2025 Author: Howard Calhoun | [email protected]. Last modified: 2025-01-24 13:10
Do not rush to close the page when you see the dull "corrective actions" paired with the very sad letters "QMS". Yes, we agree, in terms of the degree of tediousness in the eyes of employees of companies with a quality management system, only labor protection can argue. Meanwhile, the QMS is the most effective and time-tested system with a bright history and ingenious implementation tools. One of the system's key tools is corrective action.
Definitions and clarifications
Corrective action is the action taken to eliminate the causes of a nonconformity. In this case, the key word is "reasons". In other words, everything needs to be corrected so that such inconsistencies never occur again in the future.
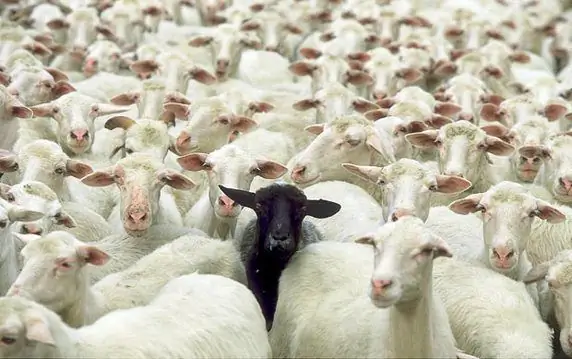
Nonconformity is a departure from established requirements. Note that in the QMS there is no place for such words as "mistake", and this is veryfundamentally. The expression "mistake" implies the presence of the culprit, and, therefore, the appropriate punishment.
There is nothing like this in QMS and never will be. Understanding and accepting is half the success in implementing the QMS.
First of all, let's put everything in its place.
Procedural trio
Corrective action in the QMS is one of the six mandatory procedures described in the legendary ISO 9000 standard. This procedure is closely related to the other two, here is what the "troika" looks like together:
- Nonconforming Product Management Procedure.
- Corrective Action Procedure.
- Preventive Action Procedure.
To put it simply, first any inconsistencies are determined, and then measures are planned and implemented to eliminate their causes.
Key problem: where do we look for "something"?
In order to correct something, you first need to find and fix this "something". Defects in manufactured products, violations of discipline, rudeness in communicating with a key client, distortion of financial statements, an increase in the number of injuries at work - there are a lot of examples of non-compliance, they can be very diverse in terms of the scale of damage to the company and by subject. But it all looks good on paper. In fact, it is very difficult to collect objective production facts of a negative nature. Usually this is done by a quality management representative who has no idea about the nuances of production and other internal secrets.
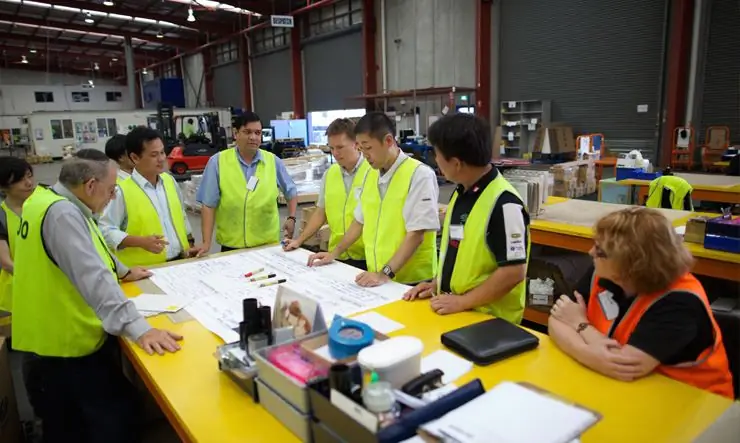
Collectionreal facts for planning and implementing corrective actions should be carried out constantly and in several sources: in internal audit, reports from employees, consumer complaints.
We will not knock on ourselves and the guys
Here it is, the main obstacle to the implementation of a cool quality system, including effective management of corrective actions. You can conduct seminars and write motivational letters to employees about the importance of filling out a non-compliance report form on time so that the company immediately rushes to plan and take corrective actions to eliminate it. They will listen with interest, nod their heads and even thank you for your contribution to the common cause.
But then you run the risk of receiving, at best, a report of a classic discrepancy from the broad masses of workers: it's all about low wages, this is the main discrepancy. Raise it, and everything will immediately become good. The most interesting thing is that most people write such a report from the heart with a sincere belief in success.
What to do and how to live on? Teach, explain, help fill out the form, negotiate with the first manager so that he writes the report first. Not by washing, but by rolling: you need to think and continue to stick to your line. Be as clear and transparent as possible.
Difference between corrective and preventive
Even QMS consultants sometimes have difficulty discussing corrective and preventive actions and explaining the difference between them. Meanwhile, it is quite simple, the difference is clear and quite tangible. Judge for yourself:
- A simple adjustment is to correct the inconsistency in place. Example: a burst pipe that needs to be plugged immediately. This will be the adjustment.
- Corrective action is the elimination of the causes of nonconformity. Why the pipe burst and what needs to be done to prevent this from happening.
- Preventive action is an action to prevent nonconformity or development when a new service or product is introduced. A good and very common example is taking preventive action in all branches of the company if a non-compliance is found in one of them.
It all started with British bombs that didn't explode
There are many examples of corrective actions, including historical ones. The beginning was the British WWII bomb story that started the process approach and all ISO standards in manufacturing.
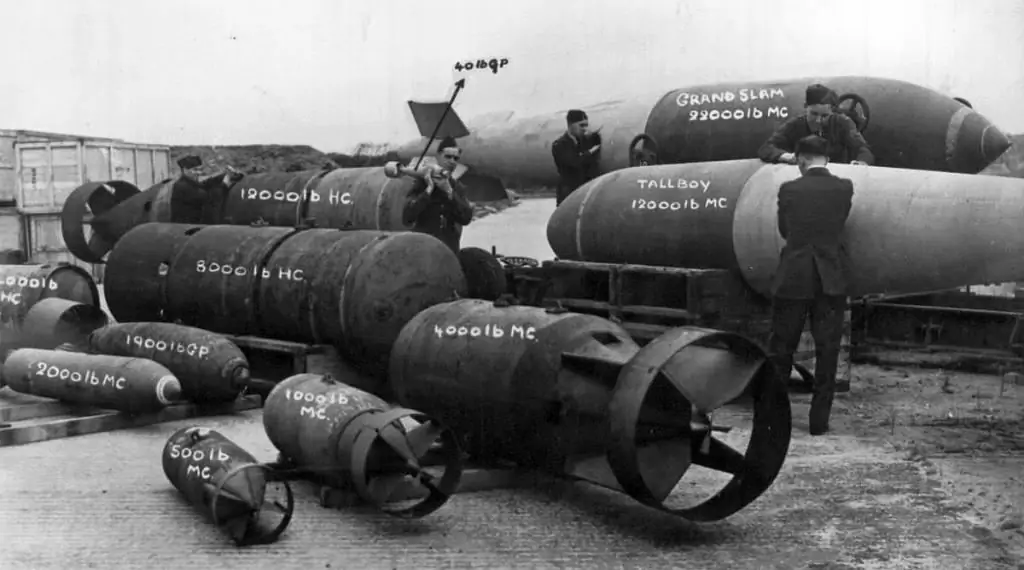
Bombs began to explode frequently in some British military factories before they were shipped (inconsistency). And at other factories, on the contrary, the bombs did not explode - another discrepancy. The solution (corrective action) was found by the Department of Defense. It sent its inspectors to each plant. Now each manufacturer was obliged to prescribe the sequence of all operations, and the controller checked whether the workers followed them. Bombs now exploded in the right place at the right time. Just? Yes. And brilliant.
Toyota and Japanese total quality control
QMS at Toyotahas long been the standard of the Japanese quality model and the subject of general study and discussion. Toyota is the main "base" of Edwards Deming, the author of the Japanese economic miracle with his famous operating principles used in Toyota factories around the world.
Corrective actions are not focused on the personality of the employee, but on his behavior. Not disciplinary measures, but human development and problem solving are the main values of Toyota in this block of questions. The Japanese system of lifetime employment assumes the highest degree of responsibility of workers. And for this, people need to work patiently and carefully.
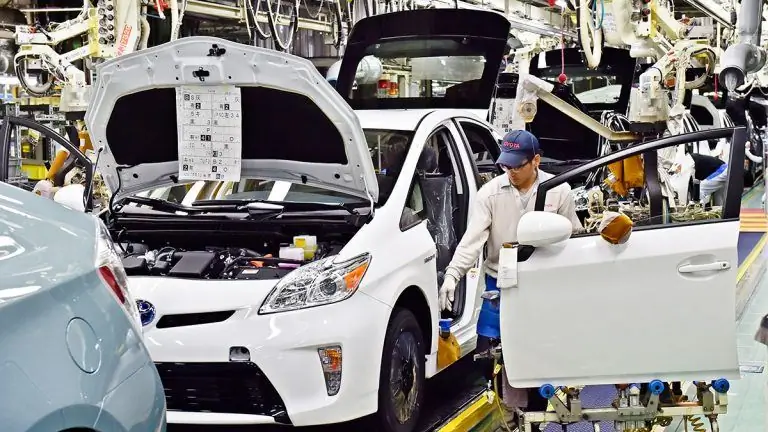
Take, for example, employee tardiness, which is unacceptable in a Japanese corporate setting. But if you think that such unacceptability is an innate quality of people at Toyota, then you are mistaken. For violators of labor discipline, a clear five-step corrective action plan is signed. Quitting is the last fifth step, which is almost never reached.
Toyota's recipe: five steps for violators of corporate discipline
- The first step is a simple reminder from the leader, preferably in the form of a joke or advice to buy an alarm clock. This is not a corrective action.
- If tardiness continues four or more times per year, the first corrective action is taken in the form of a written reminder. The employee must write what he is going to do to correct the situation.
- If the same employee is late at least twice in the next year, a disciplinary meeting will be held with the participation of high authorities. The purpose of such corrective action is to help the worker find a solution as much as possible and, attention, to make sure that the unfortunate person was aware of what the company expected of him. The analysis of corrective actions of the previous stage is carried out. At this meeting, a representative of the personnel department is always present, who acts as a lawyer for the offender.
- If there are two delays over the next year, the employee is given … time off to make a final decision and write a letter to the commission. If the commission decides to keep an employee at Toyota, they pay him this day off.
- The employee now has four years of "probation". If even one delay occurs during these years, the commission recommends that the worker be fired.
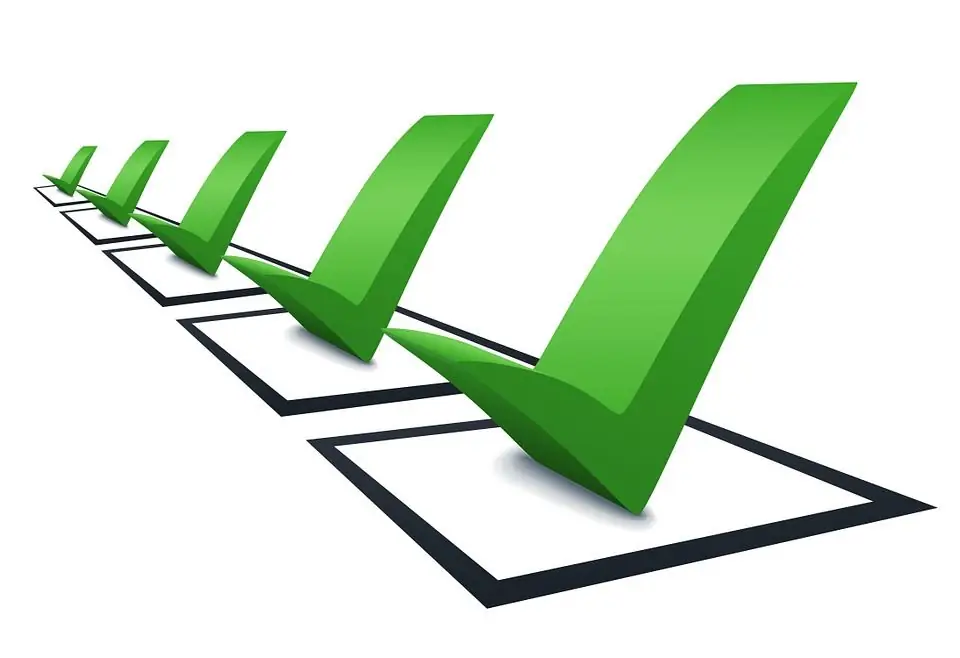
It should be noted that such layoffs at Toyota are extremely rare. Usually, everything is resolved in the previous stages of corrective actions.
You can fire. Just be careful
The principles of "Toyota" can be applied here as well. If you think about it, then the analysis of discrepancies and the search for competent corrective action are approximately the same scheme for finding causes.
Mismatch may occur due to the fact that there is no regulatory document, and employees simply do not know how to perform actions. Corrective action is the creation of an instruction ormemorandum on the order of the operation.
Another reason for non-compliance could be a lack of training or work instructions. There are rules and procedures, but no one brought them to the attention of the employee.
And now the third option: there is a procedure, and training was carried out, and reminded once again. Yes, but the employee is negligent and does not want to work. This is where he needs to be fired, this will be a tough corrective action. It is no longer necessary to prove that this decision fits into the QMS and the principles of Toyota. And in order not to repeat the mistakes when choosing and hiring a new employee for a vacant position, the description of the requirements for a vacancy in the recruiting department should be written taking into account the case with the dismissal.
Nizhny Novgorod "diamond" system: zero defects
At first, the defect rate was 65.9%. A famous example of successful Russian implementation of QMS principles. "Diamonds" is the name of a unique author's system, which was invented and implemented at the small plant "Instrum-Rand" in the town of Pavlovo in the Nizhny Novgorod Region.
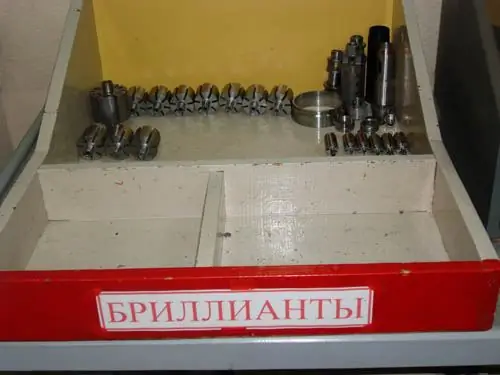
The plant produces pneumatic tools that are purchased in Europe and the USA without prior verification. Instrument-Rand is the only Russian company that has passed an engineering audit by Mercedes-Benz. Naturally, the team went long and hard to this level.
From the very beginning it was clear that any defect can be de alt with only if there is honest and comprehensive information about how it happened. Only in this case it was possible to accurately identify nonconformities and corrective actions to eliminate the cause of the defect. In other words, sincere confessions were needed from the workers, who were in no hurry to do so. The fear of losing a bonus or being punished was persistent and pervasive.

At that time, a system with "diamonds" was invented and implemented, which were … defective parts. Providing information about marriage was a positive development, no one was punished for this. On the contrary, any discrepancy was discussed in the team in order to find together the most optimal and correct corrective action. For the "diamonds" they set up special tables, as in a museum. This is how the psychology of Nizhny Novgorod workers changed, and Tool-Rand began to rise to the heights of total quality management.
Conclusion
Patience, freedom from stereotypes, a good knowledge of the history of standards and excellent communication skills are a set of quite achievable qualities for realizing the most ambitious plans in moving the company forward.
There are many new management models in business literature and the Web: some with exotic names, some with seemingly unusual approaches. Only most of them resemble new candy wrappers with classic filling.
QMS with its system of corrective actions has never let anyone down. Simple and ingenious are the two most appropriate words to describe it.
Recommended:
Mind management: concept, definition, basic principles and thematic books
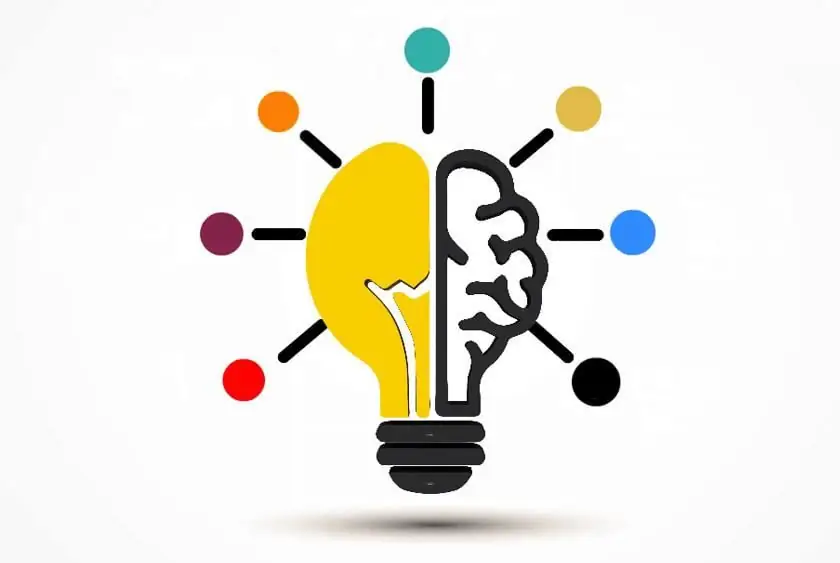
Few modern people know how to manage their time. Despite the popularity of time management, people get lost in the flow of information, and they can’t manage to fix their lives. And all why? For the reason that they do not have a single system for structuring information. Mind management will help you bring order to eternal chaos
Support staff is The concept, definition, working conditions and principles of remuneration
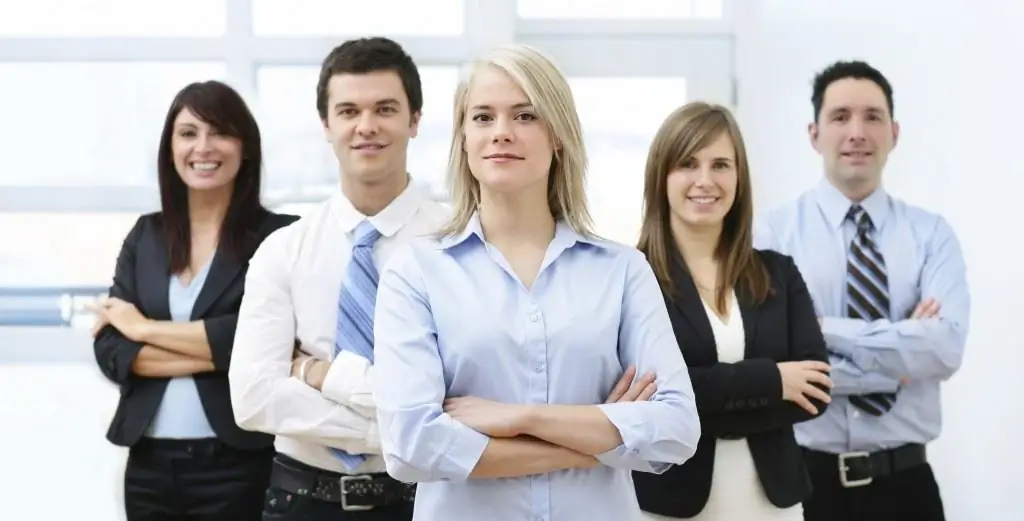
Employees of the organization are divided into main and support staff. Unlike the main support staff, they perform functions that are not related to the main activities of the company. The article discusses the features and characteristics of support staff
The accounting policy of an enterprise is Definition, principles, methods and procedures
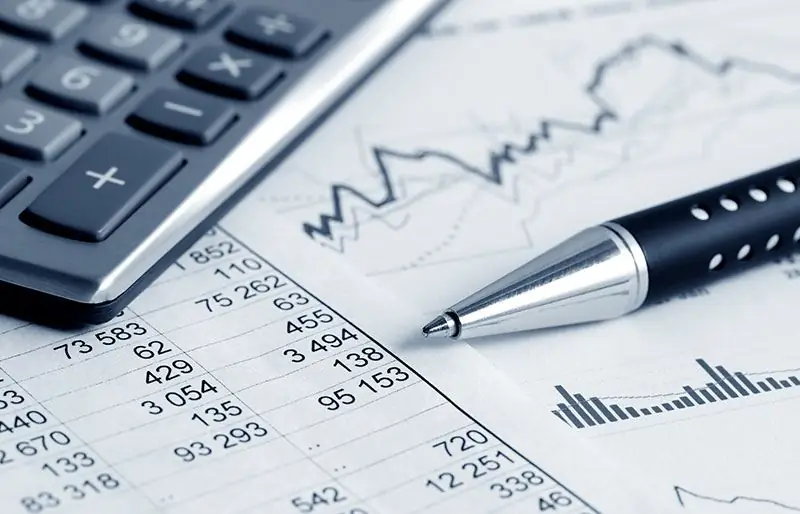
What is the accounting policy of an enterprise? What are its principles, goals, variations? The main components of the accounting policy, examples of the organization of accounting. Techniques, methods of reporting, responsibility. Organization of tax accounting. International and Russian regulations
Low-waste and waste-free technologies: definition, description, problems and principles
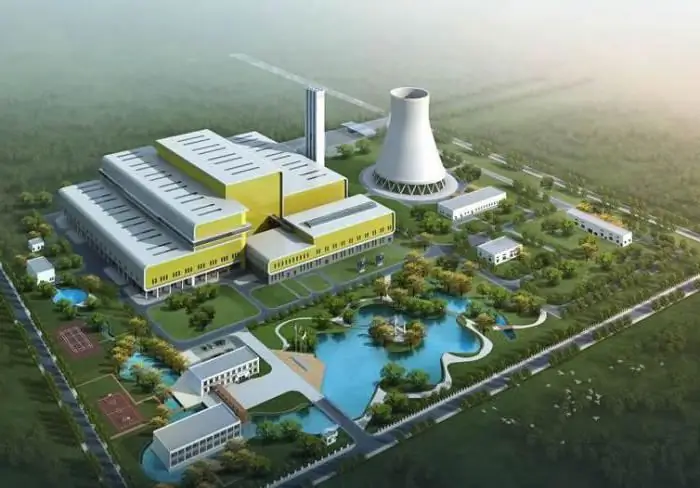
Problems of the harmful effects of industry on the environment have been worrying environmentalists for a long time. Along with modern means of organizing effective methods for the disposal of hazardous waste, options are being developed to minimize the initial damage to the environment
Administrative management: directions, administrative and classical methods, features and principles
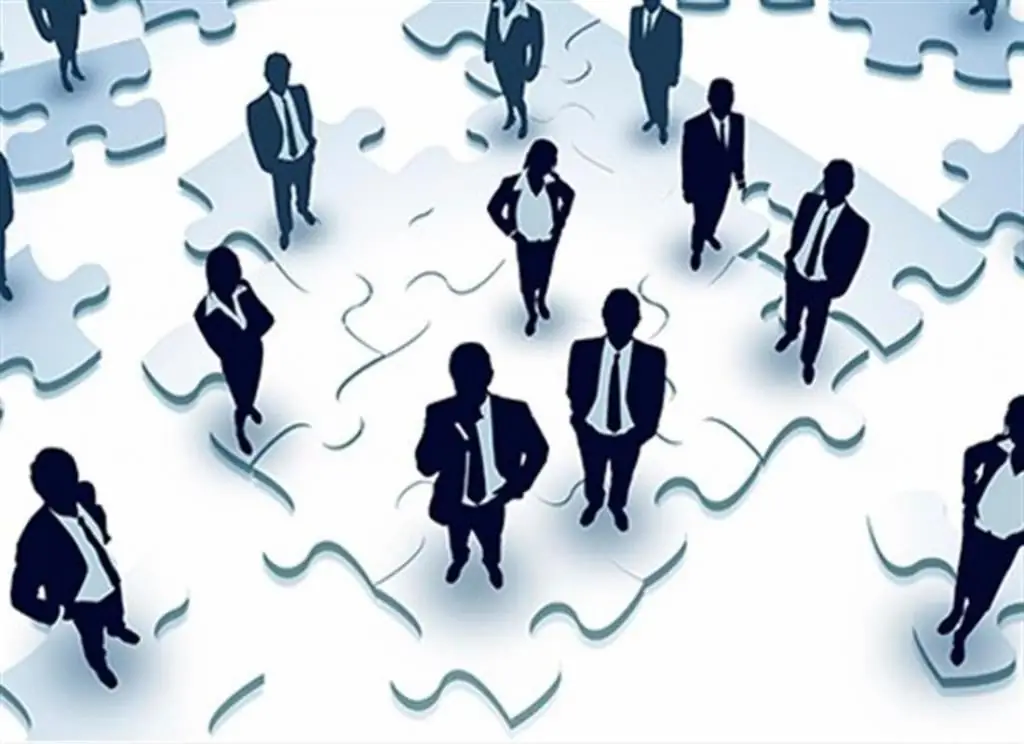
Administrative management is one of the directions of modern management, which studies the administrative and administrative forms of management. At the same time, administration itself is an organization of the actions of personnel, which is based on formalization, strict incentives and strict regulation