2025 Author: Howard Calhoun | [email protected]. Last modified: 2025-01-24 13:10
Technologies for the implementation of welding operations in relation to metal workpieces today make it possible to achieve a high level of organization of the process in terms of safety, ergonomics and functionality. This is evidenced by the spread of semi-automatic and robotic equipment for performing the main technological steps in the thermal joining of parts. In parallel with this, the requirements for the quality of seams are also growing. In this direction, the greatest success can be achieved by welding in shielding gas, which provides for the possibility of isolating the working area from the negative effects of atmospheric air.
The essence of technology
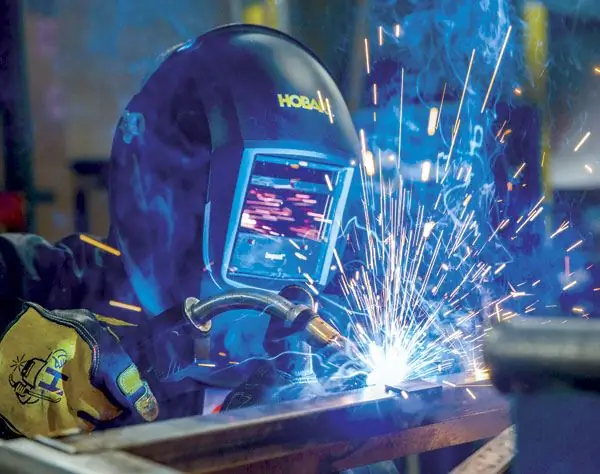
The welding process in a protective gas environment is a derivative of the combination of several methods of thermal action on metals with the possibility of structural connection of workpieces. First of all, this method is based on the arc welding method, which in itself provides optimal control over electrodes and surfaces of target parts with structures. In this format, the user can occupy any spacepositions using mobile and compact equipment. All this concerns the organizational ergonomics of the work event, and the essence of the electrochemical processes of welding in shielding gas is revealed by the specifics of the environment in which the operation is performed. To begin with, it is necessary to emphasize the importance of protecting the weld pool from the negative effects of atmospheric air. Direct contact of the billet melt with oxygen leads to the formation of slag on the surface, oxidation of the coating, and uncontrolled alloying of the metal structure. Accordingly, to exclude such effects, special insulators are used - coatings, bulk materials like flux and gas, which is introduced into the working area with special equipment. The last method of protection determines the features of the considered method of welding production.
General rules for welding according to GOST 14771-76
According to the specified GOST, this welding method can be used to perform one-sided and two-sided seams using butt, corner, tee and overlap joints. As for the main parameters of the process, they include the following:
- Thickness of parts - range from 0.5 to 120 mm.
- Permissible error when welding parts with a thickness of 12 mm - from 2 to 5 mm.
- The slope of the seam surface is only allowed if a smooth transition from one workpiece to another is ensured.
- When welding parts with a significant difference in thickness, a bevel is preliminarily performed in the direction from a larger workpiece to a small one.
- Concavity and convexity of fillet welds according totolerances of GOST 14771-76 should be no more than 30% of the leg of the angle being formed, but at the same time fit within 3 mm.
- The amount of allowable offset of the edges before welding in relation to each other depends on the thickness of the parts. For example, in the case of elements up to 4 mm thick, this figure is about 0.8-1 mm, and if we are talking about 100 mm blanks, then the offset distance will have to fit into 6 mm.
Used welding gases
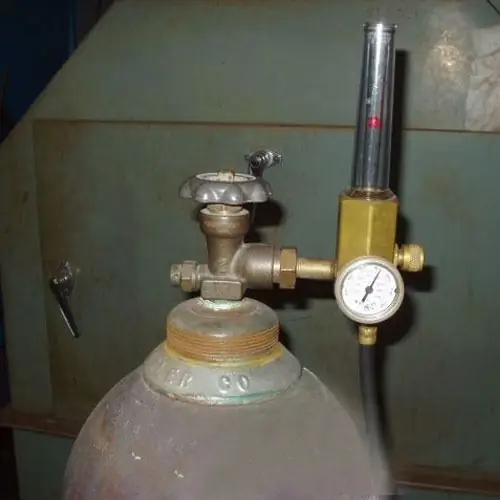
From the point of view of welding, all gaseous media are divided into inert and active. Since the main task of the gas mixture is the insulating function, the most valuable are the media that do not affect the metal being processed. Such mixtures include inert monatomic substances like helium and argon. Although, in accordance with GOST, welding in shielding gases must be carried out in a carbon dioxide environment, and combinations with oxygen mixtures are also allowed. As for active gases, they can affect the metal both in the molten and in the solid state. The presence of gases in the molecular structure of a metal is generally considered undesirable, but there are exceptions due to the specifics of such combinations under different conditions.
The nature of the influence of the gas environment on the metal
Immediately it is worth emphasizing the negative effects of gas during arc welding on workpieces. During cooling and strong heating, gas substances dissolved in the molecular structure can cause the formation of pores, which logically reducesstrength properties of the product. On the other hand, hydrogen and oxygen atoms can be useful in future doping operations. And this is not to mention the usefulness of active shielding gas in welding austenitic alloys and steels, which are difficult to melt if inert insulating mixtures are used. As a result, the problem for technologists is rather not in choosing the right gas mixture, but in creating conditions that could minimize the harmful effects of the active gas on the weld pool and at the same time preserve the positive effects of solubility.
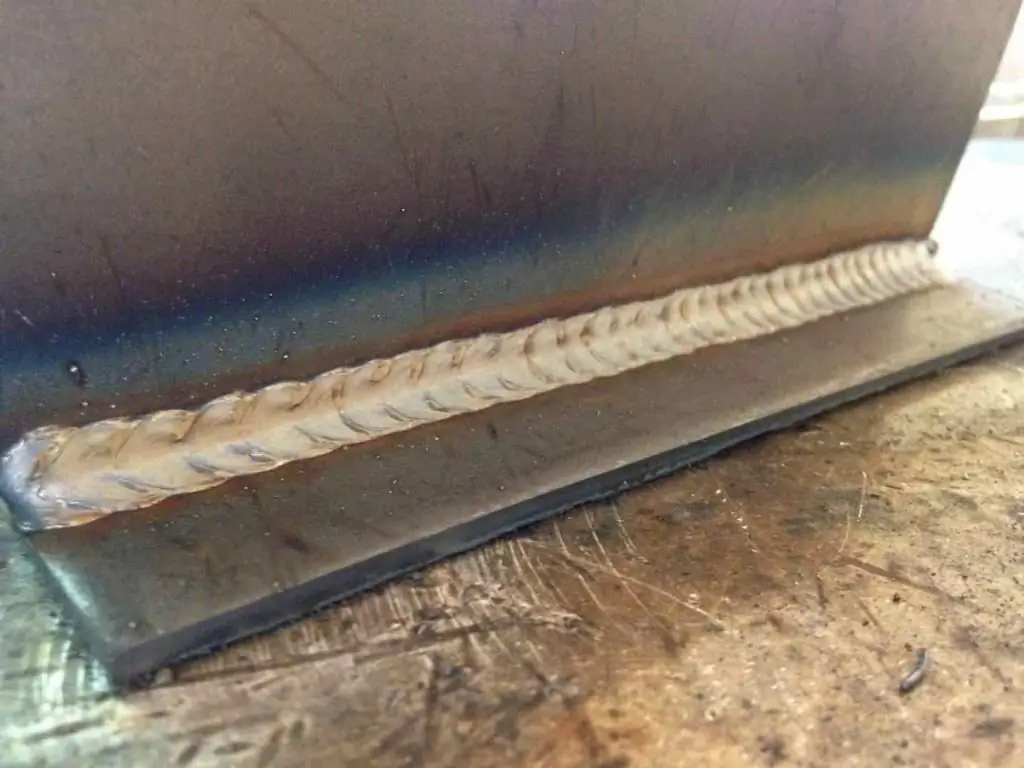
Welding process technique
A source of electric current is supplied to the workpiece and the electrode, which will later be used to create and maintain the welding arc. From the moment of ignition of the arc, the operator must maintain the optimal distance between the electrode and the formed weld pool, taking into account temperature indicators and the area covered by thermal effects. In parallel, gas is supplied to the working area using a burner from a connected cylinder. Gas insulation is formed around the arc. The intensity of the formation of the seam will depend on the configuration of the location of the edges and the thickness of the products. As a rule, the proportion of the base metal in the weld structure, which is formed during welding in a protective gas, is 15-35%. The depth of the working area in this case can reach 7 mm, and the indicators of its length and width - from 10 to 30 mm.
Equipment for gas welding
A set of devices for suchkind of operations depends on the modes and format of welding production. The technical base is directly formed by semi-automatic devices, suspended welding heads, power sources, rectifiers and complex automatic modules with electrode holders, which maximally save the operator from performing typical manipulations. The emphasis today is on mechanized welding in shielding gas, the infrastructure of which is also formed by a gas line, burners, devices for convenient placement of equipment in different positions, etc. Special posts are organized at large industries with the necessary set of technical equipment for welding. Conversely, an optimized format for performing such tasks at home requires the use of only a compact inverter with converters and a gas cylinder with flow control equipment.
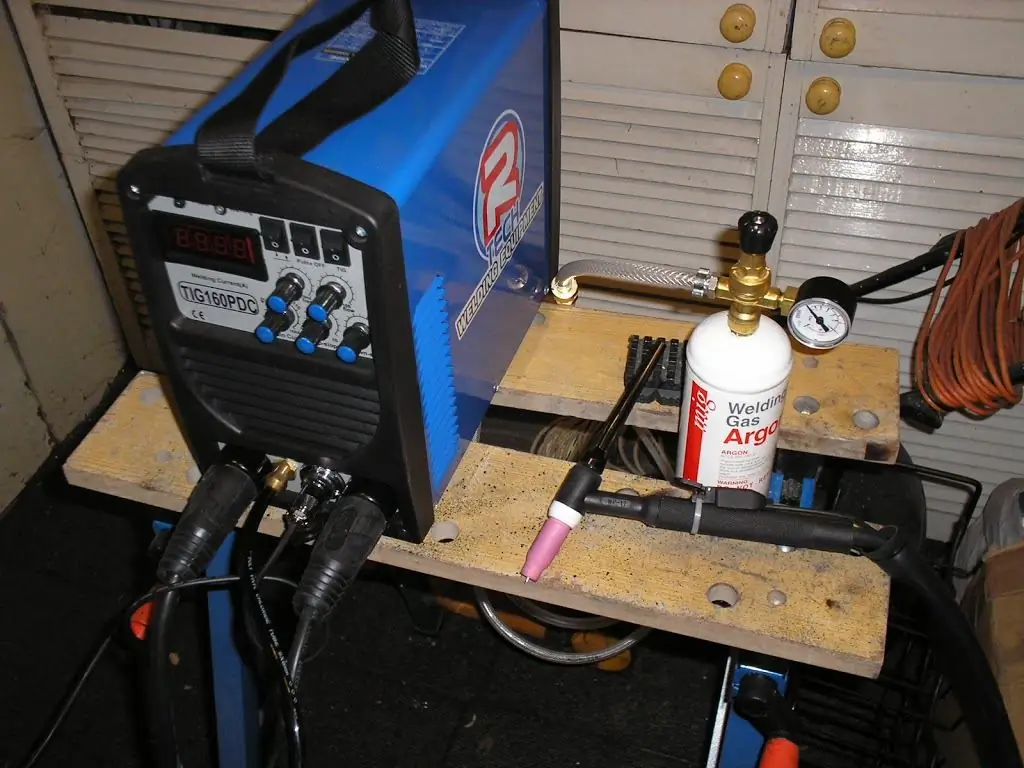
Accessories
Additional technical means and devices mainly perform communication between the main equipment, and also allow solving secondary tasks that are not directly related to welding. These devices include:
- Gas cylinder infrastructure including coils, reducers, heaters, casing, etc.
- Cleaning tool and separators designed to remove combustion products in the working area. This is especially true for welding operations in shielding gases with a non-consumable electrode, the melt of which is not directly included in the structure of the product. Both during and after the operationSeam sanding may be required.
- Dryer. Eliminates and regulates moisture contained in carbon dioxide. A kind of desiccant that works at high or low pressures.
- Filtration devices. Cleans gas streams of unwanted solids, also ensuring a clean weld.
- Measuring equipment. Typically, pressure gauges are used to monitor the same pressure and gas flow meters.
Welding modes and their parameters
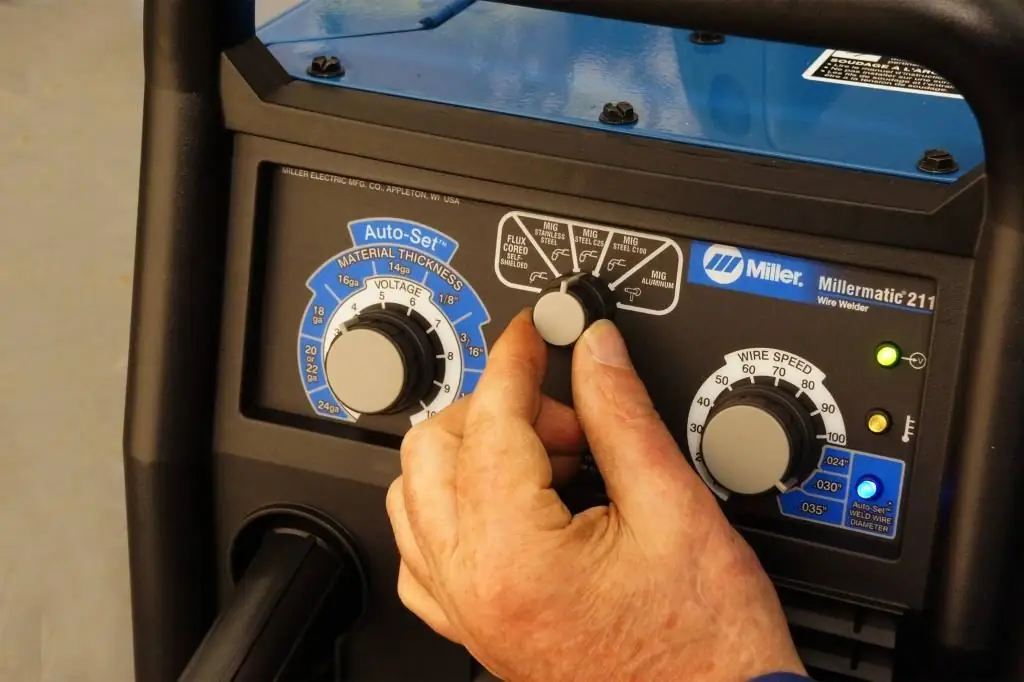
Approaches to the organization of the welding process in this case differ according to several criteria, which ultimately allow us to talk about the allocation of different modes of operation. For example, the methods differ according to the principle of the technical execution of the task - manual, semi-automatic and automatic. In a more detailed calculation of welding modes in shielding gases, the following parameters are taken into account:
- Current - range from 30 to 550 A. As a rule, most typical operations require the connection of sources of 80-120 A.
- Electrode thickness - from 4 to 12 mm.
- Voltage - 20 to 100 W on average.
- Welding speed - from 30 to 60 m/h.
- Consumption of gas mixture - from 7 to 12 l/min.
The choice of specific indicators largely depends on the type of metal, the thickness of the workpiece, the conditions of the operation and the requirements for the formed joint.
Manual welding
The key role in the process is played by the skill of the operator and the characteristics of the electrode. Almost all welderkeeps the process under its control, orienting the arc relative to the working surface and monitoring the parameters of the gas mixture supply from the cylinder. In terms of performance, the density and current strength, as well as the length of the welding path, will come to the fore. In manual welding in shielding gas, several passes are most often performed, especially if a thick workpiece is being machined. In other cases, an increase in the number of passes is associated with the need to correct the weld, change its length and the characteristics of the surfacing.
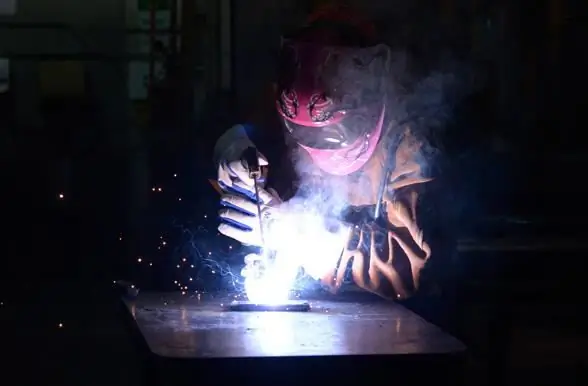
Semi-automatic welding
Today, this is the most popular welding production mode in a protective environment. The main difference between this method and the manual one is the presence of mechanization elements with rectifiers and the possibility of automatic wire feeding from a special coil. With semi-automatic welding in shielding gas, the operator does not need to be interrupted to change consumables, but the technique of interaction of the arc with the surface of the workpiece is still up to the user. The operator monitors the process of formation of the welding joint, correcting the current parameters, changing the angle of inclination, etc.
Automatic welding
Fully mechanized welding process, in which the user can only indirectly influence the supply parameters of consumables, gas mixture and powder flux. Technically, the operation is provided by multifunctional stations and platforms with robotic equipment. On highly specialized modern production facilities for automatic welding in shielding gasthe so-called tractor is used, the design of which provides for all the necessary functional units. This is a mobile machine that moves during the welding process along the seam formation line and at the same time guides the protective mixture into the welding zone. A mandatory component of such modules is the control unit, which initially contains a set of algorithms with actions for each executive body.
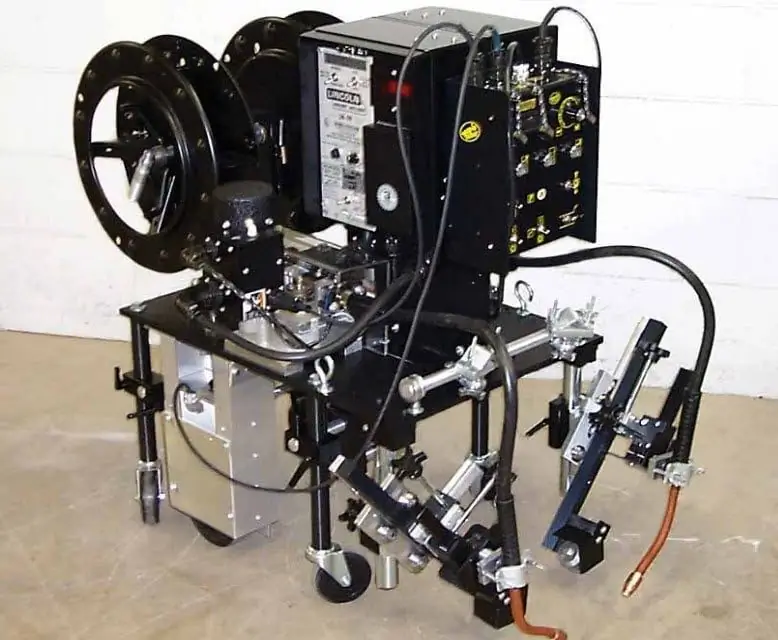
Conclusion
The use of methods for protecting the weld pool from oxygen allows, if not completely eliminating, then minimizing characteristic defects in the formation of the seam. This applies to lack of penetration, cracks, burns, sagging and other flaws that may occur due to contact of the molten surface of the workpiece with open air. The advantages of welding in shielding gases over the technique of using flux include the absence of the need to remove sludge in the working area. At the same time, other positive qualities of the process are preserved, such as the possibility of visual observation of the quality of the formed compound. If we talk about the shortcomings of the method, then its negative factors are the thermal and light radiation of the arc, which requires the provision of special measures for the individual protection of the welder.
Recommended:
Welding of ultrasonic plastics, plastics, metals, polymeric materials, aluminum profiles. Ultrasonic welding: technology, harmful factors
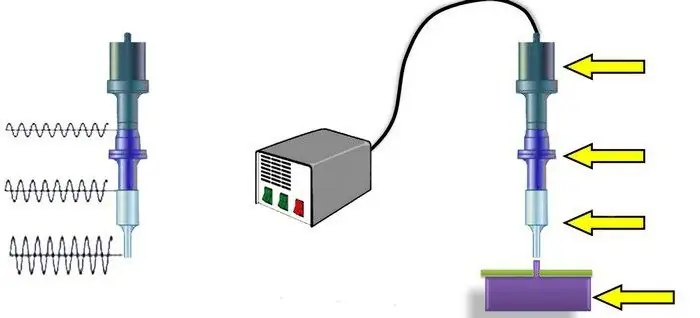
Ultrasonic welding of metals is a process during which a permanent joint is obtained in the solid phase. The formation of juvenile areas (in which bonds are formed) and the contact between them occur under the influence of a special tool
Thermite welding: technology. The practice of thermite welding in everyday life and in the electrical industry
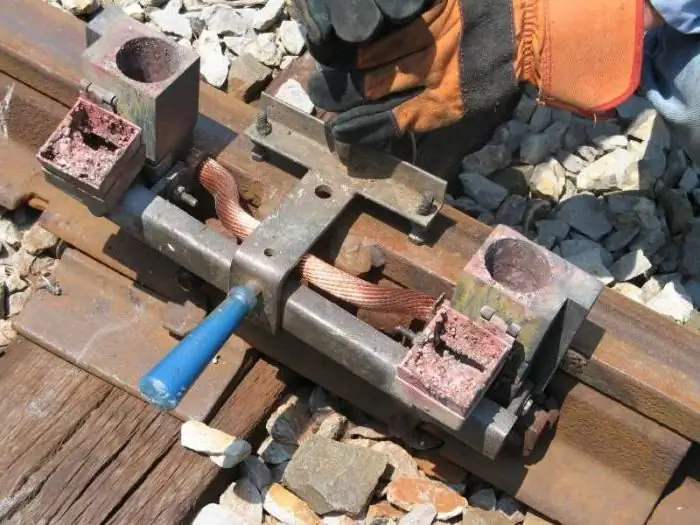
The article is devoted to thermite welding technology. The features of this method, the equipment used, the nuances of use, etc. are considered
Arc welding in shielding gas: description of technology, modes, methods
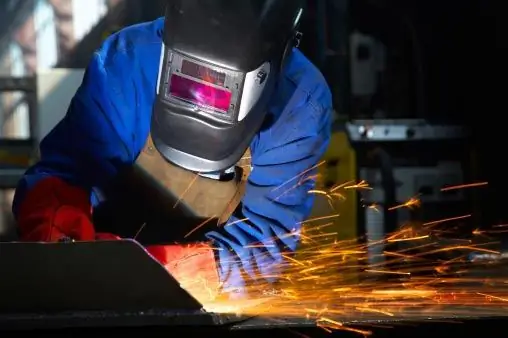
Gas shielded arc welding is a method that significantly improves the quality of the work result. This technology has a number of features. Before applying it, the master must familiarize himself with the basics of arc welding, which is carried out in a shielding gas environment. The features of this technology will be discussed in the article
Welding in a shielding gas environment: work technology, process description, execution technique, necessary materials and tools, step-by-step work instructions and expert advice
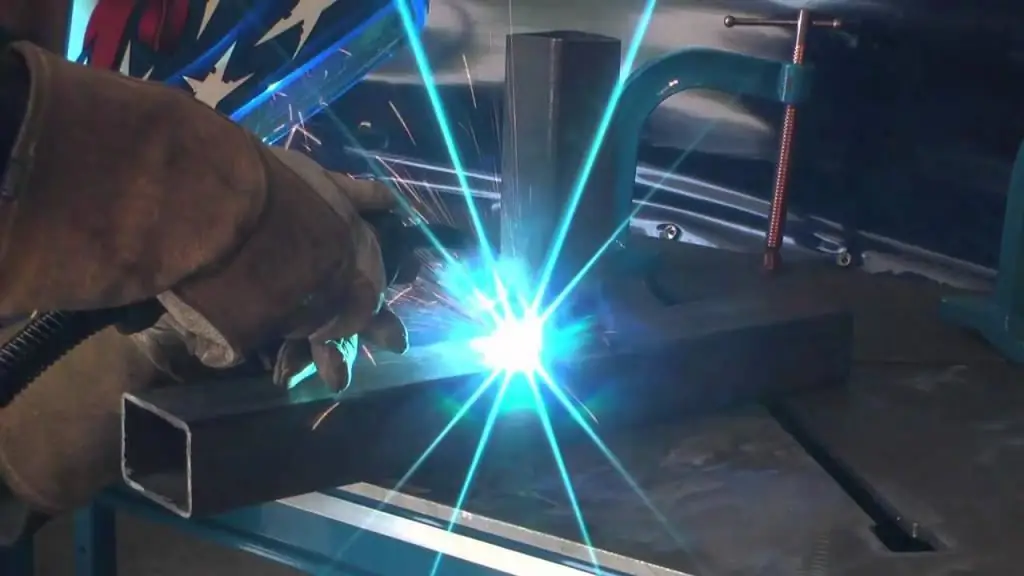
Welding technologies are used in various branches of human activity. Versatility has made welding in a protective gas environment an integral element of any production. This variety makes it easy to connect metals with a thickness of 1 mm to several centimeters in any position in space. Welding in a protective environment is gradually replacing traditional electrode welding
Flux for welding: purpose, types of welding, flux composition, rules of use, GOST requirements, pros and cons of application
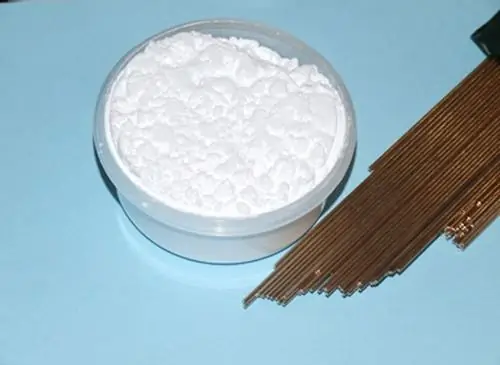
The quality of the weld is determined not only by the ability of the master to organize the arc correctly, but also by the special protection of the working area from external influences. The main enemy on the way to creating a strong and durable metal connection is the natural air environment. The weld is isolated from oxygen by a flux for welding, but this is not only its task