2025 Author: Howard Calhoun | [email protected]. Last modified: 2025-01-24 13:10
Nitric acid is one of the most demanded types of industrial raw materials. Its production can be carried out by different methods - depending on the variety in which the acid should be supplied to the customer. What is the essence of the relevant technologies? How do they compare with the type of nitric acid produced at the factory?
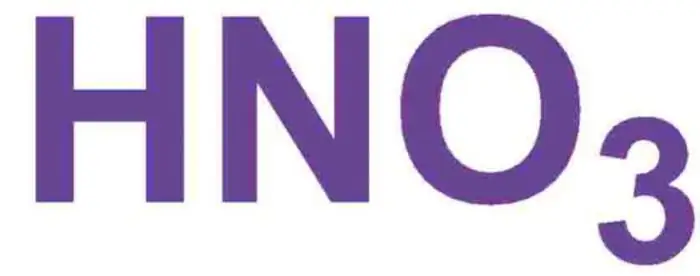
Industrial production of nitric acid: a history of technology development
First of all, it will be useful to study the historical facts about how the production of nitric acid developed in Russia. In the domestic industry, the release of this substance, according to available information, was initiated under Peter I. Subsequently, M. V. Lomonosov proposed a method for the production of nitric acid from s altpeter - this substance was actually considered the main raw material for the production of the substance in question until the beginning of the 20th century.
Along with s altpeter, the production of nitric acid in industry was carried out using sulfuric acid. The two substances under consideration, interacting with each other, formed nitric acid and sodium sulfur oxide. The advantage of thisthe method was the ability to obtain nitric acid at a concentration of about 96-98% (subject to the use of raw materials of the required quality).
The corresponding technology has been actively improved - in favor of increasing the speed of processing raw materials and ensuring the output of a larger volume of product. But gradually it gave way to the concept that the production of nitric acid was carried out through the contact oxidation of ammonia.
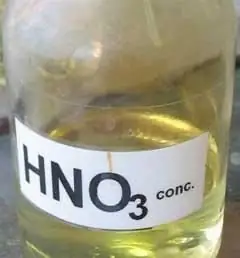
Also, a method was invented in which nitric oxide, obtained by arc oxidation of the corresponding gas from the atmosphere, was used as the main raw material for the production of acid. There is a widespread point of view that the first method is more cost-effective.
With the improvement of technological approaches to the production of nitric acid, an approach has been formed according to which the most optimal option for the production of the corresponding substance is the use of industrial infrastructure operating under high pressure. An alternative to it is the production of acid at atmospheric pressure, which is considered less profitable from an economic point of view.
The release of a substance at normal or elevated pressure involves the production of nitric acid from ammonia. There is also a combined method that combines the advantages of the other two. Features of the production of nitric acid by the combined method are, firstly, in the oxidation of ammonia at atmospheric pressure, and the implementation of its absorption - atincreased.
Ammonia is now considered the main raw material for the release of the substance in question, along with water and atmospheric air. Let's study the specifics of their use in the production of acid in more detail.
Nitric acid feedstock
So, the main raw materials used in the production of the substance in question are ammonia, air, and also water.
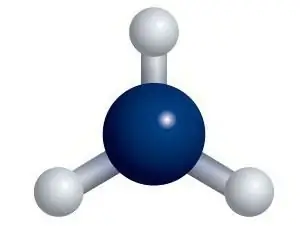
This requires the use of purified ammonia. To do this, it is purified in special evaporation and distillation equipment within the framework of various production cycles. Similarly, clean air must be used when discharging nitric acid. It is also filtered using special equipment. In turn, the water used in the production of nitric acid is purified from impurities and s alts. In many cases, pure condensate must be used to obtain the substance in question.
Let's study what varieties of the substance in question can be presented, as well as how each type of nitric acid is produced.
Varieties of nitric acid and the main stages of its release
There are 2 types of nitric acid produced in modern industrial plants - diluted and concentrated. The production of dilute nitric acid is carried out within 3 main stages:
- conversion of ammonia (its final product is nitric oxide);
- producing nitrogen dioxide;
- implementation of the absorption of nitrogen oxides atwater use.
The production of diluted nitric acid is widespread in modern industrial enterprises under the so-called AK-72 scheme. But there are, of course, other technologies for the release of this substance.
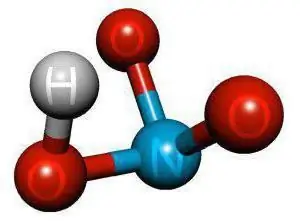
In turn, the production of concentrated nitric acid can be carried out by increasing the level of the corresponding substance in dilute form or through direct synthesis. The first method, as a rule, makes it possible to obtain an acid solution at a concentration of about 68%, which may not be enough for the application of the substance in question in a number of areas. Therefore, the method of direct synthesis is also common, which makes it possible to obtain a substance in a concentration of about 97-98%.
Let's take a closer look at how nitric acid is produced in one form or another. Above, we noted that the release of a diluted substance can be carried out according to the AK-72 scheme. Let's study its specifics first.
Production of dilute acid using AK-72 technology
The considered scheme, through which the production of nitric acid is carried out, involves the use of a closed cycle, accompanied by:
- ammonia conversion;
- cooling associated gases at a pressure of about 0.42-0.47 MPa:
- implementing the absorption of oxides under pressure of the order of 1.1-1.26 MPa.
The final product of the AK-72 scheme is nitric acid at a concentration of about 60%. Production of nitric acid withinthe technology under consideration is carried out within the framework of such stages as:
- ensuring the intake of air from the atmosphere into the industrial unit and its cleaning;
- compressing air, separating it into technological streams;
- evaporation of ammonia, purification of the corresponding gas from oil and other impurities, as well as its subsequent heating;
- mixing of purified ammonia and air, subsequent purification of this mixture and its transfer to the catalyst;
- obtaining nitrous gases and their cooling;
- condensate collection with nitric acid;
- concentration and absorption of nitric acid;
- cooling and cleaning the resulting product.
Finished acid is sent to storage or customer.
Along with the technology under consideration for the production of nitric acid - AK-72, another popular concept for the release of the corresponding substance is used, which involves ensuring the operation of industrial infrastructure at a pressure of about 0.7 MPa. Consider its features.
Product release technology under pressure 0.7 MPa: nuances
The technology in question produces non-concentrated nitric acid as an alternative to the AK-72 concept. It involves the implementation of the following stages of release of the substance in question.
First of all, as in the previous technology, the atmospheric air is cleaned. For this purpose, as a rule, a two-stage filter is used. Further, the air that has been cleaned is compressedby means of an air compressor - up to approximately 0.35 MPa. In this case, the air is heated - up to a temperature of about 175 degrees, and it must be cooled. After this problem is solved, it goes to the area of additional compression, in which its pressure increases to approximately 0.716 MPa. The resulting air flow, in turn, is heated to a high temperature - about 270 degrees through the action of nitrous gases. It is then mixed with ammonia in a special area of the industrial unit. The corresponding substance is activated when the acid is released initially in a gaseous state, which is formed due to the evaporation of the liquid. In addition, the ammonia must be purified. After preparation, the gas is heated and fed into the mixer simultaneously with air. This mixture is also filtered and, after purification, is fed to the conversion of ammonia. The corresponding procedure is carried out using platinum and rhodium alloy meshes at a very high temperature - about 900 degrees. The conversion rate is about 96%.
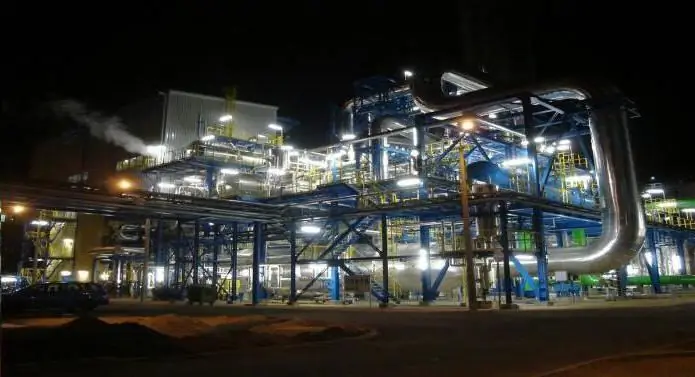
Production of weak nitric acid according to the technology under consideration involves the formation of nitrous gases. They are brought to a special area of the industrial unit, in which they are cooled. Due to this, the purified water evaporates and the appearance of steam with high pressure. Carried out through the appropriate area of the industrial unit, nitrous gases move into the oxidizer. It should be noted that their oxidation partially occurs already at the previousacid production steps. But in the oxidizer it becomes even more intense. In this case, nitrous gases are heated to a temperature of about 335 degrees. Subsequently, they are cooled in a special heat exchanger, and then they are sent to the condenser.
After that, nitric acid is formed in a weak concentration. It is necessary to separate the remaining nitrous gases from it - a separator is used for this. From it, nitric acid is fed into the absorption area of the industrial unit. The acid subsequently flows into areas of the apparatus below. At the same time, it interacts with nitrogen oxides, as a result of which its concentration increases. At the output, it is about 55-58%. It usually contains dissolved oxides that must be removed: for this, the substance is sent to the purge area of the unit. With the help of heated air, oxides are extracted from the acid. The finished product is placed in the warehouse or shipped to the customer.
Production of concentrated acid: direct synthesis
Having considered how the production of dilute nitric acid is carried out, we will study the specifics of the release of a concentrated substance. Acid production by direct synthesis from raw materials in the form of nitrogen oxides is among the most cost-effective technologies used at enterprises of the relevant profile.
The essence of this method is to stimulate a chemical reaction between the specified substance, water, and oxygen under a pressure of about 5 MPa. The technology by which the production of nitric acid is carried outconcentrated type on the basis of a dilute one, has a nuance: ensuring the transition of nitrogen dioxide into a liquid form is possible at a pressure and temperature close to atmospheric. However, in some reactions, the concentration of the corresponding substance is insufficient to transfer it to a liquid state at normal pressure, and it has to be increased.
Production of concentrated acid based on dilute acid
In this case, it is assumed that the acid is concentrated by means of absorbent substances - such as sulfuric, phosphoric acid, various solutions of nitrates. The main steps in the production of concentrated nitric acid based on diluted sulfuric acid are as follows.
First, the raw material is divided into 2 streams: the first is fed into the evaporator, the second - enters the cold area of the industrial unit. Sulfuric acid is fed into the region of the apparatus above the second dilute nitric acid stream. In turn, steam is supplied to the lower part of the unit, which heats the mixture used, as a result of which nitric acid evaporates from it. Her vapors rise up the apparatus, after which they are removed to the refrigerator. There, acid vapors condense - until its concentration reaches 98-99%.
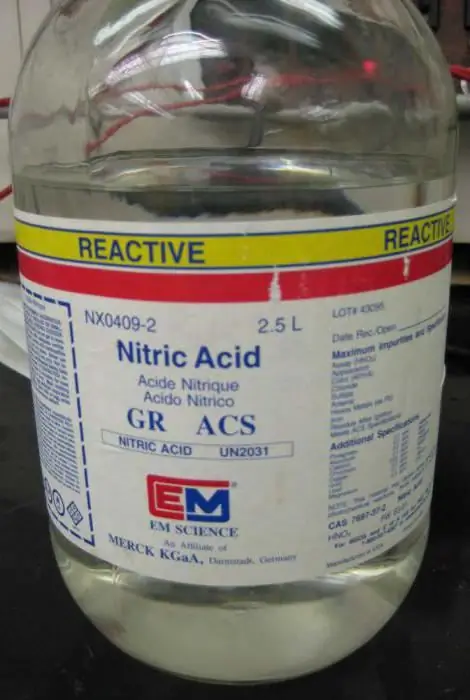
At the same time, some of the nitrogen oxides present during this production stage are absorbed by the acid. They must be extracted from the product: most often, nitric acid vapors are used for this purpose, which are sent to the condenser. The extracted nitrogen oxides, as well as acid vapors that did not form a condensate, are sent to another area of the apparatus - for absorption, where they are treated with water. As a result, dilute acid is formed, which is again fed to condensation and cooling. The finished product is sent to the warehouse or to the customer.
Features of concentration with sulfuric acid
The main task that characterizes the production of nitric acid in industry is the implementation of its cost-effective and efficient concentration. There are several approaches to developing an optimal scheme for solving it. It will be useful to consider those that are among the most common.
We noted above that sulfuric acid can be used to concentrate the substance in question. There is a fairly common way to increase the effectiveness of its use - a preliminary increase in the concentration of nitric acid through evaporation. Optimally, before treatment with sulfuric acid, the corresponding substance will have a concentration of about 59-60%. It should be noted that in practice this technology for the production of nitric acid is characterized by a low level of environmental friendliness. Therefore, as an alternative to the use of sulfuric acid, the use of nitrates is common. Let's study their specifics in more detail.
Concentration with nitrates
Most often, magnesium or zinc nitrates are used to solve the problem under consideration, which characterizes the production of nitric acid from ammonia. First of all, it is significantly more environmentally friendly than the methodinvolving the use of sulfuric acid. In addition, this technology ensures the highest quality of nitric acid as a final product.
At the same time, it has a number of shortcomings, which predetermine the appearance of difficulties in its widespread application. First of all, this is a rather high cost of the production process. In addition, this technology in many cases involves the production of solid waste, the processing of which can be complicated.
Use of catalysts for the production of nitric acid
It will be useful to consider what other substances are used along with the main raw materials for the production of the product in question in the industrial (most often catalysts are considered as such) production of nitric acid. The use of the substances in question is due to the need to increase the profitability of acid production, increase the dynamics of its output at an industrial unit.
The main requirement for the catalyst in the production of the product in question is the selectivity of action. That is, it must affect the main chemical reaction without affecting side processes. Most often, catalysts are used in the production of acid, which contain platinum.
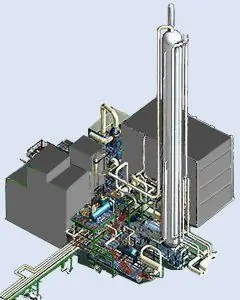
Above, we noted that when a weakly concentrated substance is released at elevated pressure, catalysts based on platinum and rhodium are used. In some cases, alloys with the addition of palladium are also used. But the main metal in them -platinum, its content is usually not less than 81%. The essence of the catalyst in this case is to stimulate the rapid passage of the main chemical reaction. As a rule, it passes within the external diffusion section.
The process depends on the limits of oxygen diffusion relative to the catalyst surface. This feature causes a higher concentration of ammonia, the main raw material for the production of nitric acid, on the surface of one or sometimes the catalyst, when compared with the concentration in air. It is possible to increase the specific gravity of various side reactions in which incomplete oxidation and the formation of nitrogen or its oxide are observed. In this regard, oxygen near the surface must be in an amount sufficient to displace ammonia. In this case, it will be possible to achieve a sufficiently deep oxidation.
It can be noted that, along with platinum catalysts, combined substances are also involved in the production of nitric acid. In particular, iron-chromium. They can significantly reduce the economic costs that characterize the production of the substance in question.
So, we have considered the methods of production of nitric acid, identified its main types. How many stages of nitric acid production need to be implemented depends on its type, as well as the specific technology for the release of the corresponding substance. It would be useful now to consider what difficulties characterize the industrial production of this product, which is in demand in many areas of the economy.
Main problems innitric acid production
So, as we already know, the production of nitric acid by the contact method - one of the most common in modern industry, involves the use of a catalyst in order to accelerate the oxidation of ammonia and increase the yield of the product. The main problem in the production of the product under consideration is the rather high price of the corresponding catalyst. However, its selectivity does not always reach the optimal value. In addition, a significant portion of the platinum that is used as the main element for the catalyst can be lost during production. As a result, again, the cost-effectiveness of the output of the product decreases.
Another problem that characterizes the production of nitric acid is environmental. Above, we noted that sulfuric acid can be used with the concentration of raw materials, and upon passing through the corresponding production cycle, harmful substances are formed. An alternative in this case may be the use of nitrates - but this, again, implies an increase in economic costs. However, the environmental factor for modern manufacturers today is as significant as the level of production profitability.
Recommended:
Clothing industry as a branch of light industry. Technologies, equipment and raw materials for the clothing industry
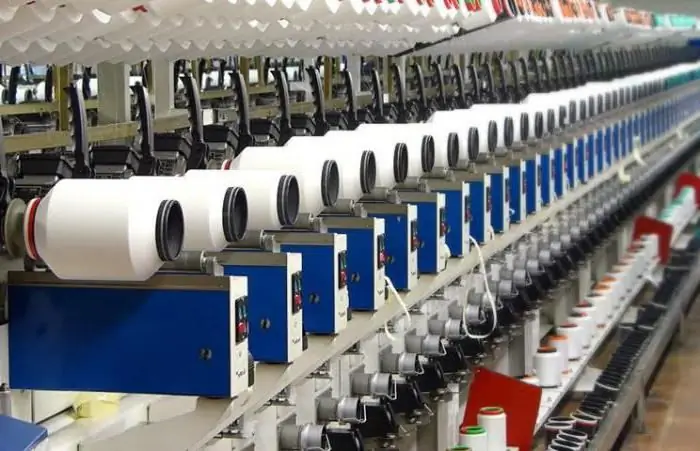
The article is devoted to the clothing industry. The technologies used in this industry, equipment, raw materials, etc. are considered
Dairy industry in Russia. Dairy industry enterprises: development and problems. Dairy and meat industry
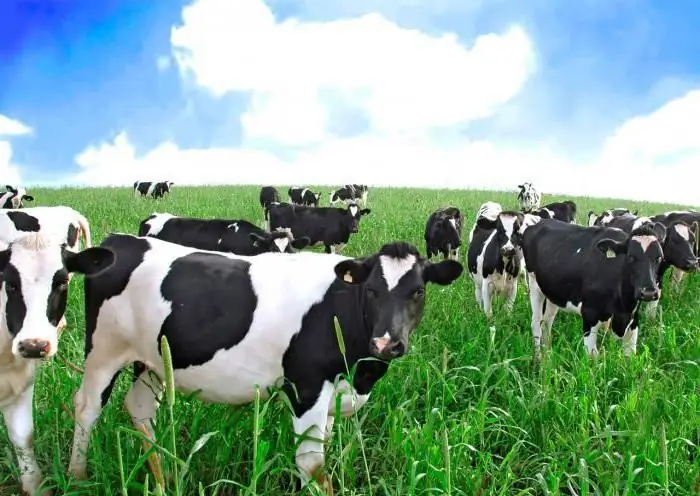
In the economy of any state, the role of the food industry is huge. Currently, there are about 25 thousand enterprises in this industry in our country. The share of the food industry in the volume of Russian production is more than 10%. The dairy industry is one of its branches
Production of plywood: technology, main stages of the process and areas of application of the material
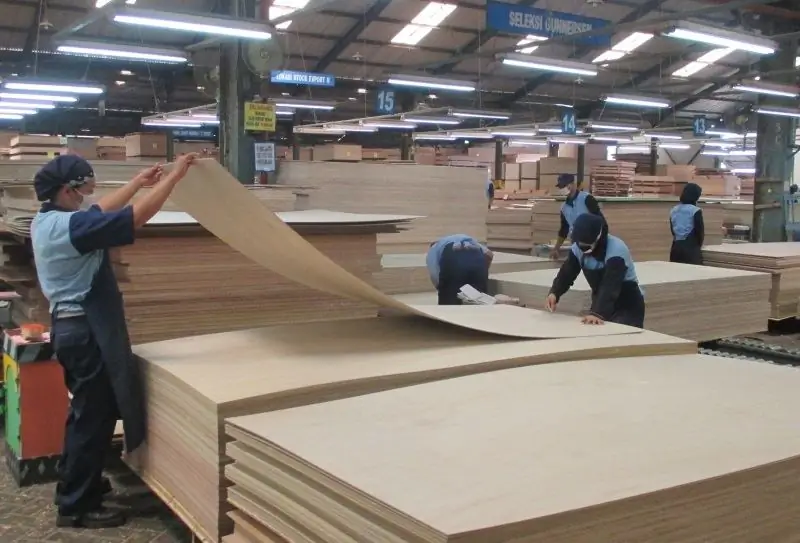
Plywood is one of the cheapest and most practical building materials. Despite the multi-layer structure, it is easy to install and can be processed at home without special equipment. Standard production of plywood involves the use of wood lamellas, with proper processing of which you can get a finishing material that is resistant to a variety of threats
Production of mineral water: technology, stages, equipment
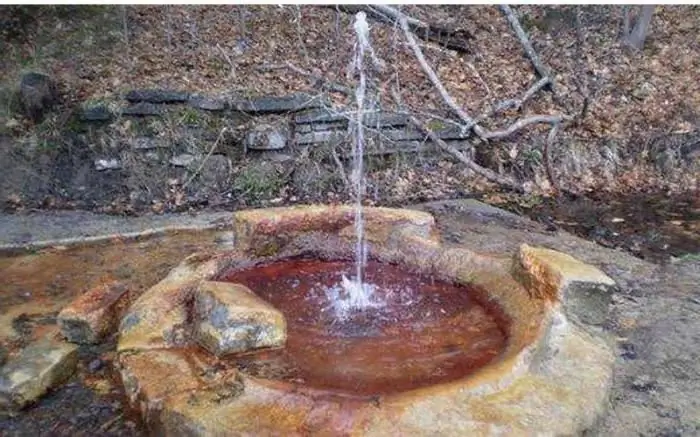
For many, the production of mineral water seems very easy. And at first glance, it may seem so. After all, nature itself took care of the quality and benefits of the product. And the entrepreneur only needs to drill a well and put on a tap so that water flows into bottles immediately. This is just a superficial knowledge of the matter
Industry Canada. The main features of the location of Canada's industry
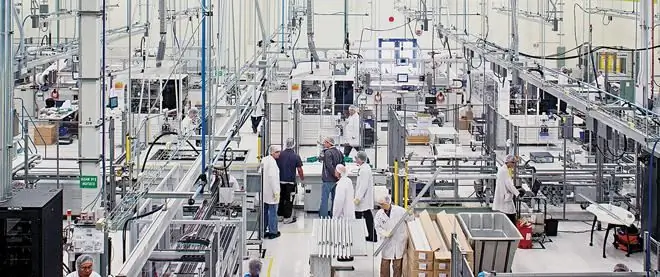
Canada is one of the most developed countries on the planet. With a relatively small population, its economy is comparable to that of the largest states - Brazil, Russia