2025 Author: Howard Calhoun | [email protected]. Last modified: 2025-01-24 13:10
Heat treatment of alloys is an integral part of the production process of ferrous and non-ferrous metallurgy. As a result of this procedure, metals are able to change their characteristics to the required values. In this article, we will consider the main types of heat treatment used in modern industry.
Essence of heat treatment
During the production of semi-finished products, metal parts are heat treated to give them the desired properties (strength, resistance to corrosion and wear, etc.). Heat treatment of alloys is a set of artificially created processes during which structural and physical and mechanical changes occur in alloys under the influence of high temperatures, but the chemical composition of the substance is preserved.
Heat treatment purpose
Metal products that are used daily in all sectors of the national economy must meet high requirements for resistance to wear. Metal, as a raw material, needs to be strengthened with the necessary performance properties, which can bebe exposed to high temperatures. Heat treatment of alloys with high temperatures changes the initial structure of a substance, redistributes its constituent components, transforms the size and shape of crystals. All this leads to minimization of the internal stress of the metal and thus increases its physical and mechanical properties.
Types of heat treatment
Heat treatment of metal alloys comes down to three simple processes: heating the raw material (semi-finished product) to the desired temperature, keeping it under the specified conditions for the required time and rapid cooling. In modern production, several types of heat treatment are used, which differ in some technological features, but the process algorithm in general remains the same everywhere.
According to the method of performing heat treatment, there are the following types:
- Thermal (hardening, tempering, annealing, aging, cryogenic treatment).
- Thermo-mechanical treatment involves high temperature treatment combined with mechanical action on the alloy.
- Chemico-thermal involves the heat treatment of metal, followed by enrichment of the surface of the product with chemical elements (carbon, nitrogen, chromium, etc.).
Annealing
Annealing is a manufacturing process in which metals and alloys are heated to a predetermined temperature, and then, together with the furnace in which the procedure took place, cool very slowly naturally. As a result of annealing, it is possible to eliminate the inhomogeneities of the chemical compositionsubstances, relieve internal stress, achieve a granular structure and improve it as such, as well as reduce the hardness of the alloy to facilitate its further processing. There are two types of annealing: annealing of the first and second kind.
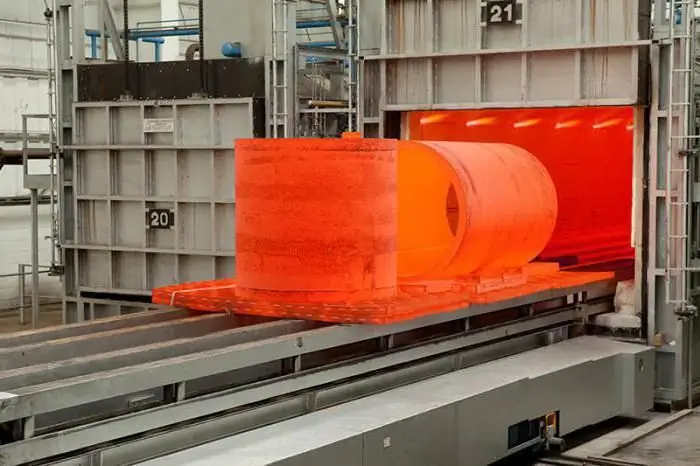
First-class annealing implies heat treatment, as a result of which there is little or no change in the phase state of the alloy. It also has its own varieties: homogenized - the annealing temperature is 1100-1200, under such conditions the alloys are kept for 8-15 hours, recrystallization (at t 100-200) annealing is used for riveted steel, that is, deformed already being cold.
Annealing of the second kind leads to significant phase changes in the alloy. It also has several varieties:
- Full annealing - heating the alloy 30-50 above the critical temperature mark characteristic of this substance and cooling at the specified rate (200 / hour - carbon steels, 100 / hour and 50 / hour - low-alloy and high-alloy steels, respectively).
- Incomplete - heating to a critical point and slow cooling.
- Diffusion - annealing temperature 1100-1200.
- Isothermal - heating occurs in the same way as with full annealing, however, after that, rapid cooling is carried out to a temperature slightly below the critical one and left to cool in air.
- Normalized - complete annealing with subsequent cooling of the metal in air, and not in a furnace.
Hardening
Tempering is manipulationwith an alloy, the purpose of which is to achieve a martensitic transformation of the metal, which reduces the ductility of the product and increases its strength. Quenching, as well as annealing, involves heating the metal in a furnace above the critical temperature to the quenching temperature, the difference lies in the higher cooling rate that occurs in the liquid bath. Depending on the metal and even its shape, different types of hardening are used:
- Hardening in the same environment, that is, in the same bath with liquid (water for large parts, oil for small parts).
- Intermittent hardening - cooling takes place in two successive stages: first in a liquid (a sharper coolant) to a temperature of approximately 300, then in air or in another oil bath.
- Stepped - when the product reaches the hardening temperature, it is cooled for some time in molten s alts, followed by cooling in air.
- Isothermal - technology is very similar to step hardening, differs only in the holding time of the product at the martensitic transformation temperature.
- Self-tempering hardening differs from other types in that the heated metal is not completely cooled, leaving a warm area in the middle of the part. As a result of this manipulation, the product acquires the properties of increased strength on the surface and high viscosity in the middle. This combination is essential for percussion instruments (hammers, chisels, etc.)
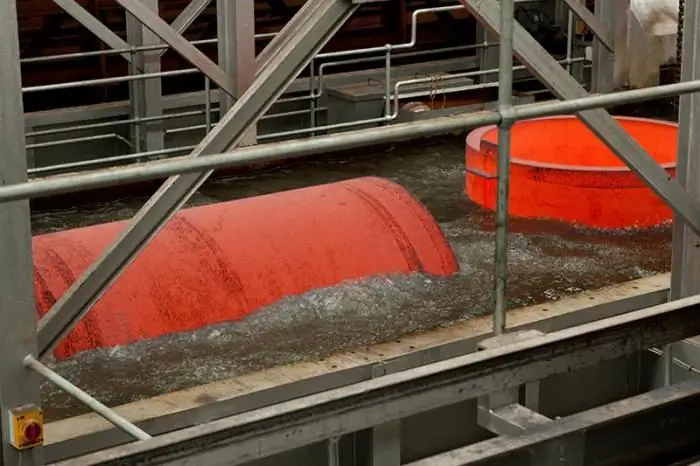
Vacation
Tempering is the final stage of heat treatment of alloys, which determinesthe final structure of the metal. The main purpose of tempering is to reduce the brittleness of a metal product. The principle is to heat the part to a temperature below the critical temperature and cool it down. Since the heat treatment modes and the cooling rate of metal products for various purposes may differ, there are three types of tempering:
- High - the heating temperature is from 350-600 to a value below the critical one. This procedure is most often used for metal structures.
- Medium - heat treatment at t 350-500, common for spring products and springs.
- Low - the heating temperature of the product is not higher than 250, which allows to achieve high strength and wear resistance of parts.
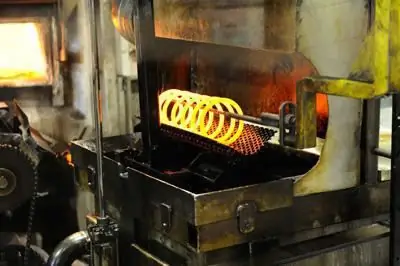
Aging
Aging is the heat treatment of alloys, causing the processes of decomposition of a supersaturated metal after quenching. The result of aging is an increase in the limits of hardness, yield and strength of the finished product. Not only cast iron is subjected to aging, but also non-ferrous metals, including easily deformable aluminum alloys. If a metal product subjected to hardening is kept at normal temperature, processes occur in it that lead to a spontaneous increase in strength and a decrease in ductility. This is called the natural aging of the metal. If the same manipulation is done at elevated temperatures, it will be called artificial aging.
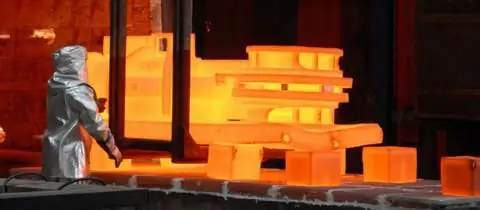
Cryogenic treatment
Changes in the structure of alloys,which means that their properties can be achieved not only by high, but also by extremely low temperatures. Thermal treatment of alloys at t below zero is called cryogenic. This technology is widely used in various sectors of the national economy as a supplement to high-temperature heat treatments, as it can significantly reduce the cost of thermal hardening processes.
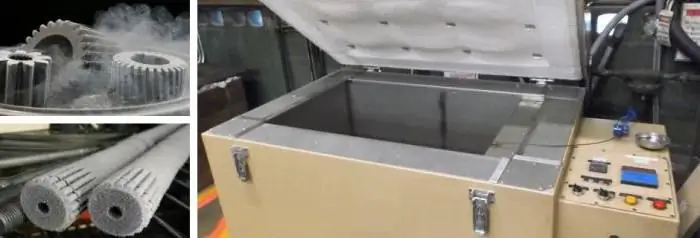
Cryogenic treatment of alloys is carried out at t -196 in a special cryogenic processor. This technology can significantly increase the service life of the machined part and anti-corrosion properties, as well as eliminate the need for re-treatments.
Thermo-mechanical treatment
A new method of processing alloys combines the processing of metals at high temperatures with the mechanical deformation of products that are in a plastic state. Thermomechanical treatment (TMT) can be of three types according to the method of completion:
- Low-temperature TMT consists of two stages: plastic deformation followed by quenching and tempering of the part. The main difference from other types of TMT is the heating temperature to the austenitic state of the alloy.
- High-temperature TMT involves heating an alloy to a martensitic state in combination with plastic deformation.
- Preliminary - deformation is performed at t 20, followed by hardening and tempering of the metal.
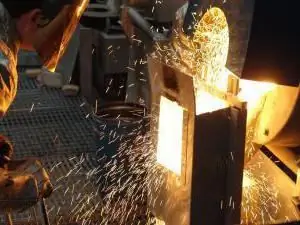
Chemical-thermal treatment
Change the structure and properties of alloysit is also possible with the help of chemical-thermal treatment, which combines thermal and chemical effects on metals. The ultimate goal of this procedure, in addition to imparting increased strength, hardness, and wear resistance to the product, is also to impart acid resistance and fire resistance to the part. This group includes the following types of heat treatment:
- Cementation is carried out to give the surface of the product additional strength. The essence of the procedure is to saturate the metal with carbon. Carburizing can be done in two ways: solid and gas carburizing. In the first case, the processed material, together with coal and its activator, is placed in a furnace and heated to a certain temperature, followed by holding it in this environment and cooling. In the case of gas carburizing, the product is heated in an oven up to 900 under a continuous stream of carbonaceous gas.
- Nitriding is a chemical-thermal treatment of metal products by saturating their surface in nitrogen environments. The result of this procedure is an increase in the tensile strength of the part and an increase in its corrosion resistance.
- Cyanidation is the saturation of a metal with nitrogen and carbon at the same time. The medium can be liquid (molten carbon- and nitrogen-containing s alts) and gaseous.
- Diffusion plating is a modern method of imparting heat resistance, acid resistance and wear resistance to metal products. The surface of such alloys is saturated with various metals (aluminum, chromium) and metalloids (silicon, boron).
Featuresheat treatment of cast iron
Cast iron alloys are subjected to heat treatment using a slightly different technology than non-ferrous metal alloys. Cast iron (gray, high-strength, alloyed) undergoes the following types of heat treatment: annealing (at t 500-650), normalization, hardening (continuous, isothermal, surface), tempering, nitriding (gray cast irons), aluminizing (pearlitic cast irons), chromium plating. All these procedures as a result significantly improve the properties of the final cast iron products: increase the service life, eliminate the likelihood of cracks during use of the product, increase the strength and heat resistance of cast iron.
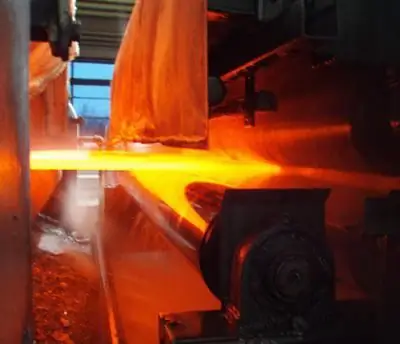
Heat treatment of non-ferrous alloys
Non-ferrous metals and alloys have different properties from each other, so they are processed by different methods. Thus, copper alloys are subjected to recrystallization annealing to equalize the chemical composition. For brass, low-temperature annealing technology (200-300) is provided, since this alloy is prone to spontaneous cracking in a humid environment. Bronze is subjected to homogenization and annealing at t up to 550. Magnesium is annealed, quenched and subjected to artificial aging (natural aging does not occur for quenched magnesium). Aluminum, like magnesium, undergoes three heat treatment methods: annealing, hardening and aging, after which wrought aluminum alloys significantly increase their strength. Processing of titanium alloys includes: recrystallization annealing, hardening, aging, nitriding and carburizing.
CV
Heat treatment of metals and alloys is the main technological process in both ferrous and non-ferrous metallurgy. Modern technologies have a variety of heat treatment methods to achieve the desired properties of each type of processed alloys. Each metal has its own critical temperature, which means that heat treatment should be carried out taking into account the structural and physico-chemical characteristics of the substance. Ultimately, this will not only achieve the desired results, but also significantly streamline production processes.
Recommended:
Heat energy tariff: calculation and regulation. Heat energy meter
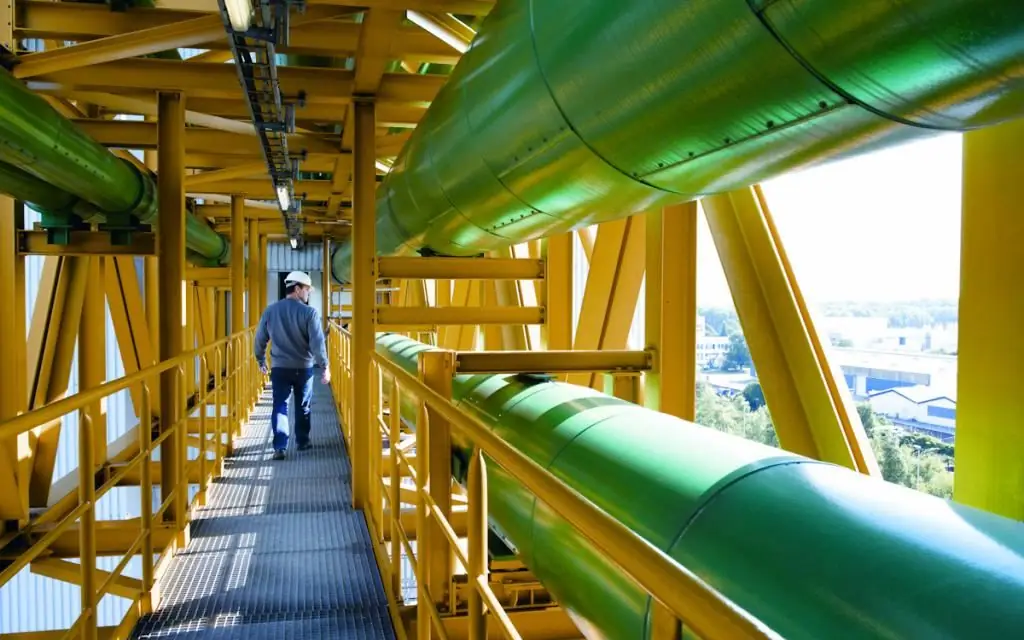
Who approves and regulates heat tariffs? The main factors affecting the cost of the service, specific figures, the trend of increasing cost. Thermal energy meters and self-calculation of the cost of the service. Prospects for billing. Varieties of tariffs for organizations and citizens. Calculation of REC tariffs, documentation required for this
Heat resistance and heat resistance are important characteristics of steels
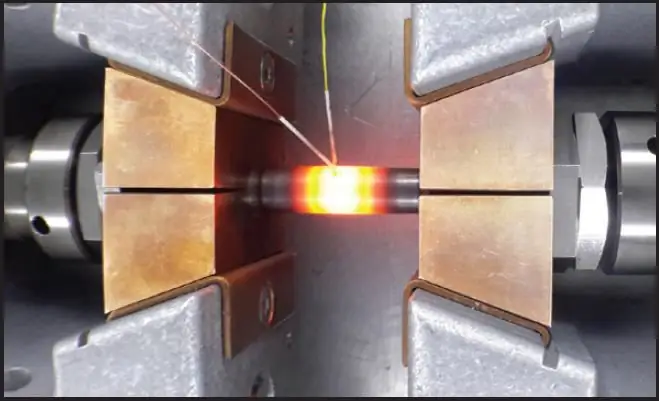
Ordinary structural steels, when heated, abruptly change their mechanical and physical properties, begin to actively oxidize and form scale, which is completely unacceptable and creates a threat of failure of the entire assembly, and possibly a serious accident. To work at elevated temperatures, materials engineers, with the help of metallurgists, created a number of special steels and alloys. This article gives a brief description of them
Heat-resistant alloys. Special steels and alloys. Production and use of heat-resistant alloys
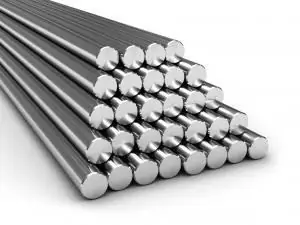
Modern industry cannot be imagined without such material as steel. We encounter it at almost every turn. By introducing various chemical elements into its composition, it is possible to significantly improve the mechanical and operational properties
Types of heat transfer: heat transfer coefficient
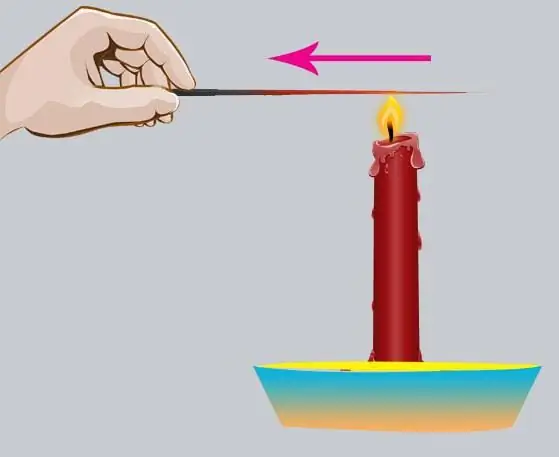
Because the heat of different substances may differ, there is a process of transferring heat from a hotter substance to a substance with less heat. This process is called heat transfer. We will consider the main types of heat transfer and the mechanisms of their action in this article
Heat treatment of steel is an important process in the production of metals
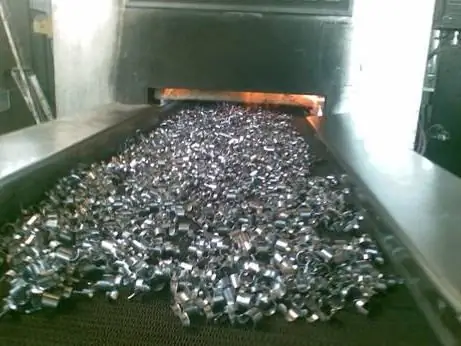
Heat treatment of steel gives any steel product the desired properties. This process is an important step in the production of iron alloy