2025 Author: Howard Calhoun | [email protected]. Last modified: 2025-01-24 13:10
Full cycle production process with waste recycling minimizes the amount of environmental pollution. Against the background of the popularization of this approach in the industry, technologies for the specialized utilization of products of industrial activity are also emerging in order to form new raw materials. These processes include the processing of used oil, which results in fuel.
Which oil is recycled?
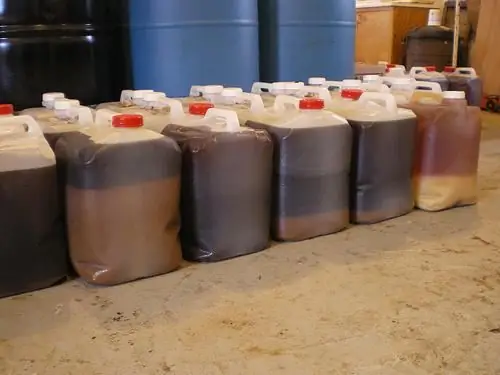
Synthetic oils are used as the main raw materials, which contain impurities that do not allow restoring the primary working composition as intended. According to GOST, used mixtures may include industrial and transport technical fluids used to lubricate mechanisms and motor additives. That is, industrial complexes, energy enterprises and even private companies can act as suppliers.motorists. Moreover, raw materials are used in different forms. Large Russian waste oil processing plants accept oil products, emulsions, sludge, effluents, fatty waste, etc. The concentration of foreign particles in the received liquid can be different - the coefficient is determined by the filtration means available to a particular enterprise. Now you can turn directly to oil processing technologies.
Settling method
The easiest and most affordable way to process technical fluids that does not require the connection of complex equipment. Its principle is the natural sedimentation of impurities and water under the action of a gravitational load. Settling can be used as one of the preliminary stages of processing before deeper cleaning, or as a complete technological process. In the first case, the processing of used oil by settling is a preparatory step before filtration. The disadvantages of this method include the duration of the procedure (waiting for particles to settle) and the possibility of eliminating only mechanical impurities of a large fraction of more than 50 microns. There is no question of chemical cleaning in this case.
Coagulation technology
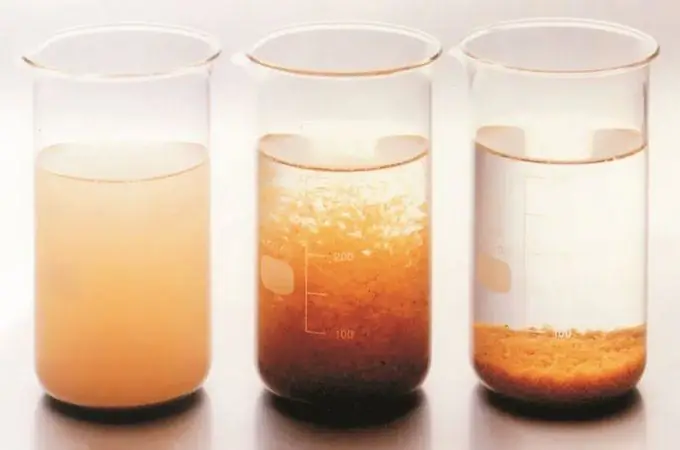
Method of enlarging undesirable particles that are present in used oil in a finely dispersed or colloidal state. Special substances act as an activator of the coagulation process - electrolytes of organic and inorganic origin, high-molecular hydrophilic compounds, andalso surface-active components without electrolytic properties. The efficiency of processing used oil using this technology is determined by the amount of coagulant introduced, the temperature of the working medium and the method of mixing. In contrast to the settling technique, this method requires only 25-30 minutes in terms of execution time. Another thing is that coagulation does not give a deep effect of physical and chemical processing, requiring subsequent filtration or centrifugal cleaning.
Adsorption processing
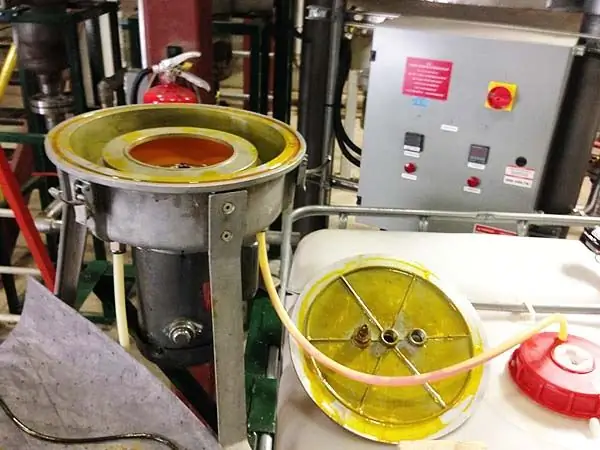
The use of adsorbents makes it possible to retain oil pollutants on a sufficient surface of the capillaries that penetrate the granules. In this capacity, natural (clay, zeolites, bauxites) and synthetic components (aluminosilicates, silica gel, artificial zeolites) can be used. The technology provides for the contact interaction of active substances with technical fluid. The oil is mixed by the percolation method or collides with the adsorbent during the countercurrent. The disadvantage of this method is the disposal of a large amount of raw materials that pollute the environment. On the other hand, it is the optimal processing of used oil into medium quality fuel - usually diesel. Although the method requires the use of sophisticated equipment and the conditions for the processing process are close to laboratory ones, the end result justifies the investment. This confirms the wide application of the method in various fields.
Ion-exchange processing
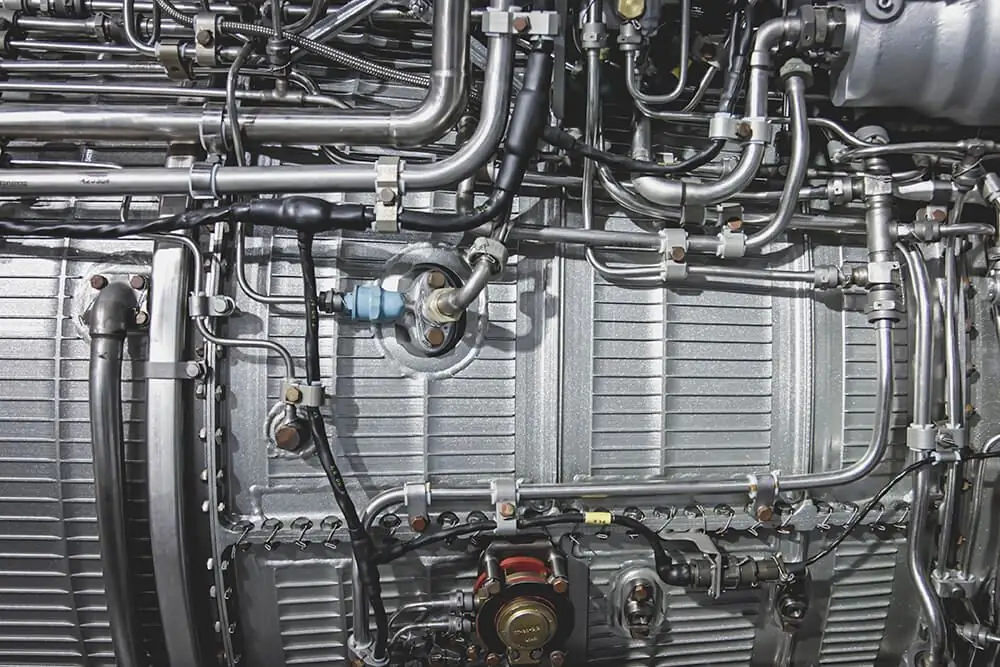
The technology is based on the ability of ion exchangers to hold contaminants, which decompose into ions in the dissolved state. What are ionites? These are hygroscopic solid gels produced in the process of polycondensation and polymerization of organic substances. The fact that they are insoluble in hydrocarbons and water allows them to be used in a wide range of engine fluids. As with adsorption, ion-exchange processing of used oil is carried out by the contact method under conditions of mixing of raw materials and ion exchanger grains with a fraction of the order of 0.2-2 mm. The use of the precollation method is also practiced, in which the liquid is passed through a column containing ion exchangers. Ion exchange gives a high cleaning effect, but does not remove resinous substances from the processed composition. The ion exchangers themselves can be restored after use. Their properties can be restored with a solvent (washing), by drying or by diluting with a 5% sodium hydroxide solution.
Waste Oil Recycling Equipment
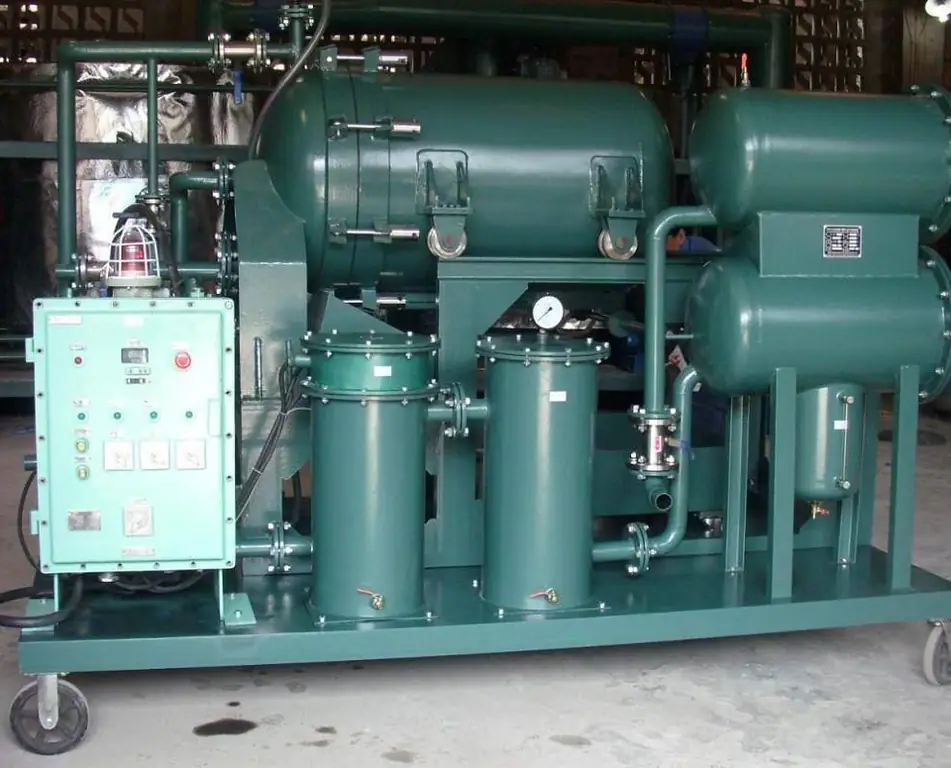
Specific types of apparatus for the processing of technical liquids will be determined by the technology used, as well as the requirements for the volume of the product produced. The standard equipment of this type is a cleaning stand, which uses the following functional parts:
- Cracking column.
- Liquid condenser.
- Centrifuge.
- Container with automatic filling level control.
- Cooler.
- Isolating valves.
- Pipeline infrastructure
- Pumping equipment.
- Feed lines for raw materials.
- Control panel.
The average waste oil processing plant is powered by electric motors ranging from 2 to 15 kW. The output is ready for further use of raw materials with a volume of 3 to 5 tons per day. As for the cost, the comprehensive provision of a mini-factory with a modular plant will cost about 1-1.5 million rubles, if we focus on the initial production level.
Conclusion
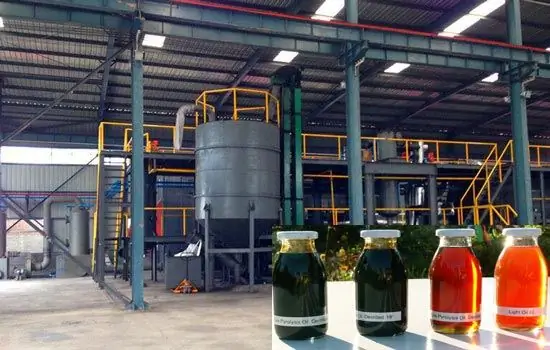
The organization of a line for the processing of technical oils can bring considerable profit if you correctly calculate the entire technological path of raw materials from the supplier to the final product. At the same time, it is necessary to take into account not only technological, but also legal nuances of this activity. To obtain a license for the processing of used oil, it is necessary to develop a project for the operation of an oil cleaning plant, and then approve it with the local authorities of Rosprirodnadzor. According to the application, an environmental impact assessment is carried out, and then a package of documents is drawn up for issuing a license for waste management. But that's not all. Already during the operation of the equipment, it is necessary to adhere to rather strict regulatory rules regarding not only processing, but also storage and transportation of oil.
Recommended:
Wastewater treatment from oil products: methods, methods and efficiency
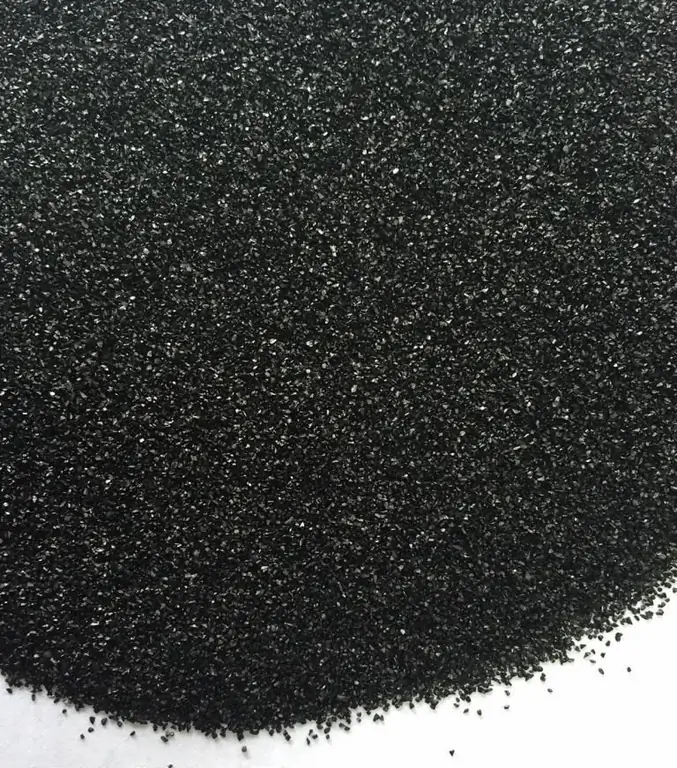
At the moment, technologies and means, methods and units, thanks to which wastewater treatment from oil products is carried out, are among the most important means of ensuring environmental protection. In our country, for about five years now, legislatively fixed standards for the purification of liquids discharged by enterprises have been in force. Documentation on this issue establishes the quality and volume of water that can be produced by industrial facilities
Oil rocker: device, purpose. Oil and gas equipment
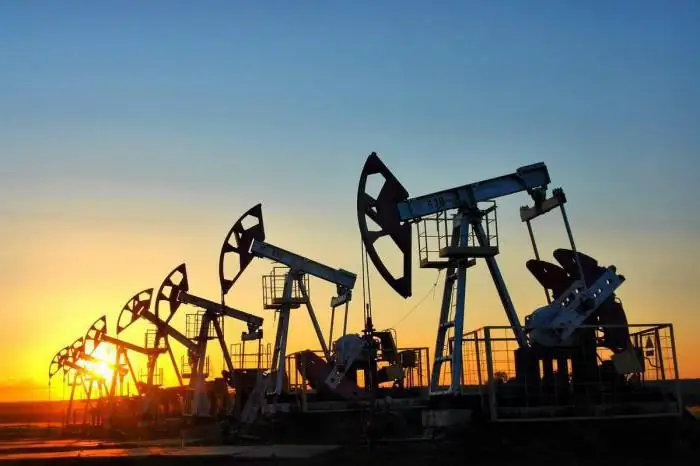
The article is devoted to oil-producing equipment, in particular pumping units. Considered the device of this equipment, characteristics, types, etc
Recycling plastic bottles as a business. Plastic Bottle Recycling Equipment
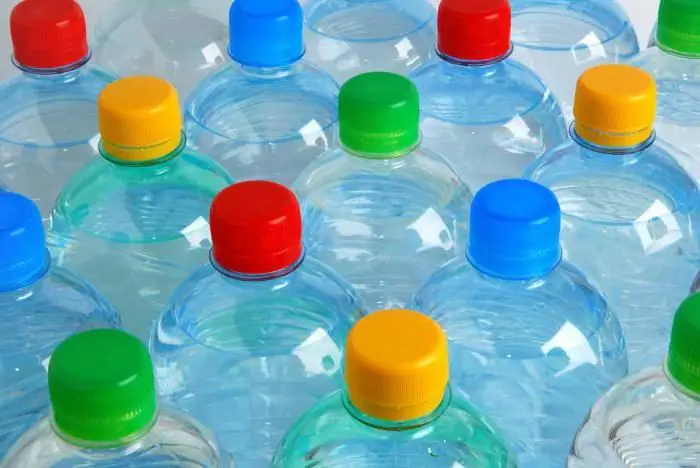
Now there are many business ideas that improve the lives of the population. If bottle recycling becomes popular among people, then it will be possible to create a permanent source of income. In our country, few people are engaged in such activities, so there is a possibility of profitability
Oil is a mineral. Oil deposits. Oil production
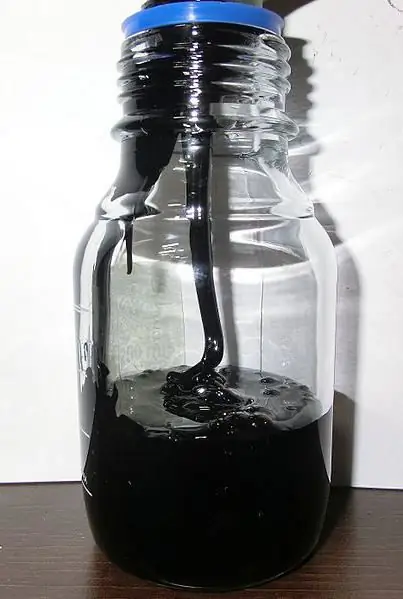
Oil is one of the world's most important minerals (hydrocarbon fuel). It is a raw material for the production of fuels, lubricants and other materials
Overview of oil sludge disposal methods
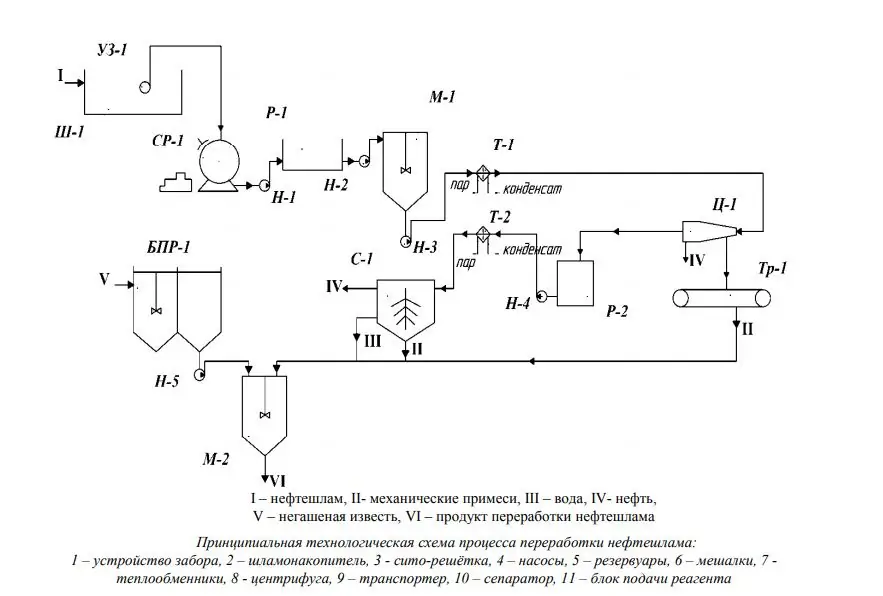
Utilization of oil sludge: classification of processing methods, their advantages and disadvantages. Brief description of chemical, biological, thermal, physical and chemical technologies. Types of oil sludge. Applied equipment for their disposal