2025 Author: Howard Calhoun | [email protected]. Last modified: 2025-01-24 13:10
Plywood is one of the cheapest and most practical building materials. Despite the multi-layer structure, it is easy to install and can be processed at home without special equipment. Standard plywood production involves the use of wood lamellas, which, if properly processed, can be used as a finishing material that is resistant to a wide variety of threats.
General manufacturing technology
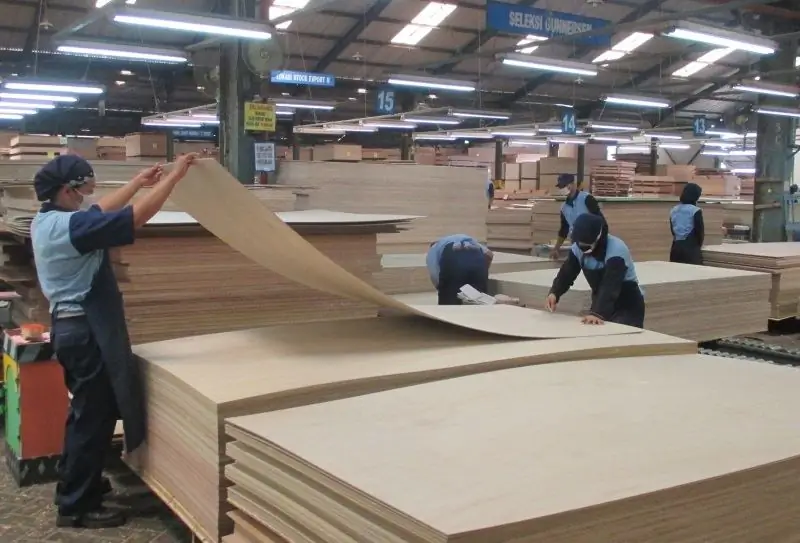
Plywood sheet is a kind of heterogeneous wood material. Only thin-leaf veneer is used as a basis, superimposed on each other under high pressure of the press. Actually, the whole process can be divided into three main stages - preparation of wood, its processing and gluing. Also, in different industries, additional stages may be included that improve or modify certain qualities of blanks or finished products. For example, modern plywood manufacturing technologies provide for repeated impregnation of the veneer structure in order to give it refractory and frost-resistant qualities. This is especially important if plywood is to be used in roof construction later on. After the production of this material, there is also a lot of waste (mainly after peeling), which can be consumed in the process of manufacturing particle boards.
Selection and preparation of wood blanks
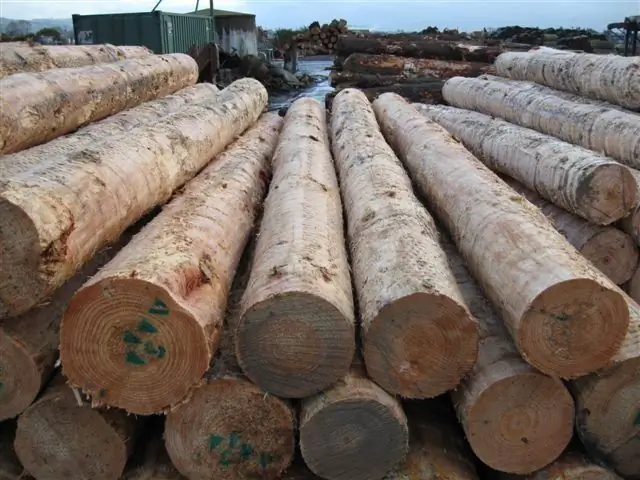
Wood blanks for plywood are called ridges. For them, massifs of birch, linden, alder and some of the conifers are usually used. As in the case of the production of other wood-based materials, plywood blanks undergo rigorous quality control, during which defective and simply unsuitable raw materials are screened out.
The main processing procedure is to increase the plasticity of the wood structure, which is important from the point of view of further obtaining lamellas. According to the regulations, the production of plywood from veneer is possible only when cutting blanks that have undergone hydrothermal treatment. This operation consists in the steam treatment of logs and their settling in the aquatic environment. For example, pools with a water temperature of about 40 ºС are used for birch blanks. Soaking lasts several days, depending on external microclimatic conditions.
Mechanical debarking is performed at the final stage of wood preparation. The bark is removed, after which blocks are formed on sawing machines. These are the piecessolid logs, the length of which varies from 130 to 150 cm on average. They are used for cutting veneer.
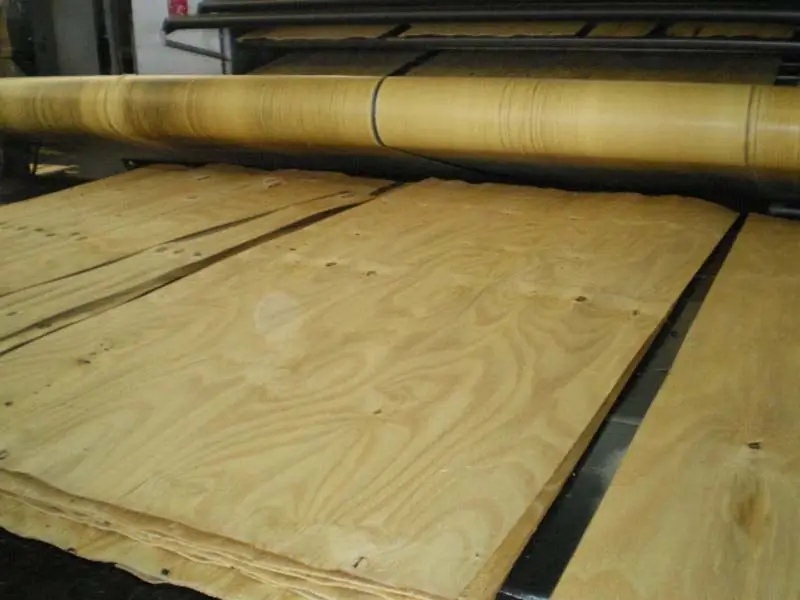
Obtaining veneer
Modern industries use several methods for cutting lamellas for plywood. Of these, peeling with the help of a circular machine stands out, planing blocks, as well as sawing them into thin strips. However, the processes of planing and sawing, due to low productivity and economy, are increasingly being replaced by peeling. For this operation, special machines are used that cut the workpieces in cross section. The log is fixed on a circular base and, in the process of rotation around its axis, is cut off with high-precision peeling knives. This is how the most critical stage in the plywood manufacturing process is performed, on which the main characteristics of the future product depend. Finished strips of lamellas come out of the lathe. They are stacked in piles, after which they are sent for further processing.
Veneer Drying
For this procedure, a special conveyor is used, on which the lamellas are blown with warm air currents. With the help of measuring devices such as a moisture meter, the line operator controls and sorts the veneer. According to the technology, the optimal moisture ratio of lamellas for plywood production should be 6%. Excessively wet sheets after heat treatment are either sent for drying or rejected. Since the lamellas have a very delicate fine structure, mechanical defects are often encountered. But in the presence of minor damage, the veneer is not discarded. On theAt this stage, it is possible to repair plywood sheets with the help of artificial inserts of fragments of a new veneer, which is selected according to texture, moisture content and size. Lamels that successfully pass this stage are checked by a scanner and sent for daily storage.
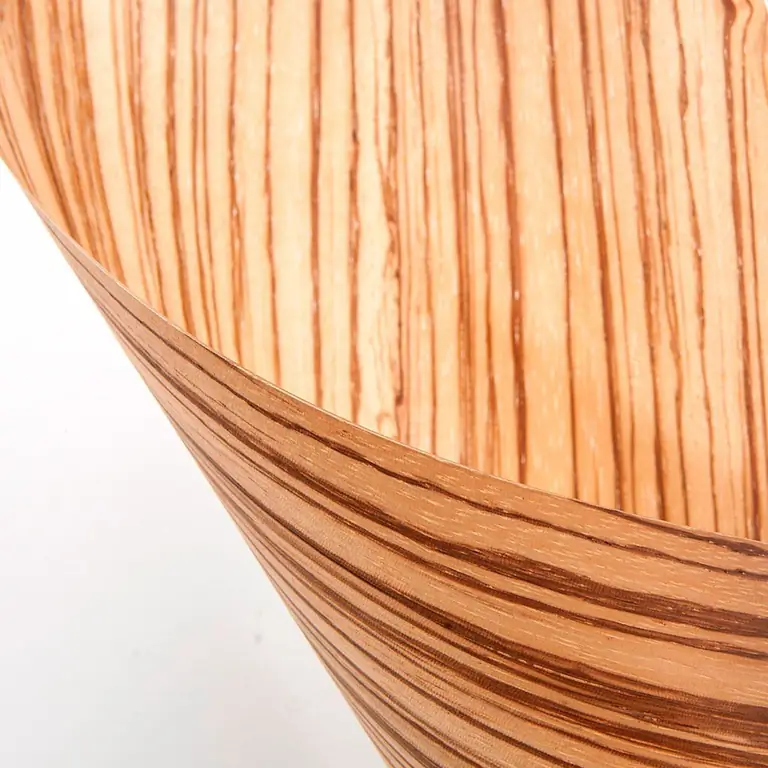
Slat bonding
Special compositions sometimes with unique recipes are used as glue. Each plant strives to develop its own methods for making an adhesive mixture that will make the plywood sheet stand out from the crowd of competitors. For example, some compositions already inside the structure provide the effect of lamination with phenol-formaldehyde resins. But more often it is practiced to manufacture laminated plywood with the application of a paper-resin film, which makes the material stronger and more resistant to moisture absorption.
The binder is applied on special machines using cylindrical corrugated drums. Lamellas treated with glue are sent to a set, where veneer packs are formed. Here the sheets are subjected to cold pre-pressing, which is a preparatory stage before the final gluing. The sheets are brought together perpendicular to each other. The main gluing procedure uses a hydraulic hot press provided with mechanical loading. Finished plywood sheets are aged for 24 hours in the workshop.
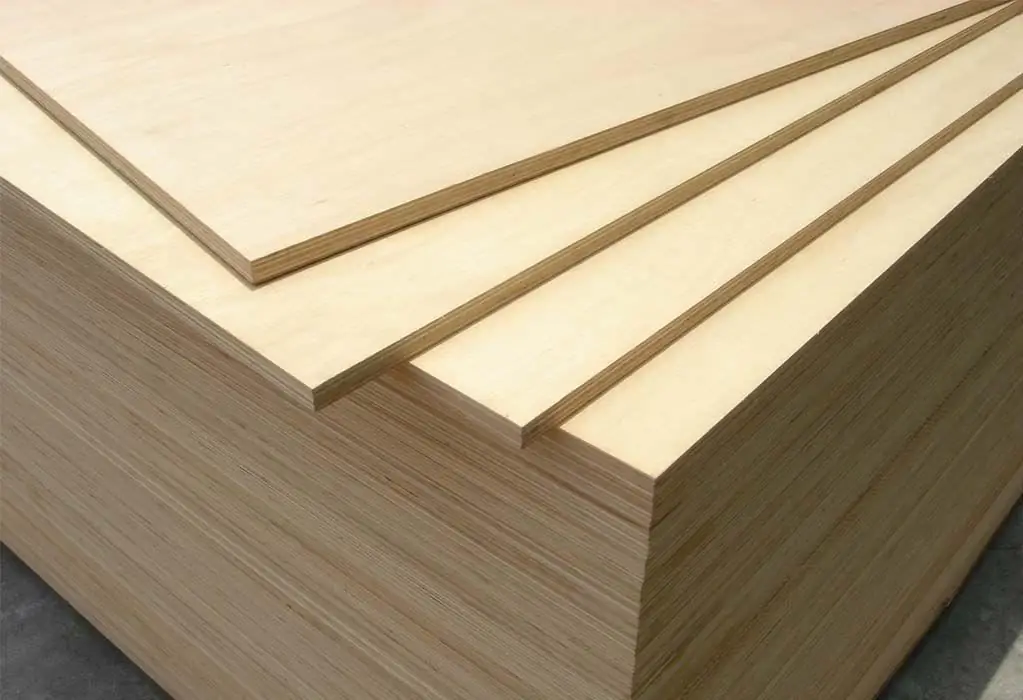
Making plywood with your own hands
The technology for the production of plywood at home is not fundamentally different from the factory. Least,the same processing and preparatory operations, such as stripping, cutting and gluing, are carried out. Log raw materials are also used (preferably from birch), after which sawing and peeling is carried out - the most difficult operation for hand-made processing, which can be replaced with special planers in small volumes. If in-line production is required, then it is better to organize a small conveyor line. For example, small plywood factories in a small area are provided with compact lines with equipment that automatically performs peeling, sawing, peeling, drying, glue pressing and sanding operations.
Plywood applications
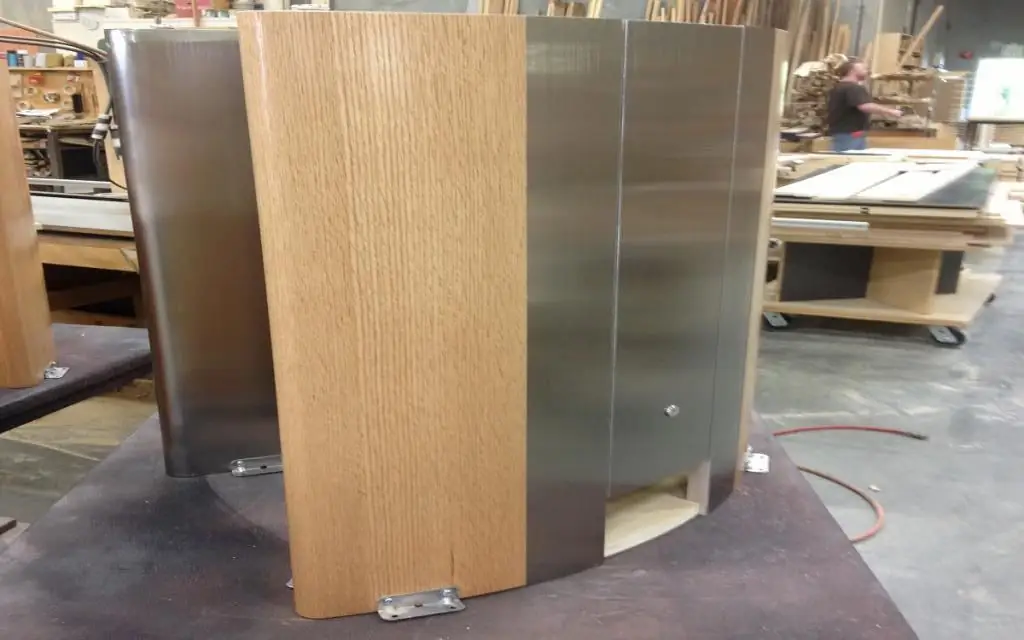
This is a versatile material that finds use in both professional environments and households. Perhaps the largest volumes of plywood are used in construction and furniture production. At home, such sheets can be used in interior design, interior decoration and household needs. The industrial production of plywood with improved technical and physical qualities allows us to offer worthy products for the automobile and carriage building industry. Again, the popularity of this material is due to its low cost and decent performance properties. Plywood is not as durable compared to metal and fiberglass, but it is more attractive against the background of chipboard products. The only serious limitation on the use of such sheets is the presence of chemically unsafe adhesive mixtures in the structure. That is, we are not talking about environmental cleanliness either.
Conclusion
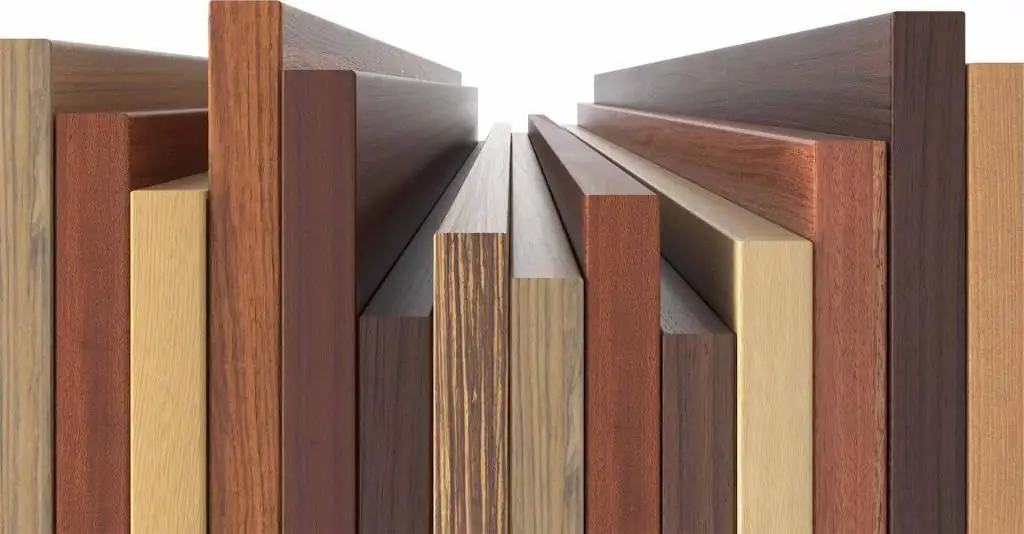
Today, plywood production technologies are quite standardized and optimized. Developers of methods for manufacturing this material are increasingly focusing on incorporating the latest protective coatings and impregnations that eliminate the physical imperfections of the tree itself. However, the cost of the modified sheet increases markedly. By the way, today the production of plywood to order on average varies from 300 to 600 rubles per sheet. Widescreen panels can cost even 1000 rubles and more. At the same time, the inclusion of additional operations of high-precision abrasive grinding or fire-resistant impregnation in the technological process raises the price tag by another 10-15%. Also, a lot will depend on the type of wood used, the quality of peeling and the type of veneer block.
Recommended:
The main stages of personnel selection, process features and criteria
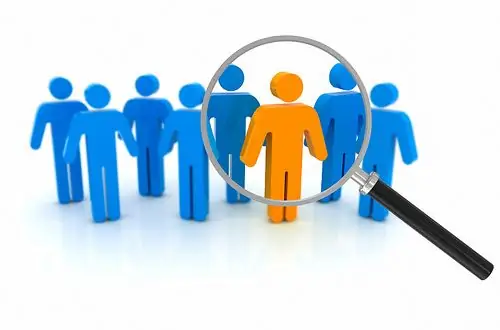
List of the main stages of personnel selection at enterprises and organizations. What are the stages of personnel selection? Description of methods and management tools in the selection of candidates and applicants for a vacant position in the company
Ceramic material: properties, production technology, application
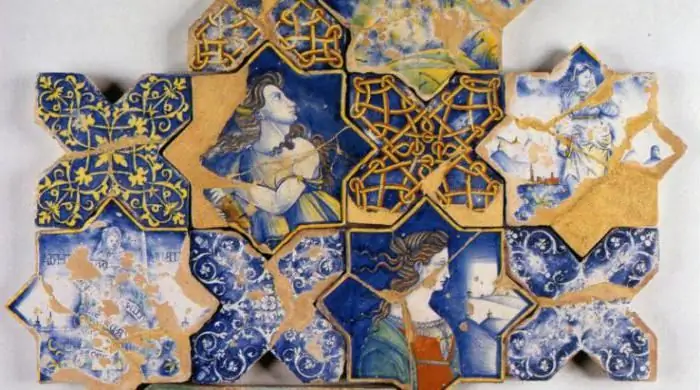
The first pottery appeared long before people learned how to smelt metal. Ancient pots and jugs that archaeologists find to this day are proof of this. It is worth noting that the ceramic material has unique properties that make it simply indispensable in some areas
Crop production - what kind of activity is this? Branches and areas of crop production
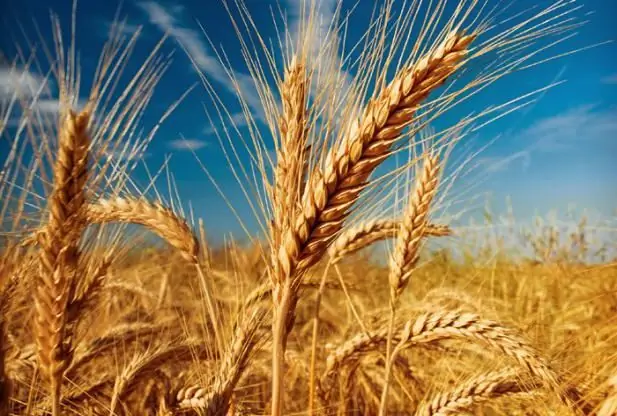
More than two-thirds of the products consumed by the population of the planet are provided by the leading branch of agriculture - crop production. This is the fundamental basis of world agricultural production. Consider its structure and talk about the achievements and development prospects of this world economy
Cold smoking technology: the concept of the process, the construction of a smokehouse, the main rules of smoking and food preparation
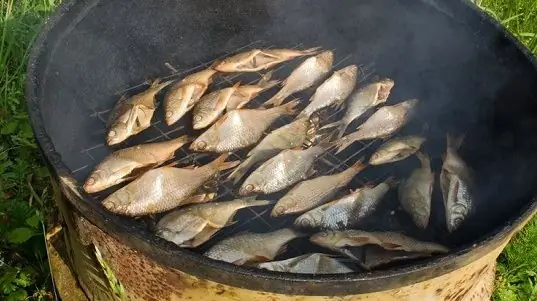
When cooking fish or meat in the country, if desired, you can also use cold smoking technology. Using this technique, it will not be difficult to get a very tasty homemade product. However, to smoke fish, meat or sausage in a cold way, of course, you need to do it right
Technical preparation of production: tasks, stages, process and management
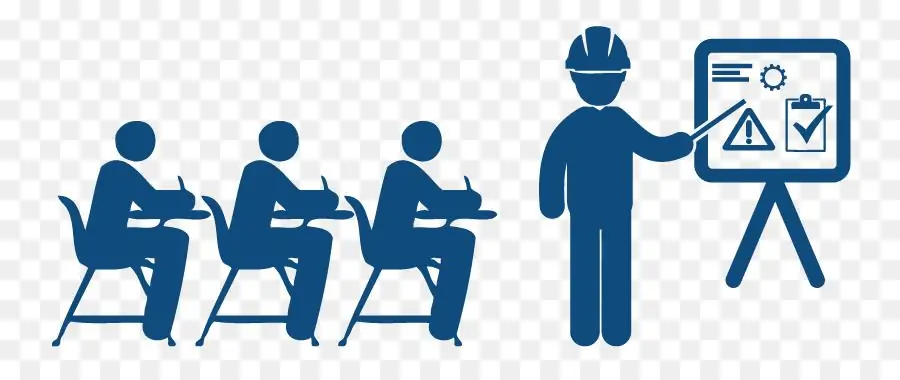
The development of new, highly efficient and more advanced products, competitiveness in the world market - all this is directly related to organizational issues, among which a special place is occupied by the technical preparation of production. Why does she have such a role?