2025 Author: Howard Calhoun | [email protected]. Last modified: 2025-01-24 13:10
Rare, but at the same time very important in many industries, the metal - zirconium - was first isolated only in 1824. However, it still contained a certain percentage of other elements. Only in the 20th century was it possible to obtain pure zirconium, free from various impurities. Alloys based on it are successfully used for the manufacture of refractories, abrasives, ceramic paints, sandpaper, textiles, deodorants and artificial stones. Of course, we must not forget about the high importance of this metal in medicine. Learn more about him.
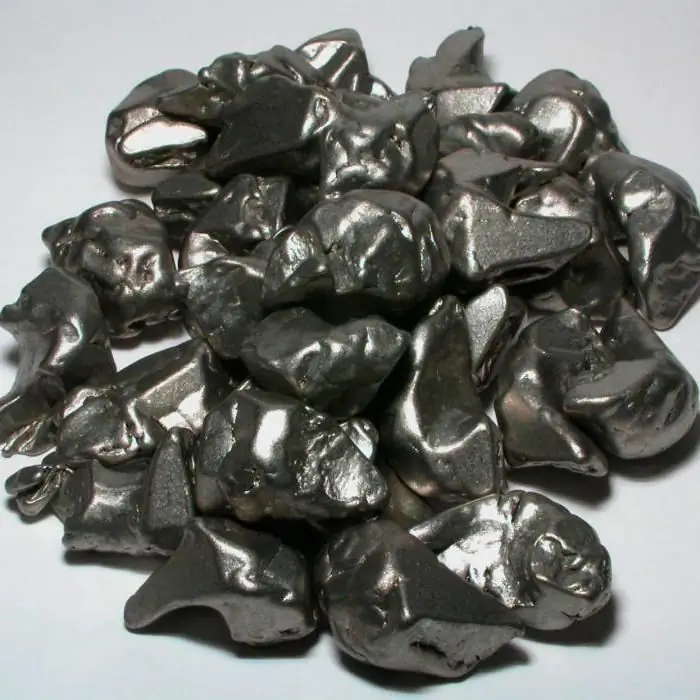
Development of metallurgy
Zirconium is the main component of alloys for nuclear power engineering. But for this it is necessary that it be as pure as possible from various impurities. The fact is that in zirconium ores there is not only such a rare earth element as hafnium, but also nitrogen, carbon and oxygen. And such non-metal impurities are quite dangerous and can be included in the composition of structural materials for nuclear reactors in an amount of no more than millionths of a percent. Therefore, obtaining pure zirconium and alloys onits basis is a rather long and laborious process. First, the concentrate is opened, then it is enriched, unwanted impurities and hafnium are separated.
Pure zirconium looks like a typical metal. In appearance, it is very similar to steel, but at the same time more durable and ductile. Of course, in alloys based on it, its characteristics can vary significantly depending on the amount of other elements. For example, oxygen (greater than 0.6%) will make zirconium more brittle. But there is also a downside: the dioxide of this metal (ZrO2) has a melting point of 2680 °C.
Main construction material
As mentioned earlier, the widest area where zirconium and its alloys are used is the nuclear industry. Their main advantage is that they have a low thermal neutron capture cross section (only 0.18 barns), good corrosion properties and a high melting point. So, TVEL is the main structural fuel element of the core of a nuclear reactor, in which nuclear fuel is placed. It is in it that the fission of heavy nuclei occurs, which means that the fuel element must be made of the most durable and refractory metal, and it must not change the character of neutron absorption in the reactor.
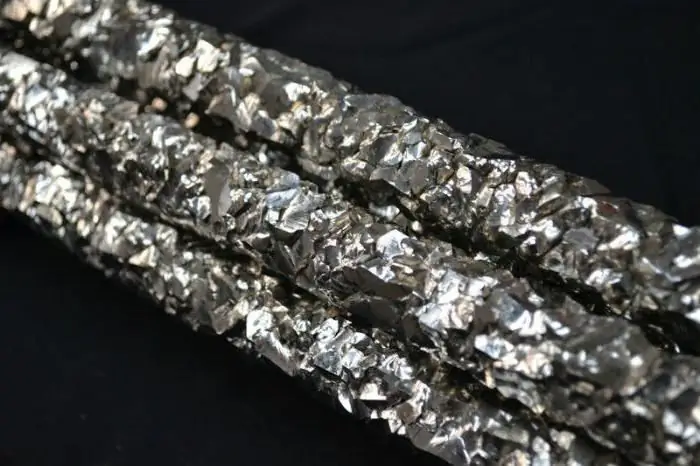
So, zirconium alloys are used to make its shell. The requirements for them are quite strict. So, alloying elements should not worsen its characteristics. In particular, this concerns the small cross section for the capture of thermal neutrons. Zirconium is alloyed in order tosuppress the harmful effect of nitrogen and improve its corrosion properties. Many elements of the periodic system of Mendeleev are not suitable, as they reduce certain characteristics.
The most famous alloy used to make fuel rods is zircaloy. Its main alloying element is tin, and auxiliary elements are iron, chromium and nickel. In Russia, niobium is most often used for alloying zirconium. It also has a low thermal neutron capture cross section, reduces hydrogen uptake, and forms only solid solutions. And this, in turn, provides alloys with high ductility.
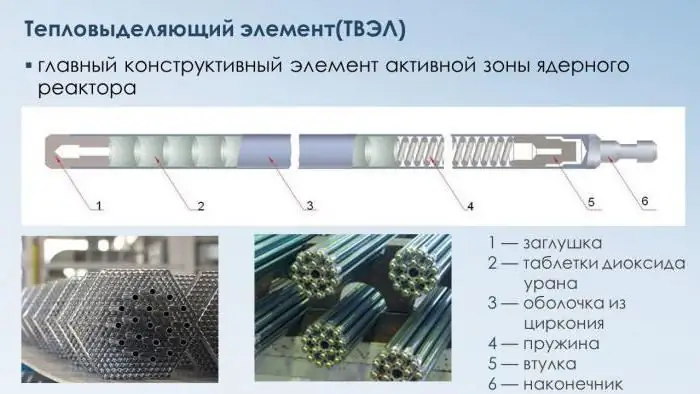
Zirconium alloying
The high corrosion resistance of this metal explains why it is so often used as an alloying element in ferrous and non-ferrous metallurgy. In addition, it is insoluble in hydrochloric and nitric acids and alkalis. Thus, multicomponent alloys of zirconium with magnesium are very popular. In addition, alloying with this metal increases the acid resistance of titanium. Alloys of zirconium with copper have high strength and electrical conductivity. Quite often it is also used as an additive in the production of various steel grades. This allows you to remove sulfur, nitrogen and oxygen from them.
Medical industry
Considering zirconium and its alloys, one cannot fail to mention one more area of their use. In the medical industry, they occupy far from the last place. More recently, steel andtitanium alloys. However, in some cases, the body rejected these metals, against which an allergic reaction appeared. Modern medicine uses zirconium and titanium alloys for the manufacture of staples, plates, implants, dentures and their fixation mechanisms.
Because this metal and its compounds are non-irritating to bones and surrounding soft tissues, it has been successfully used in jewelry making. For example, zirconium earrings do not cause an allergic reaction and heal a wound on the earlobe no worse than gold.
Power consumption
Alloy of aluminum and zirconium has many positive characteristics and is therefore successfully used in the energy industry. The fact is that steel and copper wires weigh quite a lot, and often old supports cannot withstand such a load. In 1960, in Japan, a group of scientists produced a series of alloys of aluminum and zirconium. They determined that such a material can be used for a long time at high temperatures (150-230 ° C) and at the same time it will be quite light. This allows it to be used for the manufacture of high-temperature wires. This increases the reliability and efficiency of electrical networks.
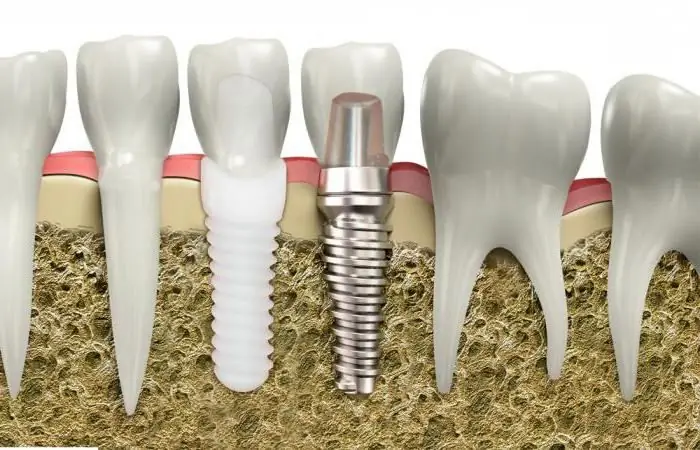
Other applications for zirconium compounds and alloys
In many antiperspirants, you can find such a component as Aluminum Zirconium Tetrachlorohydrex. It is a chemical compound that absorbs sweat and its odor. Scientists have found that it is notabsorbed into the skin, and therefore, can not cause severe harm to he alth. Despite this, aluminum-zirconium-tetrachlorohydrexglycine is banned in the EU and the US.
Zirconium oxide is used to make electrocorundum. It is obtained by smelting in tilting electric furnaces. Zirconium electrocorundum turns out to be quite strong and allows processing materials with a large clamping force. Most often it is used for rough and rough grinding.
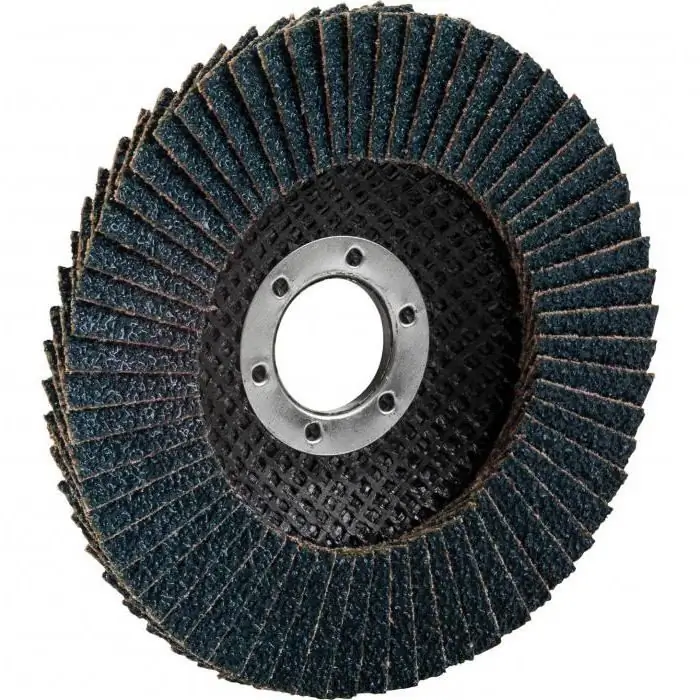
In general, it should be noted that zirconium and its alloys have a high melting point, chemical resistance, and a low coefficient of thermal expansion. It is for this reason that it is actively used in a wide variety of fields.
Recommended:
Magnesium alloys: application, classification and properties
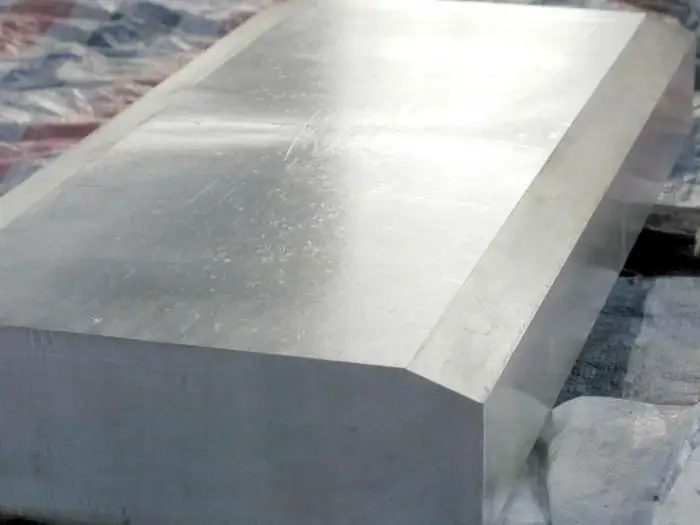
Magnesium alloys have a number of unique physical and chemical properties, the main of which are low density and high strength. The combination of these qualities in materials with the addition of magnesium makes it possible to produce products and structures with high strength characteristics and low weight
Heat-resistant alloys. Special steels and alloys. Production and use of heat-resistant alloys
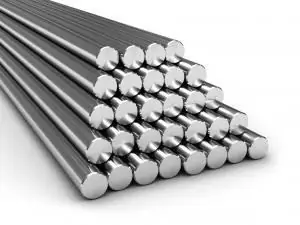
Modern industry cannot be imagined without such material as steel. We encounter it at almost every turn. By introducing various chemical elements into its composition, it is possible to significantly improve the mechanical and operational properties
Zirconium alloys: composition, properties, application
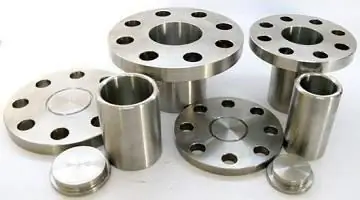
Currently, a material such as zirconium alloy has become quite widely used in some areas. Scientists identify a large number of advantages of this material
Aluminum alloys: properties and processing of metals
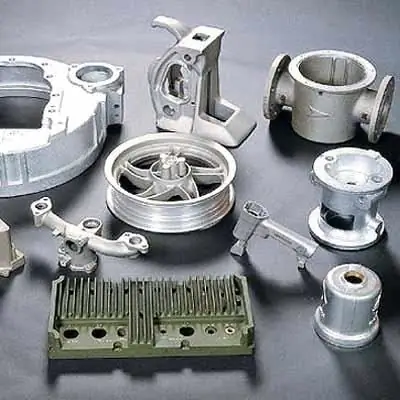
Aluminum alloys are very often used in construction, industry and other manufacturing industries. However, before using them, it is necessary to learn about the properties of alloys, as well as about the features of their processing
Duralumin is a high-strength aluminum-based alloy with additions of copper, magnesium and manganese: properties, production and application
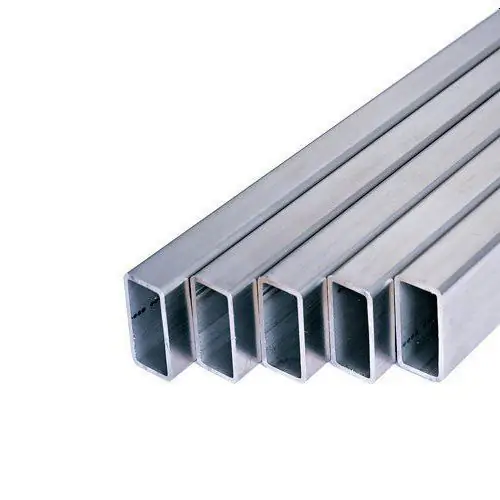
What is duralumin? What are the features of duralumin alloy? Technical and quality indicators of the alloy. A variety of products from this metal and their scope