2025 Author: Howard Calhoun | [email protected]. Last modified: 2025-01-24 13:10
Semi-automatic welding in protective gas environments is by far the most advanced technological approach to the implementation of metal joints. But even this group of welding methods is not free from shortcomings, which manifest themselves both in the splashing of the melt and in the difficulties of maintaining the standard parameters of the arc. Pulse welding helped to solve these problems in many ways, which requires the use of special equipment and compliance with special organizational rules, but from the point of view of the quality of the seam, it fully justifies itself.
Technology Features
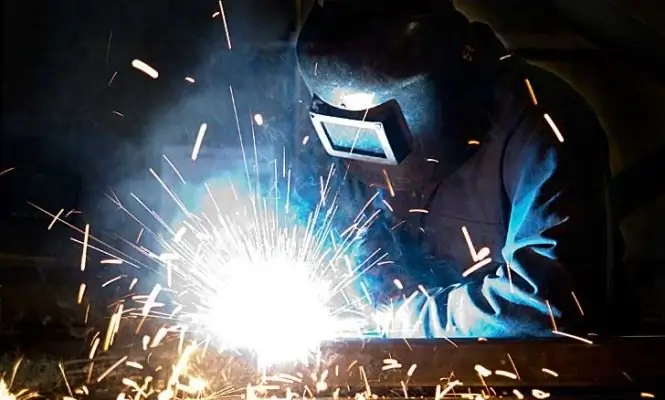
The method involves applying additional current pulses to the base welding seam, the frequency of which can reach tens of hertz. Remarkably, the percentage of pulsed current relative to the main indicator is up to 15%. Today, technologies are also being developed for feeding doublepulses under modulation conditions. This makes it possible to change the angles of inclination of the thermal effect, the shape and the gables. For the operator, this means increasing the functionality of the process in terms of the ability to control fine metal transfer. In other words, pulsed arc welding does not minimize the same effect of melt spatter with an increase in the consumption of electrode powder, but provides more means for its regulation. If we talk about the differences from conventional semi-automatic welding, then the pulse-arc technique also eliminates the need to perform cleaning of the working area, is characterized by a decrease in metal burnout, and also provides more space for the current to flow. And all this is achieved in the same temperature conditions.
What equipment is used
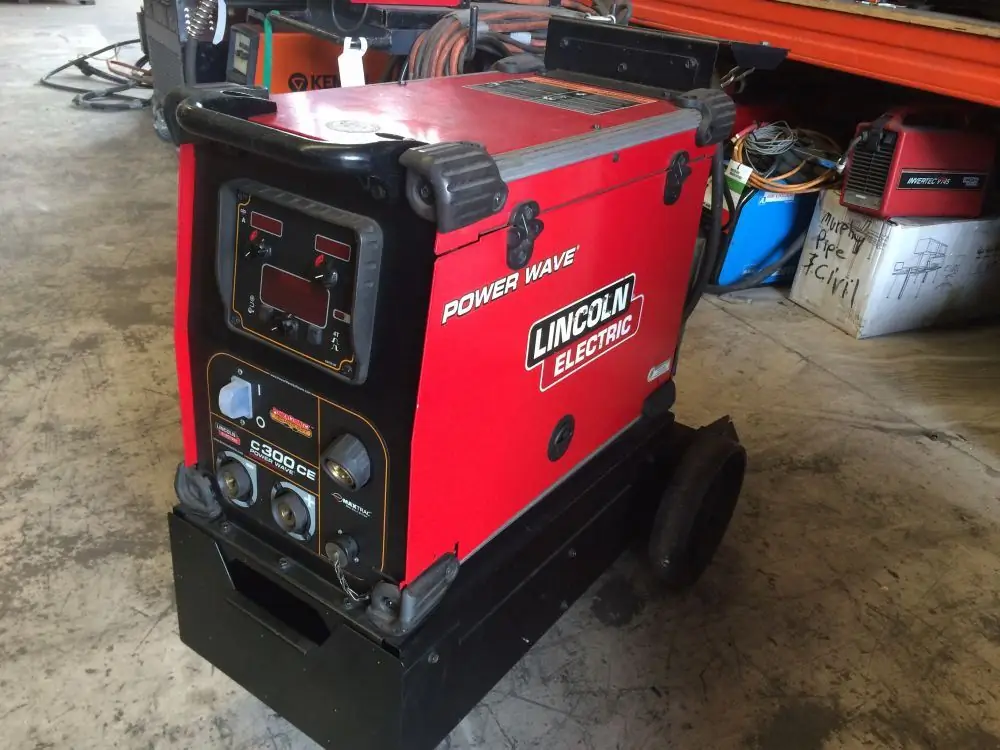
Mostly these are devices operating in MIG / MAG welding modes and supporting the possibility of smooth adjustment of currents. There are two groups of pulse welding machines:
- Models with integrated gas-cooled (automatic) wire feeder.
- Models with optional (pluggable) wire feed system. In this case, liquid cooling is provided.
In both options, the operator can rely on the possibility of point control of the frequency and size of the droplets of molten metal, which are transferred to the weld pool. Similar functions are present in standard semi-automatic machines, but there is a fundamental difference in two points. First, the current adjustment rangeextends from the minimum to the maximum value. Secondly, the pulse arc, regardless of operator control, does not allow short circuits and almost eliminates spatter. In working with non-ferrous metals, the possibilities of detailed adjustment of the apparatus for specific operating modes are especially manifested. For example, a modern semi-automatic pulse mode for aluminum welding supports synergic control, which allows auto-tuning for workpiece thickness and wire guide speed. The new MIG-Pulse modes, for example, also prevent sagging by crushing crystals in the melt zone.
Preparing the machine for operation and setting up
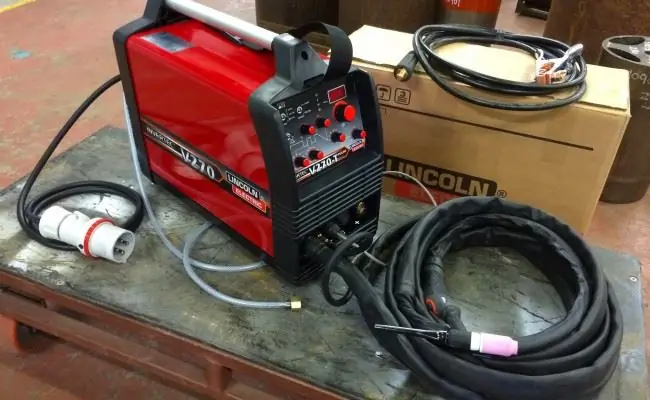
First of all, the main components of the welding station are connected. The design will include the inverter itself, transformers or converters from the power source, gas cylinder and burner. Next, the optimal modes are set. For example, how to set up pulsed TIG welding? This is done through the control panel of the device, where you can set the type of welding process, as well as specific parameters for current strength, wire thickness, etc. By the way, the frequency pulse range is usually from 0.5 to 300 Hz. The higher the frequency, the more operational effects can be realized automatically. In particular, this concerns the reduction of the pore size in the weld structure and the narrowing of the arc. Conversely, in the low range, more efficient control is realized in terms of choicepositions. So, experienced welders consider the arc direction from bottom to top (PF mode) to be the most optimal.
Advantages of contact pulse current
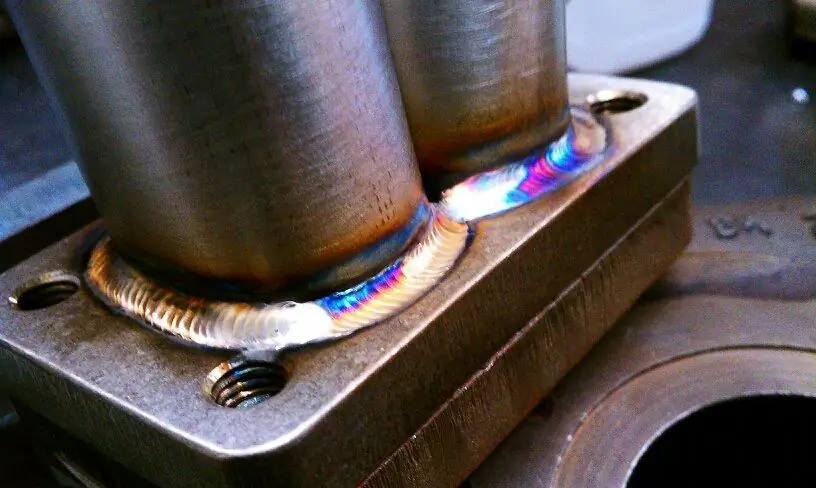
This kind of frequency controlled welding is also called resistive or fusion welding. It differs from the arc technique in that the pulsed current flows through two separated products. What are the benefits? New possibilities and advantages of pulsed contact welding are determined by the increase in the current strength that occurs at the point of contact between two products. To melt the metal, less load is required on the equipment, and the current strength and temperature conditions increase. The result is a reliable and precise connection with a neat seam. By the way, all regulatory possibilities are preserved when performing resistive welding.
Advantages of pulsed TIG welding
The combination of the pulse current mode and the TIG welding method is used infrequently, but it has a number of important advantages. To the greatest extent, they relate to the possibility of reducing heat input, but are not limited to this. When working with thin sheets of stainless steel at high frequencies, the accuracy of the formation of the seam can be achieved. Changing the current parameters during TIG welding from maximum to minimum with pauses also minimizes the heating of the workpiece and its warpage. At medium frequencies, more efficient current concentration can be achieved, which contributes to deep penetration at standard values.heat input. Also, due to the fine-grained structure, welding of stainless steels at an average pulse frequency provides high corrosion resistance of the weld. In the future, there is no need to apply special protective coatings, since the very structure of the material does not support the development of rust.
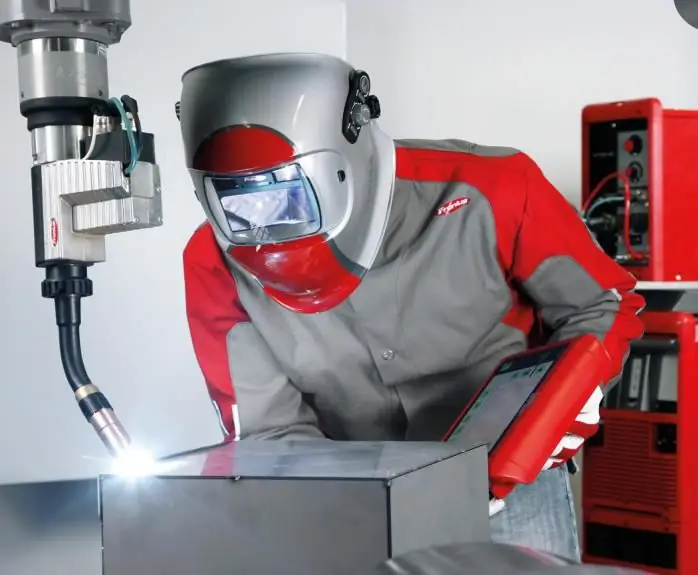
Advantages of pulsed MIG welding
The main feature of this method is the non-contact method of transferring the melt from the wire to the welding zone. In combination with the current pulse mode, this approach gives the following advantages:
- Saving gas and wire resources. Consumables with smaller parameters are used, and the protective gas environment can be used for various tasks without the selection of additional burners and tips.
- Low smoke and spatter. Again, due to a higher degree of control and power costs, in principle, the thermal treatment process is optimized and negative factors are reduced.
- High performance. In MIG mode, pulse welding provides a higher melt efficiency with the same technical and operational parameters of the equipment.
- Reliability and safety. Comprehensive control of the welding process is expressed not only in the regulation of spatter and automation of individual functions, but also in the support of a whole set of protective options with shutdown in case of overheating.
When pulse welding is used
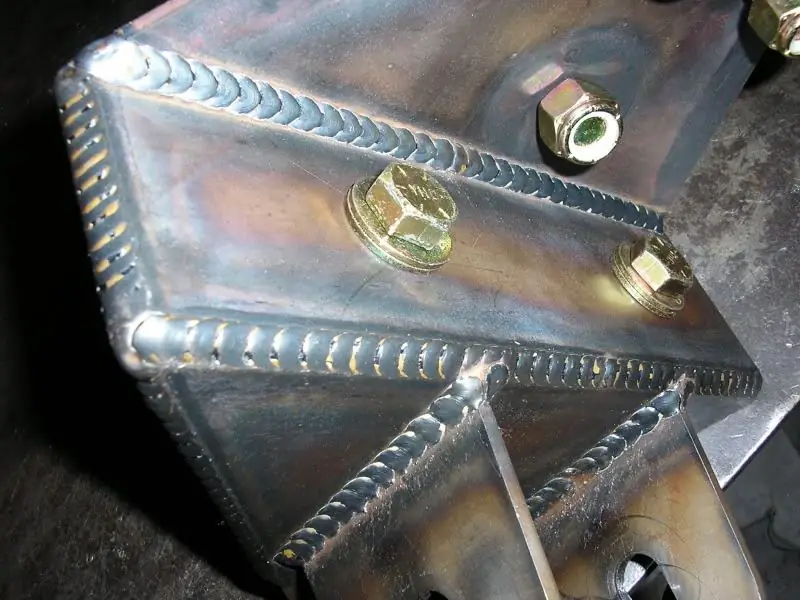
Technologywas developed primarily for stainless steel and today is one of the most effective methods for welding such steels. At the same time, its scope has expanded significantly, covering operations related to the processing and joining of low-carbon steels, aluminum, copper, as well as silver and titanium. Spot pulse welding also performs well when joining thin-walled parts made of both ferrous and non-ferrous metals. Especially the combination of pulsed current with a tungsten electrode allows minimizing the risks of burn-through of workpieces in the form of thin sheets from 1 to 50 mm.
Weaknesses of pulse welding
Like all welding technologies, including modern ones, the pulsed method is not without drawbacks. Despite the pronounced advantages, it is rarely used in solving typical problems due to the high cost of equipment, an increase in organizational costs and a number of negative technological nuances. In particular, TIG pulse welding is characterized by low productivity and low wire feed speed. The use of other modes is limited by high requirements in terms of the choice of mixtures with protective gases. That is, the method is mostly highly specialized and is only suitable for use in certain operations with certain conditions.
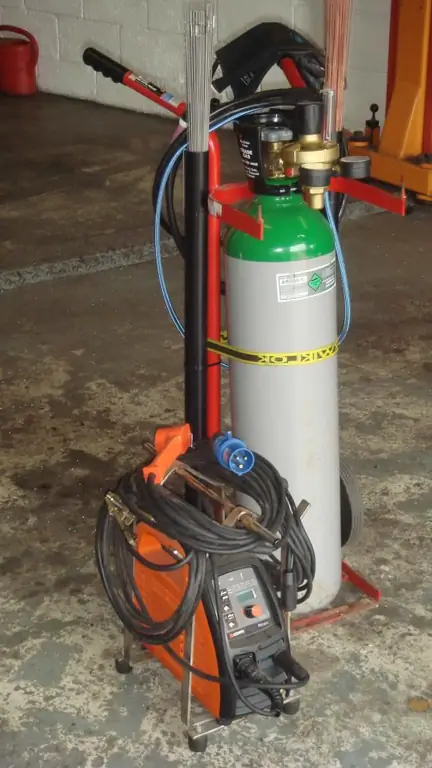
Conclusion
The ability to precisely control the current is a logical continuation of the semi-automatic inverter welding concept, which makes welding processes more flexible and functional. Another thing is that along with the extension of the optional, various restrictions on the use of the method are also imposed. At the amateur level, of course, the need for pulsed welding, for all its merits, is not yet so obvious. The same investments in equipment and consumables are unlikely to be justified even taking into account the receipt of a high-quality seam. The situation is different in industry and professional construction, where minimizing melt spatter in in-line welding justifies the organizational complexity.
Recommended:
"Quality Circles" is a quality management model. Japanese "Quality Circles" and the possibilities of their application in Russia
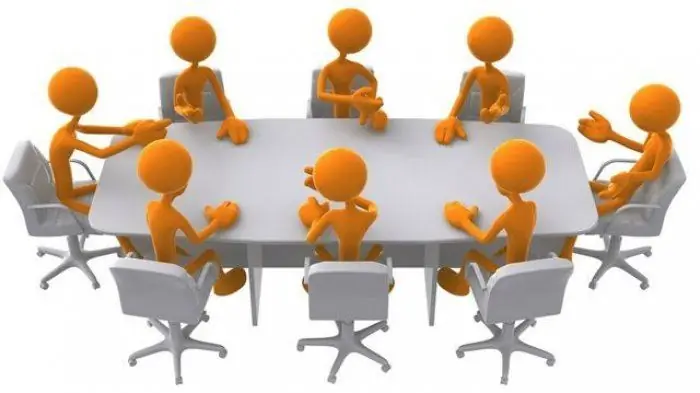
Modern market economy requires companies to constantly improve their technological processes and staff training. Quality circles are a great way to involve active employees in the workflow and implement the most productive ideas in the enterprise
FC "Pulse": feedback from employees about work, salary, employer. Pharmaceutical company "Pulse", Khimki
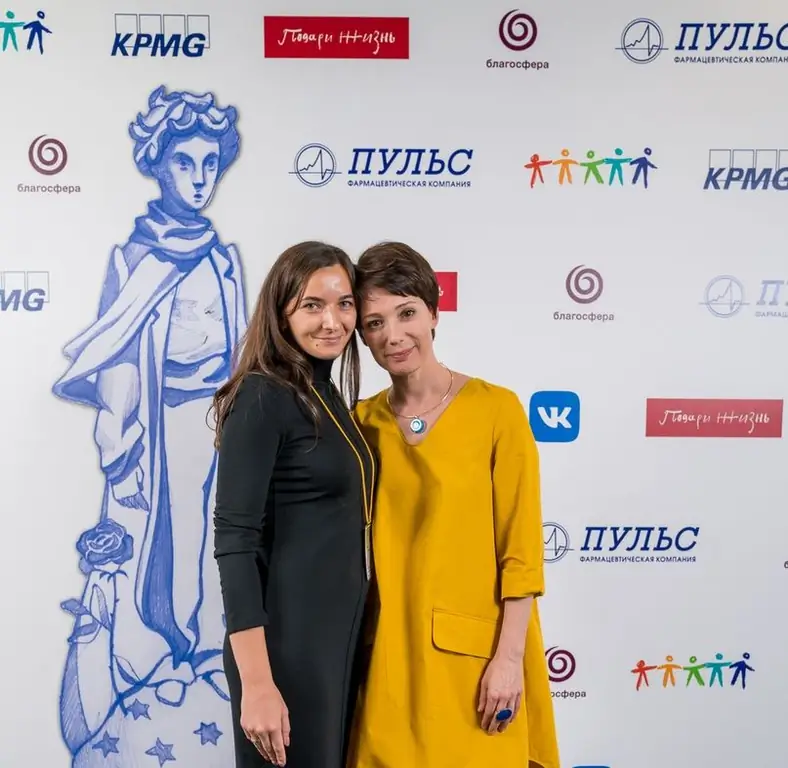
Reviews of employees about FC "Pulse" will be of interest to everyone who is going to get a job in this company. This is a fairly large pharmaceutical enterprise, which involves specialists from various professions. There are always vacancies here, as the company is constantly developing
The main consumable for welding - welding wire
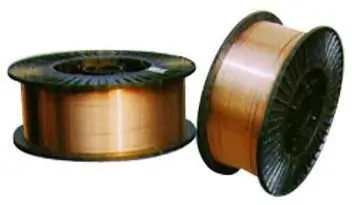
Welding wire is used in various welding operations, it is the main consumable material that acts as an electrode. Welding operations require extensive professional knowledge, a responsible approach to the choice of raw materials. For welding structures, it is unacceptable to use random wire of incomprehensible marking and unknown composition
Thermite welding: technology. The practice of thermite welding in everyday life and in the electrical industry
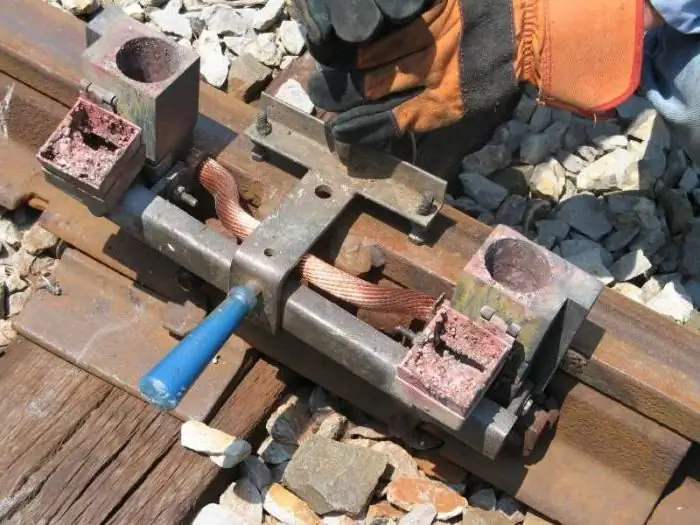
The article is devoted to thermite welding technology. The features of this method, the equipment used, the nuances of use, etc. are considered
Flux for welding: purpose, types of welding, flux composition, rules of use, GOST requirements, pros and cons of application
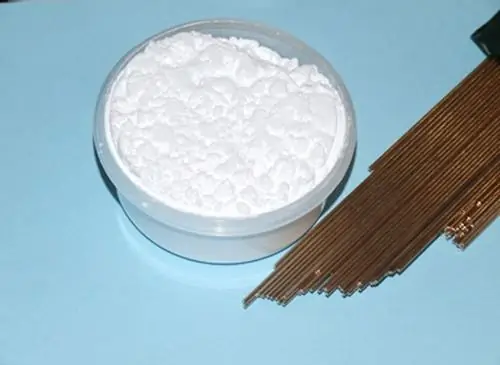
The quality of the weld is determined not only by the ability of the master to organize the arc correctly, but also by the special protection of the working area from external influences. The main enemy on the way to creating a strong and durable metal connection is the natural air environment. The weld is isolated from oxygen by a flux for welding, but this is not only its task