2025 Author: Howard Calhoun | [email protected]. Last modified: 2025-01-24 13:10
Modern designers' quest for perfection has enabled manufacturers and processors to introduce methods such as sandblasting glass and mirrors. This method is not too complicated and does not require highly skilled workers.
What is sandblasting?
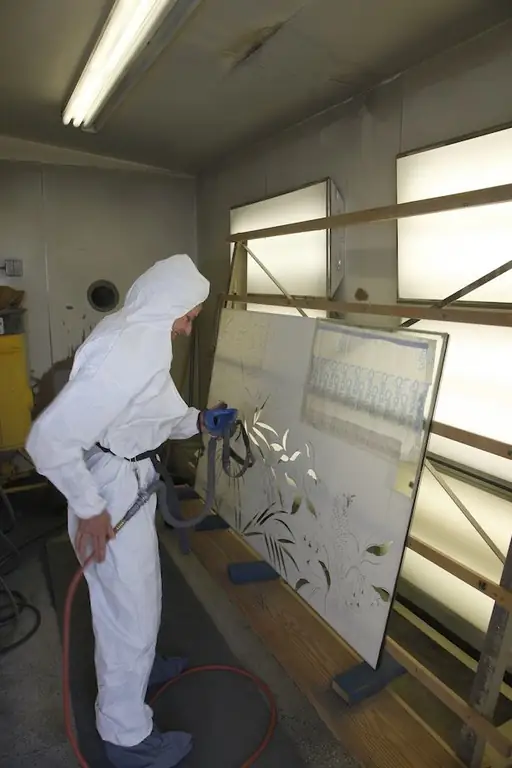
There are a huge number of methods and ways of processing glass. Manufacturers and processors are constantly changing and improving something. One such method is blasting the glass surface with high-pressure sand, the so-called glass blasting.
This method was invented almost two centuries ago. While in the desert, the military noticed that after sandstorms, matte marks remain on the glass, which do not wash off and do not disappear with time. This method was later patented and widely used.
The essence of glass sandblasting is the supply of sand under pressure through special nozzles - nozzles - onto the surface of the glass blank. As a result, its particlesleave small notches on the surface of the product, while not destroying the format completely. Modern equipment is used to produce beautiful designer products and the so-called frosted glass.
Glass sanding
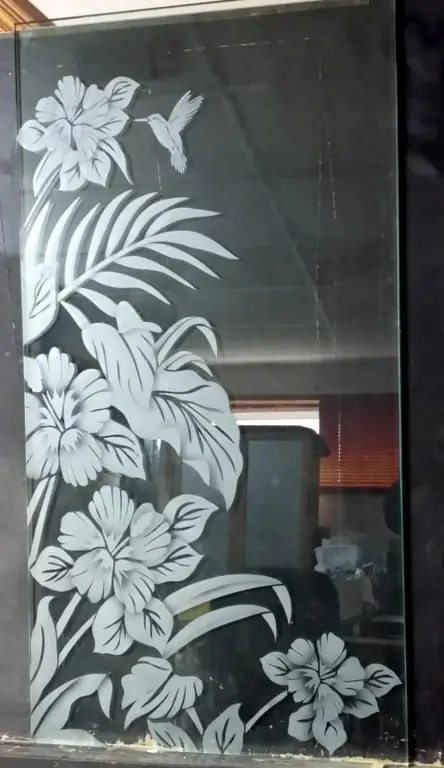
Glass blasting is carried out on specialized equipment. The work is performed by specially trained qualified personnel. Glass frosting, as the sandblasting operation is sometimes called, consists of several stages, each of which requires the use of special glass sandblasting equipment.
The first step is to prepare the material before processing. The workpiece is cut according to the dimensions stated by the customer. After cutting, it is washed from the remnants of carving oil and glass crumbs that occur during cutting and breaking.
Now the workpiece is processed on a belt machine. The device consists of two tapes rotating in different directions. During processing on such a machine, a thin layer is removed from the edge of the glass. As a result, the edge stress that occurs when cutting glass is reduced. This is done so that during sandblasting glass, the workpiece does not burst in the machine. Glass is a very fragile material and must be handled with the utmost care.
After processing on a belt machine, the workpiece is washed again and sent to a glass sandblasting machine. The operator, before starting processing, selects the intensity and size of the sand fraction, depending on the task and thicknessglass, as well as the size of the workpiece itself.
Passing through the chamber of the sandblasting machine, the glass is gradually treated with sand under pressure. Grains of sand evenly leave notches on it. Thus, complete coverage of the workpiece with matte risks is achieved. In some cases, after processing, the glass is coated with a special compound so that the coating does not get dirty during operation.
Sand processing of mirrors
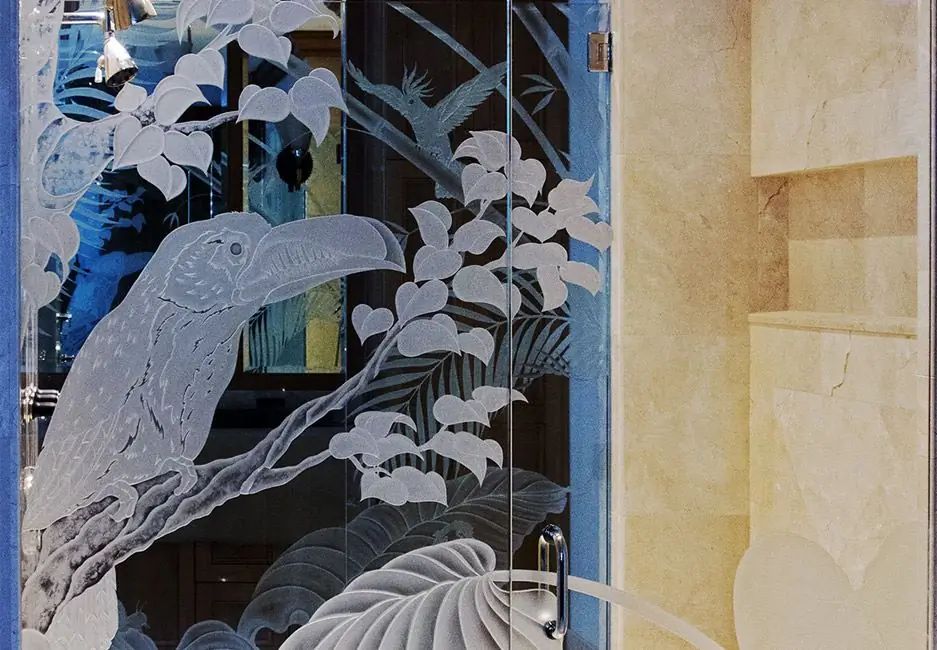
Sandblasting mirrors is not much different from glass. The workpiece is also cut to certain dimensions from the side that does not contain amalgam. After cutting, washing is carried out from foreign impurities. Work must be done carefully so as not to damage the coated side. Often, edge processing is carried out by a special method - facet, when at a distance of up to 2 cm to the edge of the mirror, the thickness of the workpiece is narrowed. This gives the product an aesthetic look.
Mirrors are matted only according to certain patterns described in the task. A film is glued onto the workpiece, on which a pattern is cut out. Full matting of mirrors is not produced - it's pointless. On mirror surfaces, a variety of patterns or pictures are usually applied to match the interior design.
Pros and cons
Sandblasting glass has its advantages and disadvantages. Benefits include:
- the ability to apply various types of patterns, the use of color processing;
- durability of use of the coating (it is not exposed to externalimpact);
- speed of processing (most of the time it takes the choice and application of a stencil), usually no more than 15 days;
- possibility to process the coating with modern means that protect against various types of pollution;
- compatibility of image types with the surrounding interior.
The main disadvantage is the difficulty in training and recruiting personnel to work on glass sandblasting equipment.
Sanding equipment
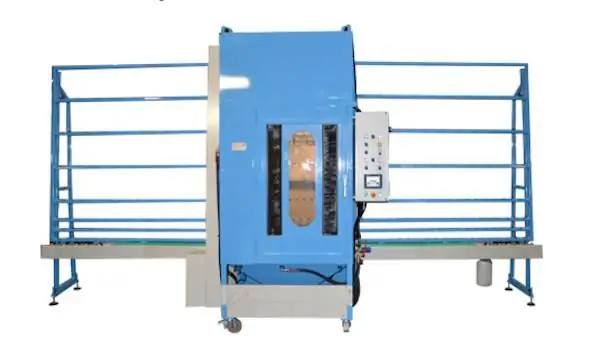
Machines, or as they are called - sandblasting chambers, are very easy to operate. They are a vertical machine with a compartment in which processing takes place. Inside it is a conveyor line for stretching the workpiece and vertically moving one or two guns with a boron carbide nozzle. This alloy is especially strong.
The sand container is under pressure. The air pressure is adjusted depending on the processing conditions and the thickness of the glass. The fraction of grains of sand also changes depending on the degree of processing depth. The equipment is filled with quartz sand. In some cases aluminum oxide is used.
Application
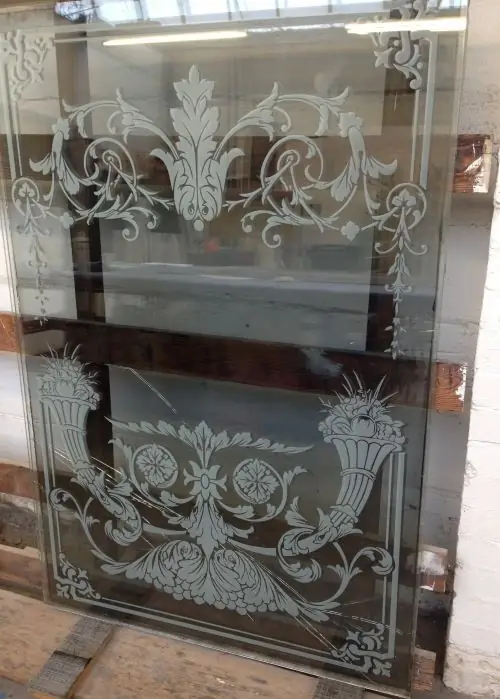
Price per 1m2 Sandblasted glass and mirrors are not very high. This allows you to widely use this processing method when decorating the interior in apartments and non-residential premises. Frosted glass and patterned mirrors are often used in offices and otherrooms where full matting of partitions and ceilings is necessary. Modern glass showers are also sandblasted.
Recommended:
How to make glass? Glass production technology. glass products
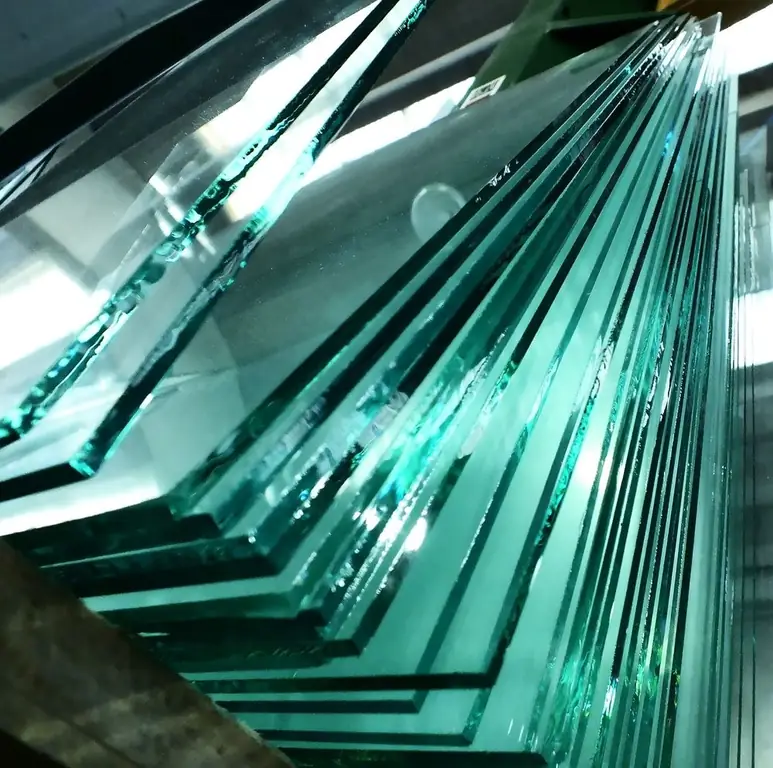
Glass is familiar to everyone. But the process of making it is extremely exciting. Each stage is important and affects the quality of the final product. The basis is sand, soda, lime. The process is almost entirely automated. Surprisingly, glass can even be made at home
Glass sandblasting: glass processing description, equipment, application, photo
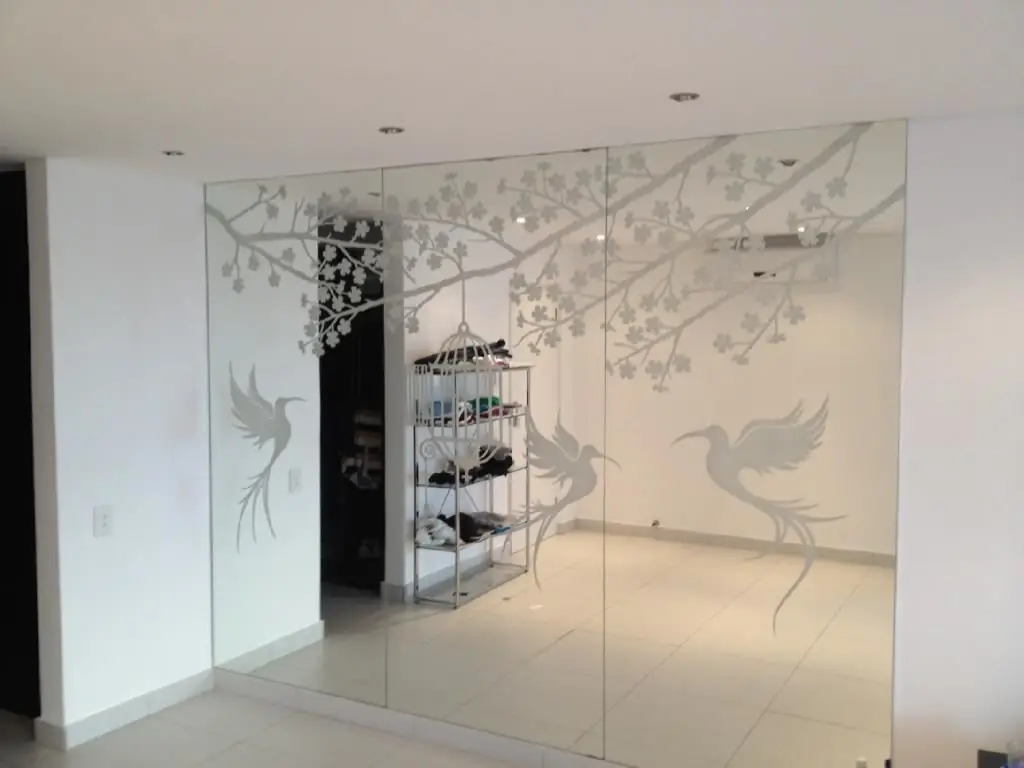
Among the numerous variations of interior decoration, sandblasting of a glass or mirror surface occupies a special place. This technology involves exposing the canvas to sand or other abrasive with a jet of compressed air released under high pressure. As a result, the surface changes and becomes matte, rough, velvety or painted with patterns. In the article we will consider what is sandblasting glass
Heat-resistant glass: manufacturing features and scope
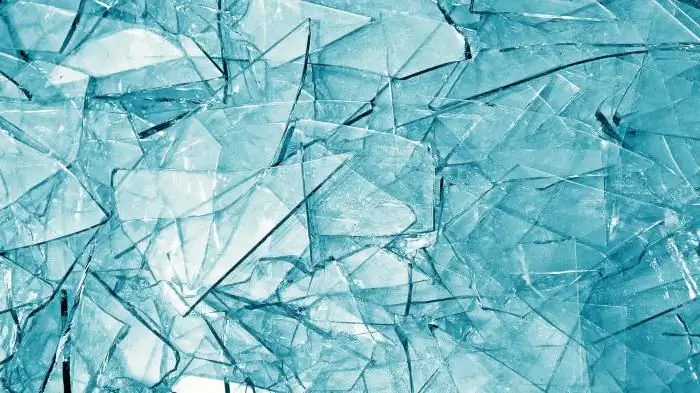
Glass is one of the most ancient and versatile materials. Glass products are all around us, but usually we do not think too much about its characteristics. They can vary greatly depending on the purpose of using the future product. One of the most common types is heat-resistant glass. Let's find out how it differs from the usual one and where it is applied
What is tempered glass: features of production, processing and applications
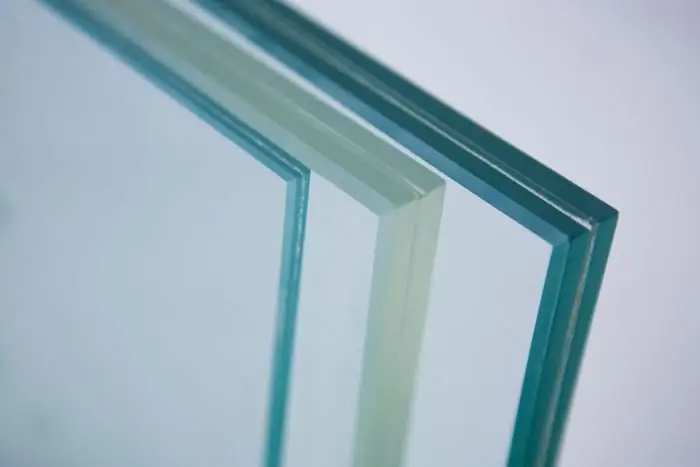
How is tempered glass different from regular glass? A description of the production process and the specifics of processing will help to find the answer to this question. Methods for determining tempered glass and possible options for cutting it without the use of special equipment
Grinding car glass. How to grind glass

The article is devoted to glass grinding. The grinding procedure, its tasks, technique, materials, etc. are considered