2025 Author: Howard Calhoun | [email protected]. Last modified: 2025-01-24 13:10
Surface grinders are special machines used to clean the surface of products from unnecessary layers. Most often, this type of equipment is used for processing wooden blanks. However, a surface grinder for metal is also a fairly common type of aggregate. They are used for processing parts made of steel, aluminum, copper, etc.
A bit of history
The surface grinder was invented in 1874 in America. Initially, as a working tool, it used circles cut from whole pieces of various kinds of abrasive rocks. Since they had to be changed often, such units did not receive much distribution at that time. However, already in 1893, after the invention of artificial abrasives, surface grinders became very popular and in demand.
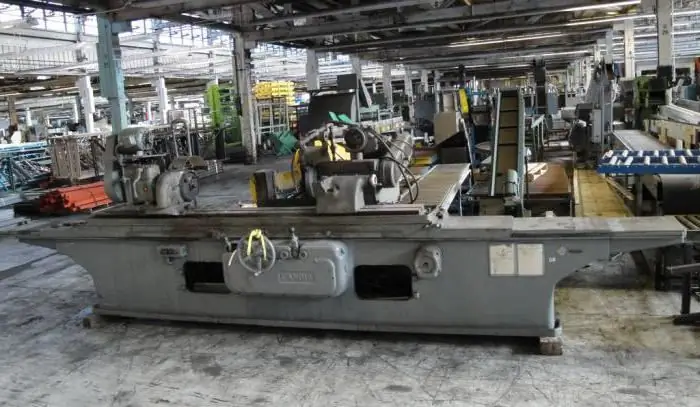
What are they used for
This type of equipment is used for:
- peeling blanks;
- cuts and cuts;
- precise surface treatment of parts;
- cleaning the teeth of the wheels;
- thread finishing, etc.
The main feature of these machines is that they are designed specifically for finishing parts with a flat surface. They are not used to refine the shape of the workpiece.
Operation principle
The operation of this type of equipment is based on a very simple principle. The workpiece is turned by means of an abrasive wheel rotating at high speed. The latter is driven by an electric motor. In this case, processing can be carried out both by the surface of the circle and by its end face. Today on sale there are also machines of this type with two circles, which are distinguished by very high productivity.
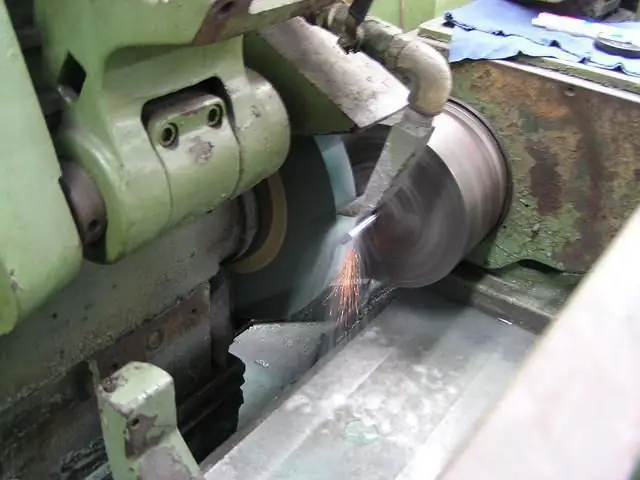
In most cases, the surface grinder functions as follows:
- The electric motor drives a gear pump that pumps oil into the channels of the hydraulic system.
- The last one, having got into the switch box, approaches the starting valve.
- When the tap is turned on, oil flows into the part feed cylinder and moves the piston, and at the same time the table fastened to it.
- At the end of its turn, the table turns the switch valve, which is responsible for directing the oil in one direction or another of the feed cylinder spool.
- The direction of the oil current is reversed and the table starts moving after it.
Design Features
Grindingmachines of this type are usually characterized by increased strength, since the parts processed on them in most cases are of considerable weight. The maximum allowable workpiece weight is 600kg and the height is 280mm.
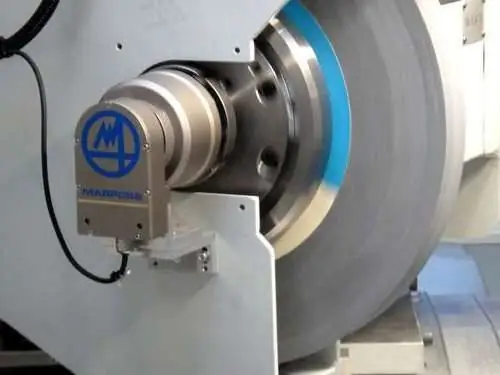
The column of this type of machine is mounted on a pedestal cast in one piece with the bed. In its middle part, it has a recess, on both sides of which there are guides. The carriage moves along the latter. Horizontal guides are fixed on it, designed for the headstock.
The workpiece in such machines is mounted either directly on the table or using special magnetic clamps. Sometimes mechanical devices are also used to fix the part.
The surface grinder table can be round or rectangular. Depending on this, the method of feeding the part is selected: longitudinal or circular. Sometimes equipment of this type is used to process parts of a very large area. In this case, the transverse feeding method is used. The table surface of the surface grinder is equipped with a special fluoroplastic coating. This ensures smooth movement and durability.
The spindle of the surface grinder can be positioned differently. On this basis, the equipment is divided into vertical and horizontal. Each of these groups has both advantages and disadvantages.
Like any other, surface grinders are designated by conditional serial numbers. Define bysuch an inscription is the functionality of the equipment is impossible. To do this, you need to study the passport of the surface grinder.
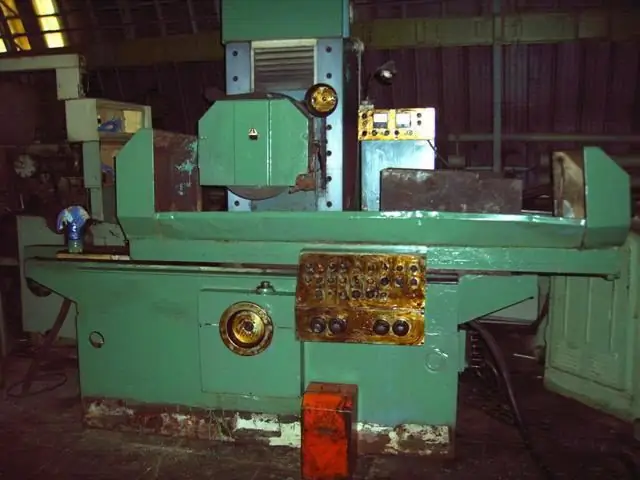
Grinding parts end face
There are several types of similar processing of parts:
- Multipass. In this case, the workpiece is placed on the working surface and moves at a speed of about 45 m/s. In this case, the part moves under the circle several times, and the latter is gradually fed into the depth until a layer of metal or wood of the required thickness is removed.
-
Single pass. This technique is used on machines with a round table. In this case, the tool is fed vertically to the full depth in one pass.
- Double-sided. On such equipment, both ends of the workpiece are simultaneously processed at once.
Sanding with peripherals
This method is used to process parts made from materials that are not too hard. Peripheral grinding happens:
- Deep. In this case, a very large layer of material is removed for each processing cycle.
- With plunge feed. This technique is used to process those blanks whose height is greater than the width.
- With intermittent feed. This technology allows the highest quality grinding even of very large workpieces.
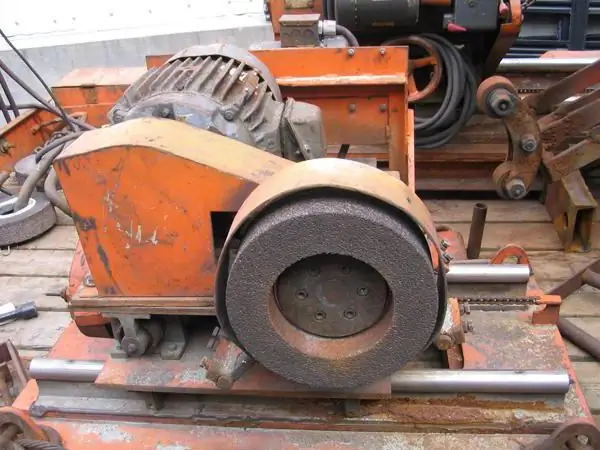
Surface grinding wheels
To make these toolsmay be in the form of a washer or a cylinder. They consist of grains of various kinds of abrasive materials of high rigidity, fastened together by a ceramic, vulcanite or bakelite bond. Grinding wheels can have different sizes and profiles. They are selected depending on the brand of the machine and the type of parts processed on it.
Optional equipment
Very often equipment such as a cooling unit is connected to a surface grinder. It is necessary in order to reduce the temperature of the working bodies of the machine during the processing of parts. This allows you to significantly extend their service life.
Also, this type of machine can use additional equipment such as feeding and receiving roller tables, speed inverters, various types of units for cleaning coolant, etc.
Specifications
Machines of this type can vary in power, performance and functionality. Schemes of surface grinding machines are presented on this page. Specifications for this type of equipment may vary. Next, let's see what parameters such machines can have using the very popular 3G71 model as an example. This unit is designed for peripheral grinding of workpieces only. Its design includes a bed, a column with a headstock, a work table and a hydraulic system.
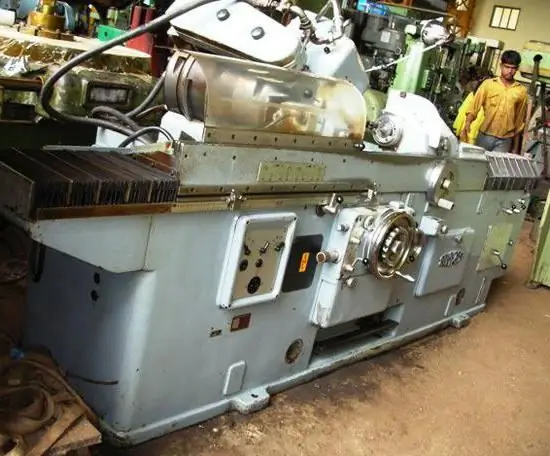
From the table below you can find out what specifications this surface grinder has.
Parameter | Meaning |
Minimum workpiece size height/width/length | 320/200/630mm |
Maximum workpiece weight | 100 kg |
Maximum distance from spindle axis to table | 80mm |
Table dimensions | 630х200 mm |
Table movement longitudinal/transverse | 70-710/235mm |
Longitudinal speed range | 5-20 m/min |
Auto cross feed speed | 0.7 m/min |
Grinding wheel dimensions | 250x25x75 mm |
Circle frequency | 3740 rpm |
Machine dimensions | 1870x1550x1980 mm |
Machine weight | 1900 kg |
Despite the fact that the 3G71 surface grinding machine was developed back in the USSR, it is still used in production and is considered quite productive and reliable. Based on it, more advanced and expensive 3G71M machines were designed.
Recommended:
Universal lathes: overview, specifications and reviews
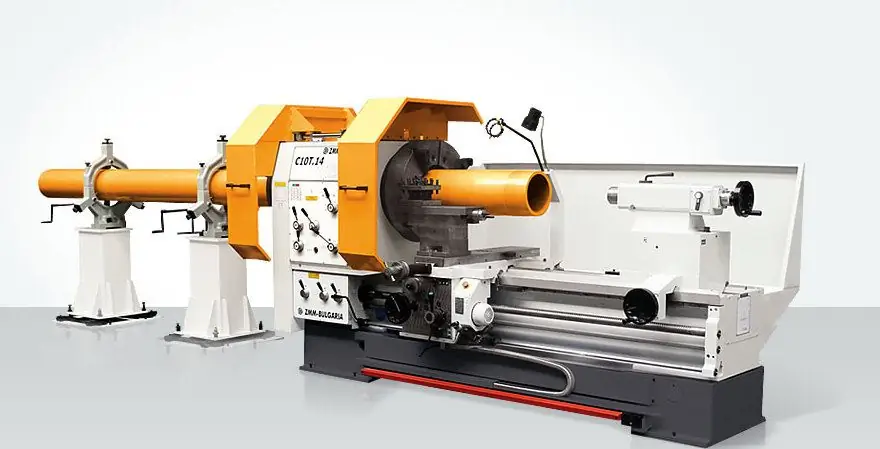
For standard operations with workpieces and not only, universal lathes with DRO are suitable. Simplified design and savings on electrics allows you to produce equipment that has a low cost. Sometimes for many customers this is the determining factor
Industrial meat grinder. Food industry equipment
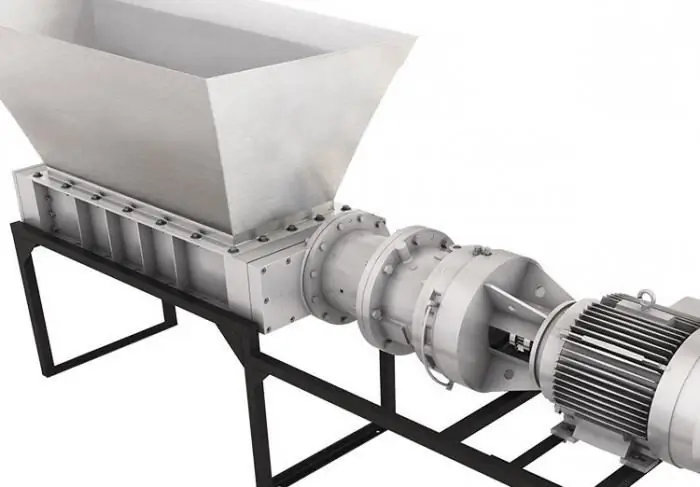
The article is devoted to industrial meat grinders. The design features, configuration options, power and tasks solved by this equipment are described
What is surface hardening of steel? What is surface hardening used for?
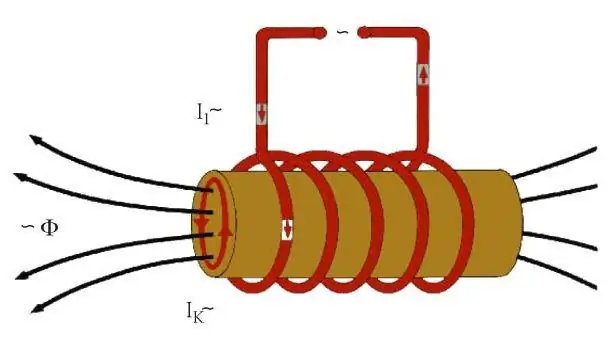
The present article is addressed to people who are far from metallurgy, amateurs who are interested in how strength differs from a good blade in an ordinary table or folding knife, surface hardening from bulk hardening, and similar issues
Culir smooth surface. Knitwear production
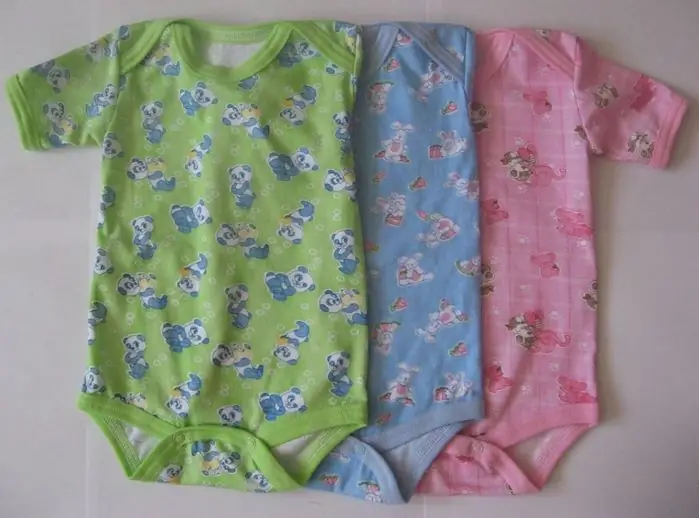
Culinary surface, what is it? Many people are familiar with the most common types of fabric, but few people come across this in everyday life. In addition, it also happens that there is such a thing in the house, but they don’t know what it is called a cooler
Passivation is The process of passivation of metals means the creation of thin films on the surface in order to protect against corrosion
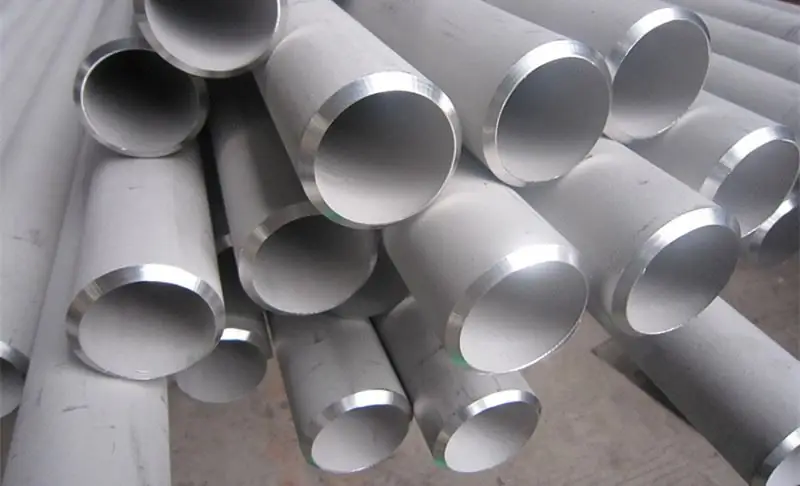
Traditional methods of protecting metals from corrosion are less and less likely to meet the technical requirements that apply to the performance properties of critical structures and materials. Bearing beams in house frames, pipeline lines and metal claddings cannot do without mechanical rust protection alone when it comes to long-term use of the product. A more effective approach to corrosion protection is the electrochemical method and in particular passivation