2025 Author: Howard Calhoun | [email protected]. Last modified: 2025-01-24 13:10
Analysis of product quality as an object of management is especially relevant if we recall the fact that a market economy reigns in our world. This system pays special attention to quality issues. The reason for this is strong competition. There are several methods of competition, and the key division is into price and non-price, that is, those involving the provision of a higher quality product or service to the client at the same cost as competitors. Quality is becoming a key factor in attracting a potential customer.
Competition and situation
The object of management in the quality system, the product presented to the public by the enterprise, is a significant material for research, giving an idea not only about a particular company or its activities, but also (indirectly) about the market as a whole. In countries dominated by a market economy, where such a system is widely developed, the struggle between companies has led to the formation of specific programs aimed at increasing quality. Practicalmeasures, theoretical studies have shown the need for the formation of such correct indicators that would allow describing the ability of an enterprise to produce a certain product that has all the significant qualities and parameters. To confirm compliance, it was decided to introduce a certification system. Those who successfully pass it receive a specific certificate that declares the parameters of the product.
Today, taking into account the characteristics of facilities and levels of quality management, it has become clear that the best prospects are inherent in enterprises that can prove at the international level: they make a really high-quality product. There are special standards adopted at the interstate level. It is they that are taken into account when certifying the product of the company's activities. The quality system certificate in the current market conditions often becomes a key factor in determining whether a contract will be awarded to an enterprise.
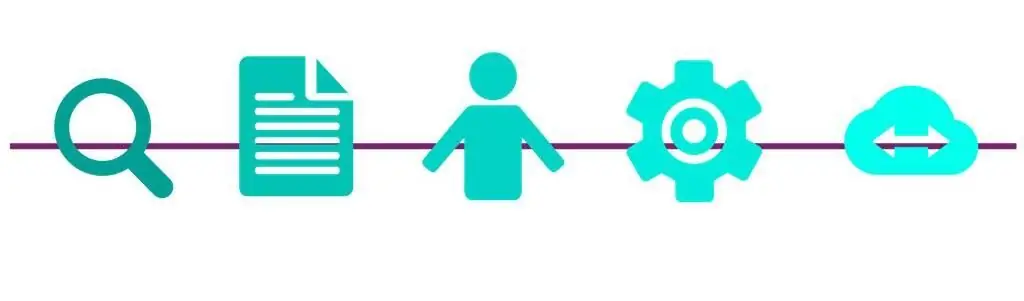
The present and the factors that determine it
Selling high quality products to the end customer is an activity that enables the company to exist, determines its success in the market. This fact is confirmed by numerous stories of enterprises that have managed to become in demand and unique at the international level. Almost every modern person knows about the McDonald's chain of restaurants. A good example of a company that put quality first and thus earned the love of customers all over the planet is Toyota. Generally positive exampleslots of. At the same time, market analysis shows that there are still a huge number of enterprises whose work ends in failure, as consumer expectations and the actual quality of the product diverge in level.
The problem of quality planning, the objects of management of the management system responsible for the quality level of the product, are considered by numerous scientists. Quite a few specialized studies have been published on this topic. Today the world has vast experience in the field of management, including the management of quality parameters. When all this useful information is summarized and put into practice, the enterprise is guaranteed to achieve excellent performance.
Terminology and understanding
At present, the representation of objects as, objects of control in the management system is somewhat difficult due to the various interpretations of terms. Quality is a purely subjective concept. Many variants and approaches have been invented to explain and define this phenomenon. At the household level, quality is usually understood as the compliance of a certain product with requirements, expectations. In management at the present time, quality should be understood as a complex object, including true consumer expectations at the current time and in the foreseeable future. Among other interpretations, one of the most popular is to regard quality as the satisfaction of consumer needs without limiting the functionality and product parameters.
The study of buying activity showed thatsome goods people buy to own status symbols. This is more often observed when choosing credit cards, purchasing vehicles. But in the general case, for each and every client, the qualities of the goods are important - they are evaluated by both those who make a status purchase and those who only seek to close their needs. In our country, the Academy of Quality Problems deals with objects of management in the quality management system at the scientific level. Its specialists have defined a conceptual understanding of the essence of quality: it is a key category that determines the way of life, the basis for the development of society and its individual representatives. It follows from this formulation that quality improvement is a very important, capacious work. At the same time, misunderstandings remain about the essence of quality as a phenomenon.

Names and formulas
In short, quality as an object of management is a phenomenon that has been trying to find a suitable decoding for a very long time, and from 1968 to the present day, more than a hundred options have been proposed, and their number is increasing every year. This is due to numerous aspects of quality as a category. From the point of view of philosophers, this is a characteristic of being, for specialists in the field of politics and economics, quality is the result of the mutual influence of price and consumer price. Particular attention in the aspect of understanding quality deserves the work of Crosby, who laid the foundation for the theory of quality management. Through his efforts, the phenomenon was defined as a correspondenceexpectations. Crosby worked simultaneously with Duran, who also made a significant contribution to science. Through his efforts, the phenomenon was defined as fit for purpose. One can see in Harrington's writings a proposal to interpret quality as meeting or exceeding customer requirements while maintaining an acceptable cost.
For some time, the analysis of what is the object of quality management, how the phenomenon of quality itself should be understood, as well as other aspects of the management of this direction, was taken up by an international company specializing in standardization problems - ISO. Experts summarized well-known and popular interpretations, based on which they determined the final interpretation of the term. It was decided to consider as a quality such a set of parameters of an object that describes its ability to satisfy the needs already known or assumed. According to researchers, quality is largely determined by customer satisfaction. This is a phenomenon formed by several blocks - the components of quality.
Aspects of the phenomenon
Speaking about the objects and subjects of quality management, you must first determine what are the aspects that form this phenomenon. All of them are among the manufacturers that deserve special attention. First and foremost is the definition of market needs, which allows you to understand what the quality of the choice of a potential client is. Quality aspects also include manufacturing and design processes, compliance with the designed quality of the finished product, as well as the level of service after the conclusion of the transaction. The enterprise hasit makes sense to invest in all these aspects of quality, as this becomes a guarantee that the buyer receives a product that meets his expectations and satisfies his needs. From a strategic point of view, such an investment of money is a well-thought-out investment. According to numerous leaders of successful companies, this type of investment is more profitable than most others. Of particular interest are such assurances from entrepreneurs who are actively introducing elements of quality management into the work of their company.
In the modern scientific approach, the objects of quality management are customer orientation and provision. The latter includes not just technical work assigned to some department of the enterprise, but a systematic process that affects the entire structure of the company. It must be remembered that the issue of quality is important both within the framework of the manufacturing process of products, and in its development, marketing promotion and service after the conclusion of a transaction with a client. Quality growth is possible only if the technology is respected and regularly updated. General qualitative growth is possible when every worker involved in the production of a product is interested in achieving the maximum result. To do this, they often resort to a variety of economic incentives that give motivation to a person.
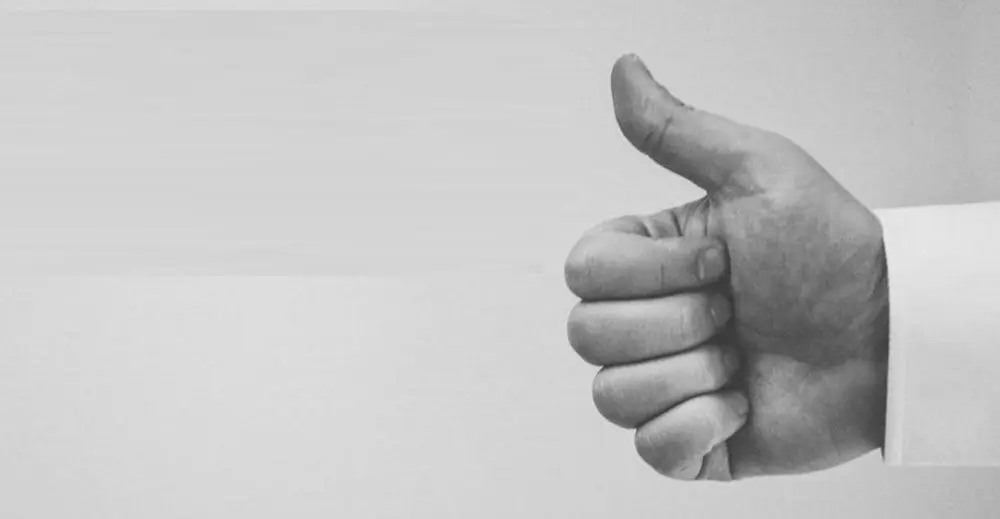
A lot or a little?
To understand the role of quality management in improving the competitiveness of facilities, one should also understand that there are measurement systemsquality. Some specific item can meet the needs of the buyer. You can call this ability a qualitative characteristic. Several types of characteristics have been introduced that allow a comprehensive description of the situation. Some of them can be abstract, others reflect specific consumer desires, customer needs. Let's imagine that there is some machine. A specific wish will be the dimensions of her cabin. Indoor comfort is an aspect that has individual value due to different people's ideas about what comfort is. Quality properties are divided into qualitative, quantitative. The latter are measured by qualimetry. Qualitative parameters are called those developed through the joint work of the consumer and the manufacturer of the product or the enterprise providing some service.
As part of the analysis of objects and subjects of quality management, it is taken into account that the quality of a product is its feature that describes how successfully a customer's need can be satisfied, to what extent the product meets customer expectations. Quality is a complex of several properties that can be possessed by various phenomena, objects that surround a person everywhere in everyday life. ISO has defined the broad concept of a quality object. Under such management theory, it is customary to understand various aspects of the enterprise. Processes, activities, systems, firms, individuals are considered as objects. You can consider as an object a product - material, intangible, as well as a combination of these two.types. A combination of the listed phenomena can act as an object.
Buyer and seller
Science dealing with subjects, objects, functions of quality management defines customer orientation as a key principle of quality management. Strategic orientation must have organizational support. The enterprise organizes technical capabilities, conducts methodological work, research in order to maintain customer focus. A well-designed process is vital for any modern firm that is forced to operate in a competitive environment. Competition and the policy pursued by the company in this aspect provide the buyer with quality goods and impeccable service. The degree of satisfaction is determined by how the purpose of the goods and the object itself correspond to each other in the eyes of the client. The consumer defines specific requirements for different types, varieties of services, products. These requirements include durability, functionality, minimum risks and other similar aspects. Requirements are generally defined as an expression of customer needs. These are an element in the formation of relationships between the goals of the client and the suitability of the goods for them.
Modern science considers the quality of education as an object of management, as well as the quality of creating a product or providing another service (for example, a lawyer). In a word, any service, any product has a quality parameter. The criteria for its evaluation are different for the client. They are evaluated according to various non-quantitative parameters, and quantitativevary, as they directly depend on the client. In order for quality management and product level control to be sufficient, the manufacturer must at least be aware of the quantitative requirements - and this is not always realistic. If necessary, qualitative parameters are transformed into quantitative ones, analyzing consumer wishes. Among the parameters that are taken into account in this case, functional ones come first, that is, the object must correspond to the work for which it is intended. Equally important is reliability, which is determined by the number of failures (allowing for repair) of the product during its service life. Two more important parameters are the absence of defects and durability. The first involves taking into account only defects that the client can identify. Durability is directly related to reliability.
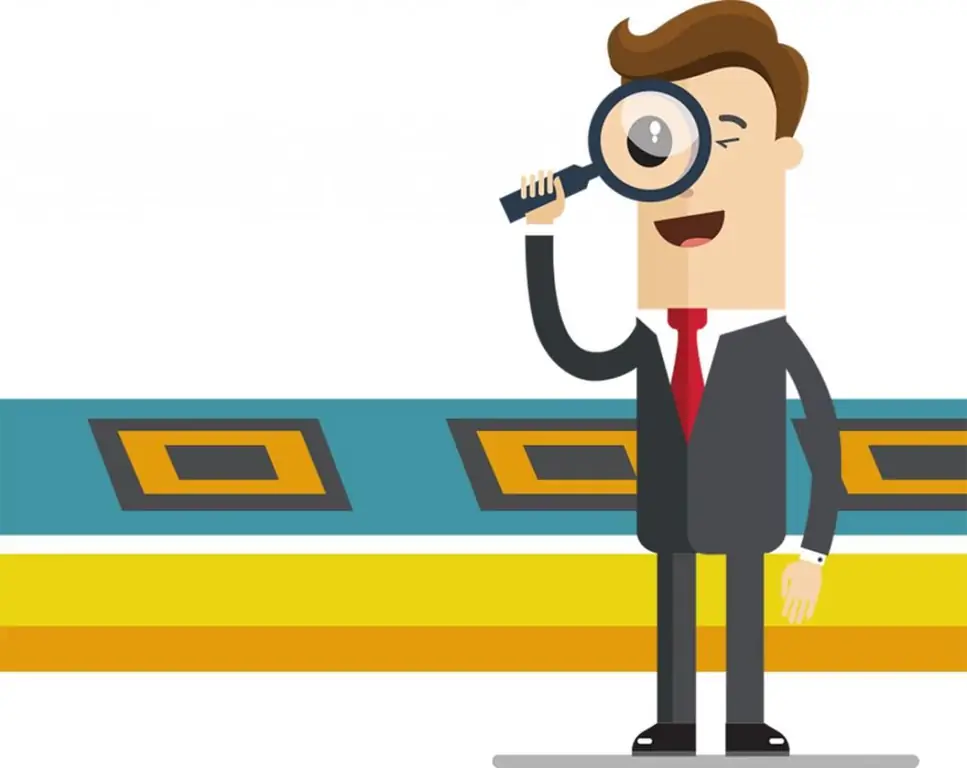
Quality and Reliability
In recent years, more and more people talk about specific qualitative parameters that are quite difficult to describe quantitatively, especially at first glance. This is especially striking in comparison with the above parameters. For example, the object of control in the quality management system is safety. An equally significant aspect that describes the demand for products and their ability to satisfy the client is design. It is important that the product is environmentally friendly - only in this way it will attract the attention of customers around the world. In recent years, the importance of additional services has become more significant. This is usually provided after the conclusiontransactions with a client, but in some cases pre-sales service is also practiced.
Both the availability and quality level of additional services should be determined by the complexity of the products. For a customer who wants to make a purchase, one of the key factors in choosing a particular product is the service offered when it comes to buying something technically sophisticated. A good object that demonstrates this clearly is a computer, and what buyers are guided by when choosing it. However, one should not underestimate the importance of additional services in terms of influencing the objects and subjects of education quality management, legal services and other complex services that are customarily provided in society. It is often quite unclear for a person how to choose the best service center. A person only knows what type of service he needs. Analyzing additional offers related to the service before and after the conclusion of the contract, he makes a decision in favor of a particular enterprise. This suggests that additional service is equally important when selling both a tangible product and an intangible service.
Local and global
Since the parameters described above act as control objects, it is clear that the manufacturer is able to guarantee that the quality level of the products presented to the client meets the requirements of the audience. This is realized through constant checks of qualitative indicators, predetermined in theoretical market research. To control the quality level, you cana certain frequency to compare the actual parameters of the product and those established by the plans. From the fact that quality can be controlled, it follows that it can also be managed.
In recent years, of particular interest to those involved in the definition of what acts as objects of management within the quality system of an enterprise, is attracted by the system of total quality management (TQM). This is to some extent a philosophical idea that can be implemented within a particular enterprise. Its main idea is to strive for the highest quality and to apply in practice such management approaches that will achieve universal quality. VUK is a fundamentally new version of enterprise management. Its main idea is a high quality level, due to the involvement of all personnel of all departments of the company, all levels of the internal hierarchy in the workflow. VUK aims to achieve long-term success of the company. This is achieved through customer satisfaction, leading to benefits for all employees of the enterprise and society in general.
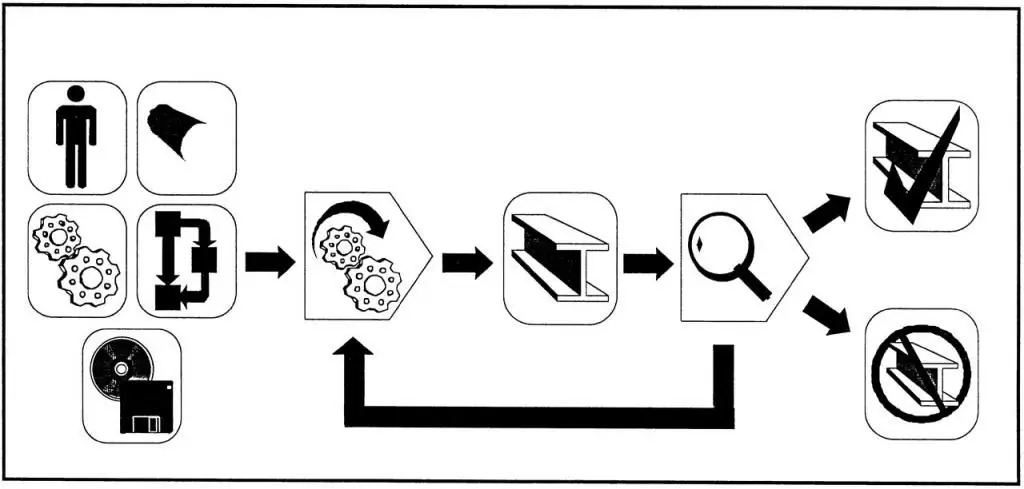
ISO and requirements
Since ISO deals with the consideration of quality as an economic category and an object of management, it is in the works published by this international community that one can see especially a lot of relevant and applicable information in practice. Standardization is actually the process of establishing and then applying certain rules in order to streamline a certain area. This process is beneficial to all participants,provides maximum savings while maintaining functionality and safety. Standardization is aimed at streamlining the objects produced by communities in different powers. It allows you to define the requirements for ordered items by normative documentation, establishes the rules for using documentation in practice. The ISO 9000 series summarizes the international practice of quality management. Such documents are the foundation for achieving a stable quality level at the enterprise. Standards are documentation designed to make it easier to ensure and maintain quality. It was formed by delegates of the international level. The standards fix the minimum requirements for the organization of labor to guarantee a quality level. It doesn't matter what kind of product the company produces.
Today, standards that define quality as an economic category and an object of management have become so in demand at the global level that there simply have not been such precedents in the history of society. The documentation series contains dictionaries, guidelines, dedicated to the definition of standards for a given situation and their application in practice. There are guidelines that define the use of serial standards, as well as documents that reflect models, quality requirements for different stages of the product life cycle. There are recommendations that reveal how to manage the quality and certain aspects of such a system.
And if in more detail?
ISO documents, which consider quality as an object of management, oblige the companydevelop, formalize, put into practice and regularly maintain a quality control system so that its performance results are constantly improved, without deviating from generally accepted norms. According to accepted standards, the organization is obliged to determine the processes that are important in the framework of quality control, apply them in all departments of the company, identify the optimal sequence and mutual influence of processes on each other. The task of the company, as follows from the ISO documentation, is to identify the methods, criteria necessary for high results in process management and their direct implementation. It is necessary to provide the information and other resources that are required to maintain and monitor the quality control processes. The task of the company is to monitor, measure, analyze quality control processes, determine and take measures due to which the planned will be implemented.
The tasks of the enterprise, as follows from the ISO documentation, which considers quality as an object of management, include the implementation of the management of all important management and control processes in such a way that it complies with the standards of generally accepted international documentation. The firm may entrust the execution of some task to a third party. There is a possibility that this will affect the quality level of the product and the degree of its compliance with generally accepted requirements. In this case, the firm is required to take control of the outsourced processes. The internal quality management system should contain blocks dedicated to tracking assigned tasks.
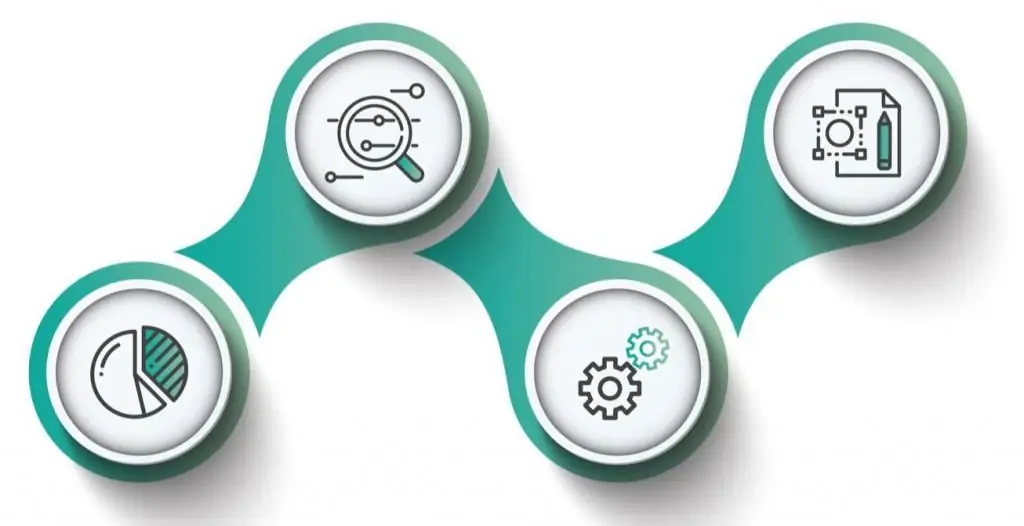
About documents
Since the object of financial management is the quality parameters that are significant for the enterprise and the client at the same time, respectively, it is very important to document each step of the workflow. Thus, the company defines a policy in terms of quality, as well as its goals. All declared statements must be carefully documented. In the form of official papers, guidelines are drawn up on the maintenance and observance of quality, as well as procedures that must be implemented following ISO. The object of financial management is the measures of effective planning, which are recorded in specialized documents officially adopted within the enterprise. It is necessary to draw up documentation that would be devoted to the implementation of the previously agreed processes, as well as control over this work.
Since quality as an object of management requires responsible documentation of the workflow, it is necessary to determine the degree of documentation of the system responsible for controlling the quality characteristics of products. In different enterprises, the level of fixation in official papers of processes, goals, tasks can vary greatly. Much depends on the scale of the enterprise, variety, field of activity. It is necessary to take into account how competent the staff is, what processes take place within the company, how complex they are, how they influence each other. Some form of documentation must accompany the work of any company. You must select the appropriate media.
Aboutdesign details
As can be deduced from the ISO rules regarding quality as an object of management, the enterprise is obliged to form a manual dedicated to quality. All the time of the company's activity it is necessary to maintain it in working condition. The manual should contain blocks on aspects of the application of the quality control rules. Details, details are recorded, and any exception is confirmed by justification. The procedures for quality control should be documented. The official documentation refers to all such developments. It is equally important to formalize the mutual influence of different quality control processes.
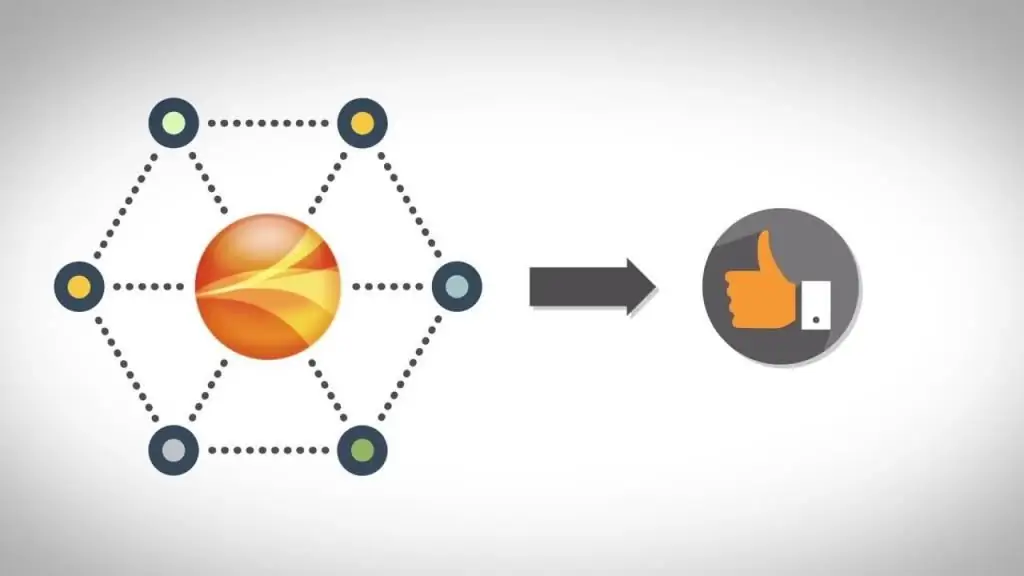
Documentation is a managed object. A record is a document whose management requirements are specified in ISO. From here you can learn that it is necessary to formulate and implement a records management procedure. All of its points are prescribed officially in the internal documentation of the enterprise. This will allow checking all documents before release, controlling their adequacy, as well as analyzing the need for a specific official document and decision, and, if necessary, determining the significance of its revision so that the document remains relevant.
Recommended:
"Quality Circles" is a quality management model. Japanese "Quality Circles" and the possibilities of their application in Russia
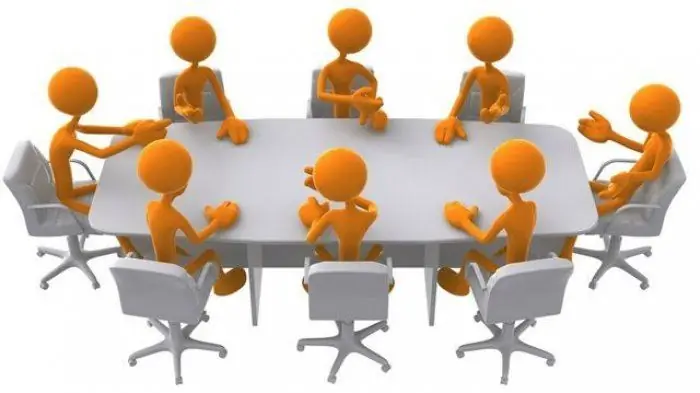
Modern market economy requires companies to constantly improve their technological processes and staff training. Quality circles are a great way to involve active employees in the workflow and implement the most productive ideas in the enterprise
Forecasting and planning finances. Financial planning methods. Financial planning in the enterprise
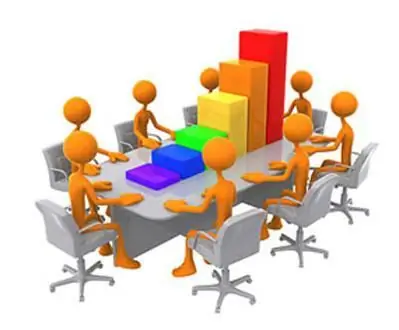
Finance planning combined with forecasting is the most important aspect of enterprise development. What are the specifics of the relevant areas of activity in Russian organizations?
Object of taxation: basic concepts and essence of its definition
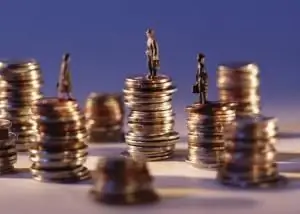
The object of taxation is a list of certain legal facts that determine the obligation of a business entity to pay tax for the implementation of the sale of goods. Also, the taxable object includes the import of goods into the Russian territory, the presence of property in personal possession, the receipt of an inheritance and simply income
Object and subject of insurance: basic concepts, classification of insurance
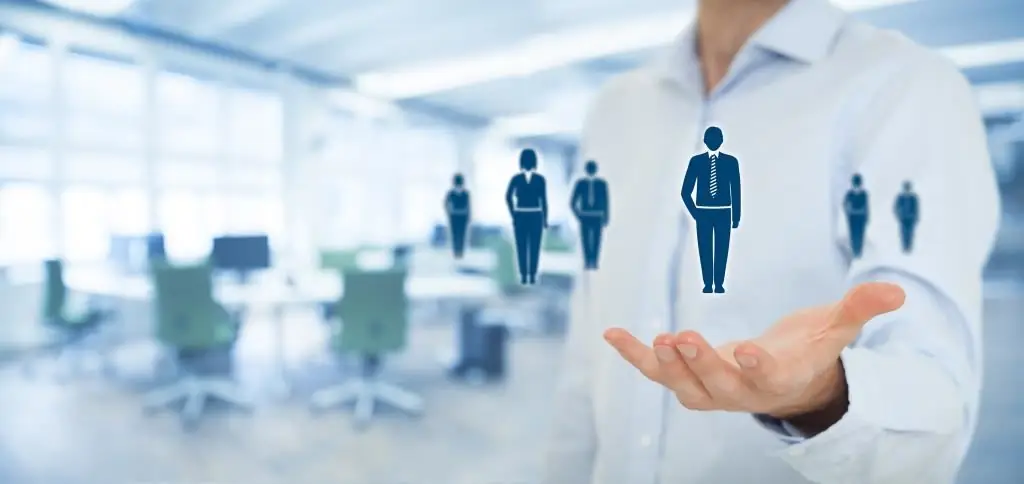
In contractual relations, legal practice, civil legal relations, there are often concepts - object and subject. Insurance is the same wide area of relationships, but not legal, but commercial. Therefore, in the same way there are participants in these relations with their expectations and interests. What is meant by the object and subject of insurance?
The subjects of the insurance business are The concept, activities of subjects, rights and obligations
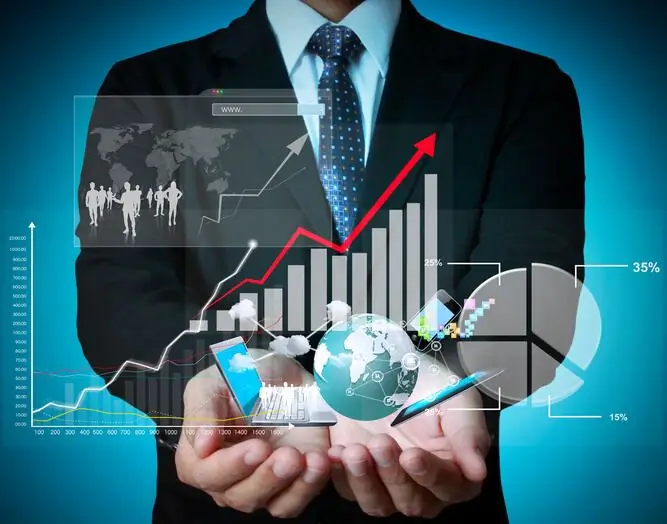
The insurance market is represented by insurance companies, their clients, insurance agents and brokers, beneficiaries and insured persons. However, you should be aware that not all of its participants are subjects of the insurance business