2025 Author: Howard Calhoun | [email protected]. Last modified: 2025-01-24 13:10
Machining is a process during which the dimensions and configuration of workpieces and parts are changed. If we talk about metal products, then special cutting tools are used for their processing, such as cutters, broaches, drills, taps, cutters, etc. All operations are performed on metal-cutting machines according to the technological map. In this article, we will find out what are the methods and types of metal machining.
Processing methods
Machining is divided into two large groups. The first includes operations that occur without removing the metal. These include forging, stamping, pressing, rolling. This is the so-called mechanical processing with the help of pressure or impact. It is used to give the desired shape to the workpiece. For non-ferrous metals, forging is most often used, and for ferrous metals, stamping.
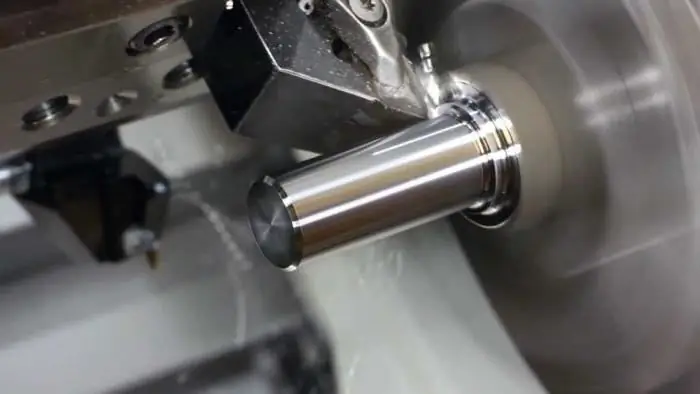
The second group includes operations during which part of the metal is removed from the workpiece. This is necessary to give it the required size. Such mechanical processing of metal is called cutting and is performed using metal-cutting machines. The most common machining methods are turning, drilling, countersinking, grinding, milling, reaming, chiselling, planing and broaching.
What determines the type of processing
Manufacture of a metal part from a blank is a time-consuming and rather complicated process. It includes many different operations. One of them is mechanical processing of metal. Before proceeding with it, they draw up a technological map and make a drawing of the finished part indicating all the necessary dimensions and accuracy classes. In some cases, a separate drawing is also prepared for intermediate operations.
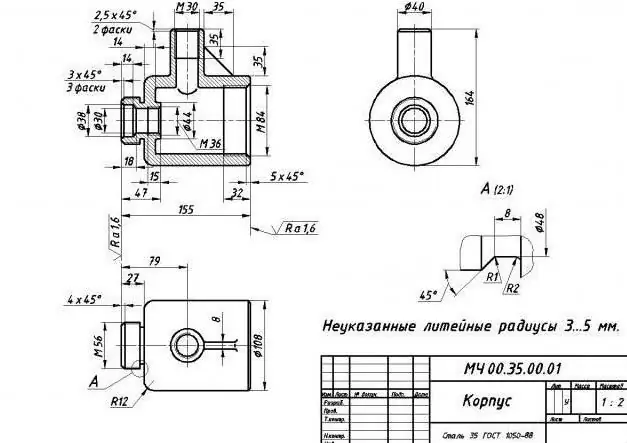
In addition, there are rough, semi-finish and finish machining of metal. For each of them, the calculation of cutting conditions and allowances is performed. The type of metal processing as a whole depends on the surface to be treated, the accuracy class, the roughness parameters and the dimensions of the part. For example, to obtain a hole according to the H11 grade, rough drilling is used with a drill, and for a semi-clean reaming to the 3rd accuracy class, you can use a reamer or countersink. Next, we will study the methods of machining metals in more detail.
Turning and drilling
Turningperformed on lathes of the group with the help of cutters. The workpiece is attached to the spindle, which rotates at a given speed. And the cutter, fixed in the caliper, makes longitudinal and transverse movements. In the new CNC machines, all these parameters are entered into the computer, and the device itself performs the necessary operation. In older models, for example, 16K20, longitudinal and transverse movements are performed manually. On lathes it is possible to turn shaped, conical and cylindrical surfaces.
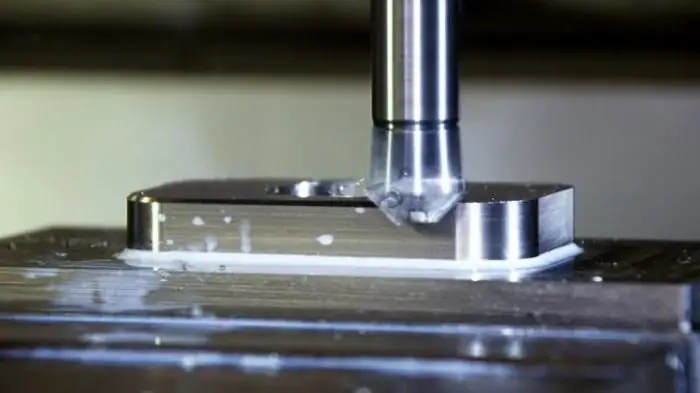
Drilling is an operation that is performed to obtain holes. The main working tool is a drill. As a rule, drilling does not provide a high class of accuracy and is either rough or semi-finishing. To obtain a hole with a quality below H8, reaming, reaming, boring and countersinking are used. In addition, after drilling, internal threading can also be performed. Such machining of metal is performed using taps and some types of cutters.
Milling and grinding
Milling is one of the most interesting ways of processing metals. This operation is performed using a wide variety of cutters on milling machines. There are end, shaped, end and peripheral processing. Milling can be both rough and semi-finishing, and finishing. The lowest quality of accuracy obtained during finishing is 6. With the help of milling cutters, various keys, grooves, wells, undercuts are machined, profiles are milled.
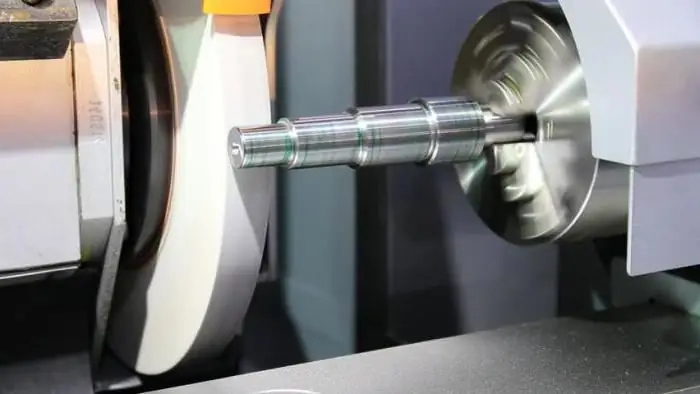
Grinding is a mechanical operation used to improve the quality of roughness, as well as to remove an excess layer of metal down to a micron. As a rule, this processing is the final stage in the manufacture of parts, which means it is finishing. For cutting, abrasive wheels are used, on the surface of which there is a huge number of grains with a different shape of the cutting edge. During this processing, the part is very hot. In order for the metal not to be deformed and not chipped, cutting fluids (LLC) are used. Machining of non-ferrous metals is carried out with the help of diamond tools. This allows you to ensure the best quality of the manufactured part.
Recommended:
Machining of metal parts
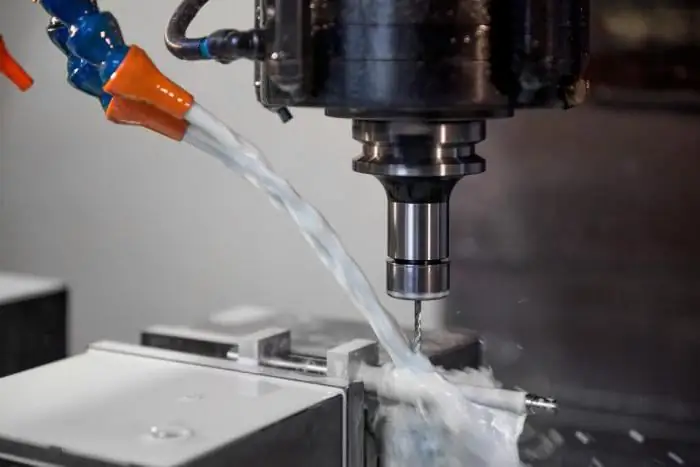
Production of a part is a labor-intensive process that includes a huge number of different types of processing. As a rule, it begins with the preparation of route technology and the execution of a drawing. This documentation contains all the necessary data for the manufacture of the part. Machining is a rather important stage, which includes a huge number of different operations. Let's consider them in more detail
Loan repayment methods: types, definition, loan repayment methods and loan payment calculations
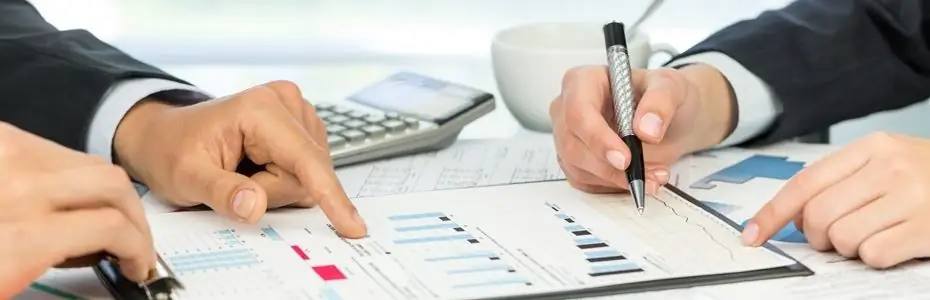
Making a loan in a bank is documented - drawing up an agreement. It indicates the amount of the loan, the period during which the debt must be repaid, as well as the schedule for making payments. The methods of repayment of the loan are not specified in the agreement. Therefore, the client can choose the most convenient option for himself, but without violating the terms of the agreement with the bank. In addition, a financial institution can offer its customers various ways to issue and repay a loan
Laying communications: types, classification, methods and methods of laying, purpose of communications
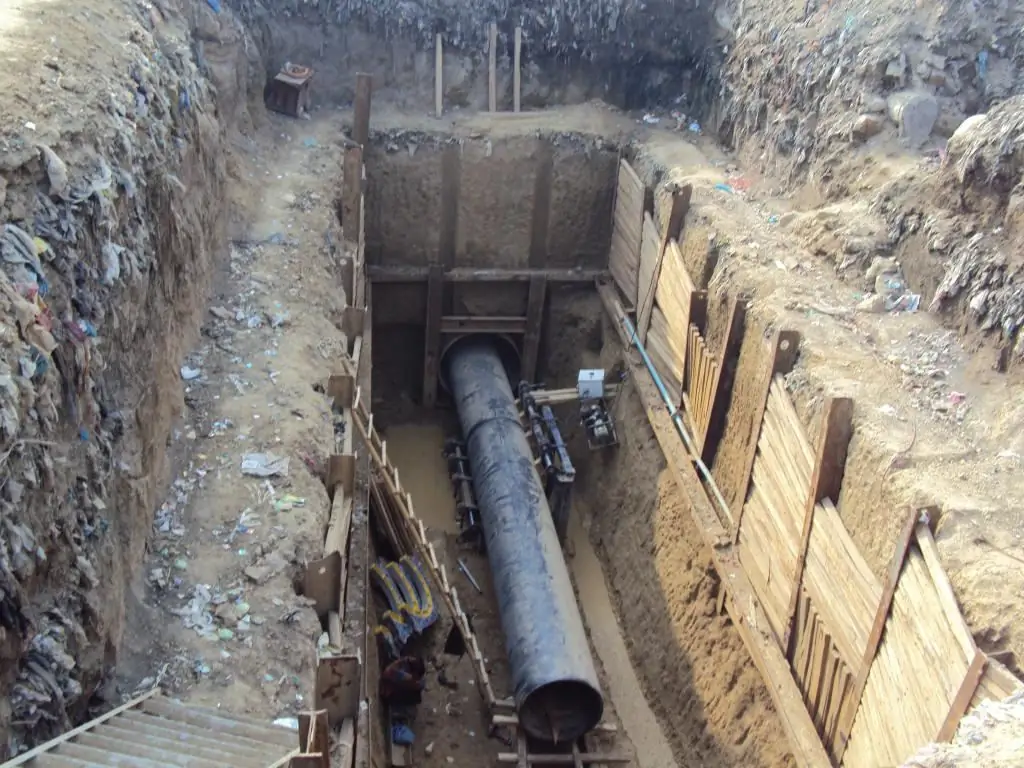
Laying communications is one of the most important stages in the construction, for example, of a new residential building. To date, there are a large number of the most diverse ways of installing communications. Their features, as well as advantages and disadvantages, have led to the fact that an individual method is selected for each case
Metal casting: process, methods, methods
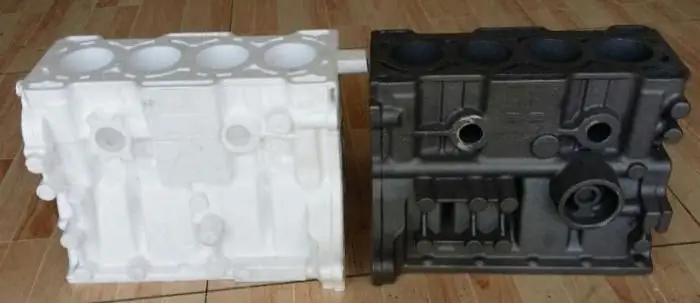
Metal is the basis of all modern civilization. In a year, modern humanity mines and processes such an amount of iron alone that before the whole world would have been digging it for at least a couple of centuries
Milling machining center: types, description and purpose
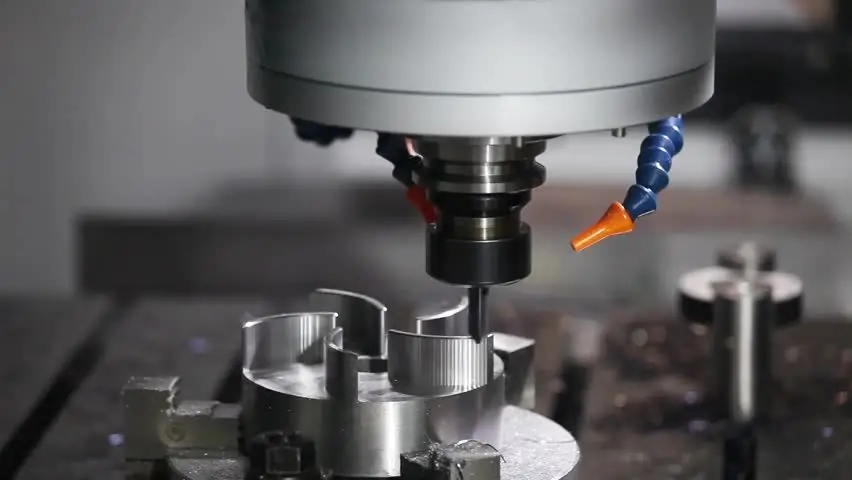
Today, a milling machining center is a multi-operation machine with numerical software. The main advantage is the ability to carry out complex machining of three-dimensional parts. For this purpose, the center is equipped with various processing devices