2025 Author: Howard Calhoun | [email protected]. Last modified: 2025-01-24 13:10
Bending machine allows you to give the workpiece the desired shape by stretching the outer and compressing the inner layers of the part. Only the sections located along the axis retain their original dimensions. The equipment is presented in various designs, differs in the type of drive, additional equipment, dimensions.
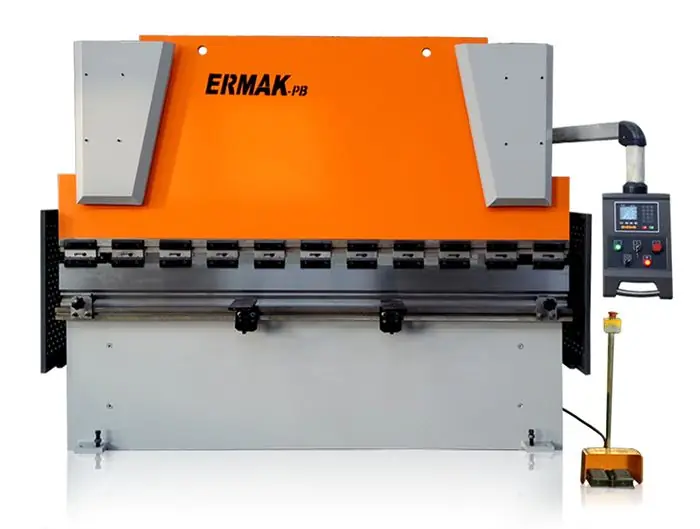
Design
Most bending machines have a similar general design. This includes the following items:
- Table for rear sheet fixation. The part is intended for the location of the workpiece to be processed, which will move on the surface in the required direction. A bender and a cutter are also provided on the table supports.
- Knife roller type. It provides a cut of metal, must have a strong and sharp base.
- Front stops. Allows you to adjust the width of the cut.
- The wooden stand serves as an additional support.
- Goniometer - allows you to accurately set the processing angle.
- Fasteners in height - adjust the same parameter of the product.
Varieties
Sheet metal bending machines come in several types, andnamely:
- The manual version is compact in size and is used for moderate-scale work. It can process copper, aluminum, galvanized and steel sheets. Working on such equipment does not require special qualifications.
- Mechanical equipment functions by transforming energy from a pre-spun flywheel.
- Electro-mechanical versions operate with an electric motor, chain or belt drive and gearbox.
- Hydraulic counterparts use a hydraulic cylinder in their design.
- Pneumatic modifications are powered by a pneumatic cylinder, ideal for processing materials coated with varnish or paint.
- Electromagnetic machines bend sheets with a powerful electromagnet, used to form segments and boxes.
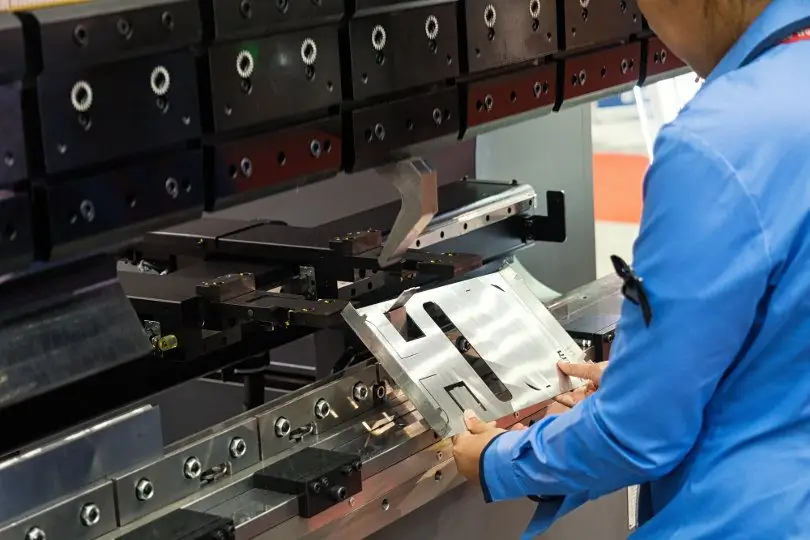
Hand tools
On such equipment there are restrictions on the depth of feed of the workpiece, the working length of processing and the maximum thickness of the part. Manual sheet metal bending machines function as follows:
- metal billet is pressed against the table by a beam;
- the sheet is bent with a special element to the required angle;
- the thickness of the bend on such a device should be approximately two millimeters.
Because the manual versions are relatively lightweight, they can be transported directly to the construction site or workshop.
Hydraulic bending machinemachine
Such equipment greatly facilitated the processing of metal blanks. It functions according to this principle:
- an energy carrier is a liquid that pushes the plunger out of the cylinder under pressure, thereby ensuring the movement of the movable transverse element with the striker;
- The sheet placed on the table is subjected to an appropriate force, causing the workpiece to bend.
Usually considered fixtures are used to transform sheets along the entire length of the countertop or for deep processing of a part. Efficiency of work and high productivity is ensured by the precise functioning of the cylinders. Without problems, you can control the movement, speed and braking of the crawler.
Application of hydraulic type bending machines:
- manufacturing of signs, air ducts, roofing elements;
- release of additional products;
- production of material for interior and exterior decoration of buildings;
- preparation of metal profiles of various shapes and sizes.
Hydraulic analogues are much more productive than manual versions, they allow processing thicker workpieces.
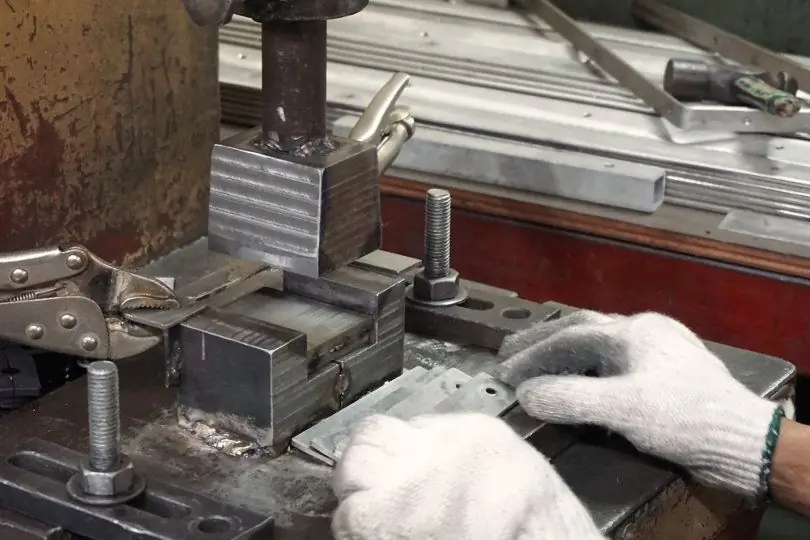
Electromechanical modifications
Electric bending machine includes in its design a powerful frame, a bending beam, aggregating with an electric drive and an automatic segment element. For ease of use, the equipment is equipped with a foot control.
Bending machineselectromechanical type are divided into pass-through or through options, which makes it possible to process non-standard workpieces in width, length and height. It is allowed to bend galvanized, cold-rolled metal sheets, copper and aluminum blanks on these devices. Processing thickness - up to 2.5 mm, length - up to 3 meters. On such machines, ebbs, facade cassettes, ventilation parts, roofs, canopies, skates and more are made.
Rebar bending machine
Such equipment allows you to bend rods of various sections at the desired angle. The machine is controlled by one operator, who sets the mode of processing workpieces. The rest of the work is done by a mechanical bending unit operating in automatic mode. Devices are in demand in the production of metal structures, building materials, fences.
Automatic rebar bending machine is designed for a long time of work, it is appropriate to operate it when doing a large amount of work. It processes the following types of products:
- rebar and carbon steel;
- metal stripes;
- threaded steel bars;
- cut-to-length steel.
The unit in question will provide high performance and decent quality of the final product, along with a high rate of accuracy and safety. You can control the equipment manually or with a foot controller.
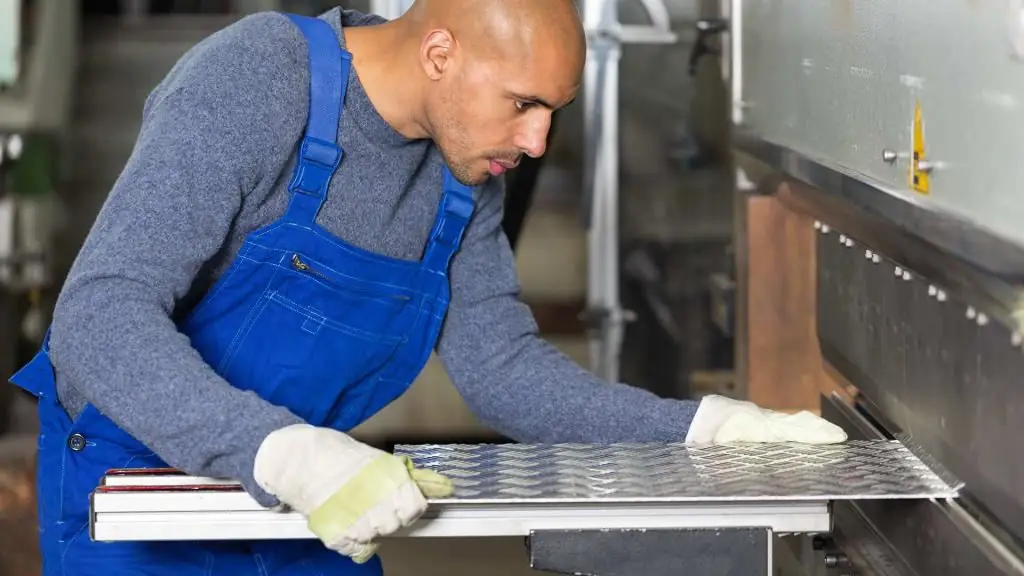
Pipe bending equipment
According to the principle of operation of pipe bending machinessubdivided similarly to leaf variants. They also differ from each other in the way they bend. The design of the device and its performance depend on this factor. There are three categories of profile benders.
- A unit that works by extrusion. In this case, the geometry of the profile pipe is modified using a deforming roller mechanism that acts as a punch. The matrix on such equipment is not provided, its role is played by a pair of strong supports mounted on opposite sides of the bend. Such elements are swivel shoes or rollers. Since the force builds up gradually while ensuring a constant perpendicular relationship to the workpiece, the method allows you to get a good final result. The method is appropriate for small-scale work.
- The second option is pressing. For the transformation of the product, the principle of locksmith yews is applied. A piece of pipe is placed between the die and the punch. Their profiles must exactly repeat the geometry of the workpiece to obtain a high-quality bend. In addition, it is necessary to take into account the residual deformation of the metal. This bending machine is suitable for home use where high precision is not required.
- The third way is to roll pipes. It is universal for both thin-walled and thick-walled products. The desired configuration is obtained by pulling the part between one rotating and two supporting rollers.
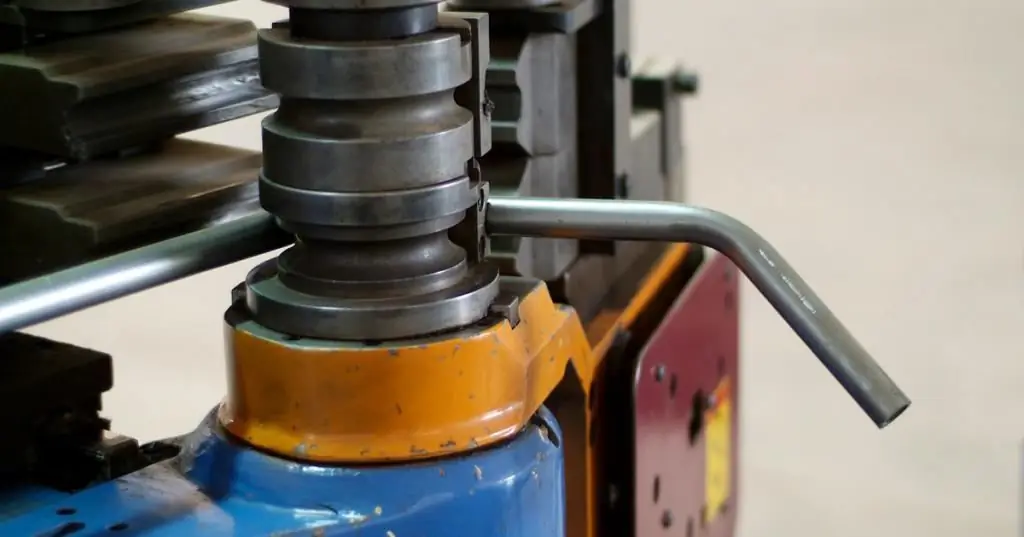
Wire bending methods
For thesepurposes, several types of equipment are provided: from the simplest manual fixtures to automated CNC wire bending machines.
Let's briefly consider all the modifications:
- Homemade version. The unit is a metal frame with a guide roller, a metal bar and holes. The above elements are screwed to it, and plates are welded to the bottom of the frame. After installing the rollers, the bar structure is attached to the corner.
- Universal CNC bending machine. On such equipment, elements of 2D and 3D configurations are manufactured. Management is carried out by a special computer that executes the program embedded in it. Such devices have high labor productivity and wide possibilities.
- Pushing machine. The principle of operation is based on the translational movement of the processed material through the profile bender. Rolling rollers give the workpiece a predetermined configuration. Working on such equipment requires high qualifications.
Other types of wire machines
Among the modifications for wire processing, three more options can be noted:
- Breaking machines. Devices of this type are focused on the manufacture of round parts. The workpiece is fed onto a shaft with a pre-set radius using guide rollers. When creating the rotation of the shaft, several bends of the wire around the working finger are carried out. This machine tool produces only one type of product. To change the configurationproducts require commissioning.
- A machine that processes wire from a metal bar. With the help of this equipment, it is possible to carry out stamping and carving on workpieces. Among the disadvantages of this equipment are low productivity and the presence of an additional device for supplying parts, which has a complex design.
- Bay analogue. It works by unwinding a coil of wire. converting it to a straight rod. The output is a product that has the desired shape. This type of equipment is used for mass production, has a high rate of productivity.
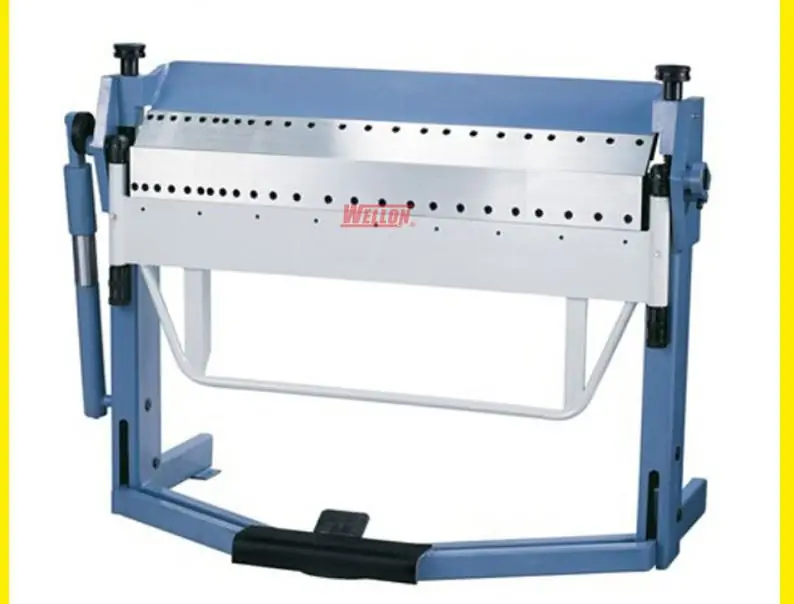
How to adjust the benders?
Because the machines are usually delivered partially disassembled, their installation requires certain rules to be followed. After installing the unit on the working platform, proceed to install the remaining elements. Consider setting up a bending machine using the example of a manual version for processing sheets.
Adjusting the height of the bending beam is done by loosening the fixing bolts, and then turning the control screw to the left or right to decrease or increase the height. After the adjustment is completed, the clamps must be tightened. It should be noted that changing the height of the beam makes it possible to adjust the bending radius of the workpiece, which should not be less than the thickness of the sheet.
Adjusting the edge of the traverse and rollers
Adjustment of the spatial position of the edge of the rotary bending traverseaffects the quality of work when changing the thickness of the workpiece. The procedure is performed with a double-sided roman nut, by turning it counterclockwise or clockwise.
The force line of the cutting roller mechanism must pass strictly along the pressing edge of the sheet being processed. The required height is corrected by placing the lower support roller and adjusted by means of the control screw.
The spatial placement of the cutting knife on the machine must be parallel to the position of the bending beam. If this requirement is not met, the elements should be adjusted using the control screws. When tearing off the lower roller fixture from the sheet surface and pulling the knife to the side, it is recommended to reduce the width of the left carriage by tightening or loosening the rollers.
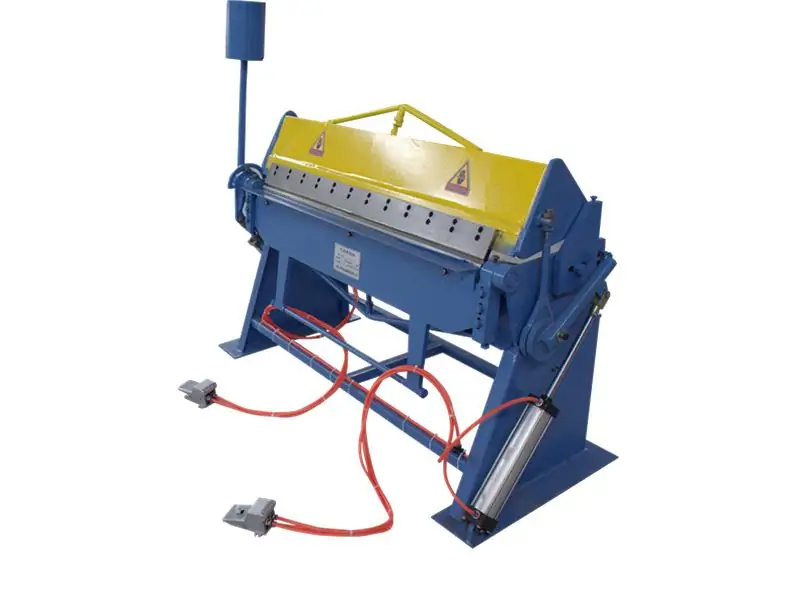
Summary
Bending machines, the characteristics of which are listed above, are widely used in industry, small specialized enterprises, as well as in the private sector. When choosing equipment, one should take into account the frequency of its operation, the average amount of work, as well as the required level of qualification of workers. For example, for a house or a small construction site, the simplest variations are suitable, which almost any worker with experience in construction can handle. If high precision is required, it is better to use professional equipment (hydraulic, electrical units or CNC machines.
Recommended:
Bending machines: types, description, principle of operation
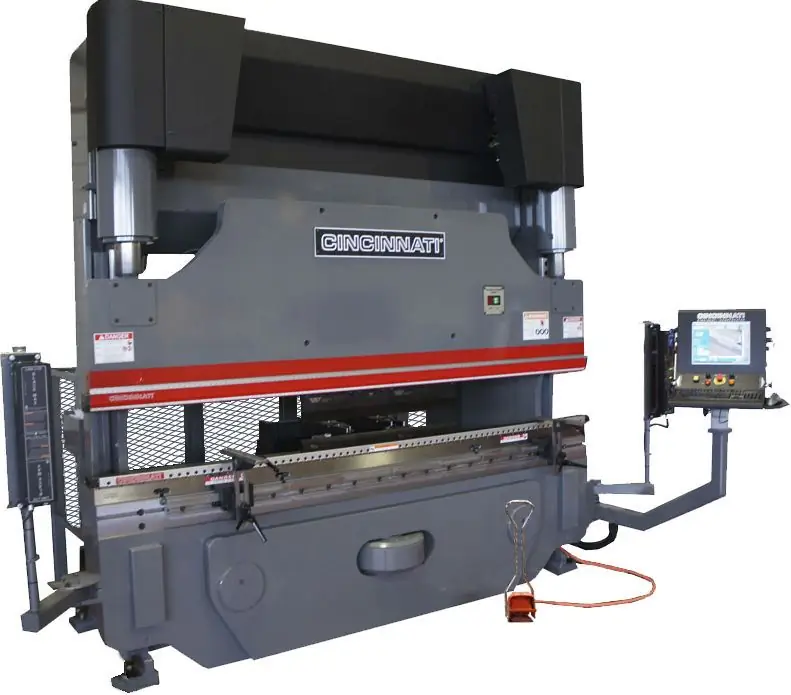
Bending machine: description, specifications, features, principle of operation, photo. Edge bending machines: varieties, device, design, parameters, manufacturers. Manual and rotary hemming machines: what's the difference?
Sheet metal cutting: description, types. metal bending
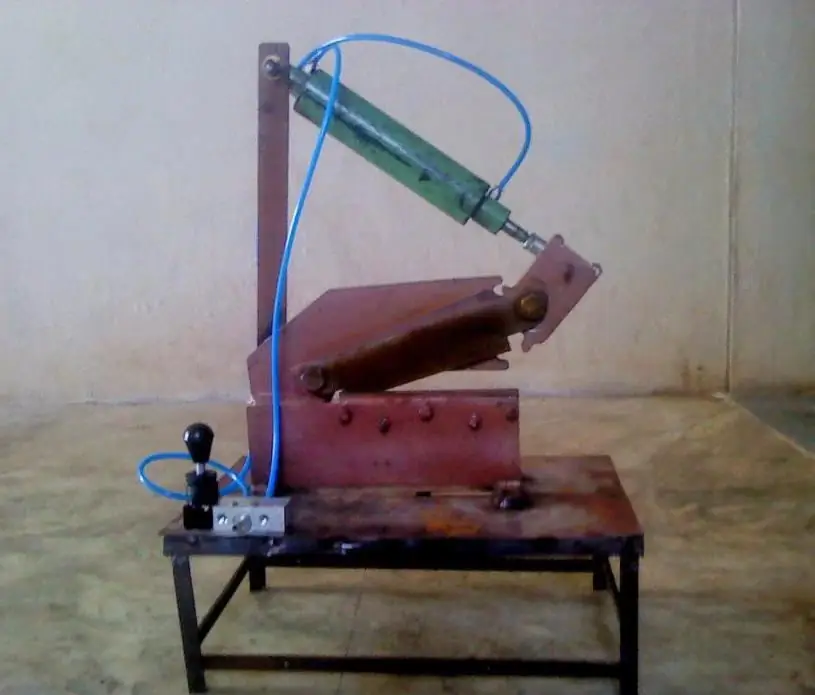
Today, sheet metal cutting is one of the fairly common technological processes that allows you to get blanks of the desired size and shape. However, there are many methods for performing this procedure and a wide variety of equipment
Do-it-yourself pipe bending machines
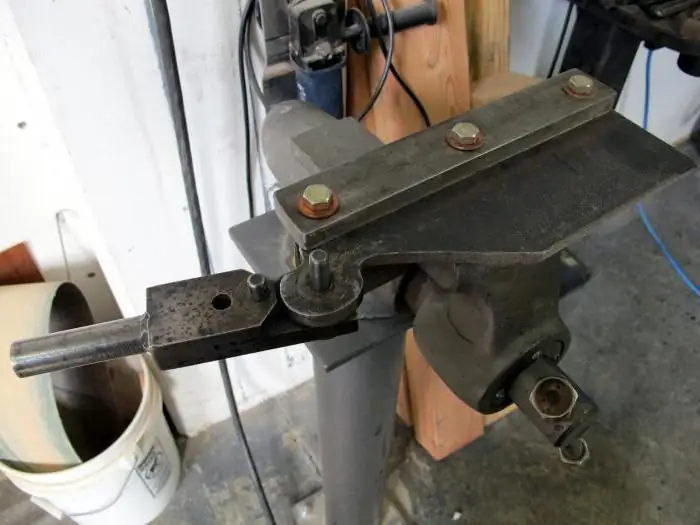
If you decide to make a manual pipe bender, you will need to form a reliable frame. Its elements are connected by bolts or welding. Next, an axis of rotation and shafts are installed, two of which will be located above the third. The distance between the axes of the shafts will determine the radius of the bend
Protection devices: purpose, types, classification, specifications, installation, features of operation, settings and repair
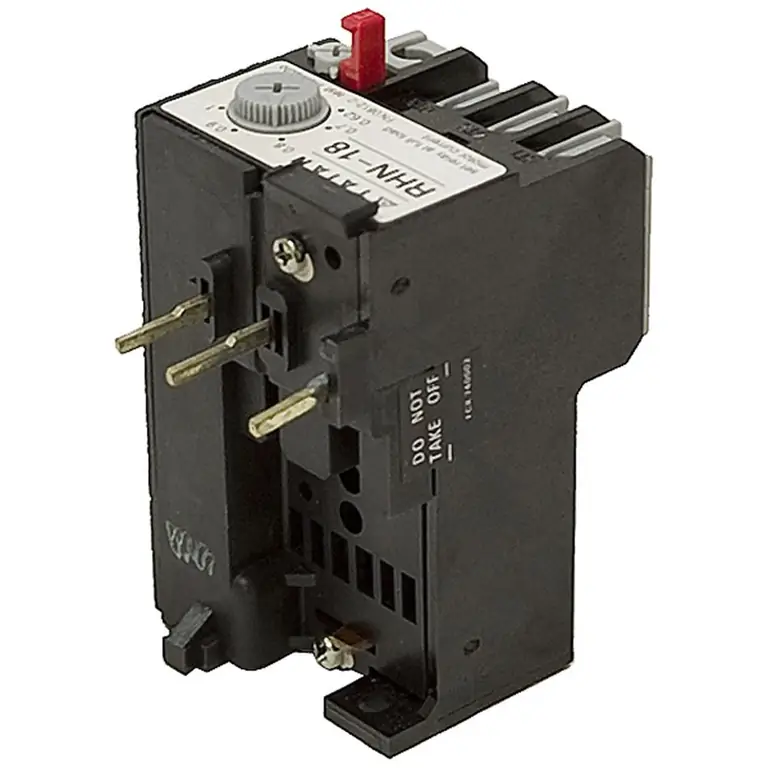
Protection devices are currently in operation almost everywhere. They are designed to protect both electrical networks and electrical equipment, various machines, etc. It is very important to properly install and follow the operating rules so that the devices themselves do not cause a fire, explosion, etc
Gear shaping machines: description, characteristics, types and mode of operation
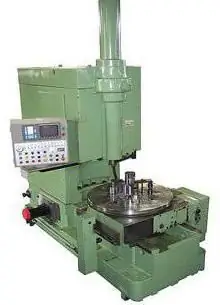
Gear shaping machines: specifications, settings, operation, features, purpose. Gear shaping machines: description, principle of operation, photo