2025 Author: Howard Calhoun | [email protected]. Last modified: 2025-01-24 13:10
PDCA-cycle (Deming cycle) is one of the basic concepts in modern management theory. It also underpins the ISO 9000 series of standards, which are used throughout the world for quality management in enterprises of all sizes and types.
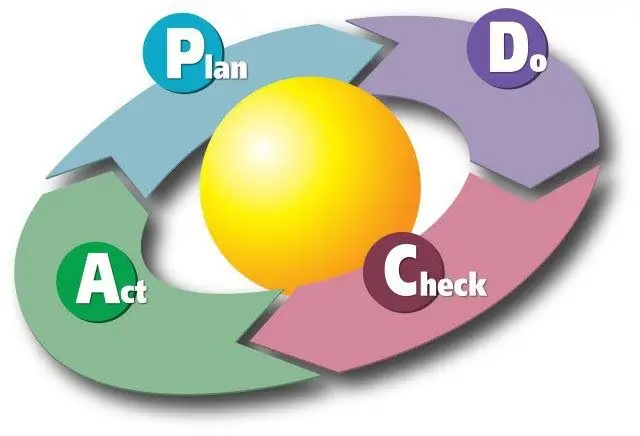
Definition
PDCA Deming cycle is a technology for continuous process improvement in business and in any other field of activity. The name of this method is an abbreviation of 4 English words, meaning a logical sequence of stages of improvement:
- P - Plan (plan);
- D - Do (do);
- C - Check (check, analyze);
- A - Act (act).
Everything is logical and simple: first you need to think over the actions. Then they are executed according to the plan. The third step is the analysis of the obtained results. And finally, the last stage - Act - involves the introduction of specific changes to improve the process and / or setting new goals. After that, the planning phase begins again, at which everything that has been done before should be taken into account.
Schematically, the PDCA control cycle is shown aswheel, which demonstrates the continuity of this process.
Now let's look at each step in detail.
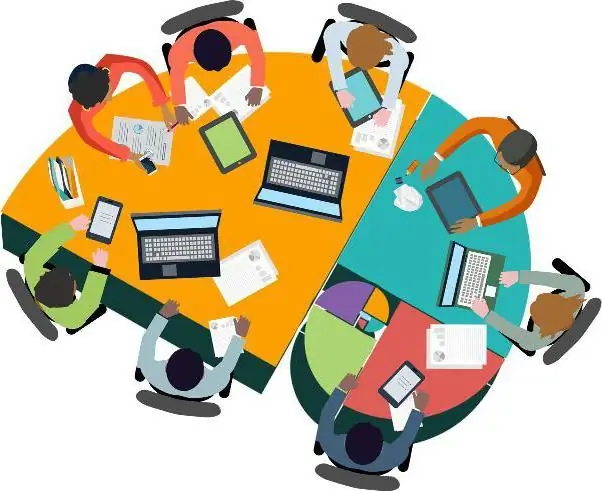
Plan (Plan)
The first step is planning. It is necessary to clearly formulate the problem, then determine the main areas for work and come up with the best solution.
A common mistake is to develop a plan based on subjective guesses and management assumptions. Without knowing the underlying causes of the problem, it is possible, at best, to neutralize its consequences, and then only temporarily. What tools can be used to do this?
Method "5 Whys"
It was developed back in the 40s, but gained popularity 30 years later, when Toyota began to actively use it. How is such an analysis carried out?
First you need to formulate and write down the problem. Then ask the question: "Why is this happening?" and write down all the reasons. After that, you need to do the same for each answer. Then we follow the same pattern, until the question "Why?" will not be asked 5 times. As a rule, it is the fifth answer that is the real reason.
Ishikawa Diagram
This method allows you to graphically represent the cause-and-effect relationships of any phenomena in business. Named after its creator, chemist Kaora Ishikawa, and is widely used in management.
When building a diagram, there are 5 likely sources of problems: people, materials, environment (environment), equipment and methods. Each of them, in turn, may contain more detailed reasons. For example,work of employees depends on skill level, he alth, personal problems, etc.
The sequence of constructing the Ishikawa diagram:
- Draw a horizontal arrow to the right, and write a well-defined problem near its tip.
- Slanted towards the main arrow, depict the 5 main influencers we talked about above.
- Use small arrows to show detailed reasons. Smaller branches can be added as needed. This is done until all probable causes are written out.
After that, all the options received are written out in a column, from the most realistic to the least.
"Brainstorm"
A group discussion with experts and key personnel, in which the task of each participant is to name as many potential causes and solutions to the problem as possible, including the most fantastic ones.
After theoretical analysis, it is necessary to find real factual data confirming that the causes of the problem are correctly identified. You can't act on hunches ("most likely…").
As for the planning itself, the specifics are also important here. It is important to set deadlines, outline a clear sequence of actions and measurable results (including intermediate ones) to which they should lead.
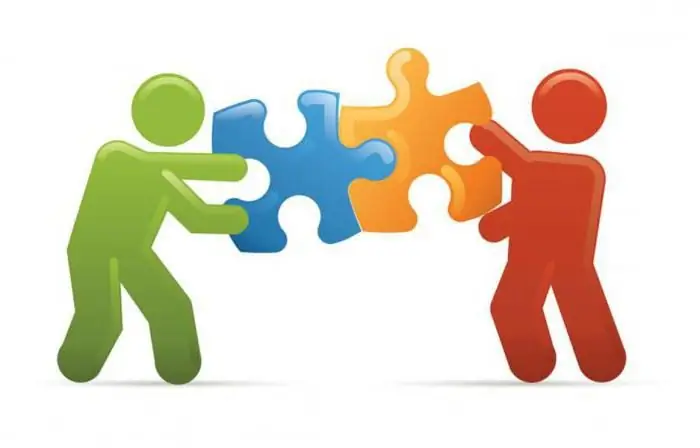
Do (Do)
The second stage of the PDCA cycle is the implementation of the plan, the implementation of changes. Most often it is more expedient to first implement the decisions made insmall scale, conduct a "field test" and check how it works on a small area or object. If there are delays, delays, it is important to understand what is the reason (unrealistic planning or lack of discipline on the part of employees). Additionally, an intermediate control system is being introduced, which allows not only to wait for the results, but to constantly monitor what has already been done.
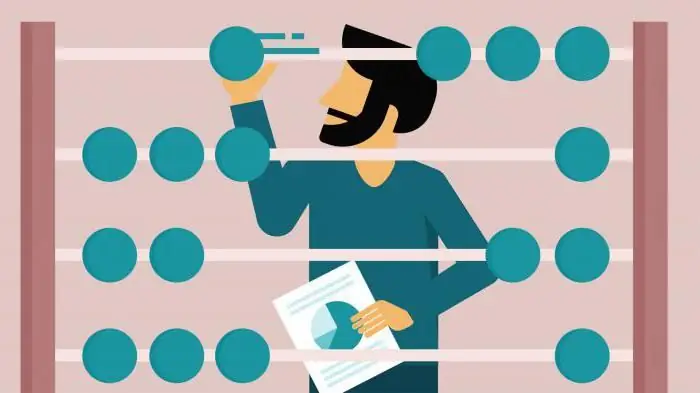
Check
In simple terms, now we need to answer one single question: "What have we learned?". The PDCA cycle implies a constant assessment of the results achieved. It is necessary to evaluate the progress against the set goals, determine what works well and what needs to be improved. It is mainly carried out by checking the reports and other documentation of the enterprise.
For the successful implementation of the Shewhart-Deming cycle (PDCA) in business, it is necessary to establish regular reporting on the work done and discussing the results with employees. The ideal tool for this is the introduction of KPI key performance indicators, on the basis of which a system of motivation and rewards for the most productive employees is built.
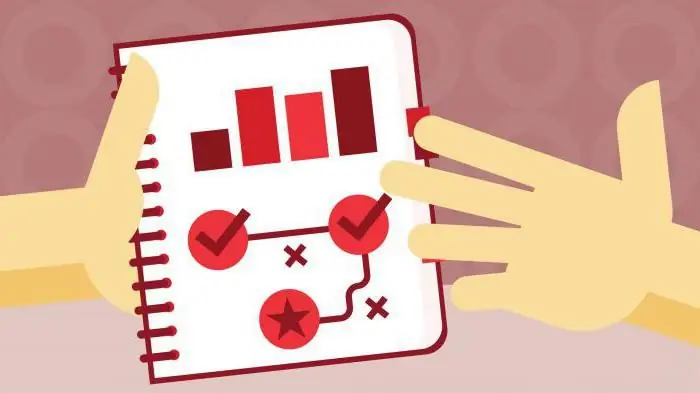
Act
The last step is actually action. There may be several options here:
- implement change;
- reject the decision if it turned out to be ineffective;
- repeat all stages of the PDCA cycle again, but introduce certainadjustments.
If something works well and can be replicated, it needs to be standardized. To do this, appropriate changes are made to the enterprise documentation: work regulations, instructions, checklists for checking work performance, employee training programs, etc. In parallel, the possibility of introducing improvements to other business processes where similar problems may arise should be assessed.
If the developed action plan did not bring the expected results, you need to analyze the reasons for the failure, and then return to the first stage (Plan) and try another strategy.
Recommended:
How to start a business in Kazakhstan from scratch? Credit for business in Kazakhstan. Business ideas
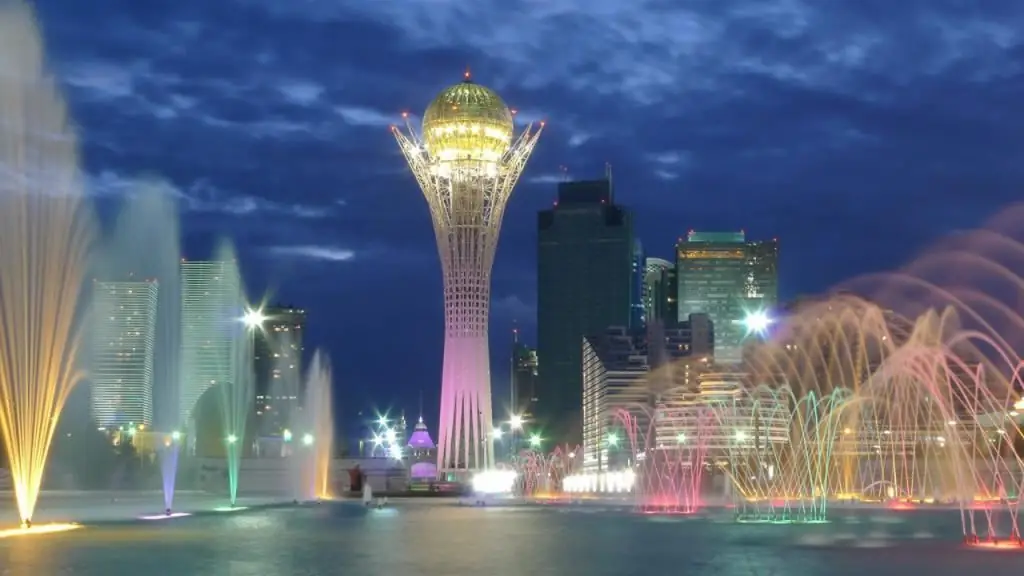
Now many people dream of starting their own business. Own business allows you to improve the material well-being of the family, helps a person to express himself and achieve success. But things in the established company do not always go well, as the founders make mistakes even at the start stage. For example, they can’t decide on a niche and choose the first one that comes across or don’t want to waste time on formalizing official documents. How to open a profitable business in Kazakhstan? Learn from this article
Small business problems. Small business loans. Starting a Small Business
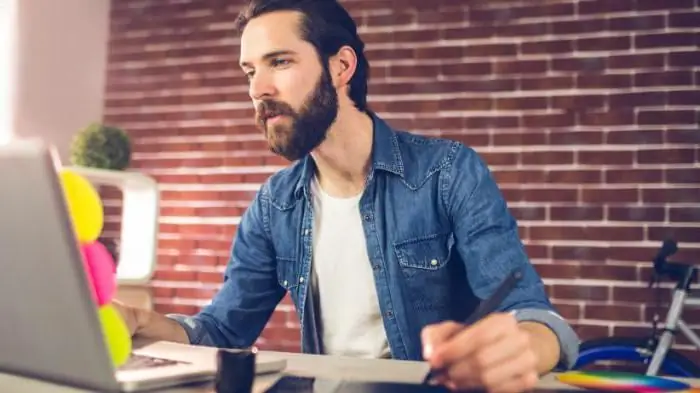
Small business in our country is practically not developed. Despite all the efforts of the state, he still does not receive proper support
Continuous casting of steel: principle of operation, necessary equipment, advantages and disadvantages of the method
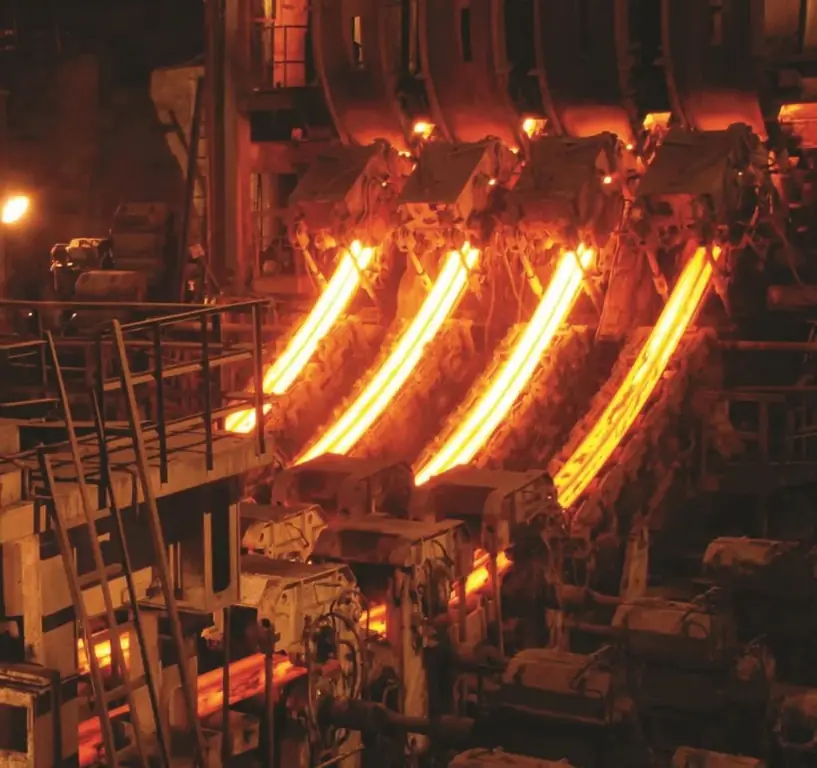
Today, a huge number of various things, parts, etc. are made of steel. Naturally, this requires a large amount of source material. Therefore, the plants have long been using the method of continuous casting of steel, characterized by the most important feature - high productivity
Is continuous experience relevant today?
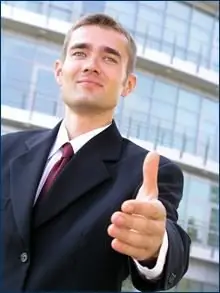
Continuous work experience is a set of hours worked, which allows only strictly defined periods of time between leaving one job and employment in another
The mission of an organization is the philosophy of its work
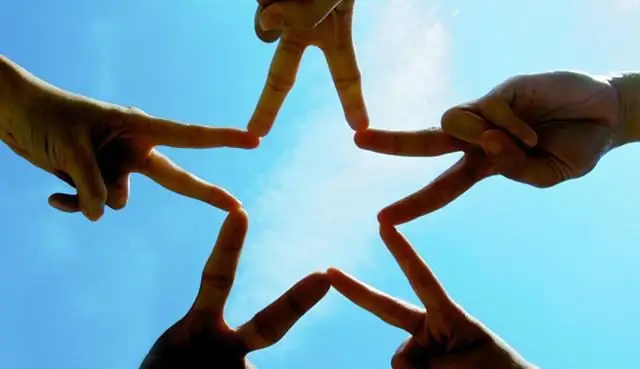
The mission of the organization is, in fact, the purpose of the organization in society, the philosophy of its activities, its raison d'être. It determines the direction and prospects for the development of the company, guidelines for the formation of intermediate goals. Is it enough for the head of the enterprise to formulate it orally?