2025 Author: Howard Calhoun | [email protected]. Last modified: 2025-01-24 13:10
JSC "Bor glass plant" is the leading manufacturer of auto glass in Russia. Since 1997 it has been owned by the AGC Europe group of companies. The company also produces: dishes, mirrors, polished glass and other products.
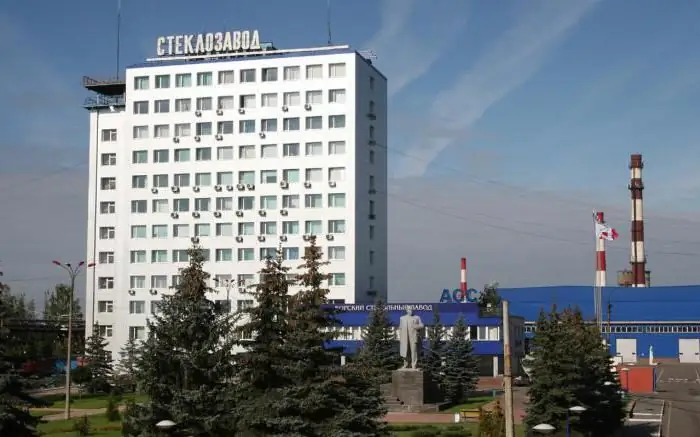
History
In the late 1920s, the government of the young Soviet republic decided to build a new glass factory in a town called Bor in the Nizhny Novgorod Region. The first work began on 1930-05-06, production - 1934-01-02.
With the development of motor transport, it became necessary to mass-produce windshields of proper quality. In 1940, the Borsky glass factory mastered the production of triplex. Over time, the celluloid base was replaced with a safer polyvinyl butyral film. Since 1948, the company has been producing "Stalinite" - tempered auto glass for rear and side glazing.
In 1997, the Bor Glassworks (BSZ) was purchased by Glaverbel, later renamed AGC Europe. The change of ownership has transformed the business. The latest in productionequipment, improved working conditions, increased productivity and wages. Since 2013, a Board of Honor has been installed in each workshop. Its heroes are chosen by the workers themselves.
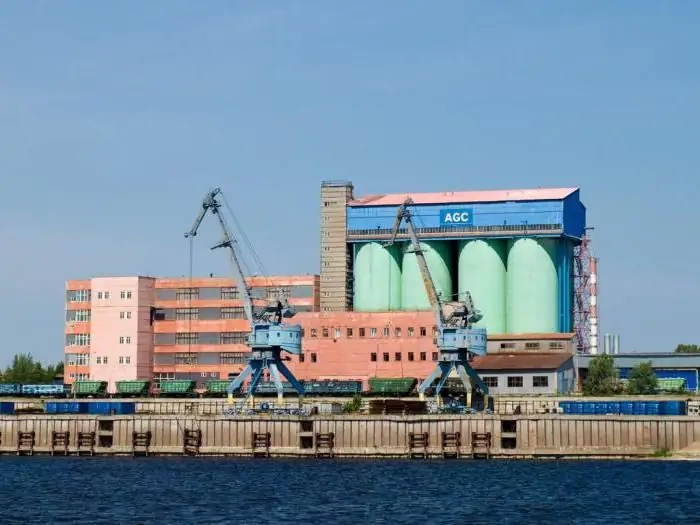
Triplex workshop
Bor Glassworks, whose products were previously supplied mainly to domestic automobile factories, has become a major supplier for such giants as Volkswagen, Toyota, Renault and others over the past decade.
Thanks to the new triplex line, launched in 2002, we managed to take a leading position in the industry. The quality of auto glass has approached the world level. The computerized complex is equipped with imported equipment:
- Bystronic cutting and processing line;
- Benteler flat and pitched glass washer-dryers;
- Svecia silk screen printing system;
- Cnud bending oven;
- Tamglass vacuum prepress oven;
- SCHOLZ autoclave;
- line of final control Sklopan.
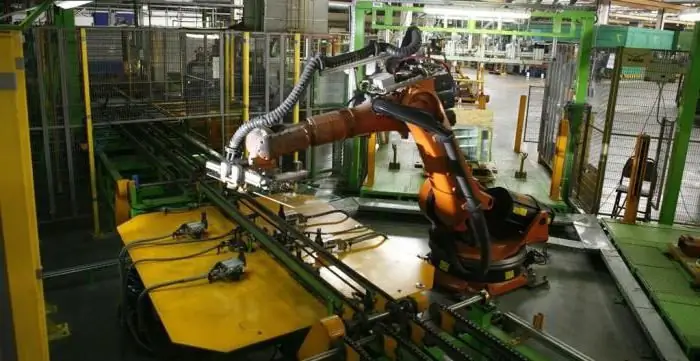
Hardening shop
Here, car glass is heat-treated to increase its strength. In 2012, the loading and unloading section of the horizontal kiln was upgraded. The 30-year-old equipment was replaced with new one. Modernization made it possible to improve the quality control of glass geometry by an order of magnitude. Now the machine decides whether a particular instance meets the specified parameters - this completely eliminates the notorious "human factor". Besides,it became possible to produce Triplex models in four streams, which increased productivity by 15%.
In the event of an unforeseen repair or changeover of equipment, it will not be necessary to stop the technological process thanks to new storage tanks with a reserve of glasses. The operation of transferring products with wrapping paper is also automated. This made it possible to get rid of defects such as scratches.
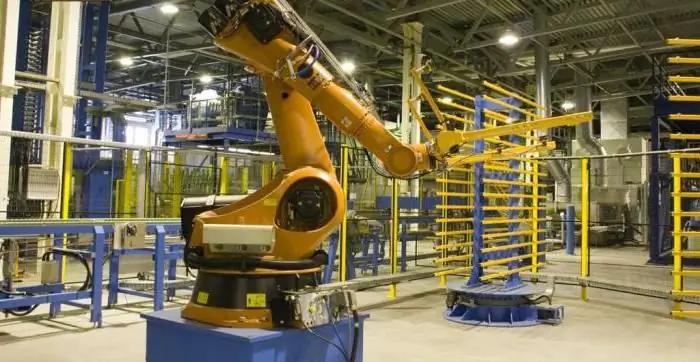
Packaging shop
Bor glass factory pursues a policy of minimizing manual labor. In 2013, a new packaging line was installed. The glass is loaded by a robotic arm. Two other robots cut off excess film - this is the requirement of foreign partners who were not satisfied with the quality of the cut at the ends.
Also, at the request of customers, products are checked for optical distortion, but not "by eye", but automatically. For this purpose, the Borsky Zavod purchased the latest Aura diagnostic unit. It checks every centimeter of glass using optical sensors. The task of the operator is only visual inspection for scratches, cracks, abrasions. At the last stage of loading products into cassettes, machines work.
Thus, 7 robots on the packaging line allowed to halve the number of staff, completely eliminate hard work, while significantly increasing productivity. When the line is fully loaded, the glass descends from it every 23-25 seconds. The quality of the products sold is comparable to the world's best analogues.
Installation of sensors
Besides automated linepackaging, robots for loading lines BRL-1 and BRL-2 were put into operation. They handle the gluing of bracket holders, mirrors, rain sensors with lightning speed. As a result, jewelry accuracy of positioning of these elements is achieved. Previously, the process was semi-automatic, and products were unloaded manually. Now productivity has increased, the cycle time is 17 seconds per glass.
Stretching-center
This is a brand new lot that started development in 2012. New German equipment made it possible to produce our own elastic stretch film. Previously, it was bought in the Czech Republic at a high price.
The launch of the site made it possible, on the one hand, to save up to 15%, on the other hand, to improve the quality due to additional cleaning on a special machine. A PVB-film warehouse has recently been added to the Triplex workshop, which used to be located several kilometers away.
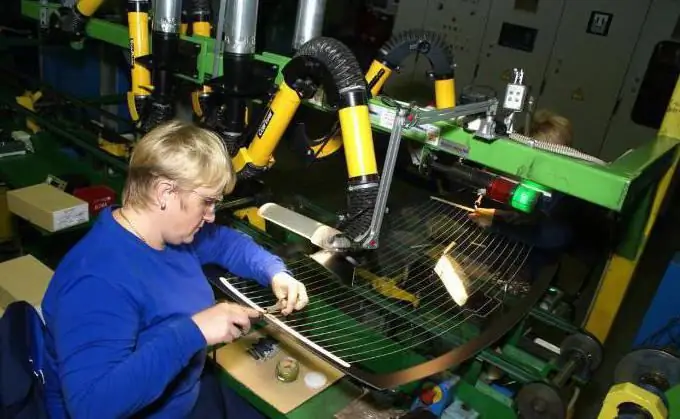
The customer is always right
Bor glass factory strives to satisfy any requirements of customers. For example, in 2012 the company began to cooperate with Peugeot. This auto concern makes very strict requirements for the quality and aesthetic appearance of the purchased products. In particular, the client was not satisfied with the fact that the rear window heaters were visible from the passenger compartment.
The factory workers went forward. Special equipment was purchased - a new printing machine closes the heating taverns with ceramic paint. The line capacity is 240 units per hour. The quality is checked at each stage repeatedly: visually by the operator andautomatically by optical sensors. As a result, the client is satisfied, and the plant receives additional profit.
Cooperation
For 80 years of its history, the Bor glass factory has been at the forefront of the industry. Product quality, strict compliance with the requirements of partners, continuous development remain the main priority of the company. Its customers are the world's leading automakers: Nissan, Toyota, Mitsubishi, Skoda, Renault, Peugeot. Recently, serial production of triplex glass for Citroen and Volkswagen has been launched. Products for old customers continue to improve, with new glass triple printing equipment installed especially for Peugeot.
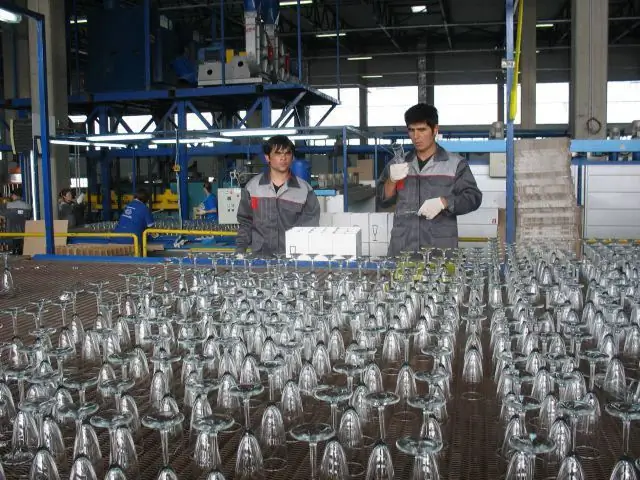
Release of tableware
The Bor glass factory is famous not only for the production of high-quality auto glass. Crockery is another pride of the company. Here is the only production of glasses, vases, glasses and other products made of tempered glass with increased mechanical and thermal strength in the post-Soviet space. Products are popular in Russia, Eastern Europe, Transcaucasia, the Middle East.
Bor glass factory: contacts
Address: 606443, Nizhny Novgorod region, Bor, highway Steklozavodskoe-1.
CEO: Shigaev Vladimir Dmitrievich.
Contact phones: (831) 59-75-506; (831) 22-00-207; (831) 22-00-210.
Fax: (83159) 28-124; (831) 22-00-208.
Recommended:
How to make glass? Glass production technology. glass products
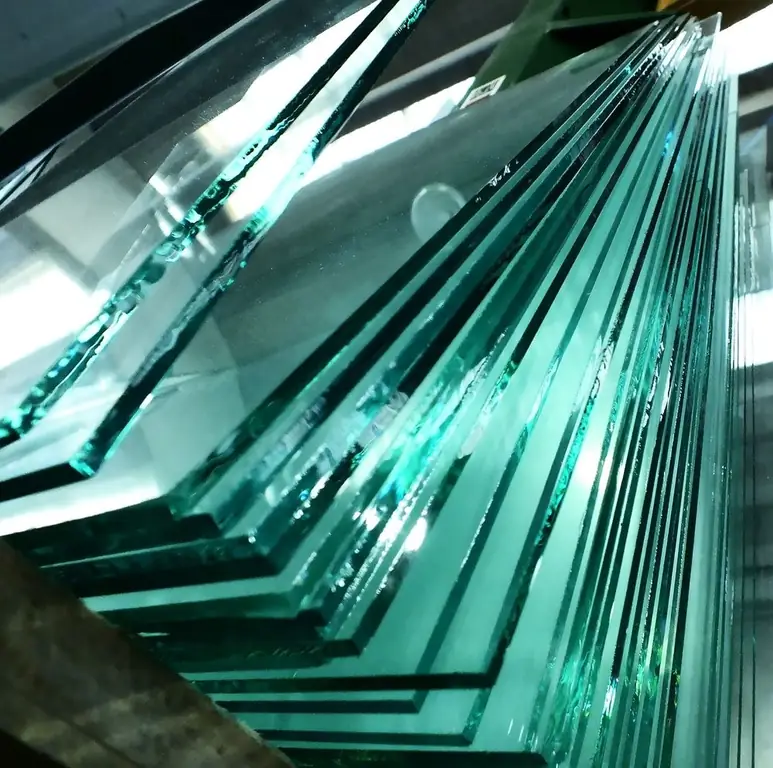
Glass is familiar to everyone. But the process of making it is extremely exciting. Each stage is important and affects the quality of the final product. The basis is sand, soda, lime. The process is almost entirely automated. Surprisingly, glass can even be made at home
JSC "Ashinsky Metallurgical Plant": history, production, products
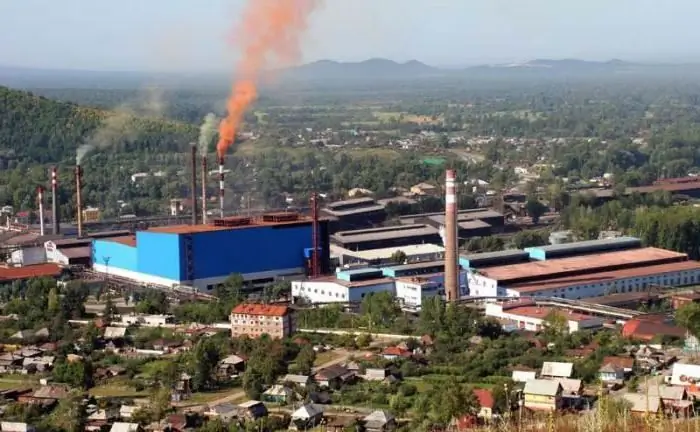
JSC "Ashinsky Metallurgical Plant" is a city-forming enterprise in the west of the Chelyabinsk region. AMZ is one of the top five Russian suppliers of thick plates, nanocrystalline and amorphous alloys. Leader in the production of tableware, household items and garden tools from stainless steel
JSC "Yaroslavl Tire Plant": description, products, production and reviews
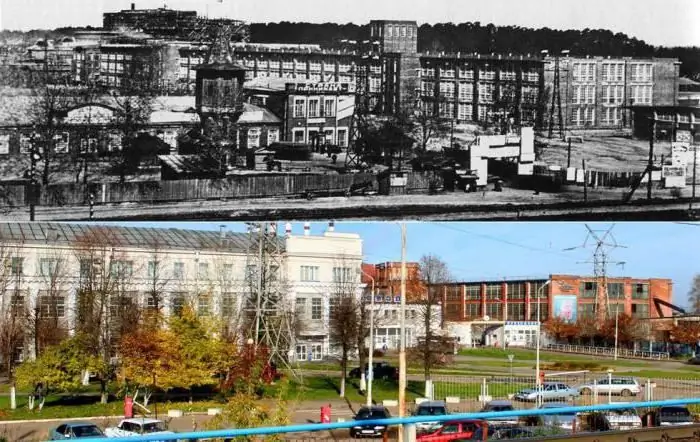
JSC Yaroslavl Tire Plant without exaggeration is the leader of the country's tire industry. Every year, the company produces about 3 million units of high quality products for various types of equipment. The company is part of the holding "Cordiant"
Bor glasses. Bor glass factory
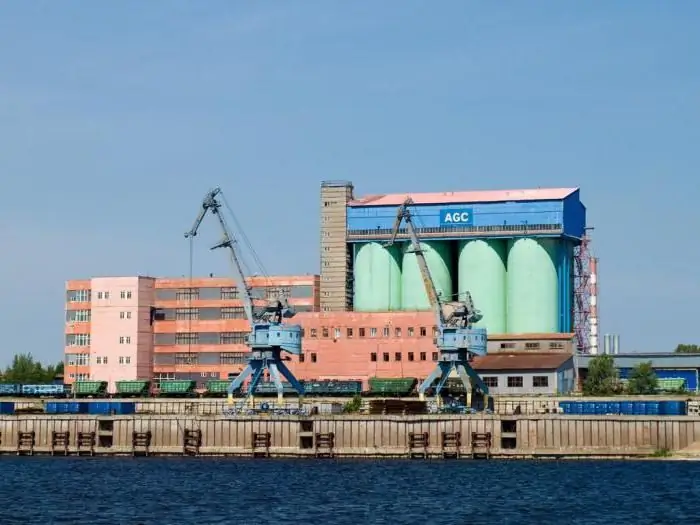
Bor Glass Factory was founded in 1930. Today it is the undisputed leader in the domestic auto glass market. The company's products comply with international standards. The main shareholder is AGC Group. Production is actively developing, the construction of triplex production buildings in 2006 raised the characteristics of products to a new level
REMIT Meat Processing Plant LLC: feedback from customers and employees, manufactured products and quality of meat products
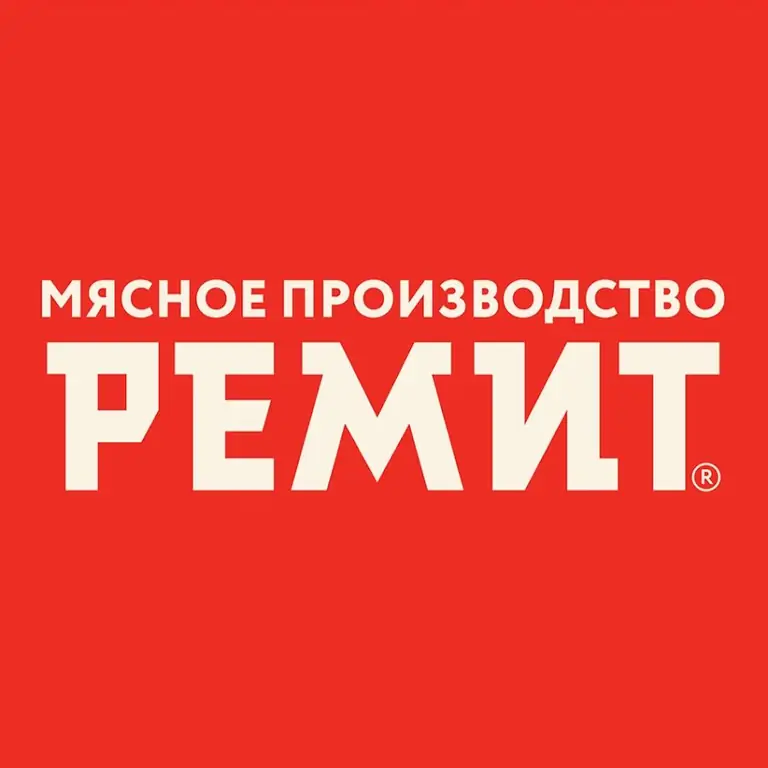
REMIT reviews are of interest to customers who are considering options for cooperation with this company, and employees who expect to get a well-paid and stable job. In this article, we will talk about this meat processing plant, what products it produces, whether its quality corresponds to the declared one, what its employees and partners say about the enterprise