2025 Author: Howard Calhoun | [email protected]. Last modified: 2025-06-01 07:12
Efficient use of resources is a condition that ensures the fulfillment of production plans. For the purpose of analysis, the organization's personnel is divided into production and administrative. Based on the name, it is clear that the first group includes employees directly engaged in the main activity of the enterprise, and the second - all the rest. For each of these groups, the average annual output is calculated and the quality of labor force use is analyzed.
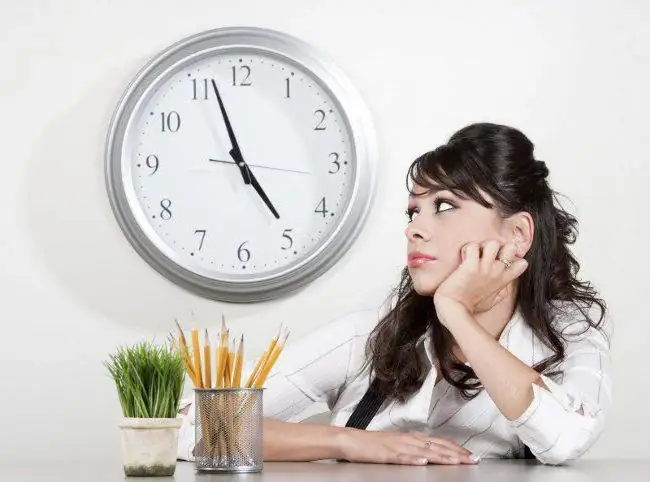
Basic concepts
The labor force analysis examines labor productivity. It shows how many products are made per hour (day, month, year). To calculate this indicator, you need to determine the average annual output and labor intensity. They best represent labor efficiency. Increasing productivity leads to higher production volumes andsaving wages.
Resource availability
The number of employed people in the enterprise is of great importance. When analyzing the availability of labor resources, the actual number is compared with the planned and indicators for the previous period for each group of workers. A positive trend is that the average annual output is growing against the background of a change (decrease) in the number of any of the groups of employed employees.
The reduction of support staff is achieved by increasing the level of specialization of persons involved in the adjustment and repair of equipment, the growth of mechanization and the improvement of labor.
The number of staff is determined by industry standards and the rational use of working time required to perform certain functions:
1. Workers: H \u003d Labor intensity: (Annual Fund of Working TimeCoefficient of Compliance with Standards).
2. Equipment workers: N=Number of unitsNumber of workers in this sectionLoad factor.
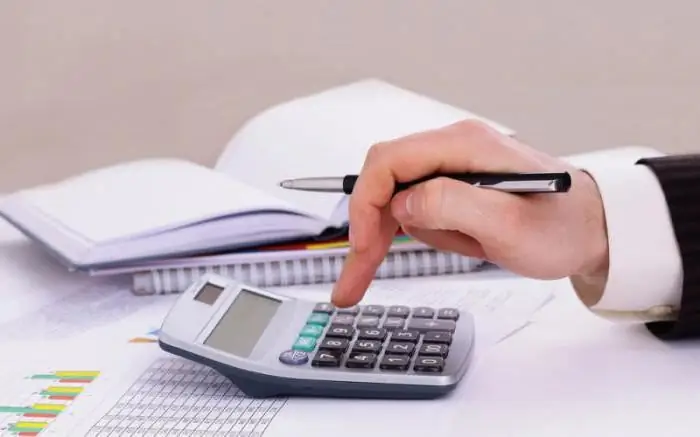
Skill level analysis
The number of employees by speci alty is compared with the standard. The analysis reveals a surplus (shortage) of workers in a particular profession.
Assessment of the skill level is calculated by summing the tariff categories for each type of work. If the actual value is lower than planned, this will indicate a decrease in product quality and the need to improve the skills of personnel. The opposite situation suggests thatworkers need to be paid a bonus for qualifications.
Management personnel are checked for compliance with the level of education of the position held. The qualification of an employee depends on age and experience. These parameters are also taken into account in the analysis. The proportion of hired and retired employees is calculated, including for negative reasons. At the next stage, the use of working time is analyzed according to the following algorithm:
1. Nominal mode=365 days - Number of weekends and holidays.
2. Private mode \u003d Nominal mode - The number of days of absence from work (vacation, illness, absenteeism, decision of the administration, etc.).
3. Useful working time fund \u003d Private modeWorking day length - Number of downtime, breaks, reduced hours.
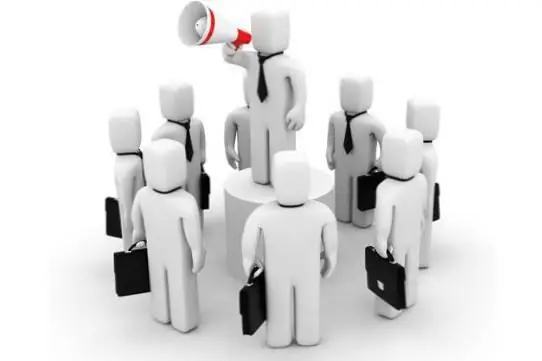
Loss of working time
Working Time Fund (FRV) is the product of the number of employees (H), the average number of days worked per year by one person (D) and the length of the day (T). If the average annual output is below the planned one, then the time losses are calculated:
- Dp=(Df - Dp)NfTp - daily.
- Tp=(Tf - Tp)DfBfH - hourly.
The reasons for such losses may be absences from work by permission of the administration, due to illness, absenteeism, downtime due to lack of raw materials or equipment malfunction. Each of these reasons is analyzed in detail. The reserve for increasing the PDF is to reduce losses that depend on laborcollective.
Time losses are calculated separately in connection with the manufacture and correction of rejected products according to the following algorithm:
- share of workers' wages in production cost;
- the amount of salary in the cost of marriage;
- the share of workers' wages in the cost price minus material costs;
- share of wages of workers involved in the correction of marriage;
- average hourly wage;
- time spent making and fixing defects.
Loss reduction=Time lostAverage annual output.
Losses can be compensated not only by a decrease in production, but also by an increase in labor intensity.
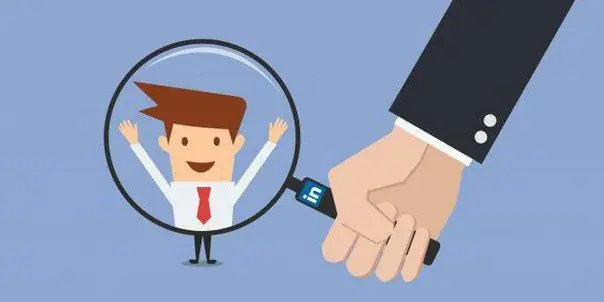
Performance
This indicator reflects the ratio of the volume of manufactured (sold) products to the number of employees. In this case, generalizing, partial and auxiliary coefficients are calculated. The first group includes, in particular, the average annual output. Formula:
B=Volume of production / Number of employees=Volume of production / Amount of time spent.
Change in average annual output may be due to:
- adjusting headcount;
- reducing labor intensity;
- growth of non-production costs;
- organization of labor - an increase in all-day downtime, absenteeism with the permission of the directorate, due to illness, absenteeism;
- changing the structure of products.
Numbers are coststime in physical terms, calculated for one man-day (man-hour).
Labor intensity
Labor intensity is the time spent on manufacturing a unit of output:
Tr=FRVi / FRVo, where:
- FRVi - time to create the final type of product;
- FRVo - the general fund of working hours.
The average annual output is the inverse of labor intensity:
- T=Cost of time / Volume of production.
- T=Headcount / Output.
To calculate the productivity of one worker, the numerator must be one in the above formula. The average annual output per worker is an inverse indicator of labor intensity. It not only displays the performance of a particular employee, but also makes it possible to plan for the next year.
When labor intensity decreases, labor productivity increases. This is achieved through the introduction of scientific and technical progress, mechanization, automation, revision of production standards, etc. Labor intensity should be analyzed not only with planned indicators, but also with other enterprises in the industry.
Production and labor intensity reflect the results of real work, on the basis of which it is possible to identify resources for development, increase productivity, save time, reduce the number.
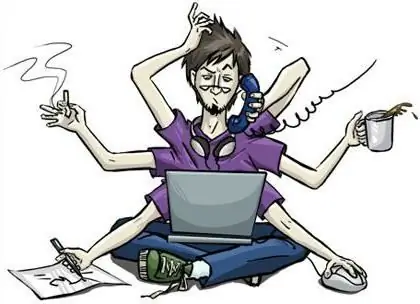
Performance index
This is another indicator of employee performance. It shows the rate of productivity growth.
ΔPT=[(B1 -B0) / B0]100%=[(T1 - T1) / T1]100%, where:
- В1 - average annual output of one employee in the reporting period;
- Т1 - labor intensity of the reporting period;
- B0 - average annual output of a worker in the base period;
- Т0 - labor intensity of the base period;
As you can see from the formulas above, the index can be calculated from output and productivity data.
Changes in the index are determined based on the planned headcount savings:
ΔPT=[E / (H - E)]100%, where E is the planned savings in numbers.
The index shows the change in performance in the base period compared to the previous one. Productivity depends on the competence of employees, the availability of the necessary equipment, financial flows.
Alternative
The following formula allows you to calculate more accurate performance:
P=(Product Volume(1 - Downtime Rate) / (LaborHeadcount).
This approach does not count downtime hours. The volume of production can be expressed in pieces, labor or monetary units.
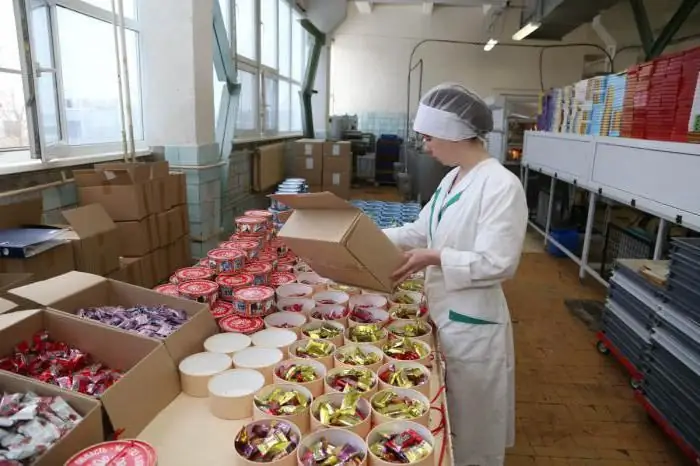
Factor analysis
Since labor productivity is calculated on the basis of the quantity of products manufactured per unit of time, it is these indicators that are subject to detailed analysis. In the course of calculations, the level of task completion, tension, increase in output, reserves for productivity growth and their use are determined.
Factors that affectproductivity can be combined into groups related to:
- raising the technical level;
- improvement of labor organization;
- improving the skills of employees, the level of education of workers, strengthening discipline and improving the system of accrual and payment of wages.
Labor productivity is analyzed in the following areas:
- an assessment is given to the level of generalizing indicators;
- the factors influencing the average hourly output are analyzed;
- reserves for productivity improvement are identified;
- investigating the labor intensity of products.
Example 1
Based on the data presented in the table below, it is necessary to determine the average annual and average hourly output of the enterprise.
Indicator | 2014 | 2015 | Dynamics, % | |||
Plan | Fact | Plan for 2014 | Fact by 2014 | Fact/ Plan | ||
Manufacture of products, thousand rubles | 80100 | 81500 | 81640 | 101, 75 | 101, 92 | 99, 83 |
Worked by workers, thousand man-hours | 2886, 12 | 2996 | 2765, 4 | 103, 81 | 95, 82 | 108,34 |
Labor intensity per thousand rubles. | 36, 03 | 36, 76 | 33, 87 | 102, 02 | 94, 01 | 108, 52 |
Average annual output, rub. | 27, 75 | 27, 20 | 29, 52 | 98, 02 | 106, 37 | 92, 14 |
Increase in productivity by reducing labor intensity:
- according to plan: (4, 7100) / (100-4, 7)=4, 91%;
- in fact: (9.03100) / (100 - 9.03)=9.92%.
The labor intensity plan was overfulfilled by 4.33%. As a result, the average annual output increased by 5.01%.
Features
- The number of employees in optimal conditions should be calculated according to the average. Each worker is counted once a day.
- Performance can be determined from revenue data on the income statement.
- The cost of labor and time is also reflected in the accounting records.
Other indicators
Average productivity is determined if there are a large number of products with different labor intensity, according to the following formula:
Vsr=ΣVolume of production of a type of product Coefficient of labor intensity of a type of product.
Value (Ki) for positions with minimum labor intensity is equal to one. For other types of products, this indicator is calculatedby dividing the labor intensity of a particular product by the minimum.
Productivity per worker:
Pr=(Output(1 - Ki) / T.
The same indicator can be calculated based on the balance sheet data:
Pr=(p. 2130(1 - K)) / (TH).
Productivity must be constantly improved through the use of new equipment, training of workers, organization of production.
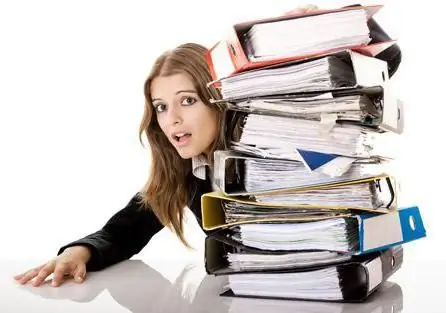
Wage Fund (WFP)
FZP analysis begins with the calculation of deviations of the actual (FZPf) and planned (FZPp) salaries:
FZPa (rub)=FZPf - FZPp.
The relative deviation takes into account the fulfillment of the production plan. To calculate it, the variable part of the salary is multiplied by the plan fulfillment factor, while the constant part remains unchanged. Piecework wages, bonuses for production results, vacation pay and other payments that depend on production volumes are included in the variable part. The salaries calculated according to tariffs refer to the permanent part. Relative deviation of payroll:
FZP=FZP f - (FZPperK + ZP constant).
Following, the factors that cause these deviations are analyzed:
- production volume (O);
- production structure (C);
- specific labor intensity of products (UT);
- salary per man-hour (FROM).
FZP lane=OSUTFROM.
Before analyzing each of the factors, it is necessary to carry out intermediate calculations. Namely: to determine the payrollvariable:
- according to the plan: FZP pl=OSOT;
- according to the plan, taking into account the given volume of production: wage bill cond. 1=FZP plK;
- according to the plan, calculated with the actual volume of production and structure: wage bill cond. 2=OUTFROM;
- actual with specific labor intensity and a given level of remuneration: wage bill cond. 3 \u003d OfUtfOtf.
Then you need to multiply each of the obtained values by the absolute and relative deviation. This way you can determine the influence of each of the factors on the variable part of the salary.
The permanent part of the wage bill is affected by:
- headcount (N);
- number of days worked per year (K);
- average shift duration (t);
- Average hourly wage (HWR).
FZP f=HKtFZP.
The influence of each of the factors on the final result can be determined in exactly the same way. First, changes in each of the four indicators are calculated, and then the obtained values are multiplied with absolute and relative deviations.
The next stage of the analysis is the calculation of the effectiveness of the use of payroll. For expanded reproduction, profit, profitability, it is necessary that the growth of productivity outpaces the growth of the wage bill. If this condition is not met, then there is an increase in cost and a decrease in profit:
- earnings (J RFP)=Average salary for the reporting period / Average salary for the planning period;
- average annual output (J Fri)=Output for the reporting period / Output for the planning period;
- labor productivity: (Kop) / Kop=J fri / J sn;
- farm savings: E \u003d FZPf((J zp - J fri) / J zp).
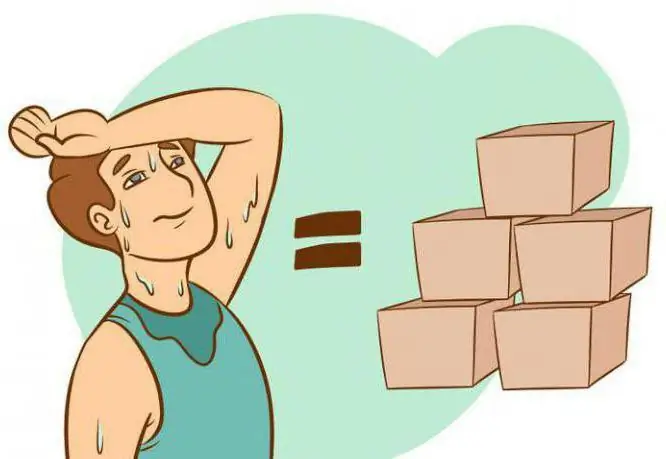
Example 2
Based on the given data, you need to calculate the output:
- production volume - 20 million rubles;
- average annual headcount of 1,200 people;
- for the year, the employees of the organization worked 1.72 million people/hour and 0.34 million people/day.
Solution:
- Hourly output of one worker=Volume of production / Man-hours worked=20 / 1, 72=11, 63 rubles
- Daily output=20 / 0, 34=58.82 rubles
- Annual output=20/1, 2=16.66 rubles
Recommended:
Design. Credit card without annual service
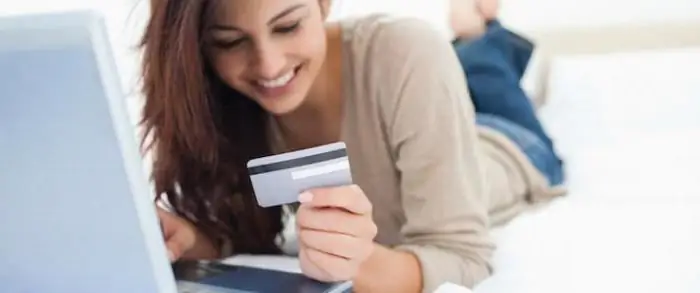
Credit cards have become quite a convenient tool for managing money. They are rightfully considered the type of loan that is easy to get and convenient to repay. Despite the wide choice, the credit card without annual maintenance is the most popular, which will be discussed in the article
Methods for calculating the cost of production. Fixed costs per unit of output
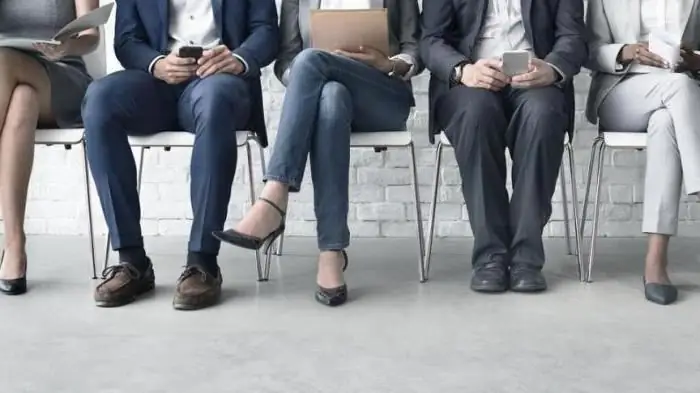
The cost of production is an important economic indicator that reflects the efficiency of production activities. Therefore, it is so important to be able to correctly carry out calculations and draw reasonable conclusions. Let us consider in more detail the main types, methods of calculation
Annual reporting: forms and deadlines
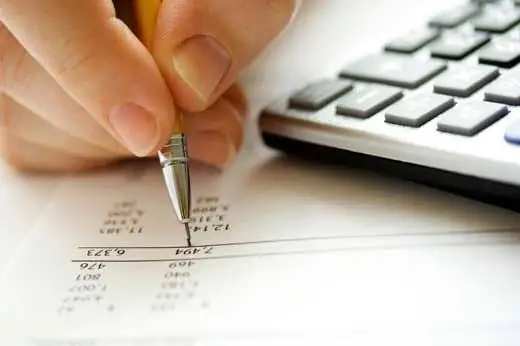
Each organization, regardless of whether it works under the general taxation system or under the simplified one, is required to submit annual accounting and tax reporting. Reporting has many purposes. The company's financial statements are of interest not only to the authorities, but also to the enterprise itself
Average annual cost of OPF: balance sheet formula
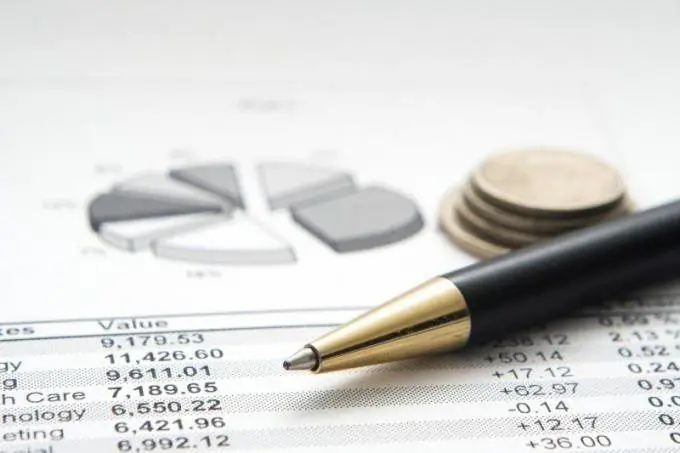
The cost of OPF tends to be passed on to finished products over a fairly long period. In some cases, it may cover several cycles. In this regard, the organization of accounting is carried out in such a way that at the same time it would be possible to reflect both the preservation of the original form and the loss of price over time
Formula for calculating vacation days. Duration of annual basic paid leave
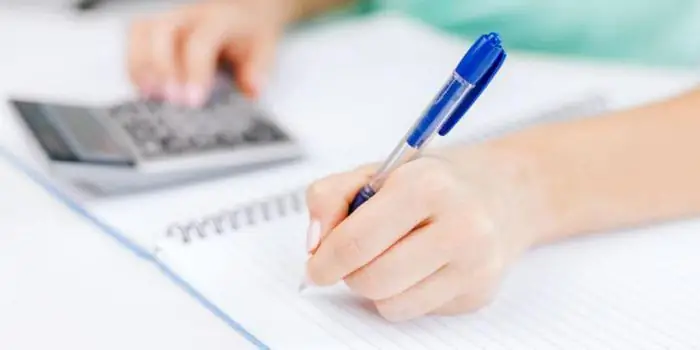
Vacation is a long-awaited period. However, despite the fact that the number of days is established by law, there are always some nuances