2025 Author: Howard Calhoun | [email protected]. Last modified: 2025-01-24 13:10
Over the past few decades, the most common type of joining parts of many metal structures has been manual arc welding. Of course, designers are constantly developing other types of welding that are more efficient, but their availability and the nature of the work can not compete with the arc method.
For home use, manual arc welding technology is the most popular, as it is the easiest to learn method of joining metals. All tools and materials of this type of welding are affordable and cost-effective. On sale there is a huge variety of models of welding transformers, inverters, as well as a wide selection of electrodes for welding any metal.
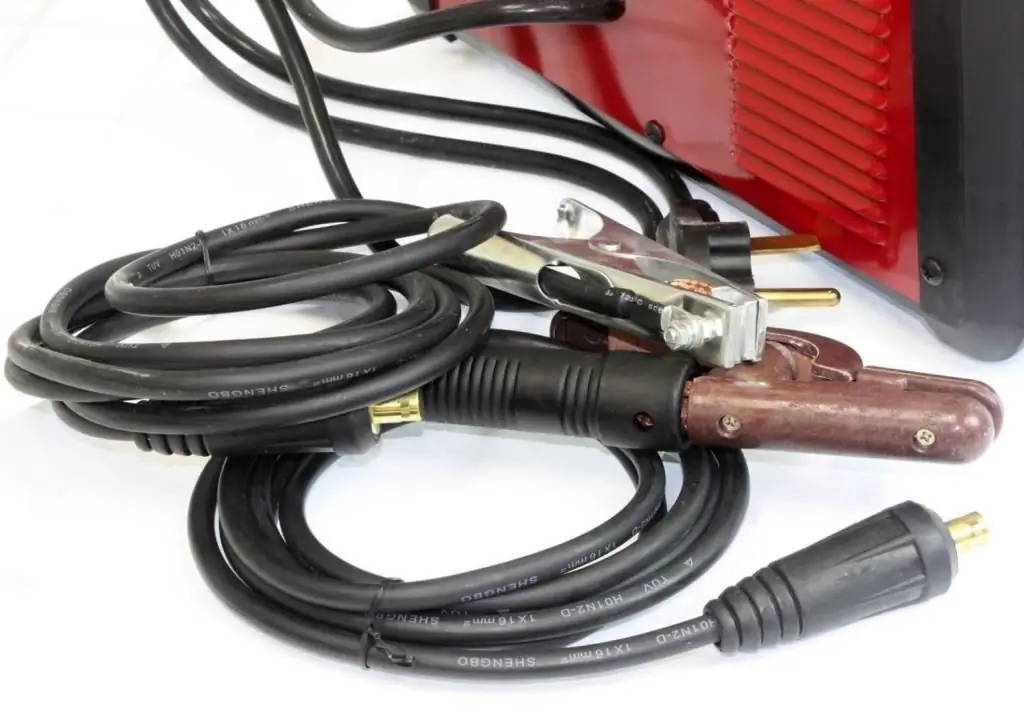
Features of using welding
Practically in any area of the national economy, welded joints by manual arc welding are used. Power sources for this type of work are widelyuse in domestic conditions, as many of them work from a standard electrical network. The quality and reliability of the resulting weld are quite acceptable both for the installation and repair of many metal structures in a home workshop, and for the creation of new products at industrial enterprises in various fields of activity.
According to GOST 5264-80, manual arc welding allows you to connect carbon steel metals in any spatial position, and the use of special electrodes makes it possible to weld parts made of cast iron and various non-ferrous metals, including alloyed steels. In this case, the connecting seams are obtained with a high degree of resistance to fracture and tear resistance.
The ability to overlay the surfaces of worn parts for their subsequent machining is another functional feature of this method of welding process.
Principle of welding process
Technology of manual arc welding is based on the melting of the base metal and the electrode rod under the influence of an electric arc. When melted, the materials to be joined and the consumable electrodes mix to form a weld pool. After solidification of this mixture, a solid metal structure is formed - a weld.
To protect the weld pool from the harmful effects of nitrogen, oxygen and other gases contained in the air, a special coating is applied to the welding electrodes. During the welding process, these components, melting together with the base metal, create on the surface of the weld poolprotective film in the form of a gas cloud and slag.
For high-quality melting of metals, it is necessary to constantly maintain an electric arc between the connected elements, which arises from a special welding machine (inverter). The temperature inside the weld pool reaches 4000℃. The slag floats to the surface of the joint, protecting the work area from oxygen exposure. Later, after the seam has cooled down, the slag film is removed mechanically.
Advantages of arc welding
The cost of manual arc welding with coated electrodes directly depends on the functionality of welding machines. The more options that the used unit is capable of issuing, the higher its price. But not only the low cost of the unit determines all the advantages of manual arc welding, there are also a number of advantages of this method of joining metals:
- possibility of welding parts in hard-to-reach places;
- welding in all spatial directions;
- quick change of bonded material;
- diverse range of manufactured electrodes allows you to join products from different types of metal;
- manual arc welder does not have to have technical knowledge, because such simple equipment can be mastered by anyone;
- small overall dimensions of the welding machine make it easy to transport it to the required place of work;
- ability to work throughout the working day;
- obtaining a high strength weld.
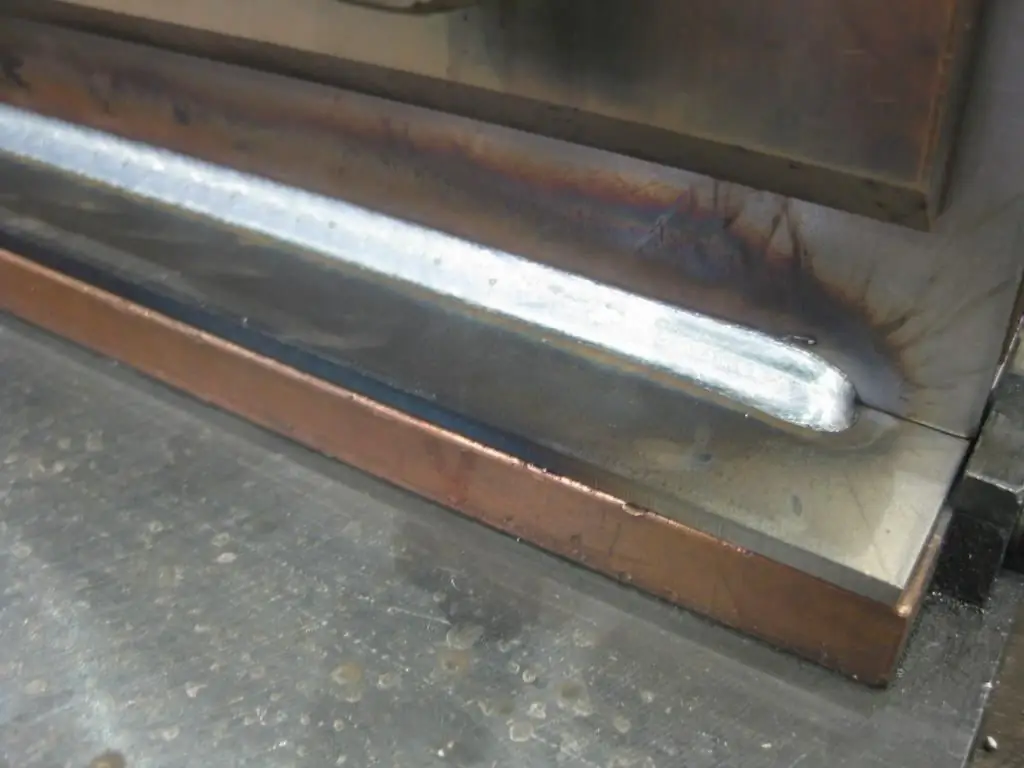
Some disadvantages of the arc connection
Among the disadvantages of arc welding are:
- harmful working conditions due to fumes and exposure to electromagnetic fields;
- relatively low efficiency compared to other types of welding;
- Insufficient experience of the welder, which can lead to poor quality of the welded joint.
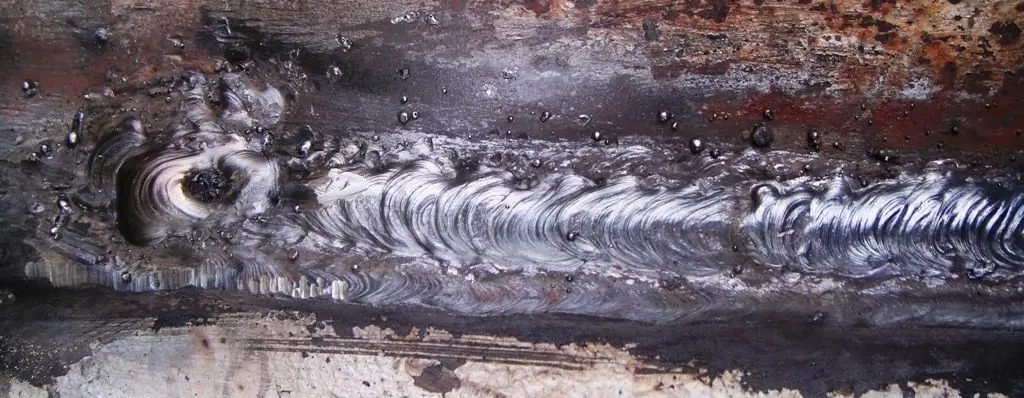
However, if you carefully follow the parameters of the correct connection and allowable weld sizes, according to GOST 5264 for manual arc welding, you can qualitatively and reliably connect metal structures in a garage, summer house or country house.
Varieties of arc welding
From the very beginning of the development of manual arc welding to the present, the joining process is carried out on two types of electric current:
- variable;
- permanent.
Special transformers are used for AC welding. The welding process is performed using consumable electrodes. This type of welding is most popular when working at home, as the equipment is not very difficult to make yourself.
To make a direct current connection, special rectifier devices are used. This type of welding greatly reduces the amount of molten metal spatter, which improves the quality of the weld.

Any of these types is used not only for joining products, but also for fusing a certain layer of metal on the surface of a worn part, which is of particular use in many repairs.
Down Welding Technology
First of all, it is necessary to carry out the correct preparation of the surfaces to be welded, for which it is necessary to cut the edges at an angle of 45 °. In the case of welding parts thicker than 6 mm, it will be necessary to set a gap of 2-3 mm in order to produce a good penetration of the joint.
The ignition of the arc is carried out by gently tapping the electrode on the mass. It is advisable to perform this operation on a separate metal plate, and then bring the already heated electrode to the welding site. After completing the preparatory operations, we grab the surfaces to be welded in several places.
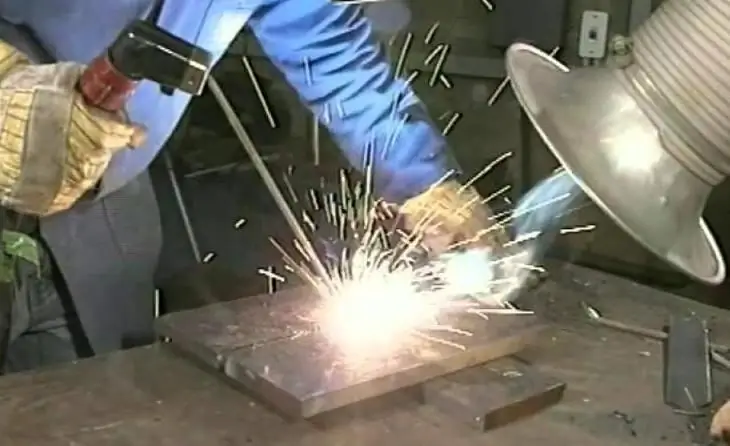
The electrode during manual arc welding is held at an angle of 45 ° in relation to the plane of the surface to be welded. In this case, the root seam is applied first. It is done by moving the electrode from one side to the other with smooth and even movements.
Further, according to GOST, welded joints by manual arc welding are performed with transverse oscillatory movements in order to fill the entire weld zone and expand it. When conducting a spiral translational movement, it is necessary to control the distance between the electrode and the metal plane (5 mm). It is better to ensure a slight inclination of the parts to be welded so that the hotslag flowed to the side. If this is not possible, this operation is performed by the welder himself with the tip of the electrode.
The end of the weld must be overlapped to avoid a crater.
Vertical seam technology
Manual arc welding can also connect products in a vertical position. To do this, it is necessary to perform work with intermittent arc technology. Liquid metal has a relatively large weight, so continuous heating of the joint will cause the molten metal to flow down. In this case, the seam is made in the form of shelves, that is, it is superimposed on each other in layers. Of course, with such a connection, the time to complete the work increases, but the quality of welding does not suffer.
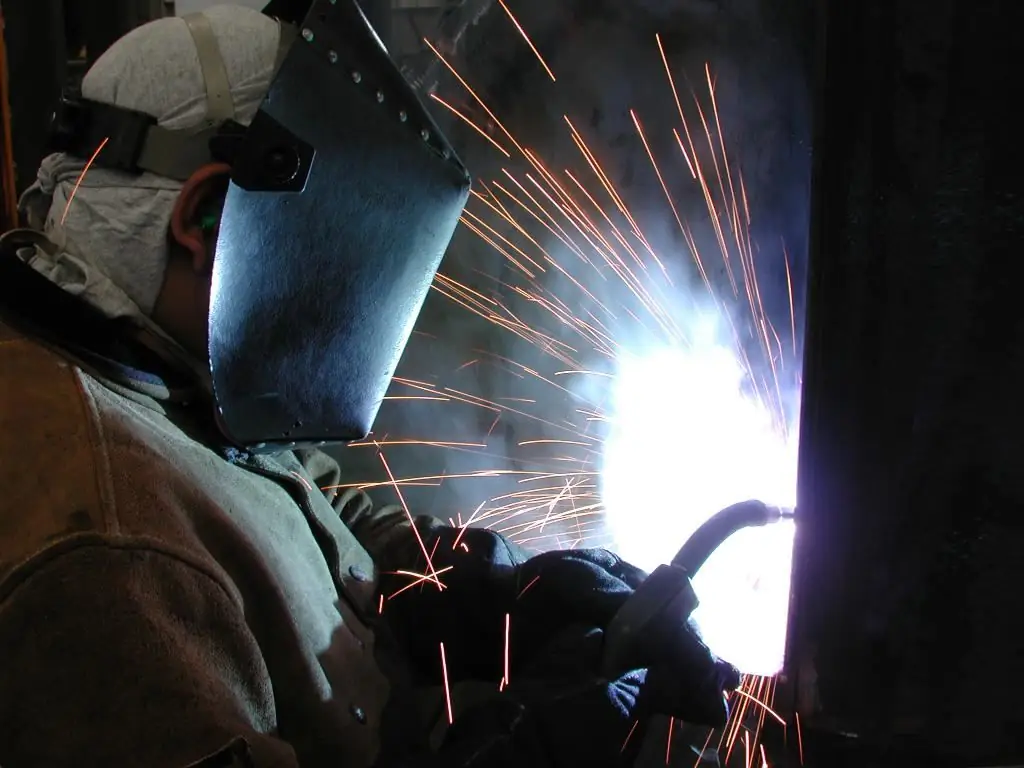
The same technology is used to weld ceiling joints. The main thing in such conditions is to choose the right welding mode.
Welding speed
The speed of the electrode in arc welding is selected in accordance with the thickness of the parts to be welded, as well as depending on the dimensions of the seam. The basic principle of weld quality is the complete filling of the weld pool with molten metal. If there are sagging or undercuts, then the welding speed was selected incorrectly.
Rapid movement of the rod leads to lack of penetration, as the temperature does not have time to reach the melting value of the base metal and the seam is thin. After it cools, cracks and deformation of the seam may occur.
When the electrode moves slowly, it forms in front of the arca mass of molten metal that also prevents optimum weld penetration.
Selection of current parameters
Increasing the welding current has almost no effect on the width of the seam. The main influence is on the penetration depth - the greater the current, the deeper the value of the temperature effect and, conversely, with a decrease in the current strength, the penetration depth is reduced.
Special importance should be given to the type of current. DC operation produces a narrow weld.
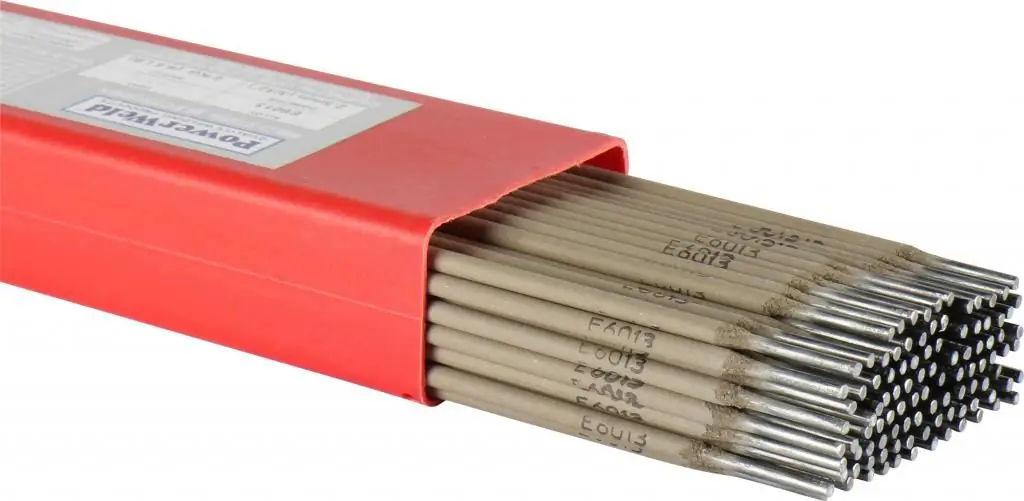
Also, the depth of the temperature depends on the diameter of the electrode. At the same current, a smaller section of the rod reduces the width of the seam and increases the penetration of the metal. But a change in the arc voltage affects only the width of the seam, while almost without changing the value of the penetration of the metal. It is by changing the voltage that the width of the metal deposition in automatic welding devices is regulated.
Welding Safety
Despite the fact that welding, at first glance, is a simple task, however, operations with high temperature and electric current require concentration and attention from a manual arc welder.
To protect human he alth, the following safety requirements must be strictly observed when carrying out welding work.
- The main requirement for safe work is the presence of a protective welding helmet with tinted glass. The use of these products will save the welder from damage by metal scale and effectively protect the eyes from the harmful effects of sparks.electrode.
- In order not to get under the influence of electric current, you need to carry out all work in rubber gloves. At the same time, it is necessary to ensure that they are without holes and are not damp.
- The welding cable must not have cracks in the insulation. Running the cable through melted snow or puddles can cause electric shock.
- Because the weld pool contains molten metal, care must be taken to avoid contact with liquid material.
Welding technology is constantly being improved, however, despite this, manual arc welding has been and remains the most popular type of metal joining - not only in industrial enterprises, but also in everyday life. If you master this type of welding correctly, you can quickly and efficiently perform almost all work with metal products.
Recommended:
Technology of electric arc welding of metals
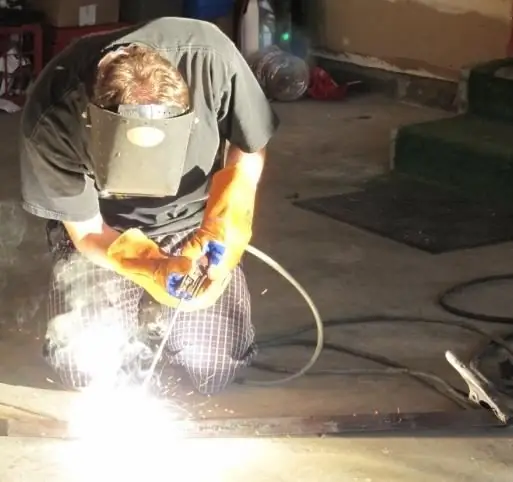
The impact of an electric arc on the structure of a material is one of the oldest ways to obtain a strong connection between metal workpieces. The first technological approaches to this welding method had a lot of disadvantages associated with the porosity of the weld and the formation of cracks in the working area. To date, manufacturers of equipment and auxiliary devices have significantly optimized the method of electric arc welding, expanding the scope of its use
Welding arc temperature: description, arc length and conditions for its appearance

Today, welding is a process that is used quite often when it is necessary to connect two metal parts together. However, few people understand exactly how welding works, as well as what is the temperature of the welding arc and what causes it
Welding of ultrasonic plastics, plastics, metals, polymeric materials, aluminum profiles. Ultrasonic welding: technology, harmful factors
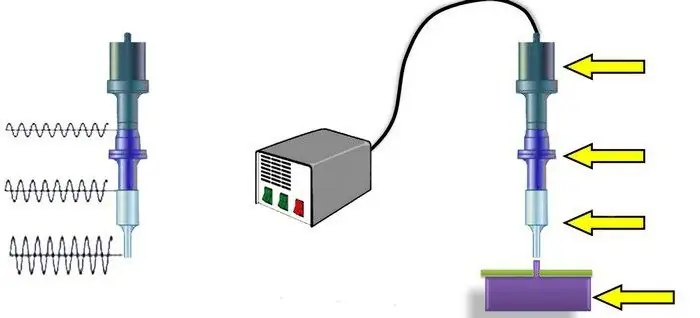
Ultrasonic welding of metals is a process during which a permanent joint is obtained in the solid phase. The formation of juvenile areas (in which bonds are formed) and the contact between them occur under the influence of a special tool
Thermite welding: technology. The practice of thermite welding in everyday life and in the electrical industry
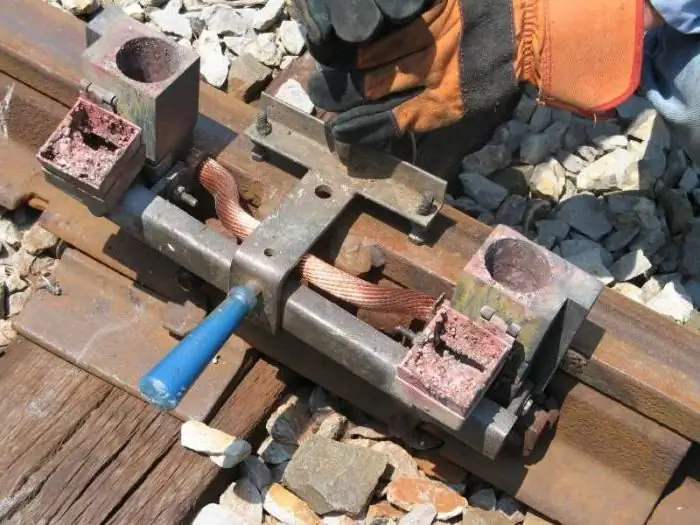
The article is devoted to thermite welding technology. The features of this method, the equipment used, the nuances of use, etc. are considered
Arc welding in shielding gas: description of technology, modes, methods
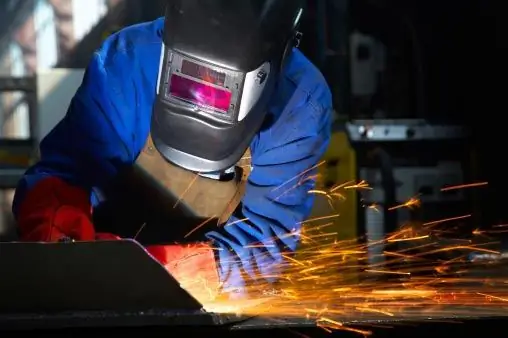
Gas shielded arc welding is a method that significantly improves the quality of the work result. This technology has a number of features. Before applying it, the master must familiarize himself with the basics of arc welding, which is carried out in a shielding gas environment. The features of this technology will be discussed in the article