2025 Author: Howard Calhoun | [email protected]. Last modified: 2025-06-01 07:12
Reinforcement is a structure consisting of rolled metal bars of various shapes and sizes. Its main task is to redistribute compressive and tensile stresses within the construction object. Accordingly, increased requirements are imposed on the rigidity of such a structure. The stiffness index, in turn, is determined by the quality of the reinforcement connection by welding. Currently, several welding methods are used. We will consider the features of some of them in the article.
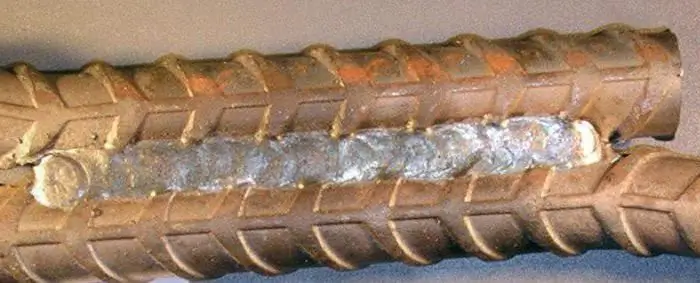
Rebar welding: GOST 14098-91
The most common types of connections are:
- electroslag semi-automatic;
- bath-suture;
- electric arc manual;
- contact;
- bathroom.
GOST defines the design, geometric parameters, types of joints obtained by electric arc and resistance welding of reinforcement.
The provisions of the standard apply to rods with a cross section of not more than 30, but not less than 4 mm, as well asmetal wire with a cross section of more than mm.
Connection types
GOST defines three types:
- lapped;
- butt;
- T-shaped.
Reinforcement overlap welding is performed on 2 reliefs and seams (electric arc manual method). The tee connection is made in inventory form (using one electrode in the bath), submerged (in this case, filler wire is not used), mechanized, manually, contact (by continuous melting of the product with resistance).
Butt welding of reinforcement is carried out in various ways. The most common are:
- In combined bearing and forming parts of twin bars with one rod.
- Mechanized using an electric arc and wire (powder additive).
- In inventory form.
- Handmade arc and multi-layered seams.
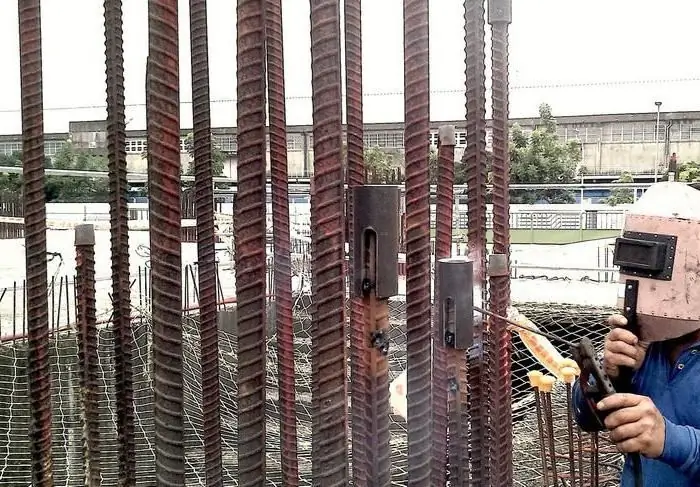
Bathroom welding fittings
This method is usually used to connect:
- Reinforcing products of large diameter (2-10 cm).
- Joints of bars arranged in several rows in reinforced concrete structures.
- Flange joints made of steel strips with a large section.
This method is perfect for welding reinforcement for foundations and other large reinforced concrete products, complex frames in the construction of various buildings. It ensures the preservation of the strength of the parameters and the rigidity of the structure along the entire length. This kind of weldingallows you to create a single power frame.
The connection can be made both horizontally and vertically. Bathtub welding of column reinforcement and other vertical products can thus be carried out without moving them and bringing them to a horizontal position.
Another advantage is that standard fixtures are used to make the connection, as in arc welding.
Important moment
The key condition for obtaining high-quality joints in bathtub welding of rebar is a clear alignment of the bars. It is necessary to ensure that the axes of the rods do not shift by more than half of their cross section relative to each other.
To comply with this condition, conductors of various types are used. In them, the geometric parameters and the location of the bars during welding of reinforcement remain unchanged.
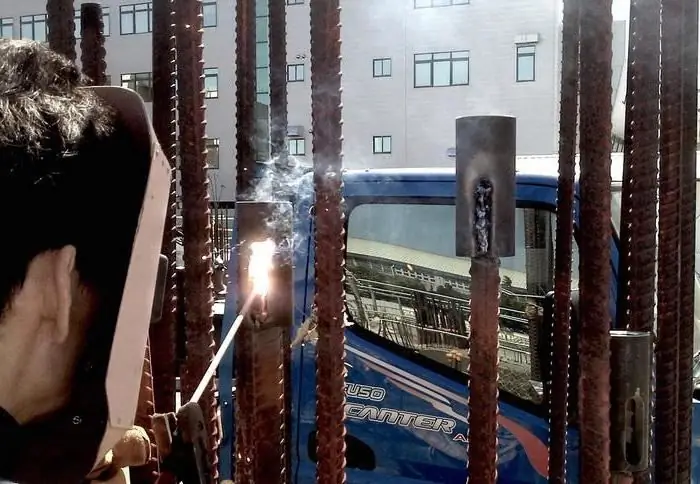
The essence of the method
Before direct welding, a steel mold is attached (welded) to the bars. It forms a bath with molten material. For this, an electric arc is used. The ends of the bars melt under high temperature. This results in one pool of weld material.
Before welding the reinforcement, the ends and surfaces of the bars are cleaned. They remove scale, corrosion, dirt. To do this, use a hard brush with steel bristles.
After cleaning, the bars are placed coaxially. There should be a gap between the ends. Its size is less than 1.5 rod diameters.
When welding the reinforcement of columns, sheet steel acts as a forming elementstamped form. It is attached to the bottom by welding without the use of additives. Fusion of the joint over the entire cross-sectional area is carried out by performing oscillatory gradual movements of the electrode. With respect to the axes of the bars, such movements are made perpendicular.
Excess slag is removed with a scoop. Then the end of the upper rod is attached to the end of the lower one, after which the metal is sent into the mold.
Slag is released from the mold through a special hole, which is burned with an electrode. After the connection of the rods is completed, it is brewed.
Bathroom welding options
In practice, three methods are used:
- Semi-automatic (in ceramic form).
- Single, three-phase electric arc using a steel clip (manual option).
- Automatic slag bath (copper mold).
The most economical is the option in which the pads are not used when connecting the rods. The fact is that for their manufacture it is necessary to spend a certain time and metal. With no escutcheons, a compact connection is also ensured.
Nuances
Welding in the bath is performed at high currents. It can be 450 amps if 5-6mm electrodes are used.
When joining products at low temperatures, approximately 10% higher than standard current is used. Professionals recommend using UONI-13/55 rods.
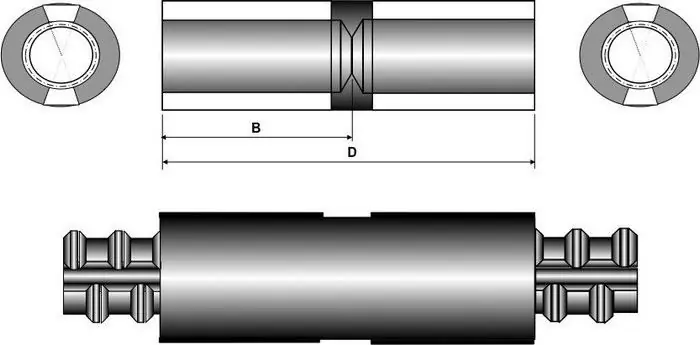
When using three-phase weldingleave a gap 1.5-2 cm larger than the diameter of the electrode. The index of misalignment of the axes of the reinforcement bars should not be more than 5% of the cross-sectional area of the electrodes. Experts recommend giving "reverse deflection" to the bars if they are longer.
Slag removal
Quite often, the ends of the rods are slagged when making a bathtub welded joint. This is due to the rapid heat dissipation. As a result, the reliability of the connection is significantly reduced. You can reduce the likelihood of slagging:
- Heating the ends before welding.
- Using metal molds made of heat-conducting materials. As a rule, copper elements are used.
Shackle
It is used to secure the joint from below. A shackle made of steel sheet with a low carbon content or made of bars is used.
The girth holds the liquid metal and prevents it from flowing. To increase the efficiency of fixation, limiters are mounted along the edges of the bracket, which prevent the spread of slag along the rod.
Do not use overhead elements made of copper, brass, bronze alloys. As a rule, they are made of pure copper. These staples last quite a long time.
Contact method
It is considered one of the most common welding methods. The place of contact of the products is melted by heating to the temperature of deformation and compression. This is done by passing current through the circuit, the links of which are, among other things, the rods themselves. The current appears in a closedchain, and the greatest resistance is concentrated at the contact area of the bars. At the same time, heat is released, which ensures maximum heating of this area.
You can reduce the welding time by increasing the current strength to 10, and in some cases up to 20 thousand amperes. In this case, the melting of the metal occurs almost instantly. Accordingly, the time of current passage through the circuit is significantly reduced.
Contact connection of products can be carried out in a butt or point way. The first is used when the end parts are butted. Reinforcement spot welding is used when the bars overlap each other. They connect at several points at the same time.
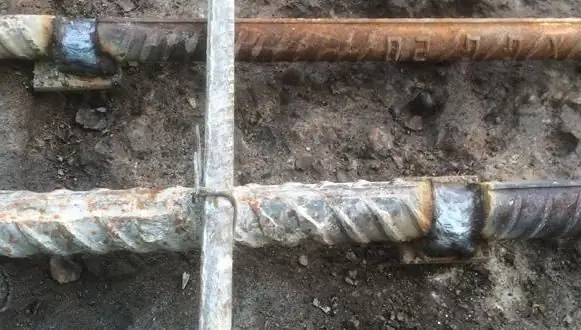
Equipment
A professional apparatus is used to connect the rods by contact. Reinforcement welding must be carried out at a certain current strength and the level of compression of the contact area, for a specified time.
All equipment is conditionally divided into mobile and stationary. The simplest apparatus can be assembled independently. It should include 2 functional nodes. The first is the power supply, the second is the remote type electrode holders.
Butt joint
Its technology is based on the use of heat at the ends of products. Heating occurs due to the passage of electric current through these areas. It is supplied after the circuit is closed by connecting the ends. High resistance heating is provided.
After the transmission is completed and the current is turned off,"draft" of the heated area. A high current load mode is used to quickly heat the metal in the joint area and prevent heat loss.
Butt welding is used to connect smooth rods with a diameter of at least 14 mm. For joining rebar made by hot process and having a profile, this method is used if the diameter of the bars is not less than 32 mm.
Features of work performance
Butt welding technology is divided into two types:
- Continuous way.
- Intermittent method.
Priority is given to the second type. Before starting work, the ends of the reinforcement are cleaned of slag formations, paint residues, and rust. For this, a chisel, a hammer and a metal brush are used. The cleanliness of the ends is essential for the quality of the weld.
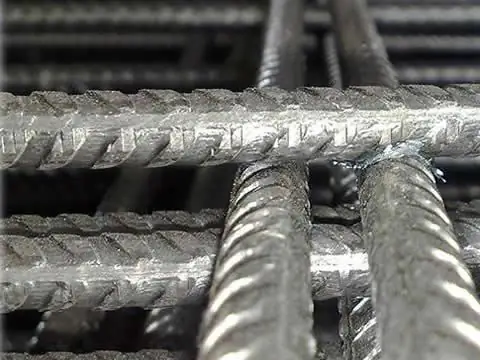
Point connection
It is mainly used in the creation of reinforcing cages, reinforcing meshes from bars with a small section.
You can also use spot welding at home, for example, when repairing household appliances.
There are two ways to connect. In the first case, the metal in the joint area is brought to a molten state and to the formation of a cast core. In the second, the metal simply heats up.
If a large current passes at the intersection of point-contact rods, high heat transfer will occur in this area. This is due to the fact that the resistance of the reinforcement bars is higher than that of the copper conductors included in the secondarycontour of the machine for welding.
The process should be carried out at high current rates. Due to this, not only performance is improved, but also the quality of the connection. For this, powerful expensive equipment is used. At home, you can use a compact device, including those made independently.
The key unit of the device for spot welding is the transformer. Due to it, a large current is generated. The device can use a standard type transformer OSM-1. However, it needs to be slightly upgraded to obtain a higher power secondary winding.
Point connection process
The work is being done in stages:
- The bars are stacked in a certain position and placed between the electrodes of the apparatus. They are pressed tightly in the area of \u200b\u200bthe future connection.
- Current is applied to the contact area; the metal is heated to the plastic state required for deformation. By pressing, a sealing belt is formed, which prevents the metal from spreading.
- The current pulse must be strong and short-lived. This will ensure that the rods make firm point contact after the feed stops.
Splice
It involves the fixation of rods partially superimposed on each other. When using this method, the bars form one line with mutual overlapping of their length at the docking areas.
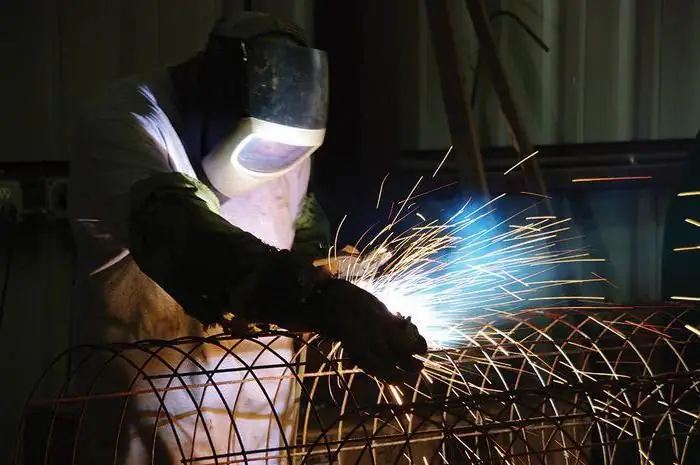
The lap joint is used to distribute the longitudinalcompressive / tensile load on the surface of the rod. When performing work, you must follow some rules:
- Overlap is allowed in areas with minimal stress on the structure.
- Sticks of different diameters should be distributed evenly. However, it is better to use the same bars.
- Overlap welding is used to connect rods with a cross section not exceeding 20 mm.
- Mutual overlap of bars should be more than 50 cm.
Overlap welding of industrial products under increased load is recommended using manual arc welding. It is carried out with one or two seams from the flanks. In order for the joint to turn out to be of high quality, the length of the seam must exceed the diameter of the bars by at least 10 times.
Manual arc welding is performed, as a rule, in a horizontal position of the rods. For operation, conventional equipment is used, which includes a transformer, gas burner, or apparatus with neutral gas.
Recommended:
The main consumable for welding - welding wire
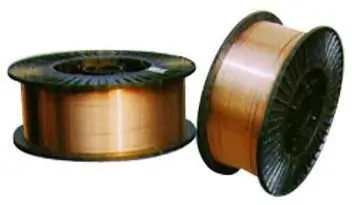
Welding wire is used in various welding operations, it is the main consumable material that acts as an electrode. Welding operations require extensive professional knowledge, a responsible approach to the choice of raw materials. For welding structures, it is unacceptable to use random wire of incomprehensible marking and unknown composition
Welding of ultrasonic plastics, plastics, metals, polymeric materials, aluminum profiles. Ultrasonic welding: technology, harmful factors
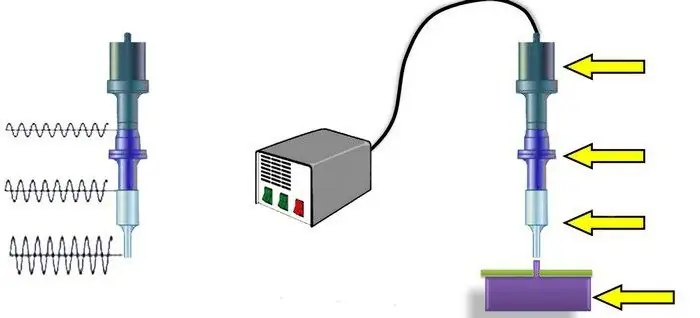
Ultrasonic welding of metals is a process during which a permanent joint is obtained in the solid phase. The formation of juvenile areas (in which bonds are formed) and the contact between them occur under the influence of a special tool
Welding consumables: definition, characteristics, manufacture, storage. Main welding material
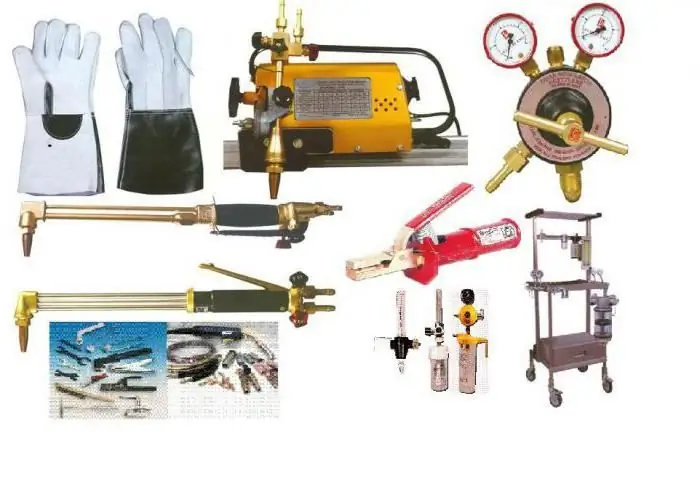
Main types of welding consumables, features of storage of explosive gases, characteristics of electrodes depending on the material and other parameters
Thermite welding: technology. The practice of thermite welding in everyday life and in the electrical industry
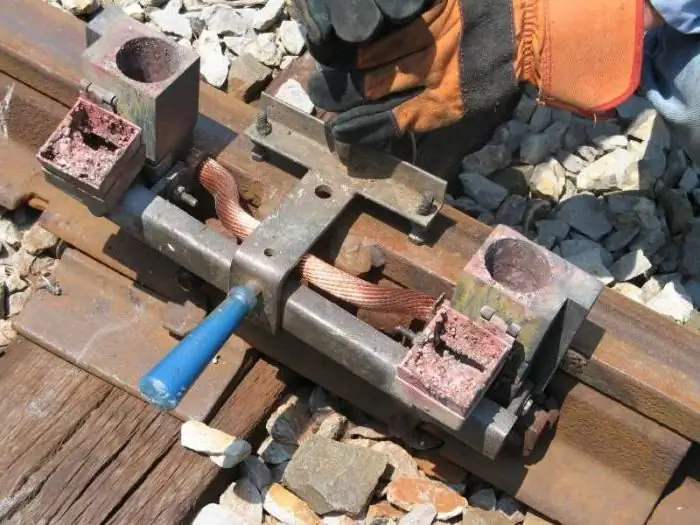
The article is devoted to thermite welding technology. The features of this method, the equipment used, the nuances of use, etc. are considered
Restoration of parts by welding and surfacing: methods and methods of restoration, features, technological process
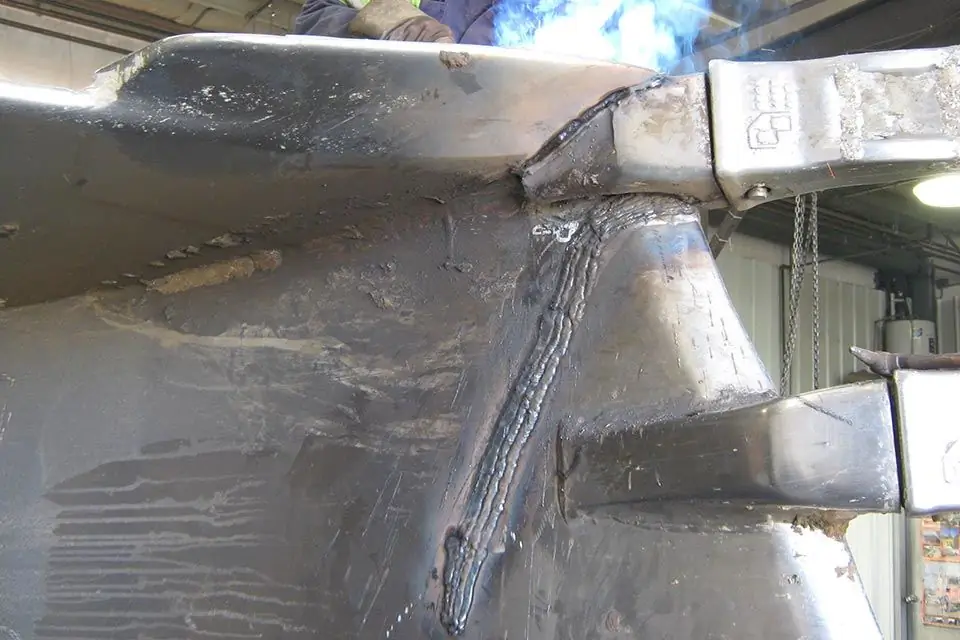
Welding and surfacing technologies allow efficient restoration of metal parts, providing a high degree of reliability and durability of the product. This is confirmed by the practice of using these methods when performing repair operations in a variety of areas - from car repairs to the production of rolled metal. In the total amount of work on the repair of metal structures, the restoration of parts by welding and surfacing takes about 60-70%