2025 Author: Howard Calhoun | [email protected]. Last modified: 2025-01-24 13:10
Lean production is a special scheme of company management. The main idea is to constantly strive to eliminate any kind of costs. Lean manufacturing is a concept that involves the involvement of each employee in the optimization procedure. This scheme is aimed at maximum orientation towards the consumer. Let's take a closer look at what a lean manufacturing system is.
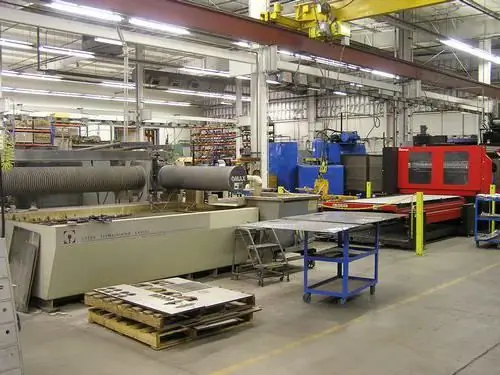
History of occurrence
The introduction of lean manufacturing into industry occurred in the 1950s at the Toyota Corporation. The creator of such a control scheme was Taiichi Ohno. A great contribution to the further development of both theory and practice was made by his colleague Shigeo Shingo, who, among other things, created a method for quick changeover. Subsequently, American specialists investigated the system and conceptualized it under the name lean manufacturing (lean production) - "lean production". At first, the concept was applied primarily in the automotive industry. After a while, the scheme was adapted to the processproduction. Subsequently, lean manufacturing tools began to be used in he althcare, utilities, services, trade, military, government and other industries.
Highlights
Lean production at the enterprise involves the analysis of the value of the product that is produced for the final consumer, at each stage of creation. The main objective of the concept is the formation of a continuous process of cost elimination. In other words, lean manufacturing is the elimination of any activity that consumes resources but does not create any value for the end user. For example, he does not need the finished product or its components to be in stock. Under the traditional system, all costs associated with marriage, rework, storage, and other indirect costs are passed on to the consumer. Lean manufacturing is a scheme in which all company activities are divided into processes and operations that add and do not add value to the product. The main task, therefore, is the systematic reduction of the latter.
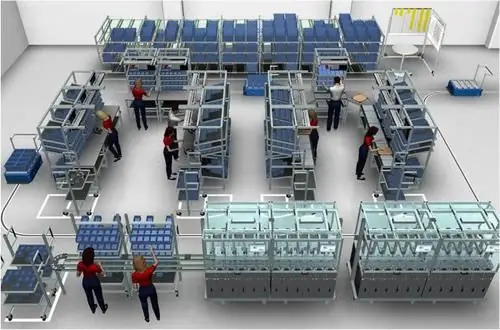
Lean waste
As a synonym for costs, the term muda is used in some cases. This concept means various expenses, garbage, waste and so on. Taiichi Ohno identified seven types of costs. Losses are generated due to:
- wait;
- overproduction;
- shipping;
- extra processing steps;
- unnecessary movements;
- releasing defective goods;
- excess inventory.
The main type of losses Taiichi Ohno considered overproduction. It is a factor due to which other costs arise. Another item has been added to the list above. Jeffrey Liker, a researcher on the Toyota experience, cited the unrealized potential of employees as a waste. The sources of costs are overloaded capacity, employees when carrying out activities with increased intensity, as well as the unevenness of the execution of the operation (for example, an interrupted schedule due to fluctuations in demand).
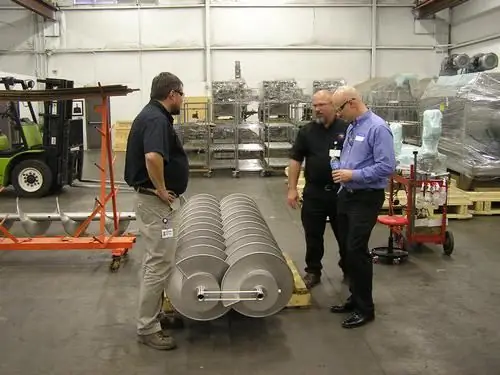
Principles
Lean manufacturing is presented as a process divided into five stages:
- Determining the value of a particular product.
- Establish the value stream of this product.
- Ensuring continuous flow.
- Enabling the consumer to pull the product.
- Striving for excellence.
Other principles on which lean is based include:
- Achieving excellent quality - first sight, zero defects, identifying and solving problems at an early stage.
- Create a long-term relationship with the consumer through the sharing of information, costs and risks.
- Flexibility.
Production system,used in Toyota is based on two main principles: autonomization and "just in time". The latter means that all the necessary elements for assembly arrive on the line exactly at the moment when it is needed, strictly in the quantity determined for a particular process to reduce stock.
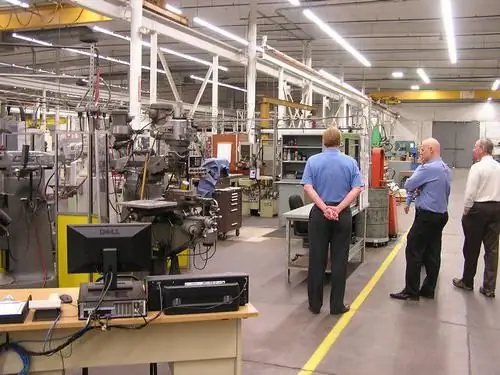
Composition elements
Within the framework of the concept under consideration, various components are distinguished - methods of lean production. Some of them may themselves act as a control scheme. The main elements include the following:
- Single item flow.
- General equipment care.
- 5S system.
- Kaizen.
- Quick changeover.
- Mistake prevention.
Industry Options
Lean he althcare is a concept of reducing the time spent by medical staff not directly related to helping people. Lean logistics is a pull scheme that brings together all the suppliers involved in the value stream. In this system, there is a partial replenishment of reserves in small volumes. The main indicator in this scheme is the logistic total cost. Lean manufacturing tools are used by the Danish Post Office. As part of the concept, a large-scale standardization of the services offered was carried out. The goals of the event were to increase productivity, speed up transfers. "Cards of in-line value formation" were introducedto control and identify services. Also, a system of motivation for employees of the department was developed and subsequently implemented. A special strategy has been formed in construction, focused on increasing the efficiency of the construction process at all stages. Lean manufacturing principles have been adapted to software development. Elements of the considered scheme are also used in city and state administration.
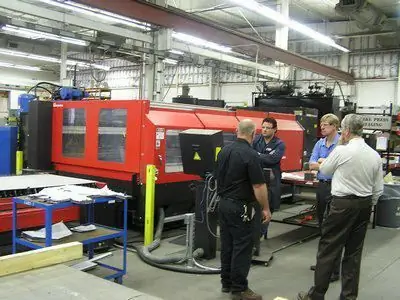
Kaizen
The idea was formulated in 1950 by Dr. Deming. The introduction of this principle has brought great profits to Japanese companies. For this, the specialist was awarded a medal by the emperor. After a while, the Union of Science and Technology of Japan announced a prize to them. Deming for the quality of manufactured goods.
Benefits of Kaizen Philosophy
The merits of this system have been evaluated in every industrial sector, where conditions have been created to ensure the highest efficiency and productivity. Kaizen is considered a Japanese philosophy. It consists in promoting continuous change. The kaizen school of thought insists that constant change is the only path to progress. The main emphasis of the system is on increasing productivity by eliminating unnecessary and hard work. The definition itself was created by combining two words: "kai" - "change" ("transform"), and "zen" - "in the direction of the better." The advantages of the system quite clearly reflect the success of the Japanese economy. This is recognized not only by the Japanese themselves, but also by expertspeace.
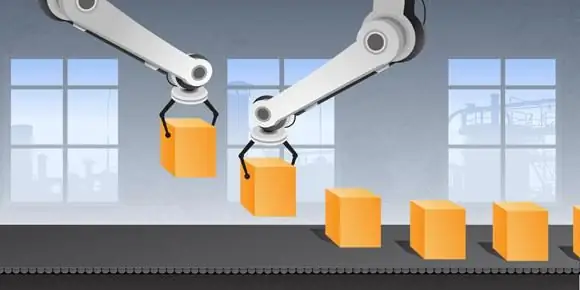
Kaizen Concept Goals
There are five main directions in which the development of production is carried out. These include:
- Waste reduction.
- Immediate troubleshooting.
- Optimal use.
- Teamwork.
- Top quality.
It should be said that most of the principles are based on common sense. The main components of the system are improving the quality of goods, involving each employee in the process, readiness for interaction and change. All these activities do not require complex mathematical calculations or the search for scientific approaches.
Waste reduction
The principles of kaizen philosophy are aimed at significantly reducing losses at each stage (operation, process). One of the main advantages of the scheme is that it includes every employee. This, in turn, involves the development and subsequent implementation of proposals for improvement at each level of management. Such work contributes to minimizing the loss of resources.
Immediate troubleshooting
Each employee, in accordance with the concept of kaizen, must counteract problems. This behavior contributes to the rapid resolution of issues. With immediate troubleshooting, the lead time does not increase. Immediate resolution of problems allows you to direct activities in an effective direction.
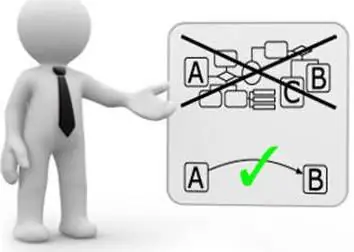
Optimal use
Resources are released when problems are solved quickly. They can be used to improve and achieve other goals. Together, these measures make it possible to establish a continuous process of efficient production.
Teamwork
Involving all employees in solving problems allows you to find a way out faster. Successfully overcoming difficulties strengthens the spirit and self-esteem of company employees. Teamwork eliminates conflict situations, promotes the formation of trusting relationships between higher and lower employees.
Best quality
Fast and efficient problem solving contributes to teamwork and the creation of a large amount of resources. This, in turn, will improve the quality of products. All this will allow the company to reach a new level of capacity.
Recommended:
Motor oil production: characteristics, technology and manufacturing process
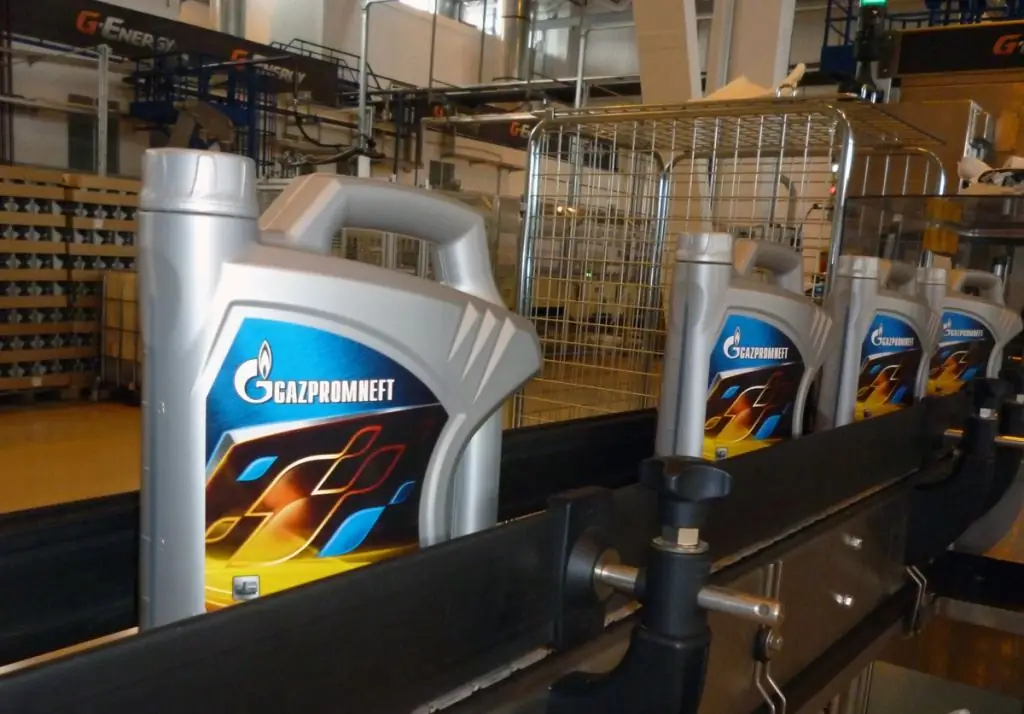
The production of motor oil, like any other, is not complete without raw materials - the substance from which the final product is obtained. Mineral oil is made from petroleum. But before it gets to the lubricants plant, it needs to go through a series of cleanings at oil refineries
Automatic lathe and its characteristics. Automatic lathe multi-spindle longitudinal turning with CNC. Manufacturing and processing of parts on automatic lathes
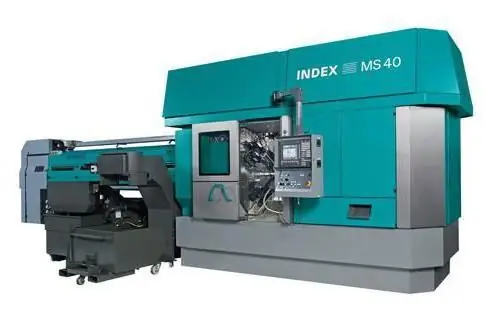
Automatic lathe is a modern equipment used mainly in mass production of parts. There are many varieties of such machines. One of the most popular types are longitudinal turning lathes
Styrofoam production business plan: step-by-step opening steps, manufacturing technology, calculation of income and expenses
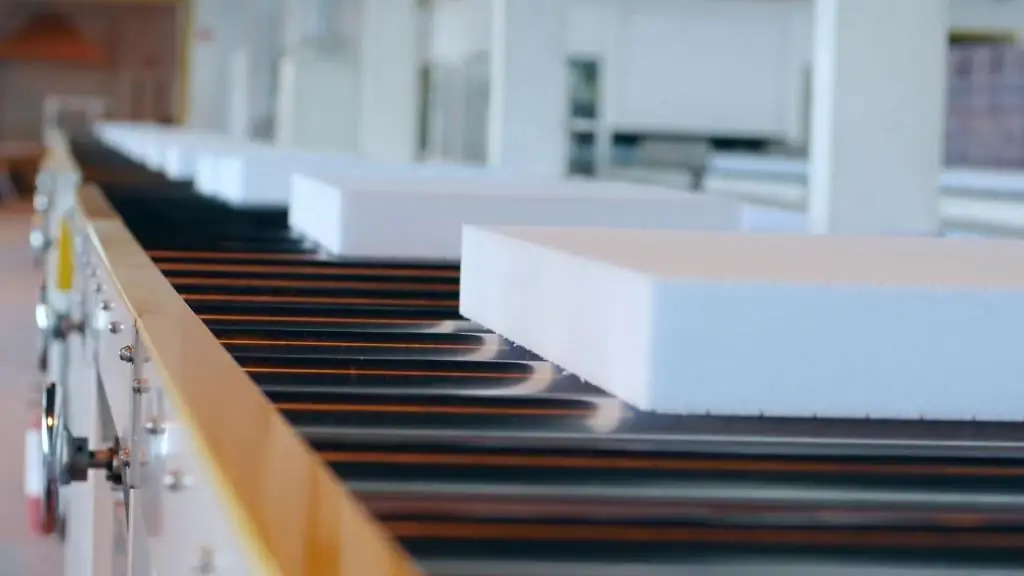
Polyfoam can be attributed to one of the most widely used building materials. The demand for it is quite high, as there is a development of sales markets, which, with a competent marketing approach, can provide stable profits for a long period of time. In this article, we will consider in detail the business plan for the production of foam plastic
Types of waste in lean manufacturing
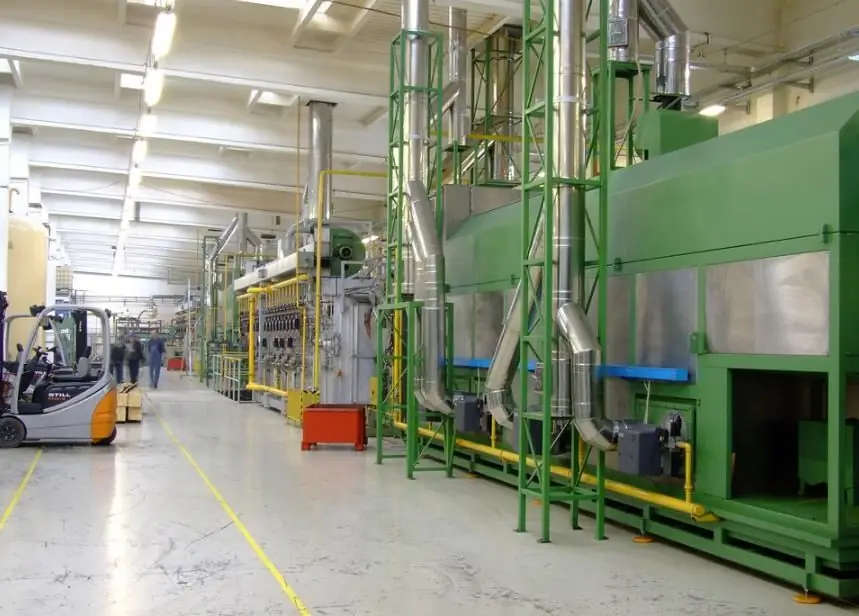
Lean Manufacturing, also known as Lean Manufacturing, or LEAN is one of the best solutions for organizations looking to increase productivity levels and keep costs as low as possible. Waste in Lean production interferes with the achievement of the main objectives of the Lean system. Knowing the types of losses, understanding their sources and ways to eliminate them allows manufacturers to bring the production organization system closer to ideal conditions
Carpet production: technology and manufacturing features
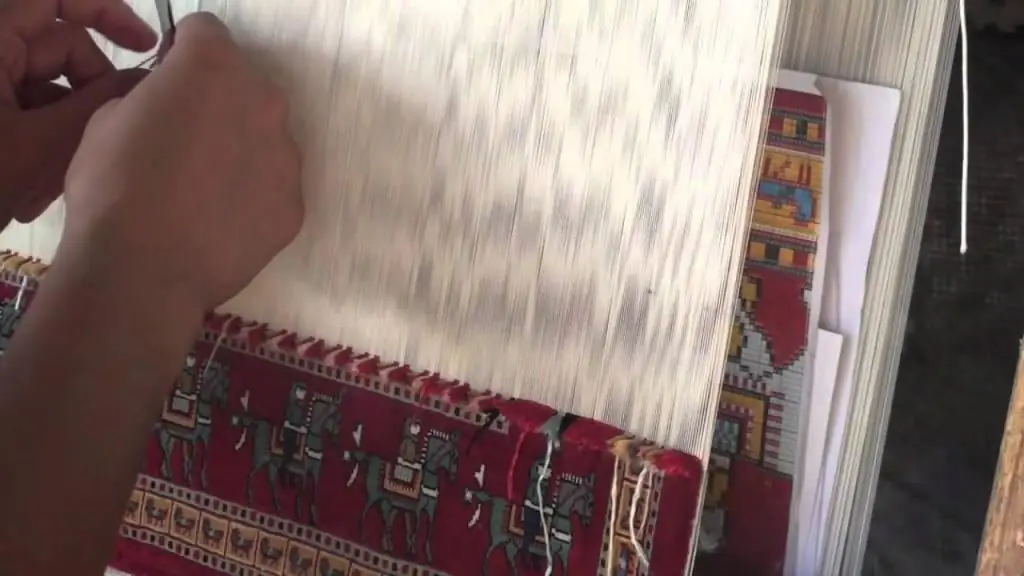
Any carpet production begins with the selection of raw materials. And if earlier the choice of materials was limited to wool and silk, today you can find a woven fabric from both natural fibers and their synthetic counterparts