2025 Author: Howard Calhoun | [email protected]. Last modified: 2025-01-24 13:10
Today, a huge number of various things, parts, etc. are made of steel. Naturally, this requires a large amount of source material. Therefore, the plants have long been using the method of continuous casting of steel, characterized by the most important feature - high productivity.
Essential equipment for work
To date, several installations for casting steel in this way are known, and they are abbreviated as UNRS. Initially, a vertical-type installation was developed and put into production, located 20-30 meters below the level of the workshop floor. However, later the desire to abandon the deepening of the floor became the main engine for the development of these installations. This led to the development and implementation of tower-type continuous casting plants. The height of these installations was 40 m. However, this version of the machine was not widely used for two reasons. First, buildsuch a unit in the workshop is quite problematic and laborious. Secondly, even more difficulties arose with its operation.
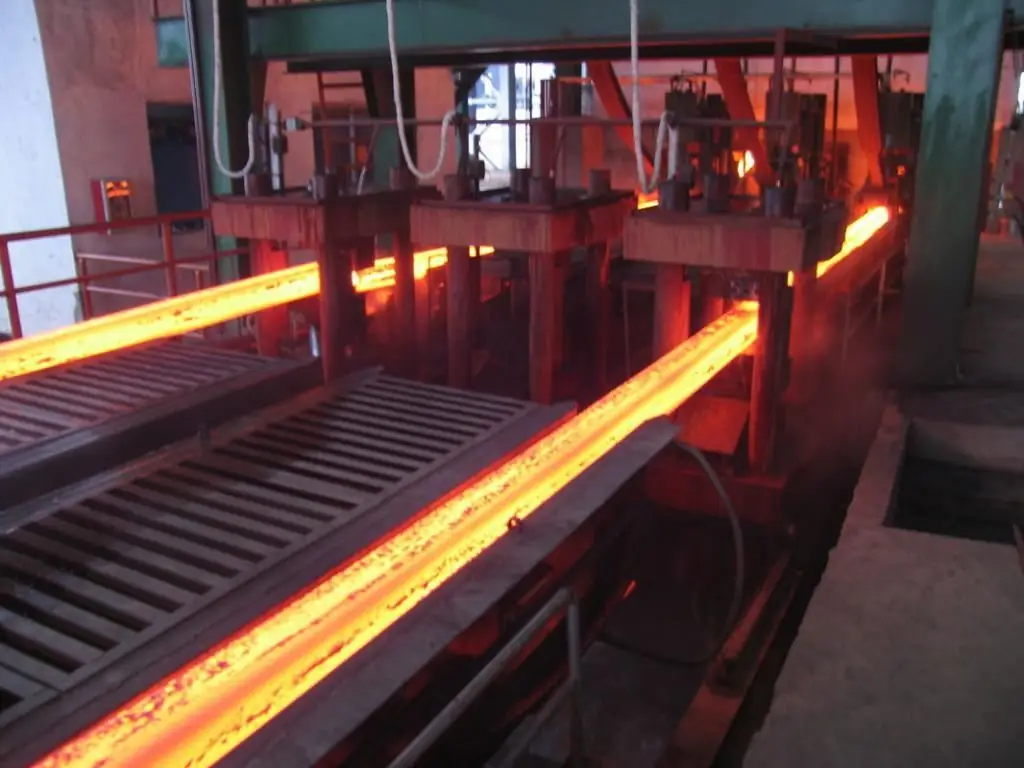
Curved and radial installations
Over time, continuous casting of steel was transferred to work with vertical bending machines. The main feature is the bending of the ingot coming out after the shafts by 90 degrees. After that, a special straightening mechanism was used in the installation to straighten the ingot, and only after this stage did the cutting take place. Continuous casting of steel on such equipment has not become very popular for some reason. First, the bend, of course, made it possible to reduce the height, but at the same time severely limited the cross section of the ingot itself. The more it was necessary to obtain a section of the material, the greater the bend had to be, which means that the height increased again. Secondly, the bending machines were placed in the steel shops with even greater difficulties than the vertical ones.
Today, installations for continuous casting of radial steel are gaining more and more popularity. On such a unit, the ingot is formed in the mold and leaves it along the same arc along which it entered it. After that, it will be straightened by a pull-correct mechanism. And then you can already start cutting the ingot into blanks. It is this design that in practice turned out to be the most rational in organizing the flow of goods in the steel shop.
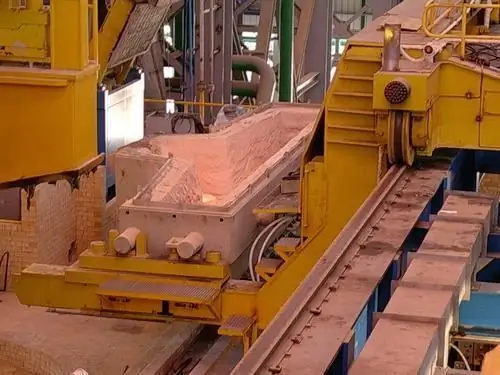
Where does casting begin
Technology of continuoussteel casting is a rather complicated process. However, it is fair to say that the principle remains the same regardless of the production setup used. You can consider the technology using the example of a vertical UNRS.
The machine is supplied with a ladle for pouring steel through a special crane. After that, the steel flows into the tundish, which has a stopper. For single strand machines there will be one stopper, for multi strand machines there will be one stopper per stream. In addition, the tundish has a special baffle to hold the slag. From the tundish, the steel will flow into the mold, passing through a dosing glass or a stopper. It is important to note here that before the first casting, the seed is introduced into the mold from the bottom side. It fills either the cross section of the entire mold, or only the shape of the workpiece. The top layer of the seed will be the bottom of the mold. In addition, it also has the shape of a swallow tail for future hitching with an ingot.
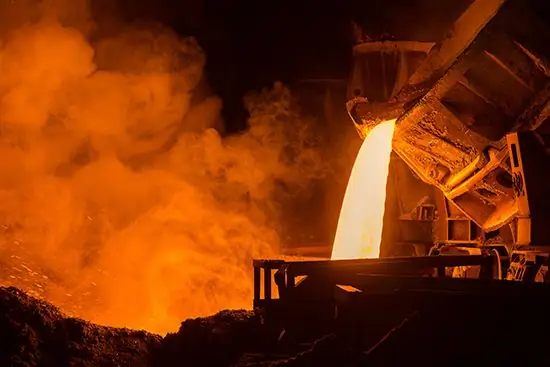
Further casting
Next, in the process of continuous casting of steel, it is necessary to wait until the level of raw materials rises above the seed to a height of about 300-400 mm. When this happens, the mechanism starts, which brings the pulling device into operation. It has pull rolls, under the influence of which the seed will fall and pull the created ingot along with it.
A continuous casting machine has a mold usually made of copper with hollow walls. He is under intenseby the action of cooling water, and its internal section corresponds to the shape of the ingot to be obtained. It is here that the ingot-blank crust is formed. At high casting speeds, tearing of this crust and leakage of metal can occur. To avoid this, the mold is characterized by reciprocating motions.
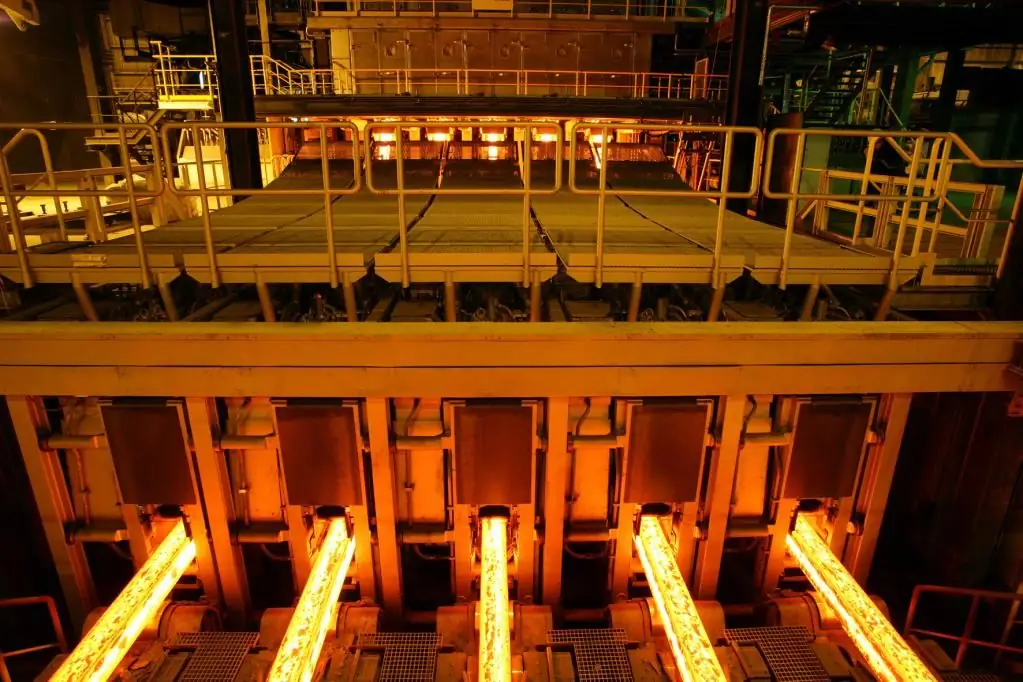
Mold performance characteristics
The continuous casting machine has an electric motor responsible for creating this reciprocating motion. This is done through the force of the gearbox with a cam-type swing mechanism. First, the mold moves in the same direction as the billet, that is, down, and after the process is completed, it returns back up. The swing stroke is from 10 to 40 mm. The mold is an important compartment in the continuous casting of steel on any type of equipment, and therefore its walls are lubricated with paraffin or any other lubricant suitable for the characteristics.
It is worth noting that in modern equipment the level of metal is controlled radiometrically by applying a control signal to the ladle stopper. In the mold itself, either a neutral or a reducing atmosphere can be created above the metal level to avoid product oxidation during production.
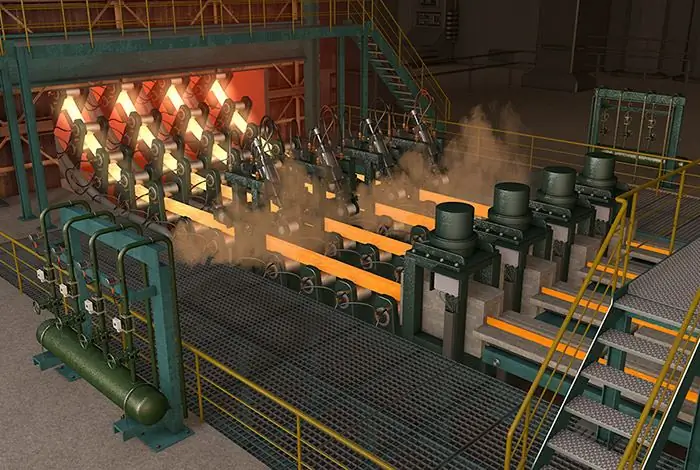
Ingot peel
It is worth noting that work under vacuum is also considered a promising casting method. One unit can carry outpouring through several molds at once. Thus, the number of streams of one installation can reach up to eight.
The heat sink action of the cold seed is used to form the bottom of the ingot skin. The ingot will exit the mold under the influence of the seed, which is drawn into the secondary cooling zone (SCZ). In the middle of the billet, the steel will still be in a liquid state. It is important to note here that, according to the requirements of the steel casting technology, the skin thickness must be at least 25 mm at the time of exit from the mold. To meet these requirements, it is necessary to choose the right material speed.
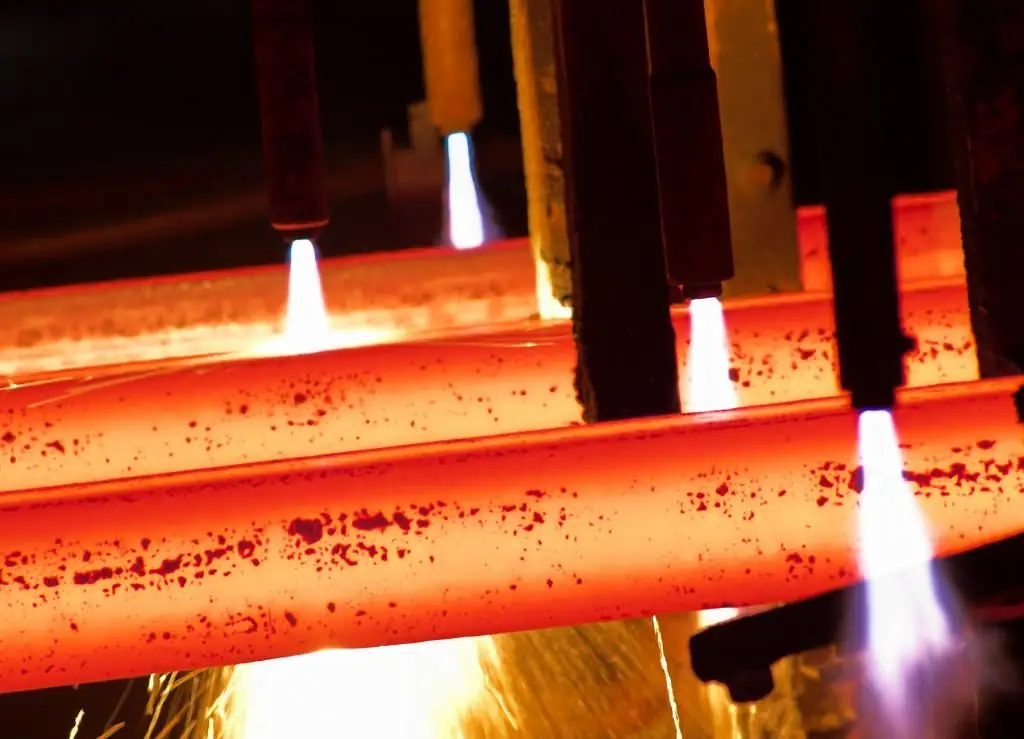
Characteristics of the installation and casting process
Technological characteristics are approximately as follows. If the section of the ingot is 160x900 mm, then its speed should be from 0.6 to 0.9 m/min. If the cross section is 180x1000 mm, then the speed is reduced to 0.55-0.85 m/min. The highest speed indicator is required when cutting a square-type ingot 200x200 mm - 0.8-1.2 m/min.
Based on the above indicators, we can conclude that the average casting speed of one strand using continuous casting technology is 44.2 t/h. If you exceed the optimal rate of speed, then the central porosity will increase.
Further, it is worth noting that the stability of the casting and the quality of the product itself are affected by the temperature of the metal. Empirically, it was found that at a temperature of more than 1560 degreesCelsius the surface of the ingot is often covered with cracks. If the temperature is lower than indicated, then the glass is often tightened. Thus, it was found that the optimal temperature for the method of continuous casting of steel would be 1540-1560 degrees Celsius. To maintain this figure, the heating temperature of the furnace before release should be in the range of 1630-1650 degrees.
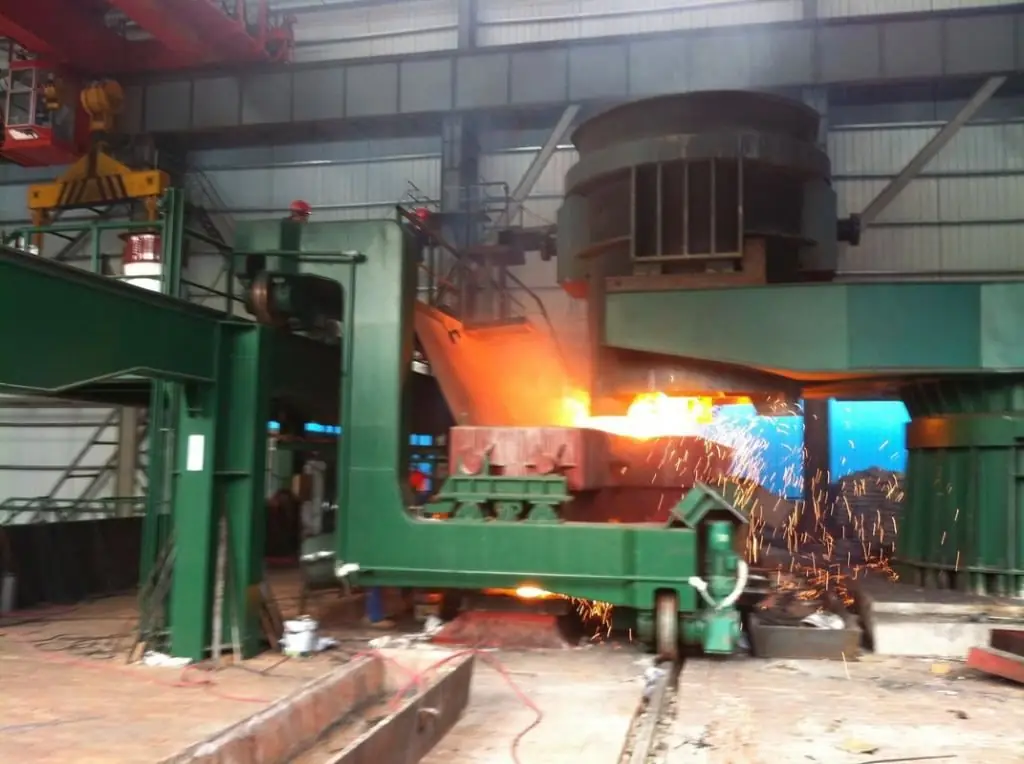
Secondary cooling zone
In this section, the most intensive and direct cooling of the ingot is carried out with the help of water coming from the spray. There is a special system of idle, not power rollers. Their rotation prevents the ingot from bending or warping. Due to intense cooling in this zone, the walls of the ingot will quickly add in thickness, and crystallization will spread in depth. The speed of drawing the ingot and the degree of its cooling should be chosen in such a way that by the time the ingot enters the pull rolls it is already completely solid.
What are the benefits of continuous casting
Since this method of casting steel has replaced the method of pouring into molds, it is worth comparing with this method. In general, it is worth highlighting the following advantages: greater productivity, reduced costs and reduced labor intensity of the process. Due to the constant formation of the ingot, the shrinkage cavity is transferred to the tail, in contrast to the molds, where each ingot had its own cavity. Because of this, the percentage of yield of suitable metal increases significantly. UNRS allows you to geta blank of various shapes, from a small square 40x40 mm to a rectangle 250x1000 mm. The use of continuous casting machines made it possible to completely abandon swaging mills. This significantly reduced the cost of the production process, and hence the price on the market. In addition, the process of metallurgical processing has been simplified.
Flaws
Despite the possibility of high mechanization and automation of the process, a high percentage of good ingots and other advantages described above, this method also has some negative sides. The disadvantages of continuous casting steel are as follows.
Firstly, there is no possibility to produce ingots of complex configuration. Secondly, the range of ingots and blanks is quite limited. It is quite difficult to convert machines to pour raw materials of a different brand, which can increase the final cost of a product of a different brand if it is produced at the same plant. Some steel grades, for example, boiling ones, cannot be made using this method at all.
The last disadvantage of the continuous method of casting steel is very significant. It is a possible equipment failure. The failure of the UNRS will lead to huge losses in productivity. The longer it takes to repair, the more losses will grow.
Recommended:
Letterpress is Letterpress printing technology, modern stages of development, necessary equipment, advantages and disadvantages of this type of printing
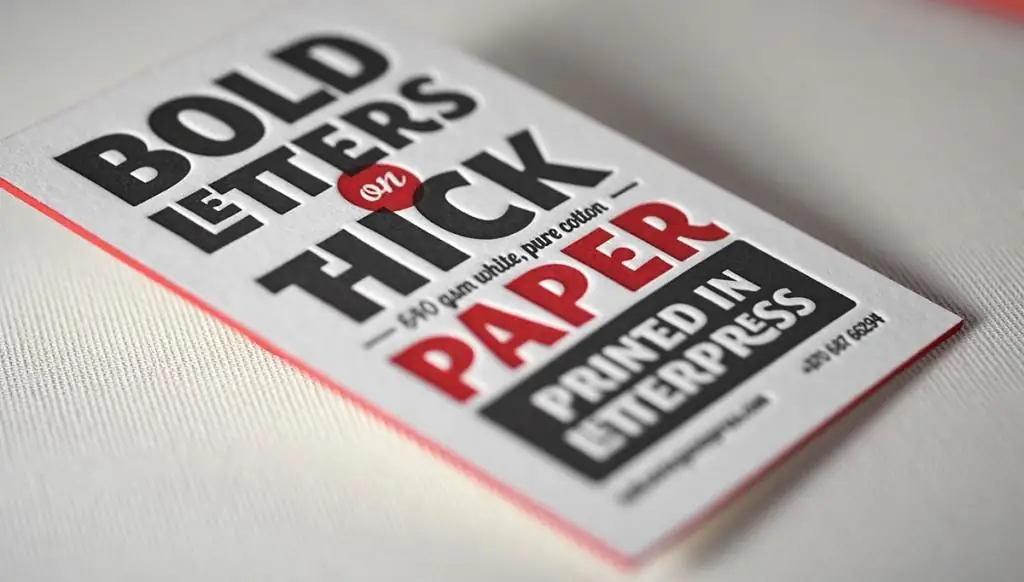
Letterpress is one of the typical methods of applying information using a relief matrix. The elements that protrude are covered with paint in the form of a paste, and then pressed against the paper. Thus, various mass periodicals, reference books, books and newspapers are replicated
Casting in silicone mold: equipment. Vacuum casting in silicone molds
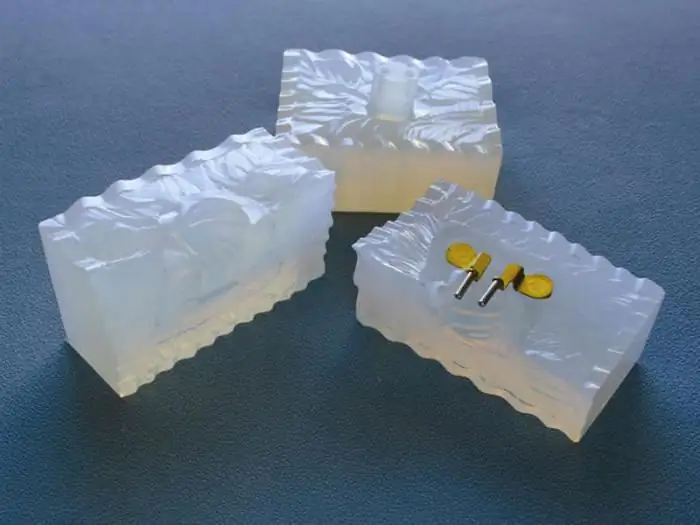
For the manufacture of a small number of plastic blanks, vacuum casting into silicone molds is most often used. This method is quite economical (making a metal mold requires more time and money). In addition, silicone molds are used repeatedly, and this also significantly reduces the cost of production
Diesel operation principle: features, advantages and disadvantages
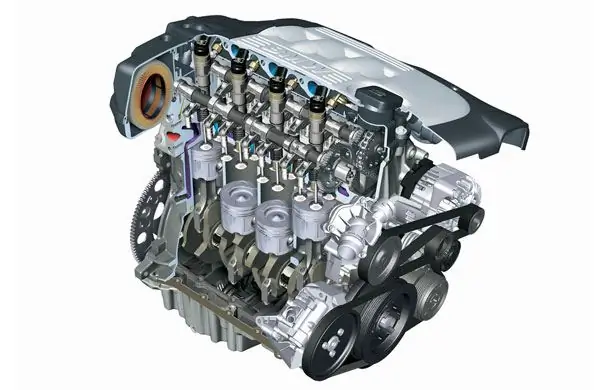
Diesel cars on our roads are by no means uncommon. In the countries of Western Europe, they are in the majority. Diesel engines have a number of advantages over gasoline engines. But at the same time, there are some drawbacks. What is this motor, what is the diesel device and the principle of operation? Consider in our today's article
Diesel submarines: history of creation, boat projects, principle of operation, advantages, disadvantages and stages of development
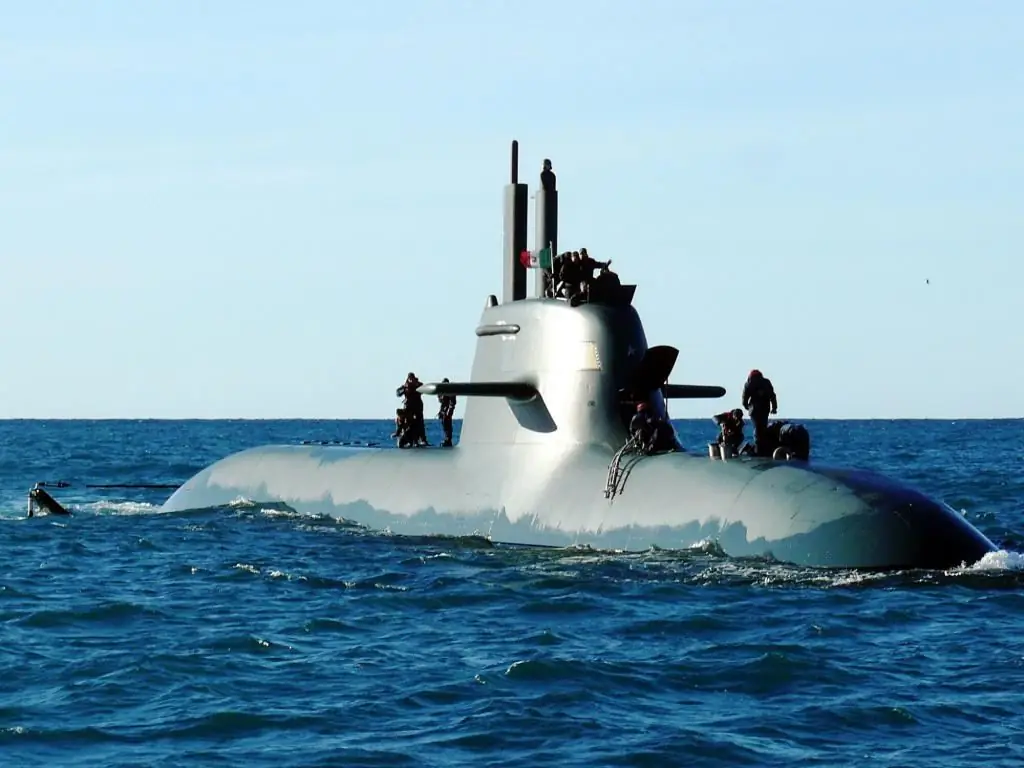
The idea of creating a submersible moving under water, actually a prototype of a submarine (hereinafter referred to as a submarine), arose long before their actual appearance in the 18th century. There are no exact descriptions of underwater vehicles in numerous legends, nor in the Renaissance genius Leonardo da Vinci
Lost-wax casting: technology, advantages and disadvantages
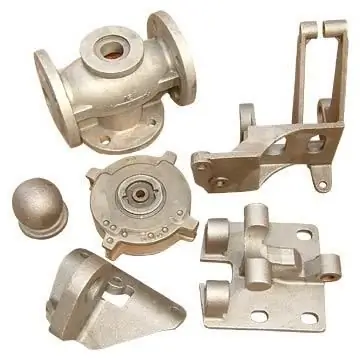
The use of investment models is a fairly popular method of foundry production. It is used where it is necessary to accurately observe the dimensions and ensure high quality of the surface of the parts. This is how turbine blades and high-performance tools, dentures and jewelry are cast, as well as sculptures of complex configuration. The mold for casting is one-piece, the model of low-melting materials is not removed during molding, but is melted out