2025 Author: Howard Calhoun | [email protected]. Last modified: 2025-01-24 13:10
Magnesium alloys have a number of unique physical and chemical properties, the main of which are low density and high strength. The combination of these qualities in materials with the addition of magnesium makes it possible to produce products and structures with high strength characteristics and low weight.
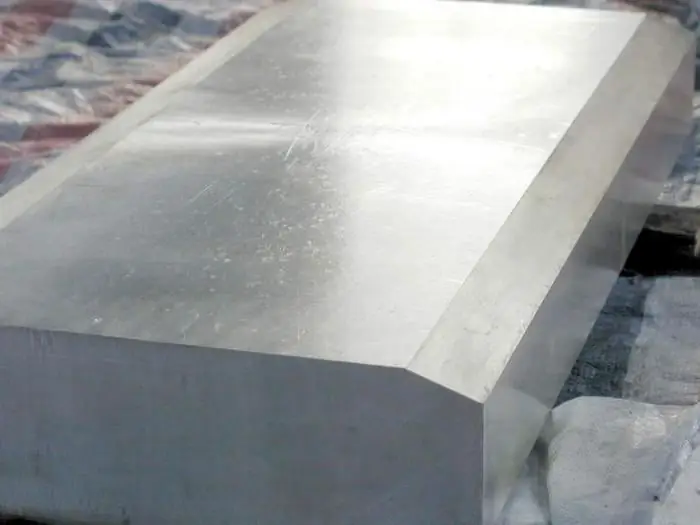
Magnesium characteristics
Industrial production and use of magnesium began relatively recently - only about 100 years ago. This metal has a low mass, as it has a relatively low density (1.74 g / cmᶟ), good resistance to air, alkalis, gaseous media containing fluorine and mineral oils.
Its melting point is 650 degrees. It is characterized by high chemical activity up to spontaneous combustion in air. The tensile strength of pure magnesium is 190 MPa, the elastic modulus is 4,500 MPa, and the relative elongation is 18%. The metal has a high damping ability (effectively absorbs elastic vibrations), which provides it withexcellent shock tolerance and reduced sensitivity to resonant phenomena.
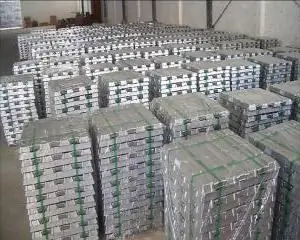
Other features of this element include good thermal conductivity, low ability to absorb thermal neutrons and interact with nuclear fuel. Due to the combination of these properties, magnesium is an ideal material for creating hermetically sealed shells of high-temperature elements of nuclear reactors.
Magnesium alloys well with various metals and is one of the strong reducing agents, without which the metallothermic process is impossible.
In its pure form, it is mainly used as an alloying addition in alloys with aluminum, titanium and some other chemical elements. In ferrous metallurgy, magnesium is used for deep desulfurization of steel and cast iron, and the properties of the latter are improved by graphite spheroidization.
Magnesium and alloying additives
The most common alloying additions used in magnesium-based alloys include elements such as aluminum, manganese and zinc. Through aluminum, the structure improves, the fluidity and strength of the material increase. The introduction of zinc also makes it possible to obtain stronger alloys with a reduced grain size. With the help of manganese or zirconium, the corrosion resistance of magnesium alloys is increased.
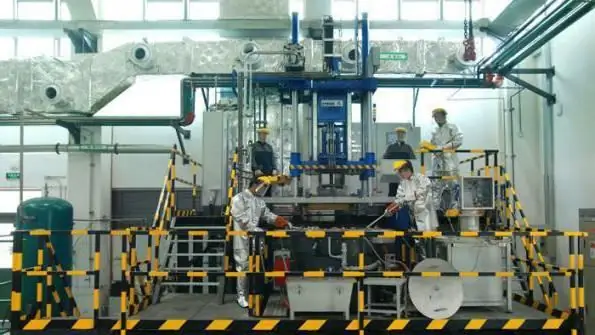
The addition of zinc and zirconium provides increased strength and ductility of metal mixtures. And the presence of certain rare earthelements, such as neodymium, cerium, yttrium, etc., contributes to a significant increase in heat resistance and maximization of the mechanical properties of magnesium alloys.
To create ultra-light materials with a density of 1.3 to 1.6 g/mᶟ, lithium is introduced into the alloys. This additive makes it possible to reduce their weight by half compared to aluminum metal mixtures. At the same time, their indicators of plasticity, fluidity, elasticity and manufacturability reach a higher level.
Classification of magnesium alloys
Magnesium alloys are classified according to a number of criteria. This is:
- according to the method of processing - for casting and deformable;
- according to the degree of sensitivity to heat treatment - into non-hardened and hardened by heat treatment;
- by properties and applications - for heat-resistant, high-strength and general purpose alloys;
- according to the alloying system - there are several groups of non-hardenable and heat-hardenable wrought magnesium alloys.
Casting alloys
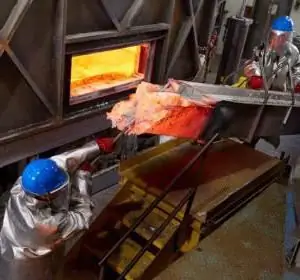
This group includes alloys with the addition of magnesium, designed for the production of various parts and elements by shaped casting. They have different mechanical properties, depending on which they are divided into three classes:
- medium strength;
- high strength;
- heat resistant.
In terms of chemical composition, alloys are also divided into three groups:
- aluminum + magnesium + zinc;
- magnesium + zinc + zirconium;
- magnesium + rare earthelements + zirconium.
Casting properties of alloys
The best casting properties among the products of these three groups have aluminum-magnesium alloys. They belong to the class of high-strength materials (up to 220 MPa), therefore they are the best option for the manufacture of engine parts for aircraft, cars and other equipment operating under mechanical and thermal loads.
To increase the strength characteristics, aluminum-magnesium alloys are also alloyed with other elements. But the presence of iron and copper impurities is undesirable, since these elements have a negative effect on the weldability and corrosion resistance of alloys.
Cast magnesium alloys are prepared in various types of melting furnaces: reverberatory furnaces, crucible furnaces with gas, oil or electric heating, or crucible induction furnaces.
Special fluxes and additives are used to prevent combustion during melting and casting. Castings are produced by casting in sand, plaster and shell molds, under pressure and using investment models.
Wrought alloys
Compared to cast alloys, wrought magnesium alloys are stronger, more ductile and tougher. They are used for the production of blanks by rolling, pressing and stamping. As a heat treatment of products, hardening is used at a temperature of 350-410 degrees, followed by arbitrary cooling without aging.
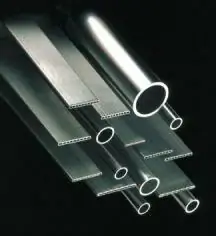
When heatedthe plastic properties of such materials increase, therefore, the processing of magnesium alloys is carried out by means of pressure and at high temperatures. Stamping is performed at 280-480 degrees under presses by means of closed dies. In cold rolling, frequent intermediate recrystallization annealings are carried out.
When welding magnesium alloys, the strength of the product seam may be reduced in the segments where the welding was performed, due to the sensitivity of such materials to overheating.
Fields of application of magnesium alloys
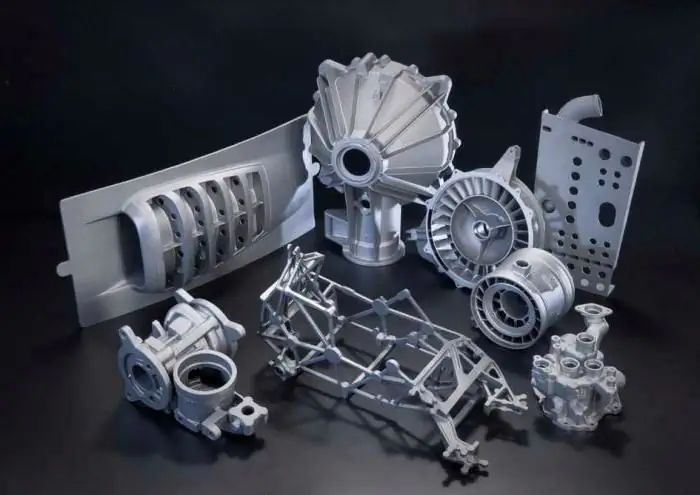
Various semi-finished products - ingots, slabs, profiles, sheets, forgings, etc. are produced by casting, deformation and heat treatment of alloys. These blanks are used for the production of elements and parts of modern technical devices, where the weight efficiency of structures (reduced weight) plays a priority role while maintaining their strength characteristics. Compared to aluminum, magnesium is 1.5 times lighter, and 4.5 times lighter than steel.
At present, the use of magnesium alloys is widely practiced in the aerospace, automotive, military and other industries, where their high cost (some grades contain quite expensive alloying elements) is justified from an economic point of view by the possibility of creating a more durable, faster, powerful and safe equipment that can work effectively in extreme conditions, including when exposed to high temperatures.
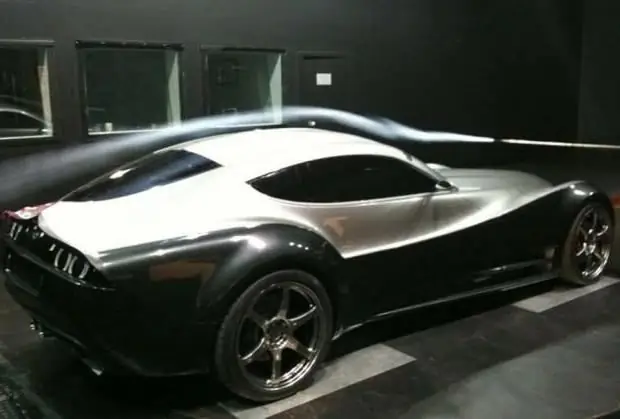
Due to their high electrical potential, these alloys are the optimal material for creating protectors that provide electrochemical protection of steel structures, such as car parts, underground structures, oil platforms, marine vessels, etc., from corrosion processes occurring under the influence of moisture, fresh and sea water.
Alloys with the addition of magnesium have also been used in various radio engineering systems, where they are used to make sound ducts for ultrasonic lines to delay electrical signals.
Conclusion
Modern industry places ever higher demands on materials in terms of their strength, wear resistance, corrosion resistance and manufacturability. The use of magnesium alloys is one of the most promising areas, therefore, research related to the search for new properties of magnesium and the possibilities of its application do not stop.
Currently, the use of magnesium-based alloys in the creation of various parts and structures makes it possible to reduce their weight by almost 30% and increase the tensile strength up to 300 MPa, but, according to scientists, this is far from the limit for this unique metal.
Recommended:
Heat-resistant alloys. Special steels and alloys. Production and use of heat-resistant alloys
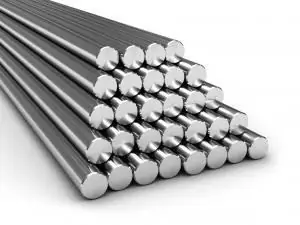
Modern industry cannot be imagined without such material as steel. We encounter it at almost every turn. By introducing various chemical elements into its composition, it is possible to significantly improve the mechanical and operational properties
Zirconium alloys: composition, properties, application
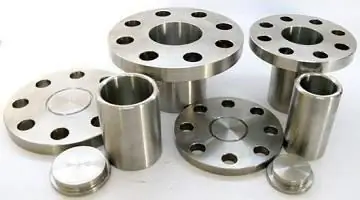
Currently, a material such as zirconium alloy has become quite widely used in some areas. Scientists identify a large number of advantages of this material
Aluminum alloys: properties and processing of metals
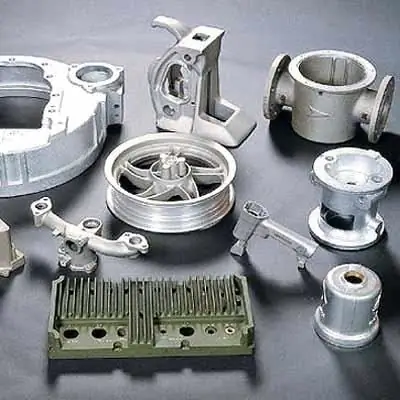
Aluminum alloys are very often used in construction, industry and other manufacturing industries. However, before using them, it is necessary to learn about the properties of alloys, as well as about the features of their processing
Zirconium: alloys based on it. Properties, application
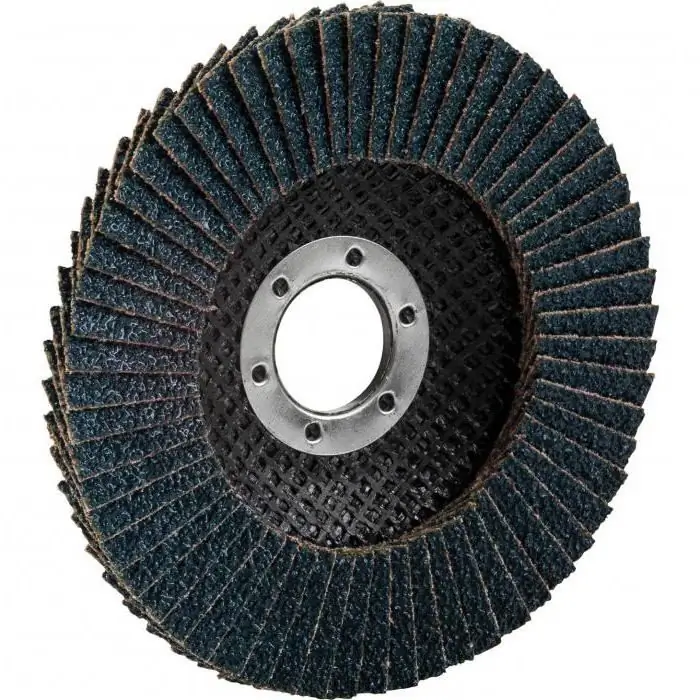
Rare, but at the same time very important in many industries, the metal - zirconium - was first isolated only in 1824. However, it still contained a certain percentage of other elements. Only in the 20th century was it possible to obtain pure zirconium, free from various impurities. Learn more about it
Duralumin is a high-strength aluminum-based alloy with additions of copper, magnesium and manganese: properties, production and application
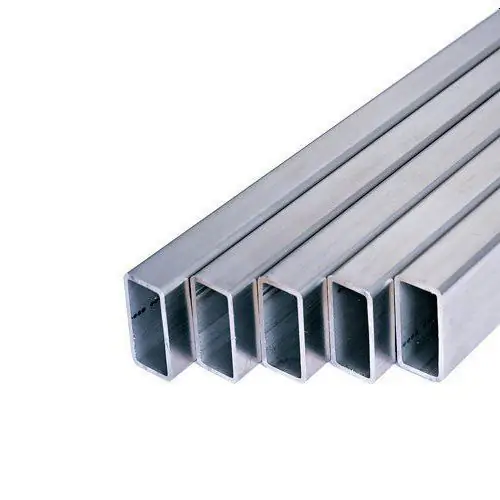
What is duralumin? What are the features of duralumin alloy? Technical and quality indicators of the alloy. A variety of products from this metal and their scope