2025 Author: Howard Calhoun | [email protected]. Last modified: 2025-01-24 13:10
From the basics of the Human Resource Management discipline, it is known that personnel is a set of employees working at a particular enterprise, according to the terms of an employment contract. Sometimes this population is called a state.
The entire staff of the company is usually divided into two large categories: non-production and industrial-production personnel.
Non-production workers
Non-production or non-industrial personnel is the staff that works at facilities related to non-production assets. These facilities are on the balance sheet of the enterprise and are not directly involved in the production of products. A striking example of such institutions will be sanatoriums based on a large machine-building enterprise (a hospital, a kindergarten, a canteen, a palace of culture, a club, etc.).
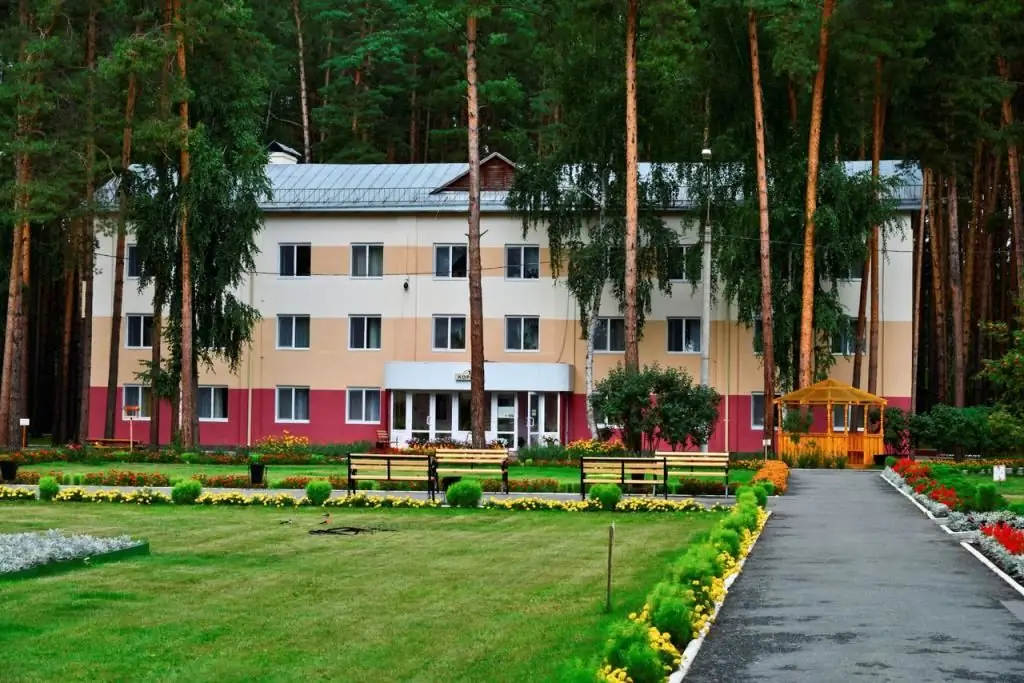
The concept of industrial production personnel
This group of workers is directly involved in the production of products and ensuring a continuous production process. The personnel of the main, maintenance, auxiliary and auxiliary production belongs to the category of industrial production personnel. It also includes employees of research and development bureaus, a management niche, as well as security structures.
The industrial and production personnel of an organization are like cells of the organs of one large organism - a company, without which the life cycle of an enterprise will not last long or end at all.
Enterprise staff classification
As mentioned in the preface, the company's staff is divided into two large subspecies. The industrial and production personnel, in turn, also consists of two links: the management link and the production link. Let's consider them in more detail, and for clarity, let's turn to the diagram below to visually represent what will be discussed.
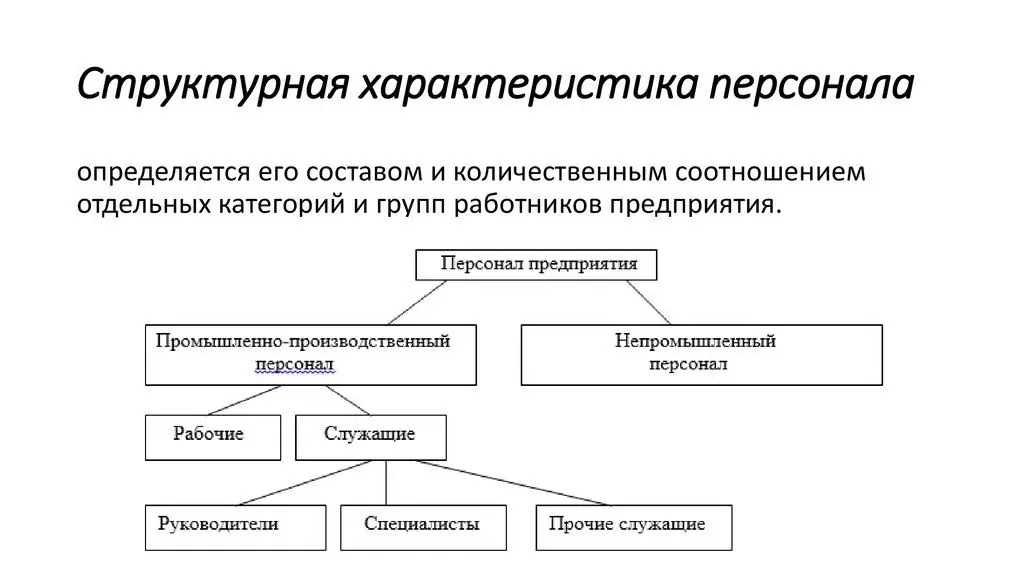
Management staff
In order for the company to successfully operate in the market and sell products with high efficiency, the owners need to assemble a team of highly qualified industrial and production personnel in the field of management. They are usually divided into three more groups. These are managers, specialists and employees.
Leaders are usually assigned to a specific unit in the organization and supervise its work. They are authorized to make the necessary decisions and give orders,in accordance with their official duties. Managerial workers are engaged in setting goals and arranging the work of their unit in such a way that in the future all the planned plans will be fulfilled.
Specialists differ from managers in that they do not have people under their command. They are engaged only in solving the tasks and finding solutions to specific problems. And only for these very decisions and options they are responsible to the main leaders. Examples of such positions are a designer, lawyer, sociologist, technologist and others.
Employees are technical performers who provide the management process for the movement of information flows in the organization. They handle paperwork or provide the necessary conditions for senior management to work. For example, secretaries, cleaners, drivers, cashiers, archive workers.
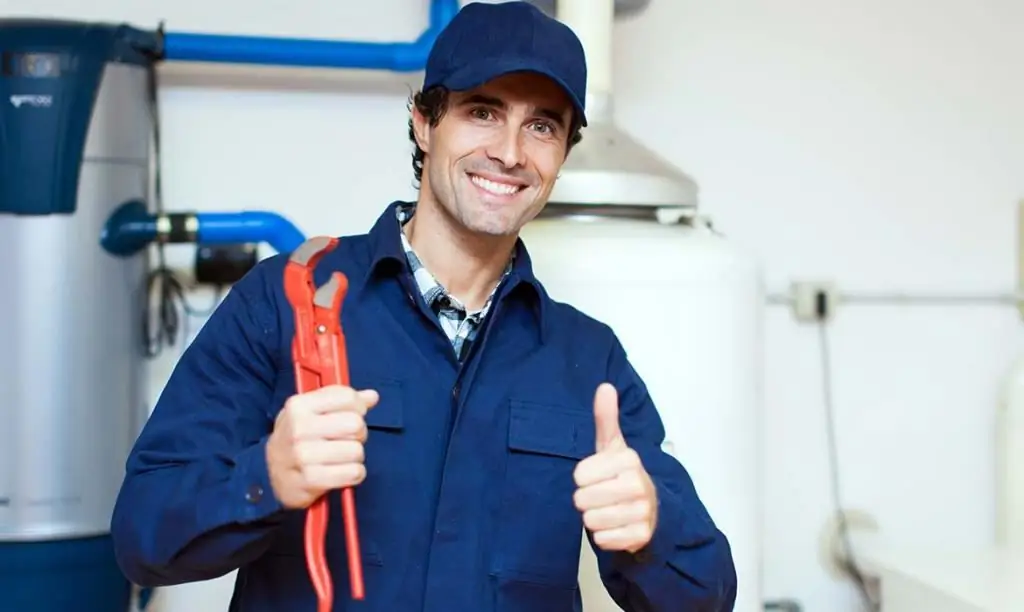
As you can see, managerial work has specifics - it does not produce material we alth, but provides information flows, decision-making and control over their proper implementation.
Production staff
Depending on whether a person produces products or provides a production process, workers of industrial production personnel are divided into main and auxiliary.
The main production worker, one might say, creates products with his own hands. Sometimes such workers use special devices or tools. For example, an adjuster of milling machines with numerical control. He is engaged in the processing of the part, gives it the desired shape. It is clear that he does not scrape metal himself, but uses special milling machines and, with the help of a written program, gives the parts the necessary shapes and monitors the correct processing of the product.
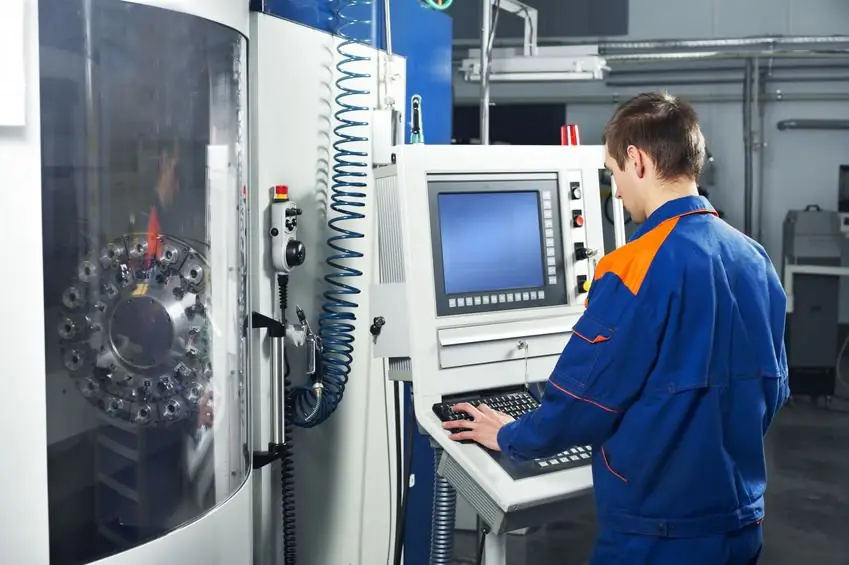
Auxiliary workers include the staff that performs service and support operations. These works are necessary for the normal flow of the production business process. For example, an auxiliary worker is engaged in transportation, warehousing, storing valuables, repairing equipment, preparing technical equipment and equipment for work, product quality control and other duties.
Another type of personnel division is also considered important. Employees of the company may differ in profession, speci alty and qualifications. Under the profession understand the kind of activity, characterized by industry affiliation. The profession requires certain knowledge, skills, and also speaks of specific working conditions. Let's take the teaching profession as an example. The profession belongs to the education sector.
For almost every profession there is a division into speci alties. A speci alty is a subspecies of a profession characterized by a narrow focus. By speci alty, we mean a deeper level of training in a particular industry. Continuing the topic of practical examples, consider such a speci alty as "primary school teacher". From the name it is clear that a person needs deep knowledge in the fieldteaching at the junior level.
However, in most cases, such a division of workers by profession and speci alty is conditional.
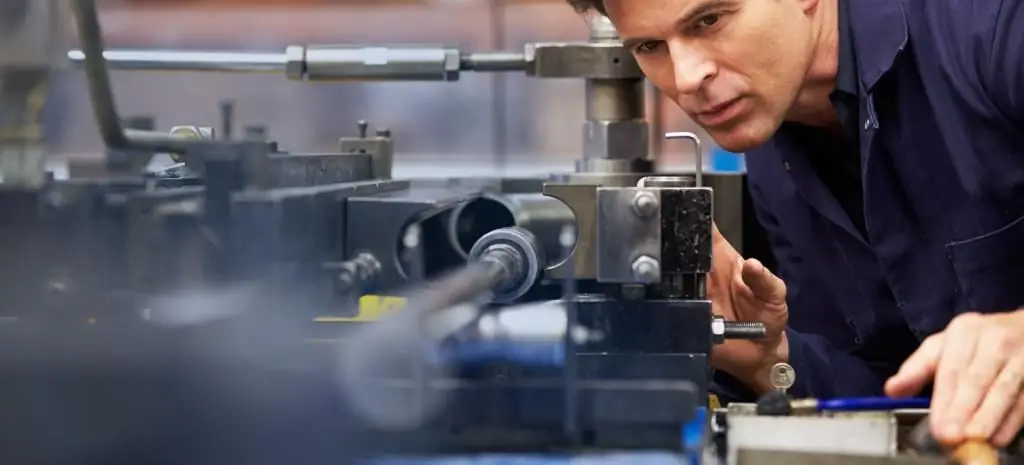
Another important characteristic of the staff is qualification - the level of professional training of the employee. In practice, it turns out that with the movement of scientific and technical progress in production, knowledge becomes more popular, and skills, on the contrary, fall into the purview of machines and computers.
According to the degree of training, the staff of the company is unskilled, low-skilled and qualified. The first type does not provide for the availability of certain knowledge for the implementation of work. The second involves on-site training for six months, and the third requires special training for 2-3 years to successfully and accurately perform job duties.
Obligations of workers
The most important duty of workers of all time is the performance of work in accordance with the employment contract and job description. In specific cases, these duties may be joined by others for certain surcharges specified in additional agreements.
Recently, the role of auxiliary workers in the production process has changed a lot. Now, in most cases, this is the personnel who services automated and mechanized production. And in the age of robots, company management is increasingly forced to either reduce support staff or completely revise personnel policy.
Tariff grades
In productionIn enterprises, personnel are distinguished by the presence of tariff categories. These indicators are still used in calculating the wages of workers. The tariff category is determined by two values: the level of complexity of the work performed and the level of professional training of the worker.
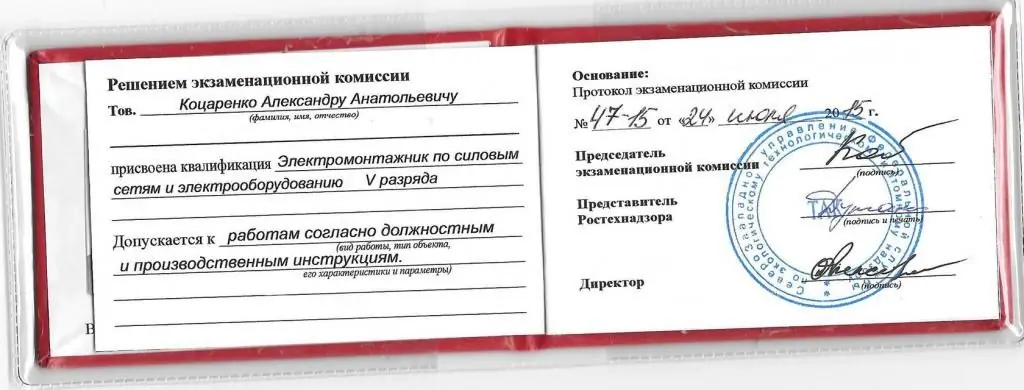
It must be said that the tariff category characteristic is unstable up to a certain point. So, for example, the same CNC milling machine adjuster already familiar to us, who has the 4th category, is trained at the enterprise in certain disciplines and, according to the results of the exams, receives the 5th category, which gives him certain privileges. These include: an increase in the tariff rate of wages, admission to the performance of more complex and labor-intensive work. After some time has passed (after working out the acquired knowledge in practice and their assimilation), he can again try himself in obtaining a higher rank. But the number of digits is not infinite. Each profession and speci alty has its own maximum number of pay grades.
Calculation of the need for workers
It helps to get information whether it is really necessary to expand the staff, to determine the number of industrial and production personnel by professions and qualifications.
The need can be current or prospective. The current headcount is determined by the sum of the required basic staff, based on production volumes, and the additional need for staff.
Basic need is the ratio of production to the output of one worker. In this caseit is better to divide workers by pay principles and categories.
The number of additional staff is calculated by the difference between the total need for staff and its availability at the beginning of the period.
The prospective number of industrial and production personnel of the enterprise is the product of the average headcount and the saturation coefficient of specialists.
The last variable is found by the ratio of the number of specialists to the volume of production.
Norms for the number of industrial and production personnel should also be calculated based on production areas, units of jobs and equipment maintenance standards.
Wages
There are two types of remuneration for industrial and production personnel of an enterprise: time and piecework. For essential workers, time work is not motivational, as they expect to receive a salary or wage rate multiplied by hours worked.
With a piecework form of wages, workers will receive money only for manufactured products in accordance with the rates of the enterprise. For those workers who have an influence on the quantity of products produced most often and set piecework wages. This is where the already mentioned tariff scale and labor intensity standards or work rates come in handy.
Professional development
When an enterprise purchases new ultra-precise and science-intensive equipment, it needs highly qualified personnel to work behind it. And since such specialists are rarely found immediately, the company's managementforced to send existing staff for retraining or advanced training.
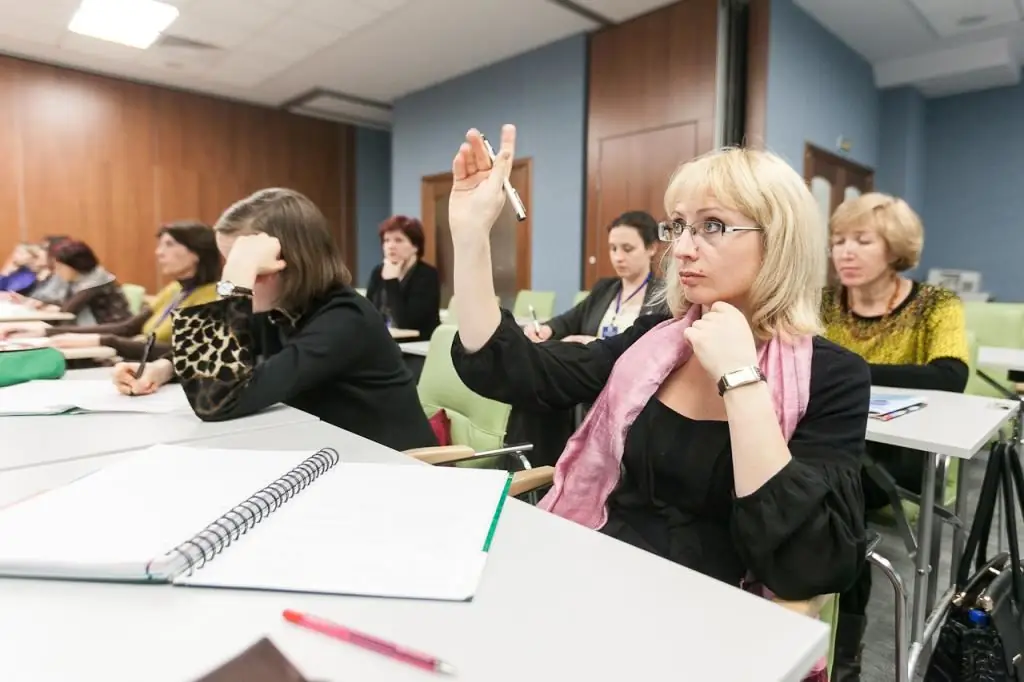
Training can be individual, team or course. There are forms of advanced training: production and technical courses, training in second speci alties, special-purpose courses, schools of masters and schools of advanced labor methods.
Recommended:
Personnel composition: concept, types, classification. personnel structure and leadership
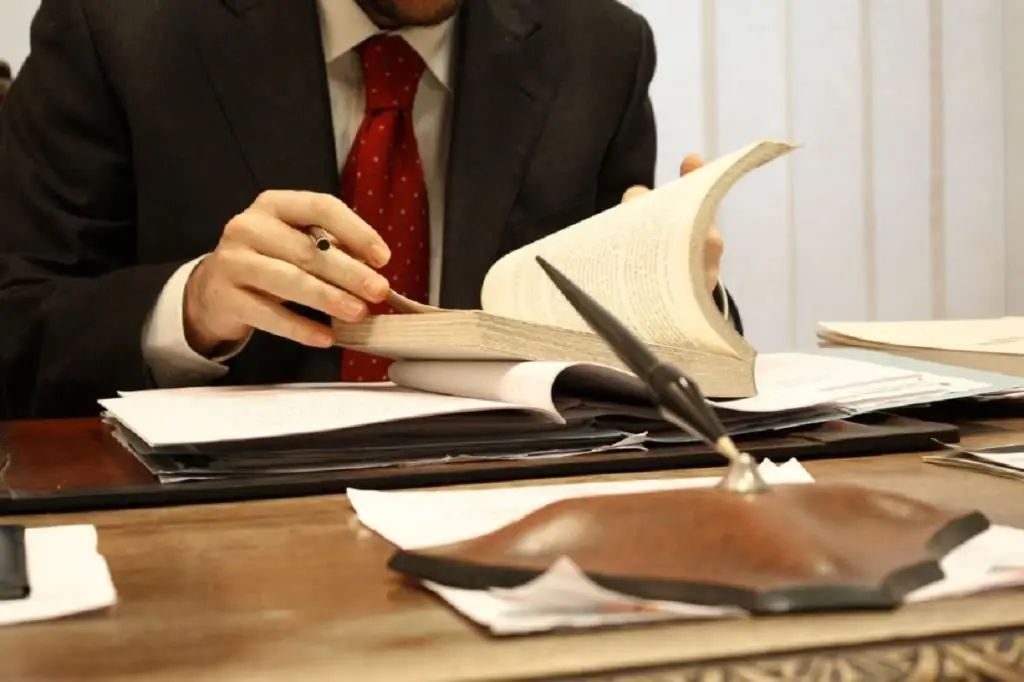
Under state-administrative activity is meant a kind of socially useful work. In fact, this is the professional work of persons involved in the apparatus of state power on an ongoing basis. Any management process implies a set of requirements for management objects, so everyone involved in the civil service must be highly qualified and have special human qualities. So what is staffing?
Production personnel: definition, number, management methods
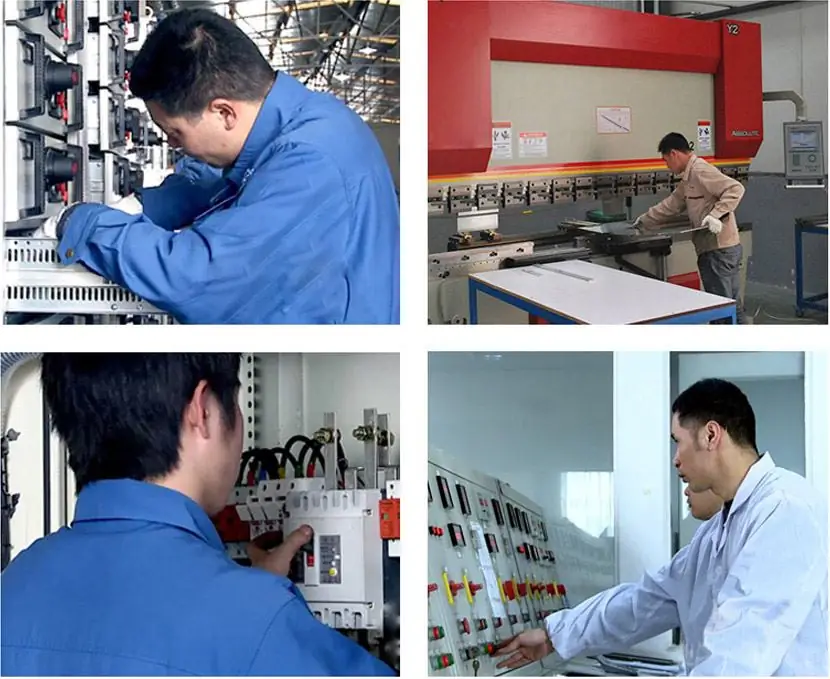
As part of this article, we will consider a general idea of the composition and formation of the production personnel of an enterprise as the main category that affects the company's bottom line
Personnel policy and personnel strategy: concept, types and role in enterprise development
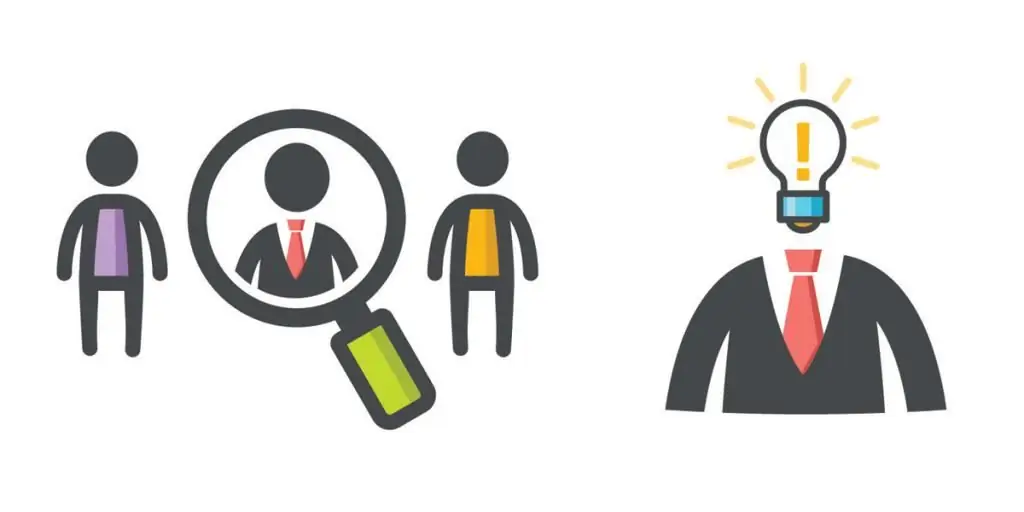
Now the personnel management function is moving to a new qualitative level. Now the emphasis is not on the execution of direct instructions from line management, but on a holistic, independent, ordered system, which contributes to improving efficiency and achieving the goals of the organization. And this is where HR policy and HR strategy help
How to check a Sberbank card: by number, phone, SMS and other ways to check the balance and the number of bonuses on the card
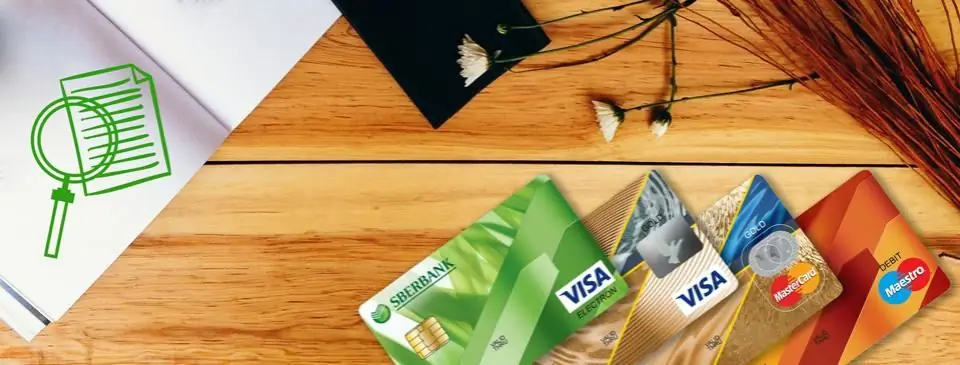
More than 80% of Sberbank customers have plastic cards. It is easy and convenient to use them, besides, they allow you to save time when performing transactions. To always be aware of the amount of funds on a credit card, you need to know how to check a Sberbank card
Employee personnel number: how is it assigned? Why do you need a payroll number?
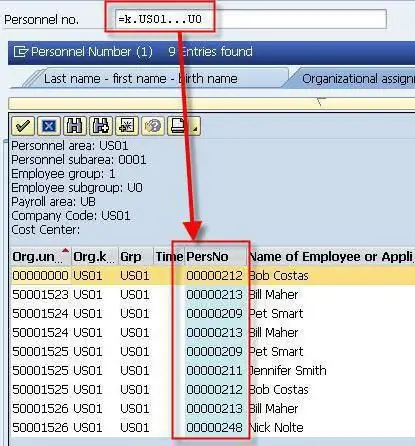
Personnel number is a concept not familiar to everyone. However, most employees have it. Some employees of the personnel department have difficulty thinking about how to correctly assign this number. However, there are no difficulties in this operation