2025 Author: Howard Calhoun | [email protected]. Last modified: 2025-01-24 13:10
Heat treatment and firing at elevated temperatures with pressure are fairly common process steps in industry. In production, in this way, the strength and hardness of the material is achieved, which improves the performance of the future product. However, such operations require special equipment. This is a vast segment, in which industrial furnaces in various modifications occupy not the last place. They allow you to process the material under conditions of increased loads, while maintaining the original characteristics of their own design. Another important feature of such equipment is the ability to work with large volumes of materials. However, there are many options for ovens, each with its own capabilities and functions.
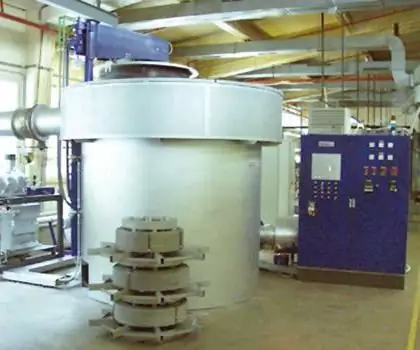
What are shaft-type furnaces for?
This is a kind of industrial furnace, which is designed for roasting, quenching and heating. Both raw materials and lumpy rocks, as well as bulk masses, can be used as blanks. In particular, such aggregates work effectively with carbonate rocks and ore materials. For metals, the shaft-type heat treatment furnacesuitable for maintenance of cast iron, aluminum and copper alloys.
For the efficient use of the capacity of such equipment, it is necessary to carefully calculate the volume of material to be laid. For example, the size of the fraction of lumpy material can be in the range of 60-120 mm. However, there are also industrial furnaces that can accept material with a diameter of more than 240 mm. This ability depends on the capacity of the chamber and the performance of the unit. Even if the equipment can physically accept an object with large dimensions, this does not mean that the camera will properly process it by thermal action. Therefore, the power characteristics of furnaces are initially compared with the qualities of the target material.
Shaft furnace device
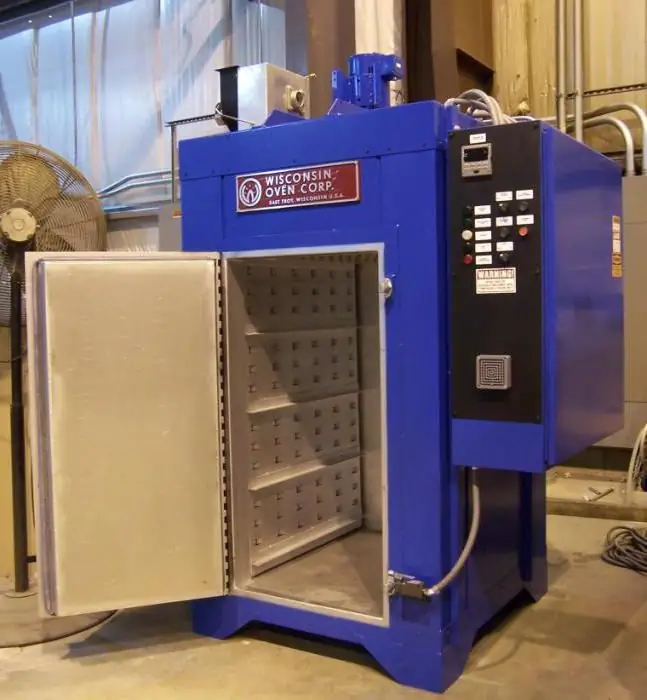
The basis of almost any shaft furnace is made up of four parts - loading and unloading blocks, as well as a chimney with a heat treatment chamber. Skip, tube and conveyor mechanisms are used to load raw materials. The choice of one or another design depends on two main parameters: firstly, on the characteristics of the material being fed, and secondly, on the operating conditions of the unit. For example, the skip system uses a reverse bucket and a winch, so it can be considered as a universal loading mechanism. The discharge device, which is supplied with the shaft furnace, also has several parts, but the main component is an intermediate container that seals and doses the material.
For withdrawalexhaust gases, a chimney is used in the form of pipes, which are most often located at the rear of the furnace. In modern models, this system often has a complex design with filters and an automatic control system. As for the combustion chamber itself, which is supplied with the shaft furnace, the main process of processing the incoming raw materials takes place in it. Using the control panel, the user adjusts the parameters of its operation in accordance with the requirements of the material manufacturing technology.
Working principle
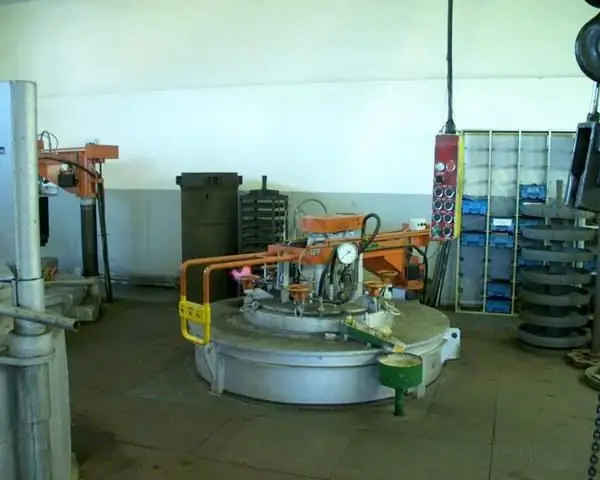
The function of such furnaces is based on the principle of countercurrent, in which the descending layers of raw materials are washed by oncoming gas flows. The processed material sequentially passes through several technological sections, including the drying zone, heating chambers, firing and cooling. In some models, the firing chamber coincides with the area in which the fuel burns. Hot gases are also formed here. The design in which the unit is made plays an important role in the efficiency of the process. If the shaft furnace is designed to work with large volumes of heterogeneous raw materials, then the distribution system comes to the fore in the choice of design. Most often, this function is performed by dividing cones, thanks to which the automatic process of filling the furnace is carried out.
Varieties of aggregates

There are several classifications that divide furnaces of this type into categories. In particular, according to the nature of the thermal effect, one can single out laboratoryand production units. If the former are rather focused on achieving high processing results, then for the latter, the intensity of the overall process and the capacity of the loading chamber are more important. Also, designs differ in the type of material used. If we talk about lumpy material, the equipment for the production of bricks is the most common in this segment. In different areas, units that work with fuel resources, ore and rocks, gas, etc. are in demand.
Mechanized and electric ovens
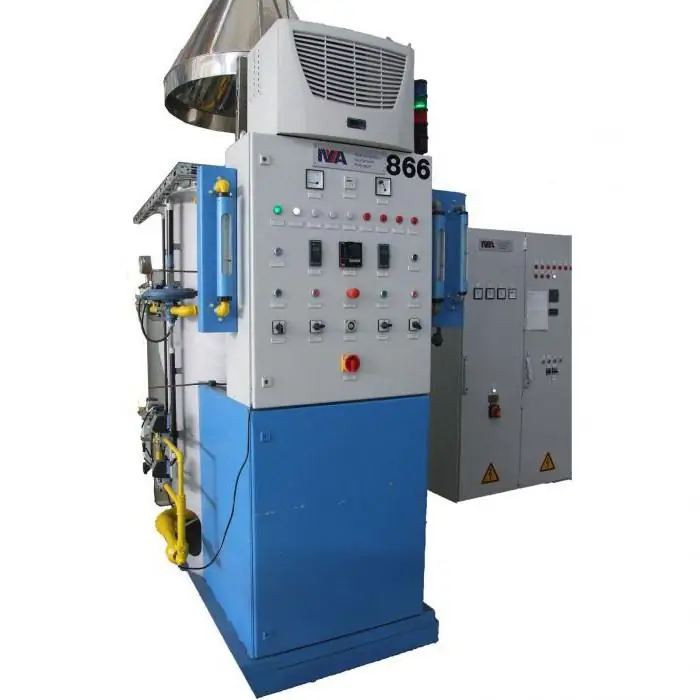
Most models of this type used in the manufacturing sector are powered by electricity. Their design includes a fan that circulates air masses, contributing to an increase in the intensity of heating. By the way, one of the main advantages of electrical units is the ability to regulate power. This option is especially useful when working with low density feedstock. For example, an electric lime kiln allows you to maintain basic quality properties by quickly changing the parameters of temperature exposure at different stages of processing. Mechanized units operate on a hydraulic drive system. The lifting and lowering of the lid in such equipment is carried out through compact mini-stations filled with oil.
Benefits of Shaft Furnaces
The operational advantages of such furnaces are determined by the design features. Nevertheless, there are common advantages that have led to the widespread use of suchaggregates. In particular, mine equipment for the production of bricks makes it possible to provide heat treatment of large volumes of clay raw materials in short periods of time. The ability to work with metals, gas, bulk materials and even waste allows us to talk about the versatility of such furnaces.
Conclusion
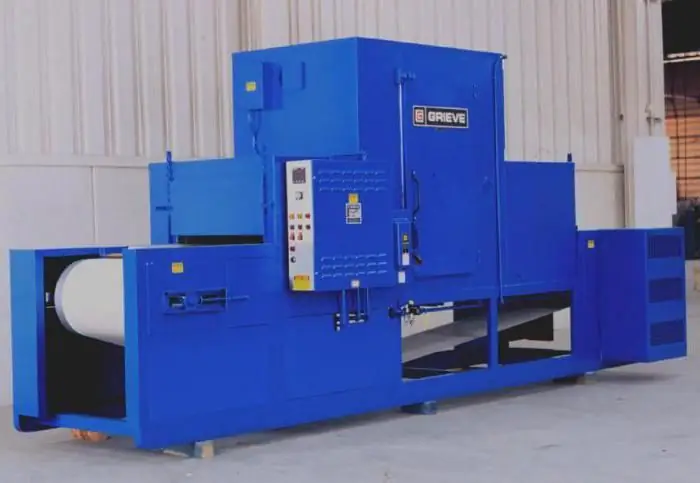
The process of technological modernization is most noticeable in industries and construction. The departure of old systems and mechanisms, which are being replaced by more functional and reliable analogues, is especially pronounced. However, the shaft furnace confirms that traditional equipment can compete with automatic and electronic developments. Of course, the introduction of individual elements of automation is inevitable, but the general principle of operation of such furnaces remains the same. The most popular models of this type are represented by hybrid units, which incorporate the best features of a classic design and advanced technological innovations.
Recommended:
Glass furnace: types, device, specifications and practical application
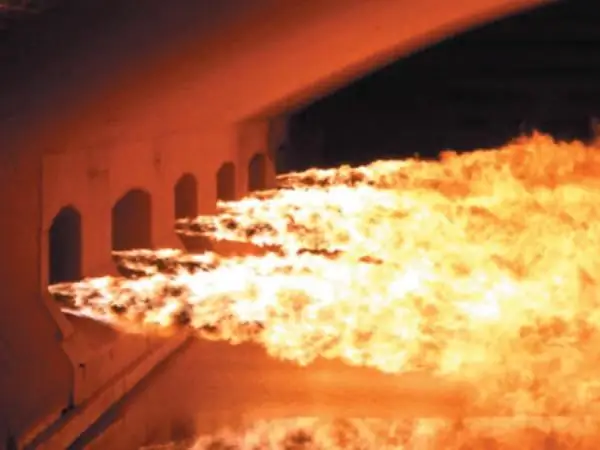
Today, people actively use glass for a variety of purposes. The glassmaking process itself is the melting of raw materials or charge. Glass melting furnaces are used to melt the material. They come in different types and are classified according to several criteria
Arc steel furnace: device, operating principle, power, control system
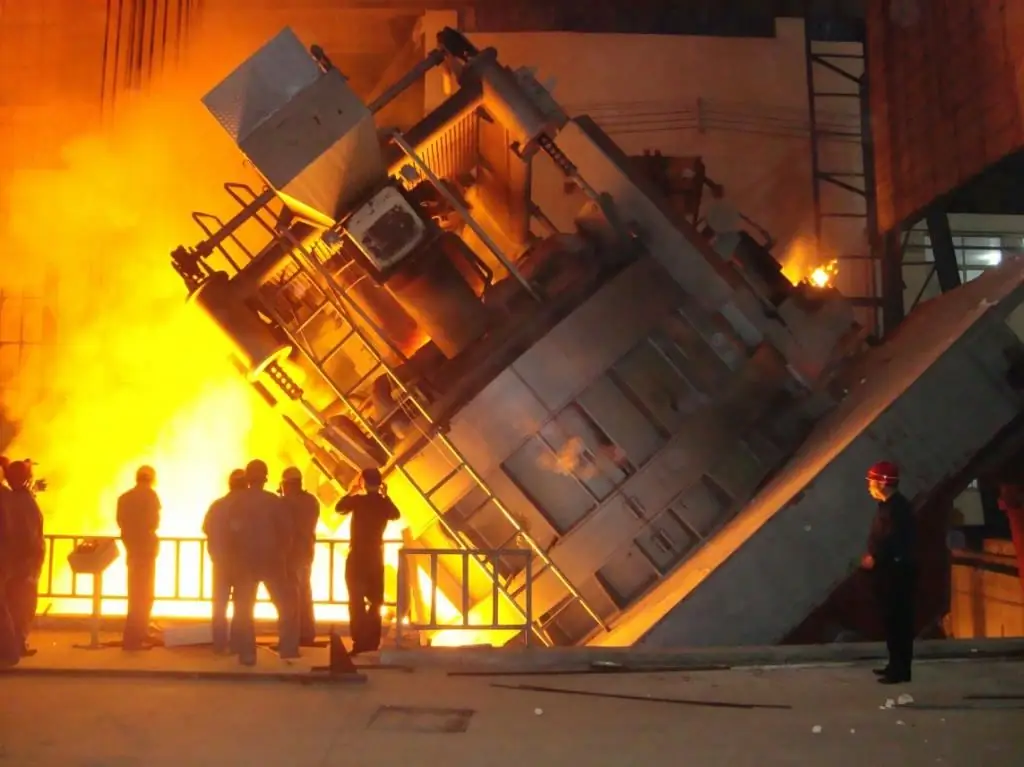
Arc steel-smelting furnaces (EAFs) differ from induction furnaces in that the loaded material is directly subjected to electrical bending, and the current at the terminals passes through the charged material
Voskhod baking ovens - types, characteristics
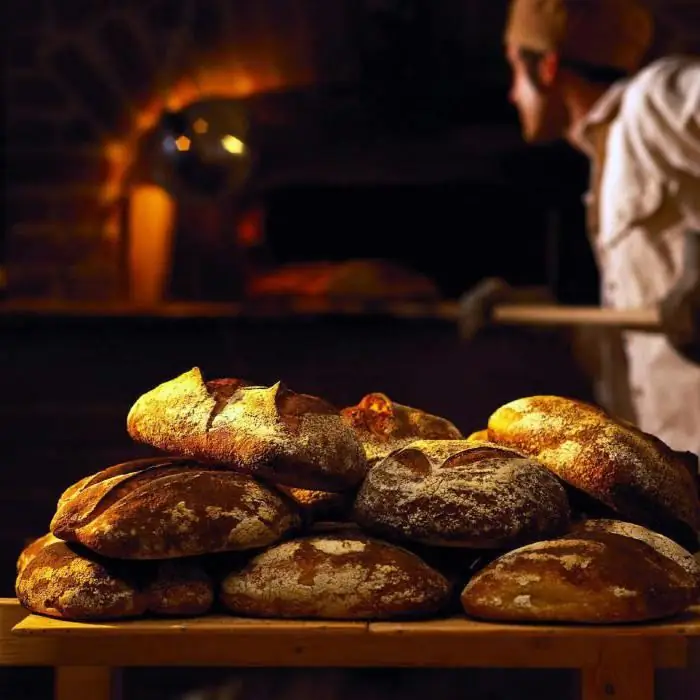
Among Russian manufacturers of industrial equipment for bakery production, the Voskhod brand from Saratov stands apart. Its assortment is wide enough to have something for a small "home business" bakery and for large-scale production. We will devote this article to the thermal equipment of the Saratov manufacturer
Shaft alignment of electrical machines: features, fixture and device
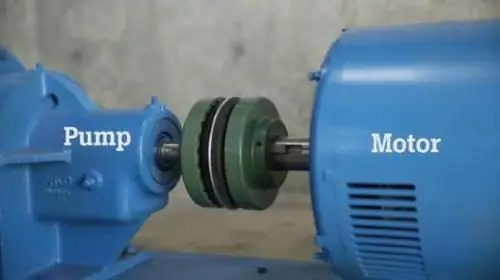
Misalignment of machine rotors is a common defect that can be corrected. To do this, it is necessary to know the factors affecting it and the methods of shaft alignment. Shaft alignment is usually carried out by concentric and parallel installation of the end surfaces of the coupling halves using special devices
Shaft grinding: technique, necessary materials and tools, step-by-step work instructions and expert advice
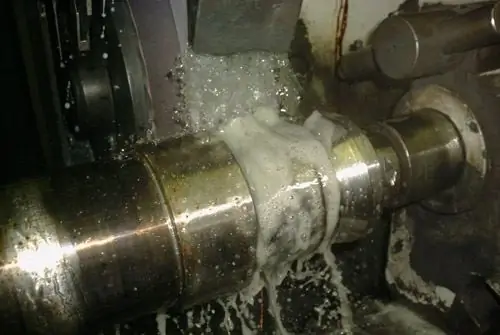
Today, shaft grinding is quite widely used in such an industry as mechanical engineering. This operation allows the preparation of parts that will have a small roughness, a slight deviation from the shape, etc