2025 Author: Howard Calhoun | [email protected]. Last modified: 2025-01-24 13:10
Production of a part is a labor-intensive process that includes a huge number of different types of processing. As a rule, it begins with the preparation of route technology and the execution of a drawing. This documentation contains all the necessary data for the manufacture of the part. Machining is a rather important stage, which includes a huge number of different operations. Let's consider them in more detail.
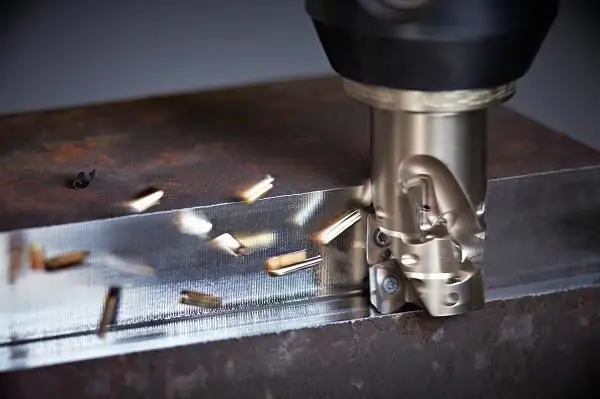
Material
Depending on the required part, the metal material is also selected. After its further processing, a finished product is obtained. In other words, the metal material is a blank. It can be of several types: stamping, forging, rolling, cermet. Each type of workpiece has a different manufacturing method. If, for example, forging, in small-scale production, forging hammers are used, then to obtain a cermet material, metal powders are pressed into a pressmolds under pressure 100-600 MPa.
Machining flat and cylindrical surfaces
Flat surfaces are processed by milling, planing, pulling. As a rule, such blanks include sheet metal and cermet.
Planing is carried out on cross- and longitudinal-planing machines. When processing on the first, the main movement is carried out by the cutter, and the feed movement is carried out by the machine table. On a longitudinal planer - the opposite is true. In addition, such machining is considered unproductive, since it has too low a cutting speed. The working tool loses a lot of time on reverse idling. The advantages of this processing are straightness and proportionality.
Milling
One of the most highly productive methods of processing both flat and cylindrical surfaces is milling. This is due to the fact that it is carried out simultaneously by several teeth of the cutter. Machining can be carried out in a serial, parallel, series-parallel and continuous way. Milling can process surfaces with roughness Rz=0.8 - 0.63 µm and such processing will be called fine.
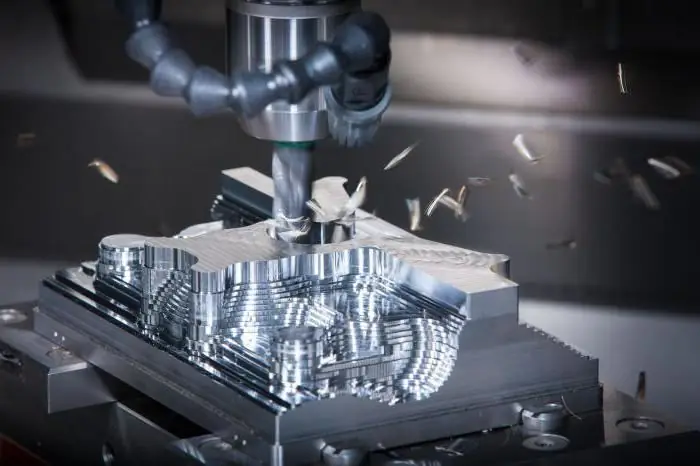
Pulling
This method is used to process parts in mass and large-scale production. In some cases, broaching can be replaced by grinding and chiselling. Such machining has a very high precision. Stretching can be done as invertical direction as well as horizontally. This machining is used for high precision operations, and the cutting tool works under huge loads such as compression, bending, tension.
For example, broaching is used in the processing of holes in firearms, for cutting keyways and splines. As a cutting tool, broaches are used, both solid and prefabricated. They are made from high speed and medium alloy tool steels.
Hole and thread machining
Mechanical processing of parts is not complete without such important tools as drills, countersinks, taps, reamers. In order to drill a hole of the required diameter, it is imperative to calculate the cutting mode for this process. As a rule, the hole is drilled to the required diameter, taking into account the allowance for subsequent processing. In order to ensure the best accuracy, a reamer is used, and a countersink can be used for semi-finishing.
Machining parts can also be done with a tap. This tool is designed for threading existing holes. There are taps for blind and through holes. For cutting external threads, cutters and dies are used. Before using them, you need to grind the workpiece a little. In order to create a high-quality and efficient entry of the cutting tool, before starting the operation, a chamfer is removed at the end of the product. It must be the same height as the thread profile.

Mechanical processing of metal parts and thread processing in rare cases is carried out using screw heads. They are attached to the quill with a shank. It can have prismatic, radial or round combs. They do not come into contact with the threaded threads during the reverse stroke, because at the end of the process they automatically diverge.
Machining of metal on machines and lines is studied in many colleges and universities. The speci alty has the code 36-01-54 and is subdivided into the following areas: milling machine operator, turner, grinder, locksmith and machine work supervisor, operator of automatic (AL) and semi-automatic lines. Since modern technologies do not stand still, it is very important to study the machining of metals on CNC and AL machines.
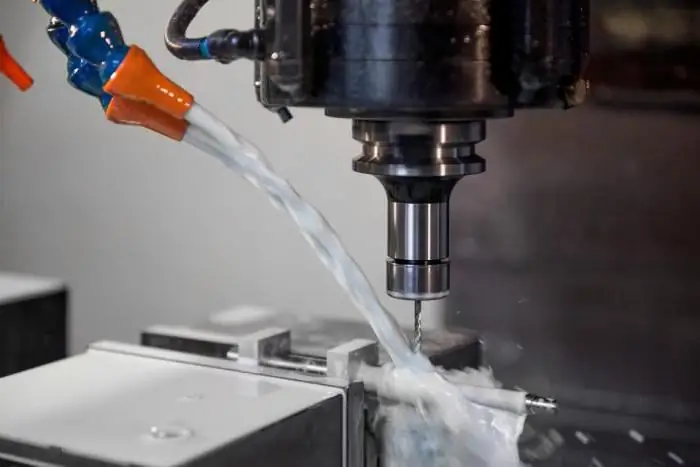
Such equipment greatly facilitates the work of operators. Their main task is to control, adjust and load and unload parts and blanks. All operations are performed by automatic lines with the help of special computer programs and practically do not require the intervention of operators. The use of AL can significantly reduce the cost of processing and the time of manufacturing parts.
Recommended:
How to open an auto parts store: rules and tips
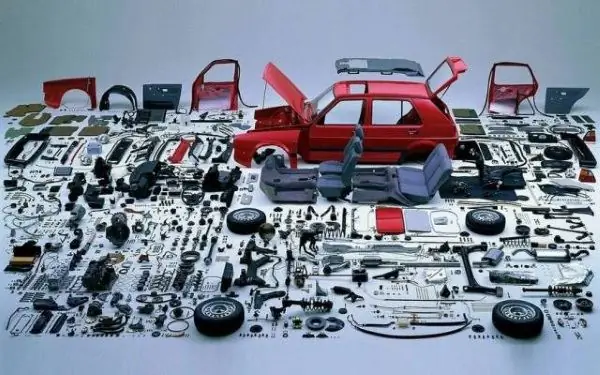
How to open an auto parts store? Who should work in it? For successful trading, you will definitely need professional consultants who specialize in the sale of automotive parts. It's good if they understand how the car works
Machining of metal: types and methods
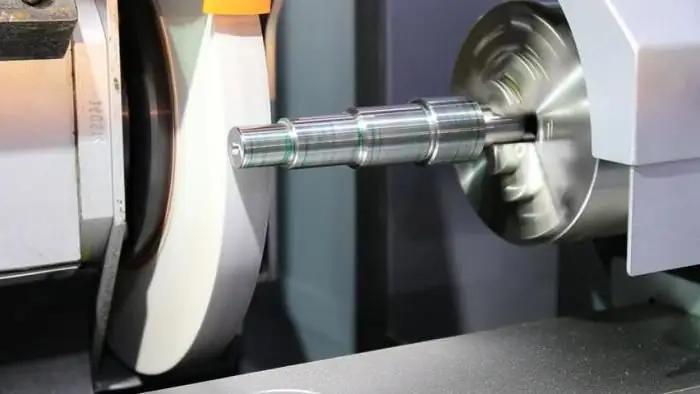
Machining is a process during which the dimensions and configuration of workpieces and parts are changed. If we talk about metal products, then special cutting tools are used for their processing, such as cutters, broaches, drills, taps, cutters, etc. All operations are performed on metal-cutting machines according to the technological map. In this article, we will learn what are the methods and types of mechanical processing of metals
CNC machining center: distinctive features, purpose, advantages over simple installations
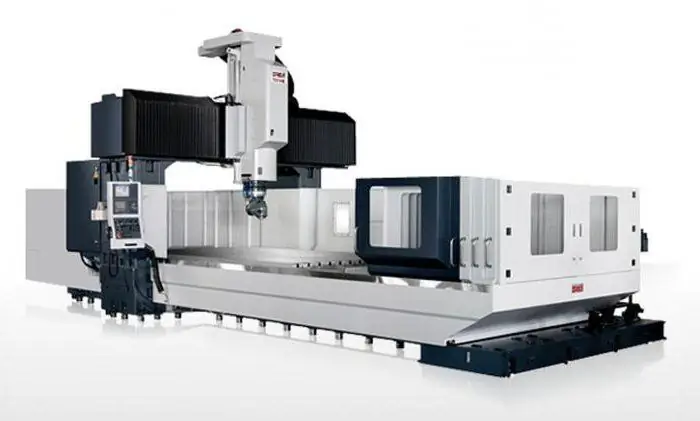
Automated plants are great for multitasking production. The machining center replaces long production lines. One device contains the functionality of a full cycle of manufacturing complex parts
Chrome plating parts. Chrome parts in Moscow. Chrome parts in St. Petersburg
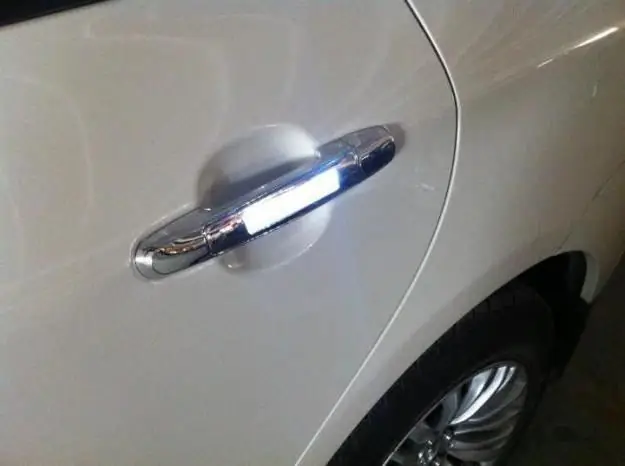
Chrome plating of parts is an opportunity to give them a new life and make them more reliable and of high quality in operation
Milling machining center: types, description and purpose
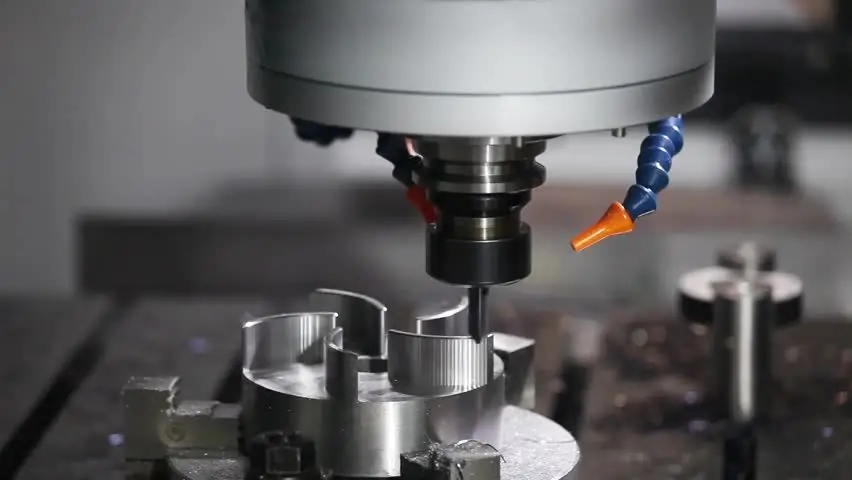
Today, a milling machining center is a multi-operation machine with numerical software. The main advantage is the ability to carry out complex machining of three-dimensional parts. For this purpose, the center is equipped with various processing devices