2025 Author: Howard Calhoun | [email protected]. Last modified: 2025-01-24 13:10
Technological processes of production and processing of various materials often include the stage of thermal exposure. In this way, hardening, drying at high temperatures, soldering and other procedures are performed. It is not always possible to implement such measures in conventional furnaces, even for industrial purposes. Restrictions may be associated with the inadmissibility of contact with the air. Therefore, to solve such problems, a vacuum furnace is used, the processing in which also eliminates the processes of excessive deformation and warping of the workpieces.
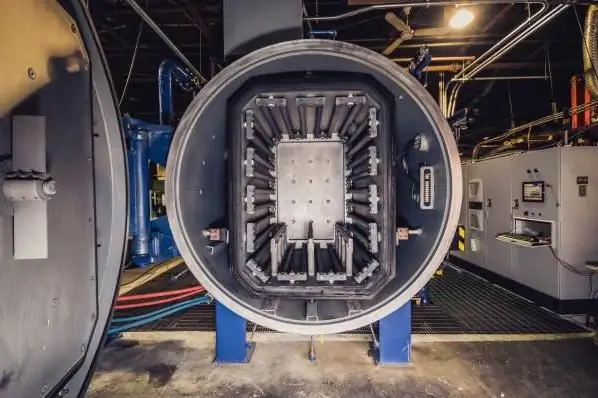
Purpose and scope of vacuum furnaces
Vacuum thermal roasting operations are used in mechanical engineering and instrument making, in the construction industry, in various industries, etc. For example, in instrument making, using such a unit, the operation of degassing elements is performed, which later become components of various equipment. Within the framework of the same direction, a vacuum furnace allows high-quality soldering and final sealing of individual sections on electrical circuit boards.
The operation of sintering is also widespread. With its help in construction and production, the necessaryperformance of ceramic products, hard alloys, refractory metal powders, etc. Separately, it is worth noting the metallurgical industry, which is also interested in heat treatment operations. For example, a vacuum furnace makes it possible to carry out quenching, aging, and tempering of alloys. Various steels, bronze and magnesium can be subjected to such treatments.

Main Specifications
The performance of the furnace design often becomes the main criterion for choosing a model. In this case, the installations have a potential of 3 to 20 kW. Moreover, this indicator affects the quality and efficiency to a minimal extent when providing thermal exposure. As a rule, power increases as the load volume increases, which already depends on the dimensions of the structure. So, in standard industrial models of this type, you can load from 15 to 40 kg of material on average. But there are also units that allow you to serve up to 100 kg at a time. The induction melting furnace endowed with medium characteristics is capable of serving up to 9000 kg in one shift. As for the quality and effectiveness of the impact inside the chamber, the temperature range should be taken into account directly. It ranges from 1800 to 2000 °C.
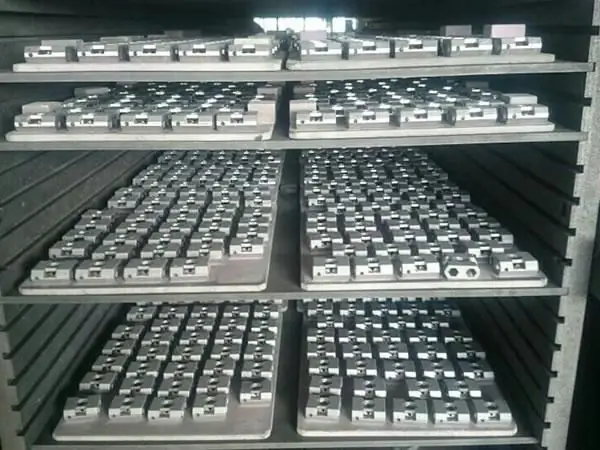
Smelting process
Technology in traditional units is based on the action of an arc discharge. There is a contact between an electric current and a gas mixture. Further, the resulting arc due to the highconcentration in vacuum provides an increased thermal effect. Even at low power, the vacuum arc furnace can melt steel billets.
There are two principles of heat transfer in relation to the material. This is a direct and indirect impact. In the first case, the arc generates energy between the electrode and the workpiece, which in this configuration receives maximum heat. Indirect heating involves working with two electrodes that act on the object at some distance. Obviously, a direct heat transfer vacuum furnace is more efficient, but it tolerates a higher percentage of negative heat treatment factors.
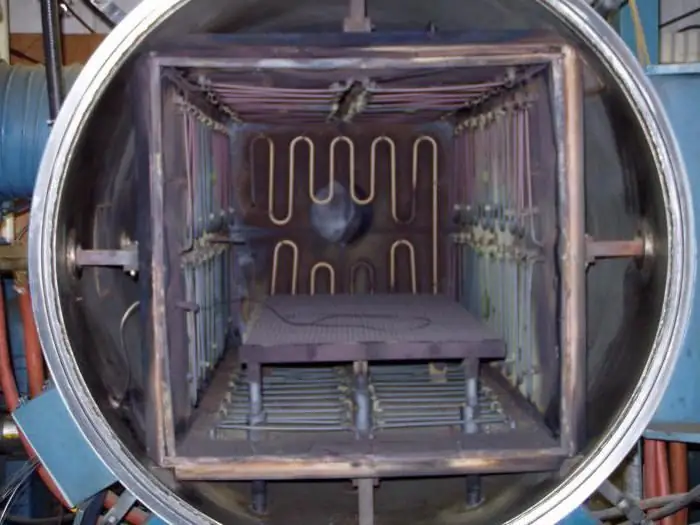
Varieties of ovens
The basic model of a vacuum furnace structure is the arc structure described above. With the help of such equipment, it is possible to service most varieties of a complex metal alloy, including refractory products. Another variation is the induction melting furnace, which has an inclined crucible. It is in the crucible that the process of remelting the material loaded into the working chamber is realized. The induction principle of operation is considered the most expensive to maintain, so it is used less often and only when it is necessary to work with complex metals. Electron-beam unit belongs to special types of vacuum furnaces. Such a device produces refined alloys and metal ingots at the output. Structurally, the equipment is a thermal gun, which, by means of a directedexposure implements beam firing of the product.
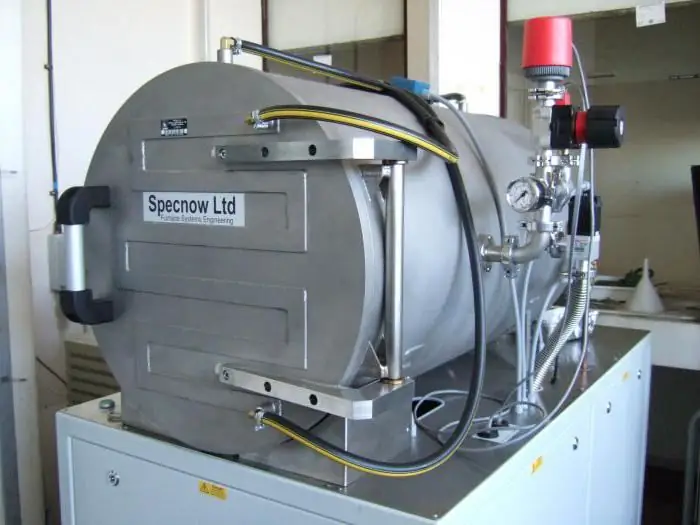
Advantages and disadvantages of vacuum ovens
Compared to conventional heat treatment furnaces, vacuum allows highly efficient heat treatment of workpieces. At the same time, the operator has the possibility of flexible adjustment of the heating parameters, which, for example, is provided by a vacuum induction furnace with a crucible. The advantages of such structures include the possibility of obtaining a relatively pure metal material. That is, the technology itself eliminates excessive contamination of the array with foreign particles - heat treatment products.
As for the shortcomings, they are associated with a low resource of the parts that form the structure. The point is not even in the flaws in the material of the constituent elements, but in the harsh conditions that are required to ensure productive heat treatment and which affect the structure of the working surfaces. In addition, a vacuum furnace, the average price of which is 500-700 thousand rubles, is available to a few enterprises. However, high quality sintering and melting is expensive and limits its use.
Producers
Vacuum furnaces are supplied only by large enterprises cooperating with institutes for the design and development of industrial equipment. Today, high-quality units of this type are supplied to the domestic market by foreign manufacturers SCHMETZ and XERION. These products are oriented both to perform typical thermal operations and to specialized tasks such asdiffuse annealing. The Moscow plant of industrial equipment, which specializes in the production of vacuum electric furnaces, also offers units that are worthy in terms of characteristics. With the help of such equipment, the owner can carry out metal tempering, sintering and standard thermal processes. Automatic models are offered by the Spetszhelezobeton Plant, which develops high-vacuum units with volumetric loading chambers.
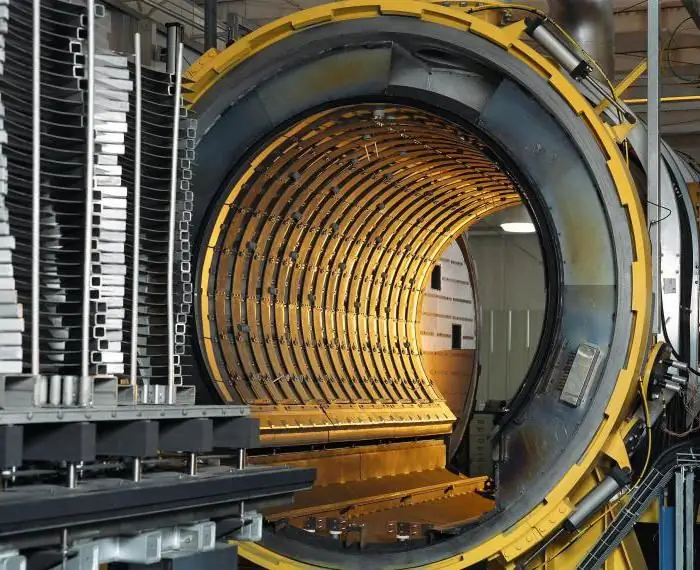
Conclusion
An example of vacuum annealing technology shows that new solutions do not always justify themselves during operation. Although the same Moscow plant of industrial equipment seeks to optimize the units for the needs of a wide range of consumer enterprises, the high cost of vacuum heat treatment for many potential customers makes this method inaccessible. The refusal of such furnaces is due not only to their cost, but the lack of the need to obtain a high-quality product. However, advanced companies operating in high-tech industries can no longer do without the use of such heat treatment.
Recommended:
Glass furnace: types, device, specifications and practical application
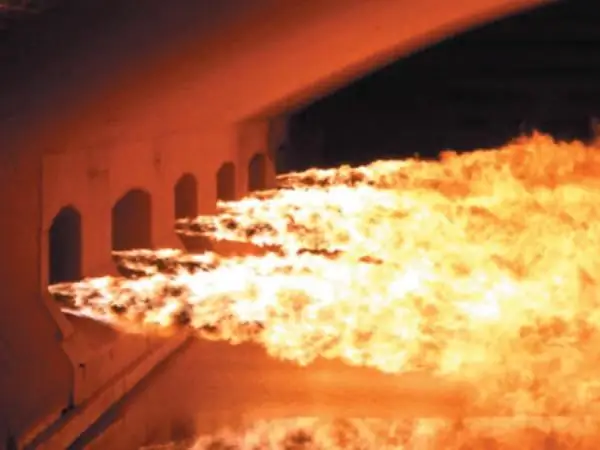
Today, people actively use glass for a variety of purposes. The glassmaking process itself is the melting of raw materials or charge. Glass melting furnaces are used to melt the material. They come in different types and are classified according to several criteria
Hydraulic stations for presses: types, specifications, purpose and practical application
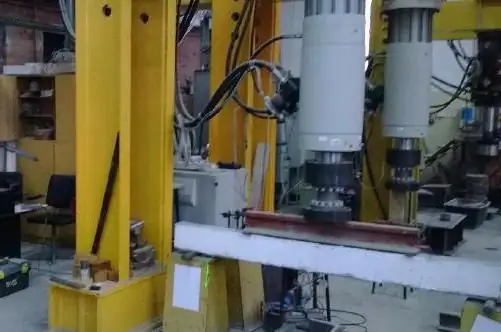
Hydraulics is one of the oldest mechanisms in the operation of power equipment. The simplest representative of this type of units is a press. With its help, large compressive forces are provided in various industries with minimal organizational and operational costs. The quality of operation of the device will depend on which hydraulic station is used for the press - whether it meets the target design in terms of working properties and whether it is able to maintain sufficient force
Industrial fans: specifications, types, purpose
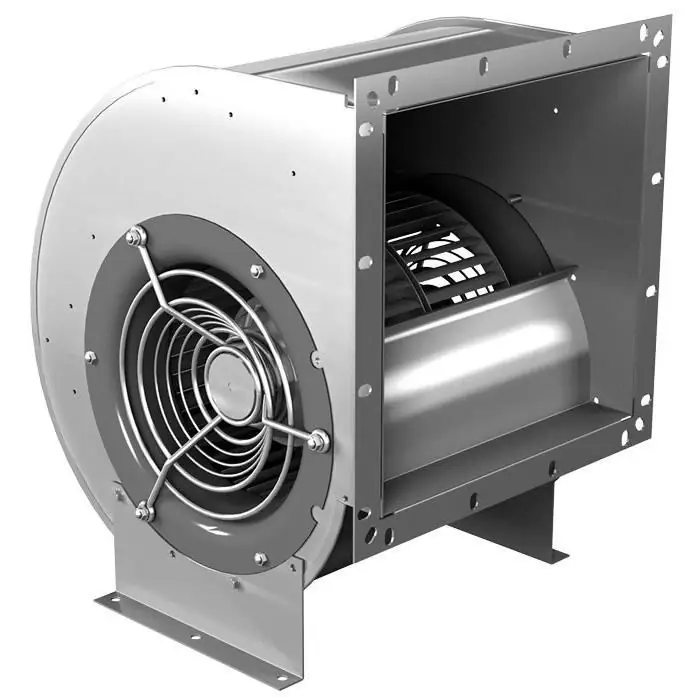
Establishing an efficient and reliable air ventilation system at the enterprise is the first step towards creating comfortable conditions for employees. Ventilation of premises can be carried out in a natural and forced way. In the second case, industrial fans are required for operation, the technical characteristics of which will determine the efficiency of the entire ventilation system
Auxiliary power unit: specifications, purpose, device and resource indicators
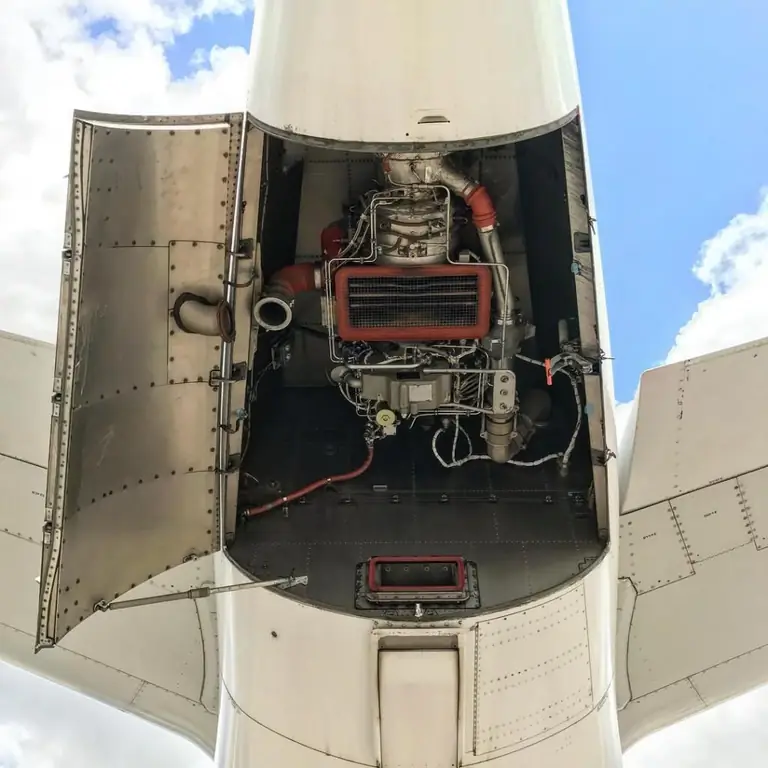
An auxiliary power unit, or APU, is a unit that is very often used in aviation technology. By itself, this installation is necessary for obtaining mechanical energy. However, it cannot be used to move vehicles
Vacuum forming machine: brands, manufacturer, specifications, working principle and application
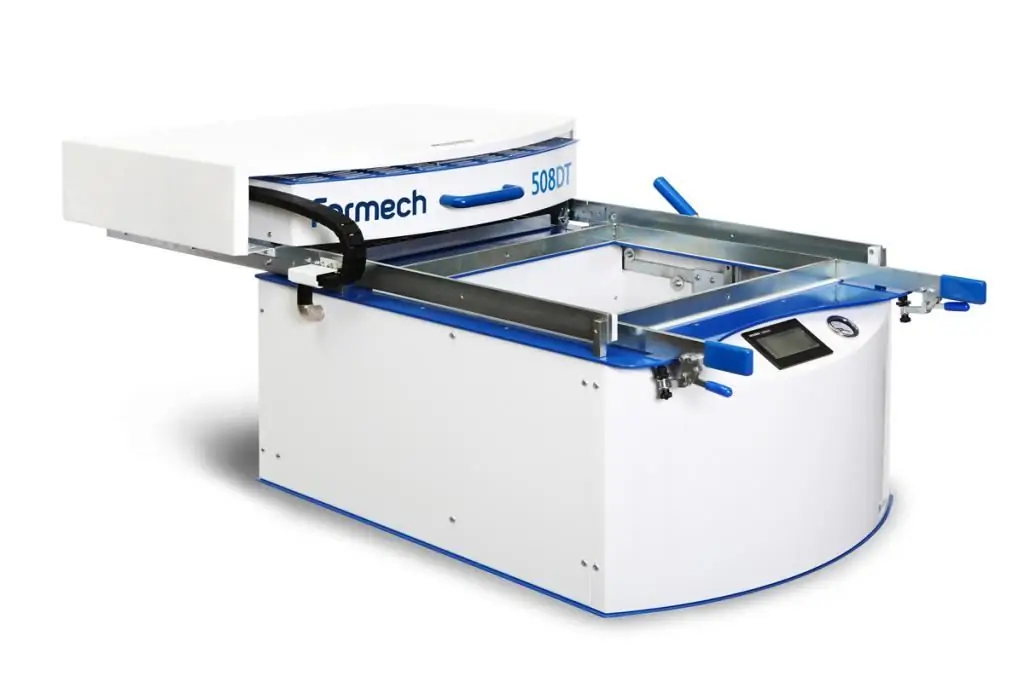
Today, people actively use plastic containers. For the manufacture of such products with a very different and complex shape, a vacuum forming machine is used. Goods made on such machines are actively used not only in everyday life, but also in food, light industry, and the automotive sector