2025 Author: Howard Calhoun | [email protected]. Last modified: 2025-01-24 13:10
Traditional construction technologies from reinforced concrete structures are currently experiencing a crisis associated with the successful development of alternative methods of constructing load-bearing structures. Masonry materials occupy a special place in this area of installation work, allowing the construction of cheap objects with high insulating qualities. The closest thing to the budget segment is the foam block production technology, which can be organized even in a household environment.
What is a foam block?
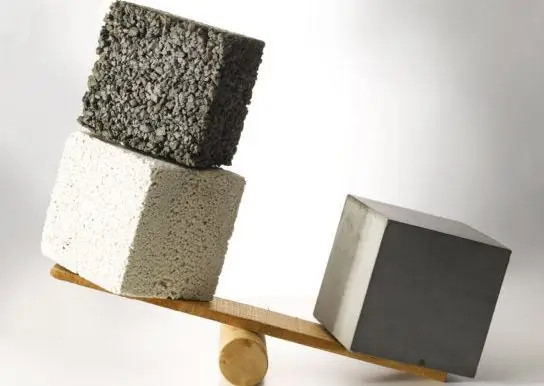
The product is included in a wide group of wall block materials, which is also formed by brick and stone materials. The fundamental structural difference of the foam block is the cellular structure. It is due to it that high insulation rates are achieved, and especiallyinsulation. Usually, among the weak points of this material, a low level of strength is called, which is true if compared with similar characteristics of the same brick. This is due to the fact that the density of the cellular structure, depending on the foam block production technology used, varies from 400 to 1200 kg/m3, while for row bricks it reaches 3000 kg/m 3.
Nevertheless, structural weakness does not prevent the use of foam block as a structural building material, albeit with limitations. As already mentioned, its advantages are also due to economic factors. Firstly, this is due to the low cost of production - both in terms of raw material supply, and in the technology of organizing the production process. As practice shows, the business for the production of foam blocks with an annual output of about 10,000 thousand / m3 income is about 1-1.2 million rubles. Another thing is that this niche has its own risks, so a comprehensive analysis of demand and competitiveness at a particular site is initially required. Secondly, like most cellular concretes, the foam block is lightweight and resistant to external factors, so you can count on cost savings in the implementation of logistics processes.
Required production raw materials for foam block
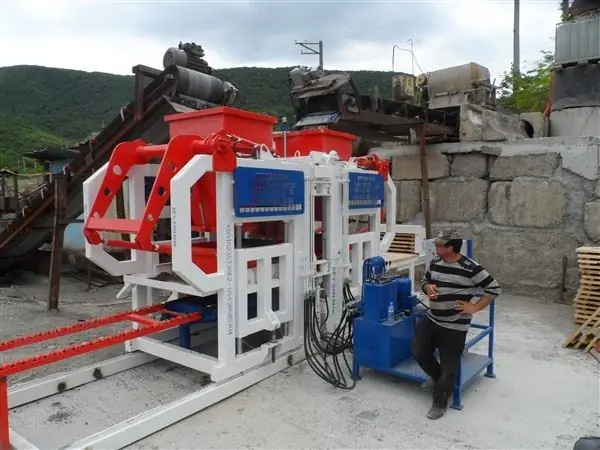
The mineral resource base for the manufacture of the base of the foam block may differ in the set of components, which depends on the requirements for the characteristics that are neededprovide building structure. But there is also a standardized recipe core, which consists of ordinary cement, water and sand. This is a kind of filler that forms the material structure of the product. On this basis, modifications can be made by adding binders, plasticizers, frost-resistant additives, hardeners and other inclusions that improve individual properties of the foam block. And vice versa, if there are no strict requirements for technical and physical indicators, then the base composition can be diluted with cheap raw materials like clay, ash, wood chip production waste, etc. Reinforcing additions are also made, including fiber and fiberglass fibers.
The main component that distinguishes foam block production technology is a foaming agent. It can be a synthetic or organic component, due to which the cellular structure is formed. Again, in order to reduce the cost of technology, inexpensive synthetic foam concentrates are used, which reduce the strength and environmental friendliness of the product. In addition, artificial components in some cases reduce the fire resistance index of the structure to zero. In turn, organic or protein blowing agents are made from a natural material that provides superior insulation, fire resistance and structural resistance.
Equipment for foam concrete mix preparation
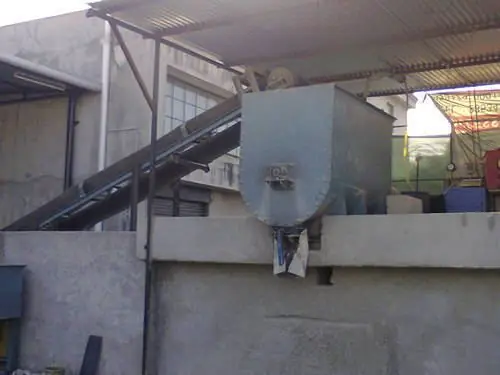
The first stage of foam block production is the one during which the solution is formed. ATat home, this part of the work can be carried out on conventional equipment for the preparation of cement mortar, but the quality of the product will be significantly lower. In the in-line production mode, it is desirable to organize the process of preparing the mixture at the following technological units:
- Water tank. A special reservoir in which the accumulation and preparation of liquid for foam production is carried out. This design is distinguished from conventional containers by a special coating of internal surfaces made of rigid polyethylene, which protects the base of the tank and prevents damage to auxiliary equipment that will come into contact with the walls. In addition, such tanks provide special equipment for filling and draining the technical fluid with a tap and valves.
- Foam generator. An obligatory functional component for the implementation of foam block production technology, through which a homogeneous finely dispersed foam with evenly distributed air bubbles is formed. Specialized installations of this type make it possible to regulate foaming parameters with high accuracy in the average range from 150 to 400 g per 1 liter. This range just allows you to vary the density of the foam block from 300 to 1200 kg/m3. When choosing a foam generator, the water supply rate and the pressure at the inlet to the pumping unit are taken into account.
- Vibrating sieve. Auxiliary device for screening sand and gravel fillers of the desired fraction to increase the uniformity of the solution. With regard to the foam block, the optimal size of the fraction of this componentis 1.5-2 mm. The design of the vibrating sieve itself is a metal mesh on a rigid frame, to which a vibrating apparatus with a power of 500-700 W is connected.
- Sand and cement dispenser. For fillers of fine fraction, weight dispensers are provided. Such installations are often used as part of foam block mini-productions to automate technological operations. The weighing accuracy of the meter can reach 0.5% when the operating range is 10 to 1000kg.
Forming production technology
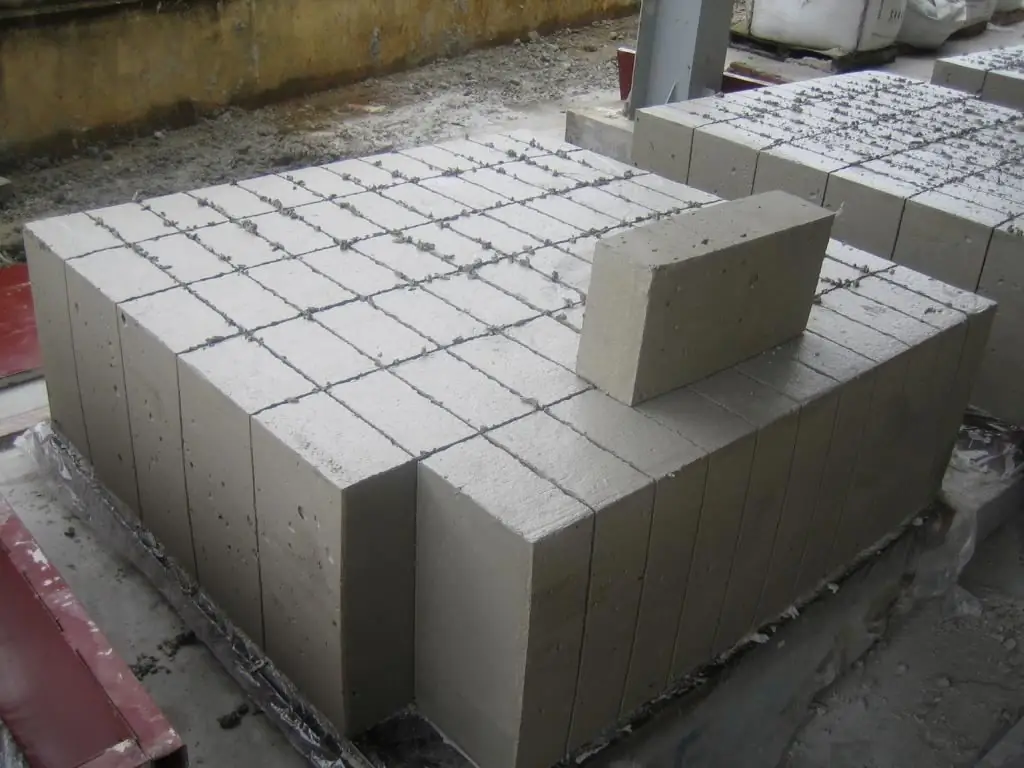
The prepared solution for the foam block is poured into a specially prepared form. This technology can be compared with traditional strip foundation methods, for which formwork is being prepared. In this case, the function of the formwork is performed by a matrix form with honeycombs corresponding to the dimensional parameters of the target block. In the conditions of factory production, a metal form is used, provided with accessories for carrying and convenient distribution of the mixture over the honeycombs. A simplified technology for the production of foam blocks at home also allows the use of wooden structures. It can be made independently according to the principles of the crate, only with a bottom and a larger size - again, the parameters are determined individually depending on the characteristics of the final product. For this form, you can use bars with planks fixed with ordinary hardware and reinforcing corners.
So, the prepared solution is distributed over the honeycombs, after which it solidifies for 10 hours. That is, within the framework of in-line production, one form can be used twice a day in shifts. After solidification, the structure is disassembled, and the blocks remain on the pre-prepared bottom.
Cut production technology
An alternative way, in fact, the same molding, but on a different principle. A niche is also being prepared to accommodate the solution, but this time without matrix cells. If we continue the analogy with the foundation, then in this case a solid formwork is mounted under a monolithic pour or screed. You can use a prefabricated wooden structure, but with major reinforcement on the sides. The insulation material inside the mold is also thought out, since at high pressure the depressurization of the formwork with smudges is not excluded, which will lead to the rejection of some of the blocks located at the edges. The array is aged for about 15 hours, after which the most important stage begins - cutting into separate blocks. This procedure is carried out with a special circular saw with sufficient blade overhang. In this case, it will be important not so much the high power of the equipment as the accuracy of the cut, which will be improved by the guides in the design of the saw.
Both of the considered methods have their pros and cons, but which foam block production technology is better for private use? The cutting process is quite laborious and technologically complex, so the molding method is more preferable at home. But it is important to keep in mind that pouring into honeycombs will not allow you to achieve the same quality of block geometry as in the case of high-quality cutting.
The foam block drying process
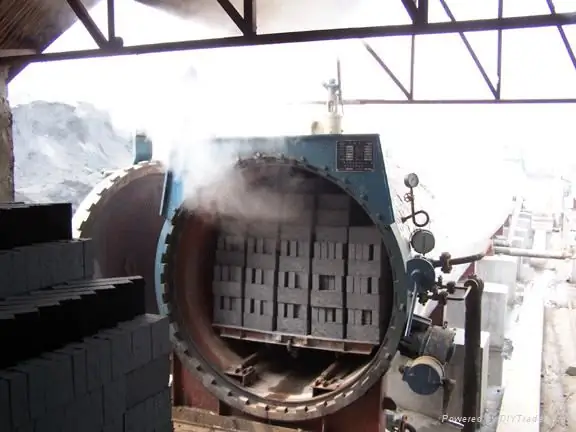
There are several important points in the organization of the intermediate stage of polymerization. Drying to a large extent determines the quality of the natural pressing of the internal structure of the material. It is desirable that this process be intensive, since a high rate of hardening will prevent the risks of, albeit insignificant, but deformation of the structure against the background of internal stress. As part of industrial equipment for the production of foam blocks, this function is performed by thermal drying chambers and ovens, which within a couple of hours allow you to achieve the desired state of the structure. At home, you will either have to stop at the option of natural drying, or use special heaters. Optimally for this operation, a heat gun is suitable, which gives a directed stream of hot air. The speed of the polymerization process will depend on the power of the apparatus and the selected thermal regime.
Mobile foam block production plants
Especially for small workshops and "garage" industries, industrial equipment developers offer optimized lines for the production of cellular block materials. The configurations of this equipment may vary, but in any version it is characterized by small size, autonomy and the ability to move. A typical machine for the production of foam blocks at home of this type is equipped with an installation with a foam generator and a capacity of up to 1000 liters. A special module is provided for cutting the prepared foam concrete into blocks of specified parameters, whichcan be adjusted according to current requirements. Despite the general concept of optimization, such installations are provided with modern electronics with automated control, the presence of dispensers with level sensors and generators, which provide the ability to work remotely from the central power supply lines.
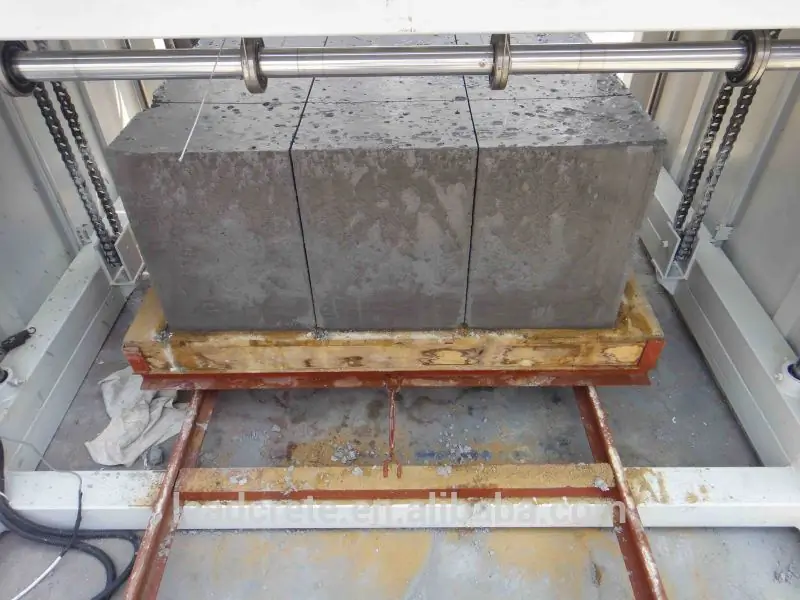
Full size foam block production line
Large enterprises use stationary lines with a full cycle of technological operations for the production of foam block materials in large volumes. These conveyors feature an automated dispenser, consumables storage tanks with self-operating hatches, and platforms for comprehensive machining of workpieces with high precision. Thus, a mini-factory for the production of foam blocks is organized within one workshop, the productivity of which can reach 150 m3 of material per shift. Integrated control of the line can be carried out through the operator's console or in automatic mode according to specified programs separately for each functional block through an industrial controller.
Application of foam block
This material is widely used in various areas of construction. It is used to construct frames of houses, light-bearing foundation structures, partitions, as well as decorative objects in landscape design. Modern equipment for the production of foam blocks allows the production of products of various shapes and sizes, which expands the possibilities for their structural application. For example, the workflow can include reinforcement and complex slotting, which gives builders more options for mounting block elements.
Conclusion
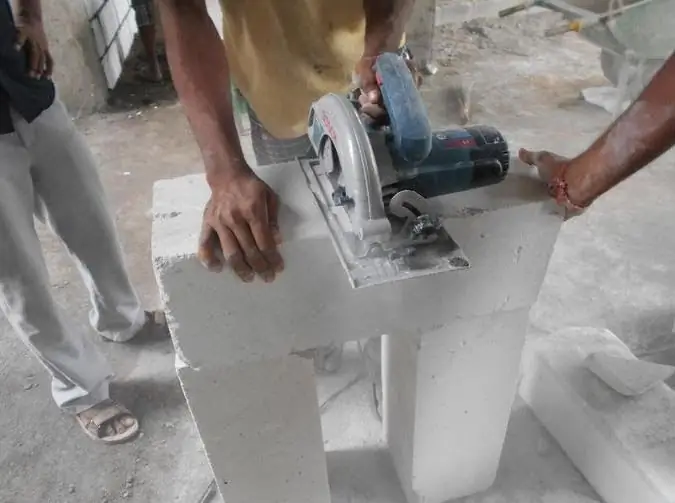
The spread of foam concrete as such was caused by the growing demand for low-cost housing with optimal technical and operational characteristics. Lowering the cost of organizing work with ready-made blocks also contributed to the popularity of this technology. Using a small-sized machine for the production of foam blocks in the household, you can get ready-made building materials for building a house, a bathhouse, a technical structure or a separate structure at minimal cost. But it is important to take into account the operational limitations of cellular concrete. The relatively low bearing capacity does not allow it to be used on seismically active soils, in the construction of multi-storey buildings, and also to perform front finishing from it.
Recommended:
Smoking shop: preparation of necessary documents, drawing up a business plan, selection of necessary equipment, goals and stages of development
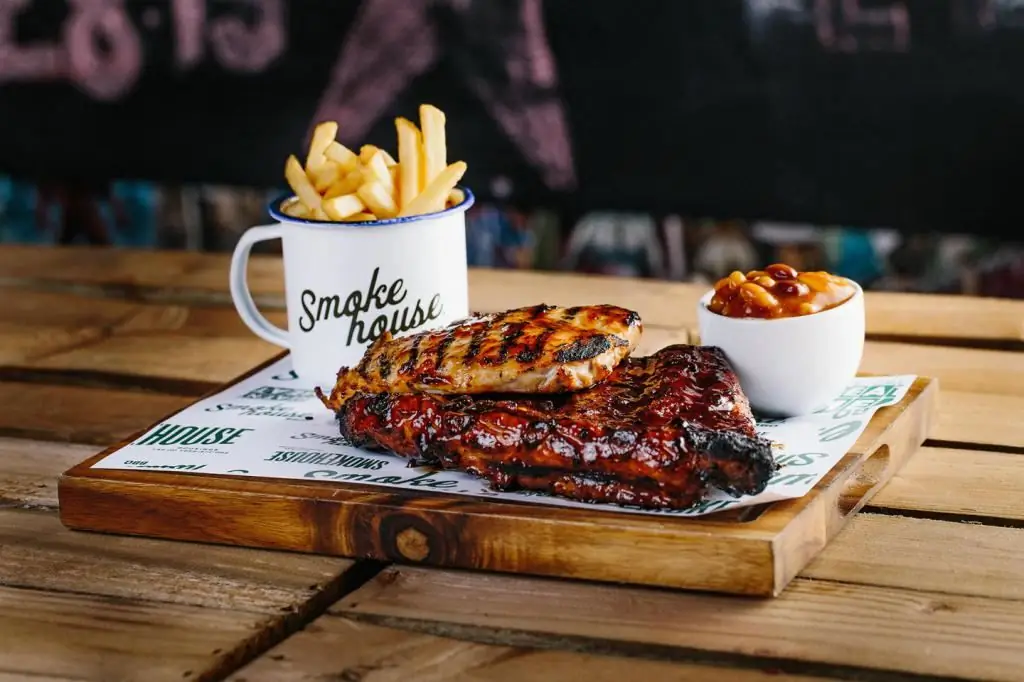
The article deals with such a business as a smoke shop. Learn how to start a business and where to start. About how to choose equipment and how it should be. About what you need to pay attention to when choosing suppliers, and about the process of producing smoked products
Hairdresser at home: preparation of necessary documents, drawing up a business plan, selection of necessary equipment, goals and stages of development
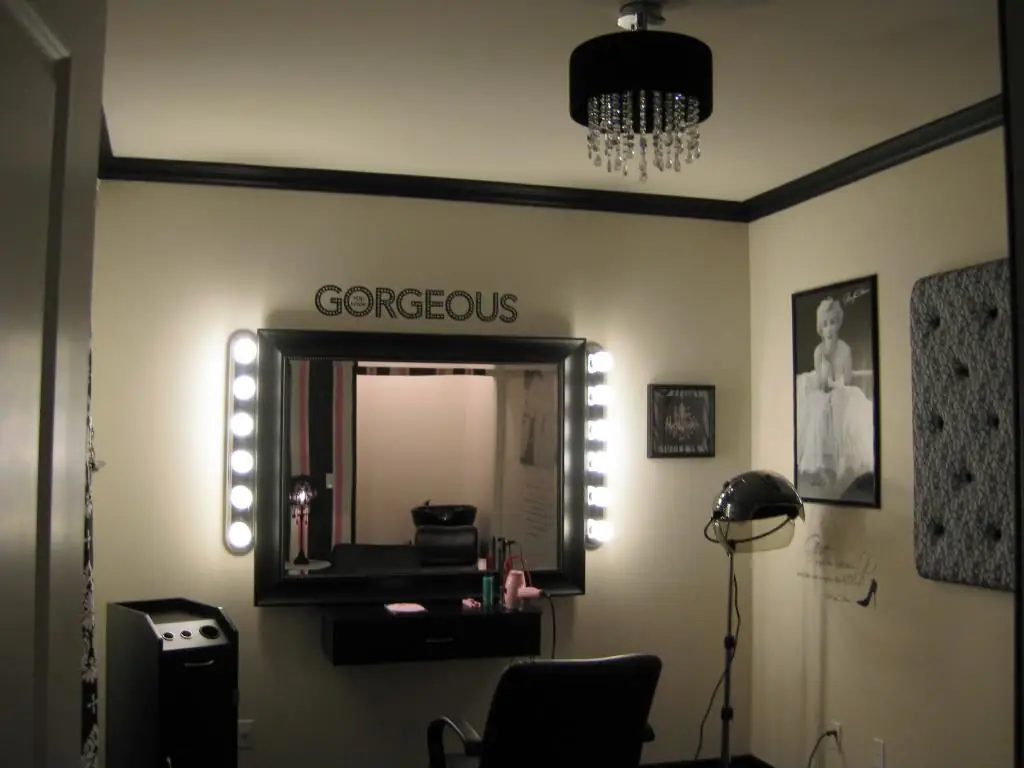
Hairdressing business for creative people is a very promising and interesting business. Well, if there is no money to open a large salon, then at first it is quite possible to start your project from the first stage. For this, a hairdressing salon at home can be organized, which does not require large investments. Is it worth it to engage in such a business, and what steps will you need to go through to open it?
Oxyfuel cutting of metal: technology, necessary equipment, safety precautions
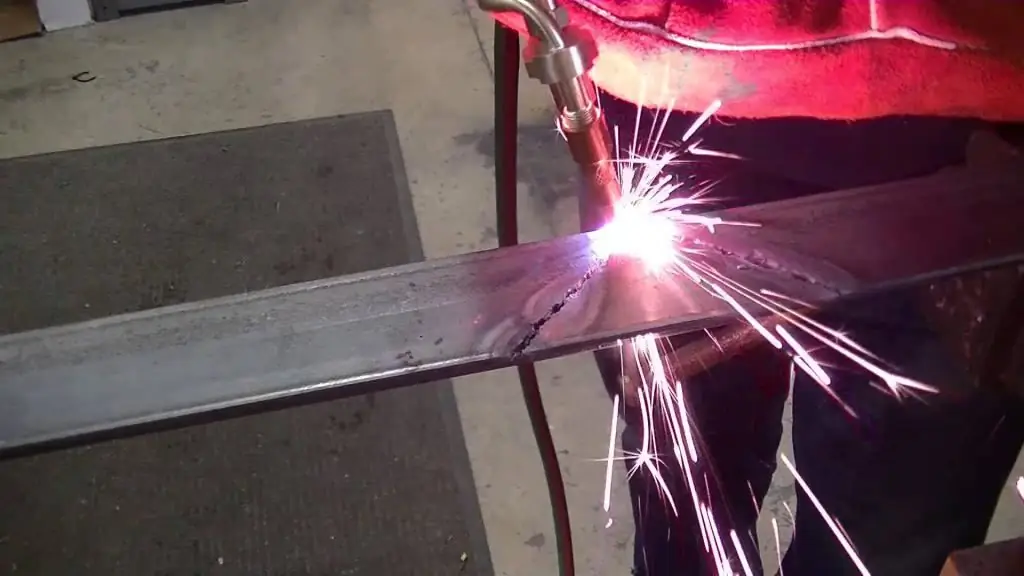
Oxy-fuel cutting of metals (in the literature you can find the term "oxy-fuel cutting") is actively used in industry for cutting sheet material from steel and other alloys into workpieces of the required length. The article contains information about the technology itself, about the necessary equipment and basic safety precautions for oxygen cutting of metals and other materials
Foam block: foam block dimensions, history of appearance and application prospects
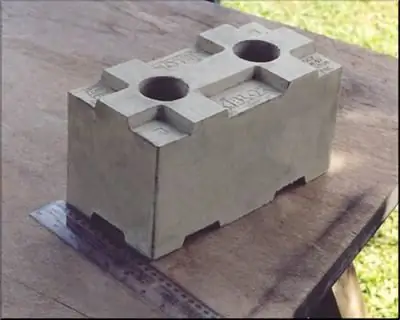
Each movement of the bricklayer is performed at a certain speed. An ordinary clay brick weighing about 3 kg or a large foam block of the same mass will be installed in the wall in the same time. But the dimensions of the foam block are eight or even twelve times the size of a brick, which dramatically increases the speed of masonry. Another important advantage of a light and warm building material is that it requires an adhesive rather than a complex cement-sand mortar
Production of polyurethane foam: technology, raw materials, equipment
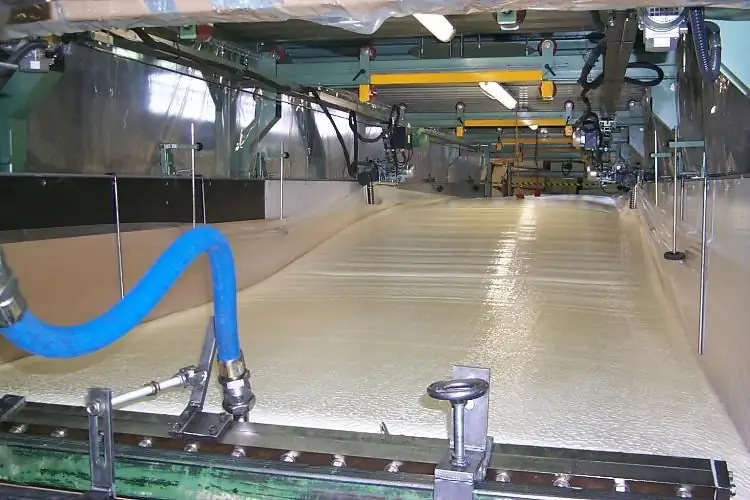
Mounting foam from the usual means of sealing window openings has long passed into the status of a full-fledged building material, which is widely used in a variety of types of work. The variety of applications of this product also determines the need for a differentiated approach to the technologies of its manufacture. However, the differences in foam production methods are more of a cosmetic nature, without affecting the basic technological processes