2025 Author: Howard Calhoun | [email protected]. Last modified: 2025-01-24 13:10
Sponge iron is obtained by reducing concentrates or high-quality iron ores under conditions of exposure to relatively low temperatures - less than 1100 degrees Celsius. Such processes exclude the smelting of the ore and its sintering.
History
It was proved quite a long time ago that it is possible to get iron from ore right away. Under laboratory conditions, this process is easy to implement. As a result, metallurgists were faced with the task of creating technological methods for extracting iron in industrial volumes directly from ore. Now such methods have been found and introduced into production.
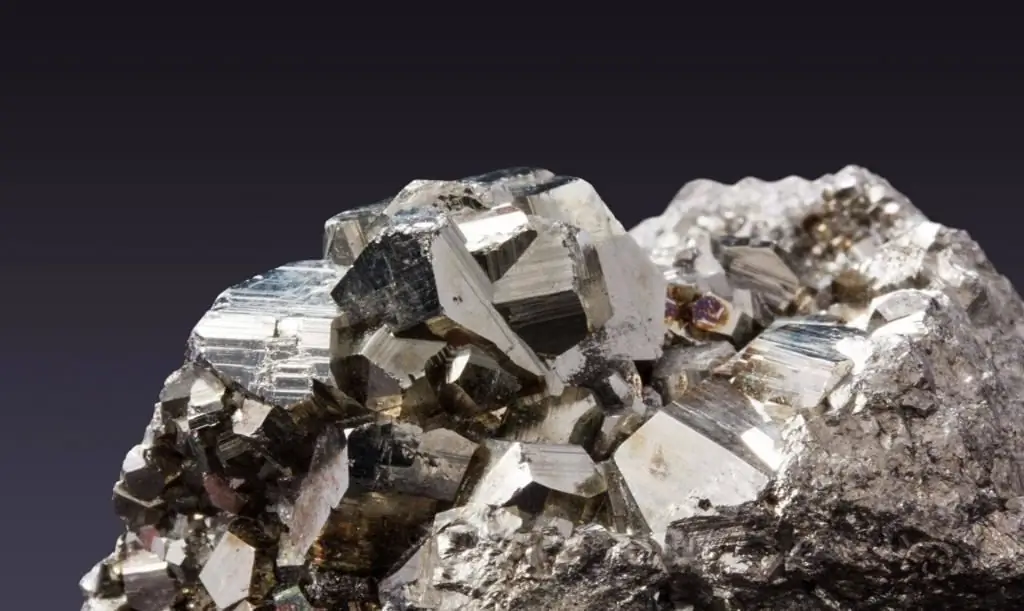
Iron obtained directly from ore is called spongy. And the retrieval methods are domainless or direct restore methods.
The first experiments in obtaining sponge iron without the use of blast-furnace melting in the Soviet Union were undertaken in the 50s of the last century.
The first production of this metal was introduced into the industry in the 70s. The first technological methods for producing sponge iron without the use of a blast furnace differed insignificantly.performance. The resulting product contained a wide variety of impurities.
Natural gas gave a new impetus to this production. In the 80s of the XX century, it began to be widely used in mining and metallurgical production. Then it was found that it is ideal for the implementation of the direct reduction of iron from ore. Moreover, other non-natural gases have also begun to be widely used (associated gas from oil production, gas fractions during the gasification of various coals, etc.).
Improvement of technological processes and their introduction in the 90s led to the fact that the energy intensity and capital costs of the direct reduction of iron have decreased significantly. A significant increase in non-blast iron production began.
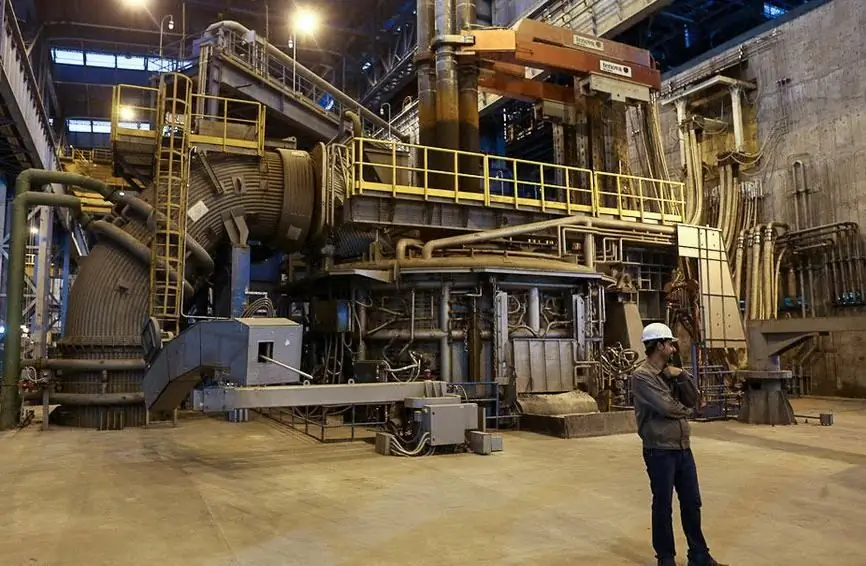
Direct non-domain production of sponge iron - processes when the metal is recovered from the ore with the help of gases, solid carbon. And also together - solid carbon and gas. It is carried out at a temperature of about 1000 degrees Celsius. At the same time, the natural rock is not brought to slagging, impurities in it are not restored, as a result of which the metal is sufficiently pure. Experts call this process and other terms:
- direct production of sponge iron;
- coke-free metallurgy;
- domainless metallurgy;
- partial metallization of ore.
Currently, methods of metal mining by such methods on an industrial scale are practiced in Russia, China, Sweden, Germany, Great Britain, Norway andother countries.
All known methods are divided into two groups:
- iron is formed when the ore is exposed to a gaseous reducing agent;
- under the influence of a solid reducing agent on iron ore.
Methods for producing sponge iron using a domainless method have been patented for almost five hundred.
Recovery of iron with a gaseous substance
Hydrogen and carbon monoxide are used for gaseous reduction. Usually, a method is used when iron ore is crushed and heated to 850 degrees, followed by roasting. Then it is sent to a rotary tube furnace. There, the metal is reduced under the influence of reducing gases moving towards the ore mass. Before leaving the furnace, it enters the cooling container. The final product is then ground using a ball mill.
Subsequently, the mass passes through a special magnetic separator. The iron sorted by the separator then goes under the press, which forms sponge iron into briquettes.
Obtaining iron by a solid reducing agent
If the production uses the technology of producing sponge iron by solid reduction, then this method involves the following operations:
- crushing and grinding ore;
- to achieve a high concentration of iron, no more than 3% gangue, magnetic enrichment is carried out;
- enriched ore is mixed with organic fuel, which includes sawdust and other similar organicstructures;
- creation of the resulting mass of briquettes, followed by their transfer to the kiln for firing.
Recovery of iron occurs due to the combustion of carbon contained in briquettes.
The obtained sponge iron, both in solid and gaseous reduction, is subsequently sent to standard processing to obtain steel.
Remelting is usually carried out in electric furnaces, while the required amount of carbon and other impurities are introduced into the metal.
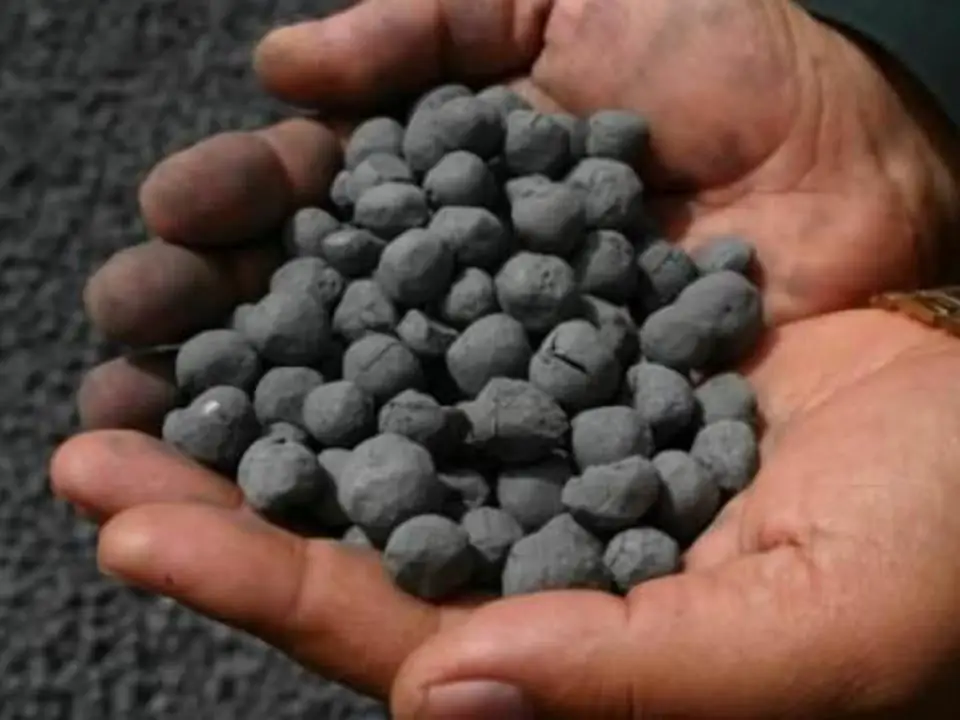
Classification of processes
Metallurgists classify the processes of blast-furnace iron production according to the type of final product, namely:
- production of materials for blast furnace with partial metallization (from 30 to 50 percent);
- production of spongy iron, a solid product, highly metallized (from 85 to 95 percent), for subsequent processing into steel;
- production of bloomery iron, plastic metallized product;
- production of semi-finished or liquid iron for further smelting process.
Direct Restore Products
Four types are commonly classified as direct iron reduction products:
- spongy;
- metallized charge;
- flashy;
- cast iron or carbon intermediate.
Spongy iron
It is obtained as a result of processes when the reduction of metals occurs without melting, at a temperature of less than 1000-1200 degrees Celsius. proceedingfrom what the initial raw material was, solid sponge iron - porous structures, or pellets. In certain cases, it is a metal powder. When this metal is also characterized by the fact that it has a fairly high porosity (shaped like a sponge) due to the fact that during the restoration, the volumetric characteristics of the raw material have undergone minor changes.
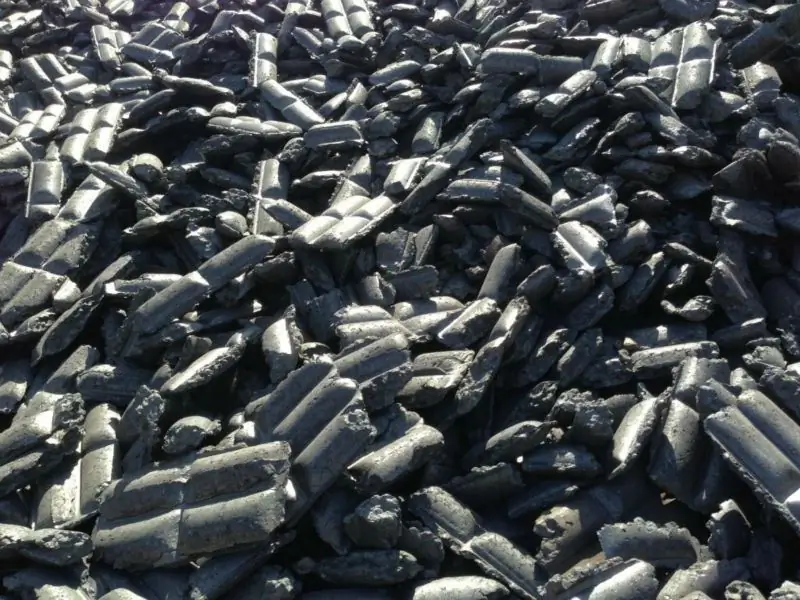
The porous surface of such iron leads to a high degree of oxidation during storage and transportation, when exposed to an unfavorable environment (high humidity).
The chemical composition of this metal owes its composition to the original raw material (ore). Compared to scrap, sponge iron is cleaner. It has a minimal presence of impurities of other metals.
Also, sponge iron obtained by direct reduction is also distinguished by the presence of barren rocks in it. Due to the fact that the source material is rich concentrates and ores, it is not subjected to additional purification. As a result, iron contains all the inclusions of the waste rock of the original ore.
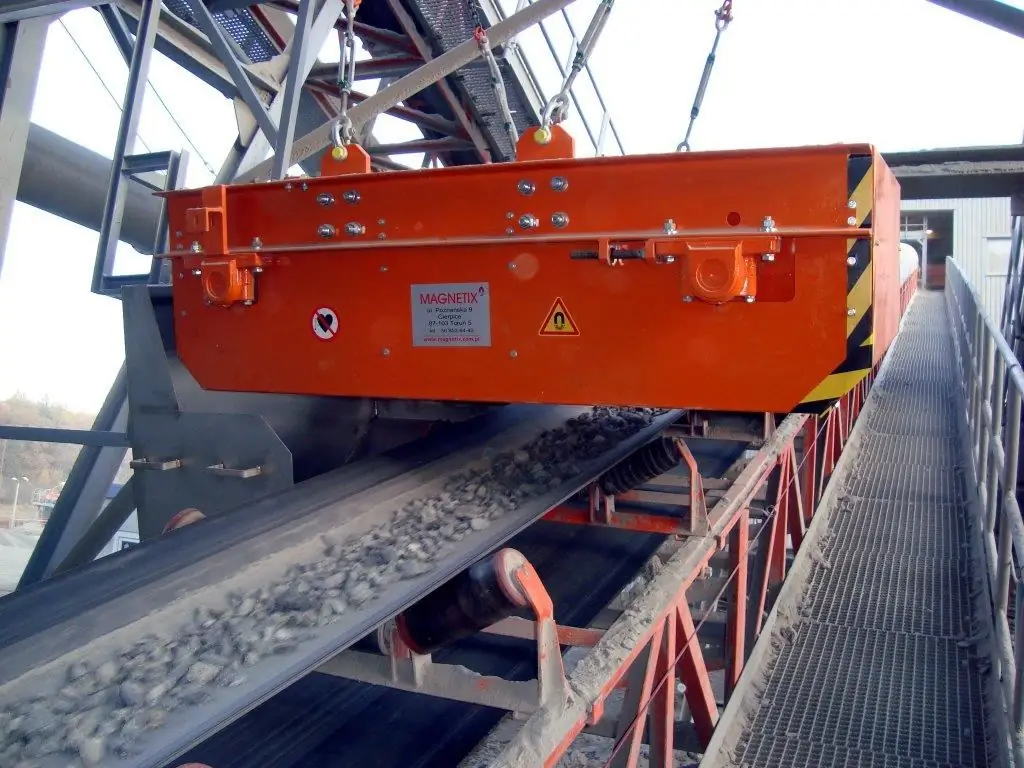
Sponge iron has found its way into steel making, iron powder making and copper carburizing.
Metallized charge
Partially reduced iron is called metallized charge. It is used to cool the smelting process, as well as for subsequent melting in blast furnaces. The recovery level of the metallized charge is below 80%. Sponge iron is much cleaner, degreeits recovery is over 90%.
Scream iron
Damn-free hot iron is produced in tubular rotary kilns. Its recovery temperature ranges from 1100 to 1200 degrees Celsius. This product is a small metal particles in which slag impurities. The volume of slag in bloomery iron is high, about 10-20 percent. This iron is distinguished by significant impurities of sulfur and phosphorus.
They use bloom for subsequent remelting in blast furnaces. Separate technologies use this product in steelmaking in electric furnaces.
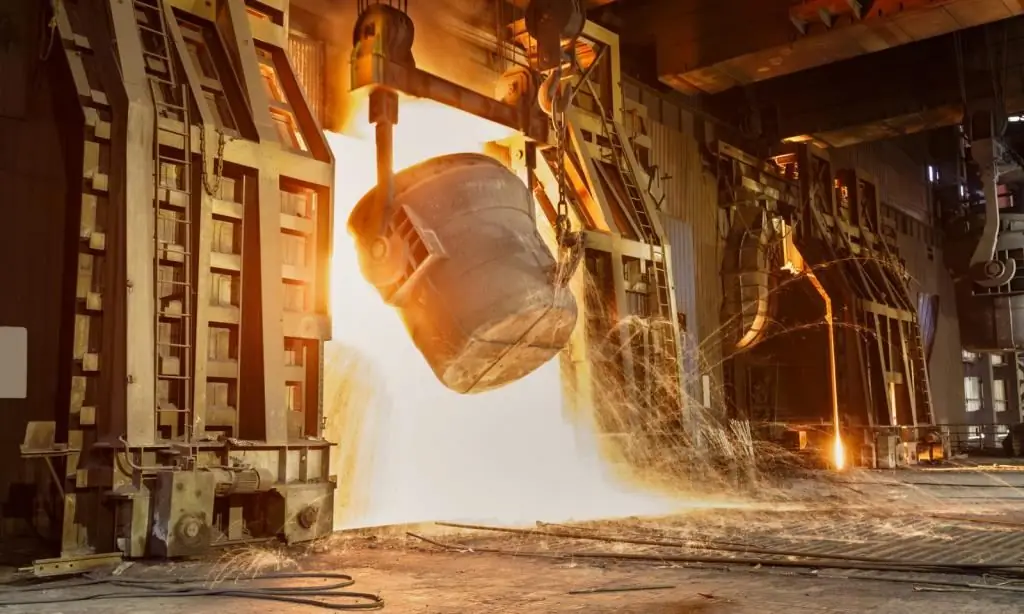
Carbon intermediate or cast iron
These products are produced by solid fuel recovery technology. According to their characteristics, they are similar to those smelted in blast furnaces. Moreover, semi-carbon or pig iron is sometimes obtained with much less foreign impurities.
Further work with these materials to obtain steel is carried out in traditional ways.
Recommended:
What is a property deduction, who is en titled to it and how to calculate it? Article 220 of the Tax Code of the Russian Federation. property tax deductions
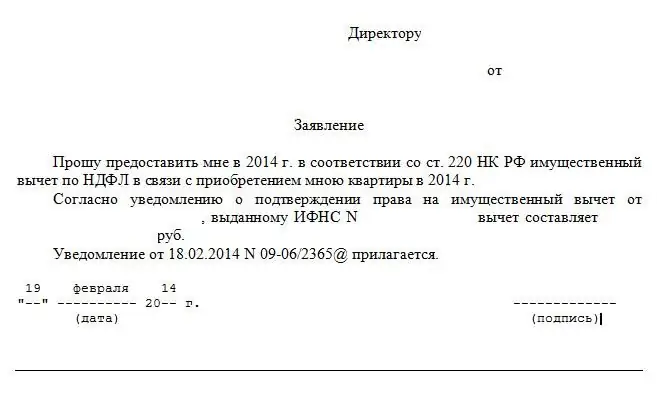
Russia is a state in which citizens have a lot of rights and opportunities. For example, almost every citizen of the Russian Federation has the right to receive a property deduction. What it is? Under what conditions can it be issued? Where to go for help?
Property tax on children: should minor children pay property tax?
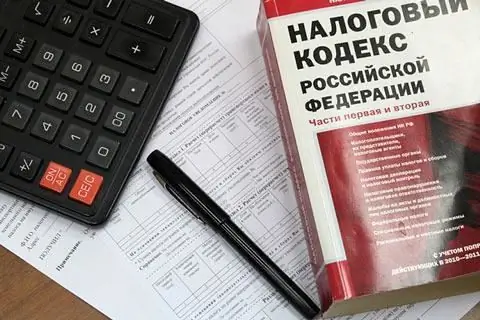
Tax disputes in Russia are something that brings quite a lot of problems to both the population and the tax authorities. Payments for the property of minors require special attention. Should children pay taxes? Should the population be afraid of non-payment of the specified fee?
Common property of an apartment building - what is it? Maintenance and repair of the common property of an apartment building
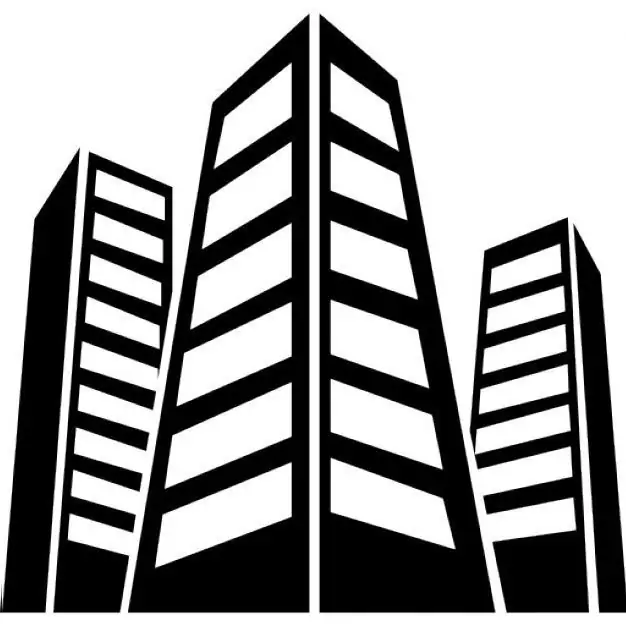
The legislation of the Russian Federation adequately regulates in detail the procedure for the use of common house property by apartment owners. What are the key provisions of the relevant rules of law?
Property tax for pensioners. Do pensioners pay property tax?
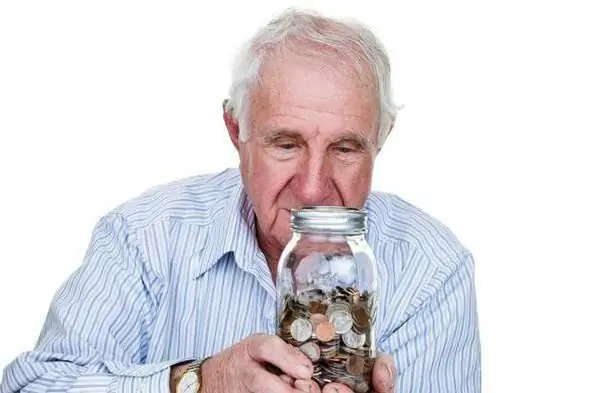
Pensioners are eternal beneficiaries. Only not everyone knows what their capabilities extend to. Do pensioners pay property tax? And what rights do they have in this regard?
Types of property insurance. Voluntary insurance of property of citizens of the Russian Federation. Property insurance of legal entities
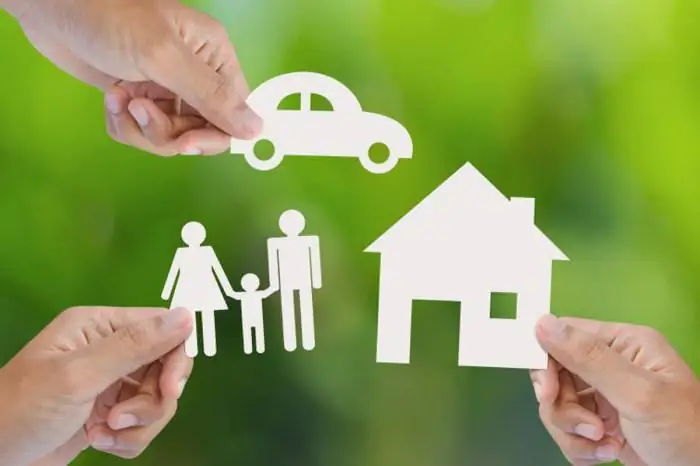
Voluntary property insurance of citizens of the Russian Federation is one of the most effective ways to protect your interests if a person owns some property