2025 Author: Howard Calhoun | [email protected]. Last modified: 2025-01-24 13:10
The alloy of an element of the eighth group of the periodic system of Mendeleev with atomic number 26 (iron) with carbon and some other elements is commonly called steel. It has high strength and hardness, devoid of plasticity and viscosity due to carbon. Alloying elements increase the positive characteristics of the alloy. However, steel is considered to be a metallic material that contains at least 45% iron.
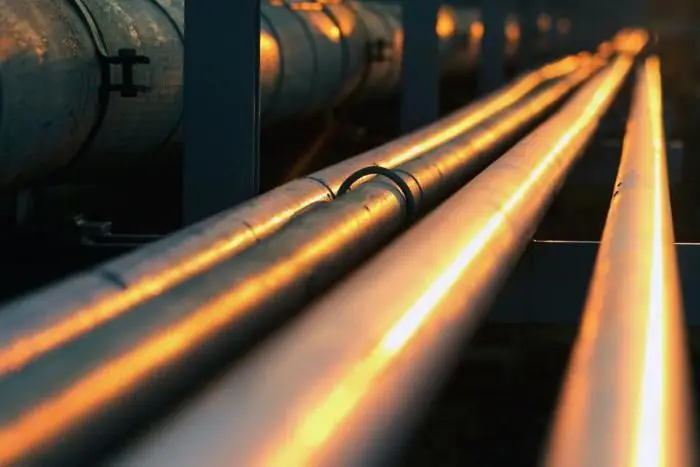
Let's consider an alloy such as R6M5 steel and find out what characteristics it has and in what areas it is used.
Manganese as an alloying element
Until the 19th century, ordinary steel was used to process non-ferrous metals and wood. Its cutting characteristics were quite enough for this. However, when trying to process steel parts, the tool heats up very quickly, wears out and even deforms.
The English metallurgist R. Muschette, through experiments, found out that forIn order to make the alloy stronger, it is necessary to add an oxidizing agent to it, which will release excess oxygen from it. They began to add mirror cast iron, which contained manganese, to cast steel. Since it is an alloying element, its percentage should not exceed 0.8%. So, R6M5 steel contains from 0.2% to 0.5% manganese.
Tungsten Iron
Already in 1858, many scientists and metallurgists worked on obtaining alloys with tungsten. They knew for sure that it was one of the most refractory metals. Adding it to steel as an alloying element made it possible to obtain an alloy that could withstand high temperatures and still not wear out.
Steel R6M5 contains 5.5-6.5% tungsten. Alloys with its content most often begin with the letter "P" and are called high-speed. In 1858 Muschette obtained the first steel containing 9% tungsten, 2.5% manganese and 1.85 carbon. Later, adding another 0.3% C, 0.4% Cr to it and removing 1.62% Mn, 3.56% W, the metallurgist obtained an alloy called samokal (P6M5). According to its characteristics, it is also similar to P18 steel.
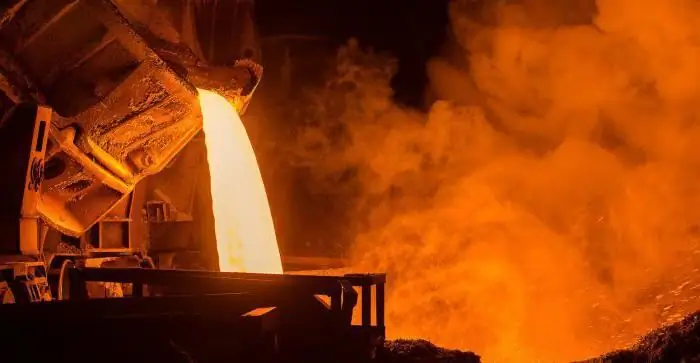
Tungsten shortage
Of course, in the 1860s, when many elements were in full abundance, steel with the addition of tungsten was considered the strongest. Over time, this element in nature becomes less and less, and the price for it grows.
From an economic point of view, adding a large amount of W to steel has become impractical. For this reason, R6M5 steel is much more popular than R18. Looking at their chemical composition, you can see that the tungsten content in P18 is 17-18.5%, while in the tungsten-molybdenum alloy it is up to 6.5% maximum. In addition, up to 0.25% copper and up to 5.3% molybdenum are present in the self-caller.
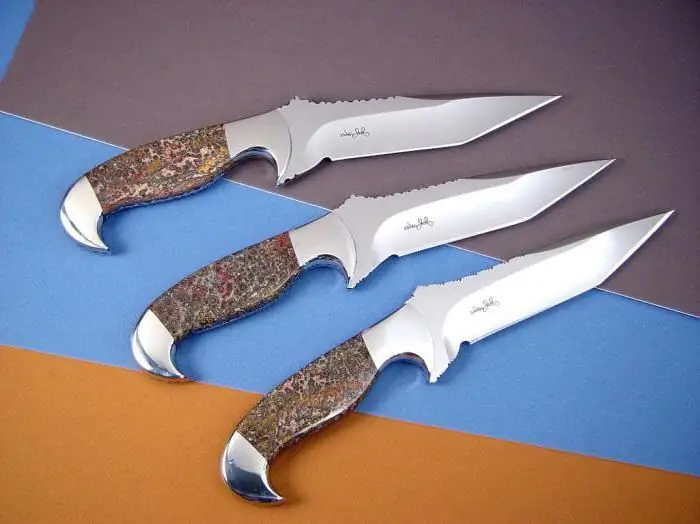
Other alloying elements
In addition to the above carbon, manganese, tungsten and molybdenum, R6M5 steel also contains cob alt (up to 0.5%), chromium (4.4%), copper (0.25%), vanadium (2.1%), phosphorus (0.03%), sulfur (0.025%), nickel (0.6%) silicon (0.5%). What are they for?
Each alloying element has its own function. So, for example, chromium is necessary for thermal hardening, while nickel increases toughness. Molybdenum and vanadium virtually eliminate temper brittleness. Some of the alloying elements improve steel properties such as red hardness and hot hardness.
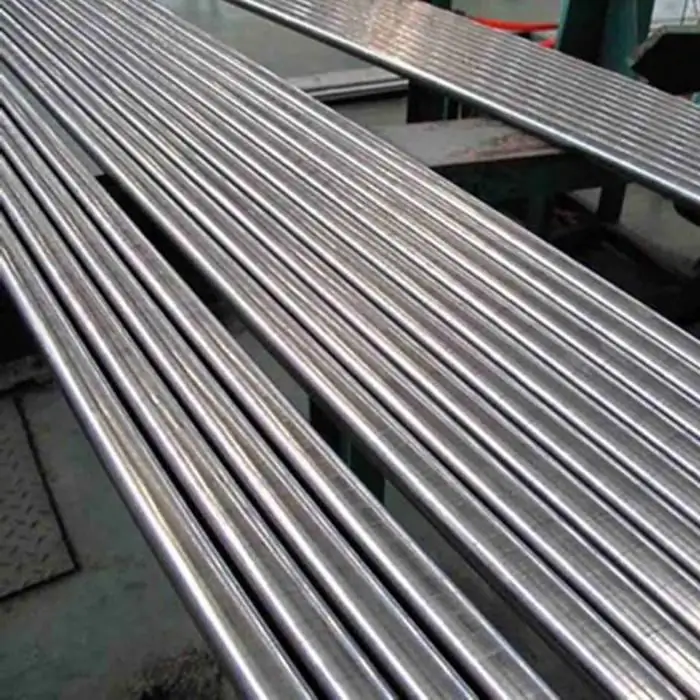
Steel R6M5, the characteristics of which we are studying, in the hardened state has a hardness of 66 HRC at a test temperature of up to 600 °C. This means that even with strong heating, it does not lose its strength characteristics, which means it does not wear out or deform.
Designation Р6М5
Deciphering steel depends on how it is made, what alloying elements it includes and how much carbon it contains. There are designations for different types. If, for example, the alloy does not contain alloying elements, then it is designated "St" and next to it is a number that shows the average carbon content in steel (St20,Art45).
In low-alloy alloys, first comes the percentage of carbon, and then the letters denoting chemical elements (10KhSND, 20KhN4FA). If there are no numbers next to them, as in the example, then the content of each of them does not exceed 1%. The letter "P" in the grade of the alloy indicates that it is a high-speed cutting (rapid).
Following it is a number - this is the percentage of tungsten (P9, P18), and then letters and numbers are alloying elements and their percentage. From this it follows that the R6M5 high speed steel contains up to 6% tungsten and up to 5% molybdenum.
Annealing
As a rule, the production of such an alloy is classical and will be used for all high-speed steels. However, it should be borne in mind that in order for the tungsten-molybdenum alloy to be truly strong, hard and wear-resistant, it must be annealed.
If other grades, for example, St45, lose their properties of strength during annealing, then high-speed ones, on the contrary, improve and become stronger and harder. That is why P6M5 is annealed before hardening. How does it happen?
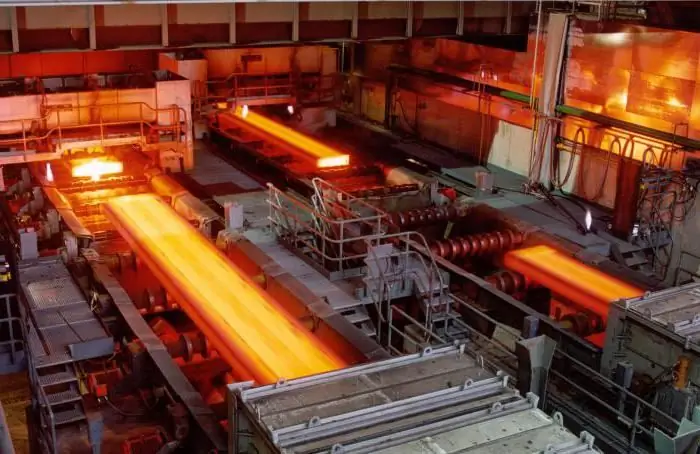
Rolled products (for example, R6M5 steel sheet) with a thickness of about 22 mm are heated in a special furnace to a temperature of 870 ° C, then cooled to 800 ° C, and then heated again. There can be about 10 such cycles.
In addition, after the fifth, it is necessary to gradually reduce the temperature. For example, heating again but up to 850 °C, cool down to 780 °C. And so on until it reaches 600 ° C.
Such a complex annealing process is due to the presence of grainsaustenite in alloyed alloys, which is highly undesirable. Heating and cooling allows the alloying elements to dissolve as much as possible, but the austenite will not grow.
If you do not withstand the temperature regime and anneal at a temperature of more than 900 ° C, then an increased amount of austenite is formed in the alloy and the hardness decreases. Cooling is recommended to be carried out using oil baths, this will protect the tungsten-molybdenum alloy from cracks and punctures.
P6M5 manufacturing method
Of course, like any other alloy, R6M5 is manufactured in various assortments. So, in some workshops, high-speed hot steel is poured into ingots. In another production, it is rolled with hot rolling. To do this, the heated ingots are pressed between the rolls of the rolling mill. Its resulting shape will depend on the shape of the shafts themselves.
R6M5 steel grade is widely used for parts operating at high temperatures. For this reason, powder-coated steel has become very popular lately.
When pouring hot steel into ingots, there is a very rapid release of carbides from the melt. In some areas, they form uneven areas of accumulation, which later become the site of crack initiation.
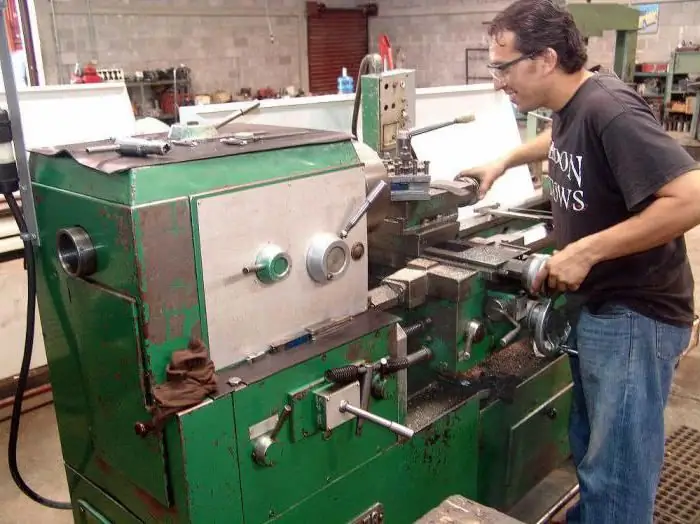
In powder manufacturing, a special powder is used, which contains all the necessary components. It is sintered in a special vacuum container at high temperature and pressure. This contributes to the fact that the material is obtainedhomogeneous.
Application
R6M5 steel is widely used in various industries. Most often it is used for the manufacture of cutting tools for turning, milling and drilling machines in metallurgy. This is due to its characteristics of strength, heat resistance, hardness.
As a rule, drills, taps, dies, cutters are made from it. The metal-cutting tool made of P6M5 steel is excellent for cutting at high speeds, moreover, it does not require coolant cooling. A knife made of R6M5 steel is also not uncommon.
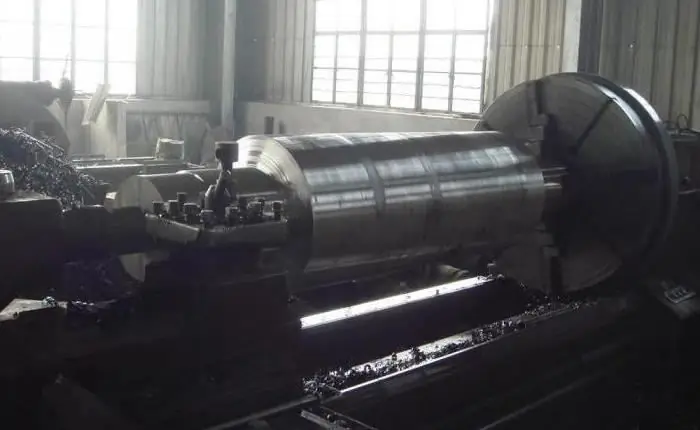
Because tungsten-molybdenum alloy has high hardness and high toughness, it is often used to make knives with strong handles and beautiful patterns.
Alloying elements in the required quantity allowed to create a unique steel that practically does not rust and has good grindability. This allows for locksmith work to increase the cutting speed by 4 times.
It is also used to produce heat resistant ball bearings running at high speed at 500-600°C. The analogues of the R6M5 alloy are R12, R10K5F5, R14F4, R9K10, R6M3, R9F5, R9K5, R18F2, 6M5K5. If tungsten-molybdenum alloys, as a rule, are used for the manufacture of tools for roughing (drills, cutters), then vanadium (R14F4) for finishing (reamers, broaches). Each cutting tool must have a marking that allows you to find out what alloy it is made of.
Recommended:
Food stainless steel: GOST. How to identify food grade stainless steel? What is the difference between food stainless steel and technical stainless steel?

The article talks about grades of food grade stainless steel. Read how to distinguish food stainless steel from technical
Corrosion resistant steel. Steel grades: GOST. Stainless steel - price
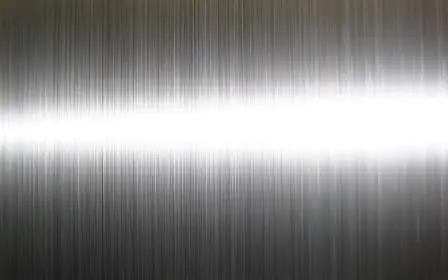
Why metal materials break down. What are corrosion-resistant steels and alloys. Chemical composition and classification according to the type of stainless steel microstructure. Factors affecting pricing. Steel grade designation system (GOST requirements). Application area
Steel grade R6M5: characteristics and application
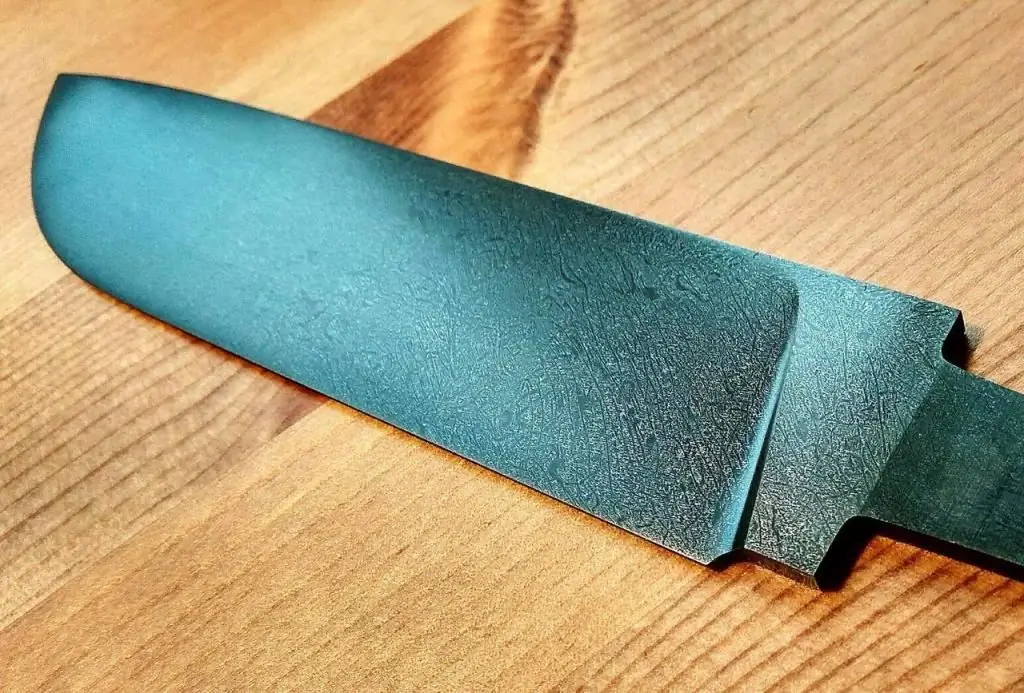
Before starting to create a knife, the master needs to clearly know all the features of the steel from which the final product will be made in the future. Each individual steel, with the exception of analogues, which will be discussed below, is unique in its composition, which means that its processing should be approached wisely. So, the focus of our attention is R6M5 steel, the characteristics and application of which we will describe in detail below
Characteristics of steel 65x13: properties, hardness. Reviews about knives made of steel 65x13
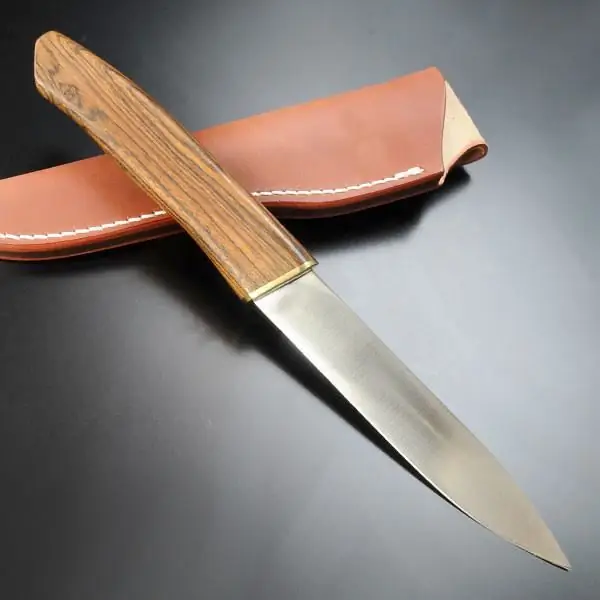
In modern metallurgy, a huge number of steels are used. Their characteristics, as well as the variety of nomenclature, are truly immense
440 steel - stainless steel. Steel 440: characteristics
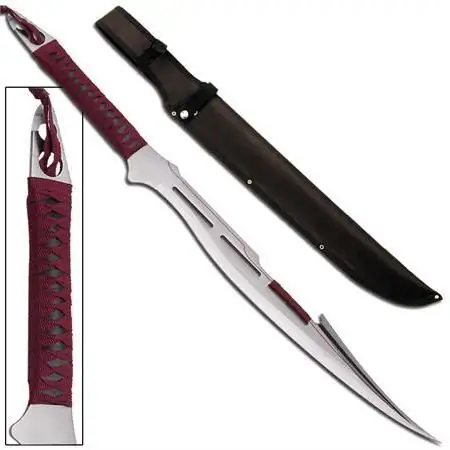
Many people know 440 steel. It has established itself as a reliable, anti-corrosion, time-tested hard material, which is most often used for the manufacture of knives for various purposes. What is the secret of this alloy? What are its chemical, physical characteristics and applications?