2025 Author: Howard Calhoun | [email protected]. Last modified: 2025-01-24 13:10
The technological process in which workpieces are processed, which makes it possible to obtain flat or voluminous finished products of various shapes and sizes, is stamping. The working tool for this purpose is a stamp, which is fixed on a press or other equipment. Stamping is two types of technology that, depending on the conditions, are performed in a hot or cold way, and therefore both equipment and technological standards differ from each other.
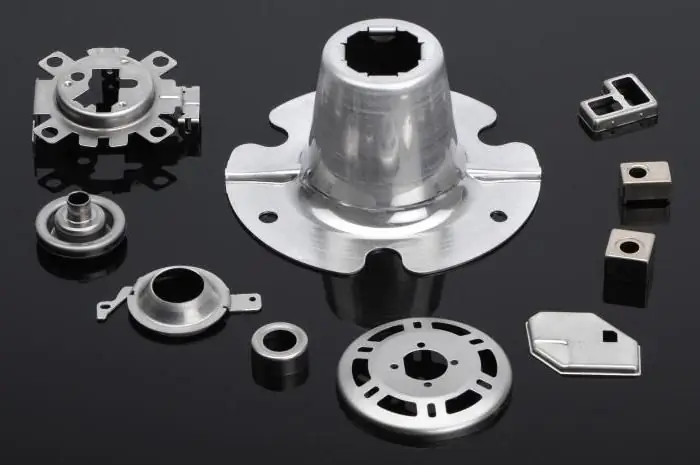
Categories
In addition to the division of technology into cold and hot methods, stamping is a whole series of categories into which material processing methods are divided. The chosen method most often depends on the purpose of the product, but the technological conditions also affect it. For example, there is a method in which part of the workpiece is separated, and this is separation stamping. This also includes punching, cutting, cutting parts. There is a category of operations when hot stamping is used, through which a sheet of metal changes shape. They are also called shaping. As a result, parts are subjected to bending, drawing and other procedures.
Cold and hot stamping are implemented using the same principle, which involves the deformation of the material, but otherwise the production of products by these methods has many differences. Preliminary heating of parts to certain (and rather high) temperatures is assumed mainly in large industrial enterprises, such as, for example, a metalworking plant. This is due to the complexity of such a technological process, a large number of operations, which can be performed qualitatively only with accurate preliminary calculation and compliance with the high accuracy of the degree of heating of the workpiece.
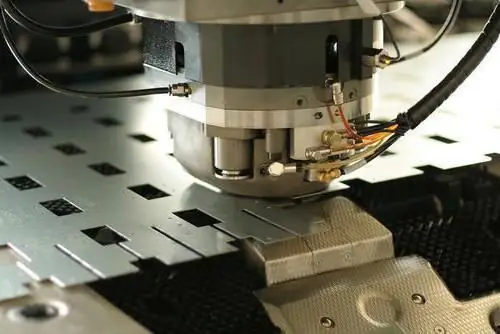
Hot way
Forged parts processed using hot technology must be of excellent quality, since, for example, such important things as boiler bottoms and other hemispherical products, including critical elements in shipbuilding, are made from sheet metal of different thicknesses. To heat a metal part, use equipment that provides the correct temperature.
These devices and furnaces can be plasma, electric or other, there are quite a lot of types. Before supplying a hot part to a stamping press, it is necessary not only to calculate the heating rate, but also to develop a detailed drawing of an already finished product, where it is necessarytake into account the shrinkage of the metal after cooling.
Cold forming
Cold stamping involves the formation of a product by means of pressure exerted on the workpiece by the working elements of the press. Such products are not subject to shrinkage, because they are not preheated. Further mechanical refinement of such products is also not needed after stamping is completed. Stamping methods can be different, but cold stamping is both more convenient and cost-effective.
Materials that lend themselves well to cold forming are not limited to carbon or alloy steels. Stamping production successfully works on both aluminum and copper alloys. The cold method is carried out mainly with the help of hydraulic presses, and their production is regulated by GOST. Serial models are very diverse, and therefore it becomes possible to choose a suitable machine for the production of any configurations and sizes of products. Dies for stamping metals are very different in their equipment from those that work with materials such as leather, rubber, cardboard, polymer alloys, and the like.
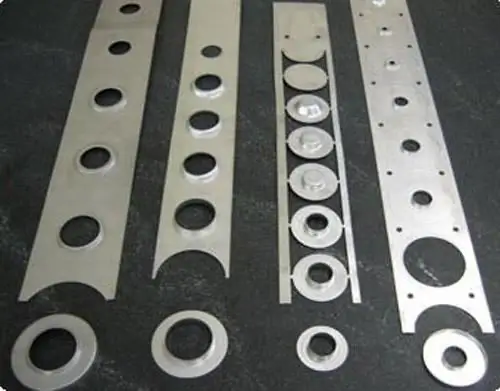
Separation Stamping
One of the most common technological operations is separation stamping, which separates a part of the metal from the workpiece. This method is used in almost all manufacturing enterprises. Special tools are installed on the stamping press, which produce cutting, punching and punching of the material. Through this processyou can separate metal parts even along a curve, even along a straight cut line. Cutting is performed by a variety of devices: guillotine shears, vibrating and disk machines, and the like. Cutting is used to cut blanks for further processing.
Punching is another technological operation. For example, a stainless sheet of metal needs to be turned into parts with closed contours. Sheet metal is provided with holes of any configuration using punching. It must be said that this technological process also requires careful preliminary preparation and a detailed plan, with the calculation of the geometric parameters of the tool that is used. Otherwise, a quality product may not work. There are a lot of technological operations related to stamping, because it is required to change the initial configuration of the parts. These are bending, forming, flanging, drawing and crimping.
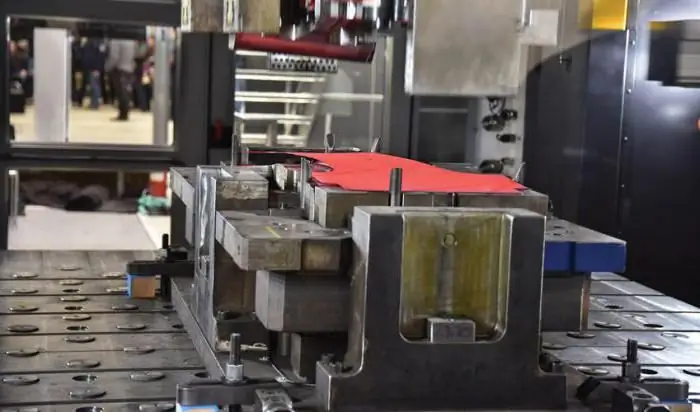
Technological operations
The most common operation that changes the shape of a part is bending, which forms planned sections with a bend on the surface of a metal workpiece. The hood is called volumetric stamping. This is an operation by which a three-dimensional product is obtained from such a flat metal surface, such as, for example, a stainless steel sheet. It is with the help of the hood that it turns into a cylinder, cone, hemisphere or takes on a box-shaped configuration. Sheet metal products must have a rim along the edge and around the holes, if they are made inside the workpiece. For example, flanging should completeend of the pipe to install a flange on it. This operation requires a special tool.
With crimping, the reverse action occurs. Flanging expands the ends of sheet metal blanks, and crimp narrows. The same ends of the pipes or the edge of the cavity require such an operation, which is carried out by means of a conical matrix externally. Molding is also one of the main operations related to stamping. It helps to change the shape of the individual elements of the stamped part, and the outer contour remains unchanged. Volumetric stamping requires the work of special equipment and complex preliminary drawings, and therefore is almost never implemented at home.
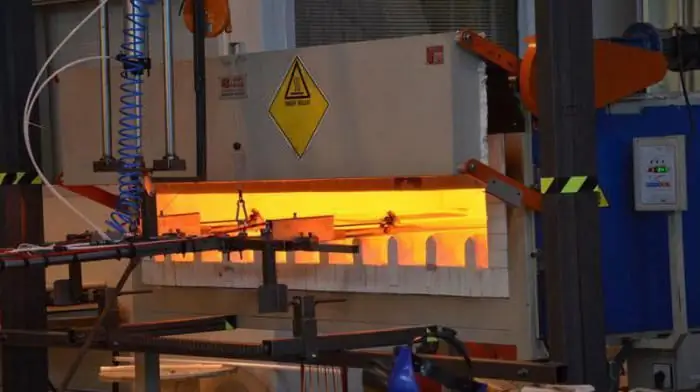
Select Abs
For the processing of metals, even the softest (for example, for stamping aluminum), special equipment is required: a hydraulic or crank press or guillotine shears. And of course, a lot of knowledge is needed. For example, how to calculate material consumption and complete technical drawings. The requirements of GOST are necessarily taken into account.
To choose the right stamping press, you first need to clearly imagine the task that he has to solve. Operations such as punching or punching require the use of single-acting punching equipment with little travel of the slider and washers during processing. But already for the hood, completely different, more powerful equipment is needed, where the slider and washers make a much wider stroke. This ability hasdouble acting equipment.
GOST equipment
Punching, depending on the conditions of the task, can be performed on equipment of the following types: one-, two- and four-crank. The latter - with the installation of large sliders. However, the equipment of the stamping press with a matrix does not depend on the design. The main work by means of movement is performed by a slider connected by its lower part to a movable stamp. And in order for the press slider to move, the drive motor is equipped with kinematic chain elements: a V-belt drive, a starting clutch, washers, a crank shaft, a connecting rod that regulates the stroke of the slider.
The slider is started using a foot press pedal, which is connected to the starting clutch, after which its reciprocating movements begin, directed to the work table of the press. The four-rod press has a different principle of operation. Its working bodies direct all the effort into the middle of the quadrangle, which is formed by four connecting rods. Such a device is successfully used for the manufacture of products of the most complex configuration: asymmetric or overall.
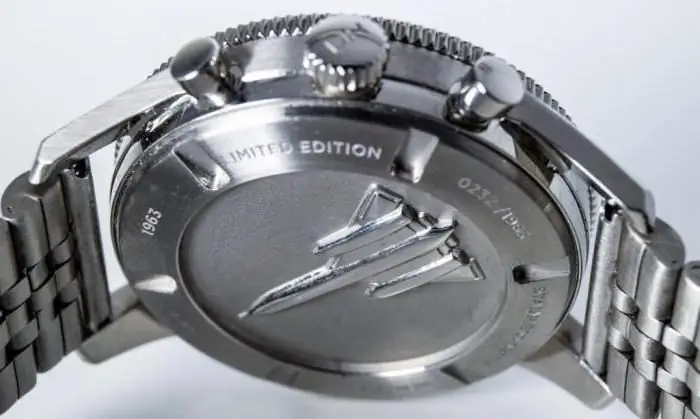
For complex items
To obtain high-quality products of complex configuration, a pneumatic type press with two or three sliders is very widely used. The double-acting press works with two sliders simultaneously: the outer one fixes the workpiece, and the inner one draws the surface of the metal sheet. Thin sheets of metal are stamped with special friction presses,and thick ones - hydraulic, which have more reliable washers.
A separate category of stamping equipment - stamping, controlled explosion. Such devices direct the power of the explosion to separate sections of a metal workpiece (usually of considerable thickness). This is innovative equipment, the work of which even on video looks very impressive. The folds and general configuration of a complex product are processed using the built-in vibrating shears.
Sheet Stamping
Sheet punching (for example, the manufacture of perforated sheet) involves the process of punching sheet metal. The rest of the stamping is volumetric. The equipment used for stamping equipment is divided into types. It can be instrumental, impulse (explosion, magnetic or hydraulic impulse), roll or stamping with elastic media. Sheet stamping can produce spatial and flat parts of various weights - from fractions of a gram, and various sizes - from fractions of a millimeter (here you can look at the second hand of a wristwatch). Sheet metal stamping also produces parts weighing many tens of kilograms and several meters in size (automotive cladding, rockets and aircraft).
They use mainly low-carbon steel for this, as well as alloy steel - with special ductility, brass, copper, aluminum and magnesium with alloys, titanium and much more. Sheet stamping is almost all industries: rocket, aircraft, tractor, auto, instrumentation, electrical industry, and so on, you can list everything. Its benefits are great.
3D stamping
Forging can be done both cold and hot. Hot - pressure treatment, where the shaping of the forging is carried out using a stamp. The blanks are rolled rectangular, round, square profile, which is cut into dimensional blanks (sometimes not cut, but stamped directly from the bar, then separating the forging directly with a stamping machine).
Forging is used in mass production and serial production, which increases labor productivity and reduces metal waste. The quality of products also meets high standards. Such stamping produces products that are extremely complex in shape, which cannot be obtained even by free forging.
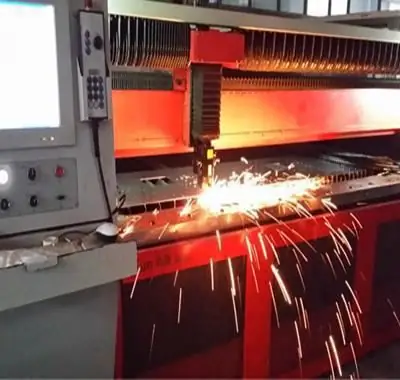
Dies open and closed
Open dies allow you to observe the gap between the fixed and moving parts of the machine. During hot stamping, flash flows into the gap - metal, closing the exit from the cavity and forcing the rest of the mass to fill the cavity completely. In the process of deformation, excess metal gets into the flash. But removing flash is difficult.
Closed stamps do not allow you to look inside and observe the process - the cavity is closed. The cover is also not provided. The device of such a stamp depends on the type of machine. Here it is necessary to strictly observe the accuracy of volumes and their equality in blanks and forgings: a lack of metal will leave the corners of the cavity empty, and an excess of it will make the forging more than the required height.
Recommended:
Foil stamping at home. Cold and hot foil stamping
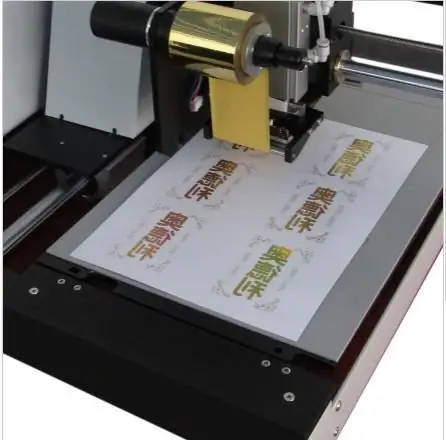
In order to make a gift or souvenir original and unusual, such an operation as foil stamping is often used. Also, using this printing technology, “wearable” leather items are often decorated, logos are applied to branded products, advertising panels are made, etc. If you wish, you can do embossing with thin metal yourself
Wood planing: types, equipment and process technology
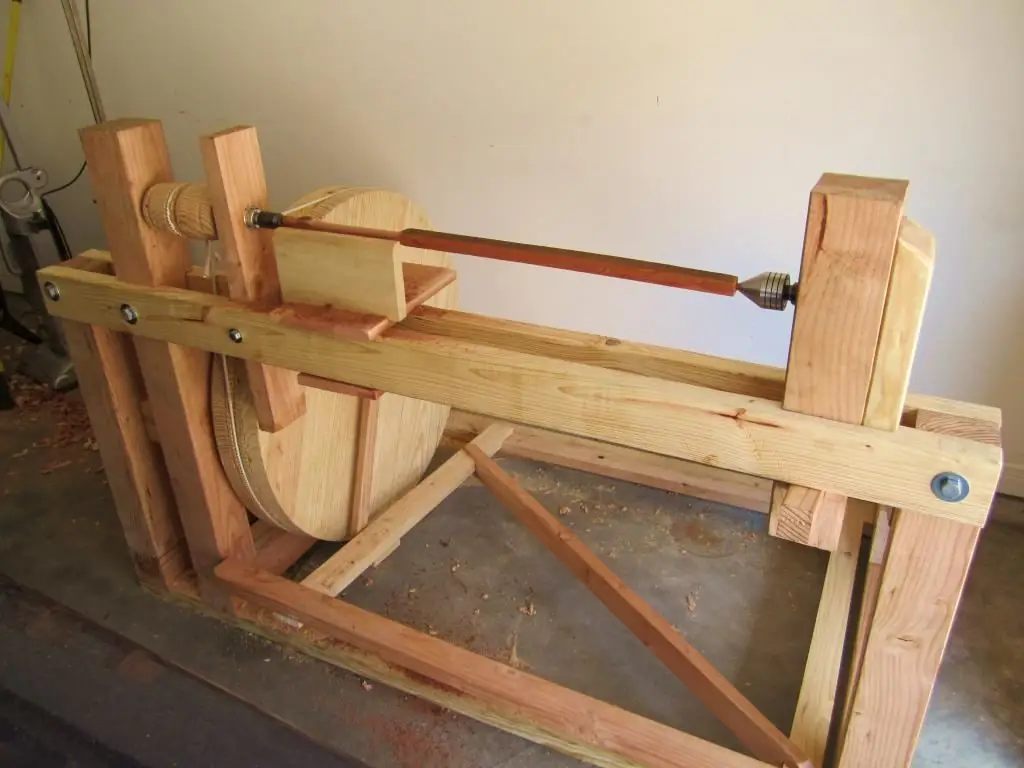
Wood planing is one of the types of processing of this material. This operation can be carried out both manually and on machines. It is important to understand that with the help of planing, any wood blank takes the desired shape and shape
Sheet stamping of parts: technologies and features of the process
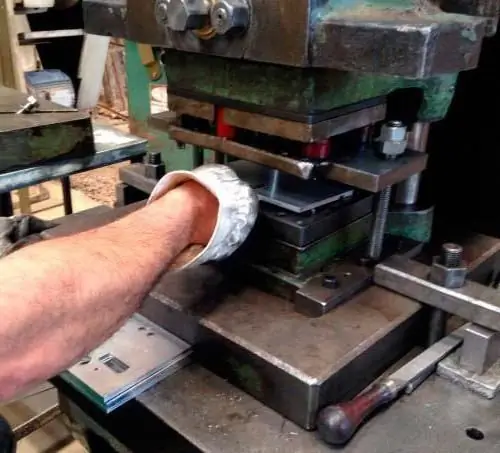
The article is devoted to sheet metal stamping. The features of this process, the advantages of the technology, the equipment used, etc. are considered
CNC machines for metalworking: overview, specifications, types and reviews
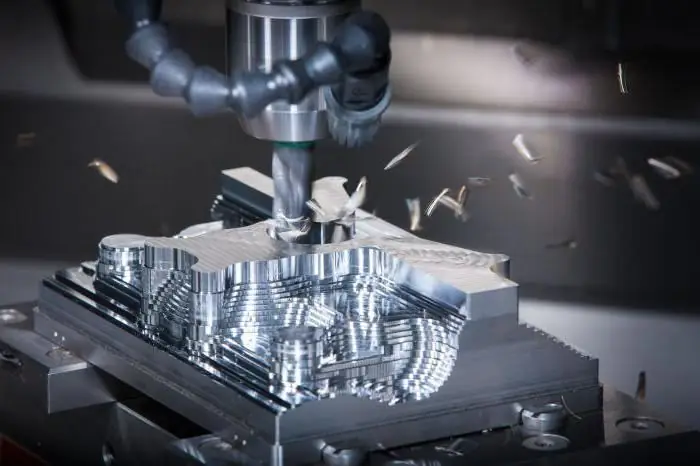
CNC machines for metalworking are used in almost every machine-building, pipe, repair plant. Modern cutting methods are intensive. The control systems are based on one service center, which is able to monitor the status of the working axes and the surrounding automation in real time. LCD screens provide information in a convenient 3D graphical format
Metal cutting with plasma. Metalworking equipment
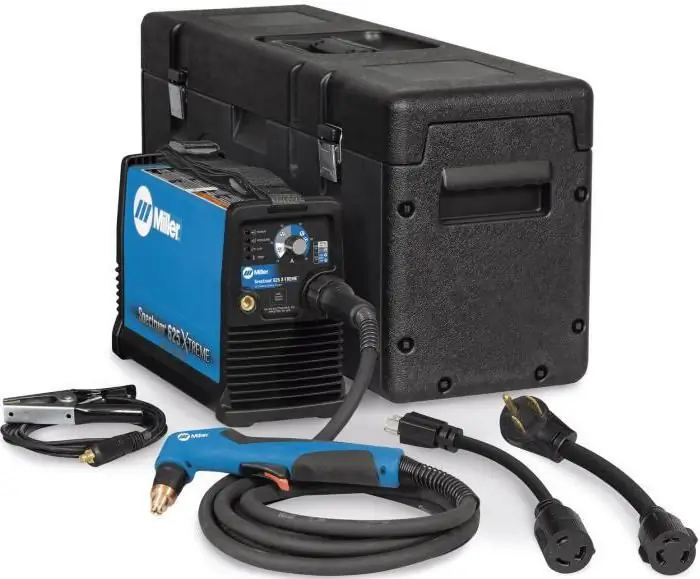
When buying a plasma cutter, you should always prioritize quality. Beware of the temptation to buy a cheap low-quality device, as its rapid wear and tear in the long run will lead to much higher costs