2025 Author: Howard Calhoun | [email protected]. Last modified: 2025-01-24 13:10
Creating new materials and controlling their properties is the art of metal technology. One of its tools is heat treatment. These processes make it possible to change the characteristics and, accordingly, the areas of use of alloys. Steel annealing is a widely used option for eliminating manufacturing defects in products, increasing their strength and reliability.
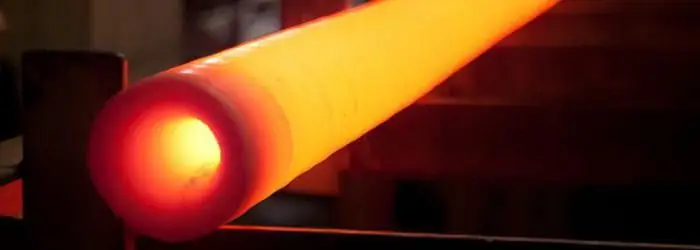
Process tasks and its varieties
Annealing operations are performed with the aim of:
- optimization of intracrystalline structure, ordering of alloying elements;
- minimizing internal distortion and stress due to rapid process temperature fluctuations;
- increasing the susceptibility of objects to subsequent cutting.
The classic operation is called “full annealing”, however, there are a number of its varieties, depending on the specified properties and the characteristics of the tasks: incomplete, low, diffusion (homogenization),isothermal, recrystallization, normalization. All of them are similar in principle, however, the modes of heat treatment of steels differ significantly.
Heat treatment based on chart
All transformations in ferrous metallurgy, which are based on the game of temperatures, clearly correspond to the diagram of iron-carbon alloys. It is a visual aid for determining the microstructure of carbon steels or cast irons, as well as the transformation points of structures and their features under the influence of heating or cooling.
Metal technology regulates all types of annealing of carbon steels with this schedule. For incomplete, low, and also for recrystallization, the “starting” temperature values are the PSK line, namely its critical point Ac1. Full annealing and normalization of steel are thermally oriented to the GSE diagram line, its critical points Ac3 and Acm. The diagram also clearly establishes the connection of a certain heat treatment method with the type of material in terms of carbon content and the corresponding possibility of its implementation for a particular alloy.
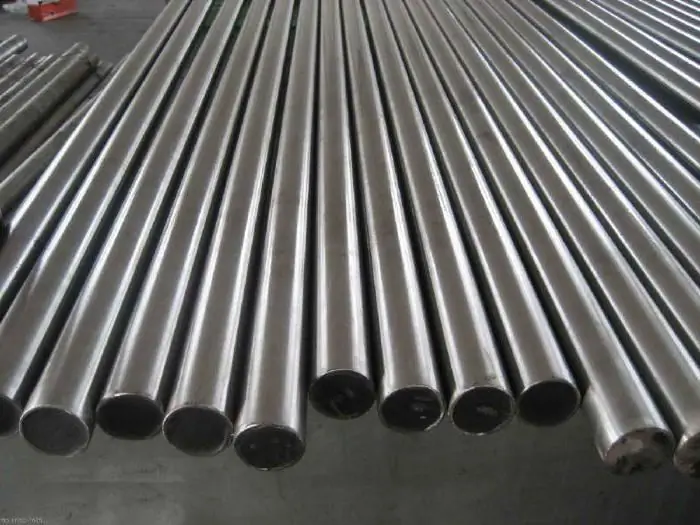
Full annealing
Objects: castings and forgings from a hypoeutectoid alloy, while the steel composition should fill carbon in an amount of up to 0.8%.
Target:
- maximum change in the microstructure obtained by casting and hot pressure, bringing the inhomogeneous coarse-grained ferrite-pearlite composition into a homogeneous fine-grained;
- reducing hardness and increasing ductility for further processingcutting.
Technology. The annealing temperature of steel is 30-50˚С higher than the critical point Ac3. When the metal reaches the specified thermal characteristics, they are maintained at this level for some time, which allows to complete all the necessary transformations. Large pearlitic and ferritic grains completely transform into austenite. The next stage is slow cooling together with a furnace, during which ferrite and pearlite are again separated from austenite, which has a fine grain and a uniform structure.
Complete annealing of steel allows to eliminate the most complex internal defects, however, it is very long and energy intensive.
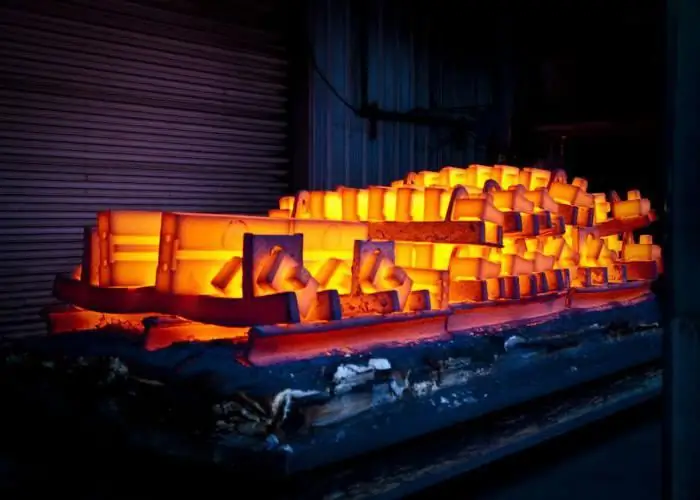
Incomplete annealing
Objects: hypoeutectoid steels without serious internal inhomogeneities.
Purpose: Grinding and softening pearlite grains, without changing the ferritic base.
Technology. Heating the metal to temperatures falling within the interval between the critical points Ac1 and Ac3. Exposure of blanks in the furnace with stable characteristics contributes to the completion of the necessary processes. Cooling is done slowly, together with the oven. At the output, the same pearlite-ferrite fine-grained structure is obtained. With such a thermal effect, pearlite turns into fine-grained, while ferrite remains unchanged crystalline, and can only change structurally, also grinding.
Incomplete annealing of steel allows you to balance the internal state and properties of simple objects, it is less energy intensive.
Low annealing(recrystallization)
Objects: all types of rolled carbon steel, alloy steel with a carbon content within 0.65% (for example, ball bearings), parts and blanks made of non-ferrous metals that do not contain serious internal defects, but need low-energy correction.
Target:
- removal of internal stresses and hardening due to the influence of both cold and hot deformation;
- eliminate the negative effects of uneven cooling of welded structures, increase the plasticity and strength of the seams;
- making the microstructure of non-ferrous metallurgy products uniform;
- spheroidization of lamellar pearlite - giving it a granular shape.
Technology.
Parts are heated 50-100˚C below the critical point Ac1. Under the influence of such influences, minor internal changes are eliminated. The whole technological process takes about 1-1.5 hours. Approximate temperature ranges for some materials:
- Carbon steel and copper alloys - 600-700˚C.
- Nickel alloys - 800-1200˚C.
- Aluminum alloys - 300-450˚C.
Cooling is done in air. For martensitic and bainitic steels, metal technology provides a different name for this process - high tempering. It is a simple and affordable way to improve the properties of parts and structures.
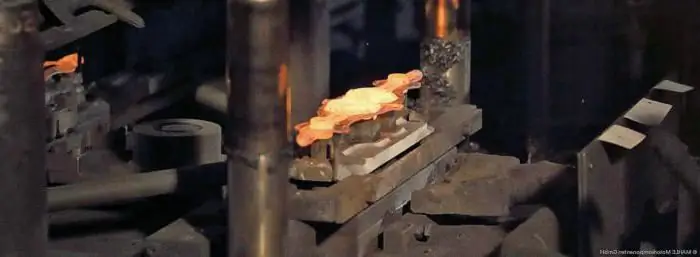
Homogenization (diffusion annealing)
Objects: large casting products, especially castingsalloy steel.
Purpose: uniform distribution of atoms of alloying elements over the crystal lattices and the entire volume of the ingot as a result of high-temperature diffusion; softening the structure of the workpiece, reducing its hardness before performing subsequent technological operations.
Technology. The material is heated to high temperatures of 1000-1200˚С. Stable thermal characteristics must be maintained for a long time - about 10-15 hours, depending on the size and complexity of the cast structure. Upon completion of all stages of high-temperature transformations, slow cooling follows.
A labor-intensive but highly effective process for leveling the microstructure of large structures.
Isothermal annealing
Objects: carbon steel sheets, alloy and high alloy products.
Goal: Improving the microstructure, removing internal defects with less time.
Technology. The metal is initially heated to full annealing temperatures and the time required for the transformation of all existing structures into austenite is maintained. Then slowly cool by immersion in hot s alt. Upon reaching the heat at 50-100˚C below the Ac1 point, it is placed in a furnace in order to maintain it at this level for the time necessary for the complete transformation of austenite into pearlite and cementite. The final cooling takes place in air.
The method allows you to achieve the required properties of alloy steel blanks, while saving time, in comparison with the fullannealing.
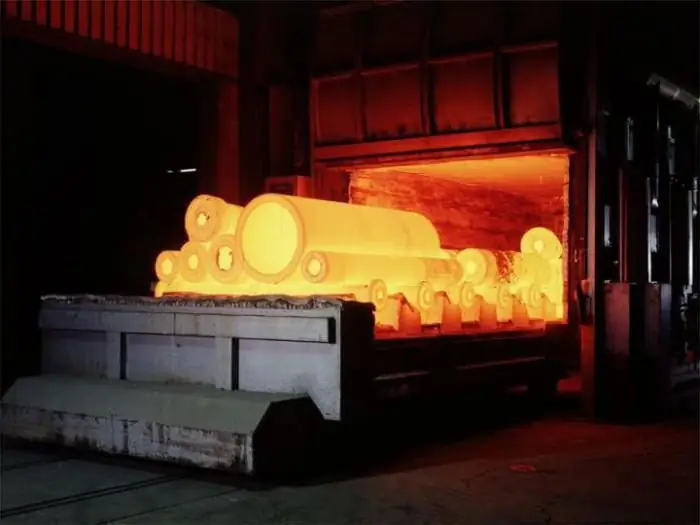
Normalization
Objects: castings, forgings and parts made of low carbon, medium carbon and low alloy steel.
Purpose: to streamline the internal state, give the desired hardness and strength, improve the internal state before the subsequent stages of heat treatment and cutting.
Technology. The steel is heated to temperatures that lie slightly above the GSE line and its critical points, held and cooled in air. Thus, the speed of completion of processes increases. However, using this procedure, it is possible to achieve a rational calm structure only when the composition of the steel is determined by carbon in an amount of not more than 0.4%. With an increase in the amount of carbon, an increase in hardness takes place. The same steel after normalization has a greater hardness along with evenly spaced fine grains. The technique allows to significantly increase the resistance of alloys to destruction and the ductility of cutting.
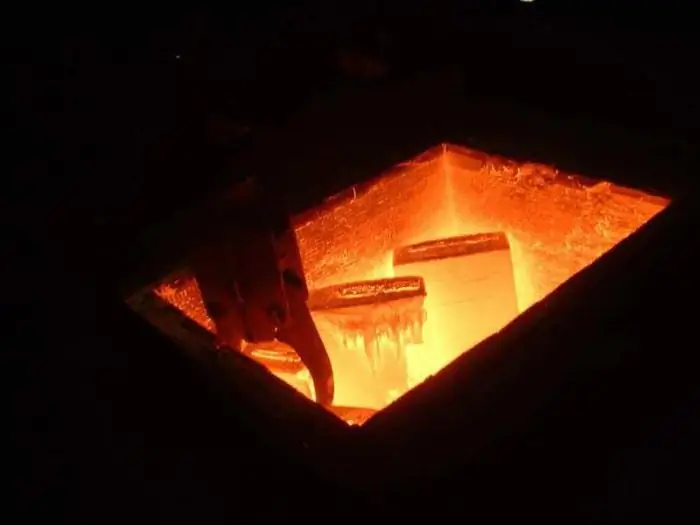
Possible annealing defects
During the performance of heat treatment operations, it is necessary to adhere to the specified modes of temperature heating and cooling. In case of violation of the requirements, various defects may occur.
- Oxidation of the surface layer and scale formation. During the operation, the hot metal reacts with atmospheric oxygen, which leads to the formation of scale on the surface of the workpiece. To be cleaned mechanically or withspecial chemicals.
- Carbon burn. It also occurs as a result of the influence of oxygen on hot metal. A decrease in the amount of carbon in the surface layer leads to a decrease in its mechanical and technological properties. In order to prevent these processes, steel annealing must be carried out in parallel with the introduction of protective gases into the furnace, the main task of which is to prevent the interaction of the alloy with oxygen.
- Overheating. It is a consequence of prolonged exposure in an oven at high temperature. It results in excessive grain growth, the acquisition of an inhomogeneous coarse-grained structure, and an increase in brittleness. To be corrected by another full annealing step.
- Burned out. Occurs as a result of exceeding the permissible values of heating and exposure, leads to the destruction of bonds between some grains, completely spoils the entire structure of the metal and is not subject to correction.
To prevent failures, it is important to carry out heat treatment tasks accurately, have professional skills and strictly control the process.
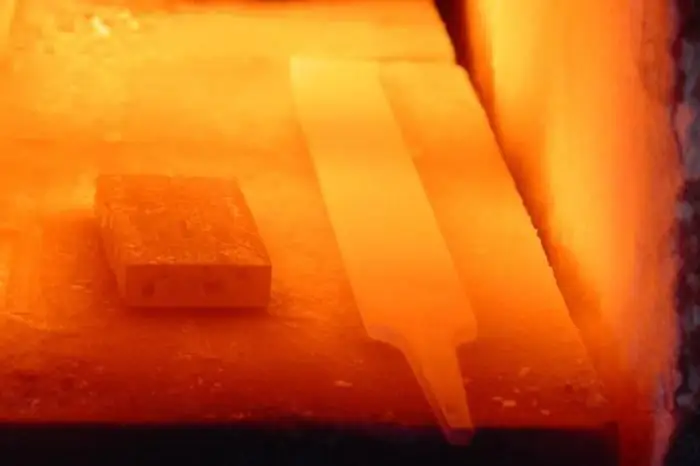
Steel annealing is a highly effective technology for bringing the microstructure of parts of any complexity and composition to the optimal internal structure and condition, which is required for subsequent stages of thermal influences, cutting and putting the structure into operation.
Recommended:
Food stainless steel: GOST. How to identify food grade stainless steel? What is the difference between food stainless steel and technical stainless steel?

The article talks about grades of food grade stainless steel. Read how to distinguish food stainless steel from technical
Anti-corrosion treatment of metal structures: materials and technology
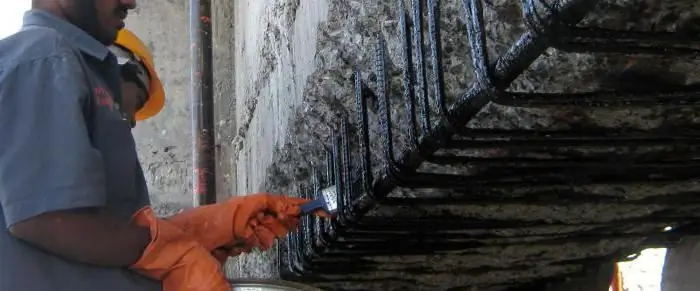
Anti-corrosion treatment of metal structures is aimed at protecting surfaces from the negative effects of environmental factors
Heat treatment of steel is an important process in the production of metals
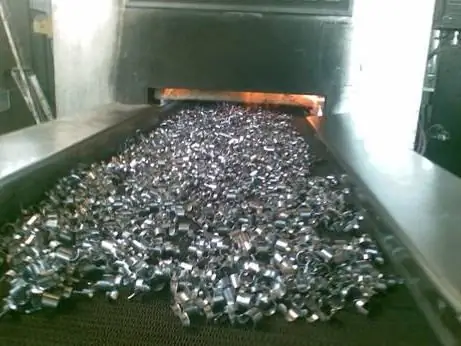
Heat treatment of steel gives any steel product the desired properties. This process is an important step in the production of iron alloy
Heat treatment of alloys. Types of heat treatment
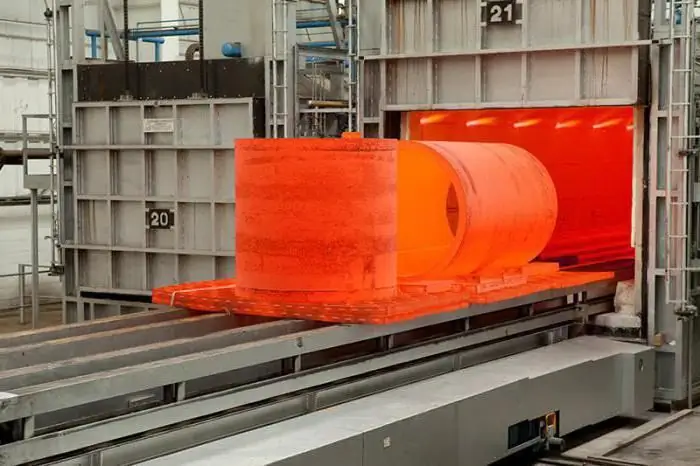
Heat treatment of alloys is an integral part of the production process of ferrous and non-ferrous metallurgy. As a result of this procedure, metals are able to change their characteristics to the required values. In this article, we will consider the main types of heat treatment used in modern industry
Steel 95x18: characteristics, reviews, heat treatment and knife making

What kind of steel are quality knives made of? How to follow them correctly? What properties do these products have? Read about this (and more) in our article