2025 Author: Howard Calhoun | [email protected]. Last modified: 2025-01-24 13:10
Lean Manufacturing, also known as Lean Manufacturing, or LEAN is one of the best solutions for organizations looking to increase productivity levels and keep costs as low as possible. The concept of Lean Manufacturing allows the company to operate effectively even in the face of serious competition.
Lean losses interfere with the achievement of the main goals of the Lean system. As well as the implementation of the main principles of the concept. Knowing the types of losses, understanding their sources and ways to eliminate them allows manufacturers to bring the production organization system closer to ideal conditions. Or almost perfect.
Basic Principles of Lean Manufacturing
LEAN concept adheres to certain principles, the implementation of which ensures the improvement of the quality of the final product and the reduction of waste. Lean principles include:
- Determination of the final value of the finishedproducts.
- Understanding the flows that create value.
- Maintain flow data persistence.
- Pull the product by the consumer.
- Continuous improvement.
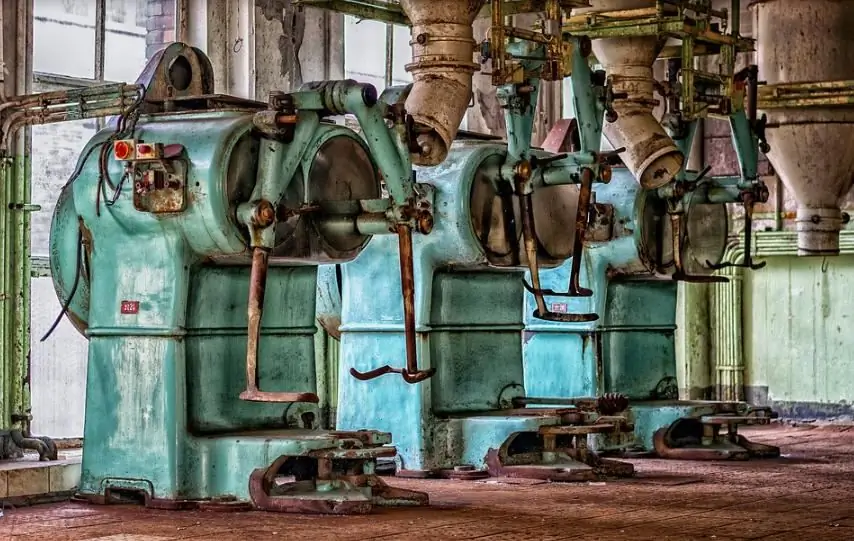
Tools and methods of lean manufacturing
Methodologies and tools of the Lean Management concept are presented in the table.
Tools and techniques | Action on application |
5S | Optimum organization of employee workplaces |
"Andong" | Quickly informing about the problem that has arisen in the production process, for its further stop and elimination |
Kaizen ("Continuous Improvement") | Combining the efforts of the organization's employees to achieve a synergistic effect in achieving common goals |
Just-In-Time ("Just in Time") |
Materials management tool to optimize financial flows |
Kanban ("Pull") | Regulation of the flow of raw materials and finished products |
SMED ("Quick Changeover") | Increase the useful life of production capacities due to the rapid changeover of equipment for small batches of products |
TPM (Total Equipment Service) | All employees of the company are involved in equipment maintenance. The goal is to improve efficiency andcapacity lifetime |
Types of production losses
Losses in any enterprise, both manufacturing products and providing services, are an integral part of the workflow and require minimization or complete elimination. Types of waste in lean manufacturing include:
- losses from overproduction;
- losses due to excess inventory;
- losses during transportation of raw materials, semi-finished products and final products;
- losses due to unnecessary movement and manipulation of employees;
- loss due to waiting and downtime;
- losses due to defective products;
- waste from over-processing;
- losses due to unrealized creative potential of employees.
Overproduction
One of the most important types of waste in lean manufacturing is the overproduction of products and services. It refers to the manufacture of such a quantity of products or the provision of such a number of services that exceed the requirements of the customer. It is overproduction that provokes the appearance of other types of losses: waiting, transportation, excess stocks, etc.
Overproduction losses in enterprises that manufacture any type of product can be represented by the accumulation of work in progress, as well as the manufacture of units that are not required by the customer.
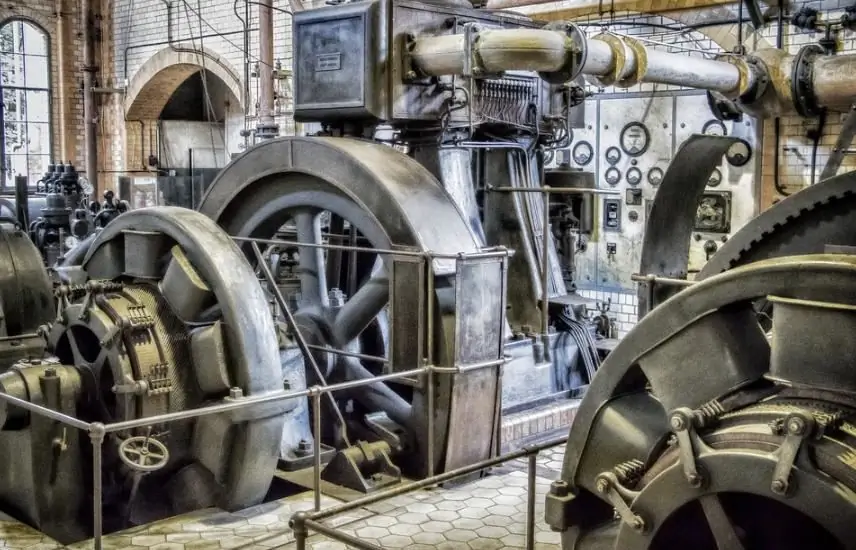
Overproduction in office work can be represented by the following examples:
- preparation of documents, reports, presentations andcopies of them that do not affect the company's activities and are superfluous in the workflow;
- processing unnecessary information that does not play an important role in the work of the company.
To reduce overproduction losses in an enterprise (in an organization), it is advisable to manufacture products (provide services) in small batches that meet the demand of the customer (client), or to produce the number of units of products in accordance with a specific order. Also, the introduction and operation of the quick changeover system - SMED.
Excess inventory
Excess production inventory includes:
- raw materials purchased but not required in production;
- work in progress, intermediate units;
- an oversupply of finished products that exceeds consumer demand and the quantity of products required by the customer.
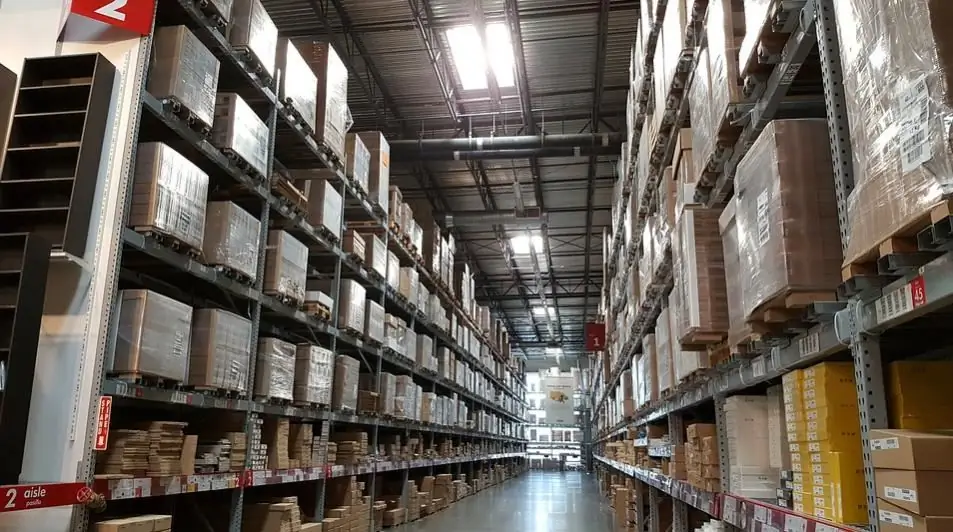
Excess inventory is considered one of the most frustrating types of waste. Excess raw materials and finished products require storage. Also entail the appearance of other production capacity losses, additional funds are used to move raw materials and semi-finished products in the production process.
As a way to improve and get rid of the loss of excess inventory, it is proposed to supply materials, semi-finished products and units of finished products in certain sizes exactly when the production process requires it - the use of the Just-In-Time system.
Transportation
Systemtransportation of materials and products in the production process with improper organization can lead to many negative consequences. They are associated with excessive consumption of transportation capacity, fuel and electricity, the losses are complemented by the irrational use of working time and the possibility of damage to products in the warehouse.
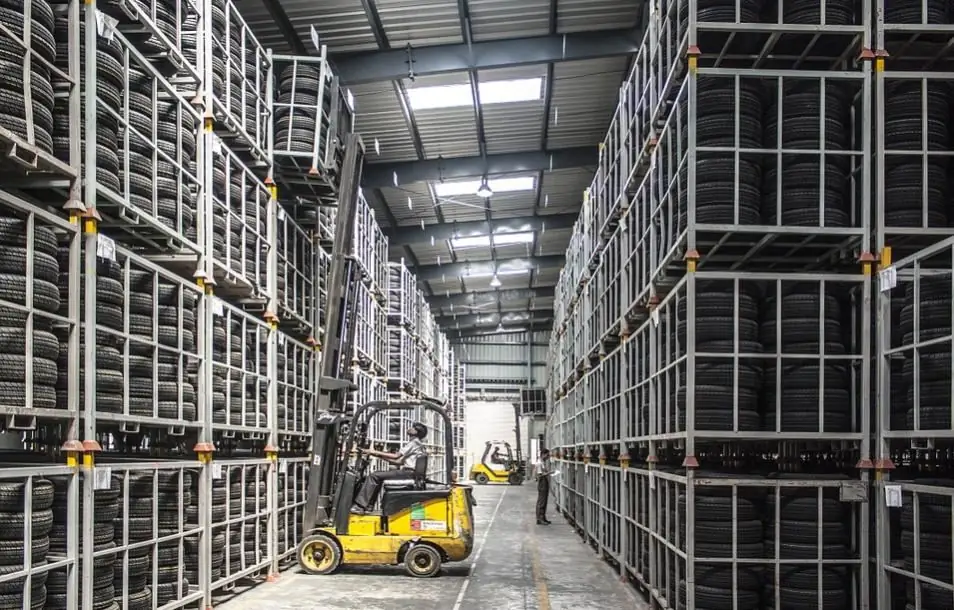
However, provided there is no negative impact on the quality of the elements of the production process, losses due to transportation are taken into account last.
Measures to deal with transportation losses include replanning, following rational trajectories, and optimizing the production process.
Movements
Losses on unnecessary movements are directly related to the actions of workers employed in production. Employee activities that do not benefit the workflow should be minimized according to the principles of lean manufacturing.
Losses due to unnecessary movements occur both in production and in office work. Examples of such irrational movements can be:
- long search for documents or data due to their irrational location;
- freeing the workplace from unnecessary documents, folders, stationery;
- irrational location of office equipment around the perimeter of the office, which forces employees to make unnecessary movements.
To measures aimed at improving the production process andminimization of movement losses should include the improvement of regulations for the implementation of a particular type of activity, training employees in rational work methods, adjusting labor discipline, as well as optimizing the production process or the provision of services.
Waiting
In the course of the production process, waiting means idle production facilities and loss of time for workers. Waiting can be caused by many factors, including insufficient raw materials, equipment malfunctions, process imperfections, etc.
In production, equipment may be idle waiting for adjustment or repair, as well as workers waiting for components and elements necessary to continue work.
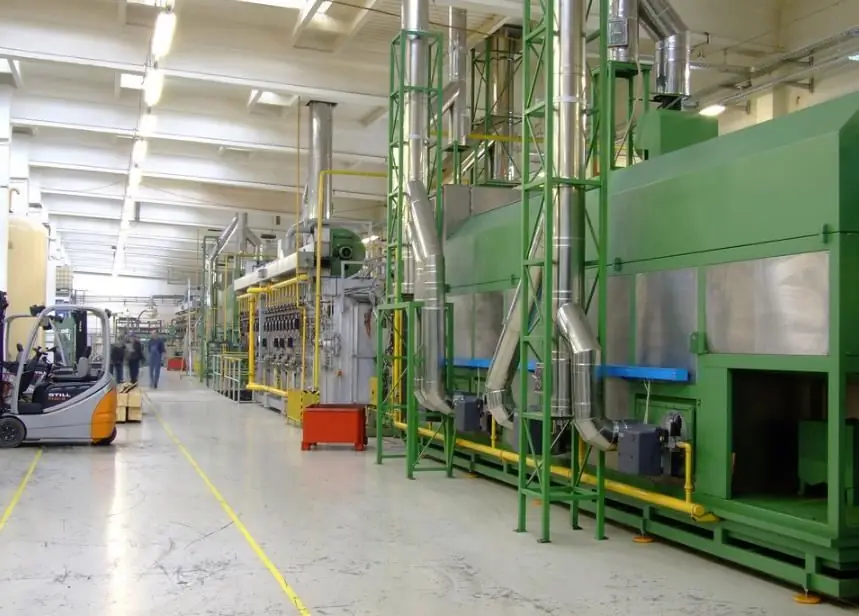
Company employees in office space may experience waiting costs due to colleagues being late for important events and meetings, late submission of data, malfunctions of office equipment.
In order to reduce the loss of waiting and its impact on the work of the enterprise or organization, it is advised to apply a flexible scheduling system and stop the production process in case of lack of orders.
Over-processing
Losses from excessive processing of products among all types of losses are the most difficult to determine. Over-processing refers to operations in a process that consume a significant amount of resources and do not add value to the final product.more. Over-processing causes waste of time and capacity, as well as waste of electricity when it is consumed in excess.
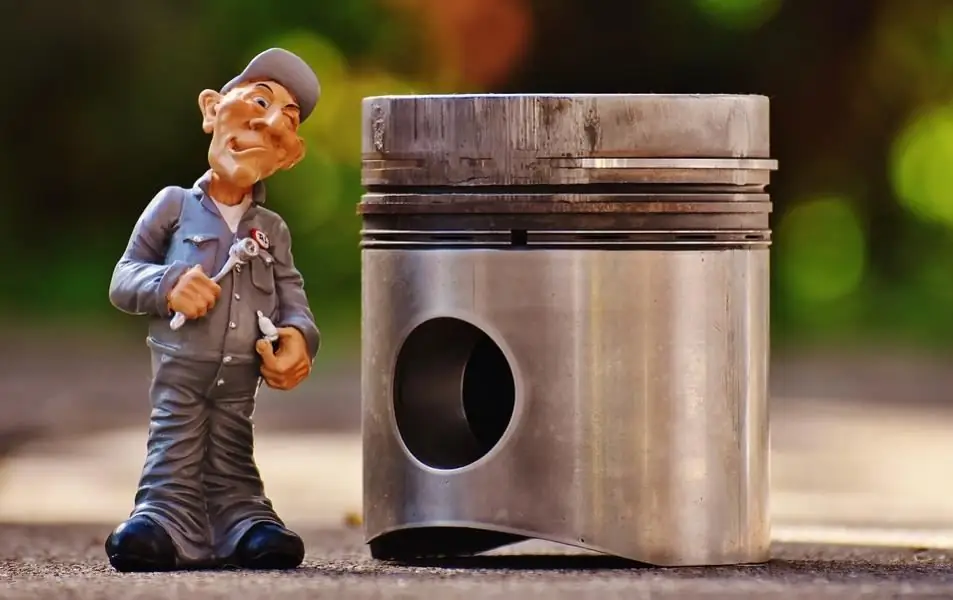
Losses from excessive processing are found both in enterprises that manufacture products, and in organizations and their parts that are not engaged in production activities. In manufacturing, examples of over-processing of products can include a large number of product inspections and the presence of elements of finished products that could be dispensed with (for example, several packaging layers).
In an office environment, over-processing can be expressed as:
- duplicate data in similar documents;
- a large number of approvals of one document;
- numerous checks, reconciliations and inspections.
Excessive processing may result from compliance with industry standards. In this case, minimizing losses is an extremely difficult task. If this type of waste is caused by a misunderstanding of the requirements of the customer for the product, it is quite possible to reduce the impact of excessive processing on the final results of the activity. Options such as outsourcing and purchasing raw materials that do not need to be processed can be considered as ways to improve the situation.
Defects
Defect loss is often a feature of organizations that strive to meet a production plan without fail. Reworking products that do not meet customer requirements due to defects will incur costs.more time and resources. Economic losses are a serious consequence.
Measures to eliminate defects in production can be the optimization of the production process, the elimination of the possibility of defects and the implementation of activities that motivate employees to work without errors.
Unrealized potential of employees
Jeffrey Liker came up with the idea of accounting for another type of waste, presented in the book "Tao of Toyota". Loss of creativity refers to the lack of attention on the part of the company to the ideas and suggestions of employees to improve the work.
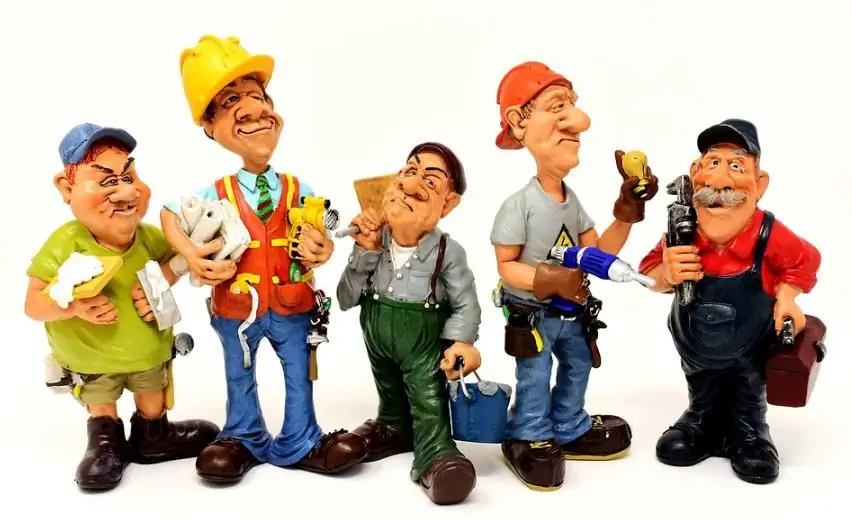
Examples of loss of human potential include:
- execution by a highly qualified employee of work that does not correspond to his abilities and skills;
- negative attitude towards enterprising employees in the organization;
- imperfection or lack of a system through which workers can express their ideas or make suggestions.
Recommended:
Low-waste and waste-free technologies: definition, description, problems and principles
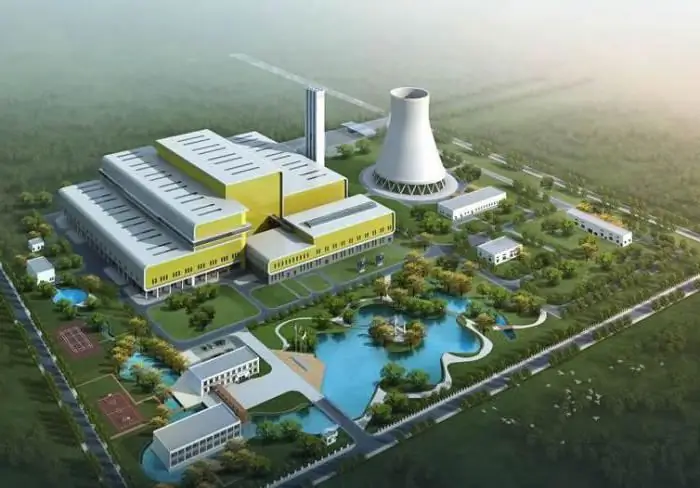
Problems of the harmful effects of industry on the environment have been worrying environmentalists for a long time. Along with modern means of organizing effective methods for the disposal of hazardous waste, options are being developed to minimize the initial damage to the environment
Waste incineration plant: technological process. Waste incineration plants in Moscow and Moscow region
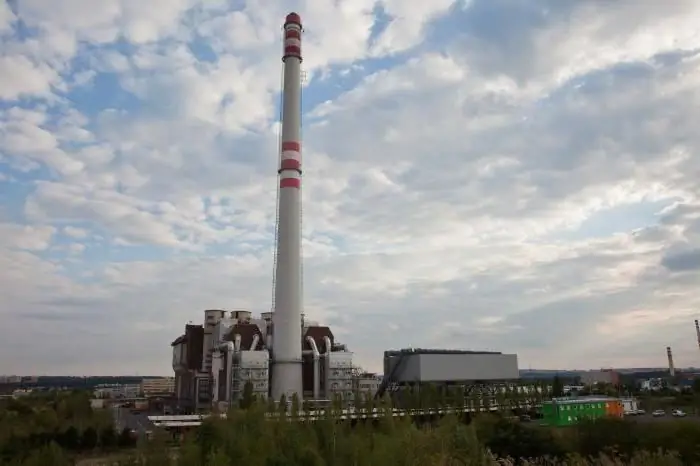
Waste incinerators have long been controversial. At the moment, they are the cheapest and most affordable way to recycle waste, but far from the safest. Every year, 70 tons of garbage appears in Russia, which needs to be removed somewhere. Factories become a way out, but at the same time the Earth's atmosphere is exposed to enormous pollution. What waste incineration plants exist and is it possible to stop the waste epidemic in Russia?
Waste sorting complex: equipment for sorting and processing household waste
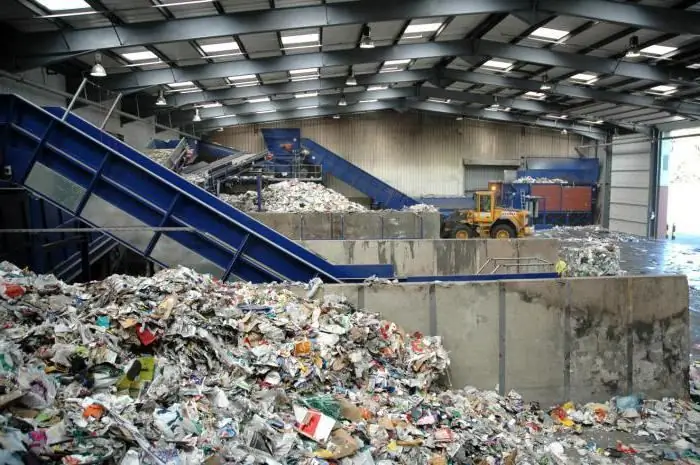
The article is devoted to waste sorting complexes. The features of this equipment, the technological steps performed, etc. are considered
Classification of production and consumption waste. Classification of waste by hazard class
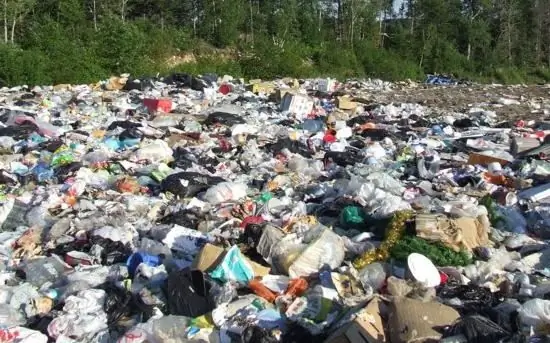
There is no general classification of consumption and production waste. Therefore, for convenience, the basic principles of such a separation are often used, which will be discussed in this article
Lean production and its tools. Lean manufacturing is
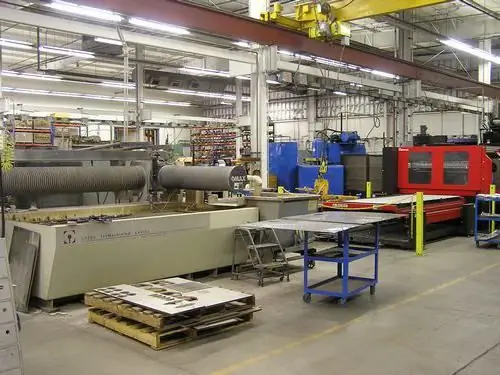
Lean production is a special scheme of company management. The main idea is to constantly strive to eliminate any kind of costs. Lean production is a concept that involves the involvement of each employee in the optimization procedure