2025 Author: Howard Calhoun | [email protected]. Last modified: 2025-01-24 13:10
To ensure the durability of metal products, anti-corrosion treatment of metal structures is used. This procedure is aimed at protecting structures from the effects of aggressive environments and precipitation. Thanks to the coating, the metal surface retains its original properties, including aesthetic ones.
The essence of the process
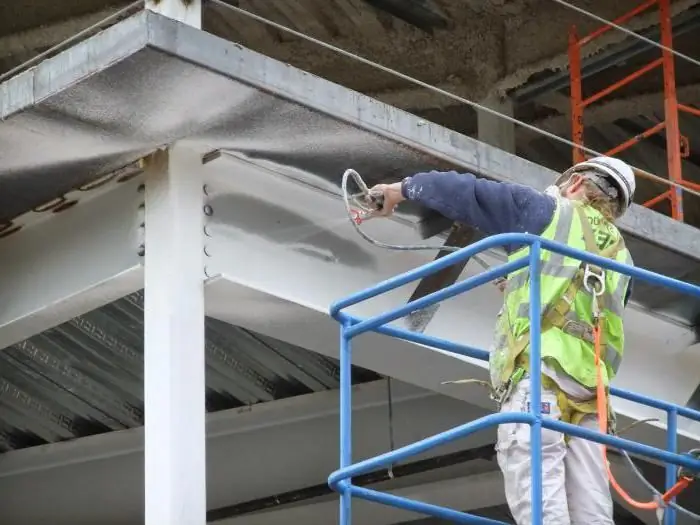
Corrosion is a process of electrochemical or chemical interaction of a metal with the environment, due to which the metal is oxidized and destroyed. Experts say that the damage from corrosion in the industrial sector reaches 4% of the gross national product of any country. Corrosion occurs due to the impact of oxygen, water on the metal, so timely anti-corrosion treatment of metal structures is required. The technology involves surface treatment with a thin layer of metal, metal alloys or non-metallic compounds.
Processing Features
Due to the fact that the metal begins to break down under the influence of an aggressive environment, the strength and physicalchemical properties of metal products. And this affects the decrease in their functionality and durability. Corrosion contributes to the failure of equipment, vehicles. That is why the anti-corrosion treatment of metal structures plays an important role, the technology of which is constantly being modernized and improved.
Outside Processing
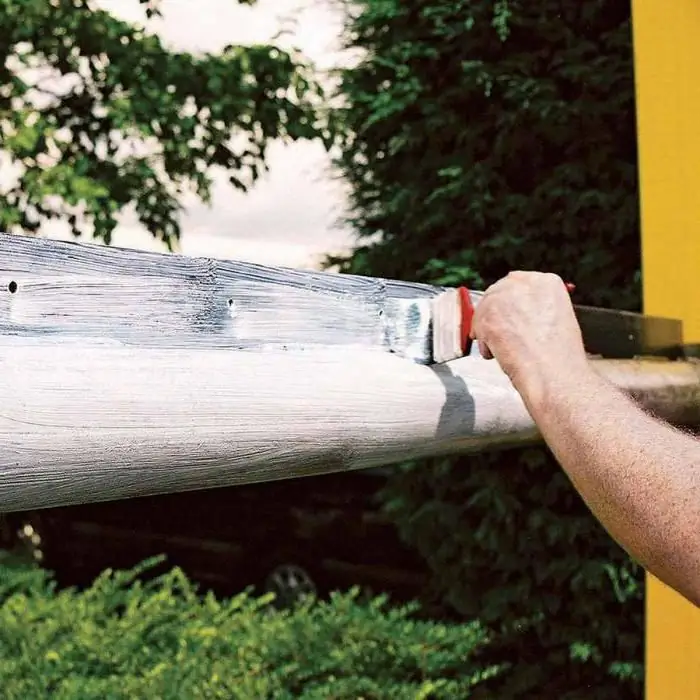
The outer surfaces of metal products are most exposed to aggressive factors. To protect them, constructive methods of protection are used. They are used in the design and manufacture of products even before the active operation of metal elements begins. Structural methods involve choosing a material that can withstand the environment. For these purposes, steels with a strong film, high-polymer materials, ceramics, and glass are well suited. In addition, anti-corrosion treatment of metal structures is accompanied by methods of rational operation of products:
- eliminating gaps, cracks, gaps that may remain in the product and through which moisture can get inside;
- eliminate areas where moisture can stagnate;
- surface protection from water;
- introducing inhibitors into an aggressive environment.
Passive Defense
When applying passive methods of protection, the metal surface is treated with some kind of coating, the task of which is to prevent contact between metal and oxygen or metal and moisture. To this endanti-corrosion treatment of metal structures is carried out. Materials for this are used modern, with improved performance properties. These coatings perform several functions:
- barrier;
- tread;
- transformative;
- passive.
Barrier protection involves the mechanical isolation of the metal surface. Most often, such tools are used for processing ferrous metals. But if the integrity of the protective film is broken, under-film corrosion can occur under it.
What materials?
When anti-corrosion treatment of metal structures is carried out, the means are selected very carefully. To passivate surfaces, paints and varnishes are used that contain phosphate acid or chromate pigments, which slow down corrosion processes. When applying passivating primers, a sprayer is used. Depending on how many components are in these compositions, they can be used for processing both ferrous and non-ferrous metals.
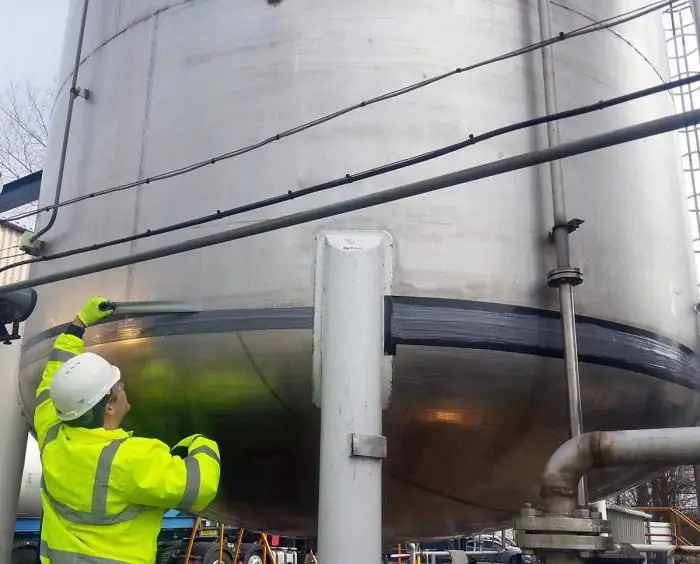
Passive treatment can also act as a protector, but in this case, paints are used that contain more than 86% metal dust from a high-recovery element compared to the treated surface. In most cases, when anti-corrosion treatment of metal structures is used, paints are selected with a filling of highly dispersed zinc powder. This technology is called cold galvanizing, which increases the termmetal surface service and abrasion resistance.
Paints and enamels
Protection of metal structures is based on three types of means:
- Paints that are easy and simple to apply and are available in a variety of colors. With the help of paints, metal structures of large sizes and any configurations can be processed.
- Plastic anti-corrosion coatings based on fluoroplast, nylon, PVC. These compositions are characterized by high water, acid and alkali resistance.
- Rubber-based coatings are used when anti-corrosion treatment of tanks and metal structures is carried out from the inside.
Active protection methods
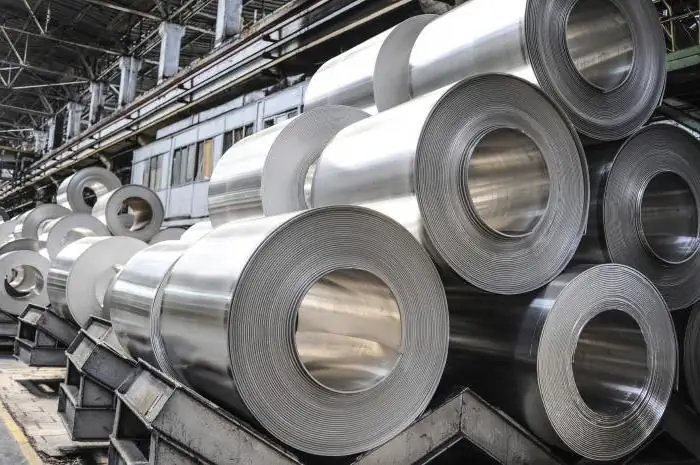
Metal requires special protection, for which active methods are used. The resistance of metal products to external factors is achieved:
- Hot-dip galvanizing of parts: according to this technology, the part is first degreased, then sandblasted or acid etched, as a result of which it is covered with a thin zinc layer. The chemical reaction causes a protective film to form on the metal surface. It shields the metal and protects it from moisture. Most often, hot-dip galvanizing is used for processing large objects - tanks, cisterns.
- Electrochemical zinc plating: this method involves the diffusion extraction of zinc ions from a slightly acidic solution during electrolysis. Galvanic processing of metal structures is applied to the processing of hardware, medium-sized parts.
- Thermal Diffusion Zinc Coating: In this technology, zinc atoms penetrate the iron surface under high temperature. The coating is durable and wear-resistant, and the original part is completely repeated, even if the surface is notched or embossed.
Anti-corrosion treatment of metal structures can be carried out in addition to electrochemical protection.
Modern methods
Most often paint and varnish coatings are used to protect a metal surface from corrosion, as they are more affordable and easy to use. But such a layer needs to be updated every 5-7 years, which is laborious and costly. And using galvanic and electrochemical methods is too expensive, although rust can be forgotten for about 50 years.
That is why more and more often anti-corrosion treatment of metal structures is carried out using "liquid rubber". This is a two-component material that is able to reliably and for a long time protect the surface from external influences. The use of an elastomer allows the application of a seamless membrane layer, which is applied with a spray gun. Rubber quickly hardens on the surface, and neither streaks nor bumps form. Moreover, you can work even with a wet metal surface. Manufacturers of such products say that such a coating can last about 20 years without losing its original properties.
Surface preparation
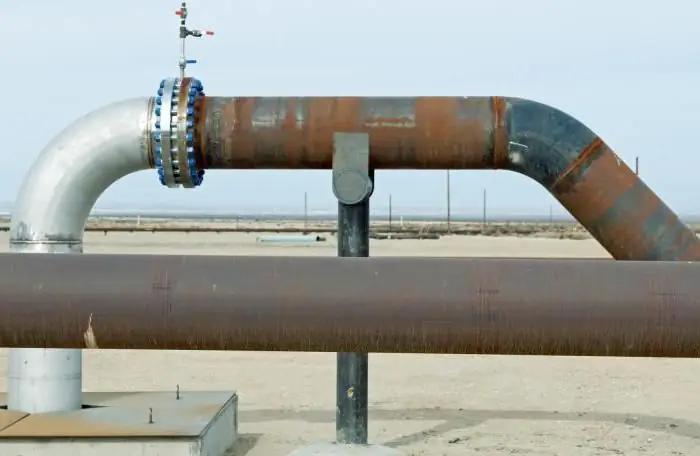
Reliable rust protection of metal can only be achieved if the surface has been properly prepared. The equipment for anti-corrosion treatment of metal structures itself is not complex, so its use will not cause any problems. Surface preparation is carried out mechanically or chemically. Chemical methods are more popular, since mechanical methods cannot provide the proper level of protective equipment. But you need to choose the technology in accordance with the selected paintwork and the conditions for their further operation.
Phosphating and chromating
Metal surface preparation is performed depending on the type of metal. Surface preparation of ferrous metals is done by phosphating, while non-ferrous metals are treated with both methods. In general, the chemical preparation of a metal surface consists of several stages:
- surface degreasing;
- flushing with drinking water;
- applying a conversion layer;
- re-rinsing with drinking water;
- rinsing with demineralized water;
- passivation.
Chemical treatment of metal is performed by spraying (jetting at low pressure), immersion, steam jet and water jet methods. The first two methods involve the use of special units that prepare the surface. The method is selected according to the production program, configuration andproduct dimensions and many other factors.
Pipeline processing
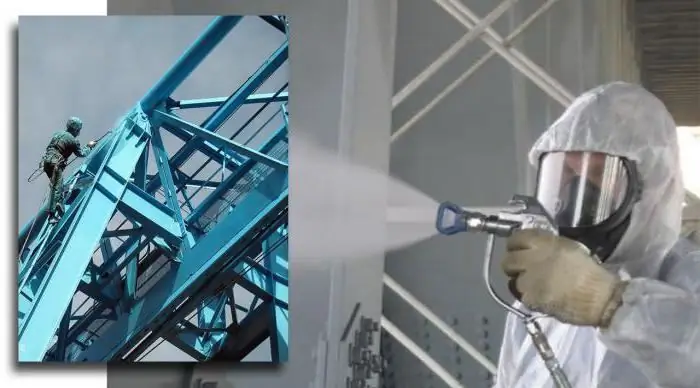
Anti-corrosion treatment of metal structures and pipelines is carried out in accordance with the requirements of state standards. Processing can be carried out both for a functioning pipeline and during its reconstruction or repair. Pipelines can be protected by active and passive methods - it is selected in accordance with the laying method. For pipes laid above the ground, materials resistant to the environment are used. With the active method, the protective surface is created with the help of substances that can provide electrochemical protection to the coating. Protection of pipelines is carried out in several stages:
- First, the surface of the pipe is freed from insulating coatings, rust, scale and all contaminants.
- Anti-corrosion materials are applied to the cleaned surface, while work can be carried out at a temperature of +5 degrees and at a humidity of not more than 80%.
After processing, you need to carefully inspect the pipeline to identify defects, if any, on the surface. Special devices determine the quality of the connection between the surface and the coating, the quality of the coating itself and the thickness of the dry film of the coating.
Active and passive protection
Anti-corrosion treatment of metal structures, the principle of which depends on the materials used, can be performed with active and passive surface protection. Both variantsare aimed at protecting metal pipes from harmful environmental factors. And if the water supply is located at a great depth, there is a need to protect the metal from contact with the ground. Thanks to the protective layers of paint, varnish, enamel, a continuous and very durable barrier is created that protects the surface from the negative effects of the external environment.
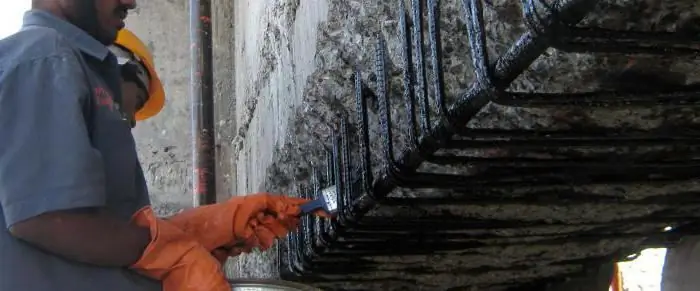
Pipeline treatment is often done with powder based plastic materials. They are applied to the pipe, which is preheated to a certain temperature.
Thus, anti-corrosion treatment is an opportunity to prevent rust on any metal surfaces. A variety of processing options and methods ensure that anything can be protected - from pipes and a car to a small metal part.
Recommended:
Metal structures plant, Chelyabinsk: history of creation, address, working conditions and manufactured products
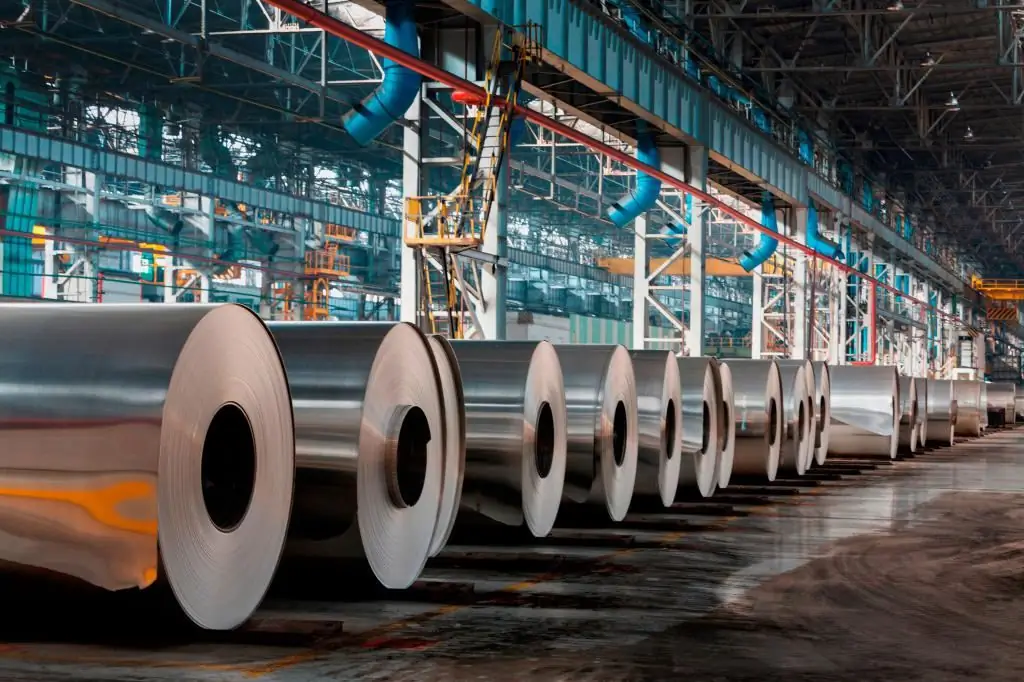
The Chelyabinsk steel structure plant is one of the industry leaders in the production of structures for industrial and civil construction, as well as bridges. The range and quality of products made the company in demand in Russia and abroad
Manufacture and installation of metal structures. Production features
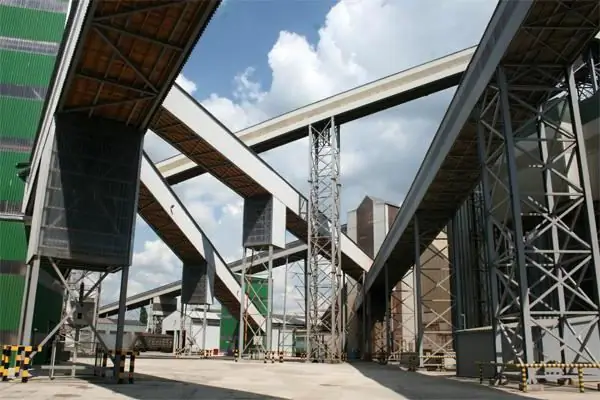
Prefabricated buildings are the best option for many businesses, which is why most consumers today prefer steel structures. Production, manufacturing and installation will be carried out by special construction organizations that guarantee high-quality construction of any type of object
Anti-aircraft missile system. Anti-aircraft missile system "Igla". Anti-aircraft missile system "Osa"
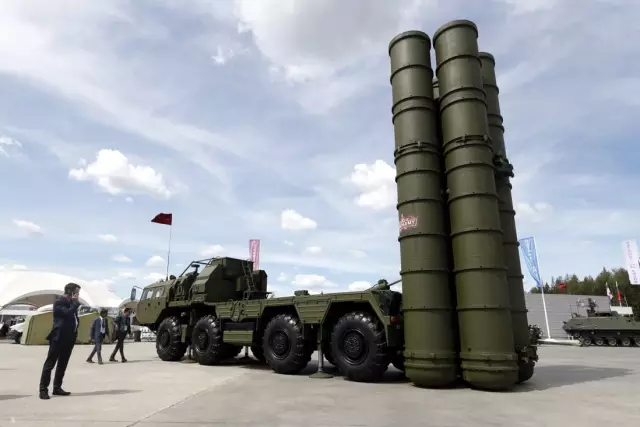
The need to create specialized anti-aircraft missile systems was ripe during the Second World War, but scientists and gunsmiths from different countries began to approach the issue in detail only in the 50s. The fact is that until then there simply were no means of controlling interceptor missiles
Steel annealing as a type of heat treatment. Metal Technology
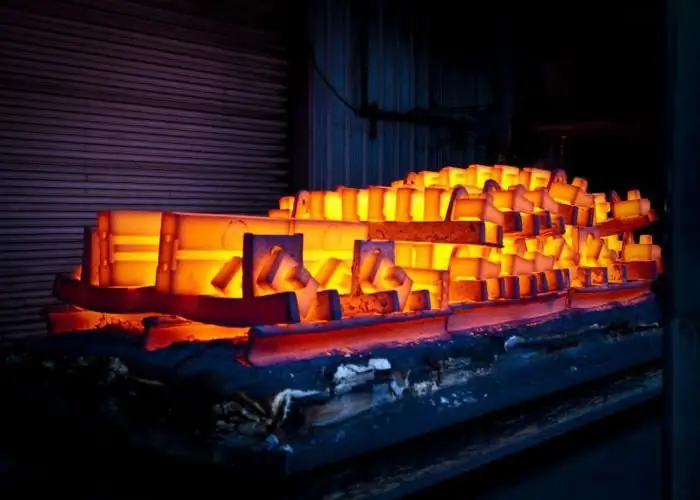
Creating new materials and controlling their properties is the art of metal technology. One of its tools is heat treatment. This knowledge allows you to change the characteristics, and, accordingly, the scope of the use of alloys. Steel annealing is a widely used option for eliminating manufacturing defects in products, increasing their strength and reliability
Welding in a shielding gas environment: work technology, process description, execution technique, necessary materials and tools, step-by-step work instructions and expert advice
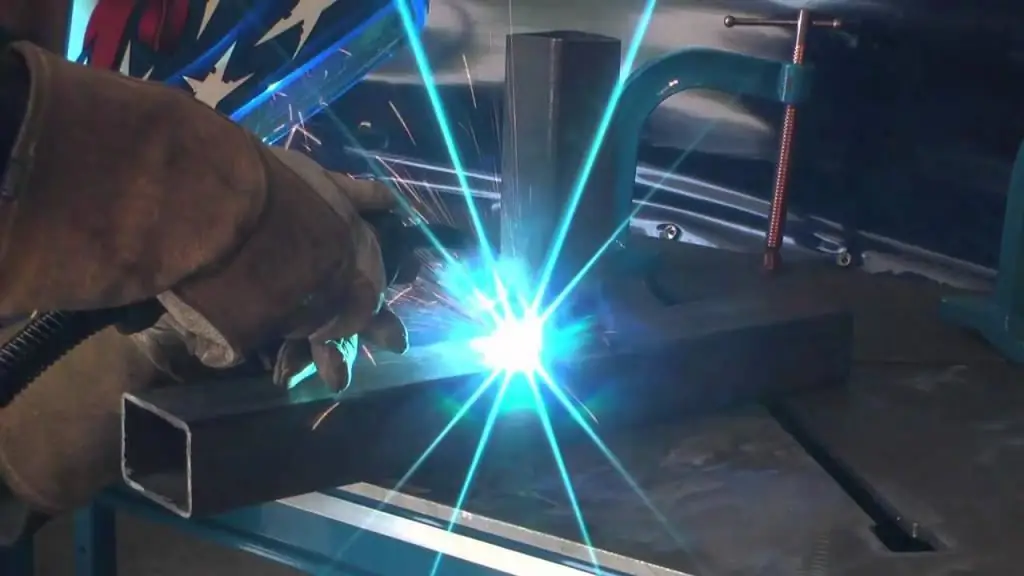
Welding technologies are used in various branches of human activity. Versatility has made welding in a protective gas environment an integral element of any production. This variety makes it easy to connect metals with a thickness of 1 mm to several centimeters in any position in space. Welding in a protective environment is gradually replacing traditional electrode welding