2025 Author: Howard Calhoun | [email protected]. Last modified: 2025-01-24 13:10
Today there is a group of metals for which it is necessary to create special conditions before starting to work with them. Machining titanium falls into this category of work. All the difficulties and features of the process are due to the fact that this material is characterized by increased hardness.
Description
Titanium is characterized by being very strong, having a silvery color and also being extremely resistant to the rusting process. Due to the fact that a film of TiO2 is formed on the surface of the metal, it has good resistance to all external influences. Only the influence of substances that contain alkali in their composition can negatively affect the properties of titanium. In contact with these chemicals, the raw material loses its strength characteristics.
Due to the high strength of the product, when turning titanium, it is necessary to use an ultra-high-strength alloy tool and other special conditions when working on a CNC lathe.
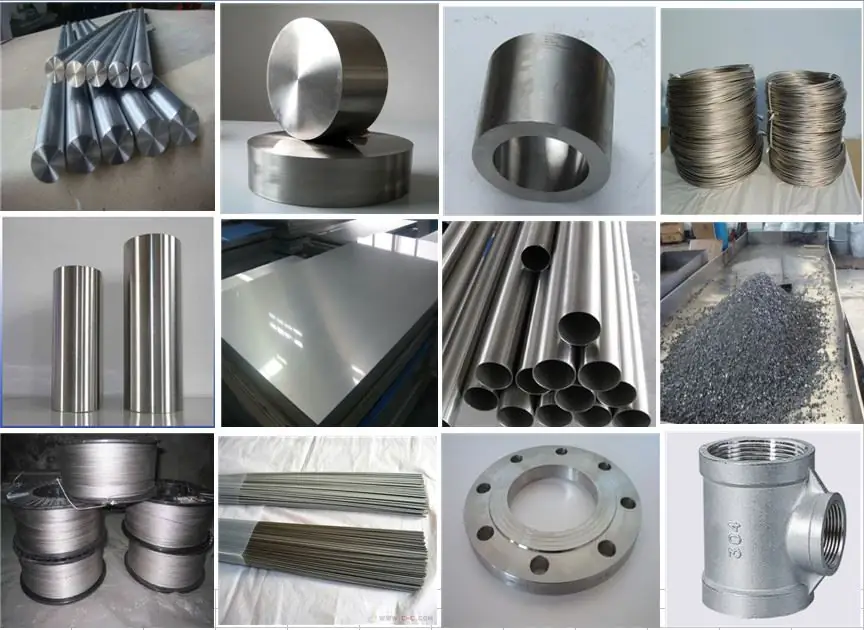
What should I consider when processing?
If it is necessary to work with titanium, the following properties must be taken into account:
- The first is sticking. Machining titanium using a lathe creates high temperatures, causing the material to melt and stick to the cutting tool.
- During processing, fine dispersed dust also occurs. It can detonate, and therefore it is very important to strictly follow all safety regulations during operation.
- In order to carry out the high-quality cutting process of such heavy-duty metal, a tool is needed that can provide the appropriate mode.
- It is also necessary to select a special tool for cutting because titanium is characterized by low thermal conductivity.
After titanium processing is finished, the finished part is usually heated, after which it is allowed to cool in the open air. Thus, a protective film is created on the surface of the material, which was described above.

Classification of processing methods
In order to cut such raw materials, a special tool is needed, as well as a CNC lathe. The process itself is divided into several operations, each of which is carried out according to its own technology.
As for the operations themselves, they can be basic, intermediate or preliminary.
When processing titanium on machines, you need to remember that vibration occurs at this time. In order to partiallyTo solve this problem, you can fasten the workpiece in a multi-stage way, and also do it as close to the spindle as possible. To reduce the influence of temperature on the machining process, it is recommended to use uncoated fine-grain carbide cutters and special PVD inserts. Here it is worth paying attention to the fact that during the processing of titanium by cutting, from 85 to 90% of all energy will be converted into heat, which will be absorbed by the chips, the workpiece being processed, the cutters and the liquid that is intended for cooling. Usually the temperature in the working area reaches 1000-1100 degrees Celsius.
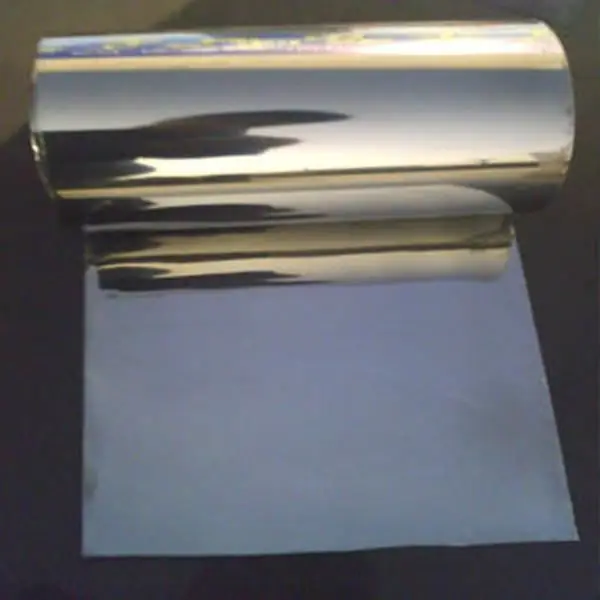
Adjust processing parameters
When processing such a heavy-duty material, there are three main parameters to consider:
- fixing angle of the working tool;
- feed rate;
- cutting speed.
If you adjust these parameters, you can use them to change the processing temperature. Under different processing modes, different parameters of these characteristics are observed.
For pre-treatment with a cut of the top layer up to 10 mm, an allowance of 1 mm is allowed. To work in this mode, the following parameters are usually set. Firstly, the fixing angle is from 3 to 10 mm, and secondly, the feed rate is from 0.3 to 0.8 mm, and the cutting speed is set to 25 m/min.
An intermediate version of titanium processing involves cutting off the top layer from 0.5 to 4 mm, as well as the formation of an even layer of 1 mm allowance. Fixation angle 0.5-4 mm, feed dimension 0.2-0,5 mm, feed speed 40-80 m/min.
The main processing option is the removal of a layer of 0.2-0.5 mm, as well as the removal of allowances. The working speed is 80-120 m/min, the fixing angle is 0.25-0.5 mm, and the feed rate is 0.1-0.4 mm.
It is also very important to note here that the machining of titanium on such equipment is always carried out only when a special cooling emulsion is supplied. The substance is supplied under pressure to the working tool. This is necessary in order to create a normal temperature mode of operation.
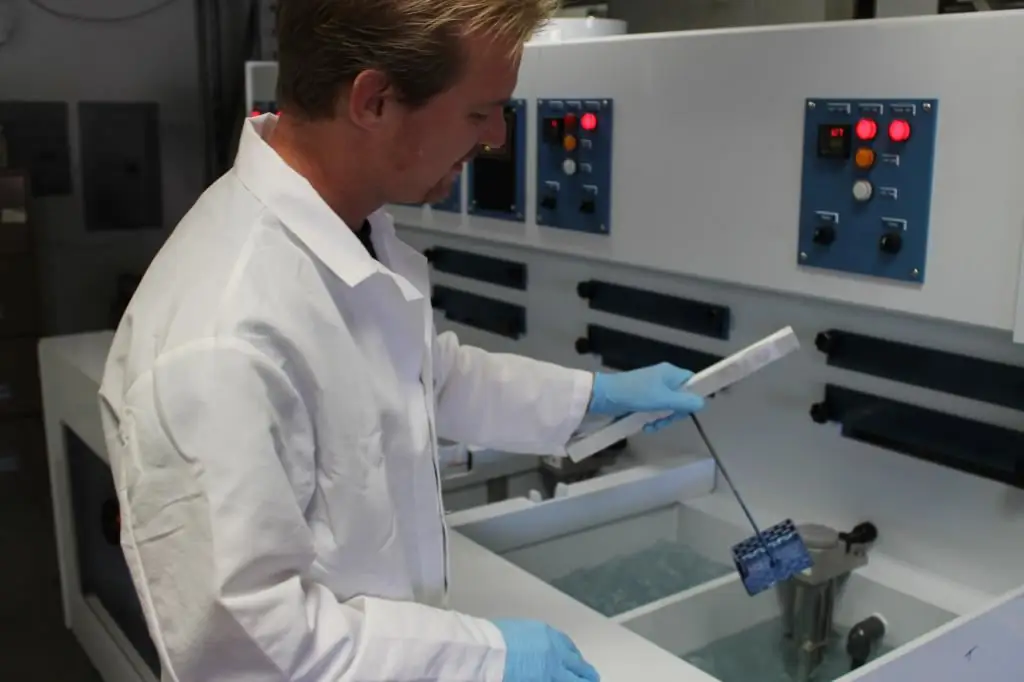
Processing tool
The requirements for the material processing tool are quite high. Most often, the processing of titanium and alloys is carried out using cutters that have removable heads, and they are installed on CNC machines. During operation, the working tool is subjected to abrasive, adhesive and diffuse wear. Particular attention should be paid to diffuse wear, since at this time the process of dissolution of both the cutting material and the titanium blank takes place. These processes are most active if the temperature is in the range from 900 to 1200 degrees Celsius.
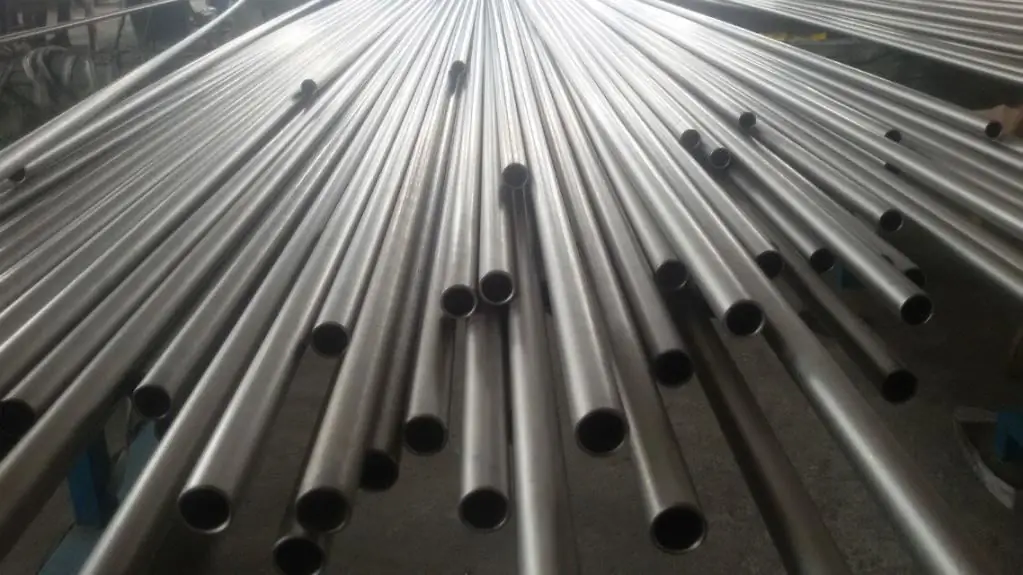
Tool requirements
The peculiarity of titanium processing is also that it is necessary to select a working tool depending on which mode of operation is selected.
To work in preliminary mode, the most commonly used inserts are round or square iC19. These plates are made from a special alloy, which is marked as H13A and has no coating.
In order to successfully process titanium in an intermediate way, it is already necessary to use only round inserts from the same alloy H13A or from alloy GC1155 with a PDV coating.
For the most responsible, basic processing method, round nozzles with grinding cutting edges are used, which are made of alloys H13A, GC 1105, CD 10.
It is important to add that when machining on CNC lathes, the smallest deviation from the shape of the part that was specified in the terms of reference is allowed. Most often, elements made from such an alloy do not have deviations from the norm at all.
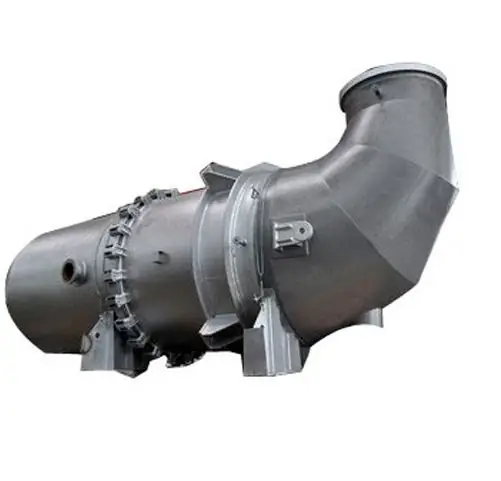
Main processing problem
The main problem encountered in the processing of this raw material is sticking and scuffing on the tool. Because of this, the heat treatment of titanium is very difficult. In addition, a lot of problems are caused by the fact that the metal has a very low thermal conductivity. Due to the fact that other metals resist heat much weaker, when in contact with titanium, they most often form an alloy. This is the main reason for rapid tool wear. In order to somewhat reduce scuffing and sticking, as well as to divert some of the generated heat, experts recommend doing the following:
- first, you must use coolant;
- secondly, when sharpeningworkpieces, for example, tools from the same heavy-duty materials should be used;
- thirdly, when processing raw materials with cutters, the speed is significantly reduced to reduce heat.
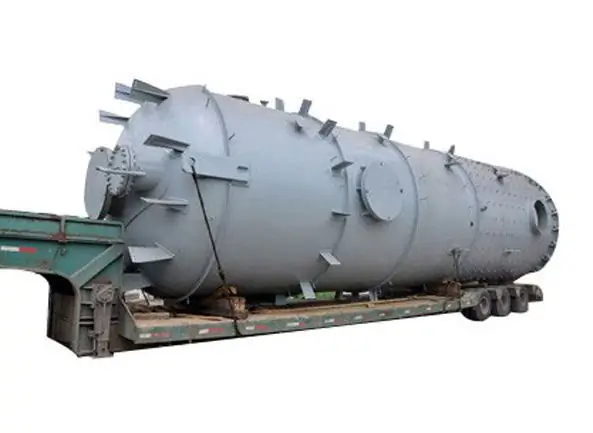
Oxidation and nitriding of titanium
It's worth starting with titanium nitriding, as this type of treatment is much more difficult than oxidation. The technological process is as follows. The titanium product is heated to 850-950 degrees Celsius, after which the part must be placed in an environment with pure nitrogen gas for several days. After that, a film of titanium nitride is formed on the surface of the element, due to chemical reactions that will take place during these days. If everything went well, then a golden-colored film will appear on the titanium, which will be distinguished by increased strength and abrasion resistance.
As for the oxidation of titanium, the method is very common and belongs, like the previous one, to the heat treatment of titanium. The beginning of the process is no different from nitriding, the part must be heated to a temperature of 850 degrees Celsius. But the cooling process does not occur gradually and in a gaseous medium, but abruptly and with the use of a liquid. Thus, it is possible to obtain a film on the surface of titanium, which will be firmly bonded to it. The presence of this type of film on the surface leads to an increase in strength and abrasion resistance by 15-100 times.
Connecting parts
In some cases, titanium products are part of a largedesigns. This suggests that there is a need to connect different materials.
In order to connect products from this raw material, four main methods are used. The main one is welding, brazing is also used, a mechanical connection method involving the use of rivets and bolted connection. To date, the main processing method for connecting products into one structure is welding in an inert gas environment or special oxygen-free fluxes.
As for soldering, this method is used only if welding is impossible or impractical. This process is complicated by some chemical reactions that occur as a result of soldering. To make a mechanical connection with bolts or rivets, you will also need to use a special material.
Recommended:
Indicators without delay and redrawing: types, principle of operation, pros and cons of application, expert advice
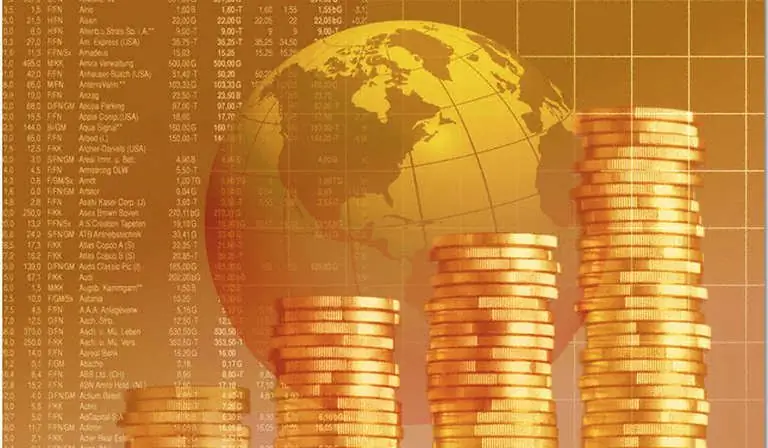
There is a wide variety of different tools in trading: graphical constructions, technical indicators, automated programs, trading signals and much more. To successfully apply them in trading, you need to understand how they work. Indicators without delay and redrawing are especially popular with traders
Stainless steel processing: popular techniques, methods and recommendations
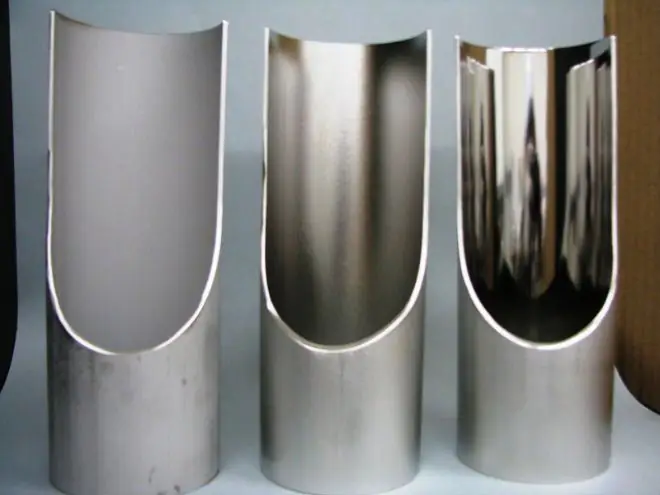
Today, people use many materials. One of the most common is stainless steel. The material is characterized by high performance, and therefore has become so popular. In addition, the processing of stainless steel also helps to keep the metal in shape
Electric locomotive 2ES6: history of creation, description with photo, main characteristics, principle of operation, features of operation and repair
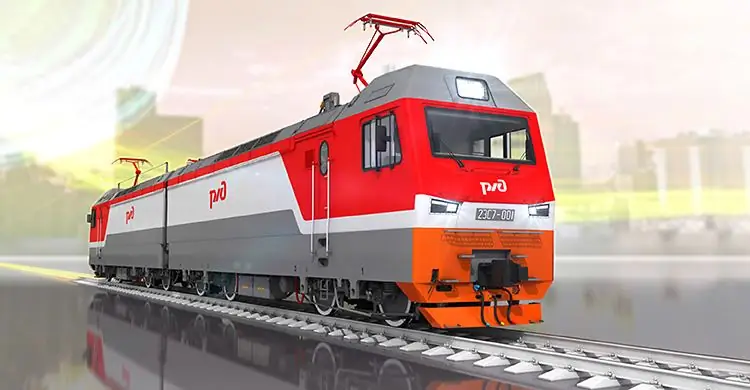
Today, communication between different cities, passenger transportation, delivery of goods is carried out in a variety of ways. One of these ways was the railroad. Electric locomotive 2ES6 is one of the types of transport that is currently actively used
Differential pressure gauge: principle of operation, types and types. How to choose a differential pressure gauge
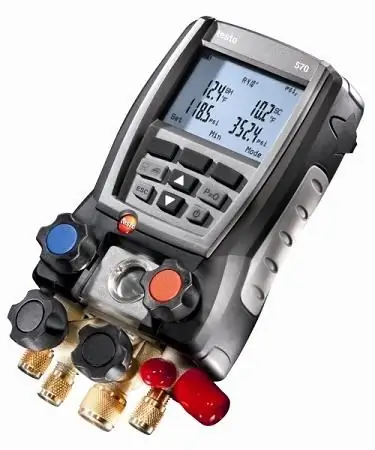
The article is devoted to differential pressure gauges. The types of devices, the principles of their operation and technical features are considered
Gas piston power plant: the principle of operation. Operation and maintenance of gas piston power plants
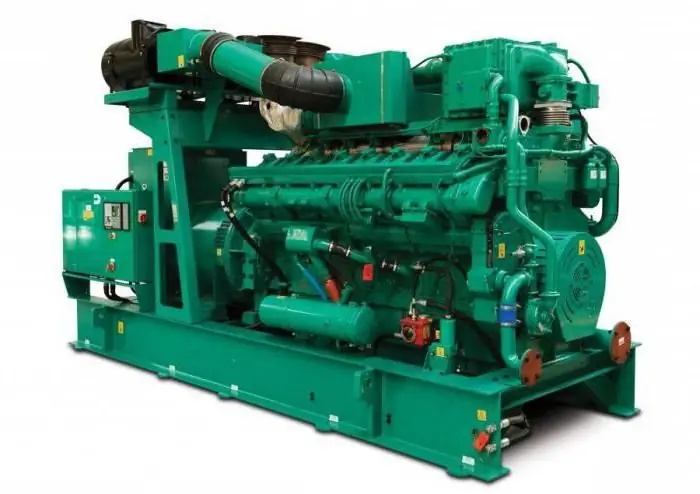
Gas piston power plant is used as a main or backup source of energy. The device requires access to any type of combustible gas to operate. Many GPES models can additionally generate heat for heating and cold for ventilation systems, warehouses, industrial facilities