2025 Author: Howard Calhoun | [email protected]. Last modified: 2025-01-24 13:10
Difficulties often arise in the processing of non-ferrous metals, as their physical properties change at high temperatures. Brass welding deserves special attention, during which zinc is actively evaporated. Despite the existing difficulties, it is quite possible to work with this alloy in domestic conditions.
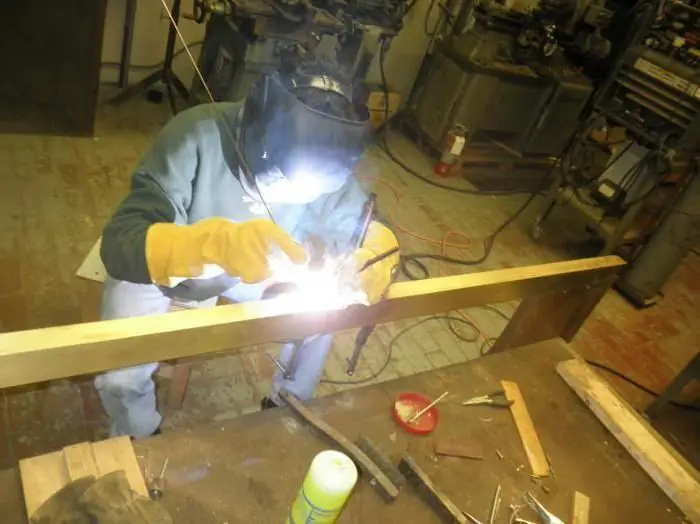
Basic material properties and obtaining
Before brass welding is considered in detail, it is necessary to familiarize yourself with the characteristics of the material itself. The composition of the alloy includes two base metals - copper and zinc. The content of the last of them can vary within 5-45 percent. It is introduced not only to improve the physical properties, but also to reduce the cost of the final product.
A large number of products are made from brass. These include all kinds of bushings, adapters, pipes and various decorative elements. During their production, alloying elements can be added that affect the quality characteristics:
- tin improves corrosion resistance:
- aluminum reduces the volatility of zinc to some extent;
- silicon improves weldability atslight loss of strength;
- lead makes it possible to obtain less hard products for easy processing by cutting.
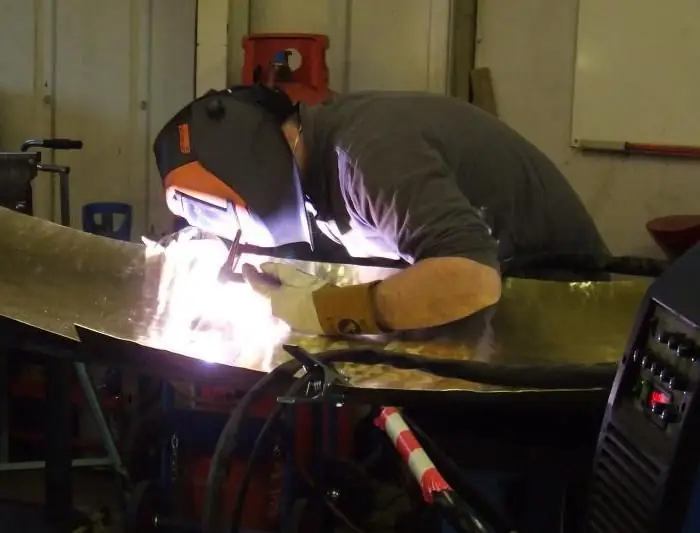
Zinc and copper blanks, as well as some types of other metals, act as the raw materials for the manufacture of the alloy. In some cases, waste from own production may be used. Melting is carried out in rooms with exhaust ventilation using induction furnaces.
Difficulties when creating one-piece connections
In order for brass welding at home to be done efficiently and safely, you need to be aware of the problematic issues. Permanent joints obtained by local heating will only be reliable if special requirements are met. In the course of work, one should not forget about safety measures, since dangerous fumes are released during thermal exposure.
The main problem lies in the active burnout of zinc, which is associated with its low melting point (only 419 degrees). Most of the substance evaporates during the work. Some of this reacts with oxygen, forming a white powder, which subsequently covers the areas near the seam.
Work Precautions
Self-welding brass should not lead to the formation of dangerous conditions for the human body. Due to the increased activity of the release of volatile compounds, respirators should be used during work. Even when using special technological methods, burnoutzinc ranges from 25 to 30 percent.
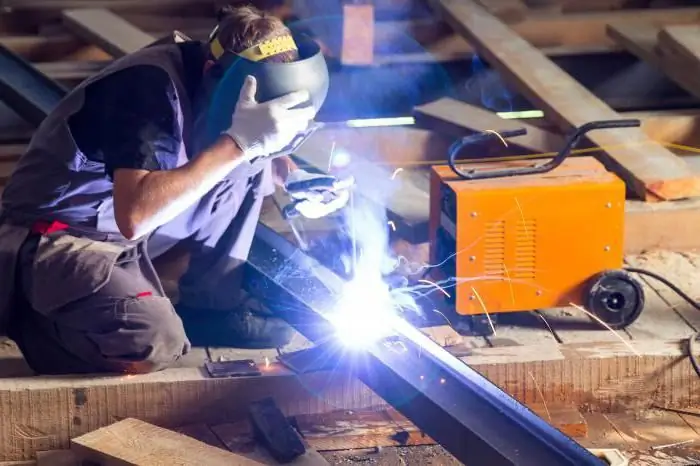
It is not allowed to carry out welding activities near materials and substances that ignite very quickly. There should be no gasoline, wood shavings, tow or gas cylinders in the immediate vicinity of the workplace. A prerequisite is the presence of ventilation in the room.
Measures to prepare the elements
When welding thin brass, there is no need to preheat. When connecting massive elements, it is recommended to perform local heat treatment. Edge preparation may not be performed for products with a thickness of 1.5-6 mm.
If the elements have a larger section, then in any case, a V-shaped cutting of the seams will be required. It is simple, but not optimal. It is best to carry out an X-shaped cut, in which the opening angle will be 30-45 degrees on each side.
Types and comparison of applied technologies
In many cases brass is welded with argon. The technology of connecting parts in an inert environment is considered the most promising, as it allows you to achieve a high speed of work. Other advantages of this option include:
- possibility of obtaining seams with clear geometry and cleanliness;
- uniformity of the structure in places of permanent connections;
- reliability of joints;
- economical due to the use of inexpensive tungsten electrodes.
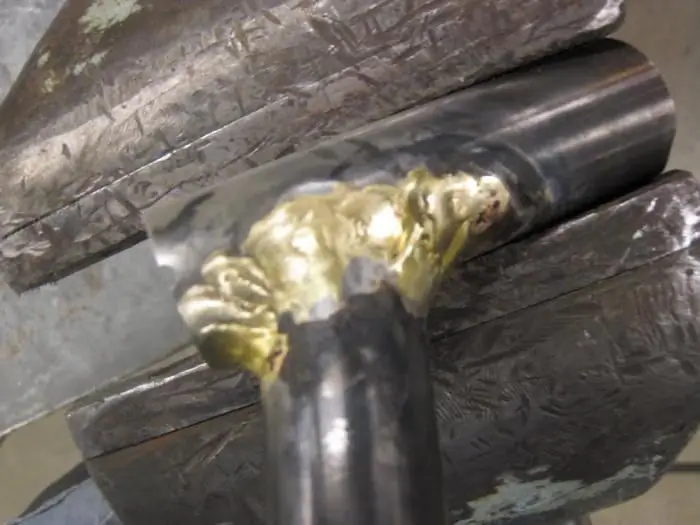
Another technology is gas welding. It does not involve the use of a source of electrical energy, which in some cases is very justified. With its use, it is possible to regulate the power of the outgoing flame within a fairly wide range. With the right selection of filler materials, high-quality welds are formed.
Argon welding of brass: process description
The shielding gas environment provides an opportunity to somewhat mitigate the negative effects. Welding of bronze and brass with this option takes place using direct current with direct polarity. Due to the high probability of burn-through, it is recommended to process the docking site with a long arc.
The electrode is inserted into the burner, which is a conductive mechanism. After that, the unit is turned on. The operation itself is accompanied by increased crackling, which appears due to the release of zinc fumes. The filler wire is inserted into the seam manually.
Parts are combined by separate rollers, and not by continuous cooking technology. When filling a crater, it is desirable to slightly reduce the arc voltage. At the final stage, it must be removed to the side. The operating voltage should not decrease immediately, but gradually.
Using gas appliances
In areas where there is no electrical source, arc technology cannot be applied. However, in this case, gas welding of brass is quite acceptable. When using it, strong connections are obtained, however, the work requires quitehazardous substances that, together with oxygen, form explosive mixtures.
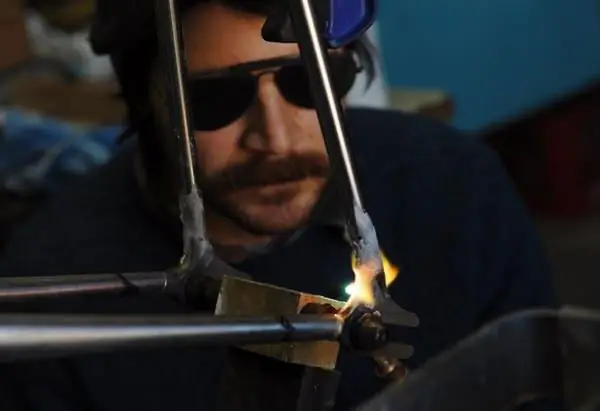
Excessive evaporation of zinc can be avoided during work by using an oxidizing flame in the working burner. There should be much more oxygen than hydrogen. When processing the joint, an oxide film appears on the surface, which allows to some extent protect the surrounding space from zinc emissions.
When welding, filler wire is recommended to be placed at an angle of 15 to 30 degrees to the side edges. Transverse oscillations should be avoided during the operation. The torch should be at an angle of 70 to 80 degrees to the workpiece.
The filler material is placed over the molten bath directly into the burner flame. Do not immerse the used bar into the inside of the seam. When driving, it is desirable to adhere to a certain speed. Usually it is 15-25 cm per minute.
If workpieces of great thickness are connected, they should be placed at an angle of 10 to 15 degrees to the horizon. Welding is carried out on the rise. As a rule, ceiling joints are not performed in this case, since the material is fluid.
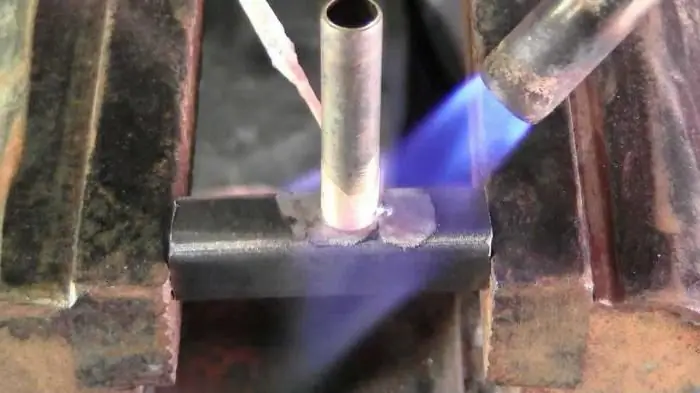
Welding with other metals and alloys
Sometimes you need to combine brass with other dissimilar materials. In this case, you need to know about the features of such work. When combined with steel, some difficulties may arise, which is associated with various physico-chemicalcharacteristics of the two alloys.
A common defect in welding is the appearance of cracks on the steel surface directly under the brass layer. To reduce the risk of such defects, it is recommended to use a nickel alloy. The best suited is argon-arc technology, performed with tungsten electrodes.
Combining titanium with copper alloys can lead to the formation of brittle chemical bonds. The best effect is achieved when using intermediate inserts. They are made of titanium alloy alloyed with niobium or molybdenum. In some cases, the use of combined alloys is allowed.
In terms of physical properties, niobium is in many ways similar to titanium, so it welds satisfactorily with brass. However, the operation must be carried out in an inert environment. Often special chambers are used in which the atmosphere is completely controlled.
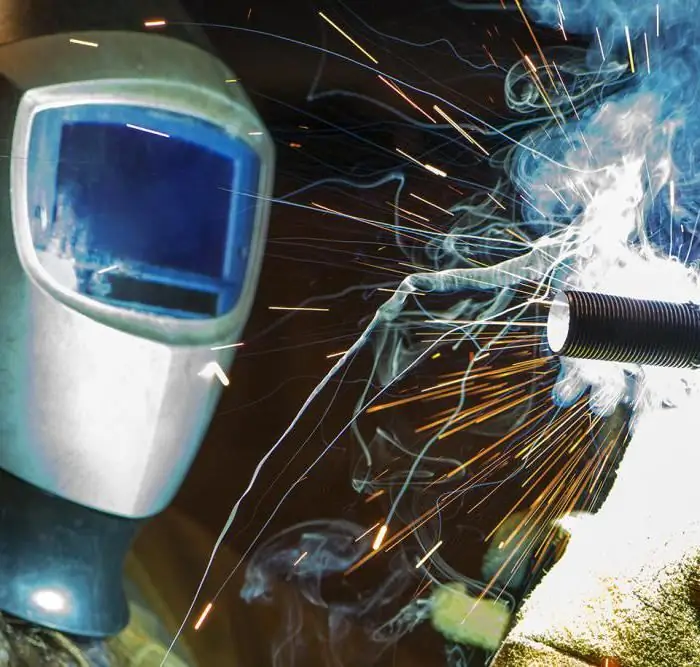
Final part
It should be noted that the technology of brass welding has its own characteristics, which should be taken into account when creating permanent joints at home without the involvement of specialists. When studying all the intricacies of the process, it is quite realistic to achieve a high-quality connection of workpieces. As for the choice of methodology, it largely depends on the availability of specific equipment and the conditions of work.
Recommended:
The main consumable for welding - welding wire
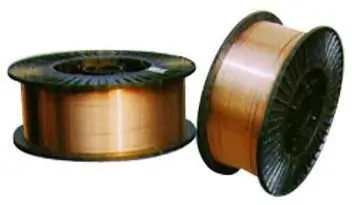
Welding wire is used in various welding operations, it is the main consumable material that acts as an electrode. Welding operations require extensive professional knowledge, a responsible approach to the choice of raw materials. For welding structures, it is unacceptable to use random wire of incomprehensible marking and unknown composition
Welding of ultrasonic plastics, plastics, metals, polymeric materials, aluminum profiles. Ultrasonic welding: technology, harmful factors
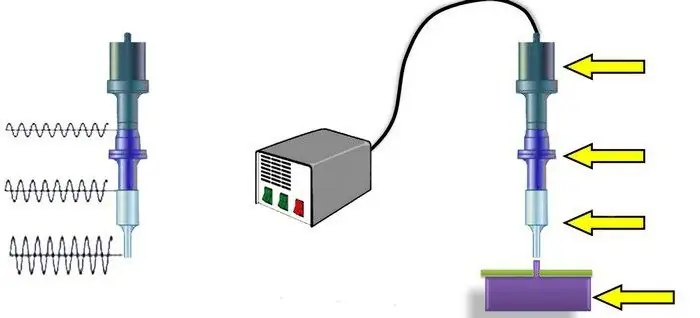
Ultrasonic welding of metals is a process during which a permanent joint is obtained in the solid phase. The formation of juvenile areas (in which bonds are formed) and the contact between them occur under the influence of a special tool
Welding consumables: definition, characteristics, manufacture, storage. Main welding material
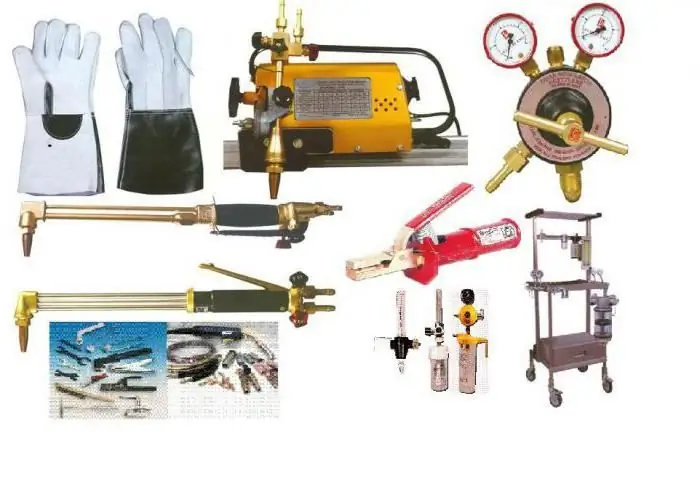
Main types of welding consumables, features of storage of explosive gases, characteristics of electrodes depending on the material and other parameters
Thermite welding: technology. The practice of thermite welding in everyday life and in the electrical industry
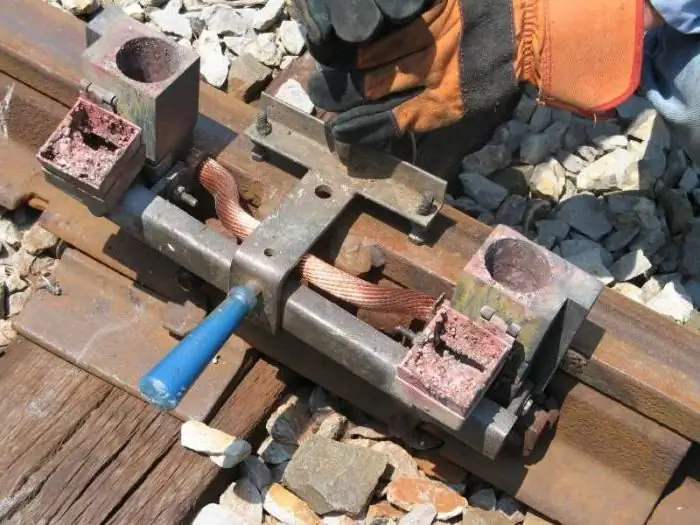
The article is devoted to thermite welding technology. The features of this method, the equipment used, the nuances of use, etc. are considered
Flux for welding: purpose, types of welding, flux composition, rules of use, GOST requirements, pros and cons of application
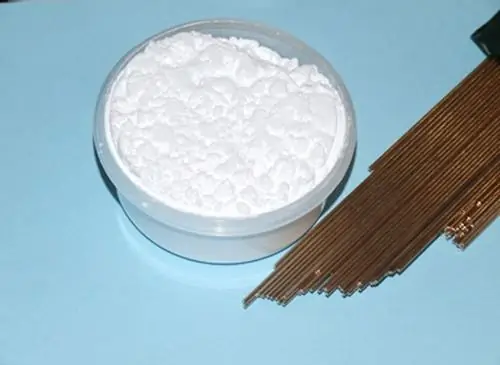
The quality of the weld is determined not only by the ability of the master to organize the arc correctly, but also by the special protection of the working area from external influences. The main enemy on the way to creating a strong and durable metal connection is the natural air environment. The weld is isolated from oxygen by a flux for welding, but this is not only its task