2025 Author: Howard Calhoun | [email protected]. Last modified: 2025-01-24 13:10
Today, people actively use glass for a variety of purposes. The glassmaking process itself is the melting of raw materials or charge. Glass melting furnaces are used to melt the material. They come in different types and are classified according to several criteria.
What is a charge?
It is important to note here that the glass melting process is already one of the last stages of production. The charge coming as a material for manufacturing is already enriched raw material. Of the main elements, this includes quartz sand, soda, limestone. Dyes, illuminators or darkeners are used as additional impurities. In addition, the charge that enters the furnace has the right percentage of moisture, the required consistency and mass uniformity.
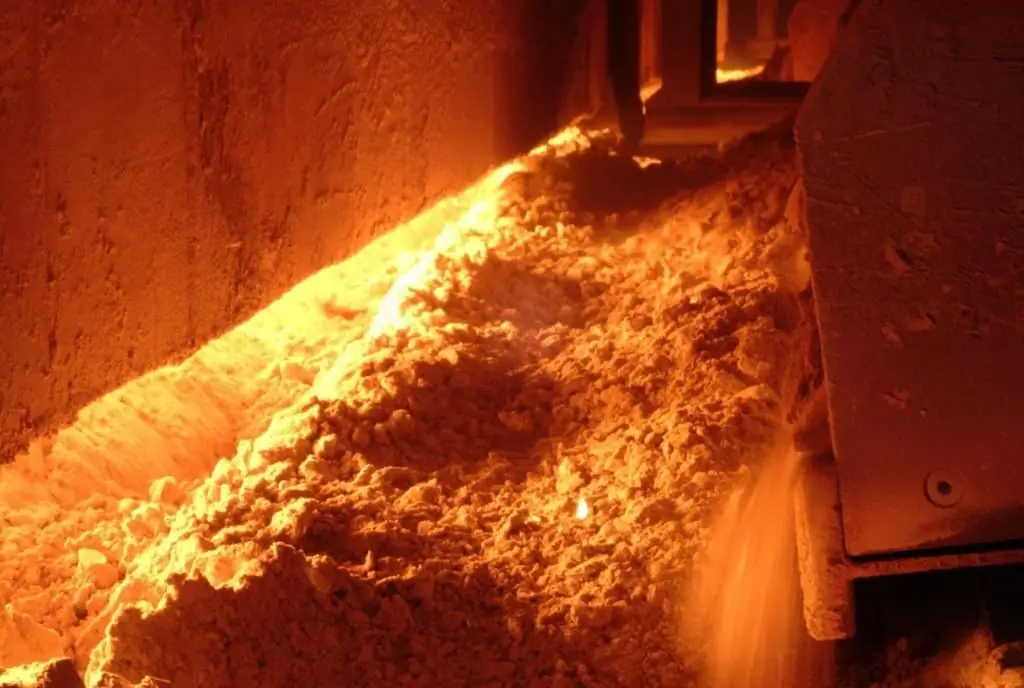
Features and device of the furnace. Pool
Glass melting furnace is a special device designed to melt charge. Gas can be used as fuel, solid fuel can be burned, and there are also electric furnaces. CostsIt should be noted that despite the variety of types, all furnaces have approximately the same device. The main elements of the glass melting furnace are the pool, vault and flame space.
The pool consists of a bottom and sides. It carries out batch cooking, material clarification processes, cooling, and direct production of glass mass. If we talk about the classification of glass furnaces according to the arrangement of the pool, then there are systems with a common pool. They do not have division into several zones. There are also completely opposite pool arrangements with clearly demarcated sections. Such baths have a zone where cooking and lighting work takes place, and it is called heated. The zone with cooling and working out is called working out.
In the heated part of the bath of the glass melting furnace there is a fiery space located between the walls and the vault. It is characterized by the presence of holes for the supply of fuel and air, as well as for the removal of hot gases that occur during the combustion of fuel.
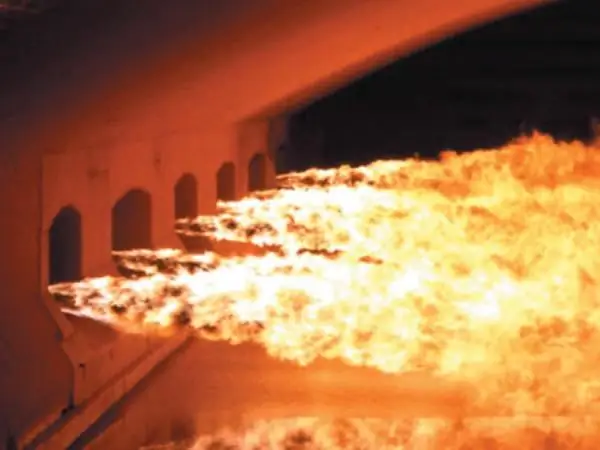
Bathtub laying and precautions
When building glass melting furnaces, special attention must be paid to the vault of the bath. It must be made of a special refractory brick called dynas.

A suitable brick can only be one that is at least 93% composed of a material such as silica. The thickness of the walls of the bath should be 500-600 mm, and the thickness of the vault 300-450 mm.
Due to the fact that the cooking processcharge in glass furnaces passes under the influence of very high temperatures, then during this process a variety of chemical reactions will occur, accompanied by the release of harmful steam. This led to the fact that one of the main precautions was the complete sealing of the interior of the furnace. In addition, in the shops where the glass-making equipment is located, a special ventilation system should be equipped to remove all harmful impurities and other products of fuel combustion from the air.
Speaking of ventilation systems, it should be noted that a similar smoke exhaust design should be installed in the furnace itself. The difference between conventional ventilation and modular ventilation will only be that the modular one is designed to maintain the required air composition inside the equipment.
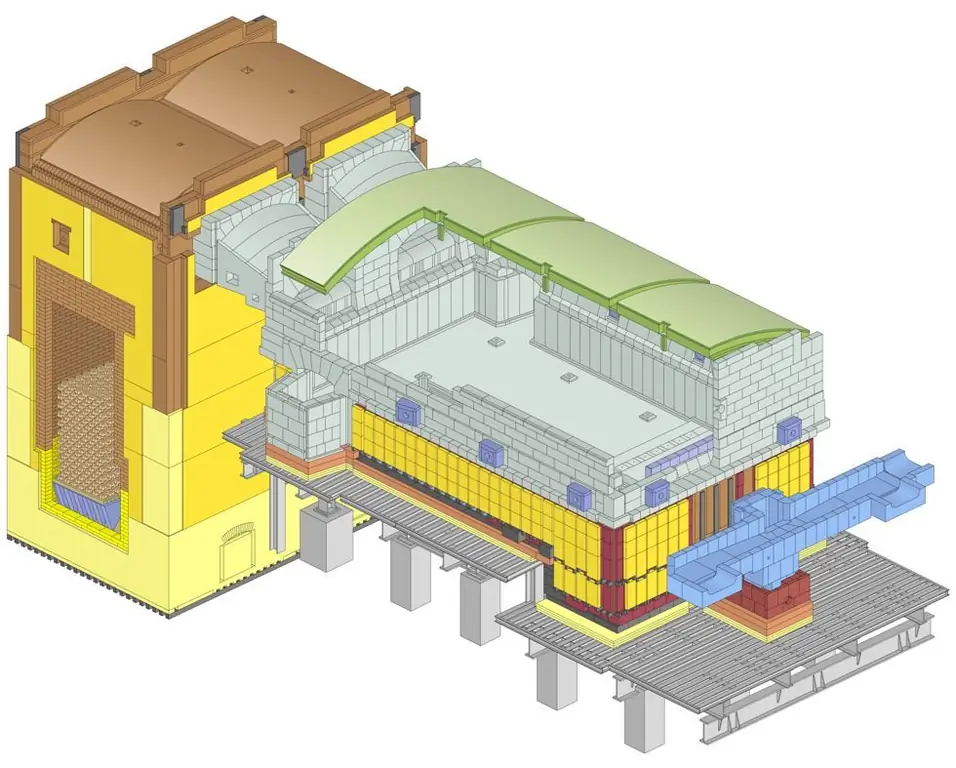
General description of oven types
Here it is worth starting with the fact that there are 2 classifications of ovens.
The first of them divides all cameras into two categories depending on the device of the working camera. These can be pot glass furnaces or bathtubs.
As for the second classification method, here the main criterion was the method of heating the glass. In this case, there are three main types - flame, electric and gas-electric methods.
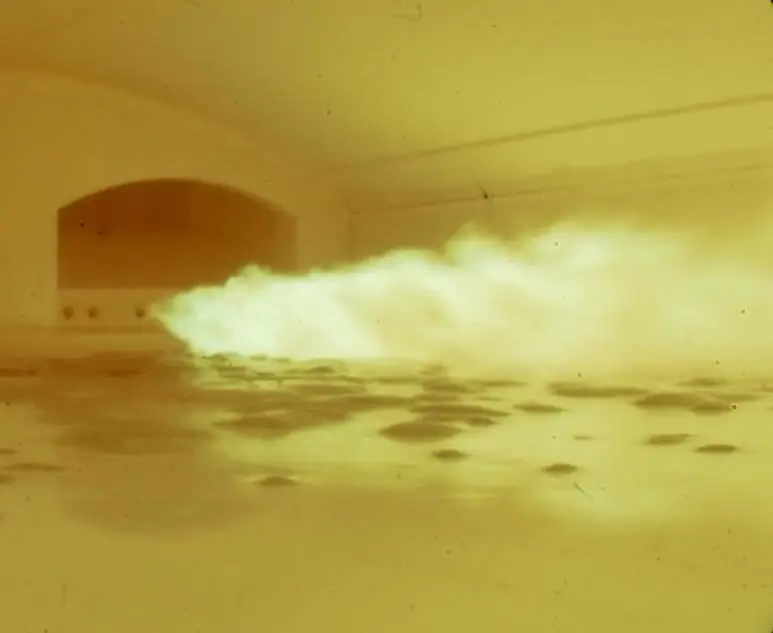
potty and bath equipment
Potting equipment is currently considered unprofitable. This is because this type of ovenrefers to intermittent devices. Because of this, a large amount of heat, and hence fuel, goes first to kindling the furnace itself, and only then to melting the charge.
Bathroom glass melting furnaces, unlike pot furnaces, are continuous devices. Naturally, a continuous process completely solves the problem of wasting resources on periodically heating the furnace, consuming fuel only for melting raw materials.
The bathtub by the stoves itself is a huge reservoir filled with molten tin. Due to the fact that the density of the glass mass will be significantly lower than the density of this metal, they will not mix with each other, being in the same container. Tin itself is used in furnaces for the gradual cooling of glass mass from a temperature of 1600 degrees Celsius to 600. This method and material were chosen due to the fact that during cooling this method does not create internal stresses in the mass. Their occurrence will negatively affect the quality of the finished product, and therefore they should be avoided. It is also worth noting here that the glass mass is distributed evenly, allowing you to get a perfectly even sheet.
Another advantage of using tin is the thermal polishing process during cooling. This process improves strength and clarity.
Flame Smelting Furnaces
This type of furnace is considered the first and in it glass melting is carried out by burning solid fuel. It should be noted here that the generated heat will be spent not only on heating the charge, but also on boilers for cooking, then the coefficientuseful action will be low. Flame furnaces have an efficiency of 25-30%.
Electric units
If we talk about efficiency, then today the first line will be occupied by electric furnaces. Their efficiency reaches 60%, which is considered the highest figure to date. This is achieved due to the fact that electricity will be transferred directly to the glass mass itself, heating it. Thus, it was possible to avoid unnecessary waste of energy for heating boilers and other things.
The principle of operation of this device is based on the fact that at high temperatures glass is capable of conducting electric current. In this regard, depending on the method of heat transfer to the mass, three types of electric furnaces are distinguished: induction, arc, direct and indirect resistance.
However, this type of equipment has a drawback, which is the need for a reliable and constant source of cheap electrical energy.
Electrodes are used to transfer electrical energy to the pool where the melting charge is located. It is because of the difference in resistance that heating occurs, and subsequently the melting of glass mass. As for the electrodes themselves, they are usually made of graphite. This material is less susceptible to deformation under the influence of high temperatures.
Gas-electric ovens
This type of device combines the principle of operation of the previous two. Gas is used to heat the chamber and primary melting of the charge; liquid fuel is used much less frequently. To heat and melt the glass mass itself, it will be usedthe principle of electrical resistance. Most often, such furnaces are used if there is a need to increase the efficiency of a conventional flame furnace, but there is no source of cheap and constant electrical energy.
At the end of the classification, it is worth adding that there are horseshoe-shaped glass furnaces. The direction of flame movement in such equipment may differ, and on this basis there are three small categories of devices, which include horseshoe-shaped ones. Their peculiarity is that they are used when necessary to produce mineral and glass wool.
Equipment repair
In the manufacture of glass, furnaces are subject to quite a lot of wear, and therefore the issue of their maintenance is quite relevant. Glass furnace repair can be of three types: current, hot and overhaul.
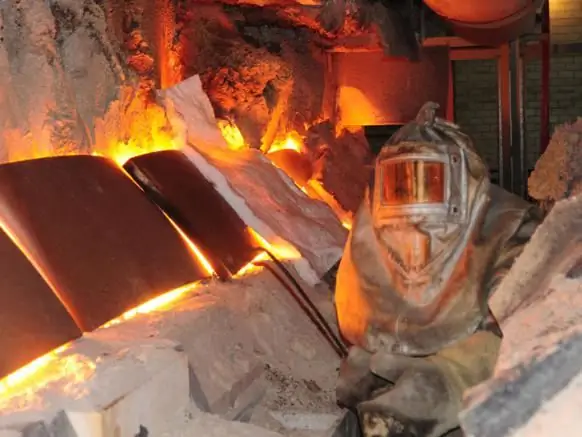
As for the current repair, it is quite simple and consists in replacing some nodes and some elements of the bath vault.
Hot type of repair is carried out without stopping the production process. Before proceeding with the work itself, it is necessary to stop the supply of flame to the heated chamber. After that, it becomes possible to replace many elements on which the first signs of damage appear. This allows you to significantly increase the period of use.
Cold, it is also a major overhaul, carried out within the time frame stipulated in the production plan. It got its name due to the fact that it is carried out only after a complete stop of the equipment, a cessation of heat supply andremoving all glass from the bath.
Major repairs
First, you need to stop the supply of charge. Stop supplying raw materials to the pool for melting glass should be 8-10 hours before it stops. After that, glass mass is introduced, heated to 1500 degrees Celsius (this increases its fluidity), and removed through special channels. This glass melt goes through a granulation process and can be used as a recyclable material in the future. Be very careful when turning off the burners. The temperature should change gradually, as its sharp drop can cause the destruction of the arch. Repair work is started only after all these actions and only after the furnace has cooled down to 100-150 degrees Celsius.
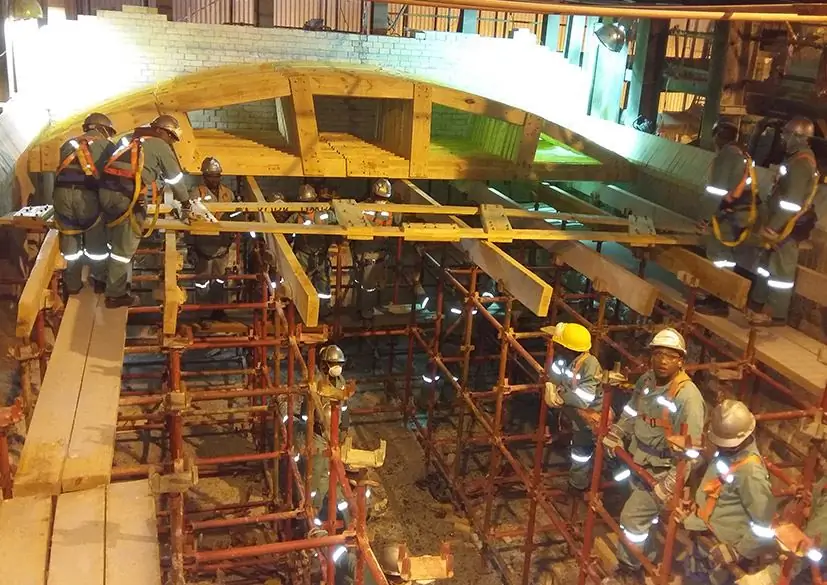
Typically, during a major overhaul, all damaged masonry sections are removed, refractory bars and bricks are replaced as needed. During the overhaul, the roof of the furnace regenerator is also being repaired.
Level control
For bath furnaces it is very important to maintain a constant level of glass mass, as they belong to continuous devices. Level fluctuation will negatively affect the quality of the finished product, as well as cause some other detrimental effects. For this reason, it is necessary to install equipment that controls this indicator. As measuring devices, you can install float, pneumatic, optical level gauges to control and regulate the levelglass mass in a glass melting furnace. Electrical installation of appliances should only be carried out by highly qualified specialists.
Recommended:
How to make glass? Glass production technology. glass products
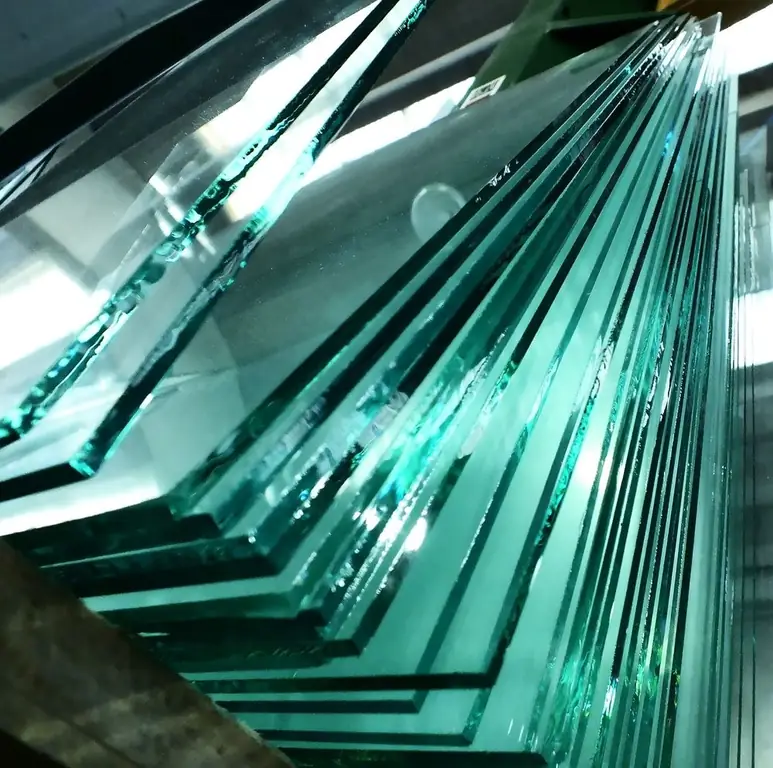
Glass is familiar to everyone. But the process of making it is extremely exciting. Each stage is important and affects the quality of the final product. The basis is sand, soda, lime. The process is almost entirely automated. Surprisingly, glass can even be made at home
Arc steel furnace: device, operating principle, power, control system
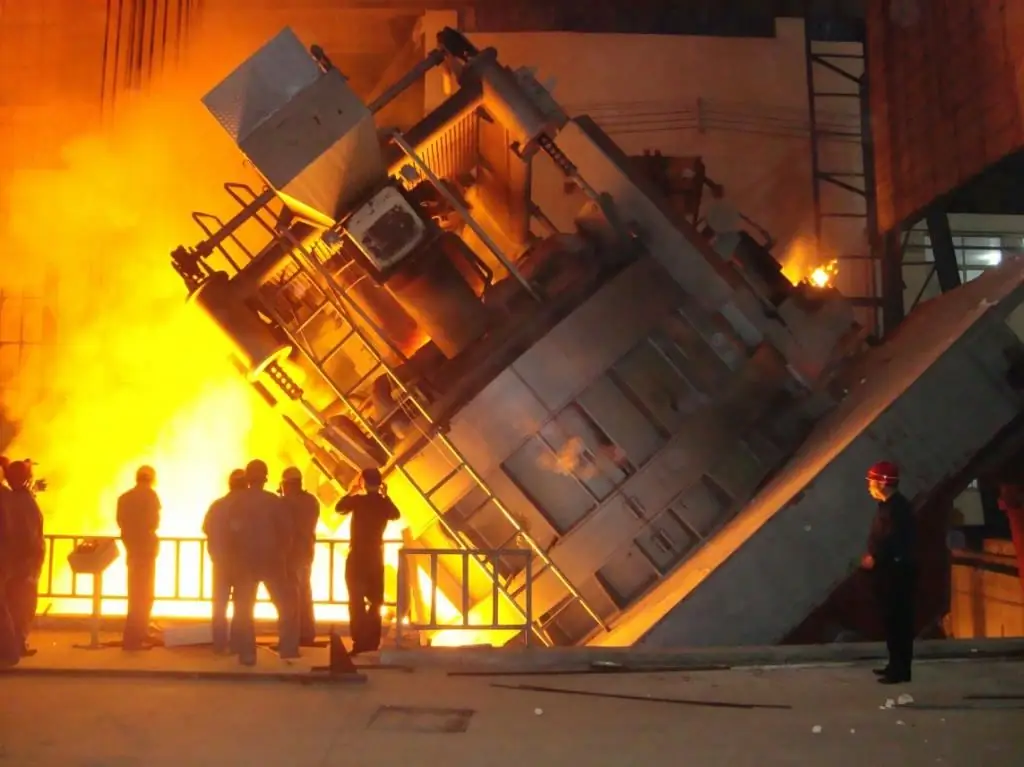
Arc steel-smelting furnaces (EAFs) differ from induction furnaces in that the loaded material is directly subjected to electrical bending, and the current at the terminals passes through the charged material
Glass sandblasting: glass processing description, equipment, application, photo
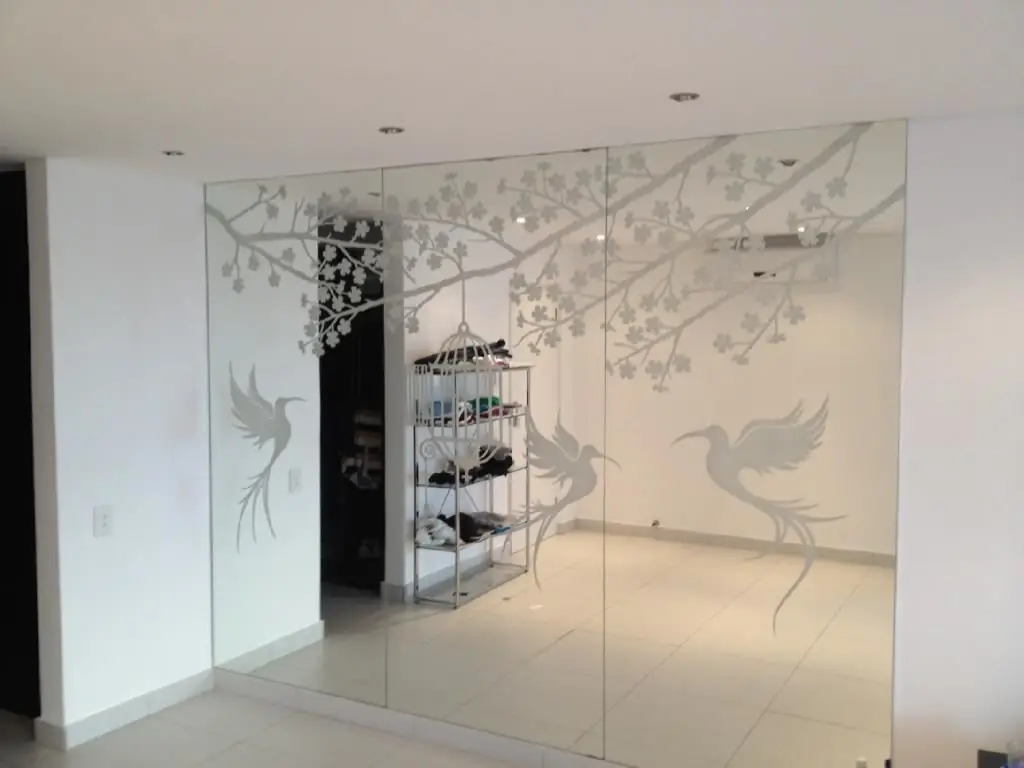
Among the numerous variations of interior decoration, sandblasting of a glass or mirror surface occupies a special place. This technology involves exposing the canvas to sand or other abrasive with a jet of compressed air released under high pressure. As a result, the surface changes and becomes matte, rough, velvety or painted with patterns. In the article we will consider what is sandblasting glass
Hydraulic stations for presses: types, specifications, purpose and practical application
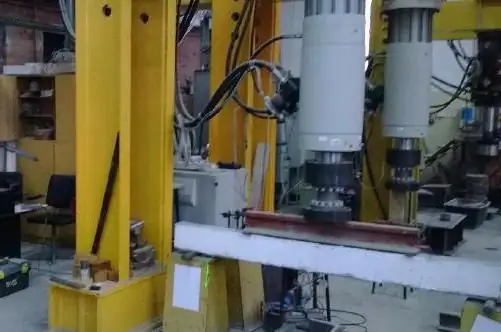
Hydraulics is one of the oldest mechanisms in the operation of power equipment. The simplest representative of this type of units is a press. With its help, large compressive forces are provided in various industries with minimal organizational and operational costs. The quality of operation of the device will depend on which hydraulic station is used for the press - whether it meets the target design in terms of working properties and whether it is able to maintain sufficient force
Artificial leather is The concept, types, differences from natural, manufacturing features and practical application
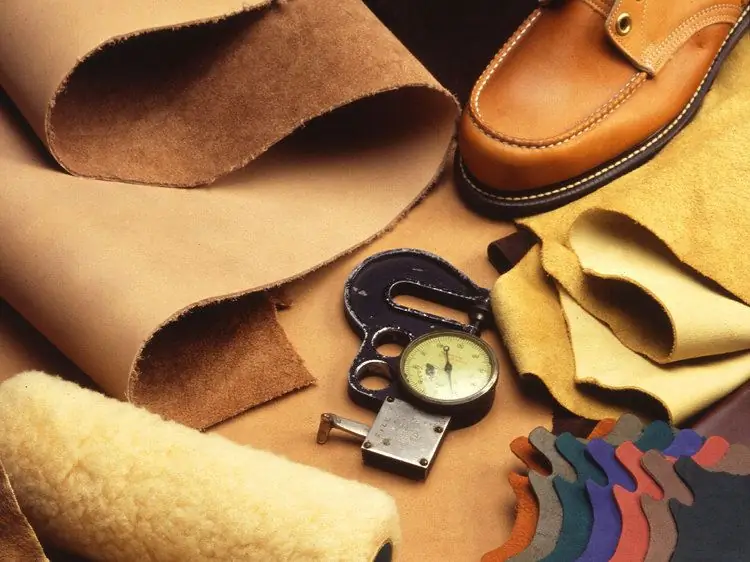
Artificial leather - what is used in the manufacture of clothing, accessories, furniture upholstery and more. This is a polymer material, the properties of which allow it to be used in almost any field. Haberdashery products are beautiful, of high quality and last as long as things made from natural fibers