2025 Author: Howard Calhoun | [email protected]. Last modified: 2025-01-24 13:10
Wood in the form of finished lumber, plywood and particle board continues to be a basic consumable raw material for many industries and construction. Its environmental friendliness and flexibility in processing allow it to compete even with high-tech fiberglass. At the same time, there are also disadvantages of the material, due to low strength and sensitivity to aggressive media. They can be minimized by special pretreatment methods. In particular, chamber drying of wood with thermal action is one of the most common ways to improve its technical and physical properties.
Applied equipment
There are different types of drying units, the general principle structure of which provides for the presence of heat carriers. From them, hot streams are distributed over the surface of the target material. The basic classification distinguishes drying chambers of dielectric and convective types. Dielectric models generate thermal energy in the process of converting high-frequency currents.
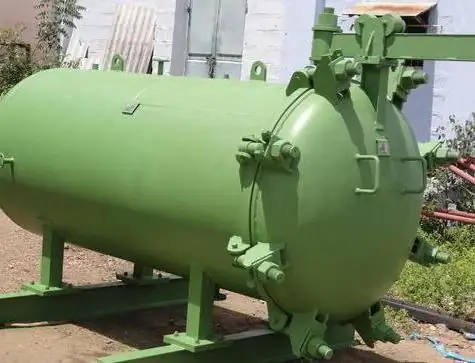
In turn, convective units pump heat flows to the lumber through preheated air, whichpromotes moisture removal. The drying agent in such an operating scheme is heated together with water vapor. The mixture is then circulated in a heat exchanger. A convective chamber for drying wood can use fire-tube, steam-water, and induction carriers as functional elements (heat conductors). Sometimes gas chambers are also used, which emit large amounts of thermal energy. Both dielectric and convective models of dryers can operate in a vacuum, that is, at low pressure.
Material preparation
The quality of drying largely depends on how correctly the stacks were prepared - the so-called packages with lumber, which are specially formed for laying in the chamber. For example, uneven drying and deformation of individual sections on the boards will just be the result of improper packaging.
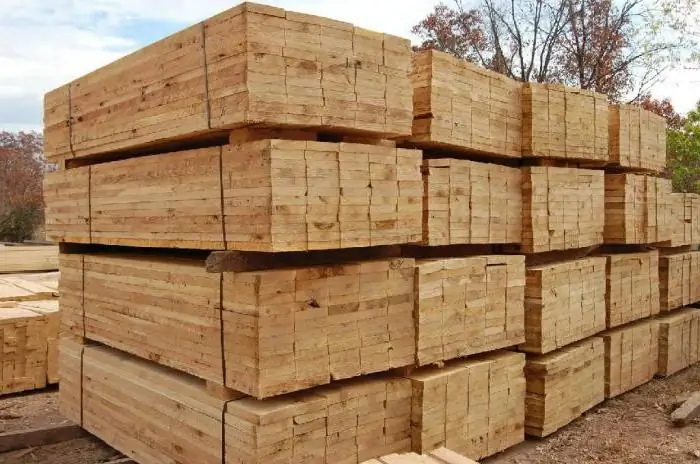
Usually two methods of this kind of preparation are used:
- single stack;
- batch bookmarking.
In the first case, one stack includes several boards stacked in the same configuration. Batch laying assumes that the lumber will be stacked in several ready-made stacks. A rigid platform with a flat surface is used as the basis for the stack. It can be a rail car formed by separate tracks.
In order for chamber drying of wood to be carried out without leakage of the heat agent, underloading of the stack is not allowed. It must be completely filled with either boards of the same length, orlumber of different sizes in a row. Between the joined boards, one or more layers of lining are provided.
Modes
There are three categories of drying:
- The first category is a high-quality mode, carried out at a temperature of about +60+70°С. This mode allows you to dry the material to a moisture content of 6-8%. The products obtained in this way of processing are distinguished by high technical and operational indicators, which make it possible to use the material in instrument and mechanical engineering, in load-bearing building structures, in the production of engineering equipment elements, etc.
- The second category provides a mode with bringing the humidity level up to 8-10%. For such purposes, drying chambers operating at temperatures up to + 75 ° C are used. The target area for the use of materials processed in this mode is furniture production, as well as the manufacture of joinery and building structures.
- The third category of drying allows you to get medium quality lumber, the moisture content of which can reach up to 15%. From such wood, containers, moldings and inexpensive building materials are later produced.
Heating wood
Primary heating is required to prevent stress processes in the internal structure of the lumber during the main drying. An intense, but short-term thermal effect is produced, during which moisture does not evaporate. In parallel with the heat treatment, saturated steam is sent to the chamber. This function is performed by a group of fans with heaters. Evaporation processmoisture throughout the thickness of the material will begin only after the cessation of thermal exposure.
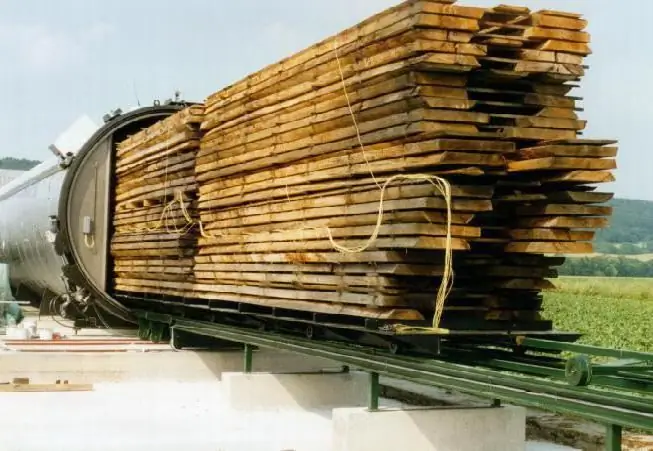
Again, so that chamber drying of wood does not damage its structure, already at the first stage of heating, the balance between the temperature regime and the rate of moisture drop is regulated. If this balance is disturbed, there is a risk of cracking. The duration of this procedure is determined by the external conditions and characteristics of the wood - an average of 1 to 2 hours.
Main Stage
After the initial warm-up, drying follows immediately. But the transition should be gradual, which is reflected in the slow opening of the air exchange dampers that remove moisture. At the same interval, the optimal parameters of heat flows are set. The temperature regime, in turn, is regulated by the level of opening of the shutters of the chamber. If it is required to increase the saturation of the agent, the supply pipes are completely closed.
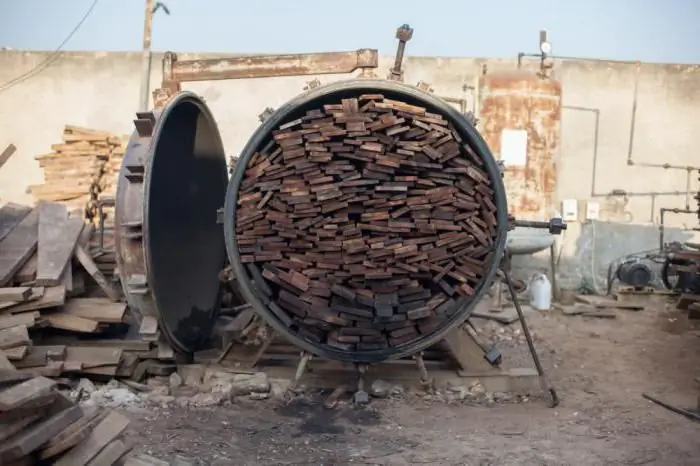
Also, the degree of saturation of the thermal effect can be adjusted by starting the steam generator. However, when the hood is open, steam injection systems cannot be connected. In the process of performing the operation, chamber drying of wood is controlled by the characteristics of the temperature and its error. In production, these values are usually logged every hour.
Moist heat treatment
This is also a kind of intermediate stage, for which special environmental conditions are created: it must provide a high intensity of moisture removal andstable temperature. Such an environment is created by means of the same steam injection with the heaters turned on. Fans and exhaust ducts can be involved in the regulation. The optimum temperature for this processing mode should be 6-7°C higher than the medium in the main drying stage, but at the same time be below +100°C.
It is important to emphasize that moisture-thermal treatment is not applied to all tree species. For example, technologies for the manufacture of dry timber provide for the use of this operation for sawn timber from cedar, pine, linden, the thickness of which exceeds 60 mm. Thick workpieces can be wet-heated several times to completely cover the internal structure.
Ending the process
After drying, a conditioning treatment is carried out, the purpose of which is to equalize the moisture and structure of the material. By means of humidifiers and heaters, a special environment is formed in which overdried areas of lumber are moistened, and insufficiently dried ones dry out. In time, such processing lasts several hours - the specific duration depends on the volume of the bookmark and the parameters of the material.
Indicators of moisture content of wood after chamber drying with conditioning treatment also vary from 6 to 15% depending on the applied mode. Further, after pre-cooling, the stacks are unloaded from the chamber. If necessary, an additional operation of forced cooling with ventilation can be activated.
Pros of technology
Chambers with temperature and humidity treatment allow for drying processes with full preservation of the environmental friendliness of the material. In most cases, such processing methods do not require the use of active chemicals that increase the efficiency of the process. The high quality of the result is also noted. If the operator did not make mistakes when organizing the process, then the resulting beam will acquire high strength and protective qualities.
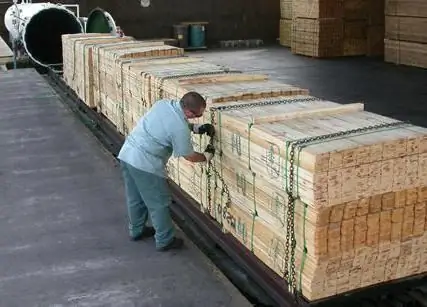
Many people also point to the high productivity of chamber drying of wood. Pluses and minuses, however, converge in this characteristic. On the one hand, batch processing really makes it possible to serve large volumes of wood in short time intervals. On the other hand, the impossibility of processing small packages with a reduced load limits the scope of such equipment.
Cons of technology
The main criticism of this drying technology comes down to the risk of numerous defects in the lumber during the operation. One of the most common of these is warping. Violation of technology can provoke both longitudinal and transverse deformations.
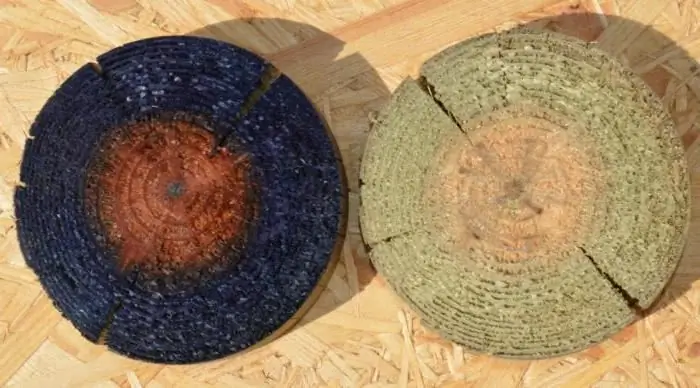
Usually, such processes are the result of insufficient moisture removal before the main stage of drying. Often the material receives defects in the form of cracking at the ends. Similar flaws occur if the lumber dryer was operated in the shaped mode during the initial stage.warming up. The technology requires that this process, even at minimum temperatures, be carried out in conditions of softening the structure of the lumber.
Conclusion
The simplification of the principles of management and maintenance of processing units contributed to the formation of entire segments of equipment designed for domestic use. How justified is the organization of your own line for drying lumber? This will depend on processing volumes.
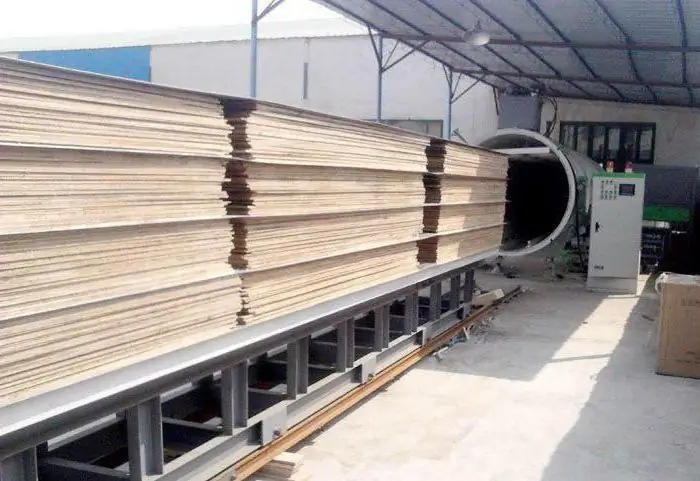
And it is also important to consider the cost of chamber drying of wood. The price of 1 m3 averages 2-3 thousand rubles. Of course, if you build your own house from a bar, then the benefits will be obvious. But the equipment itself is not cheap, not to mention the nuances of operation and the risks of getting the same defects without professional support.
Recommended:
Heat-treated wood: main characteristics, production technology, pros and cons

Almost every one of us has come across such a concept as heat-treated wood. However, few have thought about what it really means. Meanwhile, this material can be considered innovative. Due to the high temperature - from +150 °C to +250 °C - the material is strong and durable
Wood processing technology and production of wood products
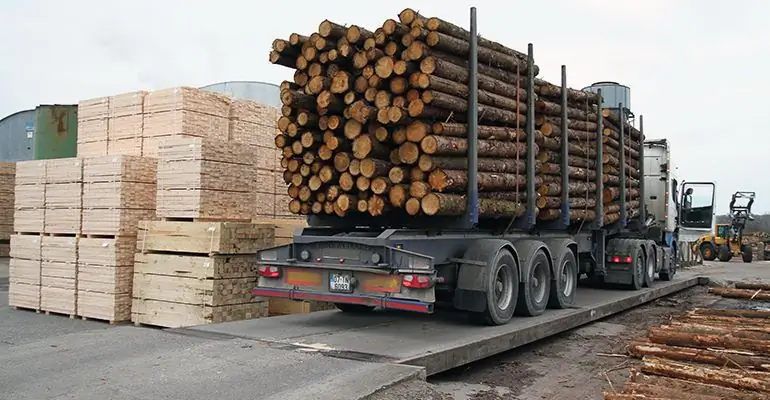
Wood is an unusual and especially valuable material. For all its familiarity, it has an amazing set of technical and physical properties that a person cannot repeat with the help of synthetic substitutes. This is due to the extensive use of blanks made of natural wood in a variety of industries. Modern wood processing technologies and the production of wood products in general make it possible to provide people with furniture, building materials, decorations, utensils, etc
Wood planing: types, equipment and process technology
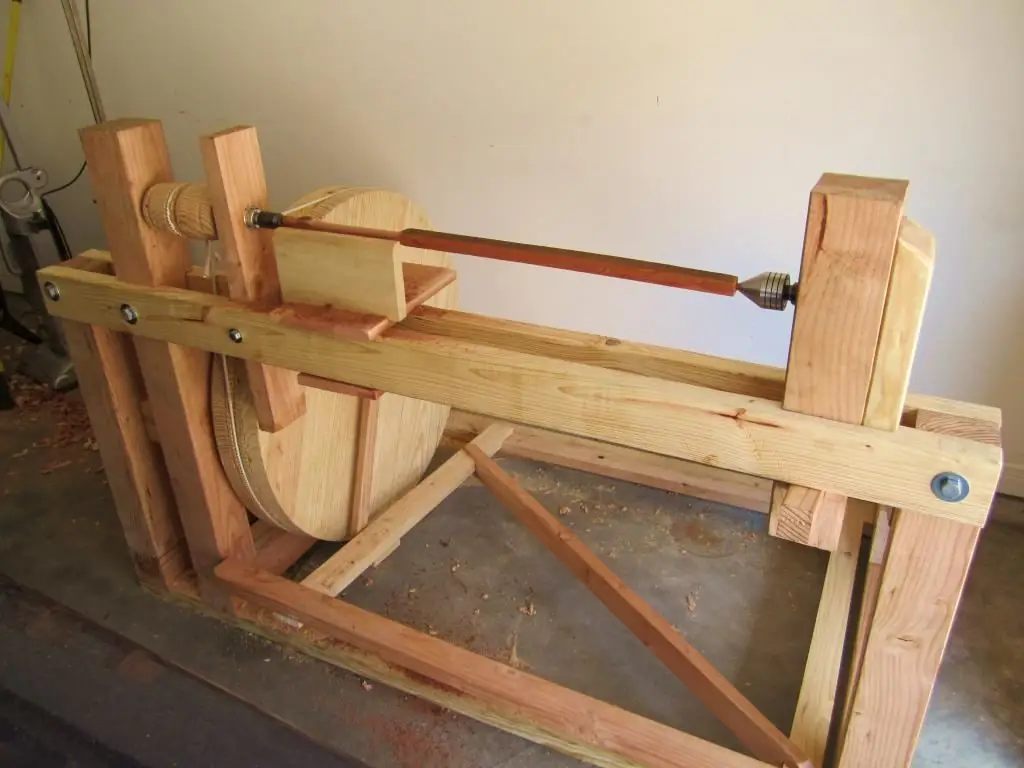
Wood planing is one of the types of processing of this material. This operation can be carried out both manually and on machines. It is important to understand that with the help of planing, any wood blank takes the desired shape and shape
Drying wood and its features
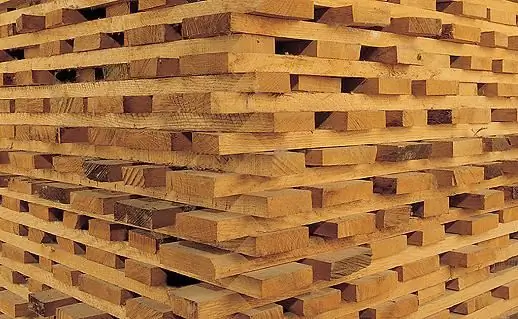
In order for wood products to be durable and retain their original dimensions, wood drying is necessary, which has many features
What is better to open: LLC or IP? Pros and cons of sole proprietorship and LLC. The difference between sole proprietorship and LLC
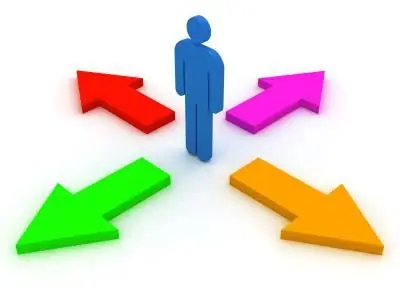
What is better to open: LLC or IP? Having decided to throw off the shackles of office slavery and no longer work "for your uncle", developing your own business, you should know that it must be legal from a legal point of view