2025 Author: Howard Calhoun | [email protected]. Last modified: 2025-01-24 13:10
The textile manufacturing industry occupies a special place in the national economy, providing consumers of various levels with one of the most common types of material goods in the light industry segment. Depending on the direction of activity of the participants in this market, we can talk about the production of fabrics, knitwear, carpets, etc. As it developed, the weaving industry became more complicated and supplemented with new functions and capabilities. But first, you should familiarize yourself with the historical stages of the formation of this industry in Russia.
History of weaving
Weaving in Russia as a full-fledged technological process for the manufacture of textile materials should be considered starting from the reign of Peter I, when the army needed new uniforms. High-quality production of ancient Russian cloth fabric was possible only with the organization of the work of weavingfactories, which began in 1706, when the first linen production was opened. Further, the process of launching cloth, silk and linen manufactories was mastered, the products of which were not limited only to garments and fabrics. By the middle of the 18th century, the domestic industry could provide the domestic market not only with the simplest fabrics, but also with special artistic canvases for church purposes, as well as special upholstery for furniture.
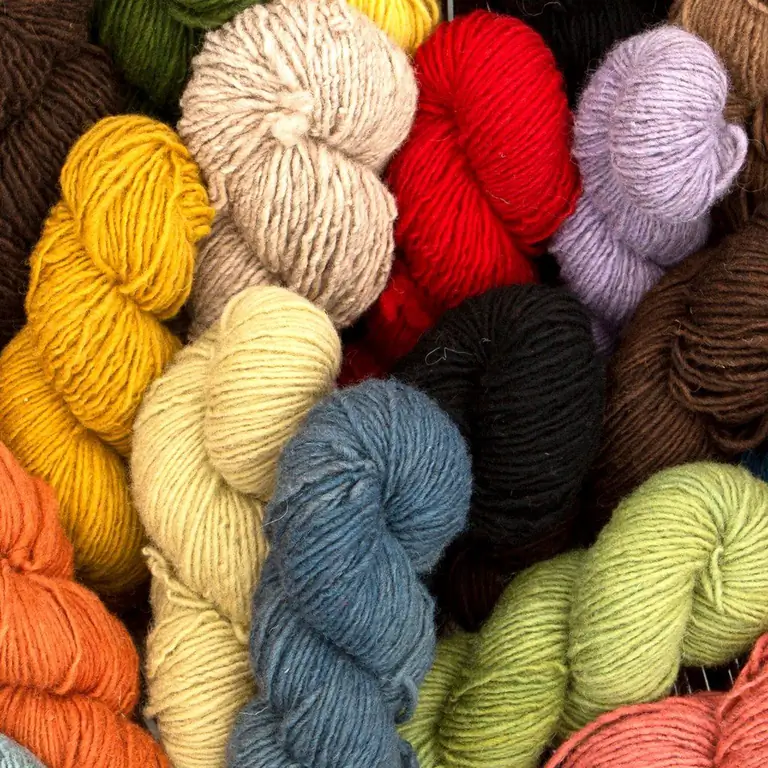
At the same time, until the beginning of the 20th century, the history of weaving in Russia was closely connected with the industry of more developed European countries, as well as many other industries. A sharp decrease in dependence on foreign experience and technology occurred in the first half of the 20th century against the backdrop of intensive mechanization of textile enterprises, which had a positive effect on both product quality and productivity. By the way, in 1928 it was recorded that the Soviet textile industry uses about 4,000 modern looms with a high degree of mechanization at that time.
At the same time, the process of enlargement of mills with woolen workshops was actively going on, shuttleless machines were introduced, and the organizational structure of production was reconstructed in general. In the future, the tasks were set to increase capacities with an increase in production volumes within the framework of the established planned principle. However, the idea of modernization was no longer on the list of priorities, which was reflected in the quality of new products. Long time before the 1990sthe same technical fund was operated without updating, which led to the need to meet the needs of the domestic market at the expense of more attractive imported products in terms of consumer qualities.
Structure and directions of production
The textile industry has several branches. The main ones include the following:
- Cotton.
- Linen.
- Woolen.
- Silk.
Further, the production of the textile industry stands out, including weaving along with cocoon winding, spinning, dyeing and primary (basic processing of raw materials). At the same time, it is impossible to consider each of these industries strictly separately, since in most cases they include combined technological operations, which is especially evident in the example of full-cycle enterprises. The basis of the general technological process is spinning and weaving, which can be represented as a combination of pneumatic and mechanical operations. As part of this process, yarn is formed from natural and man-made fibers. Then, a fabric with certain characteristics is formed from the prepared threads. But even within a narrow view, purely weaving operations can be classified according to the type of materials used. Usually factories specialize in the production of products from specific raw materials - linen, wool, cotton, etc.
Weaving production processes and finishing operations are supplemented. In a single cycle, weaving and finishing production providepreparation of yarn, threads and fabric, which is subjected to special processing, printing and dyeing. Full-fledged dyeing and finishing shops can also be noted, which are organized within the framework of weaving factories and provide comprehensive procedures for thermal, chemical and mechanical preparation of the material.
Technological map of weaving
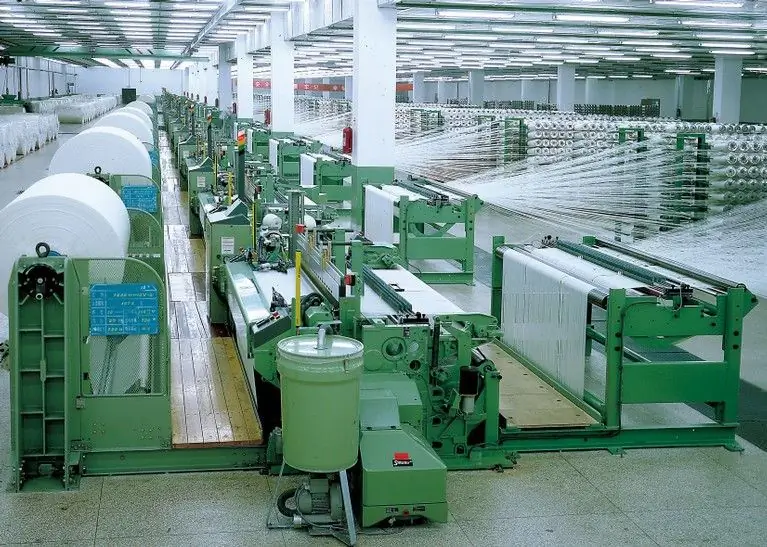
Ensuring a sufficient level of productivity while maintaining proper product quality is impossible without the preliminary development of the production infrastructure of the enterprise with all the logistics stages and mechanical processes for processing raw materials. The following are used in the form of initial data for the development of a technological map of the production process:
- Forging shapes.
- Type of raw material used.
- Characteristics of weft and warp threads.
- Destination of fabric to be made.
- The configuration and structure of the fabric.
- Requirements for organizing workflows.
A specific set of operations to be performed is determined on the same basis. In the mode of the full cycle of warp yarn production, weaving technology provides for the following work processes: rewinding, warping, sizing, piercing, tying, etc. For weft threads, a different group of processes is used, such as rewinding, oiling, moistening, steaming or emulsifying.
The warp threads, which are sent to the spinning packages, are wound into bobbins. Some enterprises exclude this process, since the threadsInitially, they go to spinning or twisting equipment in reels. When warping on special machines, a certain number of threads of a given length are wound onto a package. At this stage, a weaving beam or a warping shaft can be used. The prepared threads are impregnated with dressing - this is a solution that increases the resistance of the material to mechanical stress.
The sizing threads are sent to the weaving shop. At this stage, the parting department is connected, where the threads are threaded into the lamellas. This operation is performed on a parting machine or using a knotting unit. Along with tying, weaving can be considered as the final operation of preparing the threads for the production of the product.
Materials
Weaving products are made from textile materials entering the final stages of production in various forms. The basis for the preparation of such raw materials are fibers, yarn, threads and their derivatives like fabric, felt, felt and knitwear. In a broad sense, textile material refers to strong flexible bodies with a limited length and small transverse dimensions. The main requirement for the use of textile raw materials in weaving is suitability for the manufacture of yarn or finished textile products. This suitability is determined by a wide range of properties and characteristics of raw materials.
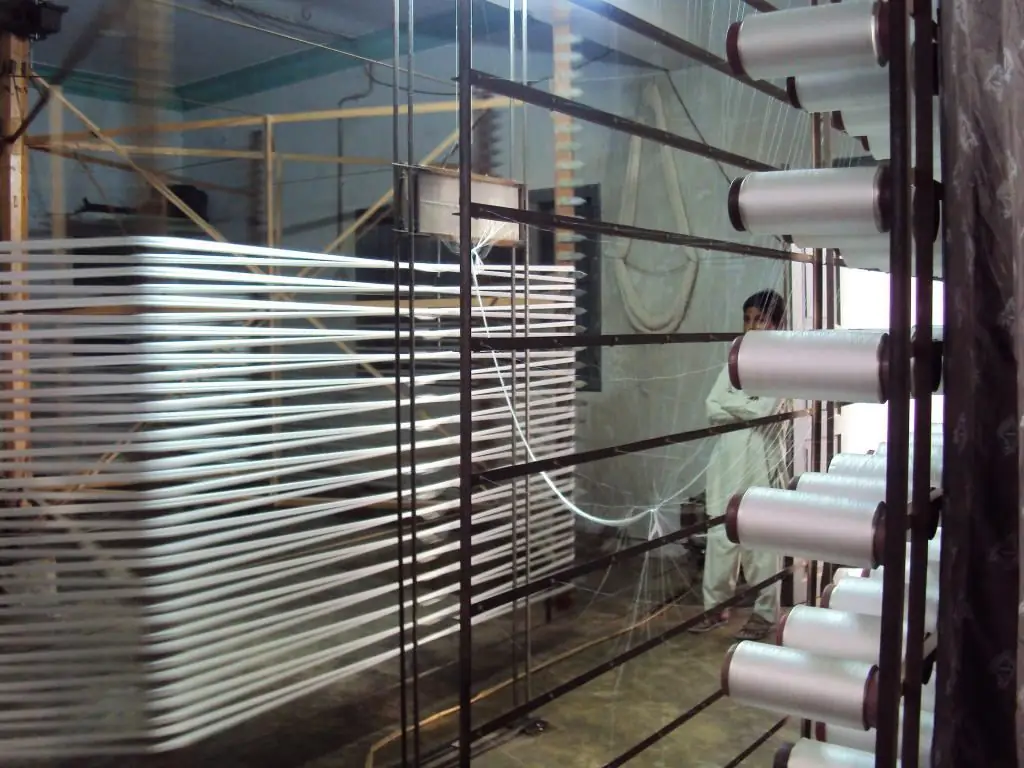
All textile fibers are conditionally divided into elementary and technical. The former are single fibers that do not allowseparation. We can say that this is a small raw material unit, from which more complex blanks are formed. Technical fibers, in turn, are formed by a group of glued elementary fibers in one or another combination. According to weaving technology, both elementary and technical fibers must have a limited length in the range from tens to hundreds of millimeters. The longest filaments are made from silk or chemicals that have undergone special processing.
To create textile products, threads are used, which are also a group of fibers longitudinally interconnected. In this case, primary and secondary threads are separated. Primary fibers are obtained as a result of a chemical operation of spinning or spinning fibers. To prepare the secondary threads, texturing or twisting techniques are used. This is a more complex raw material, which gives more opportunities to change the shape and technical and physical properties of the product.
Applied equipment
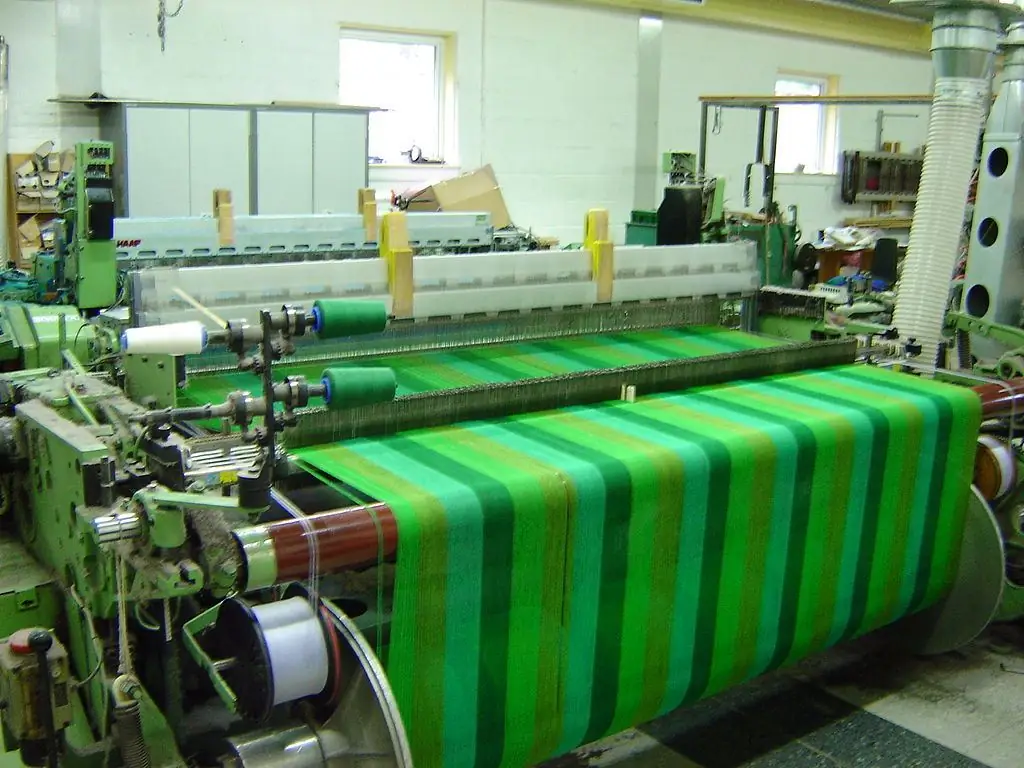
In modern production conditions, it is impossible to do without the use of high-tech machines and auxiliary mechanisms that provide mechanical weaving operations. The general workflow of this equipment is aimed at forming fabric with predetermined parameters and properties. This process can be mechanized by a loom or a group of machines equipped with the following devices:
- Shedding mechanism - provides movement of the mainthreads in the vertical direction.
- Combat unit - lays the weft thread through the shed.
- Batan device - performs the operation of nailing the weft thread to the fabric edge.
- Brake - releases the warp of the thread from the beam and sets it to sufficient tension.
- Commodity regulator - performs several operations, including the movement of the main thread in the longitudinal direction and the removal of the accumulated fabric.
Depending on the conditions of a particular production, various auxiliary units and technical units can be used. It is mandatory for weaving mills to use safety devices, which reduce the risk of defects. For example, in the event of a thread break, they automatically stop the workflow by giving a corresponding signal to the control panel. Restores the process of the weaving master, also monitoring the operating parameters of the loom in normal mode.
Produced materials
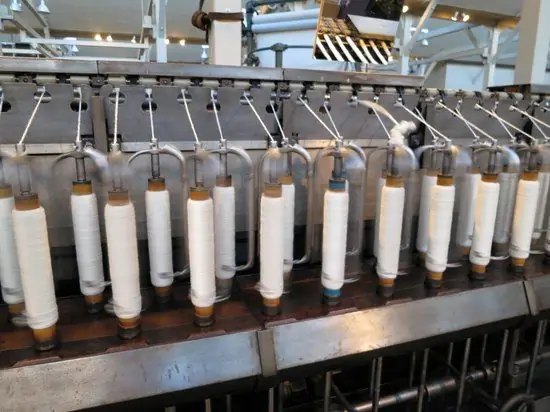
In Russia, the total market of weaving products has about 4,000 types of textile products. The basis of this assortment is formed by fabrics made from the fibrous composition of linen, cotton, wool and silk threads. In addition, fabrics are distinguished by several features that determine the existence of a standard, trade and accounting classification. Each type of fabric is given an article number in the form of a numerical designation that reflects the characteristics of the product, for example, its performance and structural parameters. More onAt the planning stages of weaving production, the enterprise determines the basic range of properties that the products will be guided by. At a minimum, this should be the number of threads used, the linear density, the width of the fabric, etc. A clear definition of the characteristics of the product will form an effective production logistics and focus on it a balanced supply of energy capacities of the enterprise.
Application of new technologies in production
The future of the industry, in terms of technological development, can be associated with the active implementation of developments that improve the quality of work processes. Already today, the production lines of advanced weaving factories are being comprehensively transferred to an electronic control platform with robotic elements. Particular attention is paid to the use of sensors and control mechanisms in areas of probable rupture, which reduces the percentage of rejects and damage to fibers. At the same time, the improvement of weaving production technology is not complete without economic factors. Like all industrial equipment, weaving machines require significant energy costs. New technologies allow to reduce the energy consumption of machine tools from 5-10% to 35-50%, depending on the principle of operation of the unit. Just innovative control systems allow you to combine electrical power supply with pneumatic traction, achieving a high optimization of energy costs. Structural changes also give positive properties to the organization of the production process. In this direction, one can note an increase in the flexibility of the drive when opening the throat, an increase in the resourceshafts and equipment downsizing.
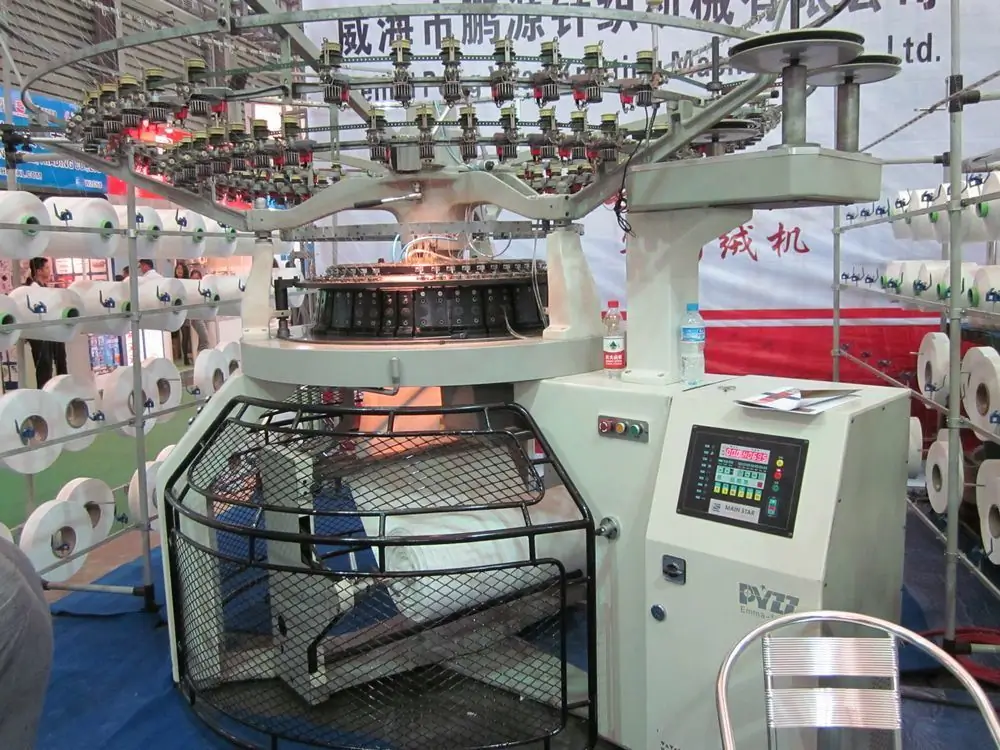
Weaving professions
In a broad sense, textile workers are presented as weavers. However, within the industry there are many individual speci alties. To date, most of them are associated with the tasks of the operator who controls the operation of a particular group of equipment. So, the main professions of weaving production include the following:
- Card operator. Ensures the operation of the card, loads it, and also eliminates breaks when exiting the machine.
- Spinner. Serves the spinning machine, checking the quality of the roving and the thread that is sent to the equipment. The spinner's job also includes quality control of the final yarn.
- Winder. Controls the winding process of the yarn, adjusting the optimal tension and eliminating breaks.
- Weaver. Directly the basic profession in the weaving industry, whose activities are associated with a wide range of activities. He must remove the wound fabric, detect fabric defects, perform equipment maintenance, etc. A member of this profession can generally control the production process at different stages.
- Quality controller. Specialists of this type work on the rejection and measuring units, identifying the rejection of the fabric, as well as evaluating its compliance with the established characteristics. They also carry out the labeling of the product.
Defects
The appearance of defects in the manufacture of fabric can be associated with various defects in weaving - from the initially low quality of raw materials to the incorrect use of machine mechanisms when performing a particular operation. Common problems of this type include the following:
- Blizna - breakage of the main thread, which leads to a violation of the weave and the formation of a longitudinal slit.
- Podpletina - a break in the group of warp threads, entailing a change in the design of the fabric in a particular area.
- Nickle - weft thread seal that goes beyond the allowable norm. These types of defects in weaving are often caused by machine failures and are especially evident when the dye is applied unevenly.
- Tagging - a lack of one or more weft threads, due to which a transverse gap is formed on the fabric.
- Undercut - thinning of the threads caused by violations in the setting of the machine. This defect contributes to the weakening of the structure of matter and the appearance of visible banding in dyed fabrics.
Conclusion
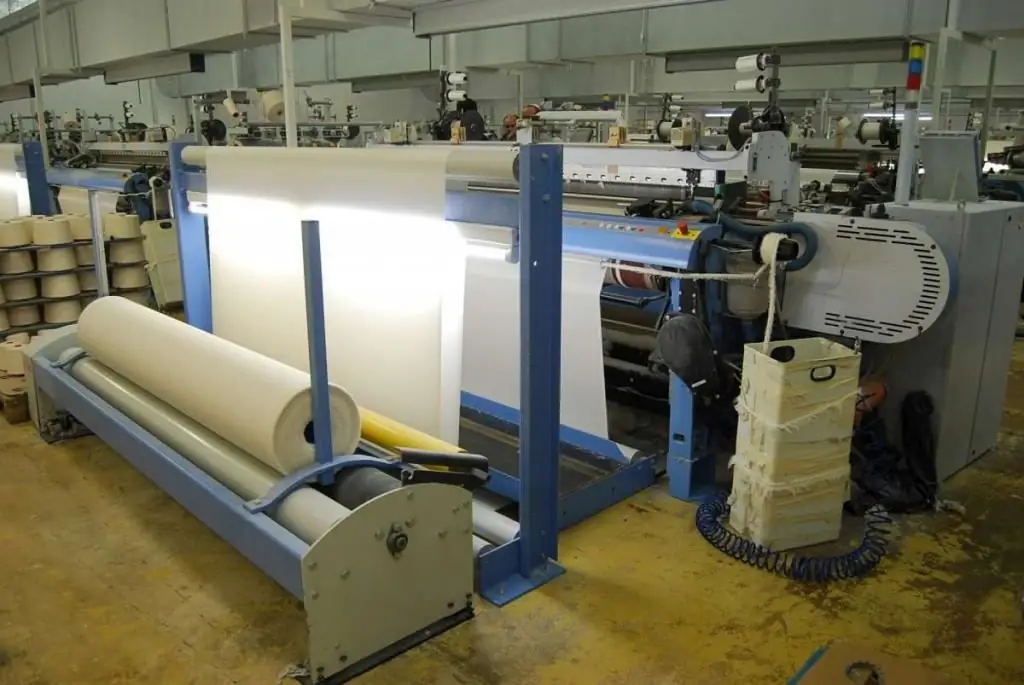
Despite the rich history of formation and technological development, the textile industry continues to be one of the most labor-intensive and complex sectors of the national economy. This is also due to the fact that even large factories tend to work in one specific niche, providing the consumer with a limited range of products. Nevertheless, weaving production in Russia is also represented by enterprises with a wide field of activity. These include LLC"KamyshinLegProm", engaged in the spinning of cotton fibers and the production of fabrics from its own raw materials. On the other hand, Bryansk Worsted Plant LLC specializes in the manufacture of fabrics specifically for suits, uniforms and corporate clothing.
Recommended:
Paper twine - description, manufacturing technology and features
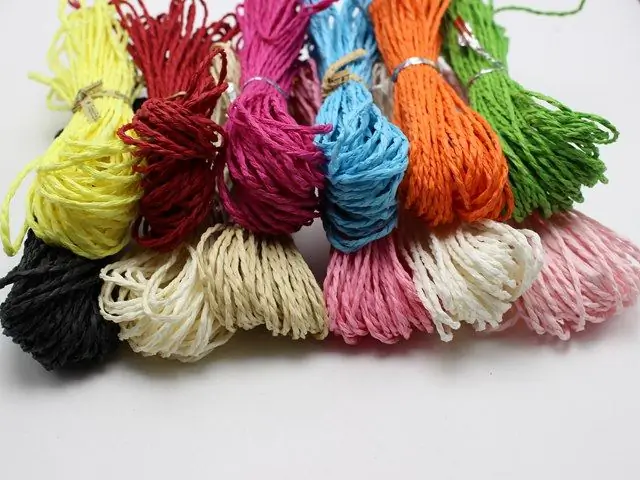
Technology does not stand still, the same trend can be seen in the packaging materials industry. However, there are such unshakable and irreplaceable things over which neither progress nor time has power, such products include paper twine. The article describes its properties and capabilities. Issues of manufacturing technology and operational characteristics are raised
Process engineer: job description. Process Engineer: Job Responsibilities
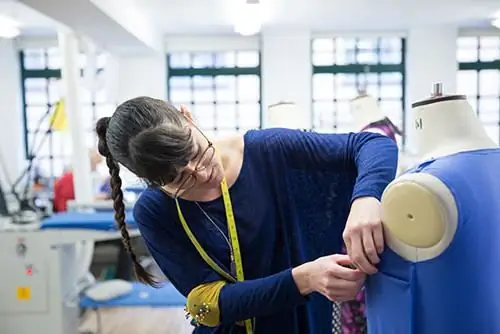
The job description of a process engineer is an addition to the employment agreement and defines the duties, rights and degree of responsibility of the person applying for the specified vacancy. This administrative document is intended to specify the powers of the administrative apparatus in relation to the specialist technologist, as well as to designate the functions of an employee
Rip-stop fabric: what is it, composition, characteristics, weaving threads and application
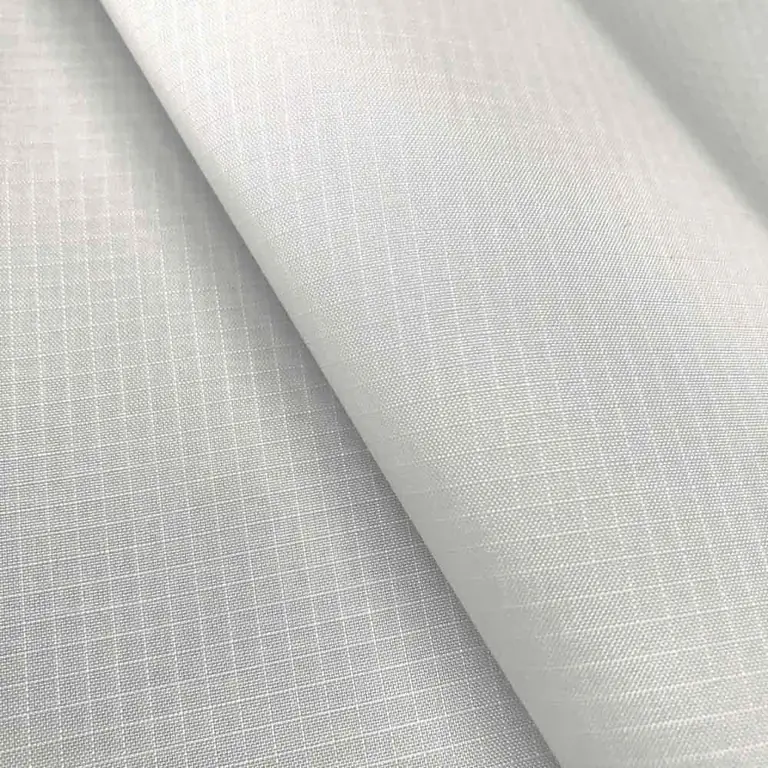
Rip-stop fabric - what is it? This is a high-strength material that has a combined weaving structure with reinforced yarn. It has many modifications. Rip-stop fabric is used for sewing all kinds of uniforms and things for recreation and sports, expeditions and hiking, fishing and hunting, overalls. Consider what composition it has, what properties it has
Oil stabilization: technology description, preparation process, installation device
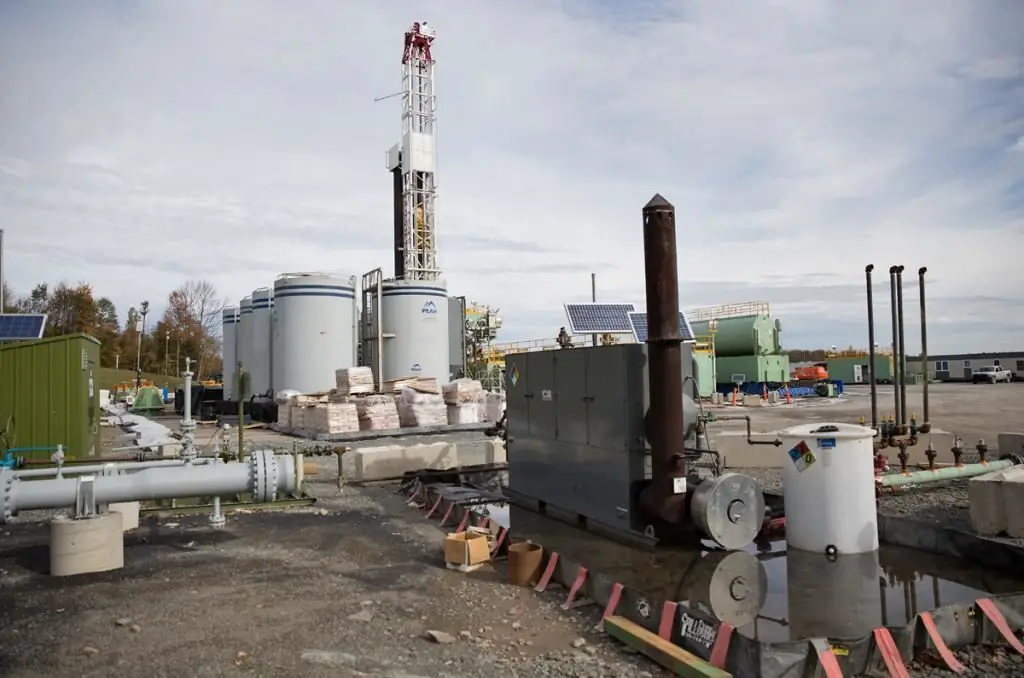
Processes of exploitation of oil wells in the fields are often accompanied by flooding of the treated formations, against which stable water-oil emulsions are formed. The result is the formation of precipitates, which increase the viscosity of the mixture and increase its pour point. In this state, the resources must be subjected to primary processing, one of which is the stabilization of oil and related emulsions
Welding in a shielding gas environment: work technology, process description, execution technique, necessary materials and tools, step-by-step work instructions and expert advice
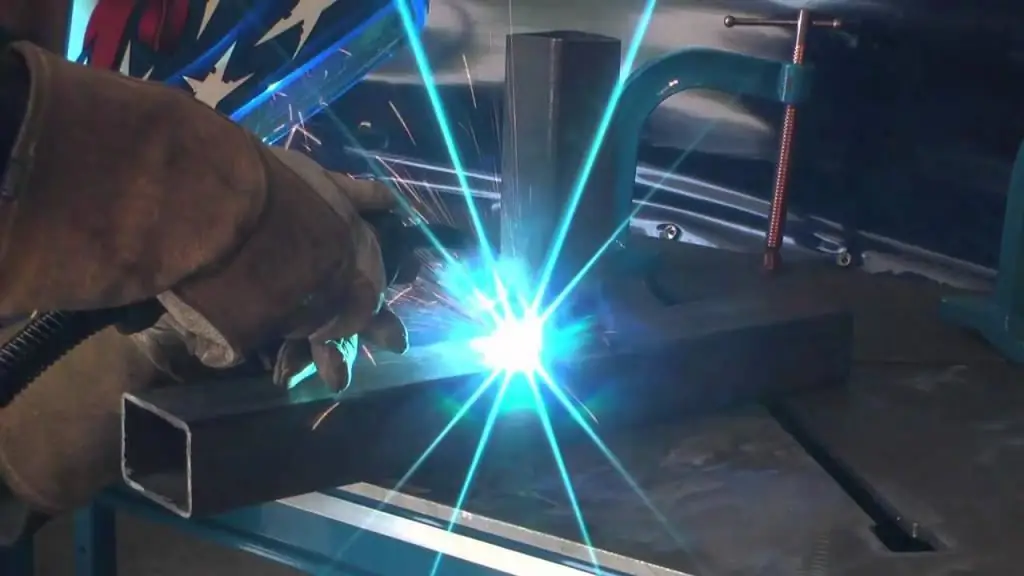
Welding technologies are used in various branches of human activity. Versatility has made welding in a protective gas environment an integral element of any production. This variety makes it easy to connect metals with a thickness of 1 mm to several centimeters in any position in space. Welding in a protective environment is gradually replacing traditional electrode welding