2025 Author: Howard Calhoun | [email protected]. Last modified: 2025-01-24 13:10
The word came to us from the Japanese language. And it is already quite common in business circles, in world and Russian news. But what is gemba? In this article, we will try to tell you in detail.
What does gemba mean?
Gemba, gemba or genchi genbutsu - all these words define the same phenomenon. It is often referred to as a lean manufacturing tool. The word comes from the Japanese 現地現物, which means "goods in the field".
So what is it? Gemba is an approach actively used in Japanese management practice called kaizen. This is the name of a philosophy (practice) that focuses on the continuous improvement of production processes, planning, management, auxiliary business schemes and aspects of human life in general.
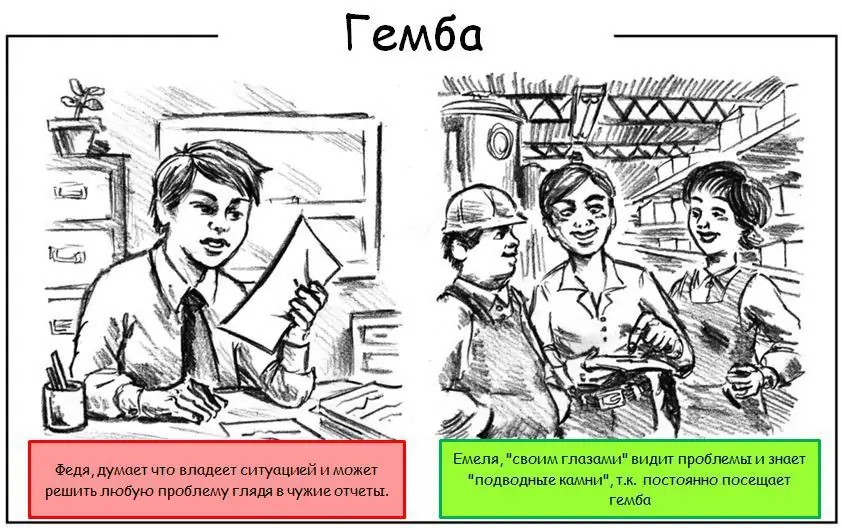
Thus, in order to understand exactly what's what, you need to come to the gemba - the direct place of deployment of the workflow, get acquainted with the facts and make the right decision based on this.
The term became known to the general public after articles about the quality management system of the well-known Japanese corporation Toyota. Gemba in kaizen- problem solving immediately at the place of its occurrence. This approach is fundamentally different from the popular American one, which is characterized by remote work of a manager.
From kaizen to gemba
To deal with gemba will help familiarity with the philosophy of kaizen. I must say that it is not static - practice is constantly being supplemented and improved. Let's present some of its main principles for a manager:
- Don't forget about self-discipline. Control your behavior. Respect workers as you would yourself.
- Self-improvement is important. Start by solving your own problems and defining your area of responsibility.
- Don't forget to inform every employee about the company's activities.
- Always focus on the customer. After all, they are the main goal of your work.
- The essence of kaizen is continuous, daily change for the better.
- Openly admit your problems. Only after understanding them is it possible to improve. Do not be afraid of public discussion of problems.
- Promote openness. It is wrong if employees limit their communication to a certain group.
- Create work teams.
- Develop yourself so that your experience becomes an example for the whole company.
- Trust certain responsibilities to each employee so that he can see his own worth.
- Learn to plan. And always compare what you expect with the result.
- Prevent production problems from recurring.
- Standardization and quality is something that should never be forgotten.
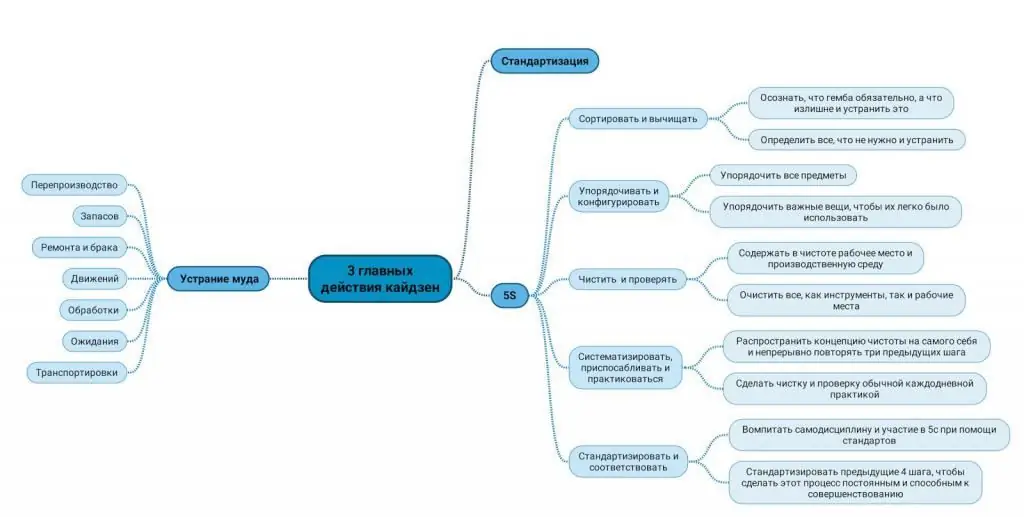
From here you can identify five important steps to improve yourself and the company:
- Tidiness.
- Order.
- Clean.
- Standardization.
- Self-discipline.
Gemba management rules
What is gemba? These are the 5 basic rules of a manager:
- If there is a problem, you should immediately go to the gemba. That is, to the place of the workflow where it appeared.
- On the gemba, the first thing you need to do is get familiar with the genbutsu - environment, equipment.
- Finding a key solution to a problem must be done at the site of its origin (gemba).
- Now find the cause of the abnormal state of affairs.
- Fix in guidelines, rules or standards a way to prevent this problem from reoccurring.
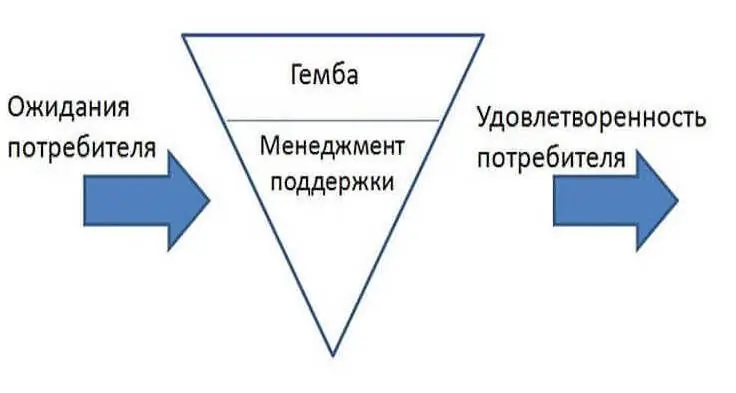
How to practice gemba?
Having de alt with the word "gemba", we will briefly indicate how it is possible to practice this approach in modern Russian conditions:
- Continuously monitor production processes.
- Check the proper execution of previous orders.
- Always solve problems on the spot, without delay, involving ordinary employees in the process.
- Hold business meetings at banners with company performance indicators.
- Introduce the practice of short discussions directly in the production spaces.
Recommendations for implementing the approach
Many leaders, having learnedwhat it is - gemba, make a decision on the imminent implementation of it in their enterprise. There are a number of useful recommendations that allow you to go through this process quickly, smoothly and successfully:
- Gemba should be practiced all the time, not occasionally.
- A "Plan G" ("Gemba Plan") should be drawn up to help focus on the "sore" points of the workflow.
- A manager should remember to look into the most unexpected and remote corners of production.
- When a problem arises, the manager should report to the gemba as soon as possible. And the manager should be interested in solving it.
- The leader should be intolerant of detected deviations.
- The manager should not forget about strict observance of safety regulations.
- All deviations must be recorded, as well as a specific deadline for their elimination.
- An important duty of a manager is to check how quickly and efficiently his instructions are carried out.
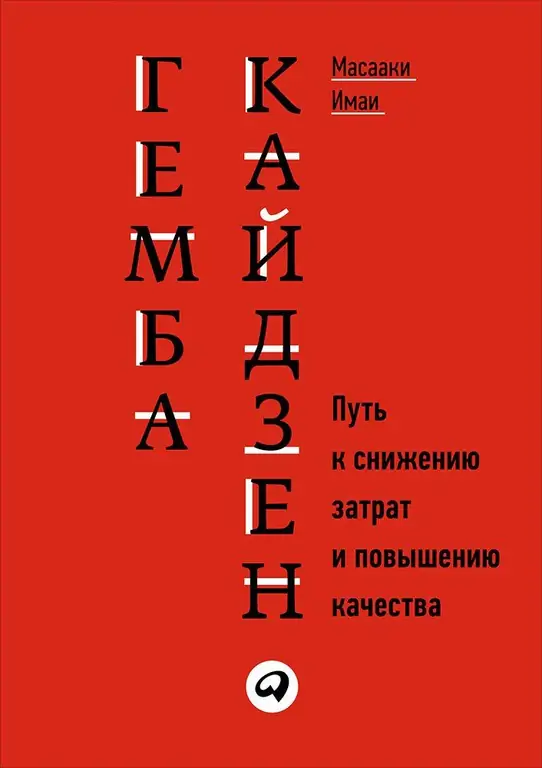
What else is this?
Gemba is a mountain of the Poloninsky Range of the Ukrainian Carpathians. It is the highest point of the massif called Polonina Borzhava - 1491 m. Geographically located in its southwestern extension (Transcarpathian region).
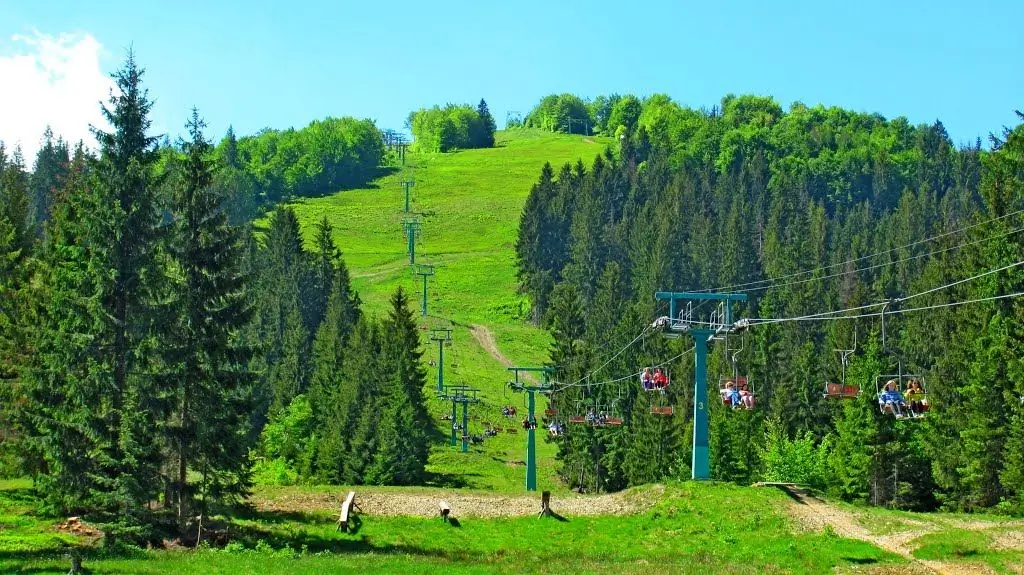
This is a domed, crescent-shaped mountain. One of the famous Ukrainian waterfalls - Shypit (or Shypit) is located on it. It is also a developed recreational area - here is the secondin importance in the country (after Dragobrat) is a ski resort with 8 ski lifts for athletes. It is distinguished by the longest route in Ukraine - 3.5 km.
But the most popular meaning of the word "gemba" today is one of the approaches in Japanese management. Its brief essence is the solution of the problem at the place of its occurrence.
Recommended:
Japanese Brands: Products, Brand Names, Top Best Brands and Famous Japanese Quality
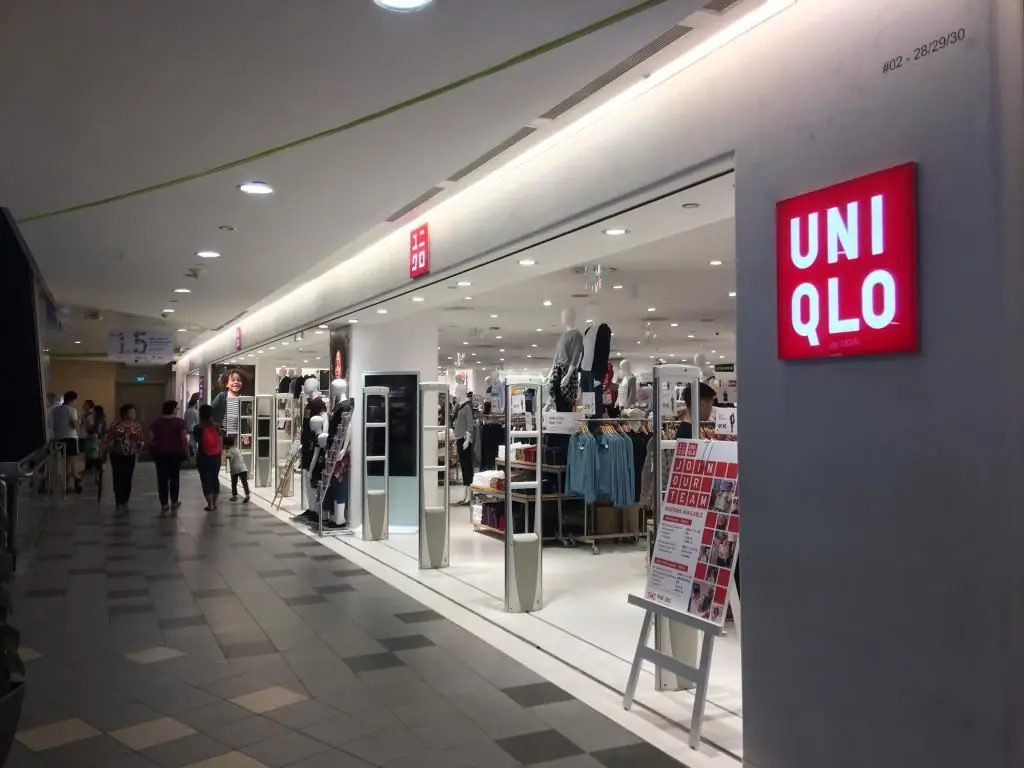
Every kind of goods is produced in Japan. Given the huge number of manufacturers, it is often difficult for the buyer to decide on the choice of products. Everyone knows what Japanese brands of cars and household appliances exist. But this country also produces excellent clothes, perfumes, and cosmetics. We offer a rating of brands of these products
"Quality Circles" is a quality management model. Japanese "Quality Circles" and the possibilities of their application in Russia
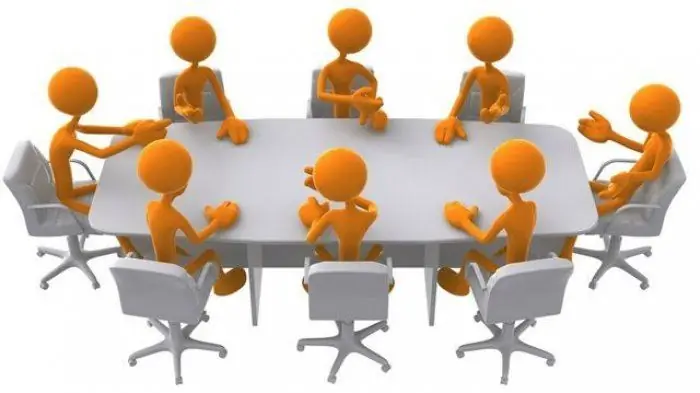
Modern market economy requires companies to constantly improve their technological processes and staff training. Quality circles are a great way to involve active employees in the workflow and implement the most productive ideas in the enterprise
Income approach to real estate and business valuation. Applying the Income Approach
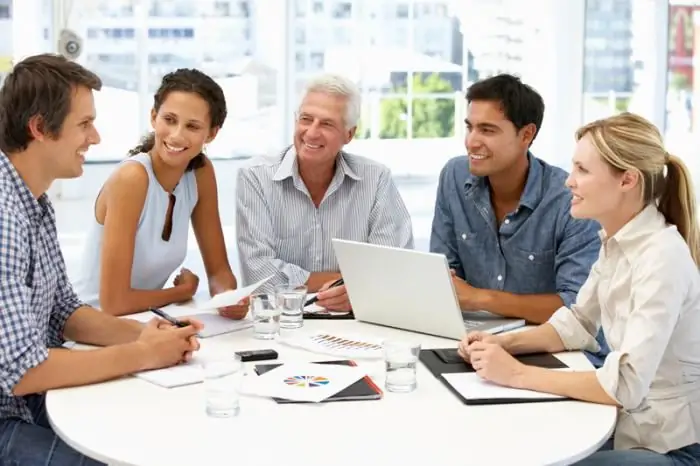
The income approach is a set of methods for estimating the value of real estate, the property of an organization, the business itself, in which the value is determined by converting the expected economic benefits
System approach to management. Advantages and disadvantages
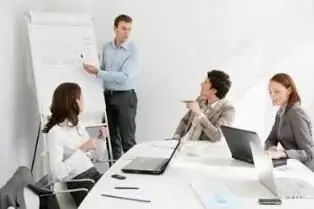
Now more and more businessmen realize the value of such a science as management. This includes many different directions on the most incredible topics. It is a systematic approach to management that allows you to optimize all stages of work at the enterprise, which in turn will certainly lead to a reduction in costs. It views your company as a single organism, made up of many separate pieces and elements, focusing on the connection between them
What is a unique payment identifier? How to find out the unique payment identifier?
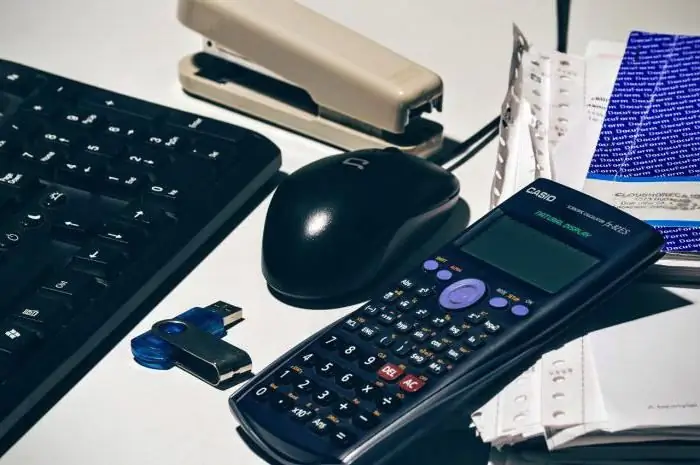
Unique payment identifier - what is it? What is it for? These are the most common questions that entrepreneurs ask when paying taxes at a bank, when a bank employee requires you to specify this requisite. This is bewildering. Where can I find it, how to get it and can I do without it? Thus, a tool created to simplify the procedure has led to new questions that need to be clarified