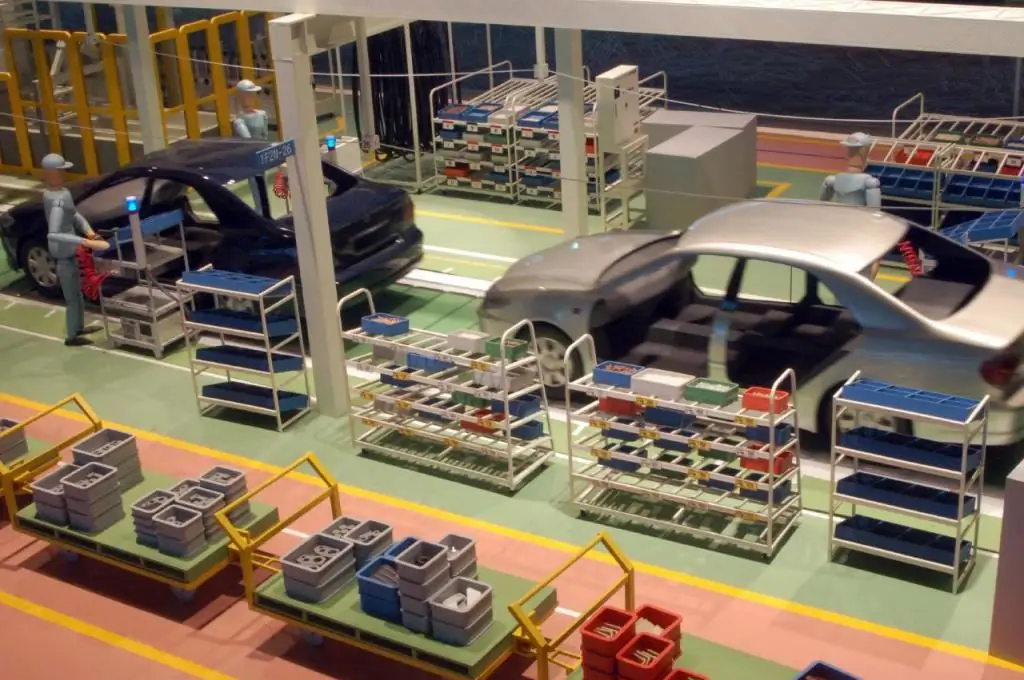
Push or Pull?
Kanban was born as a result of just-in-time enterprise improvement to reduce waste and improve product quality. At the same time, its creation and subsequent use opened up a new type of management. If until the middle of the twentieth century, the efforts of researchers were mainly aimed at improving the mechanisms of push production (i.e., those that operate under a strict plan), then from the moment the Kanban system was applied, pull-type enterprises appeared in logistics. In this case, the direction of the information flow changes.
In push-type shops, the control signal goes from left to right, actually “pushing” the product from one area to another according to the accepted technology. For pullers, the last section generates a request for the necessary components from the previous stages of production.
Kanban production system is not a completely new type of production. Strictly speaking, the production management models that have emerged over the past half century represent superstructures for classical industrial enterprises. The most accurate term for Kanban capabilities is "efficiency". Since progressive methods of modernizing production are aimed at increasing it.
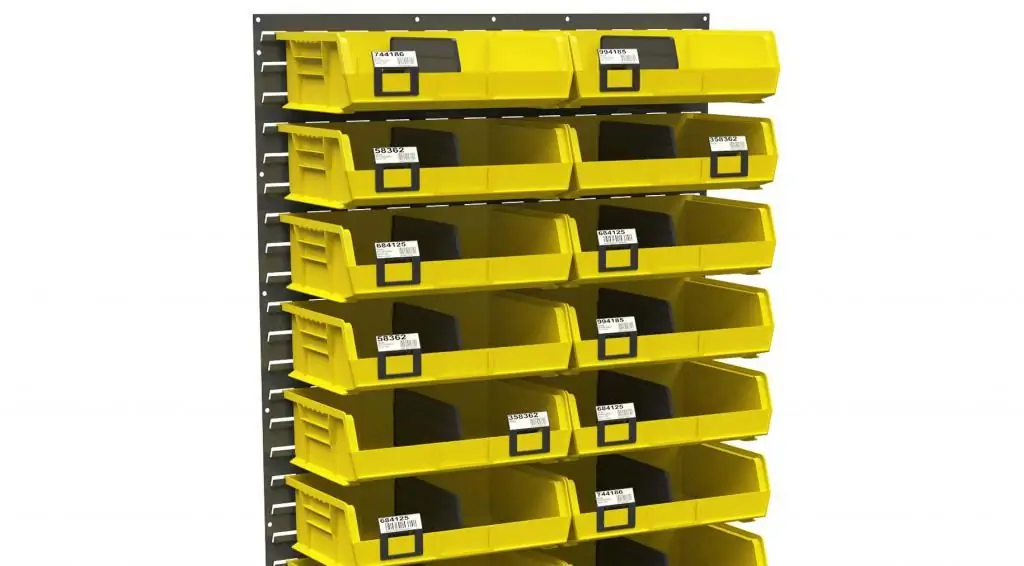
What's the difference?
The essence of the Kanban system is to organize the smooth execution of production tasks at all work positions (places) of the productionprocess. Distinctive features are the minimization of stocks at all stages of the product life cycle.
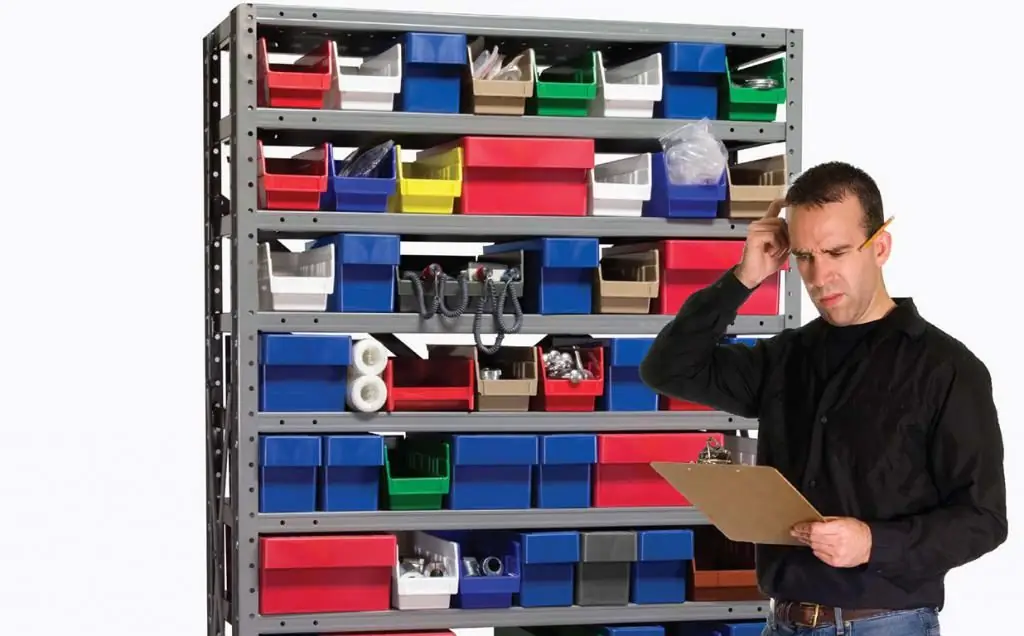
Material stocks are one of the bottlenecks of modern production. In practice, one of the following options is highly likely to occur:
- insufficient inventory;
- stock reserve.
The consequences of the development of the first scenario will be:
- interruptions in the rhythm of production;
- decrease in output by employees;
- increased number of spares and components due to late maintenance;
- increase in manufacturing costs.
For the second option, the characteristic features are:
- low turnover;
- decrease in production;
- increased losses on supporting infrastructure (storage space, personnel, utilities).
The Kanban system reduces the risks of both scenarios due to the accepted restrictions on the allowable amount of resources in the production chain. As a result, “transparency” of processes appears - interruptions in the operation of equipment, the actual amount of marriage, the actual throughput of workplaces are visible. The result of the introduction of the system is an increase in product quality against the backdrop of a significant reduction in costs.
Key elements of the system
"Kanban" is the control of production processes with the help of special control signals. Note that for effectivefunctioning requires a developed infrastructure of interaction between the structural components of production, sophisticated manufacturing technology, teamwork of labor personnel. The main element of information in the production chain was plastic cards of different colors with different information (the meaning of "Kanban" from Japanese is "card"). Its appearance depends on the type of control.
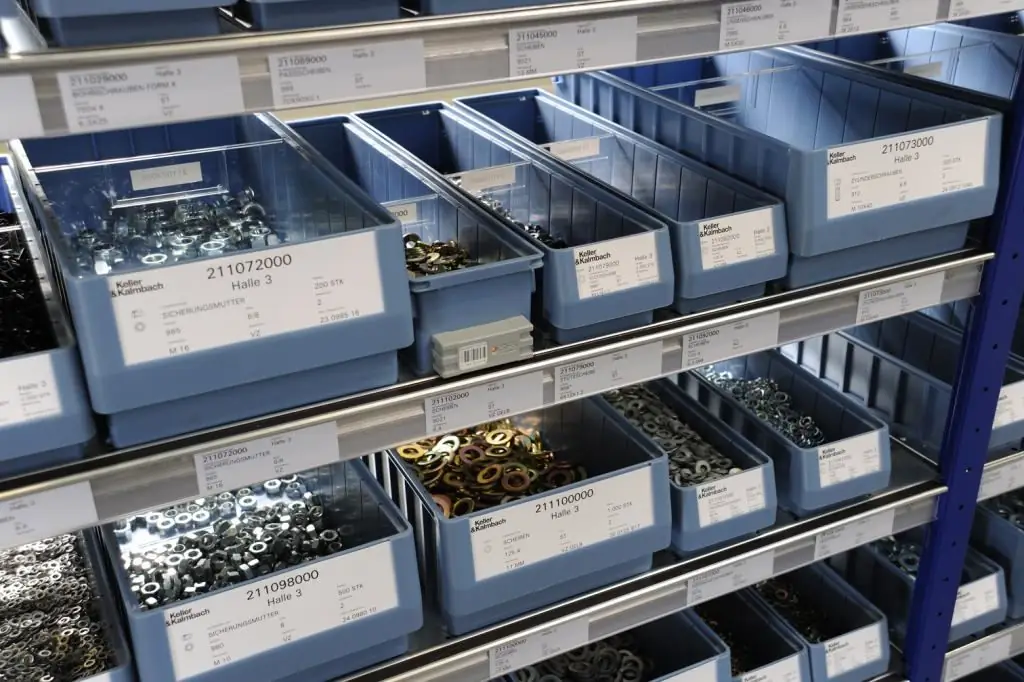
Tare Kanban
The data card is mounted on the container. The production order is determined by the position of the container itself on the rack. The ordering algorithm is carried out as follows: when the number of parts in the first container with the map decreases, it is moved from the working position to one of the tiers of the rack (which serves to place orders and receive a signal from the transport service employee) and starts working with another. The transporter picks up an empty container, the presence of a kanban card on which indicates the need to order material from a storekeeper or supplier. The main disadvantage of this type of kanban is the additional amount of packaging for each type of part used.
Card Kanban
Multi-colored card with production information, the color determines the spatial parameters of the necessary supplies. In practice, the card is divided into several segments that show information regarding the sender and recipient.
There are different schemes for using the color palette of cards. From monochrome (white, black) to multi-colored. The number of colors and their choice depend oncomplexity of manufacturing processes. If it is necessary to use signals between different working functional areas, the following scheme can be proposed:
- blue color - "production kanban" (connection between work area and supply area);
- red color - "warehouse kanban" (connection between warehouse and pickup area);
- green color - "cross-shop kanban" (communication between different shops or complexes).
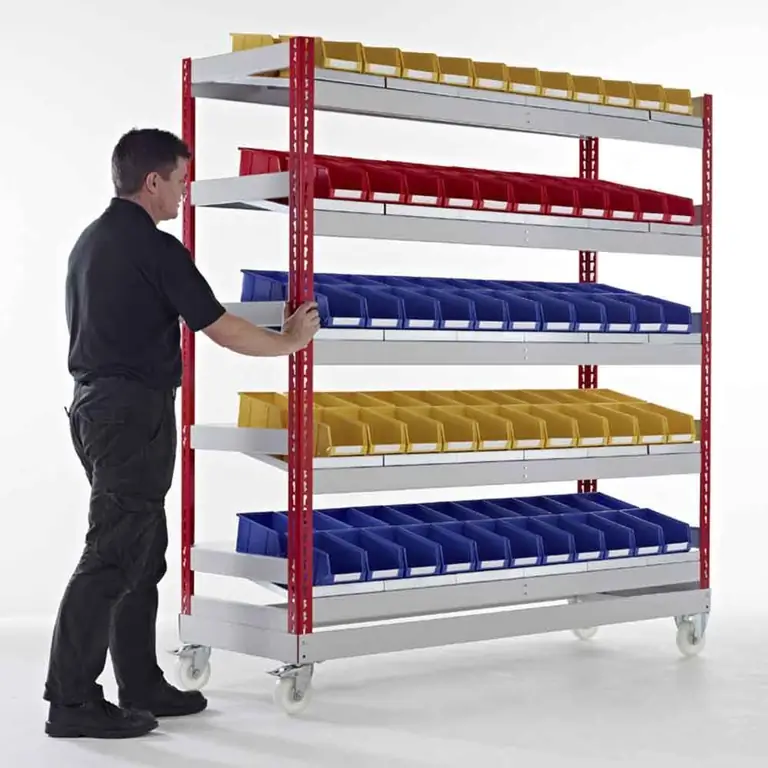
Pros and cons
The Kanban system has a number of advantages over traditional production management methods. This is confirmed by feedback from employees. It reduces lead times, reduces equipment downtime, optimizes inventories, reduces scrap, eliminates WIP, improves space utilization, increases productivity and increases overall plant flexibility. At the same time, the limitations of the method are inevitable - it is necessary to create a reliable supply chain of inventories, there is no possibility of long-term planning of production tasks. According to the leaders, high demands arise for the synchronization of the actions of employees of various services.
In conclusion, the Kanban system is not just a process improvement method, it is a production philosophy that, with systematic and constant use, allows to achieve high performance of the enterprise.
Recommended:
Classification of management functions: definition of the concept, essence and functions
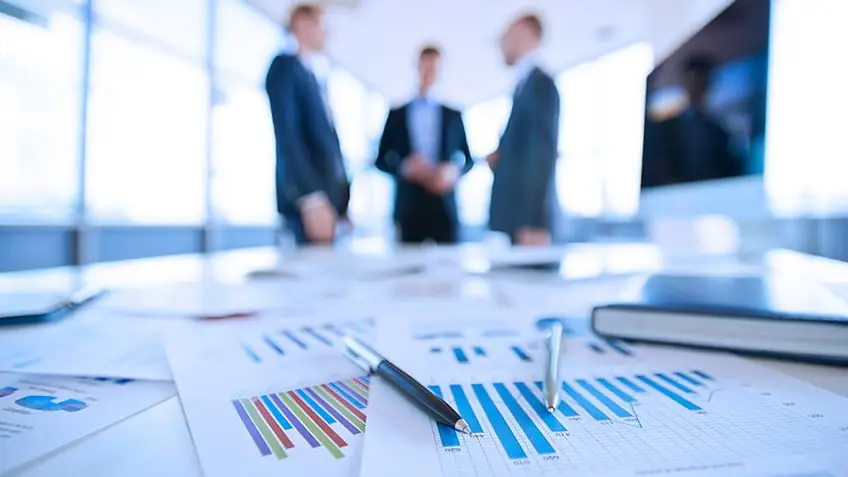
Management is a complex and multifaceted process. Why is it needed and what is its essence? Let's talk about the concept and classification of control functions, consider approaches to this problem and characterize the main functions
Centralized management: system, structure and functions. Principles of the management model, pros and cons of the system
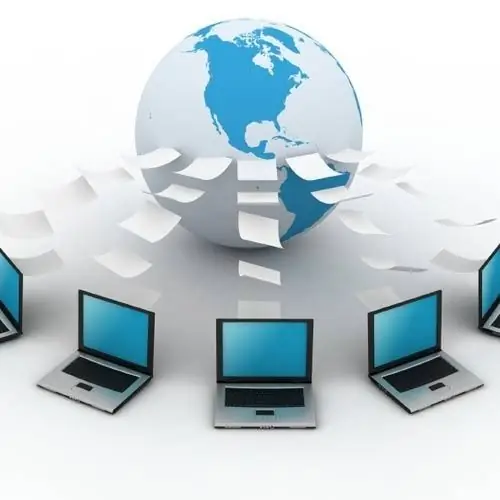
Which management model is better - centralized or decentralized? If someone in response points to one of them, he is poorly versed in management. Because there are no bad and good models in management. It all depends on the context and its competent analysis, which allows you to choose the best way to manage the company here and now. Centralized management is a great example of this
Insurance: essence, functions, forms, concept of insurance and types of insurance. The concept and types of social insurance
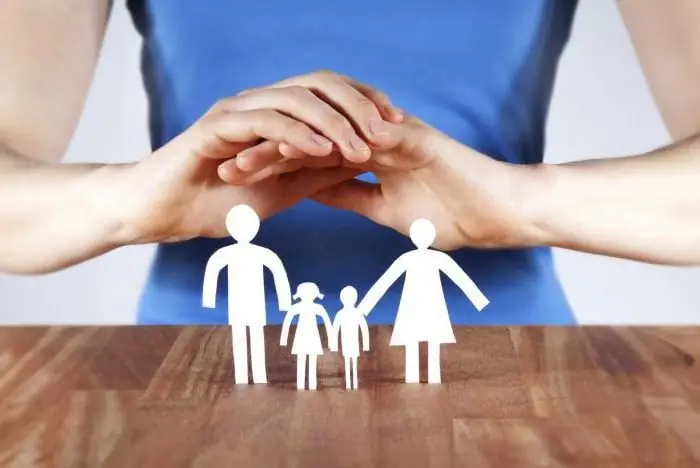
Today, insurance plays an important role in all spheres of life of citizens. The concept, essence, types of such relations are diverse, since the conditions and content of the contract directly depend on its object and parties
Voluntary pension insurance - description, system and functions
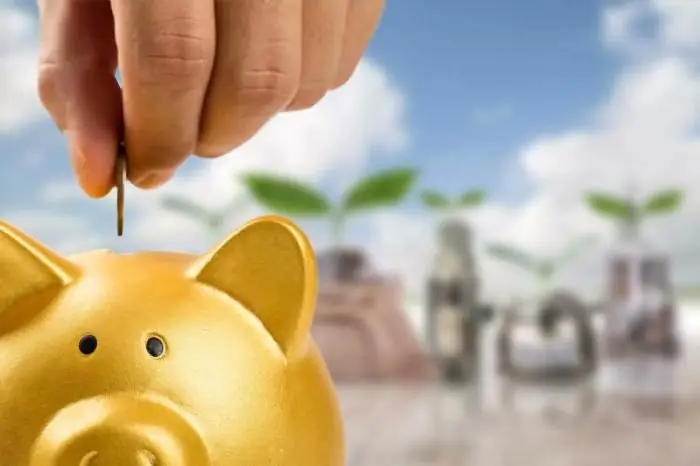
Compulsory pension insurance guarantees the realization of certain rights of both citizens of the Russian Federation and foreigners who live in our country. Voluntary pension insurance is an addition to the mandatory one due to the lack of effectiveness of the latter in guaranteeing the material interests of any social groups of the population. What can all this mean?
The "5C" system in production: description, features, principles and reviews
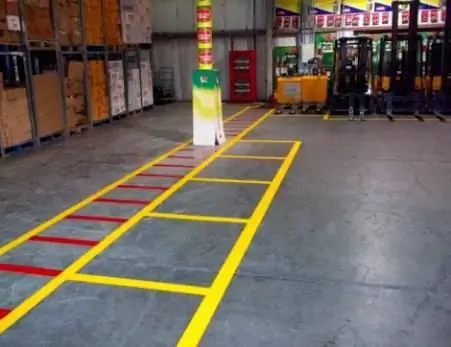
The head of any enterprise, regardless of the field of activity, dreams that profits grow and production costs remain unchanged. The "5S" system in production (in the English version 5S), which is based only on the rational use of internal reserves, helps to achieve this result