2025 Author: Howard Calhoun | [email protected]. Last modified: 2025-01-24 13:10
Today, a milling machining center is a multi-operation machine with numerical software. The main advantage is the ability to carry out complex machining of 3-dimensional parts. For this, the center is equipped with various processing devices.
What is OC
The milling machining center is equipped with many different tools. As well as special devices designed for automatic change of nozzles. Due to this, the productivity of such centers is very high. In addition, such equipment allows you to perform both roughing and semi-finishing or finishing.
Today, the simplest milling machining centers contain from 5 to 12 tools in their tool magazine. Medium models contain 15-30 instruments in their drum. The most advanced multi-operation machines boast a stock of 50-100 types of tools, and special OTs can have even more. Milling machining center canhave an additional work table or a device for dividing products. The pitch of this dividing device is pre-set. The ability to rotate the workpiece allows it to be processed from several sides without reinstalling it on the machine.
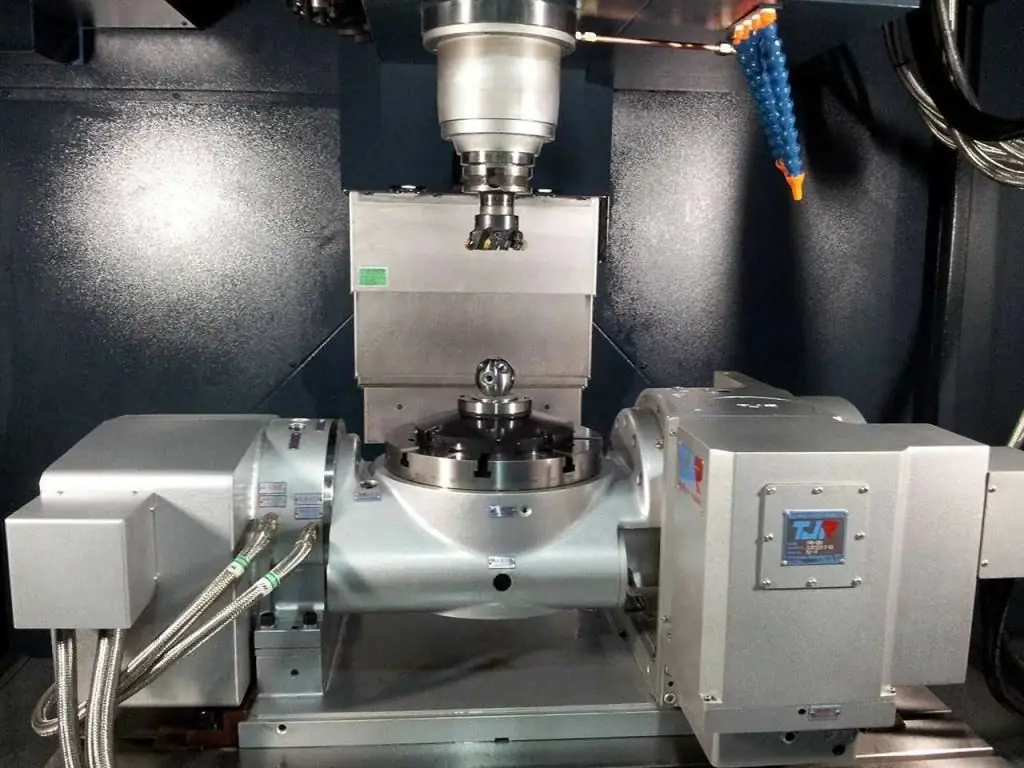
Application of OT in production
Metal milling center is capable of working with a part by rotating it in three axes. The accuracy of movement along these axes is ensured by the presence of a special servo drive, as well as a CNC system. This function is considered built-in. In addition to them, some OZ models have additional functions that allow you to calibrate and change the position of both the tool and the part.
Further, it is worth noting that CNC drilling and milling machining center is an expensive piece of equipment. For this reason, it is usually used only to work with those workpieces that are characterized by high technological complexity of manufacture. One such machining center can replace about three to five CNC machines or five to ten universal machines.
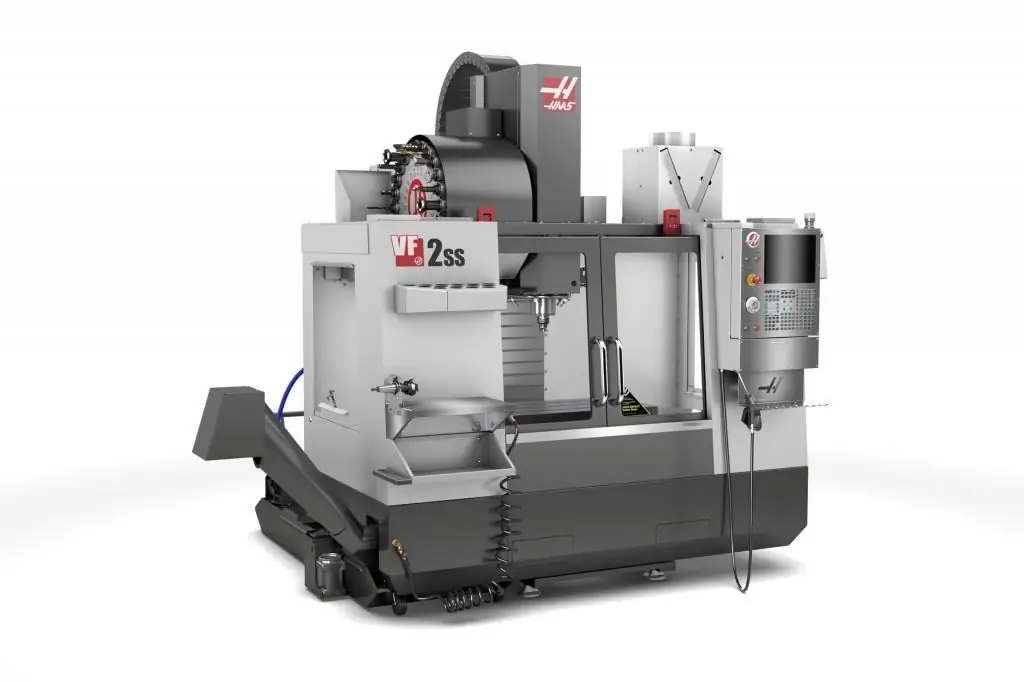
Description of vertical machines
Vertical milling machining centers have become one of the most common types of multi-operation machines. These devices have higher performance. This is due to the fact that this type of equipment has an increased processing speed. As a result, the heating temperature in the zone increases.processing, as well as parts and the tool itself. To combat this drawback, vertical-type machines have a coolant supply system, which can be supplied in two ways. The first option is the delivery of liquid through external flexible hoses, the second is the flow of liquid through the spindle of the device.
It is worth noting that the last cooling option, spindle-tool-part, is considered the most effective and allows you to increase the speed of processing the part and the accuracy of work.
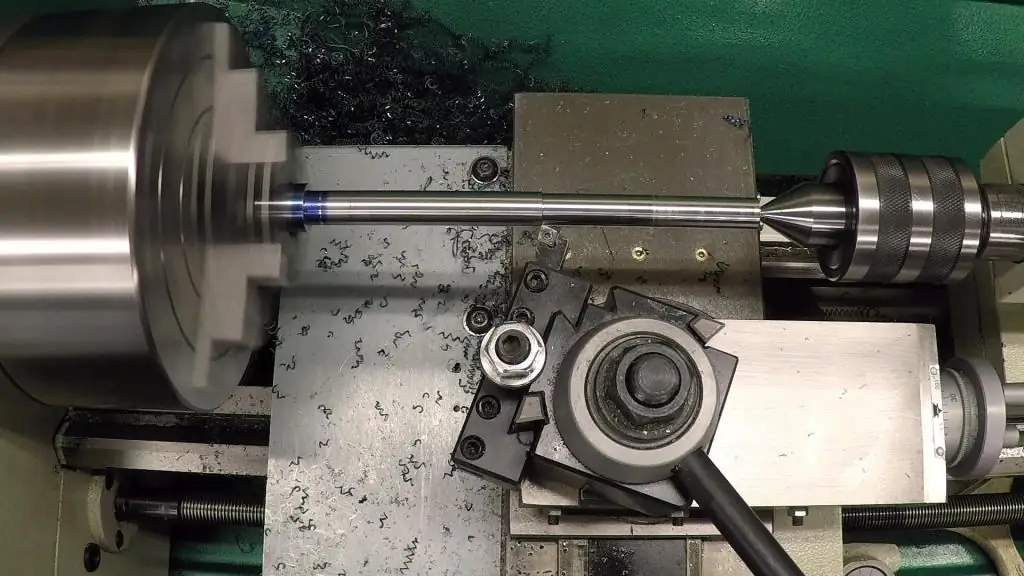
Features and operation of the vertical center
The main difference between a vertical multi-operational machine and a conventional milling machine is that it moves the spindle directly along the guide columns, and not the table, like a conventional machine. In this case, for vertical OCs, the table guides rest on the frame, which, in turn, stands on the foundation. This design made it possible to achieve greater rigidity, as well as to increase the accuracy of processing. This advantage in practice has led to the fact that vertical milling machines are often used for processing parts with large mass and dimensions.
As for the automatic change of working tools, vertical types of machines usually have 24 to 30 positions. Such a number of places is associated with the design of the drum, which is very similar to the revolver. The axis of rotation can be horizontal or vertical. The diameter, and therefore the number of positions, of such a magazine depends on the depth of the machine.
However, if you usecaterpillar or belt type changers, diameter restrictions can be avoided.
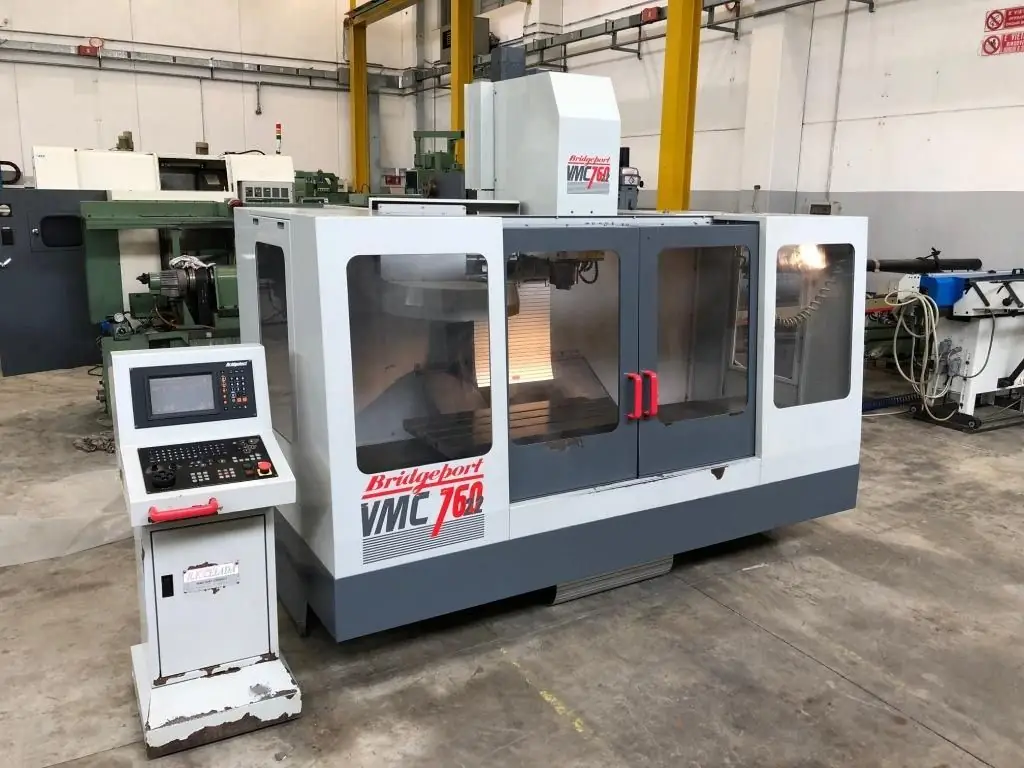
Description of horizontal machine types
Another popular variety. In this case, we are talking about a horizontal milling machining center. In some situations, it is simply impossible to do without it. But, as practice shows, their use is limited, and usually depends on several factors, such as the design and strength characteristics of the part, processing features, the need to drain coolant, and chips from the cutting site. They are the ones who force you to use it. In some cases, it is much more convenient than the vertical one.
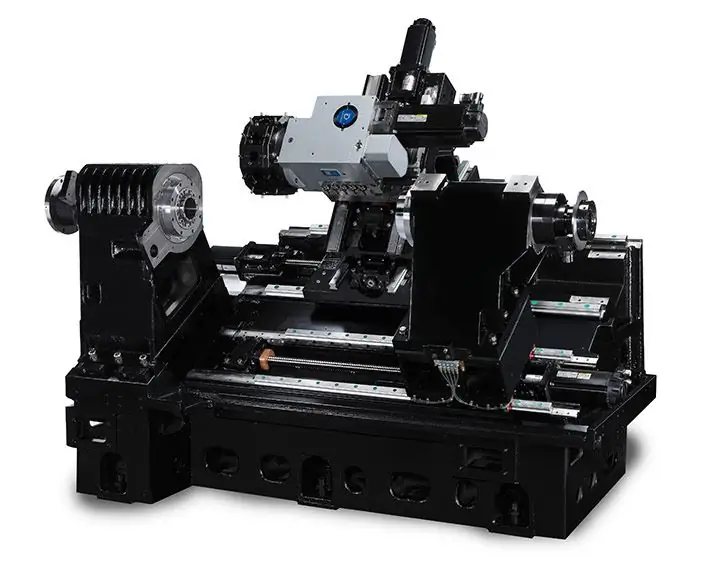
Main advantages of horizontal instruments
Today, there are three main advantages that a horizontal machine has:
- The horizontal position of the spindle itself is considered an advantage due to the fact that in this position the chips do not accumulate in large quantities at the cutting point. In addition, the horizontal version of the spindle is more rigid and has anti-vibration system.
- The second advantage is that the working table is made of two pallets, there is a fourth coordinate available: the ability to rotate the part in a horizontal plane in increments of 1 or 0, 001 degrees. The second pallet allows you to save time on the removal and installation of a new part. This item comes out on the first line in the case of mass production. In addition, the ability to rotate the table will allow you to process the workpiece from all sides.
- The third feature and advantage is the very horizontal location of the spindle and the ability to use a caterpillar-type changer. In the case of using not two wheels, but more of them, it becomes possible to equip a "caterpillar" with a complex design. Its peculiarity is that it is small in volume, but at the same time it allows you to place 40, 90 and even 120 positions.
Otherwise, both vertical and horizontal types of equipment are designed for complex processing of workpieces made of ferrous or non-ferrous metals.
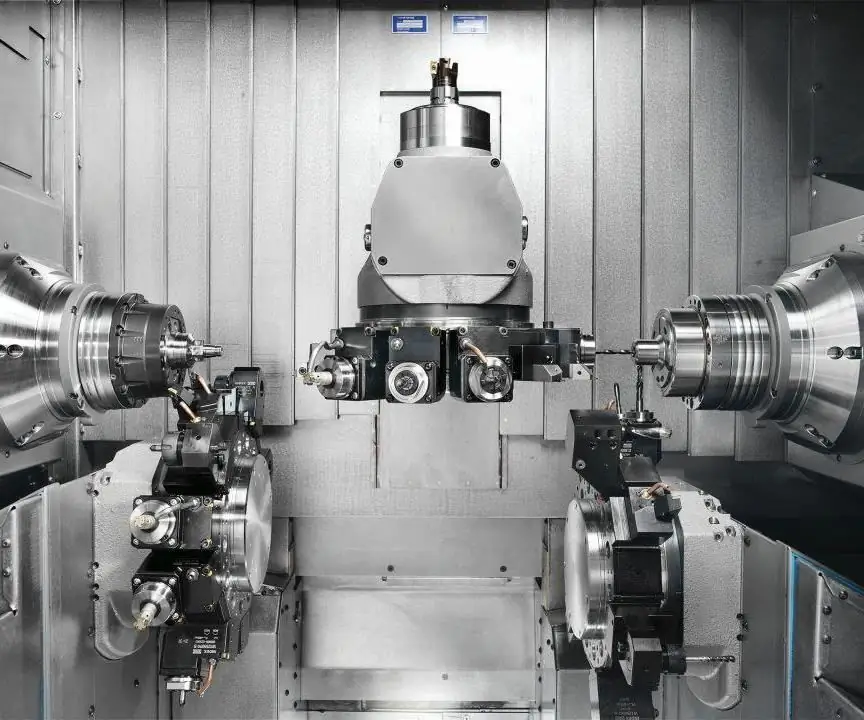
Turning and milling MC
Today, the turning and milling machining center is popular not only in industry, but also in everyday life. Naturally, its power is significantly lower, as are its dimensions. But at the same time, such centers are still capable of performing both turning and milling operations, and at a very high level.
It is worth noting that this type of machine can carry out both drilling and milling. Old turret-turning models had low turret mobility, and therefore were not widely used. The turning and milling center of the new development is free from such a disadvantage.
C-axis turning and milling equipment
The machine with such an axis became one of the first centers that could perform milling and turning operations. The main difference from previous models was that each drill andthe cutter had its own drive, rotating the tool.
The C-axis version of the center allows you to control the speed of rotation of the tools, as well as, according to experts, to monitor the angular position of the part. In this case, the angle indexing accuracy will be less than 0.001 degrees.
Based on the above, one can understand why these types of machining centers have gained such wide popularity.
Recommended:
Cutting speed for milling, turning and other types of mechanical processing of parts
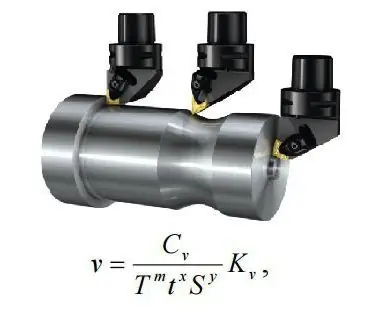
Calculation of cutting conditions is the most important step in the manufacture of any part. It is very important that the calculation itself be rational. This is due to the fact that for various mechanical operations it is necessary to individually select the cutting speed, spindle speed, feed rate, and also the depth of cut. A rational mode is one in which production costs will be minimal, and the quality of the resulting product will be as accurate as possible
Machining of metal: types and methods
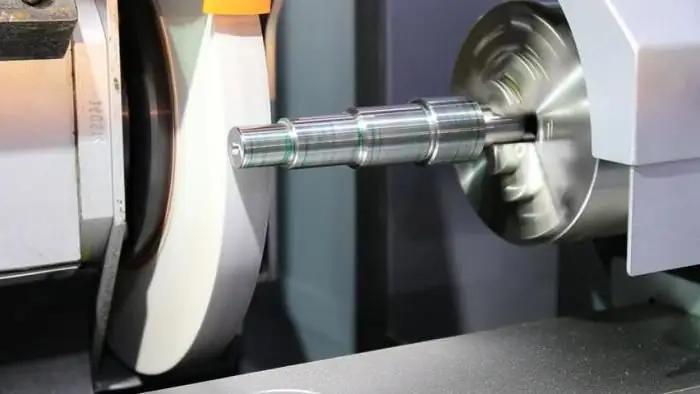
Machining is a process during which the dimensions and configuration of workpieces and parts are changed. If we talk about metal products, then special cutting tools are used for their processing, such as cutters, broaches, drills, taps, cutters, etc. All operations are performed on metal-cutting machines according to the technological map. In this article, we will learn what are the methods and types of mechanical processing of metals
Milling is Milling fixture and procedure description
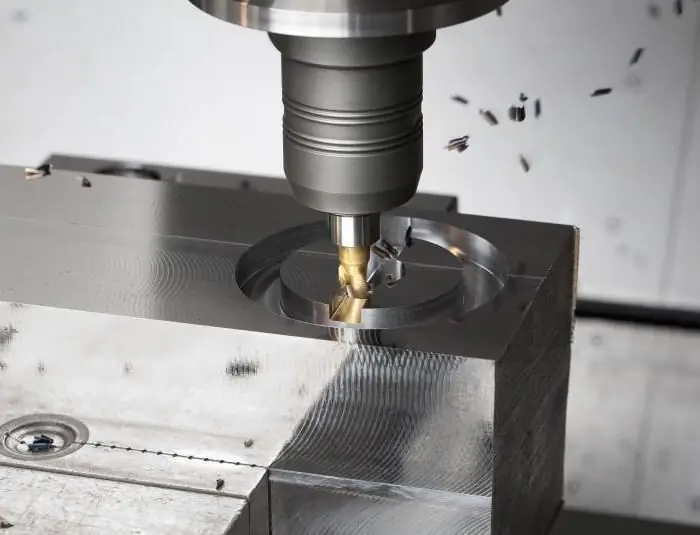
Milling is a surface treatment method based on the alternate operation of the teeth of the cutter. There is a huge variety of tools depending on their functional purpose, processed materials, characteristics of manufactured parts
CNC machining center: distinctive features, purpose, advantages over simple installations
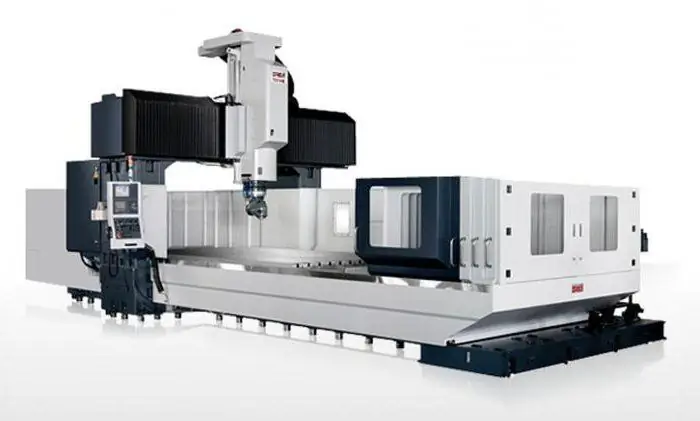
Automated plants are great for multitasking production. The machining center replaces long production lines. One device contains the functionality of a full cycle of manufacturing complex parts
Vertical milling machine, its device and purpose
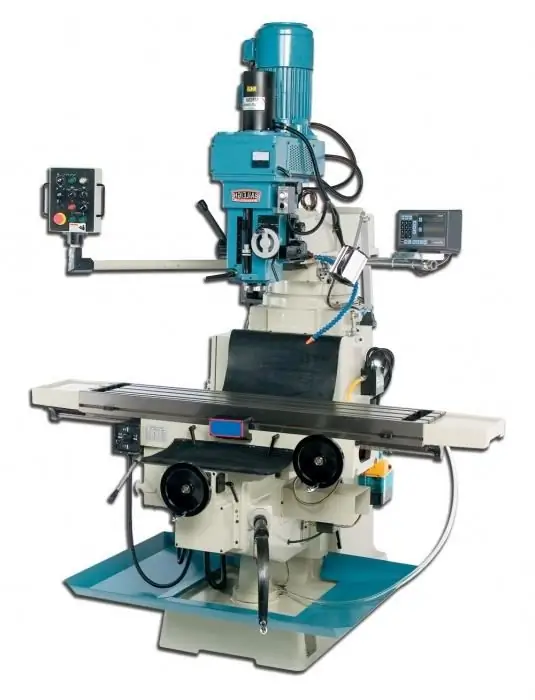
To date, it is quite typical to use parts of complex configuration in various branches of mechanical engineering - shaping surfaces of stamps, molds, gears, copiers and many others. The main methods for manufacturing such complex-shaped products are the following: casting, stamping and cutting