2025 Author: Howard Calhoun | [email protected]. Last modified: 2025-01-24 13:10
Automation and dispatching systems for boiler houses ensure the efficient and safe operation of these facilities. They allow real-time assessment of the serviceability and efficiency of equipment, timely shutdown in emergency and pre-emergency situations. When servicing a number of boiler houses located at a considerable distance from each other, all the necessary information can be sent to a single control room, which significantly reduces maintenance costs.
Tasks
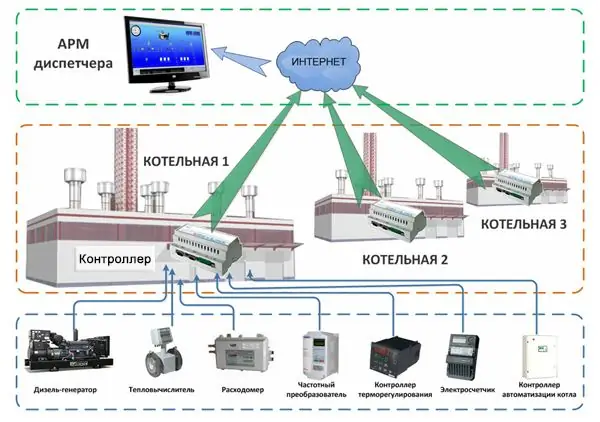
The main purpose of the boiler room automation and dispatching system is:
- management of starting and stopping boilers (including emergency situations);
- automatic and manual adjustment of boiler power;
- cascade control of the total heat output (starting the second boiler from the reserve, if the first one is not enough to maintain the required temperature at the consumer, then turning on the third one, transferring the spent boiler to the reserve);
- characteristic adjustmentcoolant at the outlet of the unit;
- starting backup equipment in case of failure of the main one;
- activation of alarms and transmission of messages;
- transition to energy-saving mode and implementation of other program settings (maintaining the coolant temperature depending on the street temperature, according to a given schedule, taking into account day and night mode).
General Description
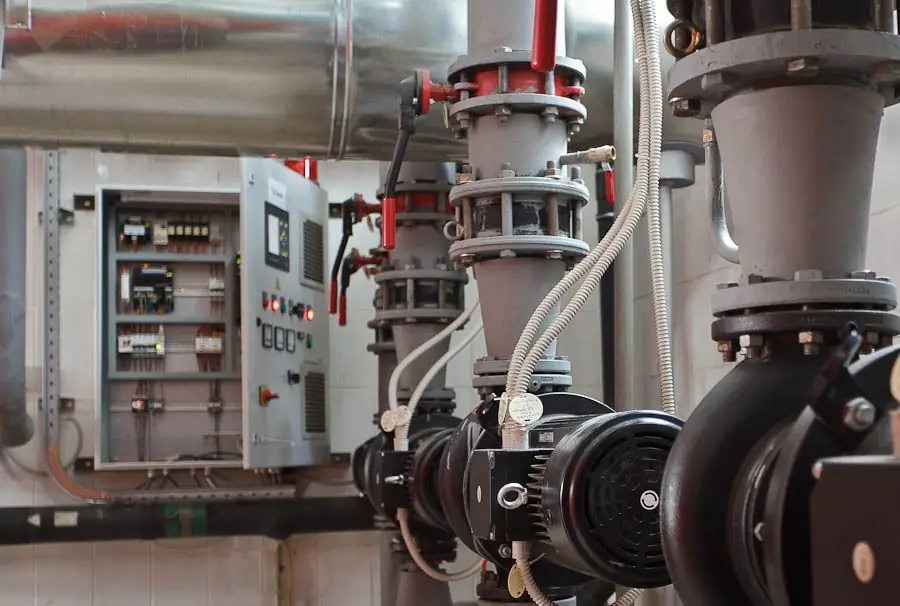
Modern boiler room dispatching systems are built as a complex of unified modules, the main elements of which are:
- power cabinet;
- automation cabinet;
- control and management console (dispatcher console);
- electric actuators;
- sensors.
The equipment and technical characteristics of this equipment depend on the technological solution of the heating system, manufacturers' recommendations, and automation features. Collection, processing of data, formation of working algorithms and control commands are combined into functional groups and distributed among controllers and modules.
Information from all devices is sent to the control panel and can be displayed on the dispatcher's computer. To visualize and set parameters, special software is used (SCADA package, APROL and others).
Controllers
Controllers for automation and dispatching of boiler rooms are used with programmable logic. Their peculiarity is that they serve as independentdevices have universal inputs and outputs (which ensures their high interchangeability).
The line of programmable logic controllers is very diverse in terms of functional, technical and design characteristics. Thanks to their use, checking and adjustment of cabinets is facilitated, high reliability of all equipment is ensured.
Functions
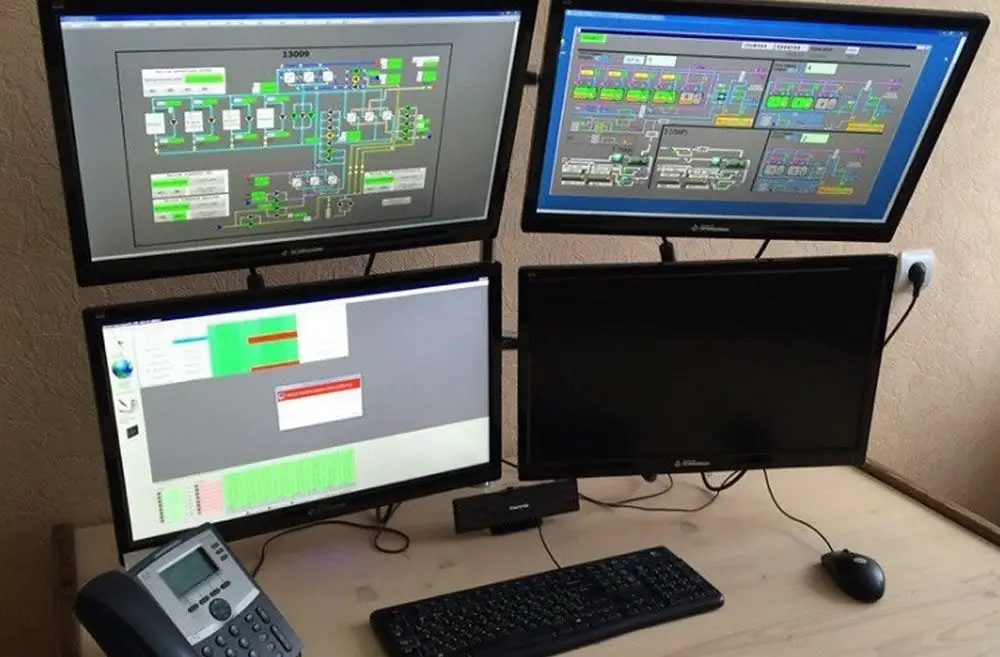
The boiler house dispatcher performs the following functions:
- Control of sensor readings: temperature (T) and water pressure (p) in the forward and reverse lines; T and p at the inlet / outlet of the boiler; p fuel in gaseous or liquid state; T and p of the supply and return water of the heating circuit; T and change in the composition of the ambient air in the boiler room and on the street; liquid level in the make-up tank.
- Control of devices and equipment: status of differential pressure sensors on circulation pumps; automatic or manual operation of boilers and pumps; the transition of mechanisms designed to move the regulatory body to various states (“open”, “closed”); transfer of the boiler to the “on”, “off” or “emergency” state.
- Control: emergency shutdown of boilers, power off automation; closing the solenoid shut-off valve to stop the supply of liquid or gaseous fuel; starting in the summer once a day the network pumps and the heating control valve; turning on the second (third) boiler in case of insufficient thermal power, turning off the exhausted one - rotation according tooperating time; control of make-up and circulation pumps, as well as valves.
- Protection of elements of the technological scheme of the installation in the following situations: drop of p in the boiler circuit as a result of coolant leaks; increase in p and T of water at the outlet of the boiler in excess of the allowable; burner inoperability; fire or increased gas contamination (exceeding the MPC for carbon monoxide or methane).
- Alarm: emergency; pre-emergency; sending SMS-messages via GSM channel; remembering the cause and exact time of the accident.
Power control cabinet
The control cabinet is used for switching power circuits of pumps, boilers, electric motors, valves and other equipment. It is equipped with the following devices:
- control mode selectors to select command source;
- signal lamps (light indication of equipment operation);
- switching elements for manual and automatic control (switches, contactors, thermal relays, etc.).
Structurally, it is made in the form of a metal cabinet in a wall or floor version, on the back wall of which mounting panels with the above devices are mounted.
Automation cabinet
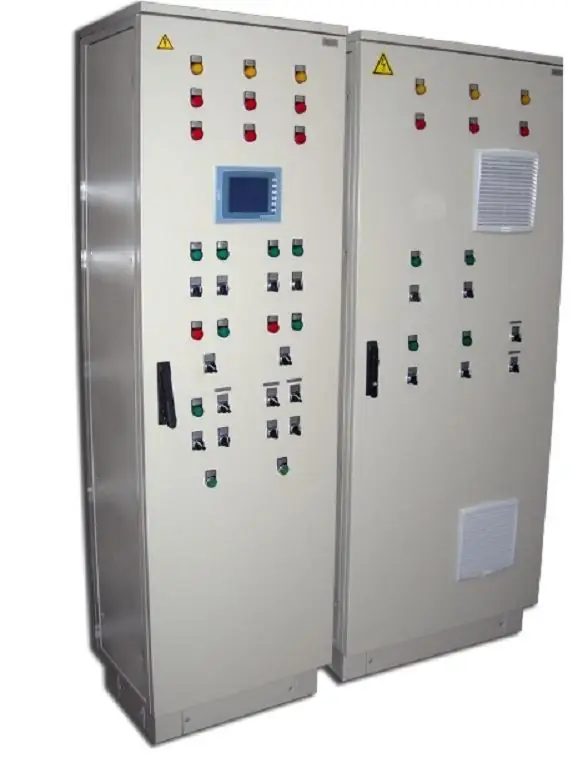
The complete set of the control cabinet depends on the selected technological solution. It may include the following elements:
- controllers and software and hardware systems;
- touch screen remote control on the front door of the boiler cabinet;
- push-button control post;
- uninterruptible power supply unit;
- devices for controlling the modes of drives of regulating mechanisms;
- GSM modem;
- signal working and emergency lamps;
- devices for checking and disabling alarms.
Dispatcher item
Organization of dispatching of gas boiler houses is as follows: a mnemonic diagram is displayed on the dispatcher's screen, which graphically shows the structure of process equipment, pipelines and fittings. The display also shows the main parameters of the coolant.
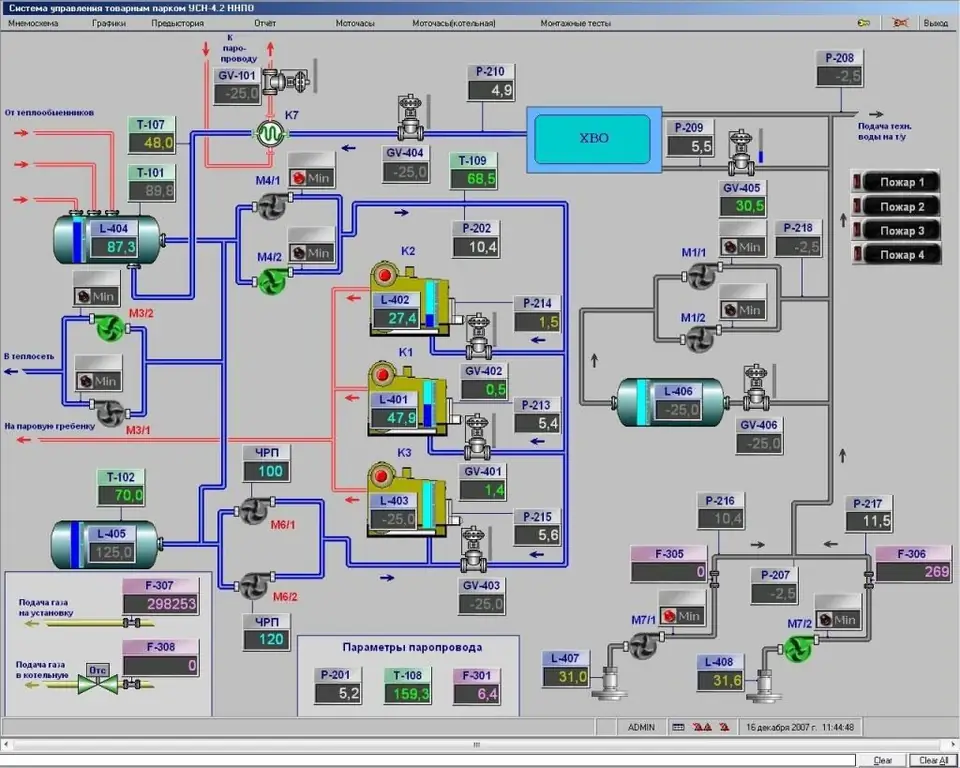
There are virtual buttons that can change color when creating an emergency. The diagram shows the location of the accident and its cause. Additionally, SMS messages are sent to persons responsible for the safe operation of the boiler room (dispatcher on duty, engineer). If necessary, these workers can remotely intervene in the management process and change certain parameters. For various users, a ban on access to some of the information (projects, schemes and their elements) may be imposed.
For the purpose of convenient analysis, technical data can be formed in the form of tables, graphs, daily archives. For the boiler house dispatching system, there are practically no restrictions on the nature and number of operating mode parameters, the number of control points and the distance between objects. Its organization can be carried out using a local, remote, global (Internet) network or a combinedscheme.
The industrial software package SCADA and its domestic counterparts are used as dispatching tools. The main functions of the control room are:
- data collection and performance evaluation;
- visualization of the received information;
- formation and storage of an archive about the technological process and operator's actions;
- limitation of access rights;
- print tables, graphs and other information, export it to other systems.
Benefits
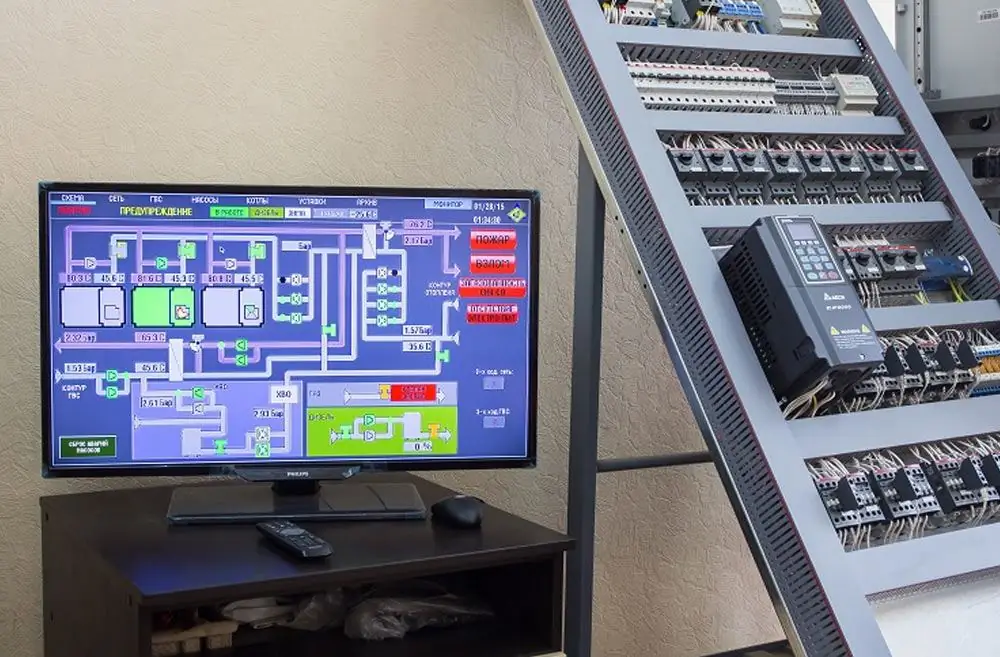
Automation and dispatching of boiler rooms has the following advantages:
- the ability to control processes without the direct participation of a person;
- cost savings associated with service personnel;
- ensuring the reliability of process equipment, increasing its service life and reducing repair costs;
- timely, automatic liquidation of accidents;
- reducing energy costs, the possibility of implementing resource-saving programs;
- reducing downtime;
- opportunity to expand coverage of objects;
- quick receipt of a complete report on the current state of the boiler room.
Scheduling
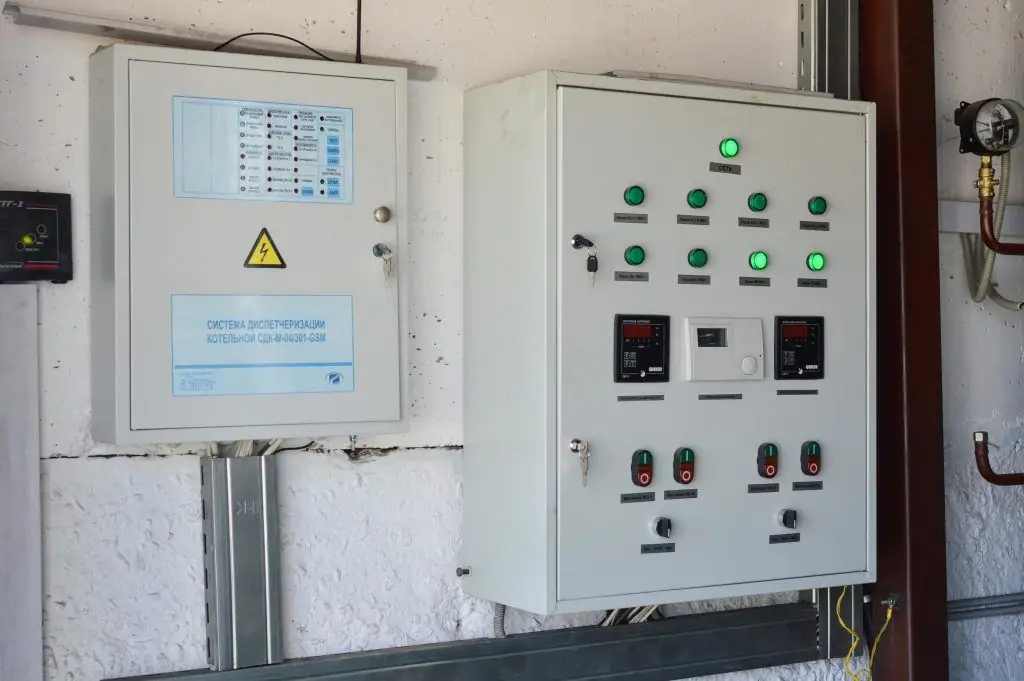
For the design and implementation of an automation system, it is necessary to develop a set of documentation: schematic and wiring diagrams, a plan for laying cables, linescommunications; working drawings, instructions for automation devices. Such work can be done by the engineering services of the enterprise operating the boiler room, or with the help of third-party organizations that provide professional services in the field of automation.
In the latter case, an agreement is drawn up for dispatching a boiler room, which indicates the objects of automation, the cost of work according to the estimate, payment terms, deadlines and responsibilities of the parties. After the completion of construction and commissioning works, a commission of interested parties accepts the control room and the technological equipment connected to it. Acceptance tests are being carried out according to the approved program and methodology.
The estimate for the dispatching of the boiler room includes the following main sections:
- list of mounted equipment, automation equipment, their price list and required quantity;
- types and cost of installation work;
- cost of auxiliary materials;
- overhead;
- estimated profit.
Recommended:
Essence and concept of organization. Form of ownership of the organization. Organization life cycle
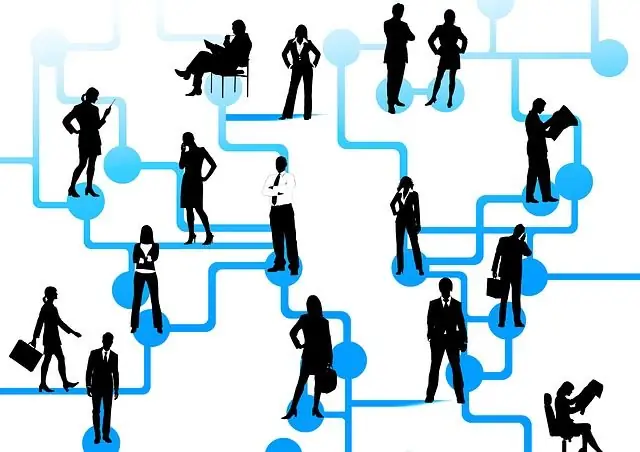
Human society consists of many organizations that can be called associations of people pursuing certain goals. They have a number of differences. However, they all have a number of common characteristics. The essence and concept of organization will be discussed in the article
The concept of organization. The purpose and objectives of the organization
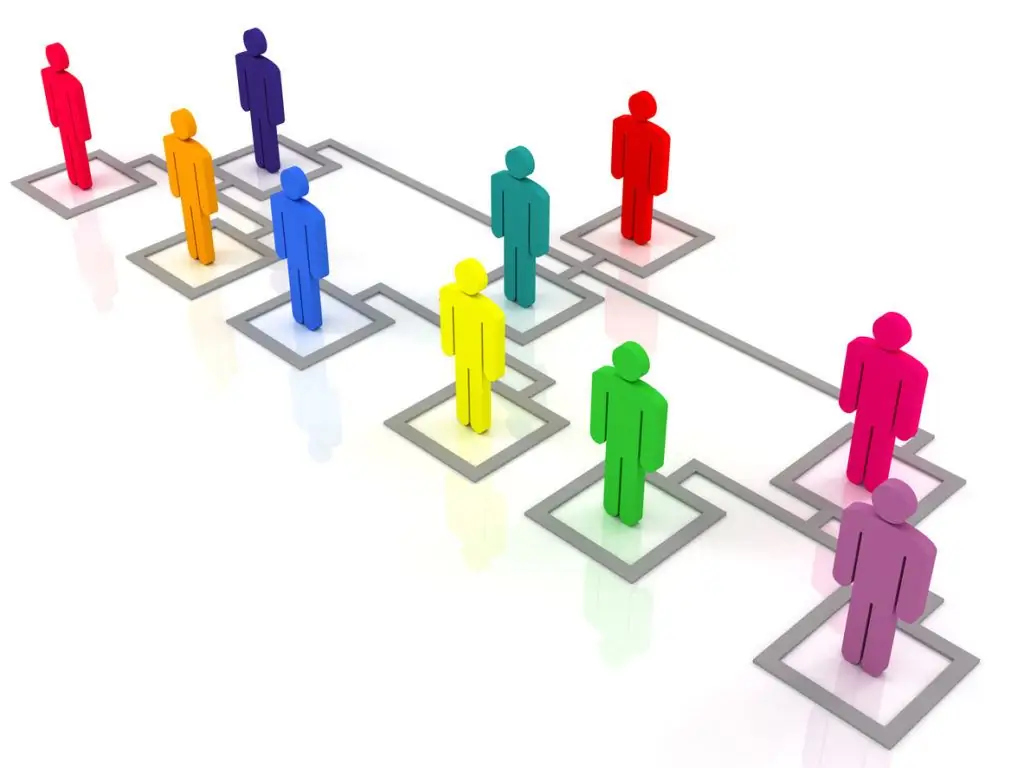
An organization is defined as a group of people interacting with each other to achieve common goals, with the help of financial, legal and other conditions. Goals before them are set by the head and provides them with material, labor, information resources. This approach is an effective method of coordinating work in the company to quickly achieve certain desires
Helicopter: device, types, control system, purpose
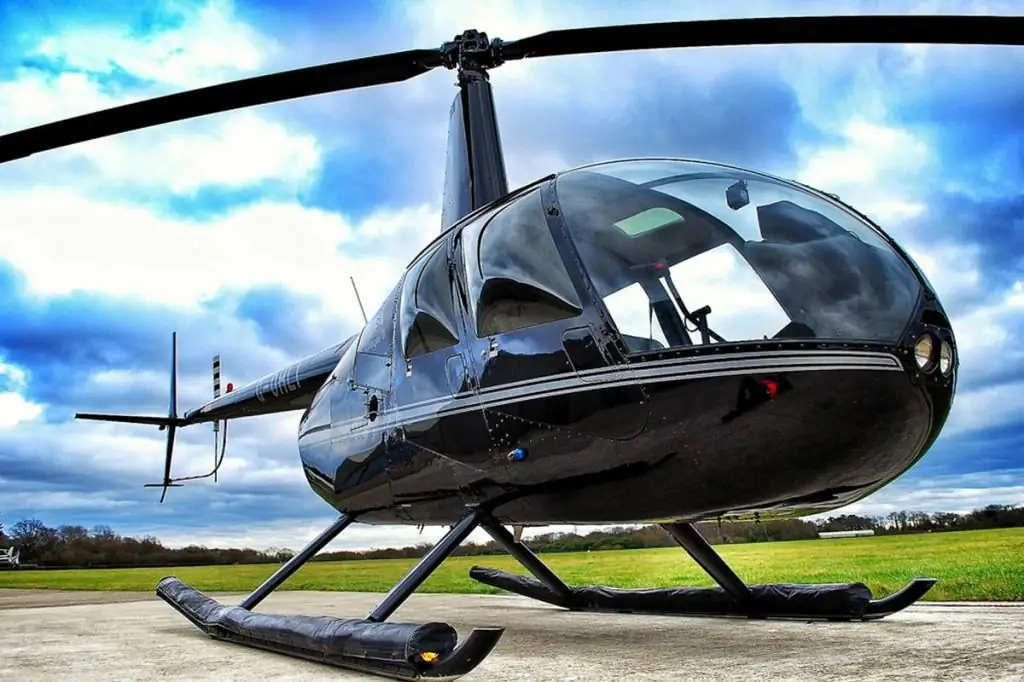
A lot of time has passed since the launch of the world's first helicopter. The design of the machines has undergone considerable changes. Today, several types of helicopters are distinguished depending on their design, number of engines and other characteristics
Organization of labor is The system of labor organization
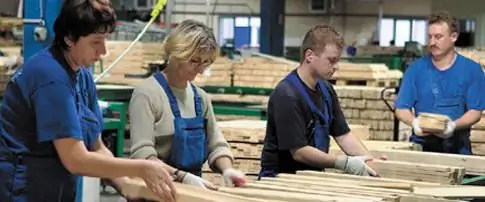
In modern conditions, the need for high labor organization is growing as the competitive environment and production efficiency grow. Organized labor has always provided and provides the highest results. The system of labor organization at a high level becomes a guarantee of effective activity in any field
Organization of an internal control system in an organization: creation, purpose, requirements and analysis
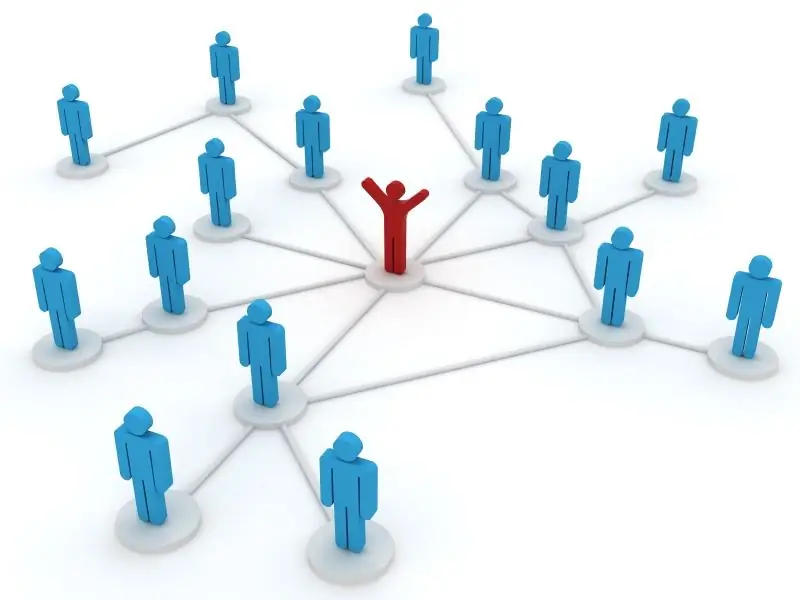
Any profitable enterprise carries a potential profit for its owner. What competent entrepreneur would not be interested in the conditions of functioning of his own offspring, bringing him such serious income? It is precisely because every businessman in his right mind and with an objective attitude to the management of his company is afraid of losing his profit and becoming bankrupt one day, he introduces a system of internal control over the organization's activities