2025 Author: Howard Calhoun | [email protected]. Last modified: 2025-01-24 13:10
Traditional methods of protecting metals from corrosion are less and less likely to meet the technical requirements that apply to the performance properties of critical structures and materials. Bearing beams in house frames, pipeline lines and metal claddings cannot do without mechanical rust protection alone when it comes to long-term use of the product. A more effective approach to corrosion protection is the electrochemical method and, in particular, passivation. This is one of the ways to use active solutions that form a protective and insulating film on the surface of the workpiece.
Technology overview
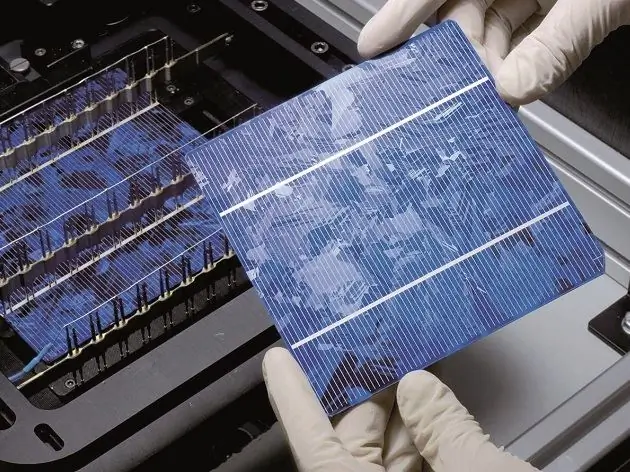
Passivation should be understood as the process of forming a thin film on a metal surface, the structure of whichcharacterized by high resistance. Moreover, the functions of this coating can be different - for example, in battery electrolytes, it not only prolongs the service life of the electrodes, but also reduces the intensity of self-discharge. From the point of view of corrosion protection, passivation is a way to increase the resistance of a material to an aggressive environment that provokes the development of rust. The very same mechanism of formation of a protective-insulating coating can be different. Electrochemical and chemical methods are fundamentally different, but in both cases, the final result will be the transition of the external structure of the workpiece to a chemically inactive state.
Principle of electrochemical anti-corrosion protection
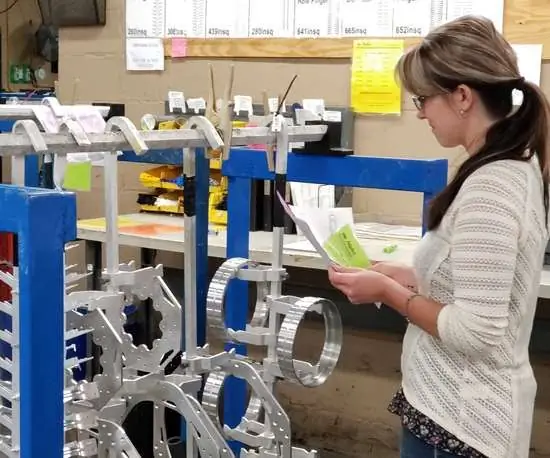
The key factor in electrochemical passivation is the effect of an external current on the target surface. At the moment of passage of the cathode current through the corroding metal structure, its potential changes in the negative direction, which also changes the nature of the process of ionization of the workpiece molecules. Under conditions of anodic exposure from the side of an external polarizer (typical for acid media), an increase in current may be required. This is necessary to suppress the polarizer and subsequently achieve full anti-corrosion protection. However, with increased passivation of the surface due to external current, the release of hydrogen increases, which leads to hydrogenation of the metal. As a result, the process of hydrogen dissolution in the metal structure begins, followed by a deterioration in the physical properties of the workpiece.
Cathodeprotection method
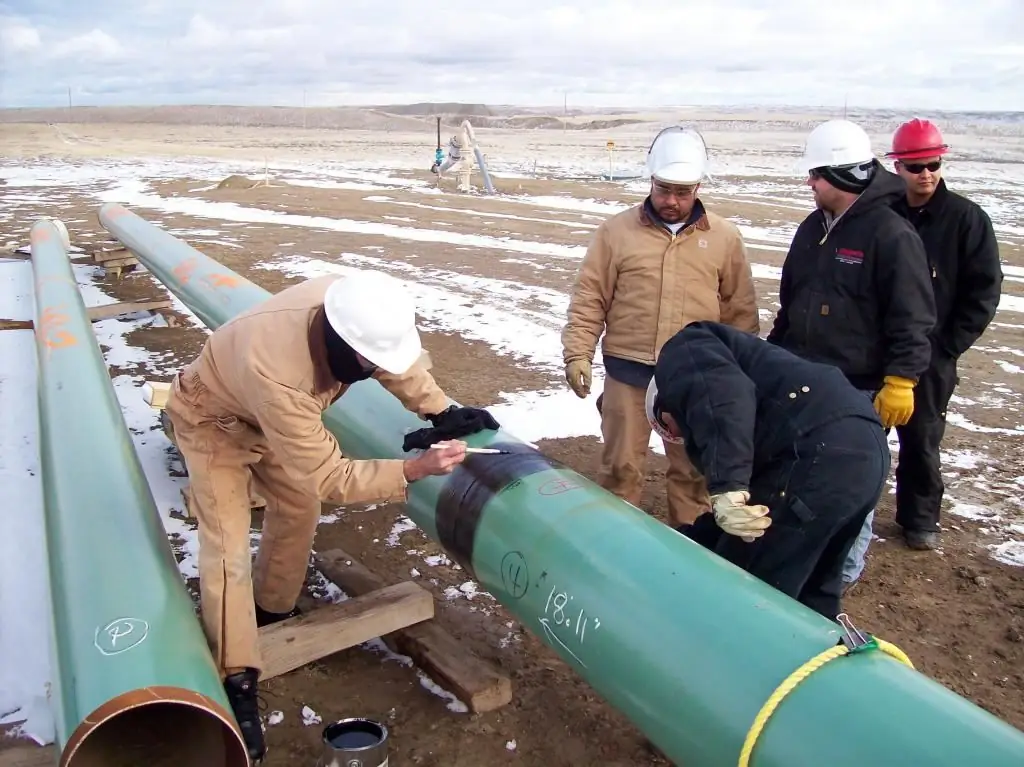
This is a kind of electrochemical anti-corrosion insulation that uses the technique of applying cathodic current. But this method can be implemented in different ways. For example, in some cases in production, a sufficient potential shift is provided by connecting the part to an external current source as a cathode. The anode is an inert auxiliary electrode. This method performs passivation of seams after welding, protects metal platforms of drilling structures and underground pipelines. The advantages of the cathodic passivation method include efficiency in suppressing various types of corrosion processes.
In addition to general rust damage, pitting and intergranular corrosion is prevented. Such methods of cathodic electrochemical action as protective and galvanic are also practiced. The main feature of these approaches is the use of a more electronegative metal as a polarizer. This element is in contact with the protected product and acts as an anode, being destroyed during the operation. Similar methods are usually used when insulating small structures, parts of buildings and structures.
Anode protection method
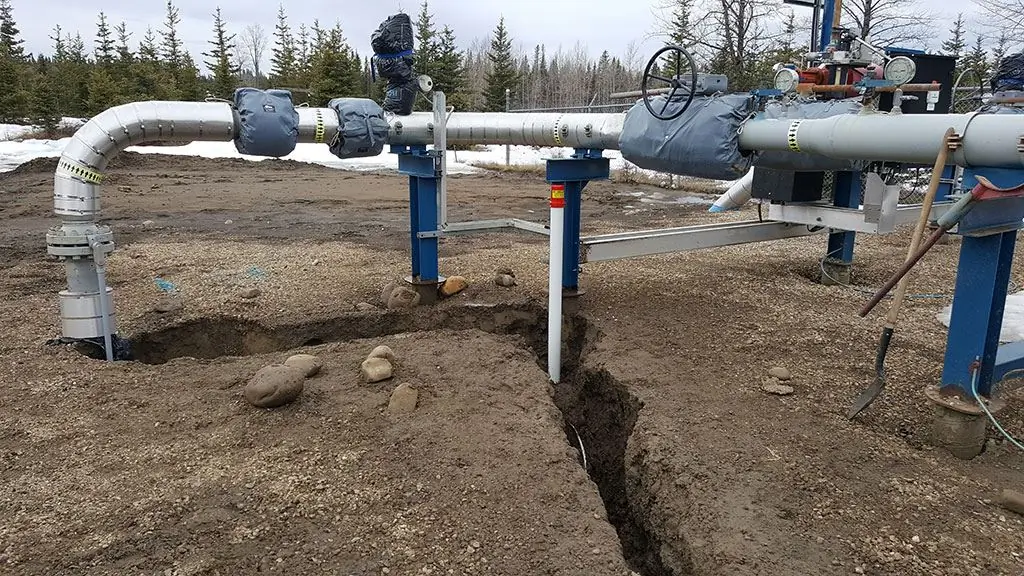
With anodic insulation of metal parts, the potential shifts in a positive direction, which also contributes to the resistance of the surface to corrosion processes. Part of the energy of the applied anode current is spent on the ionization of metalmolecules, and the other part - to suppress the cathodic reaction.
Among the negative factors of this approach is the high rate of dissolution of the metal, which is incomparable with the rate of reduction of the corrosion reaction. On the other hand, much will depend on the metal to which passivation is applied. These can be both actively dissolving materials and parts with incomplete electronic layers, the structure of which in the passive state also contributes to braking and destruction reactions. But in any case, to achieve a significant effect of anti-corrosion protection, the use of large anode currents is required.
From this point of view, this method is not advisable to use for short-term maintenance of insulation, however, low energy costs for maintaining the superimposed current fully justifies anodic passivation. By the way, the formed protection system in the future requires a current strength of only 10-3 A/m2.
Use of chemical inhibitors
An alternative technological approach to increasing the resistance of metals when operating in aggressive environments. Inhibitors provide chemical passivation, which reduces the intensity of dissolution of metals and, to varying degrees, eliminates the harmful effects of corrosion damage.
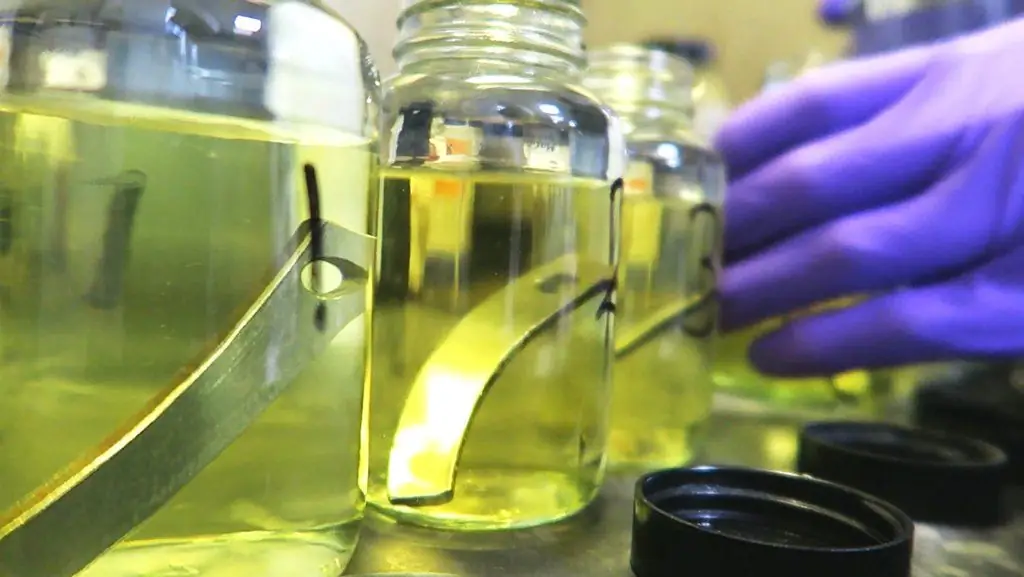
In itself, an inhibitor is, in a sense, an analogue of the superimposed current, but with a chemical or electrochemical combined action. Organic and inorganic substances act as activators of the protective film, and more often -specially selected complex compounds. The introduction of an inhibitor into an aggressive environment causes changes in the structure of the metal surface, affecting the kinetic electrode reactions.
The effectiveness of protection will depend on the type of metal, external conditions and the duration of the entire process. Thus, in the long term, the passivation of stainless steel will require more energy resources to counteract an aggressive environment than in the case of brass or iron. But the mechanism of action of the inhibitor itself will still play a key role.
Inhibitors-passivators
Active corrosion protection according to the principles of formation of passive resistance can be formed by different inhibitors. Thus, adsorption compounds in the form of anions, cations, and neutral molecules are widely used, which can have a chemical and electrostatic effect on a metal surface. These are universal means of anti-corrosion protection, but their effect is reduced in environments where oxygen polarization dominates. For example, a special inhibitor with oxidizing properties must be used to passivate stainless steel. These include molybdates, nitrites, and chromates, which create an oxide film with a positive polarization shift sufficient to release oxygen molecules. On the surface of the metal, chemisorption of the resulting oxygen atoms occurs, blocking the most active areas of the coating and creating an additional potential to slow down the dissolution reaction of the metal structure.
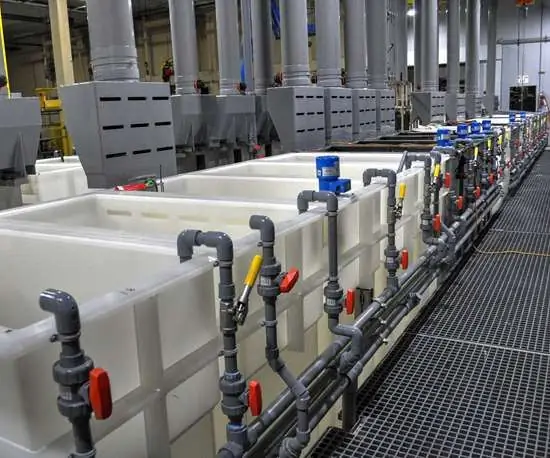
The use of passivation in the protection of semiconductors
The operation of semiconductor elements under high voltage requires a special approach to corrosion protection. In relation to such cases, the passivation of the metal is expressed in the circular isolation of the active region of the part. An electrical edge protection is formed using diodes and bipolar transistors. Planar passivation involves the creation of a protective ring, as well as coating the crystalline surface with glass. Another method of mesa passivation involves the formation of a groove in order to increase the maximum allowable stress level on the surface of a structural metal crystal.
Modification of anti-corrosion film
The coating formed as a result of passivation allows a variety of additional reinforcement. This can be plating, chrome plating, painting and creating a conservation film. Methods of auxiliary strengthening of anti-corrosion protection as such are also used. For zinc coatings, special solutions are being developed based on polymer and chromium components. For a regular galvanized pail, flushing non-reactive additives can be used.
Conclusion
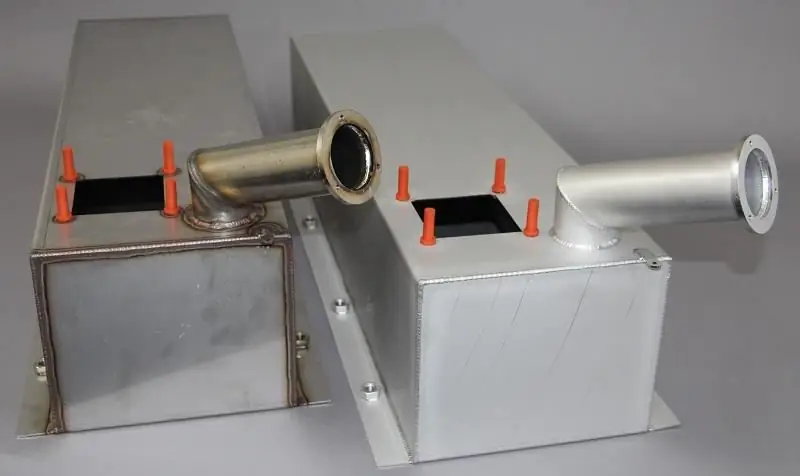
Corrosion is a destructive process that can manifest itself in different ways, but in each case it contributes to the deterioration of certain operational properties of the metal. It is possible to exclude the occurrence of such processes in various ways, as well as the use of noble metals, which are characterized by an initially reducedrust sensitivity. However, due to certain financial and technological reasons, the use of standard anti-corrosion protection or the use of metals with high corrosion resistance is not always possible.
Passivation becomes the optimal solution in such cases - it is a relatively affordable and effective method of protection of metals of various types. According to some calculations, one electrode with a properly selected inhibitor can be enough to protect against corrosion an 8-kilometer underground pipeline line. As for the disadvantages, they are expressed in the technical complexity of using electrochemical passivation methods in principle.
Recommended:
Tread protection against corrosion. The main ways to protect pipelines from corrosion
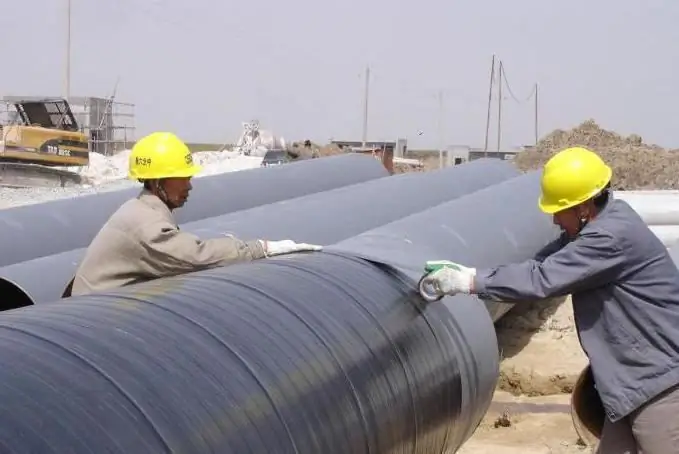
Protective corrosion protection is a universal solution when it is required to increase the resistance of metal surfaces to moisture and other external factors
Pitting corrosion: causes. Methods for protecting metals from corrosion
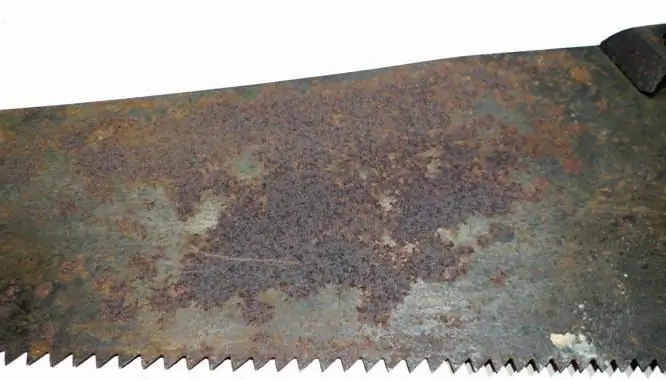
During the operation of metal products, they are exposed to various types of destructive effects, among which pitting corrosion stands out as the most dangerous and unpredictable
What is surface hardening of steel? What is surface hardening used for?
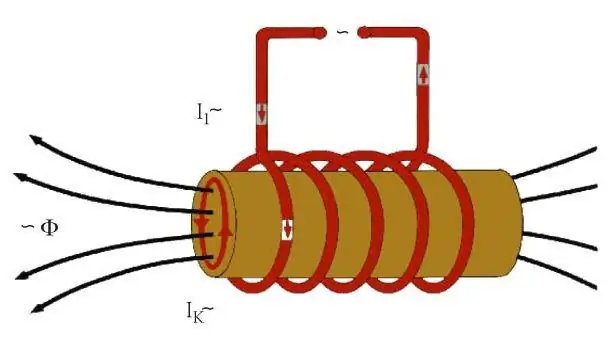
The present article is addressed to people who are far from metallurgy, amateurs who are interested in how strength differs from a good blade in an ordinary table or folding knife, surface hardening from bulk hardening, and similar issues
Effective methods to protect the gas pipeline from corrosion
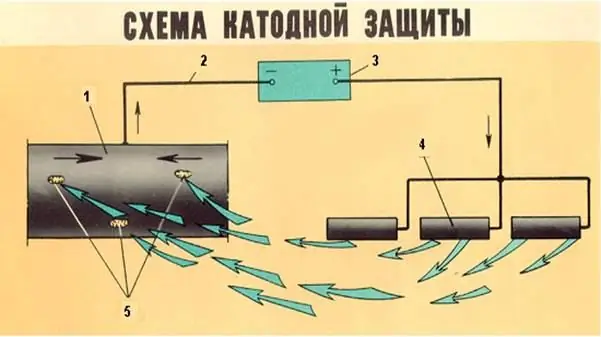
Protection of gas pipelines from corrosion: effective methods, features, special compositions, photos. Active and passive protection of gas pipelines from corrosion: types, processing technique, duration of action. How to protect underground gas pipelines from corrosion?
Welder's mask is a reliable means of protection against the most harmful factors of the welding process
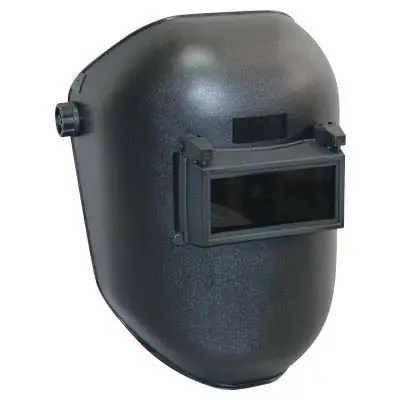
Of course, metal welding is one of the most dangerous for humans, because all welding work is accompanied by a constant release of harmful substances and factors. Some of the most dangerous are: electric arc, bright glow, toxic gases, infrared and ultraviolet radiation