2025 Author: Howard Calhoun | [email protected]. Last modified: 2025-01-24 13:10
1K62 lathes are reliable and productive devices designed mainly for use in individual and small-scale production. They can be used to process parts made of various structural materials: non-ferrous and ferrous metals, cast iron, etc. You can use these machines to cut threads of any kind, as well as Archimedean spirals.
History of equipment
Modern lathes 1K62 are an improved modification of one of the oldest and highest quality models of the Soviet era 1D62 of the DIP200 series. This equipment was produced at the Krasny Proletarian plant from 1949 to 1956. The abbreviation DIP means “catch up and overtake”, and the numbers after it are the height of the centers above the bed. The machines of this series were universal and had a gearbox.
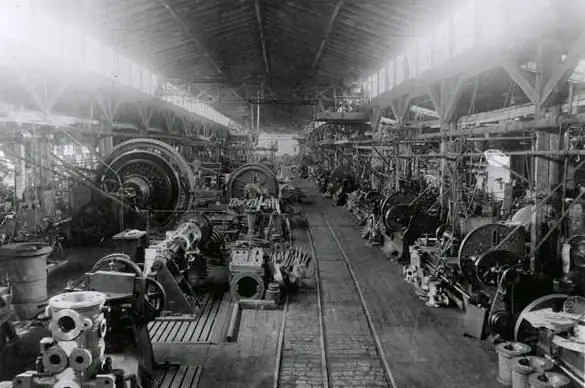
The new model 1K62 began to be produced in 1956. It is distinguished from 1D62 primarily by such improvements and modifications:
- more powerful engine;
- V-belt drive (instead of belt);
- three handlesspindle speed;
- reinforced friction clutch;
- reverse mechanism used in threading;
- electric pump for coolant supply, etc.
Currently, both 1K62 machines and their even more advanced version - model 1K625 are used in production.
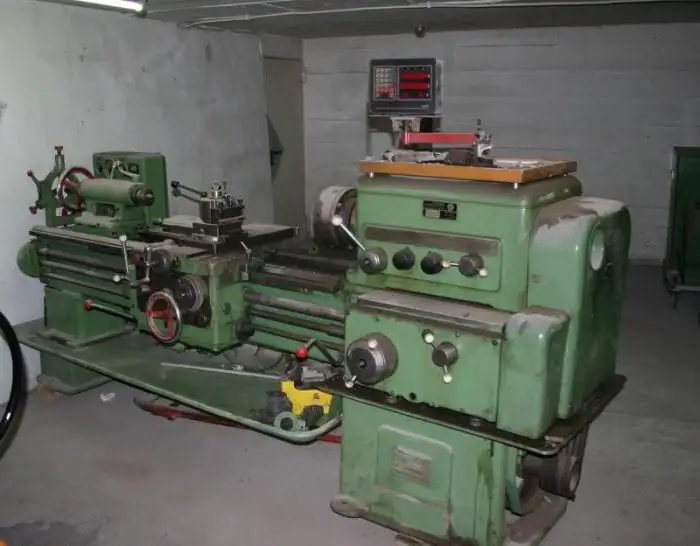
Hardware Advantages
Lathes 1K62 belong to the class of head-type machines and can be used for processing low workpieces of very large diameters. The spindle of the model is mounted on special bearings that ensure its rigidity. Therefore, on 1K62 machines, it is allowed to process, including parts made of hardened metal. The main advantages of this model include:
- high power main drive;
- strength of all elements of kinematic feed chains;
- vibration resistance;
- wide speed range;
- capable of using tools such as cermet and carbide lathe cutters.
The rear beam of 1K62 machines is shifted in the transverse direction. This makes it possible to process shallow cones. Moving the carriage in the longitudinal direction, if necessary, is limited by a special stop. When using it, the maximum speed of the caliper is 250 mm/min.
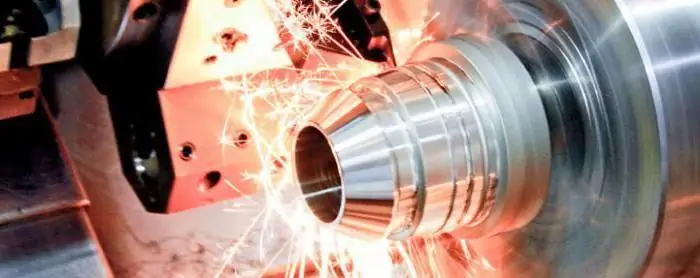
Design Features
Repair and operation of machines of this modification should be carried out exclusivelyhighly qualified specialists. The design of this equipment is quite complex.
The box frame of the 1K62 machine is supplemented with transverse ribs. It rests on two hollow legs. The main stroke electric motor is mounted on the left, and the pump pumping the coolant to the workpiece processing site is mounted on the right. The rotational movement to the spindle is transmitted through the chain "friction shaft / multi-plate clutch / gear mechanism".
The apron of the machine is equipped with four cam-type clutches that allow both forward and reverse movement of the carriage. The simultaneous inclusion of transverse and longitudinal gears is excluded due to the presence of a special blocking device.
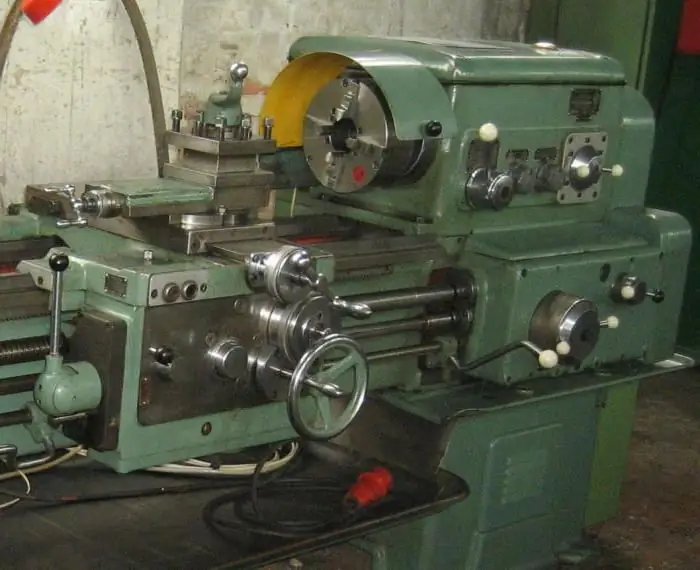
The 1K62 metal lathe is equipped with three-jaw self-centering chucks with a diameter of 250 mm. If necessary, they can be replaced with a four-jaw version 400 mm. Fastening parts in the chuck is done by means of a key without using levers.
Work on machines of this modification, among other things, can be carried out using steady rests - movable with an installation diameter of 20-80 mm and fixed at 20-130 mm.
Wiring diagram
The device of the 1K62 lathe is quite complicated. There are many nodes and mechanisms in this equipment. Their work is provided by motors operating from a 220 V network.
As the main drive in 1K62 machines, an asynchronous squirrel-cage is used. The spindle speed is controlled by the gearbox gear. The second motor, also asynchronous, is responsible for the movement of the caliper. To ensure the long service life of 1K62 machines, a thermal relay is provided in their design. It shuts down the equipment in case of overheating.
In addition to the spindle and caliper motors, the machines of this modification have hydrant and cooling pump motors. The control circuit is powered by an isolating transformer. The start of the main stroke motor is carried out by pressing a special button. At the same time, the pump and hydrant motors turn on.
Quick movement of the caliper is carried out by turning the corresponding handle on the apron of the machine. When the operator performs this action, the contact of the switch included in the design closes the circuit of the coil that transmits voltage to the motor. The spindle of the machine is turned on by turning the friction clutch of the control handle up.
1K62 machines are equipped with local lighting with 36 V lamps. The latter are powered by a separate transformer winding.
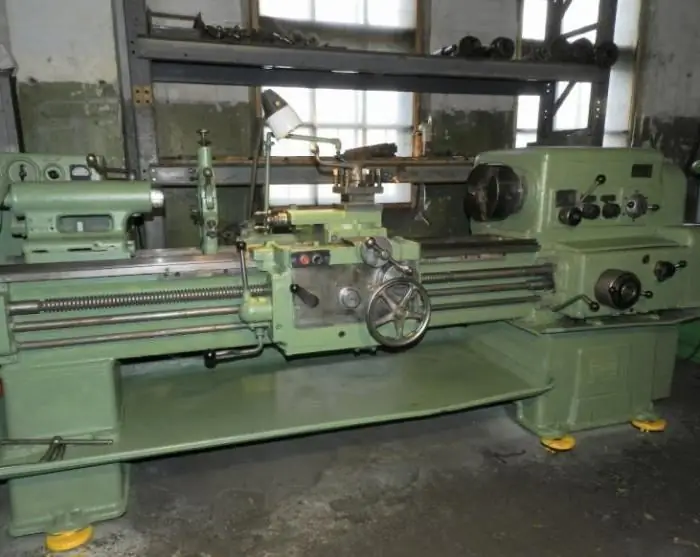
Character failures
Most often, 1K62 lathes have to be repaired for the following reasons:
- Impossibility to switch the gear unit. In some cases, turning off the motor and switching it on the “freewheel” helps to eliminate this problem.
- Arbitrary stop of the working tool. This usually happens simply due to the operation of a thermal relay. In this case, it is recommended to reduce the processing speed of workpieces.
- Pump offcooling. You can correct the situation by adding water to the tank.
- Vibration of the machine. This problem is usually caused by incorrect installation.
- Poor accuracy of machining parts. To correct the situation, you should try to adjust the rear beam, preload the part or tighten the chuck mounting straps.

Specifications
The device of the 1K62 lathe allows you to perform various types of work on workpieces made of various metals. The versatility and high performance of this equipment is determined by its excellent performance, which can be found in the table below.
Characteristic | Meaning |
Workpiece height above bed | Maximum 400mm |
Maximum workpiece length | 1000 mm |
Diameter of workpiece over caliper | 220mm |
Machine weight | 2140 kg |
Dimensions | 2812 x 1166 x 1324 |
Power of main engine | 10 kW |
Caliper drive motor power | 0.75 or 1.1 kW |
Cooling pump | 0, 12 kW |
Thread Pitch Limits | 0.5-192mm |
Number of threads | 45 |
Number of longitudinal caliper gears | 0, 7-4, 16mm/rev |
Transverse | 0.035-2.8mm/rev |
Maximum Torque | 2 kNm |
Maximum workpiece weight | Chuck 300kg, centers 1300kg |
As you can see, the 1K62 lathe, whose characteristics are simply wonderful, can be successfully used in the workshops of enterprises and is of high quality and reliability. The installation of such equipment allows you to produce parts at high speed, avoid downtime and ultimately significantly increase the profitability of production.
Safety Rules for Switching On
Of course, lathes of this brand, as well as metal-cutting machines, milling and others, are quite dangerous equipment in operation. In their design there are elements moving and rotating at high speed. In the latter, the worker's clothes, his hair, etc. can get stuck (or wrapped around them). The consequences of getting into moving and rotating parts of body parts can be truly catastrophic.
Therefore, the repair and operation of lathes of this modification, like any other, are procedures that require compliance with certain safety standards. Before starting work, the turnerrequired:
- put on overalls, glasses, button up sleeves and inspect the workplace;
- Check the serviceability of the protective casing of the cartridge;
- adjust lighting;
- check at idle the serviceability of the controls, lubrication and cooling systems, fixing the switching levers;
- check the he alth of the protection units.
Features of operation
During the operation of the machine is prohibited:
- lean on bed;
- allow chips to wind around the part;
- allow indoor cleaning;
- Machining parts in case of vibration.
The 1K62 machine should be turned off during a temporary shutdown, in the event of a power outage, when lubricating and cleaning its components. Pulling the plug from the network or turning the handles to the “off” position is also required when performing such an operation as repairing a 1K62 lathe: replacing components and parts, tightening nuts, etc.
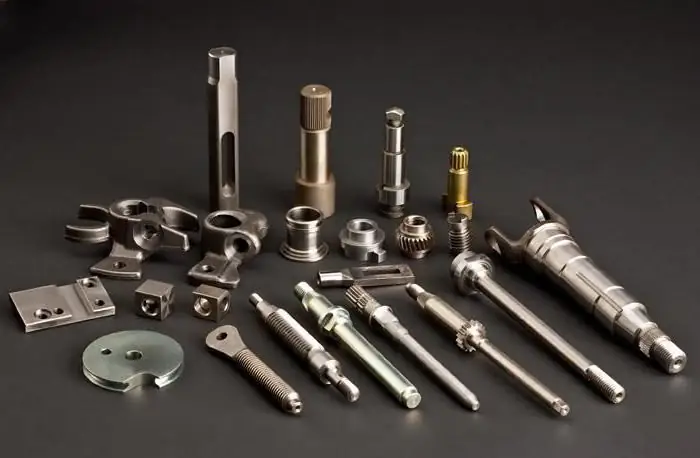
Installation rules
In order for this equipment to function as efficiently as possible, it must be properly mounted. When installing, first of all, a grounding system should be provided. The wires are brought into the control cabinet from below through a special hole. A separate grounding is arranged for the hydrant.
The equipment itself should be installed as level as possible. In order to achieve this, you should use a level. In case of distortions, the bed will begin to vibrate. Additionally withequipment of this type is usually installed metal-cutting machines, milling machines, etc. In this case, everything depends on the characteristics of production.
Machine tools 1K62 - reliable and high-quality equipment, very easy to use. With proper installation and following the recommendations for operation, it pays off pretty quickly. Moreover, the price for it is relatively low - 150-200 thousand rubles.
Recommended:
Automatic lathe and its characteristics. Automatic lathe multi-spindle longitudinal turning with CNC. Manufacturing and processing of parts on automatic lathes
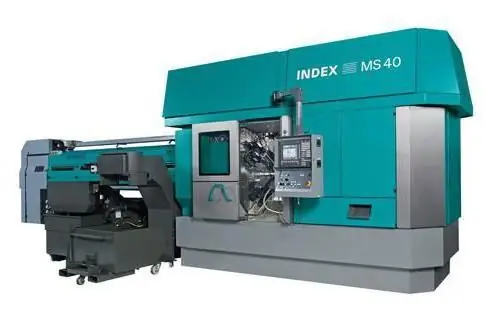
Automatic lathe is a modern equipment used mainly in mass production of parts. There are many varieties of such machines. One of the most popular types are longitudinal turning lathes
Electric locomotive 2ES6: history of creation, description with photo, main characteristics, principle of operation, features of operation and repair
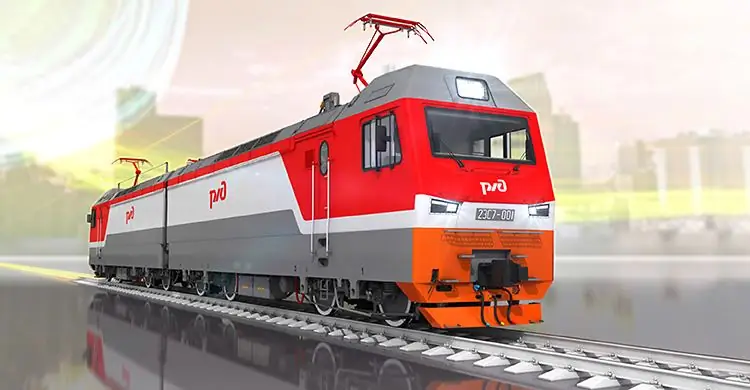
Today, communication between different cities, passenger transportation, delivery of goods is carried out in a variety of ways. One of these ways was the railroad. Electric locomotive 2ES6 is one of the types of transport that is currently actively used
Thermal expansion valve: principle of operation, device and characteristics
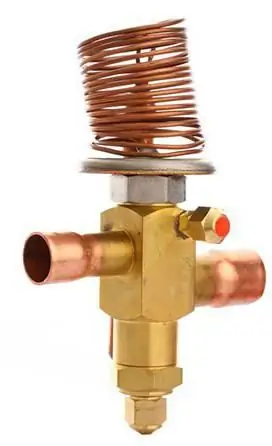
Today, expansion valves are used in many devices. With their help, you can easily adjust the temperature in a living room, they can be added to the design of a tap, used in car air conditioners, etc
Low pressure heaters: definition, principle of operation, technical characteristics, classification, design, operation features, application in industry
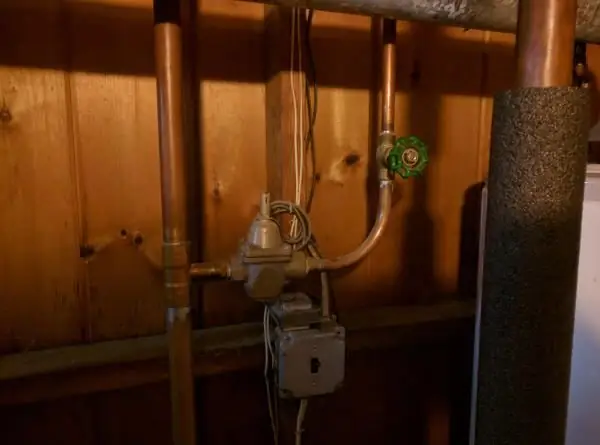
Low pressure heaters (LPH) are currently used quite actively. There are two main types that are produced by different assembly plants. Naturally, they also differ in their performance characteristics
Repair of the engine block: step-by-step instructions with a description, device, principle of operation, tips from the masters
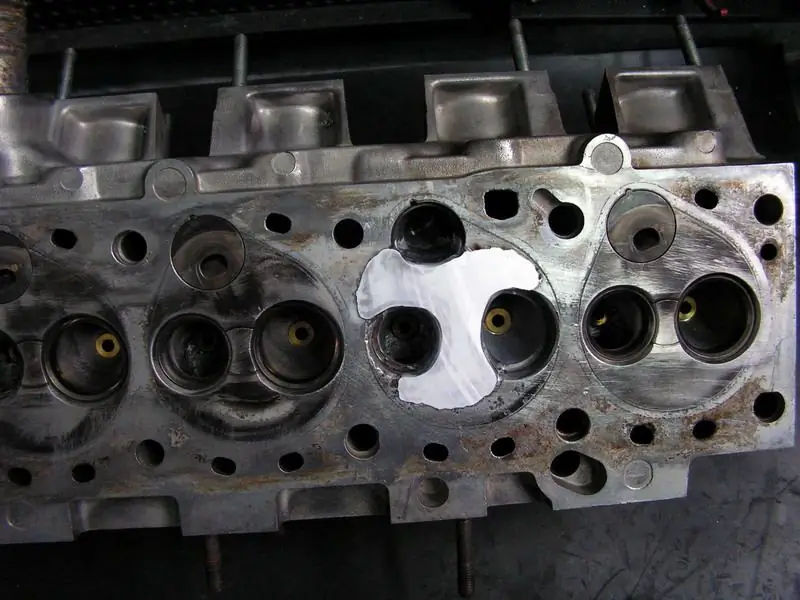
The block is the main part of almost any internal combustion engine. It is to the cylinder block (hereinafter referred to as the BC) that all other parts are attached, starting from the crankshaft and ending with the head. BCs are now made mainly of aluminum, and earlier, in older car models, they were cast iron. Cylinder block failures are by no means uncommon. Therefore, it will be interesting for novice car owners to learn how to repair this unit