2025 Author: Howard Calhoun | [email protected]. Last modified: 2025-01-24 13:10
CNC bending machine is a modern universal tool for the production of parts of complex shape from sheet material (usually metal). Choosing the right equipment with a huge number of options is not so simple. Everyone wants a durable, accurate and reliable machine at the best possible price.
Design
Consider the device of a CNC bending machine:
- Working moving parts.
- Electric stuffing.
- Software.
The main working body of a CNC bending machine is a traverse. The exact dimensions of the resulting part depend on its movement. Since the length of this beam is quite large, 2 points along the edges are used to control the position. 2 displacement sensors installed.
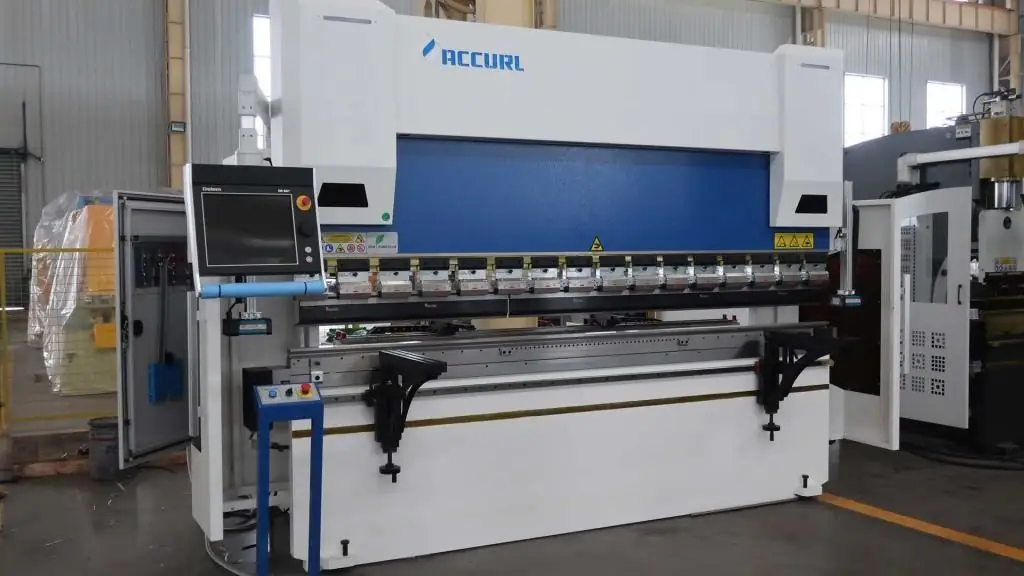
In some machine models, the middle part is controlled, called the rear programmable stop. Traverse movement accuracy can reach 0.01mm. The resulting bends of the part depend on the design features and the availability of options: straight, semi-circular, with several bends.
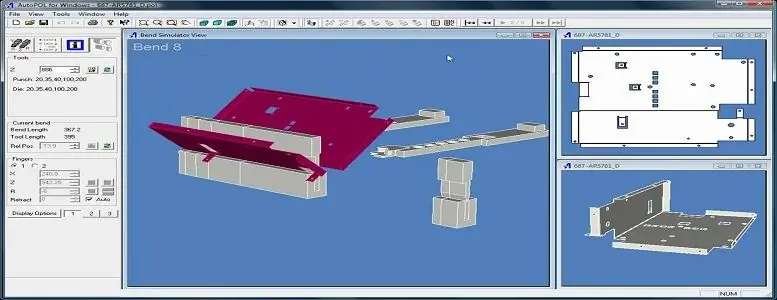
To practice the technology and learn rack programming, there are CNC bending machine simulators. Models on the screen are presented in 2D and 3D views. Primary development of the process of bending a part on a computer allows you to reduce the risks of programming errors. This will avoid the cost of released marriage and breakage of the working bodies of the press.
Which model to choose?
The main criteria for choosing a CNC bending machine:
- Dimensions of the working space corresponding to the dimensions of the workpiece: length, width, sheet thickness.
- The type of metal affects the capabilities of the machine. It is recommended to purchase a machine designed for a large thickness multiple of three. For example, copper can be bent with a traverse that will no longer pull steel of the same thickness. The margin of safety will allow expanding production tasks in the future.
- Availability of options. One of these is the ability to install special sponge nozzles so as not to scratch the painted surfaces of the part.
- The presence of add-ons to eliminate the effect of sagging of a long traverse. This usually becomes necessary when the machine is longer than 3 m.
- Machine transportation options.
CNC bending machine can be quickly dismantled to move to another production area. The most accurate are stationary presses with heavy beds.
How does the equipment work?
The traverse before the bend is at the top point. In manual mode, the workpiece is brought to the desired point and the pedal is pressed. Oftenthe operator holds the buttons on the remote control with both hands to start the press. This is a kind of protection against pinching the hands in the bend zone.
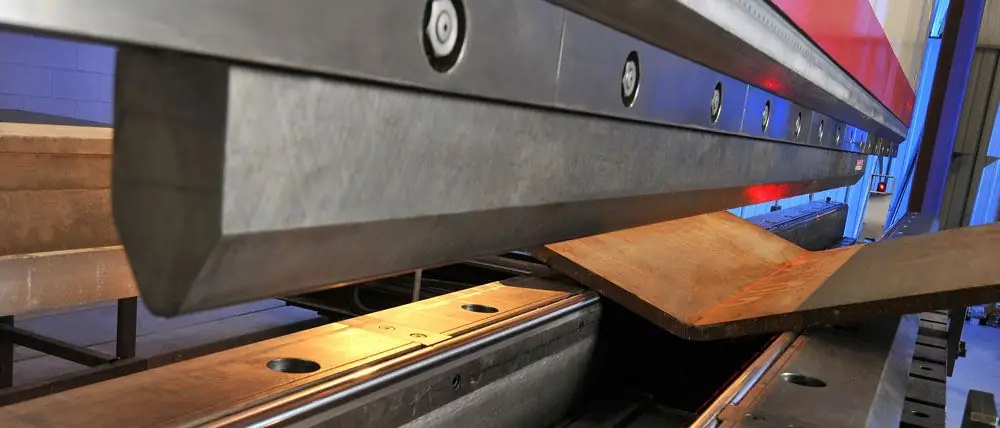
For each type of material and its thickness, a certain working speed of the traverse is selected. This is necessary to eliminate defects when bending the sheet. The movement is carried out from a controlled drive with a displacement sensor - linear and angular - in the engine.
Two sensors provide backlash compensation in transmission mechanisms. Traverse movement accuracy is comparable to that of rulers. You can choose more expensive models with axis positioning of a few microns.
Description of the ERMAKSAN model
Turkish CNC bending machine Power-Bend PRO 2600-100 from the manufacturer Ermaksan has a low cost. An option such as a manual sheet deflection compensation system can be added to the current model. Working length of the unit - up to 2600 mm.
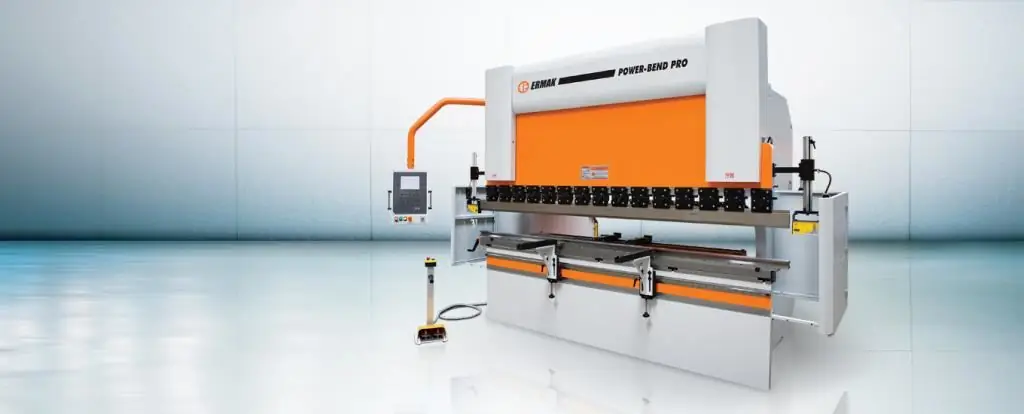
The movement is carried out by hydraulics. The front of the sheet is supported by two stops. Machine operation from Cybelec CybTouch 12 PS controller. The operator sees a 2D model of the process on the screen. The CNC controls four axes. Bending parameters are entered manually, the rest of the process is calculated automatically.
Positioning accuracy is carried out using linear sensors with a resolution of 0.01 mm. A similar sensor is used to control the X axis, which is responsible for the approach and withdrawal of the back gauge. The machine is equipped with a front caliper withT-slot and punch type clamping system.
The machine develops a force of 100 tons. It is recommended to select power modes 3 times higher than the requirements of the technology. This will reduce the likelihood of rapid wear of the working parts, and expand the possibilities of production in the future. It must be remembered that different types of metals with the same thickness bend with different forces.
Recommended:
Glass bending: description of methods and application
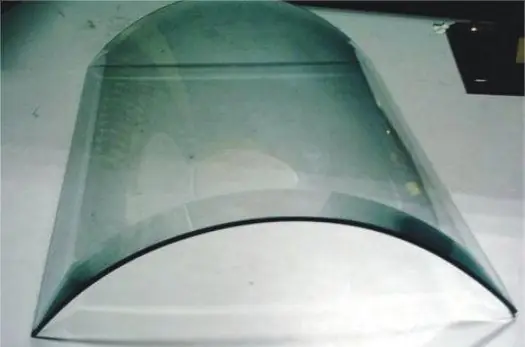
Modern design idea has no boundaries, while pushing building materials manufacturers to create new components and technologies for their production. One such material is curved glass
Bending machines: types, description, principle of operation
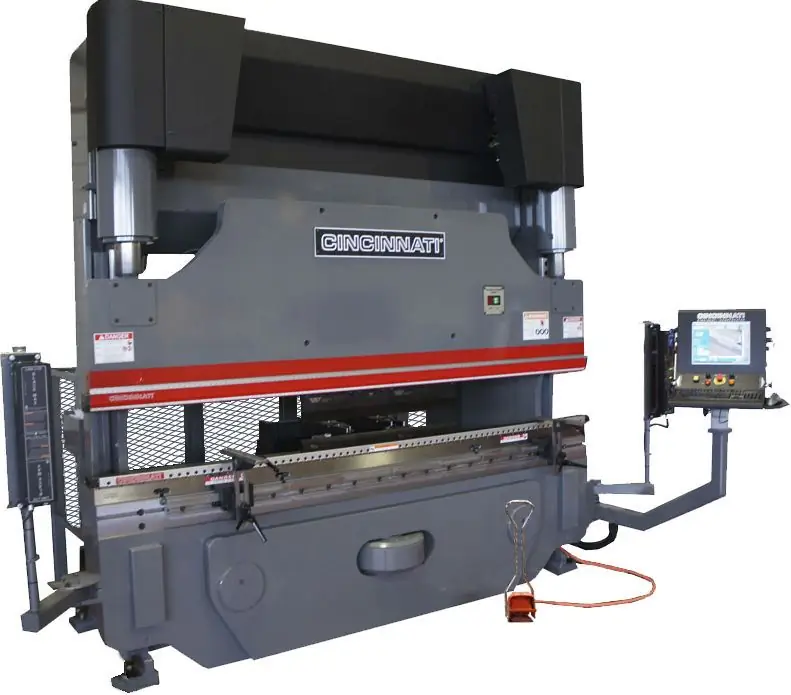
Bending machine: description, specifications, features, principle of operation, photo. Edge bending machines: varieties, device, design, parameters, manufacturers. Manual and rotary hemming machines: what's the difference?
Sheet metal cutting: description, types. metal bending
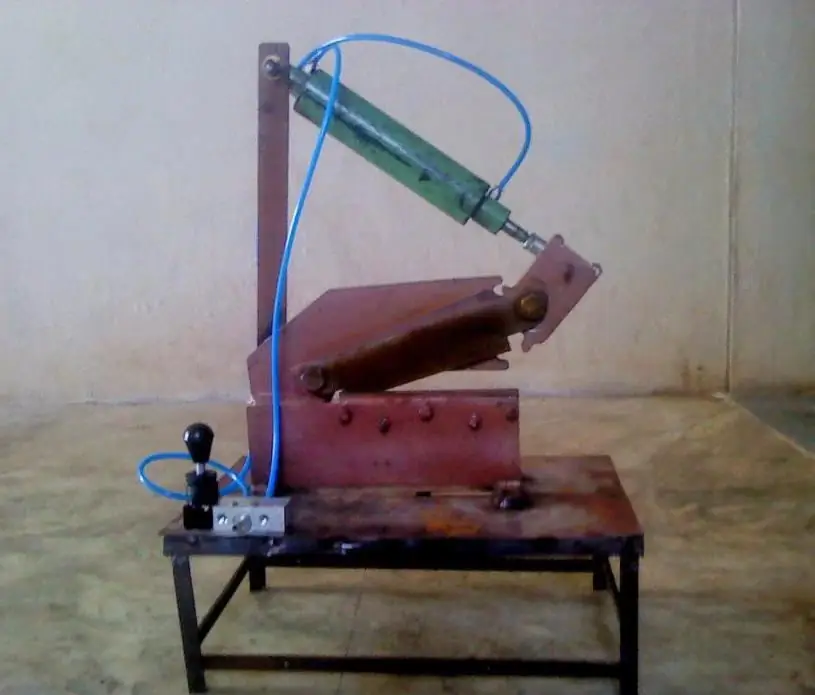
Today, sheet metal cutting is one of the fairly common technological processes that allows you to get blanks of the desired size and shape. However, there are many methods for performing this procedure and a wide variety of equipment
Pipe bending: technology description, features and methods
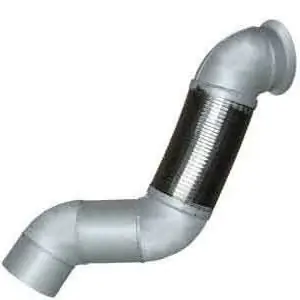
A plastic pipe is a PVC product with a reinforcing layer inside. Thanks to the rapid development of modern technology, such materials quickly replaced heavy and bulky cast iron pipes from the construction industry. Therefore, at home, when arranging underfloor heating and installing a water supply system, the question often arises of how to bend pipes. You will find a description of the technology, features and methods of working with PVC pipes in our article
DIY metal bending machine: features, drawings and recommendations
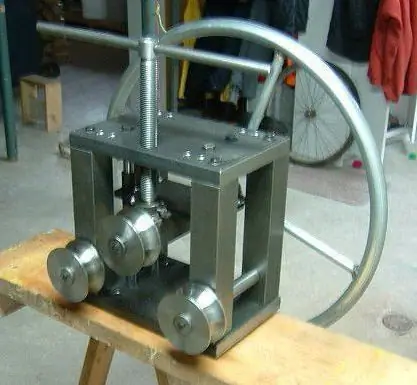
At present, when many buildings and products are made of metal, the relevance of the metal bending machine is becoming more and more. Buying such a device will be quite expensive, but the plus is that it is quite possible to assemble it yourself