2025 Author: Howard Calhoun | [email protected]. Last modified: 2025-01-24 13:10
Most people prefer to build their homes primarily from natural wood. Moreover, even accessories are selected from this material. And, despite the presence of wear-resistant analogues of artificial origin, which are becoming more and more lately, the tree is always highly valued. However, in its original form, this natural material is short-lived - it rots, it warps at a high level of humidity. In addition, he is not able to withstand the attack of insect pests, including fungus. Heat treated wood eliminates many problems and is also hygienic.
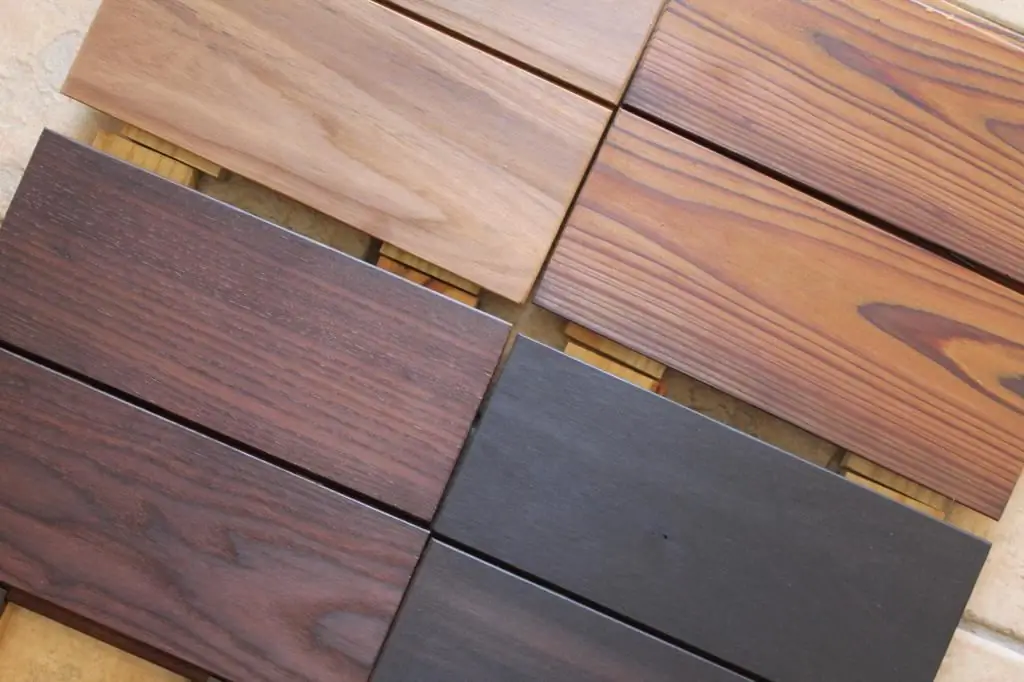
Even in ancient times, craftsmen thought about how to increase the service life of wooden products and structures. And, ultimately, it all ended with an innovative solution. What is this raw material?
General information
Under the term "tremodine" hides a material thatheat treated at high temperature. It can range from +185 °C to +250 °C. No chemicals are added during the production process! As a result, a new material of the 21st century is born, which meets modern quality requirements.
Many consumers appreciate the environmental friendliness of the raw materials used, no matter how much time has passed. And the physical and mechanical properties of materials are priceless. And it would seem that other modern analogues, which are in no way inferior and have more chances for universal recognition. The reality is a little different.
Natural material, and in particular heat-treated wood (what do you now know), compares favorably with them, at least in that people will not soon abandon it. Perhaps this will never happen. Here, as with the classics - it is immortal and out of competition with fashion trends.
What did the ancient masters know about?
The benefits of heat treatment of wood have been known to mankind for a very long time, and already in those distant times it was put into practice. The craftsmen noticed that pre-boiling the workpieces using oil helps to increase the service life of the products. Thanks to this treatment, the material stopped absorbing moisture, so there is no decay, and the shape is preserved for a long time.
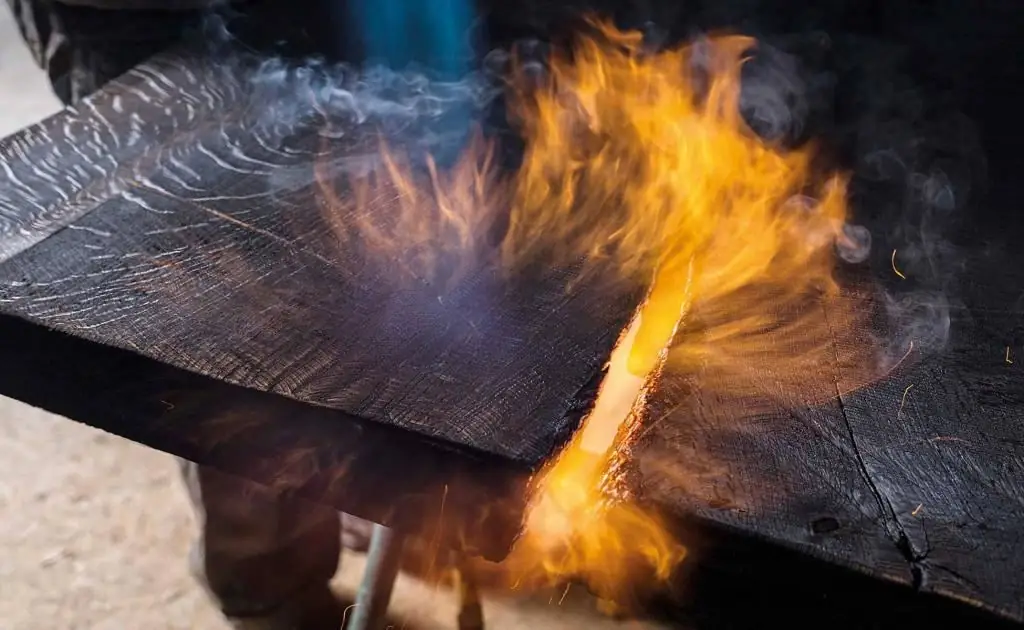
But this is far from the only technique used. What has not been done in order to extend the life of wood:
- The Normans resorted to firing the material in the openfire.
- The masters of the Germanic and Slavic tribes held in high esteem soaking and boiling.
- Even the Indians were familiar with the firing technology - they increased the strength of their arrowheads and spears.
As for examples, you don't have to look far for them. Evidence of the use of heat-treated wood is found in antique mill wheels. But many of them have survived to this day!
Chemistry - both good and bad
Chemical treatment of wood has also been widely used since ancient times, and is still used today. Its essence lies in the impregnation of the material by various means. Among the most common formulations:
- antiseptics;
- polymer substances;
- paint;
- lacki.
Moisture protective films were also in use. The benefit of chemical treatment is an increase (and significant) resistance to negative external influences. However, there is also harm, because wood loses its main advantage - environmental friendliness.
Technology development
Thermal treatment of wood has been of interest since the 30s of the last century. Scientists from Germany took the initiative, and a few decades later it was picked up by the Americans. About what it is - heat-treated wood, humanity has known for a very long time. Therefore, specialists were busy conducting experiments and experiments. But in the end, the technology was not widely used.
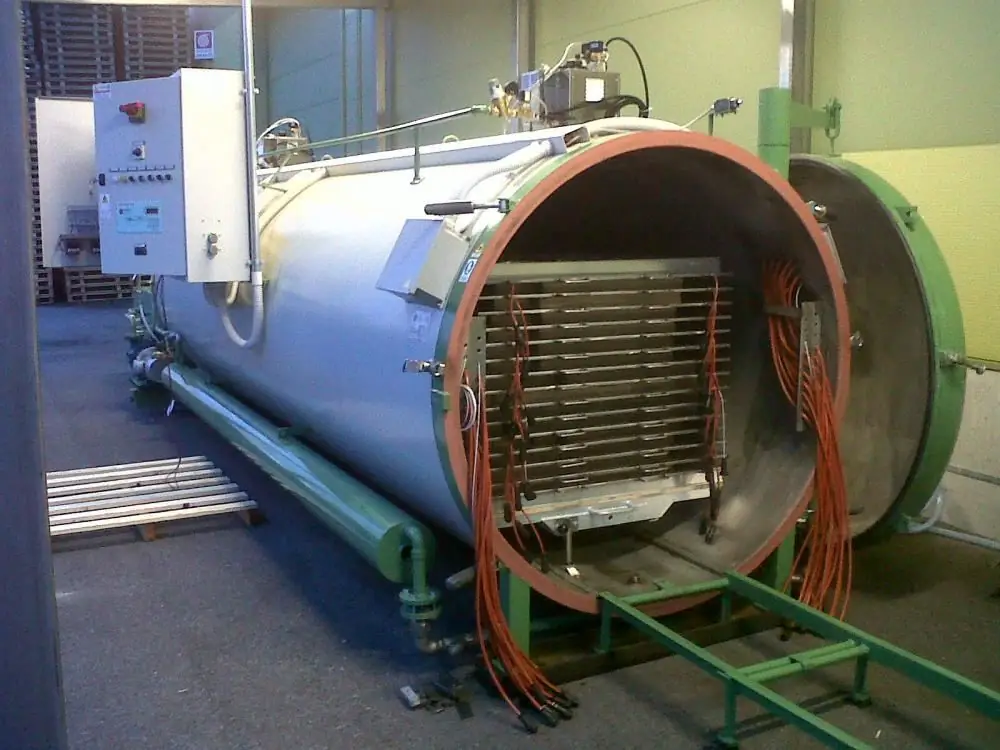
In the late 80s in the city of Novy Urengoy in Russiathe beginning of its own development of the technology of heat treatment of wood was laid. It is based on the experience of ancient masters. And after receiving the new material, the production of furniture and sports equipment began.
At about the same time, specialists from other countries - Germany, Finland, France and the Netherlands - also took up exposure to high temperatures. Scientists conducted studies that proved that because of this, structural changes occurred in the wood. As a result, the material was made more wear-resistant and durable, which expanded its scope.
Finland
And yet, the technology for the production of heat-treated wood for the first time began to emerge in this country. Its residents noticed for the first time how exposure to high temperatures affects the resistance of the material. Samples were taken on various trees:
- birches;
- Firs;
- pines;
- aspen.
According to their methodology, the whole process consists of several stages:
- Moisture is removed from the fibers of natural material by drying in closed chambers at a temperature in the range of +130…+150 °C.
- Under the influence of high pressure and temperature (+200…+240 °C), as well as water vapor, hardening of wood occurs. At this stage, the material takes on a characteristic hue.
- The temperature regime goes down, the percentage of moisture content is brought to 4-6%, no more.
The result of such a cycle leads to the formation of a new structure in wood, and changesoccur at the molecular level. This is due to the splitting of the fibers and the bonds between them - this is precisely what the high temperature and pressure affects.
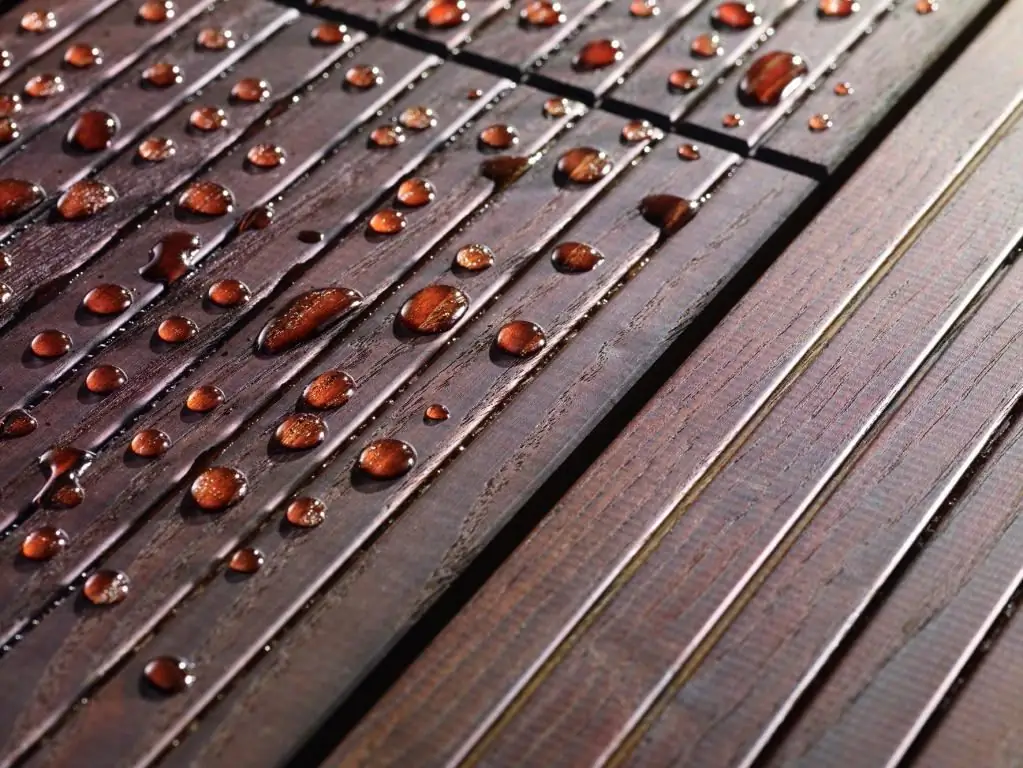
The result of using Finnish technology - heat-treated wood is able to withstand moisture and not be subjected to deformation under heavy rains. And all by reducing the porosity of the surface of the material.
Developed technologies
As noted by many experts from all over the world, today there are about two dozen technologies for the thermal treatment of wood. Many of them have patents and among them the most famous technologies are the following types of production:
- Thermowood is the native technology of Finnish craftsmen. According to this development, many factories operate in the country. At the same time, the Italian company Baschild and the French company BCI-MBS are using this technology.
- German development is based on drying wood, which is carried out in a liquid medium of organic origin (oil) with alternating temperature.
- Plato - this technology was developed by craftsmen from Holland. It involves thermal hydrolysis of wood under the influence of temperature in the range from +160 °C to +190 °C.
- Retification is already our own production of heat-treated wood from French specialists. In this case, the process takes place under the influence of a higher temperature (+200…+250 °C) in a supersaturated steam environment.
Onterritory of the Russian Federation, as well as in the USA, Canada and some other European countries, developed their own technologies for the thermal treatment of wood.
Strengths of thermowood
As a result of exposure to high temperatures, natural material loses those qualities that limited its scope. At the same time, the useful properties of the tree are fully preserved. All this contributes to the fact that wood acquires new qualities that can be considered the advantages of this modern and innovative material.
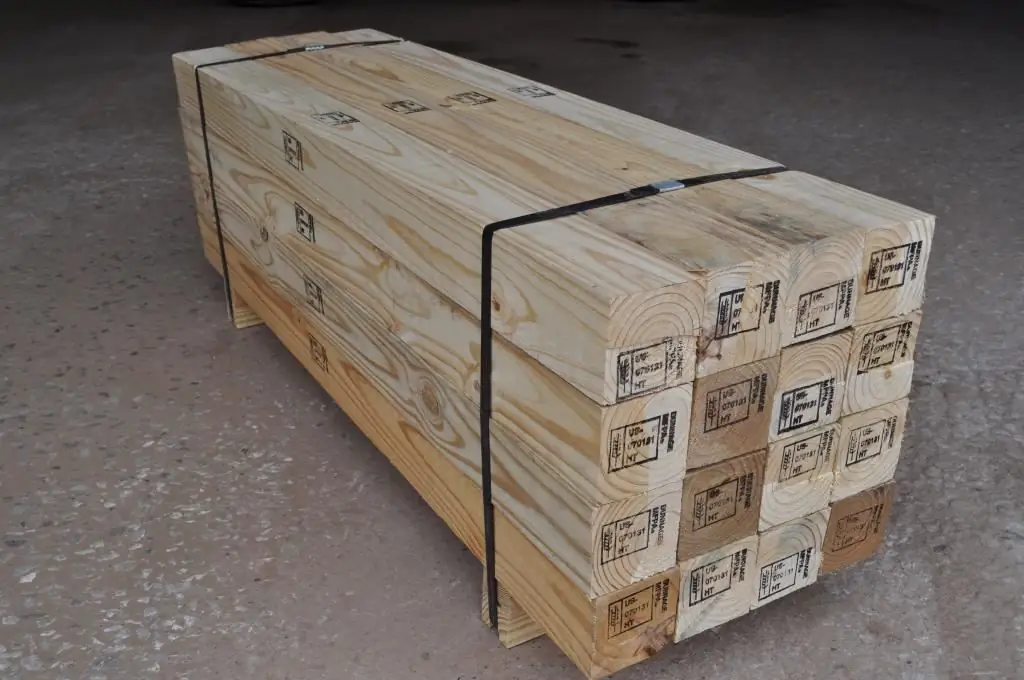
Among the significant advantages, the following advantages should be highlighted:
- Durability - after heat treatment, wood no longer absorbs moisture, therefore it does not swell or crack. This is achieved through the breakdown of polysaccharides, which are a favorite treat for fungi and other pests.
- High level of fire safety - heat-treated wood acquires hardness and density, which causes it to ignite very slowly than untreated wood.
- Strength - thanks to the thermal "modification" procedure, the material is resistant to mechanical stress.
- Attractive appearance - heat treatment promotes a strong manifestation of the wood structure. Due to this, even simple varieties acquire a new look, which is in no way inferior to the appearance of elite breeds.
Largely due to these qualities, today this innovative material is in great demand among professional builders and home craftsmen.
Classification
Since the heat treatment of wood is carried out under the influence of a fairly high temperature with a large gap (+150 °C to +240 °C), all thermal wood is divided into several classes.
The first group includes timber that is processed at a temperature not exceeding +190 °C. Its surface is lightly tinted and its technical performance is low.
The second group is represented by heat-treated wood that has been fired at +210 °C. This made it possible to increase its resistance to decay and this can already be considered a high-strength material. However, wood, although to a lesser extent, is fragile and ductile.
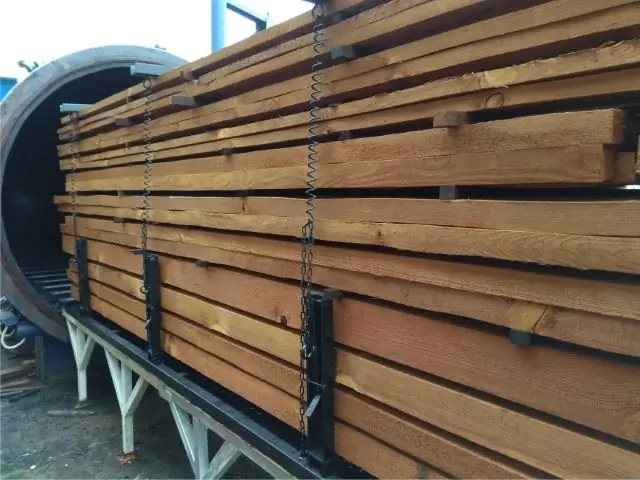
The third group includes materials of the highest quality - here the process takes place under the influence of the highest temperature of +250 °C. The result is a very dense and hard wood. It is resistant to any external impact.
Creating a DIY process
The thermowood is produced on an industrial scale using special equipment. Those who are interested in how such a process can be translated into reality on their own will be disappointed. It will not be possible to completely repeat everything that is done in factories for the simple reason that the technology is very difficult to implement. And at home, it is simply impossible.
As you know, wood without proper processing rots and quickly becomes unusable. At home, although it will not work to get closer to industrialproduction scale, but there are some good options:
- grinding;
- roasting;
- treatment with antiseptics.
That is, it is still possible to make heat-treated wood with your own hands. Moreover, all this can significantly extend the service life of wooden products and structures. Grinding and the firing process are folk methods. They were used in practice by our grandfathers and their parents.
If necessary, you can treat with chemicals that are specifically designed for this purpose. However, as already noted, the environmental friendliness of the material is lost. Therefore, they should be used consciously and not in all cases.
Good alternative
For burning wood, a blowtorch or a gas burner is used. Only pre-treated wood is wetted with water so that it does not catch fire. The procedure is carried out until a brown tint appears.
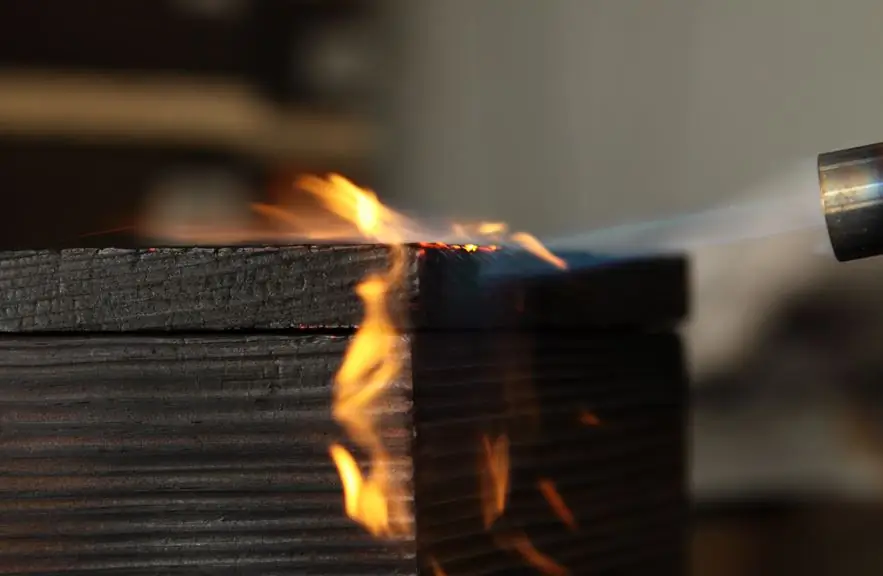
After firing, carbon is removed from the wood with a metal brush. Heat treatment under the influence of a lamp or burner can give the wood an aged effect that is appreciated by many admirers. In addition, now the material is reliably protected from the development of fungi (including mold) for a long period of time.
At the same time, such a home technology for the production of heat-treated wood with your own hands does not allow you to achieve the qualities of the material that thermowood “born” in the factory has.
Recommended:
Wood processing technology and production of wood products
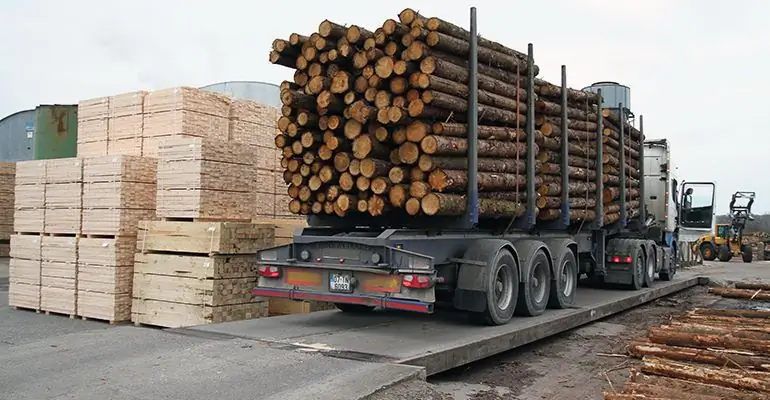
Wood is an unusual and especially valuable material. For all its familiarity, it has an amazing set of technical and physical properties that a person cannot repeat with the help of synthetic substitutes. This is due to the extensive use of blanks made of natural wood in a variety of industries. Modern wood processing technologies and the production of wood products in general make it possible to provide people with furniture, building materials, decorations, utensils, etc
Heat resistance and heat resistance are important characteristics of steels
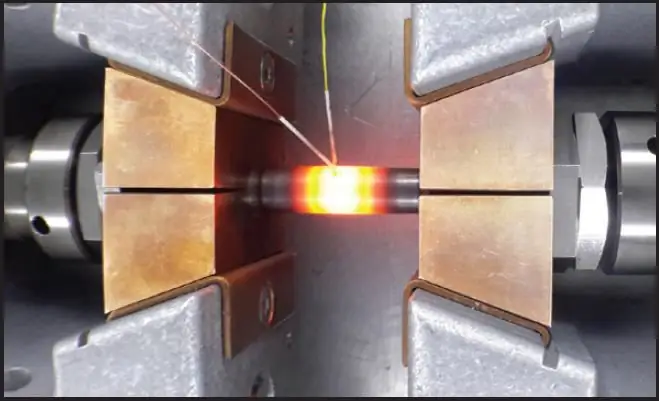
Ordinary structural steels, when heated, abruptly change their mechanical and physical properties, begin to actively oxidize and form scale, which is completely unacceptable and creates a threat of failure of the entire assembly, and possibly a serious accident. To work at elevated temperatures, materials engineers, with the help of metallurgists, created a number of special steels and alloys. This article gives a brief description of them
Heat-resistant alloys. Special steels and alloys. Production and use of heat-resistant alloys
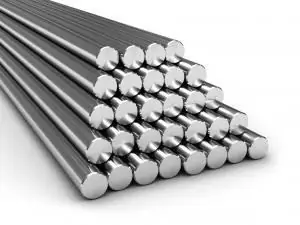
Modern industry cannot be imagined without such material as steel. We encounter it at almost every turn. By introducing various chemical elements into its composition, it is possible to significantly improve the mechanical and operational properties
Thermal conductivity of sandwich panels: concept, main characteristics, dimensions, thickness, thermal conductivity coefficient, installation rules, pros and cons of operation
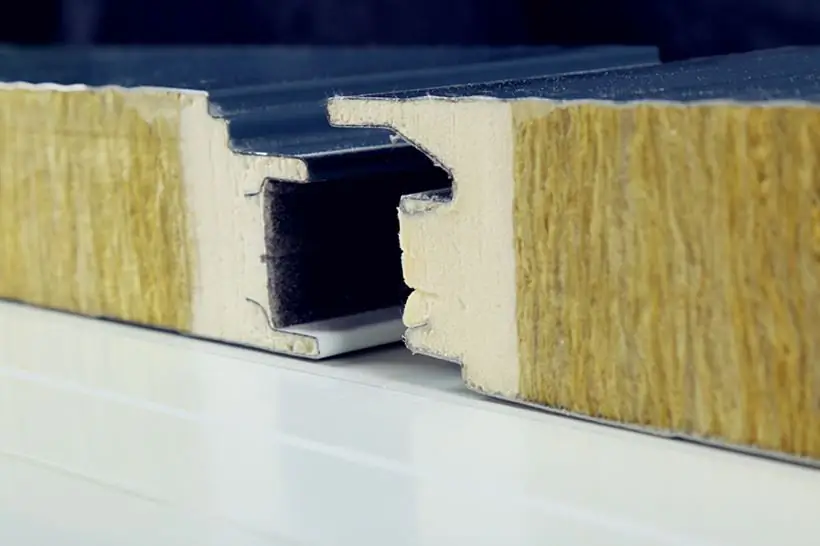
Thermal conductivity of sandwich panels will be the lowest if polyurethane foam is the basis. The parameter under consideration here varies from 0.019 to 0.25. The material is strong, dense and light. It is chemically resistant and does not absorb moisture. Rodents are indifferent to polyurethane foam, fungi and mold do not develop inside it. Working temperature reaches +160 ˚С
Chamber drying of wood: technology, pros and cons
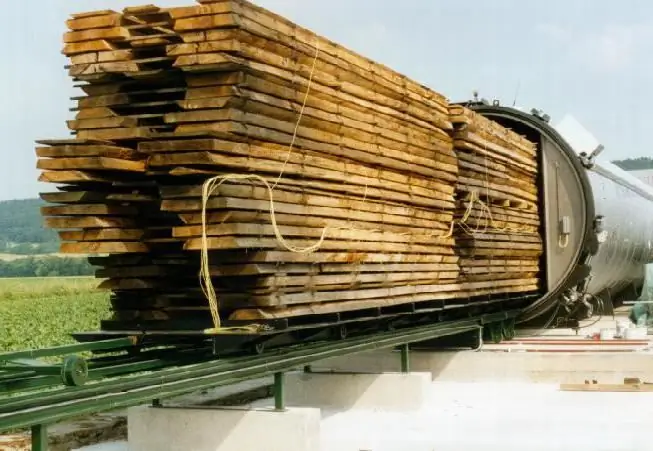
The article is devoted to chamber drying of wood. The drying technology, stages and main operations, as well as its advantages and disadvantages are considered